No, a good, well-set-up vinyl playback system should be almost silent and exhibit no audible hum, either at rest or when playing records.
This is one of the great revelations about vinyl that many folks discover on the journey from basic equipment to more aspirational gear. Some, sadly, never progress far enough to reach this realisation, however.
The short version is that, if you haven’t listened to a serious vinyl rig, you need to, if only to have a reference point for how good vinyl can sound.
What is ‘Hum’?
The term ‘hum’ describes continuous low-frequency tones of a constant frequency or pitch, usually centred around 50/60Hz or 100/120Hz. Hum can be mechanical or electrical in origin and usually indicates a problem in the playback system. Whatever the origin, hum should be tracked down to the source and eliminated or minimised.
Electrical Hum
Bad or missing earths/grounds are a common cause of electrical hum in vinyl playback systems. The high sensitivity and gain of a vinyl playback chain will take tiny ground currents that cause hum and amplify them to the point where they will become an audible problem. Any currents flowing in the ground system will be audible, and so we want to eliminate them.
By definition, current flows between two points with a different potential or voltage. Ground currents that cause hum occur where two elements in the playback chain reference different grounds and therefore sit at slightly different potentials. Bad cables can play a part here, as some do not have an effective ground linking both ends of the cable structure.
Therefore, the trick to ensure a quiet system is to ensure the turntable/pre-amp/amplifier combination is effectively grounded together and that at least one piece is system ground-referenced. All grounds must be of a low impedance, made using clean, quality wire and connectors.
Mechanical Hum
Mechanical hum can originate from turntable motors and mains transformers. The hum from both sources can often be resolved with the right attention and some new parts, with specific attention paid to damping and isolation.
Cheap phono preamps, cartridges and cables will always be noisier than good ones, and active preamps will always be noisier than transformers. An English brand of turntables that shall remain nameless opts not to use a separate headshell/arm ground. These decks are generally noisier than turntables with better, separated ground arrangements. Equipment type, set-up and installation can all contribute to hum.
Acoustic Feedback
Mechanical vibration from the turntable itself or other equipment can be coupled through a turntable, back into speakers, creating what’s called a positive feedback loop. These loops can occur through shelving, for example shared by speakers and turntables, wooden floors and other resonant structures.
In these cases, the hum makes its way to the speakers, which energises the turntable, arm, and record at the hum frequency, which is then fed back into the signal chain and further amplified, creating what we call a positive feedback loop.
Positive feedback loops can very quickly go out of control and destroy speakers and even amplifiers, so if you have a hum that appears to be coupled through your turntable, resolve it or seek expert help immediately!
Rumble
Rumble is another source of low-frequency noise generated by a turntable’s spindle and/or motor bearings. This is typically a broader-spectrum LF noise than hum and may consist of several fundamentals or tones, and their harmonics.
Rumble intensity is generally inversely correlated with turntable price. In other words, the cheaper the turntable, the greater the rumble, and vice versa. This is because cheaper decks have poorer mechanical quality, looser bearing tolerances and greater bearing surface roughness. Consequently, cheap turntables are often rumbly.
More expensive machines have bearings machined to tighter tolerances, better bearing surface finishing, higher quality motors and other parts, heavier chassis, better lubrication, and so on. These elements contribute to lowering the noise floor of better gear, such that it becomes essentially inaudible.
Quiet
In well-set-up vinyl playback systems consisting of quality components, correctly connected, there is no audible hum. The predominant noise in systems like this is groove noise, a residual component of the cutting lathe, the friction between the stylus and the groove itself.
There will also be some phono preamplifier noise in the form of a soft and gentle ‘rushing’ sound that will be inaudible during normal listening. Some white noise is present in all systems, but hum is absent from all good ones.
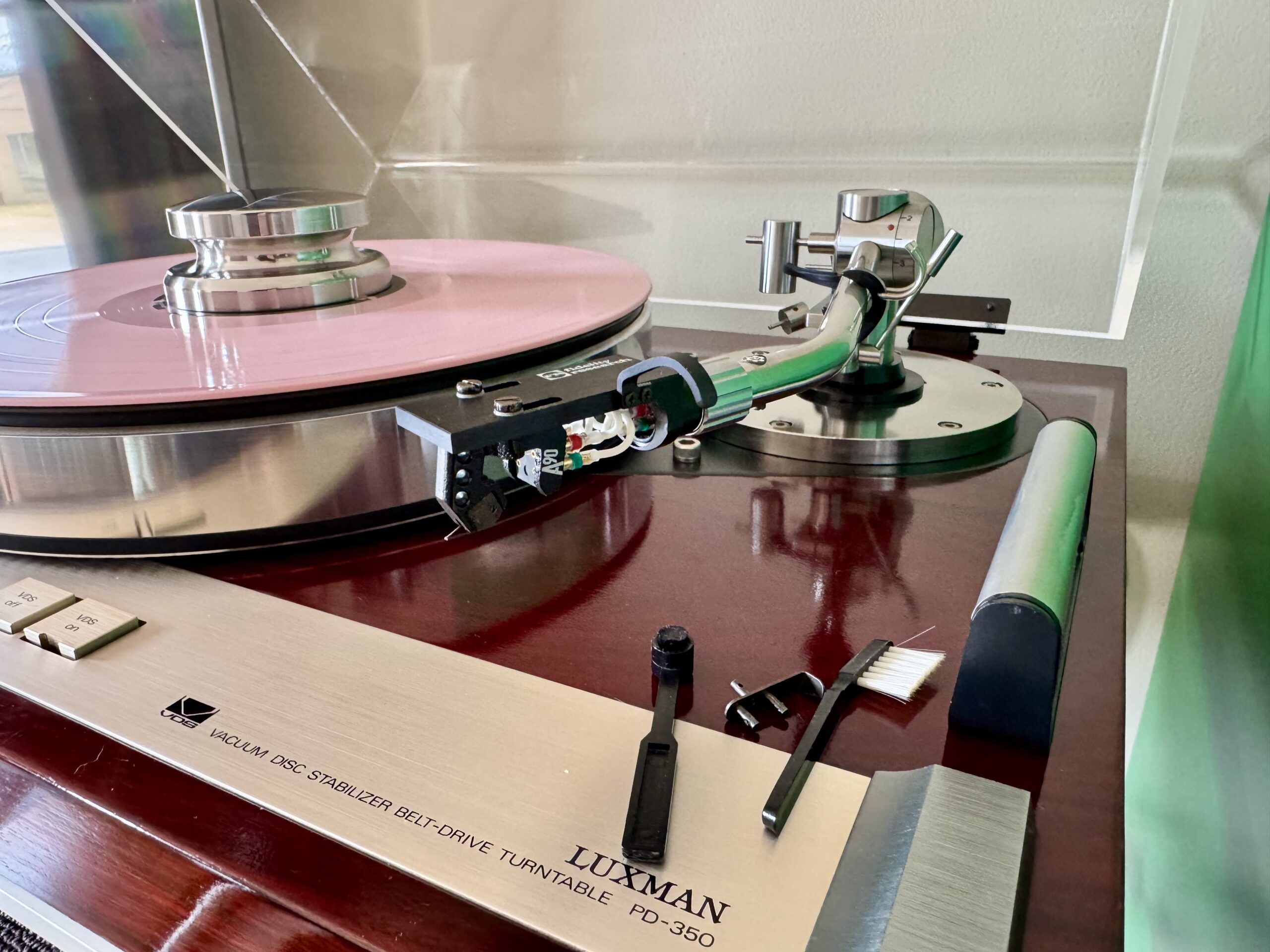
There’s absolutely no hum in my reference set-up (above) consisting of a Luxman PD-350, Fidelity Research FR-64S, RS-141, Ortofon MC-A90, feeding my Accuphase C-290/AD-290 and Accuphase A-75.
Mike, by “no hum” do you mean very little hum..?
Ah, no, I mean no hum – none, zero, nada! There should be no audible low-frequency components in a good vinyl system. If there is, the system either has a weak link letting it down or poor setup elements creating a problem, maybe even both.
If you are curious about how quiet a vinyl playback system can be, let me know. If I’m not too busy, I may have a moment to demonstrate my reference system. This will provide a sonic baseline from which to make comparisons.
Discover more from LiQUiD AUDiO
Subscribe to get the latest posts sent to your email.