Welcome to our comprehensive, categorised FAQs.
Frequently asked questions or FAQs, are questions about a topic or theme that are often asked. Ours answer more than 140 questions I’m commonly asked about amplifiers, turntables, vintage vs modern equipment, equipment service and repair, Liquid Audio and more.
FAQs are organised into categories grouping questions thematically. I go into considerable detail, providing information to help people make more informed decisions. Many of the answers are significant articles in their own right and make interesting reading. Some of the most popular include:
- Class A, class AB and class D amplifiers
- Is turntable hum normal?
- Should I play records on radiograms?
- How can I detect audio ‘guru’ BS?
- Do cables, connectors, etc matter?
- What’s better – vintage or modern CD players?
- Cartridge alignment WTF?
- What’s better – belt-drive or direct-drive?
- How much will my repair cost?
- Is the Denon DL-103 any good?
- Choosing a better amplifier
Don’t hesitate to contact me if you have a question I’ve not answered here. Suggestions are always welcome!
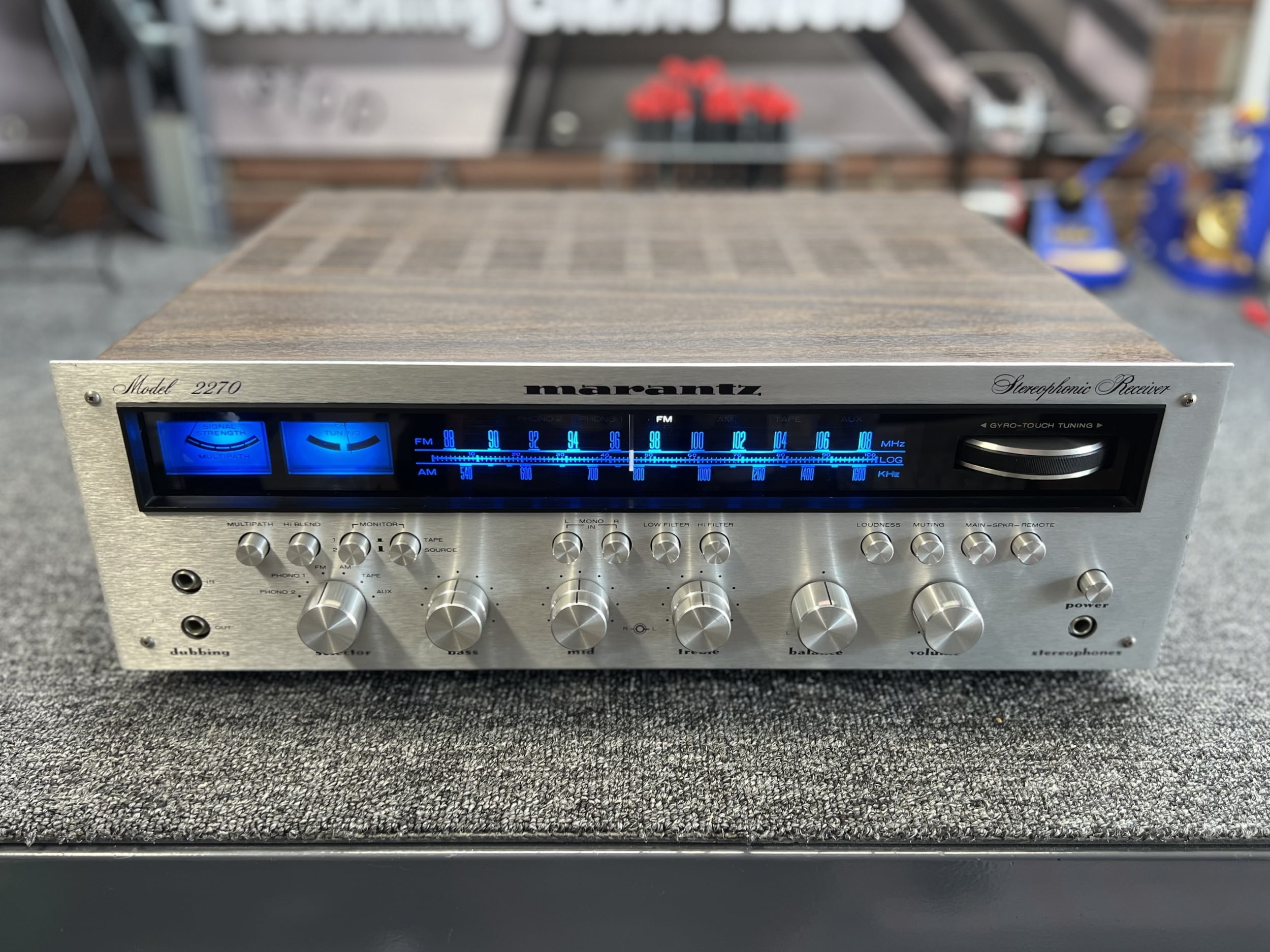
FAQ Categories
- All
- Amplifiers & Speakers
- Cassette Decks
- CD Players
- General Hi-Fi
- Liquid Audio
- Service & Repair
- Tuners & Radios
- Turntables & Vinyl
- Vintage vs Modern
Mike, do you want to pay more than retail for my hi-fi equipment?
Ah, no, but thanks for asking…?!
Incredibly, this is a question I’m asked frequently. The basic concept/question is: do I want to pay retail, or even above retail prices, for someone’s equipment? The extra bits that are obviously not considered are that I need to repair, service, clean, photograph, list and offer a three-month warranty on that equipment, whilst still making a useful profit. You’ll see the problem.
For any business to buy and sell equipment sustainably, they need to acquire it for significantly less than they sell it for. Keep in mind that I need to spend time and energy on every piece to ensure it meets the high standards we set for pre-owned equipment we sell, often many hours, and every piece carries some risk.
Logically, I can’t pay $1000 for something that I can only sell for $1000, let alone something I’ve not seen, have to spend time repairing and preparing for sale and then listing, and offer with a warranty. I can’t even pay $500 for something I sell for $1000, and I can’t pay ANYTHING for equipment that I cannot inspect and test.
There has to be profit in it, or the exercise is pointless, but more importantly, this concept has to be commonsense, or there is a real problem! There are plenty of curb-crawler Gumtree flippers out there who add no value, offer no warranty and dream of a reputation like ours. Even those guys won’t pay retail prices for equipment!
Do you enjoy your work?
I do, I genuinely love helping people improve their enjoyment of hi-fi, and I especially love solving technically challenging problems with hi-fi gear. I also love hi-fi gear and music, it all goes together, so yes, I very much enjoy my work, far more than any corporate or government job I’ve ever done!
Are you leading a conspiracy against bad technicians?
Of course not, these guys create all the trouble they find themselves in, with zero help from any of us. But I don’t like seeing good people ripped off and equipment destroyed, and I will talk about that. Not sorry.
The worst offender has started telling people that there is “a conspiracy” against him, led by, guess who? Me! Why? Because I’ve dared to expose just a fraction of the terrible work he has done and warn people about it.
This silly assertion reflects the level of brain rot we are dealing with here: It’s not the bad work, telling reviews, court cases, including a high-profile loss in Joondalup Magistrates Court in 2024, irate customers, incoherent, unprofessional rants at customers, and blown-up equipment. Of course not. Rather than take any responsibility, this gentleman blames me for his problems.
That’s right – It’s all MY fault! The disasters I’ve documented as a public service in the Hall of Shame, the people who’ve taken this guy to court, the bad work my colleagues and I have been discussing and dealing with for over a decade? We apparently should be acknowledging this guy as some sort of misunderstood genius!
The truth is, these perpetrators are upset because they don’t want anyone showing you what they really do, and they can’t handle that others do good work and are respected for doing so. Well, that’s too bad. I refuse to sit by and do nothing about the destruction of equipment by unskilled individuals, and I don’t care how upset that makes them!
Can tuners sold in Japan be used in Australia?
No, and this is a commonly made mistake.
AM/FM tuners are still sought after for their high performance with high-quality analog FM stereo signals. In Australia, the FM broadcast band is 88 – 108 MHz, so any tuner you purchase needs to cover that same frequency band. Tuners from Europe and North America do, tuners sold in Japan do not.
The problem is that the Japanese FM broadcast band is 76 – 90 MHz. There is just a 2 MHz overlap with our FM band here in Australia. Because tuners (radios) rely on tuned circuits utilising inductors, capacitors, etc, there isn’t a simple switch that can be flicked to fix this.
Almost all good tuners have two different RF front ends to deal with this, and they are installed at the factory, based on where the tuner is going. You need to choose a tuner designed for 88 – 108 MHz. No Japanese market tuner is.
Can you give me an equipment valuation?
Certainly, if bookings are available simply fill out the contact form and request an assessment/valuation!
Check our booking status table and contact us via the contact page. Note that I can’t offer a valuation on equipment I have not carefully inspected and tested in the workshop. A thorough (ie proper) assessment and valuation helps sellers achieve the most for their equipment, but requires time and expertise.
How important is customer loyalty to you?
Very important. Allow me to explain.
Loyalty and integrity are core values @ Liquid Audio, driving how I run my business and care for my customers. I’ll always support those who value my work and what we stand for. I supported a customer in getting this guy banned from StereoNet. I’ve helped many deal with shonky repairers, RF’d gear and deadbeat sellers. I educate the hi-fi community with articles and advocate for improvements in my industry to benefit all. I even support people like YouTuber Stephan Fischer, who was sued for reviewing DCS lithium batteries:
Given all that positive effort, I appreciate those I’ve helped returning the ‘mojo’ via recommendations, reviews, and bookings, particularly for equipment we specialise in. Unfortunately, some who’ve benefited most from my help have given the least back, and worse: misled me and others, dishonestly taken advantage of my expertise and even engaged competitors or Hall of Shamers for equipment I’ve assisted them with or helped them acquire.
I wrote about problematic individuals precipitating operational changes a few years ago, with that article receiving overwhelming community support. It seems we all know people who abuse the favour and consume time and energy that would be far better spent on others. To protect my valuable time and energy, I focus on those who value and appreciate it. Those people are cherished as much as the equipment we care for.
What are the most brutal dark metal tracks you’ve heard?
Epic question, here are the most brutal metal tracks I’ve heard.
I’ll add more as I think of them and feel free to tell me your faves because I want to know what they are!
Desolator, by FacePalmGawd
This song is truly brutal, and I love it for that.
Tryzub Miy Styah, Tryzub Miy Horn, by Burshtyn
What a metal epic this tune is, incredible!
Obliquity of the Ecliptic, by Blood Incantation
I can’t tell you how much I like this song, but it’s a lot!
Beg for Life, by Tomb Mold
Epic, brutal!
Can you tell my technician what parts to use?
No, I don’t get involved in repairs I’ve not been engaged to undertake.
Read this FAQ for more about why, but here are the key reasons:
- My site already assists via more hi-fi repair contributions than most other reputable sources.
- Remotely assisting with equipment I haven’t inspected and diagnosed is not a service we offer.
- My work is copied, often for commercial gain, without acknowledgement or remuneration.
- “Can you tell my technician?” is often code for “Can you tell me, and I’m the technician”, relating to point 3.
- Bottom line: it’s not my responsibility to help other repairers.
In all seriousness, I’ve lost track of how many times people have told me “their technician” asked them to contact me, only to discover that these enquirers are technicians or store owners trying to steal my help/time/expertise by misrepresenting their situation and getting my help for free. That’s not how this works.
I get nothing from these interactions, so helping people who ask this, and the related “Can you help me fix my equipment?“, is not high on my list of priorities when I have a workshop full of customer equipment to repair. It’s nothing personal, it’s just a simple business consideration.
Can I visit outside your business hours?
No, please don’t!
I love my customers, but I run regular business hours, as all businesses do.
I’ve had people arrive here unannounced, early on a Sunday morning and late at night. I get calls and messages at all hours from people I don’t know. I’ve even had people I’ve specifically instructed not to arrive before I open, do it anyway. That’s not OK!
I don’t know of anyone available 24/7, except those guys who extinguish oil well fires. Their rates are higher than mine and more than most can afford, so for the record, I am only available during my business hours, advertised on the home and contact pages, in my Google business profile, and here:
Owner: | Mike Fitzpatrick BSc(Hons) GDipEd(Sc) UWA |
Location: | Carine, Western Australia |
Specialty: | Service, repair & restoration of classic hi-fi stereo equipment |
Focus: | Integrated/pre/power amplifiers, turntables, CD players/DACs, tuners, cassette decks |
Open: | Tuesday – Friday, 10 am – 5 pm Saturday, 10 am – 1 pm, Perth time |
Bookings: | By appointment |
Phone: | (+61) 0439 690 436 (Voice calls, no SMS messages please) |
Why have you stopped writing upgrade articles?
I haven’t completely stopped writing them, I’m just tightening up a few things.
Upgrade articles take a ton of time and effort to generate, so I often include a prompt:
“If you’ve found this article helpful, consider shouting me a drink using the donate button in the footer.”
The problem is that, despite the thousands who utilise them, few say thanks, let alone make a financial contribution of any kind. Given that these articles are a public service and often used by others for commercial gain, I find this to be problematic.
I get that everyone wants everything for free. My entire website is free! Creating content that helps my competitors yet generates no revenue, just isn’t a great business idea, though. For this reason, I’ll stick to my regular content that most readers enjoy and that brings in a little business at the same time.
What is the “only 50 hours” cartridge meme?
This one is a real gem and unfortunately causes much pain.
The “only 50 hours” cartridge use meme has been part of the hi-fi community for decades. Briefly, it’s where someone selling a cartridge dramatically understates the number of playing hours a cartridge has seen to get a better price at sale.
Typical phrases include: “Less than 50 hours,” “Only 50 hours,” and even “Only 20 hours.” Dishonestly misrepresenting the amount of use something has seen is the equivalent of rewinding the odometer on a car. This is a dog act and only the worst people do this. Thankfully, karma always gets them in the end!
Wear
Cartridges wear out, based on playing hours, the condition of your vinyl and other factors like stylus profile and tracking force. I’ve written more about stylus life in this FAQ.
A typical suspect cartridge-for-sale ad might read:
“Ortofon MC Jubilee moving coil cartridge for sale, like new, only 50 hours!”
50 hours is almost new for a premium line-contact type stylus of the type used in the MC Jubilee, perhaps only 2 – 3% worn. The really stupid part is that people are rarely creative in terms of their usage estimates. Folks invariably settle on the 50-hour estimate, no matter how ridiculous or implausible it is that every cartridge for sale has “only 50 hours” of use!
Actual wear and usage can be estimated, a specialist service we offer, and something I helped my customer with, in the case I’m about to describe. In this case, we got a dishonest seller banned from the platform he was selling on.
Example
Based on what I’ve seen over the years, one should probably use a 10x multiplier with many or even most cartridge listings. Take this example from a seller in Tasmania, advertising on StereoNet here in Australia.
This Ortofon 2M Bronze moving magnet cartridge, a transducer I’m very familiar with, was listed as having “Only 20 hours of use”, and in supposedly “excellent condition”. Yeah, right. One of my customers purchased it and asked me to install it on his Pioneer PL-71 direct drive turntable, after servicing the deck for him.
I realised after closely inspecting the cartridge that it was damaged and the suspension was at end of life, likely from misuse. It looked more like it had seen 200+ hours, perhaps many more, tying in with my 10x multiplier advice. It might look like this after 20 hours of ploughing my garden beds, but certainly not playing good, clean vinyl.
The seller’s photos were poor and/or misleading because they lacked the resolution, detail and angles needed to see the condition of this dud. Unhelpfully, the seller did not respond to my customer when he raised his concerns which already raised suspicion.
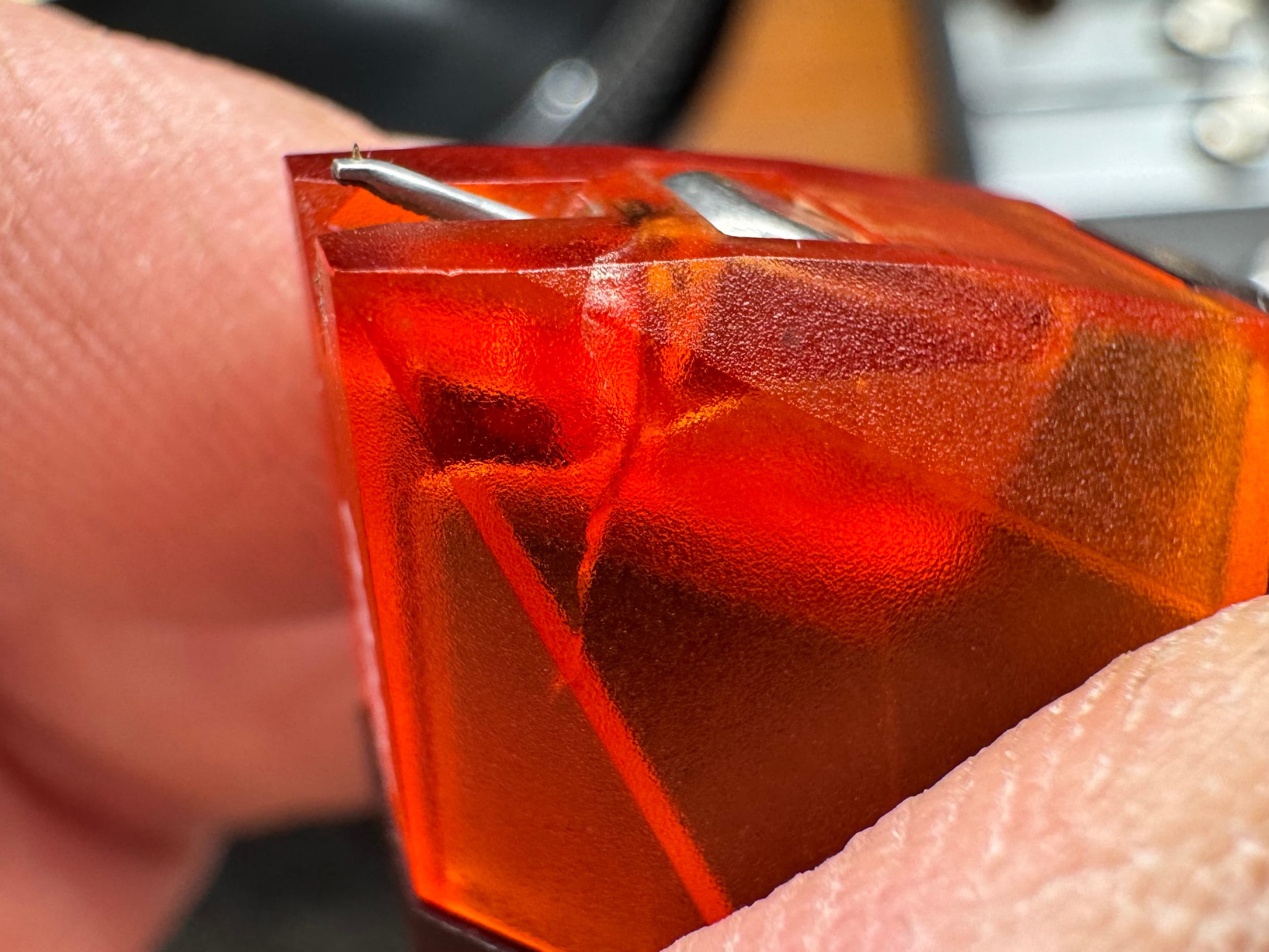
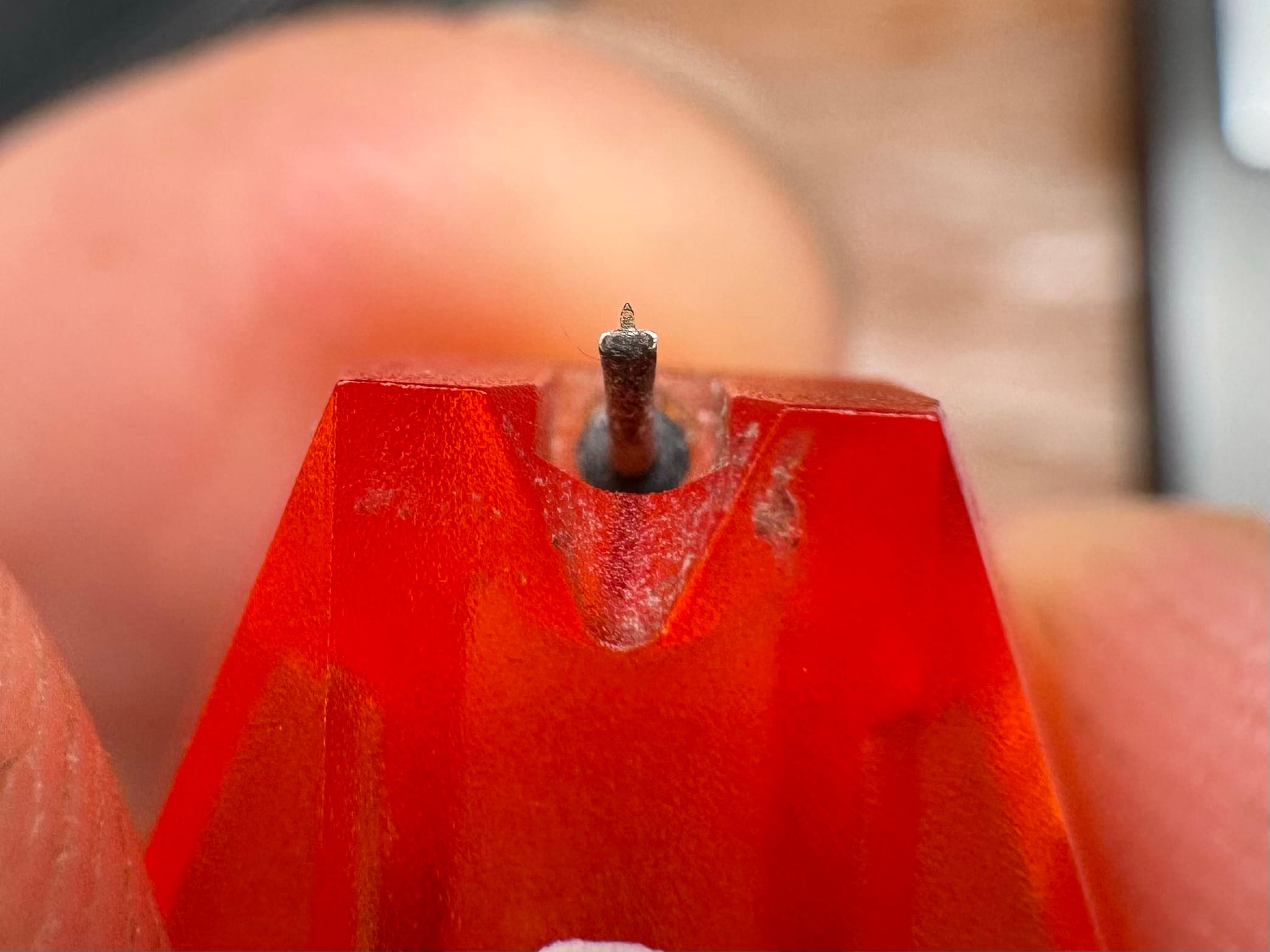
This is easily fixable with a new $500 stylus of course, but that defeats the purpose of buying a cartridge with only “20 hours” of use. I find it hard to imagine the seller/s didn’t know about this and shame on them for passing this on if they did. The worst thing is that folks like this seller scream the loudest when someone sells them junk, but they are often quite happy to do it to others. Great.
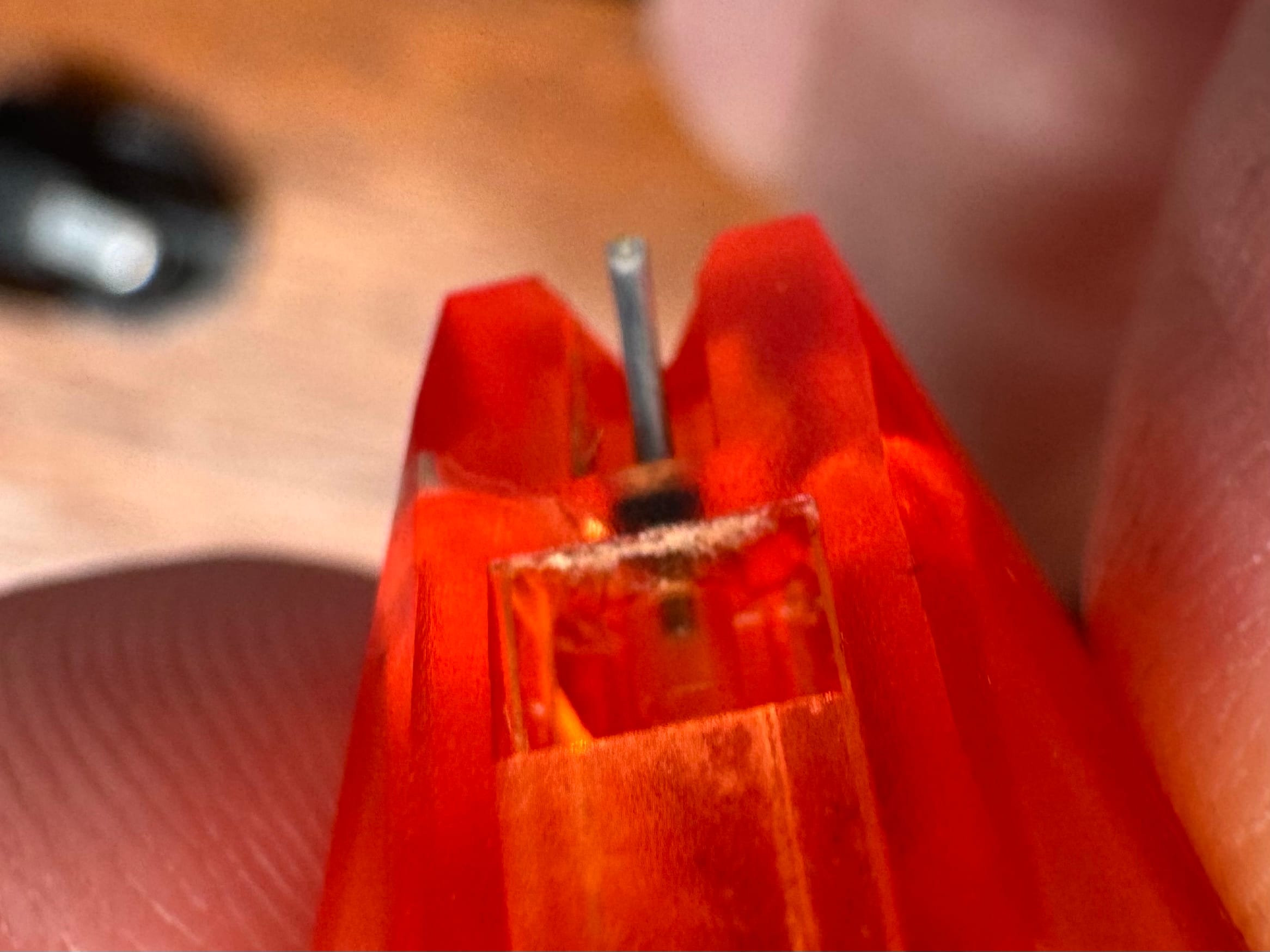
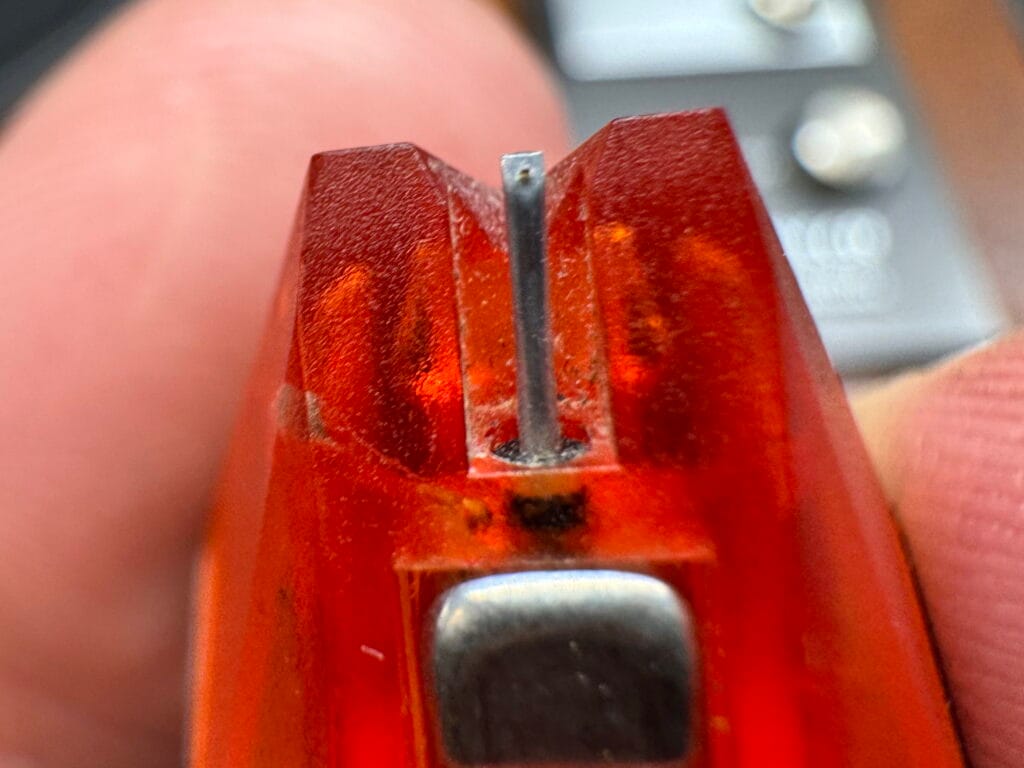
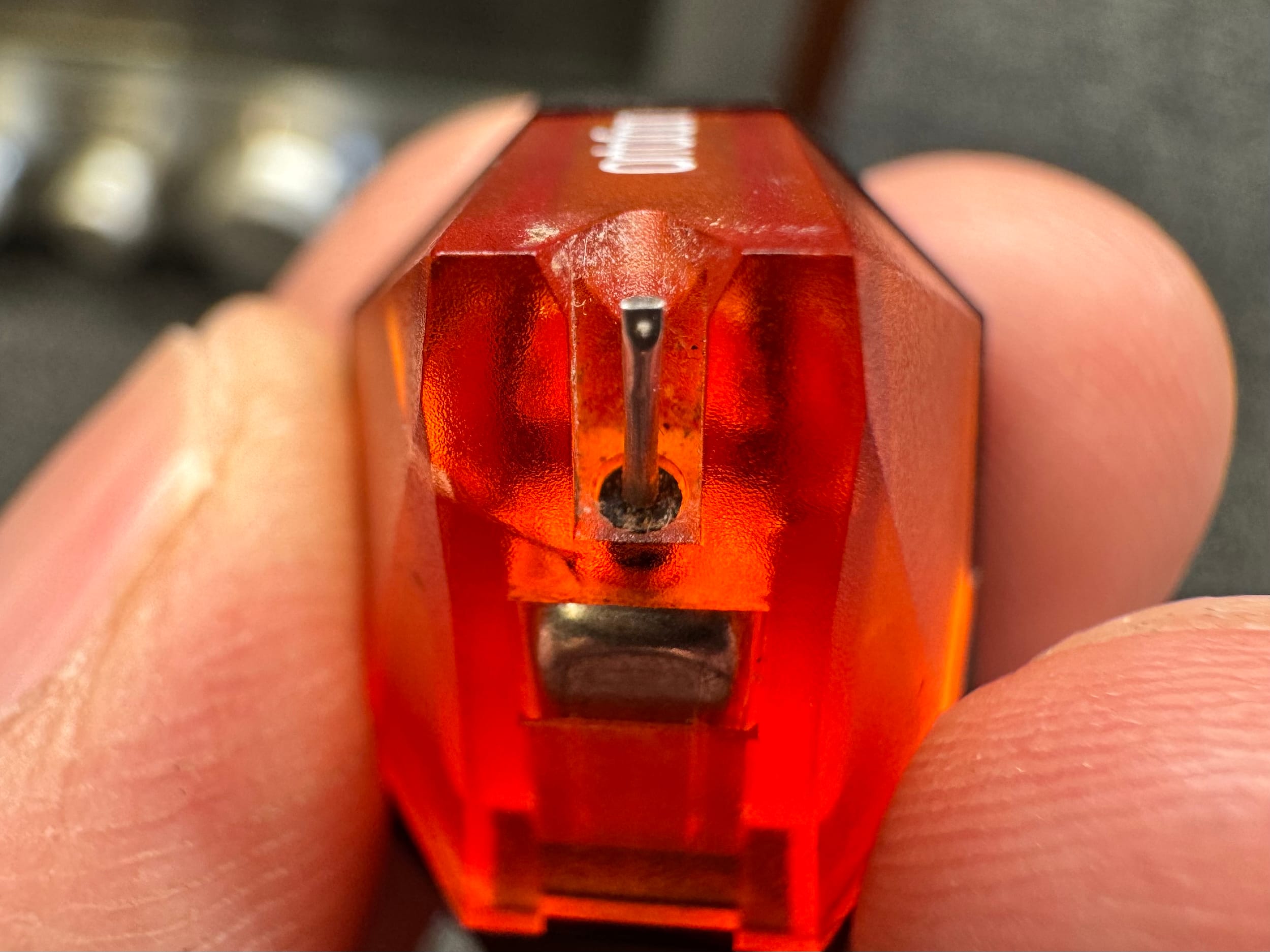
Update
The gentleman who sold the cartridge above with “Only 20 hours” of use has been banned from StereoNet Australia for not offering a full refund as instructed by their review team. Well done to the team for enforcing ethical behaviour and stomping on this.
The seller claimed the cartridge was sold to him in this condition. If true, this is also terrible, but it certainly doesn’t reduce his ethical responsibility. There is too much of this going on, unfortunately. We can always blame others, but ultimately we have to accept responsibility for things within our control. I’ll never understand why one wouldn’t immediately issue a refund in a case like this, but to me it indicates guilt.
Lessons
There is one very obvious lesson here: Don’t do this! Legitimate sellers will of course list cartridges with “only 50 hours” and various other low-hours numbers and many of these will be legit. Just know that near-new cartridges look near-new and one should be extremely wary of very low-hours claims.
Many cartridges that are damaged, with bent cantilevers, or with much higher than stated wear appear for sale on various platforms. Sellers often obscure details and many buyers lack the experience to know better. High-resolution inspection will, of course, tell the story though. We offer this service, as do others. Be careful and ask lots of questions, especially with much higher-priced “50-hour” carts.
My advice is to avoid trying to save a couple of hundred bucks on what is already a low-priced cartridge and just buy a new one. Oftentimes, trying to save a small amount of money ends up costing much more and that’s exactly what happened here.
Considerations for non-local customers
Here are a few important considerations for non-local customers.
- Packing, shipping and insurance costs should be determined by a shipping company such as our shipping partner Pack & Send. We do not offer packing or shipping services and are unable to provide quotes for such services.
- Cut-price packing/shipping services such as Sendle, Aus Post, Couriers Please, Startrack, Fastway (Aramex) etc are often associated with slow delivery times and equipment damage and or loss and should be avoided.
- Equipment should be double-boxed, with strong corner, side, top and bottom protection. Heavy amplifiers and other sensitive equipment like valuable turntables should be palletised.
- Insurance against total loss is critical and should be utilised in most instances.
- Packing/unpacking and transporting equipment necessarily incur additional handling time and therefore cost. This must be factored in when sending equipment to us for work.
- Deliveries to and collections from Liquid Audio should occur within our business hours.
- Customers are responsible for all shipping costs to and from Liquid Audio.
Mike, what’s the silliest thing anyone has said to you?
I was a science teacher for 15 years and worked at a university, so I’ve heard plenty of silly things.
If we restrict the silliest things to those related to running Liquid Audio, though, the silliest thing anyone ever said to me has to be when a customer accused me of stealing his old capacitors.
I replaced 40-year-old capacitors in a preamp for a gentleman I’d helped enormously regarding other issues he’d had with other repairers. I missed the red flags there, I’ll admit that! This individual failed to realise several points:
- 40-year-old dead electrolytic capacitors have no value
- BRAND NEW electrolytic capacitors have little value
- I own/stock thousands of premium new and NOS capacitors
- I don’t need or want old capacitors, all are disposed of
- There is no old capacitor black market
- Thieves steal more valuable items like catalytic converters, diamonds, hi-fi equipment…
What’s the deal with capacitors?
Capacitors are important, and I have thousands in my inventory. Let’s dig into why.
To answer this we perhaps need to look first at what they do and how they are made. Capacitors store charge, like little reservoirs. They also block the flow of direct current and therefore DC voltages. Some are made of aluminium foil and are polarized, some of metalised plastic, some of ceramic materials or tantalum.
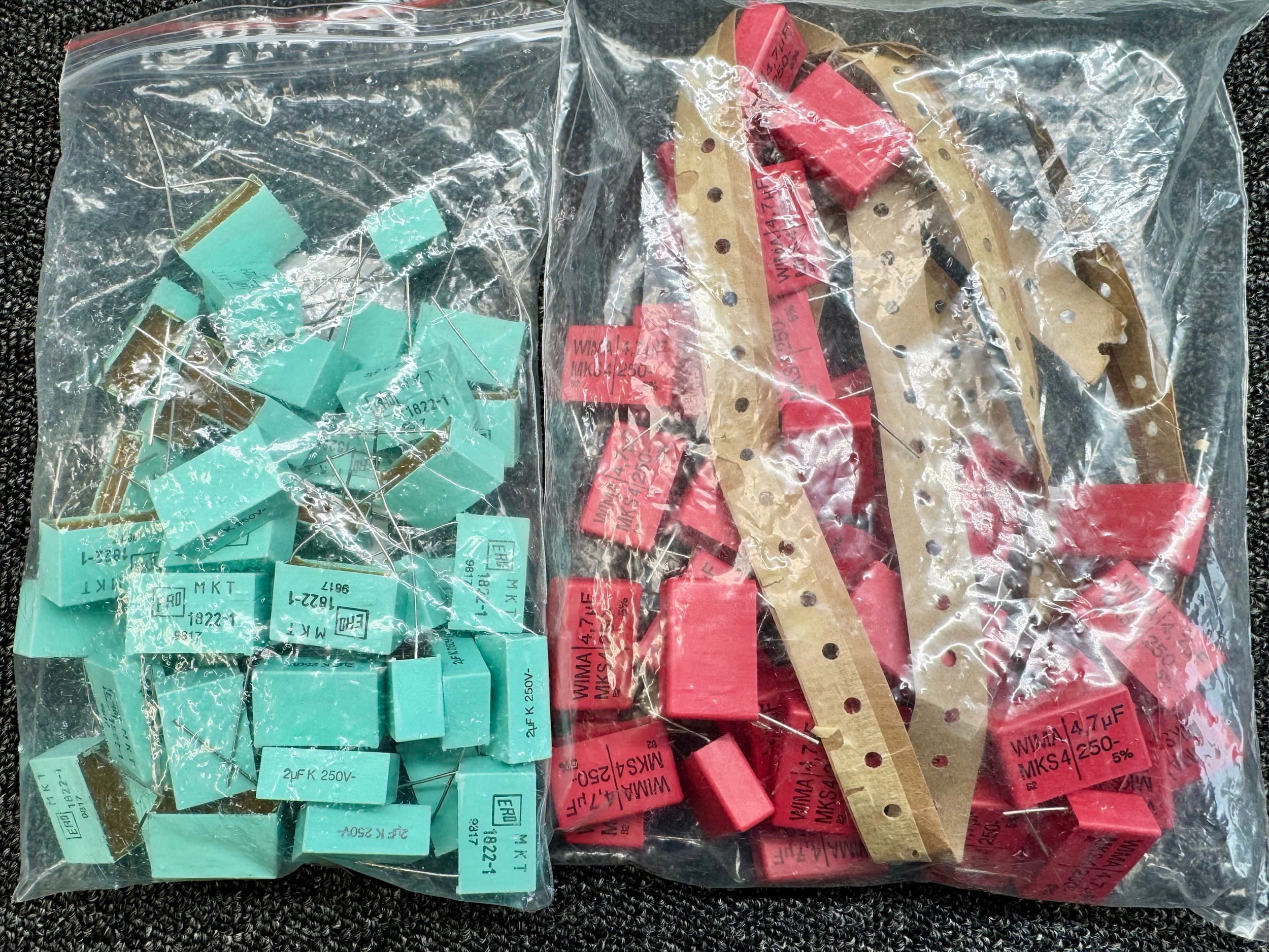
The Best Cap is No Cap
This is true where they can be avoided, and very often that isn’t possible. A good rule of thumb is that capacitors in the signal path are best avoided, but in certain scenarios they cannot, because they block DC, in tube amplifiers for example.
There are certain types of capacitors one would rather have in the signal path. Often, manufacturers use cheap aluminium electrolytic capacitors in this role, but polarised capacitors can never be symmetrical in their operation. This means they introduce distortion into AC signals – the signals we want to be able to hear.
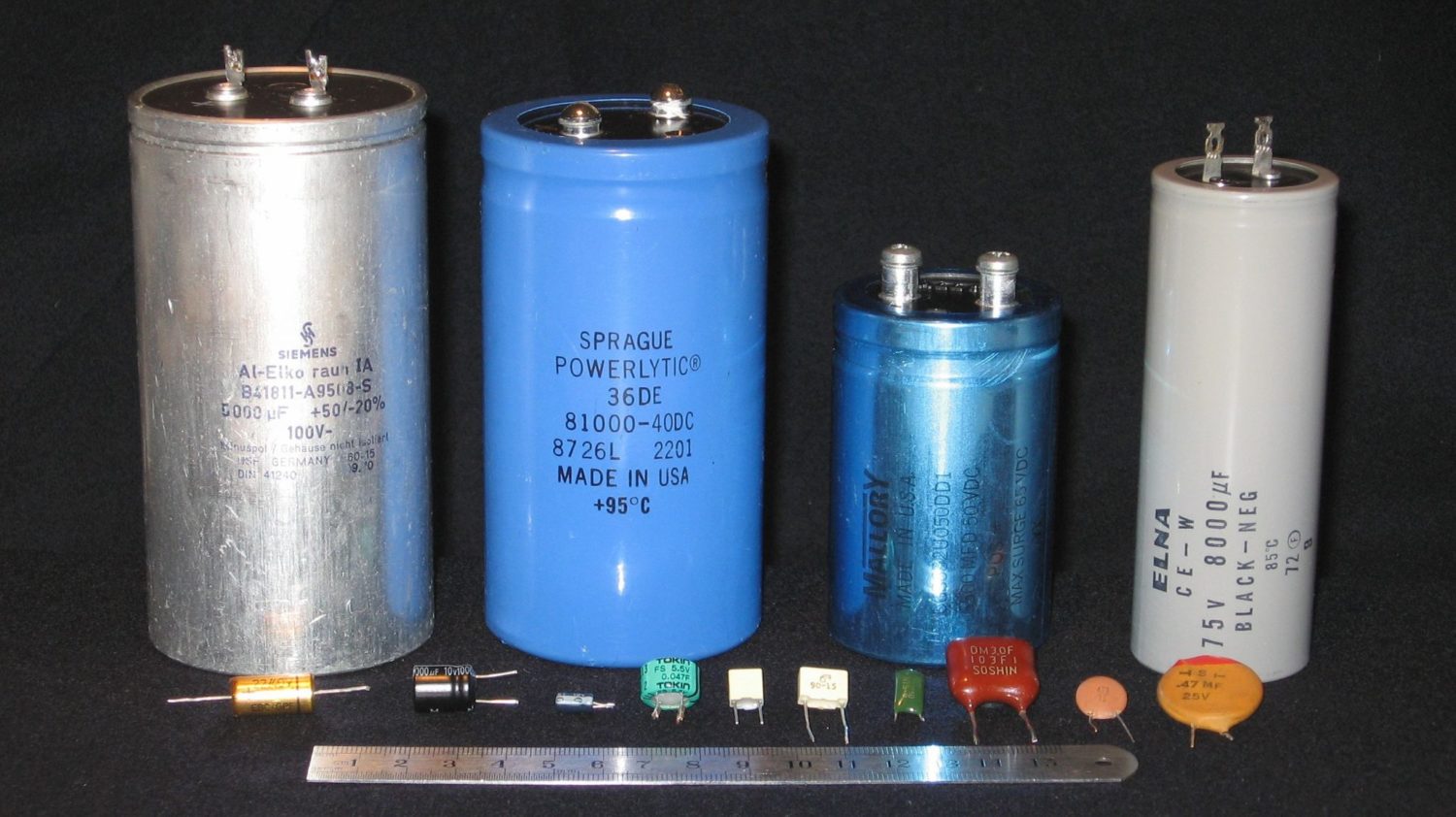
Signal Path
Signal path capacitors are best when they are metalised plastic or polyester, oil-filled or other non-polarised types. Still, these are more expensive and are often omitted for this reason. I often change out the aluminium electrolytic signal path capacitors for types that sound far better for my customers. They cost more, hundreds of times more sometimes, hence the reason they are often not used as original equipment from the factory.
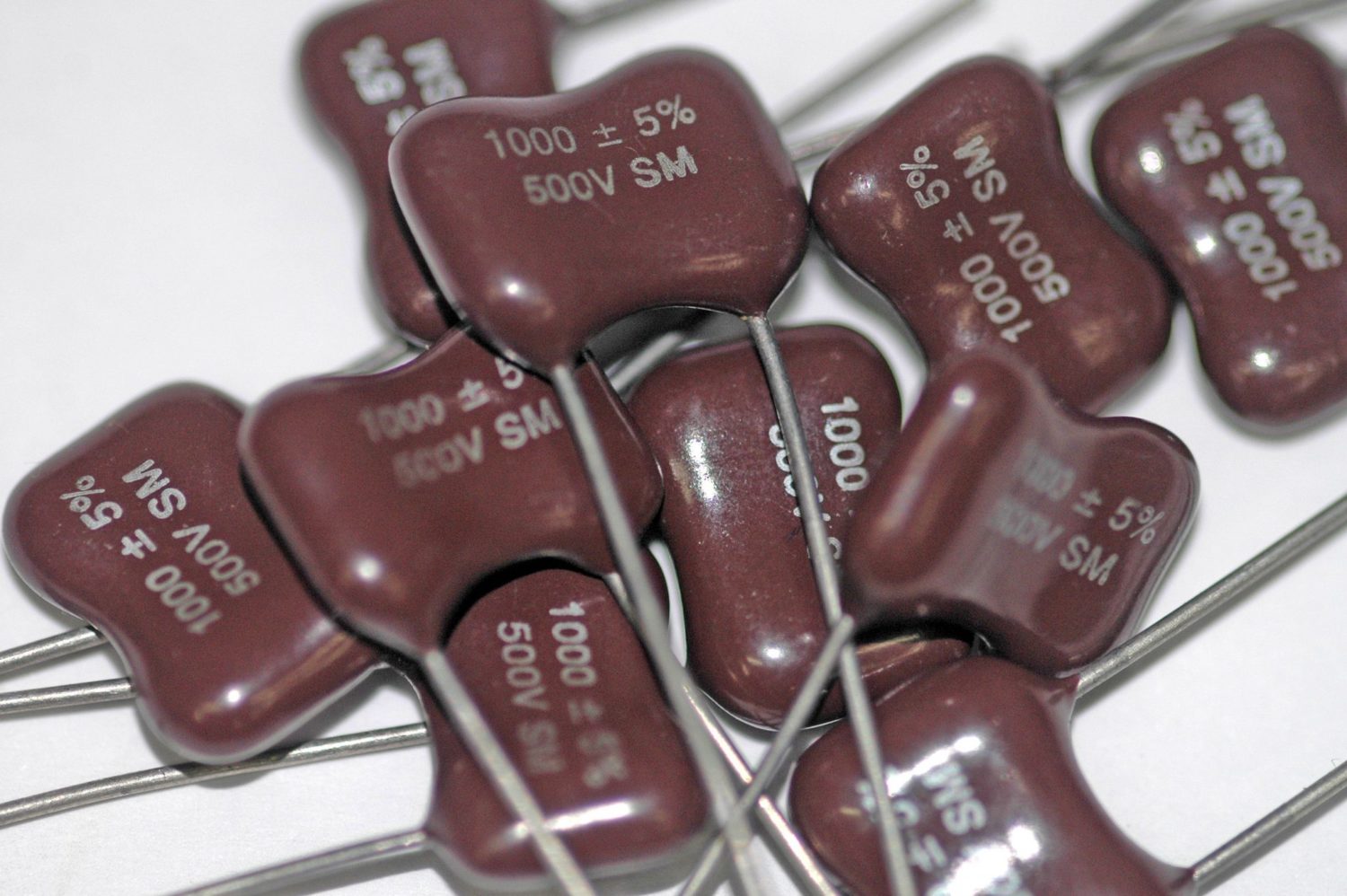
Because capacitors store charge, they are used in power supplies to smooth out the ripple in the rectified AC and remove the noise. Here we need high capacitance for a given size, and aluminium electrolytic types are perfect because of their very high capacitance-to-volume ratio.
The problem is again one of cost, though. Manufacturers need to save money, so they often use economy parts to boost margins, but in turn, this reduces reliability and longevity. Cheap parts are rated for shorter working life and lower operating temperatures.
They also have poorer electrical characteristics, such as higher equivalent series resistance or ESR. In effect, this wastes energy and reduces the performance of equipment that needs high power and low impedance supplies, like amplifiers.
Replacing Capacitors
This topic is more poorly understood than most, thanks largely to the internet, DIY forums, etc. Capacitors age, some more quickly than others. Aluminium electrolytic capacitors wear out fastest, their performance gradually degrades over time, resulting in increased ESR, increased leakage and decreased C. The key is to understand this aging process, what influences it and how to measure the life remaining in capacitors.
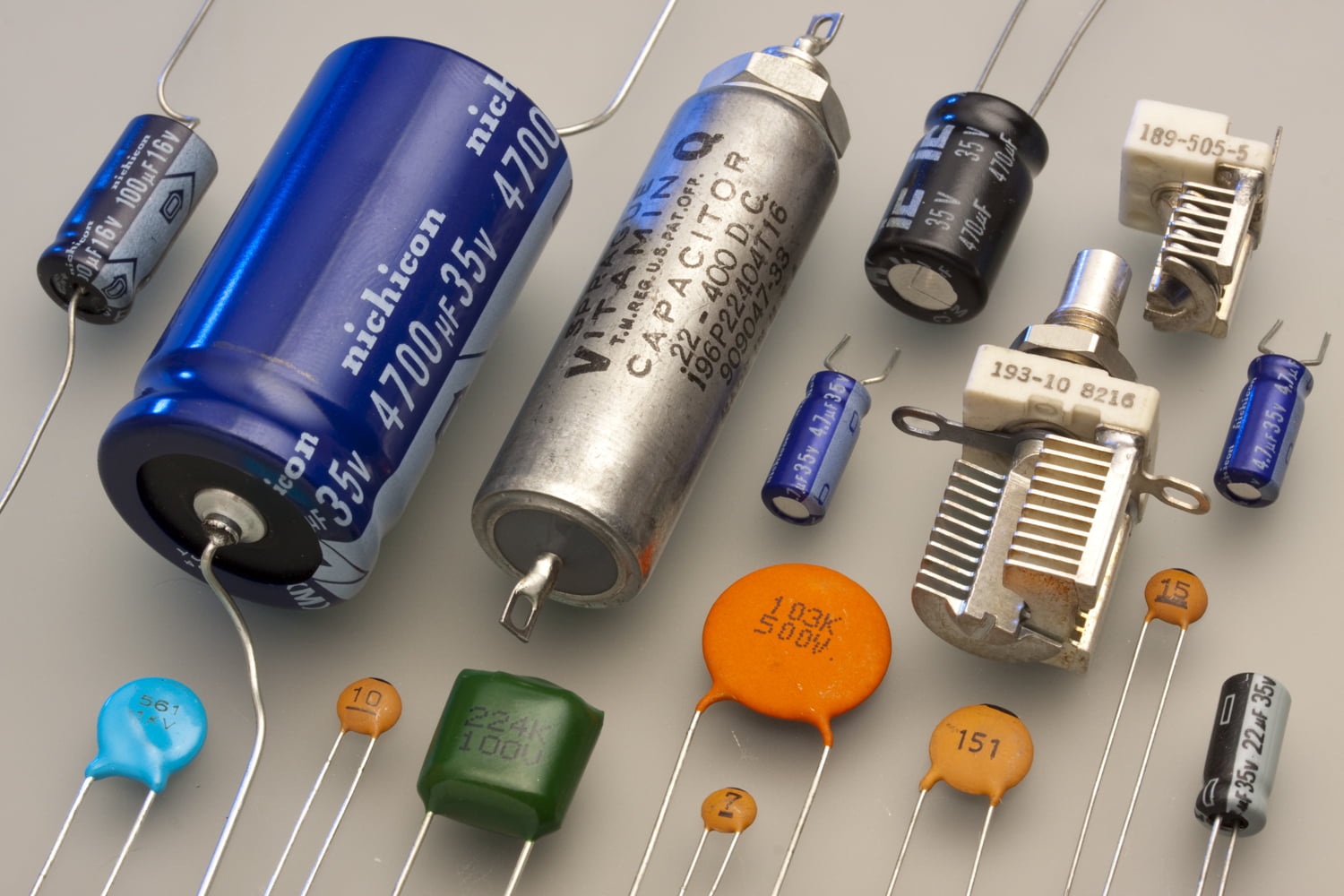
This reduced performance over time is due to the gradual increase in internal resistance inside the capacitor, usually due to a gradual deterioration of the electrolyte. This is all bad, but all easily fixed. Good electrolytic power supply caps can cost $10 – $100 EACH, depending on size.
Here’s an example, with a DAC that has to sell for say $1500. The dealer pays $1000 for it, the distributor pays $500 for it, and so it could only cost the manufacturer a maximum of around $100 to build. You can’t possibly have several hundred dollars worth of capacitors in the power supply when the WHOLE DAC has to cost no more than $100 to manufacture. See how this works? See how a $1500 DAC is essentially nothing?
Herein lies the great conundrum – designers would of course rather use the best parts. If they did, the DAC that should sell for $1500 would have to sell for $5000, and this is not an option. Instead, the manufacturer’s marketing and production droobs will trim each part down to the most basic spec that will get the job done.
In terms of how all this applies to hi-fi gear, we can replace old capacitors that wear out, and use better quality parts at the same time, where necessary or beneficial, and kill at least two birds with one stone.
Decoupling
Finally, we need to consider decoupling, which is where small-value solid capacitors are often used to reduce high-frequency noise. Again, better capacitors sound and perform better. I often use military parts bought in surplus, in large quantities. These military caps are fantastic because they are not made for the ‘audiophile’ market, and so there is no marketing bullshit involved.
What you DO get with mil-spec parts is parts that are the best performers, and have the best lifespan. Remember – these parts are made to operate under military conditions of extreme heat, vibration, and humidity. Knowing this, you can probably see why these parts are best and why I use them where I can.
To summarise, capacitors have a huge impact on the sonic performance of audio gear and the measured technical performance as well. Almost any piece of equipment – even brand new – will benefit from carefully considering the capacitors installed and alternative replacements.
Can you include more technical details of your work?
I try to provide a balance of general and technical details in my articles.
Most people want broad brush strokes, including some history and ‘how does it sound?’ type stuff. Competitors love it when I include all the technical details and proprietary stuff, though. For this reason, I give a little bit of everything, without too much of anything. Keep in mind that most professional repairers don’t even write articles. I provide a ton of detail that cannot be found anywhere else.
Why do you run a business from home?
Like many new, specialist small businesses, I don’t need a store or retail presence, so operating from home makes a lot of sense.
We don’t offer retail sales or deal with drop-in enquiries from the general public, so I don’t need the added cost of a retail shopfront. Working from home suits me and my customers well, for many reasons.
Does being a musician help with the work you do?
Very much so!
Knowing what real instruments sound like in a live music environment is both unusual and incredibly helpful when appraising hi-fi equipment and systems. Unlike many, I know what real drums, guitars, basses, keyboards and other instruments do sound like, and should sound like. I still have my drum kit.
On the flip side, being a musician and having played the drums and attended so many live music events, my ears have suffered over the years and I am paying the price for it now, despite having used hearing protection for decades. Strangely and despite having damaged my hearing, I’m somehow still able to make very subtle observations about sound and sonic differences between hi-fi gear. Go figure. There will be a scientific explanation for this, but I don’t know what it is.
Do CD transports sound different from one another?
Another great question and yes, they do, significantly so in a high-resolution system.
This CD transport ‘thing’ is one of the more puzzling hi-fi truths and paths to improving your Redbook CD playback. Long story short, transports sound different, dramatically so in some cases. I have even been surprised by this in a case I describe below, so if you want to hear more about that, read on!
What is a Transport?
First, let’s clarify what the term ‘CD transport’ means. A CD transport is a CD player that outputs a digital signal rather than an analogue one. It is therefore designed for use with a DAC and is the least integrated and therefore potentially the best-performing CD-playing solution.
A regular CD player can also be used as a transport where it outputs a digital signal and can be used with a DAC. Either way, when we use the term transport, we are referring to a player used to extract a digital signal from a Redbook CD, which can then feed an external DAC.
Ones and Zeros
You’d think that CD players and transports, outputting digital bitstreams as they do, would all sound much the same, given that they read the same data off the disc and extract the same data. They should, and I use that term carefully, generate the same bitstream, in theory. They don’t though and for various reasons, all transports sound a bit different, reading the same data, from the same disc. Curious.
For those wondering why they all sound a bit different, I think it comes down to differences in error correction, timing accuracy and a related aspect of that, jitter. There are some obvious contributors to this in the form of build quality, laser quality, health and precision of adjustment, power supply isolation, and so on. These factors generally correlate with cost, so it’s perhaps no surprise what I discovered recently.
I’ve always known that CD transports sound different from one another, even if the reasons why are less obvious than they are with turntables for example. But, these sonic differences between CD transports have never been more apparent to me than when I changed my transport from my beloved Sony CDP-X7ESD to my recently acquired Accuphase DP-90.
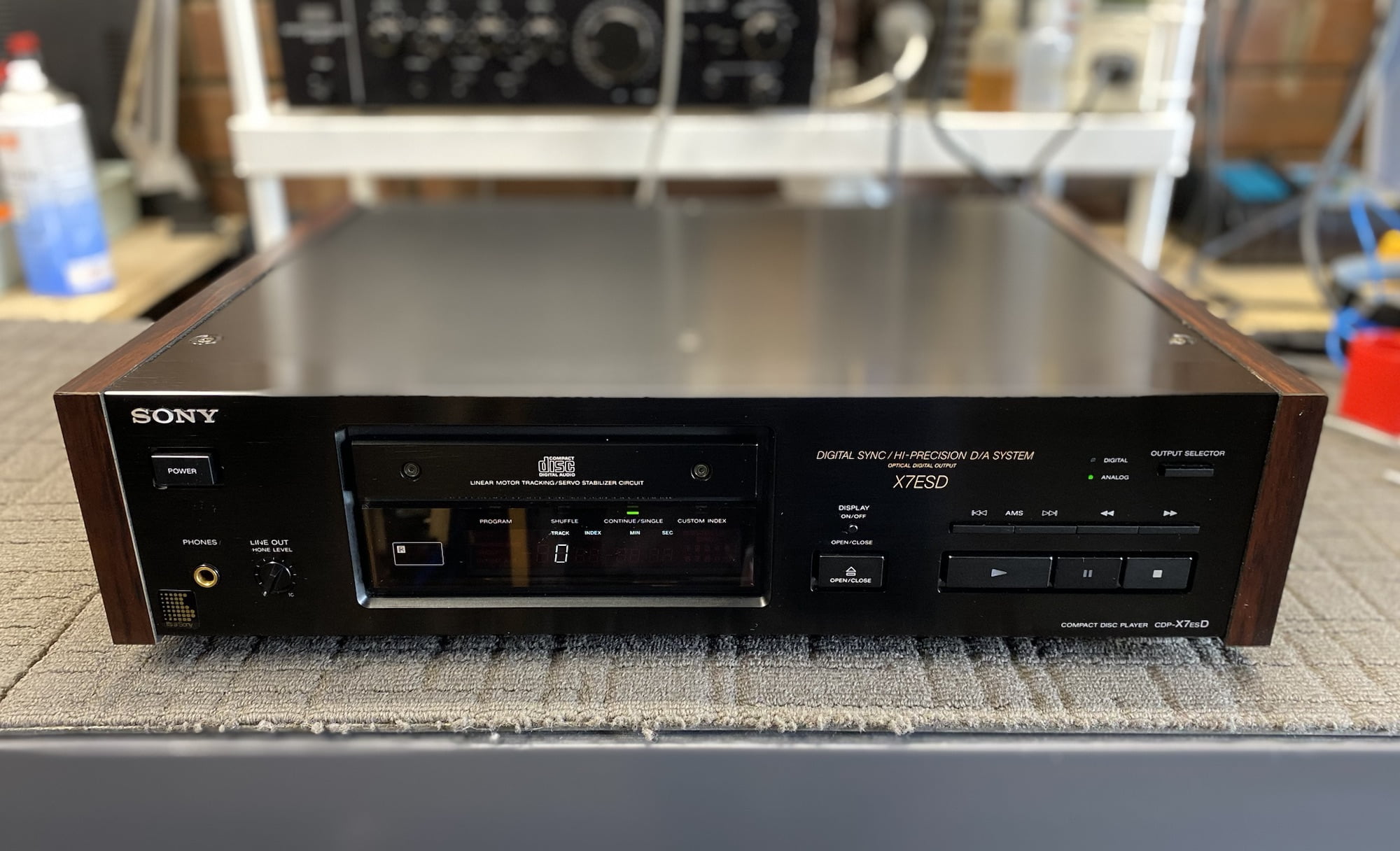
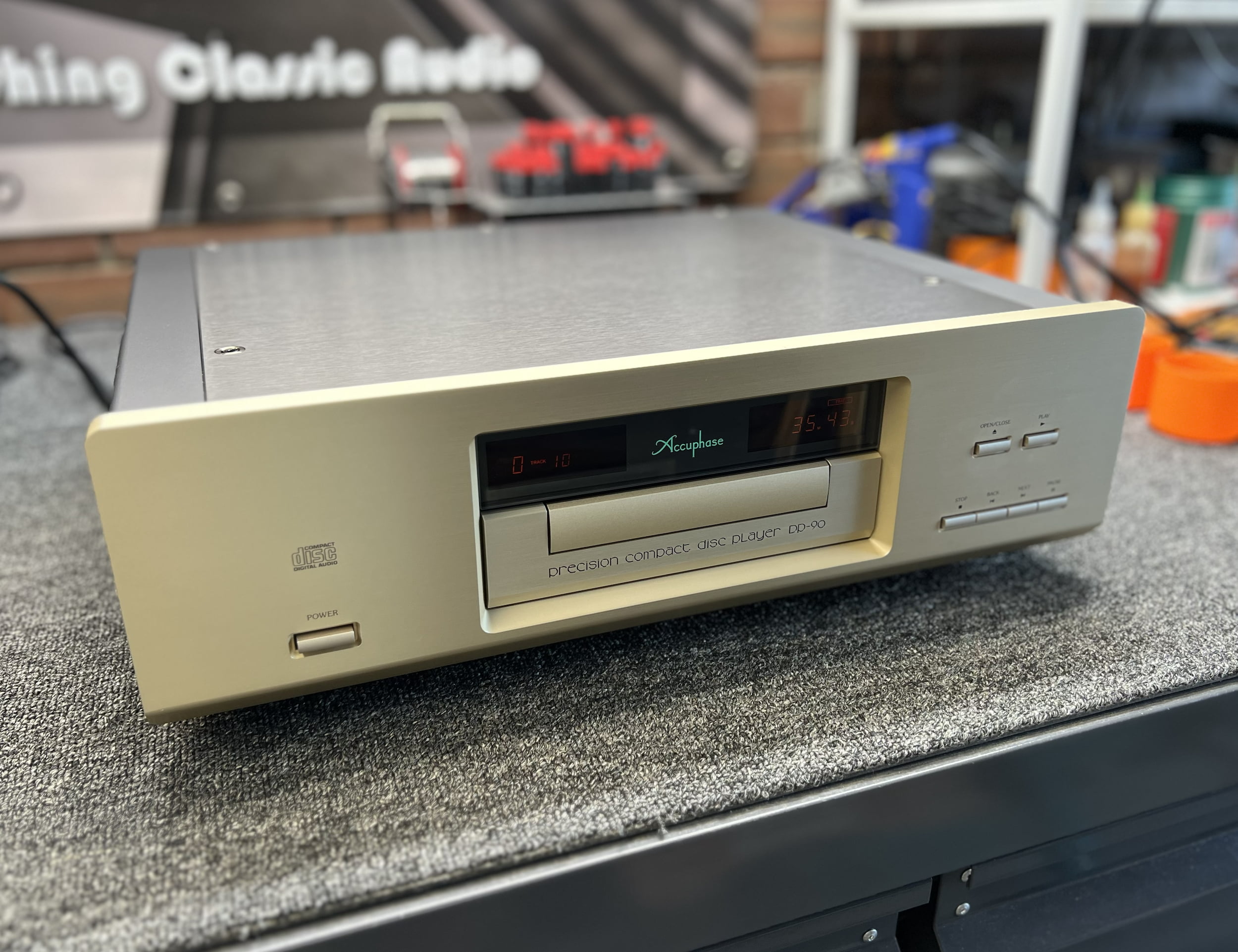
The differences between these two transports in terms of the sound output by my DAC are night and day. The Sony is a great-sounding super-smooth operating transport in its own right. It’s also perhaps even nicer in terms of the loader action and smoothness than the much more expensive Accuphase, but there’s not much in it. In terms of sound though, the Accuphase DP-90 takes everything to 11.
With the DP-90 feeding my DAC, the bass is massively extended, mids are more real and everything is better fleshed out and resolved in a way that’s obvious when not even in the listening room. As soon as I hit play I was stunned, and I was prepared for the worst after importing this baby from Japan.
I was hoping for improvements, not necessarily expecting anything major, but from the first track of the first disc, my best possible hopes were confirmed by a night and day improvement over an already outstanding transport. Who knew?! Perhaps I should have, but not many people get to use, let alone own gear like this, so cut me some slack on this one! None of my hi-fi friends and colleagues have a transport this good.
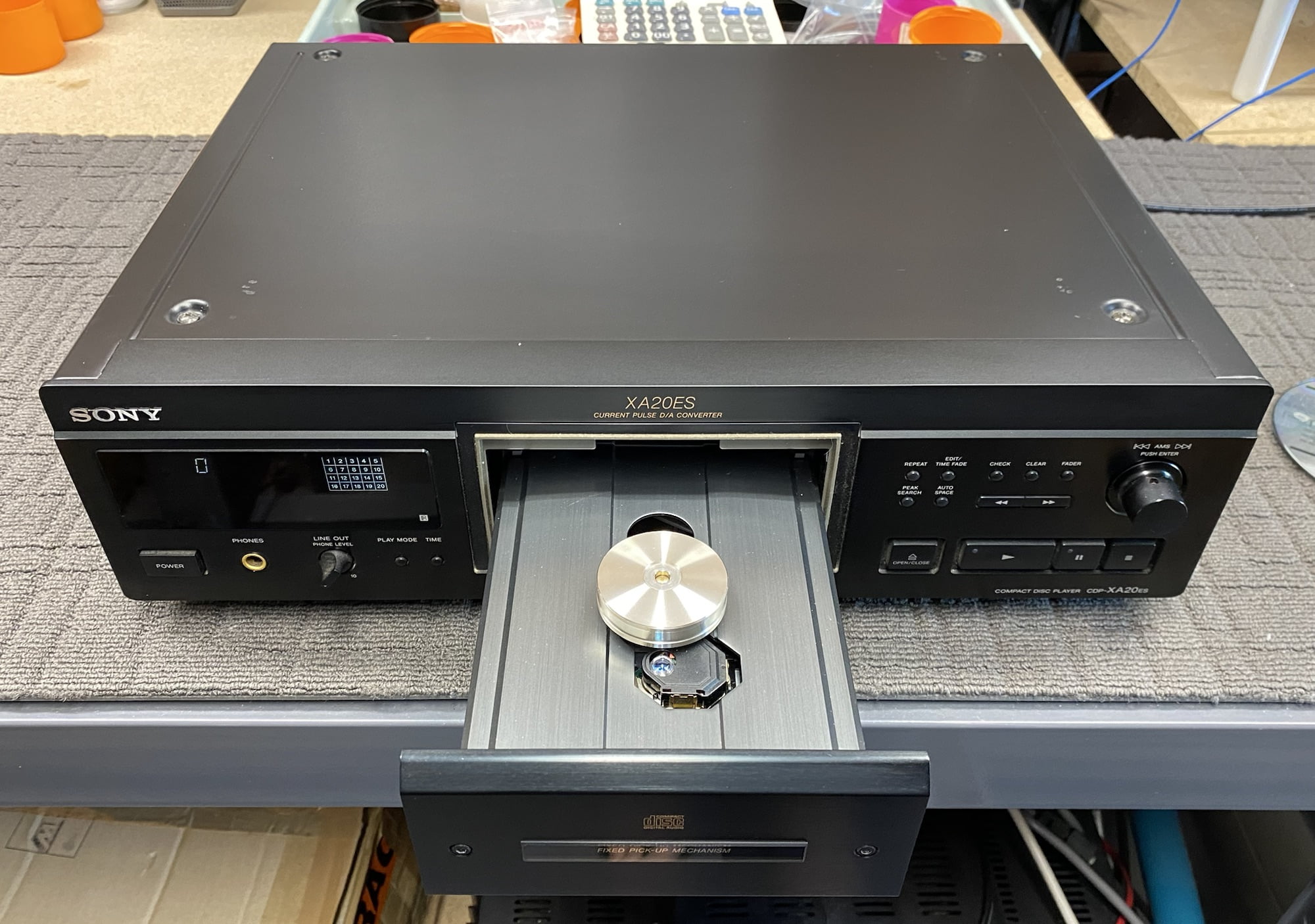
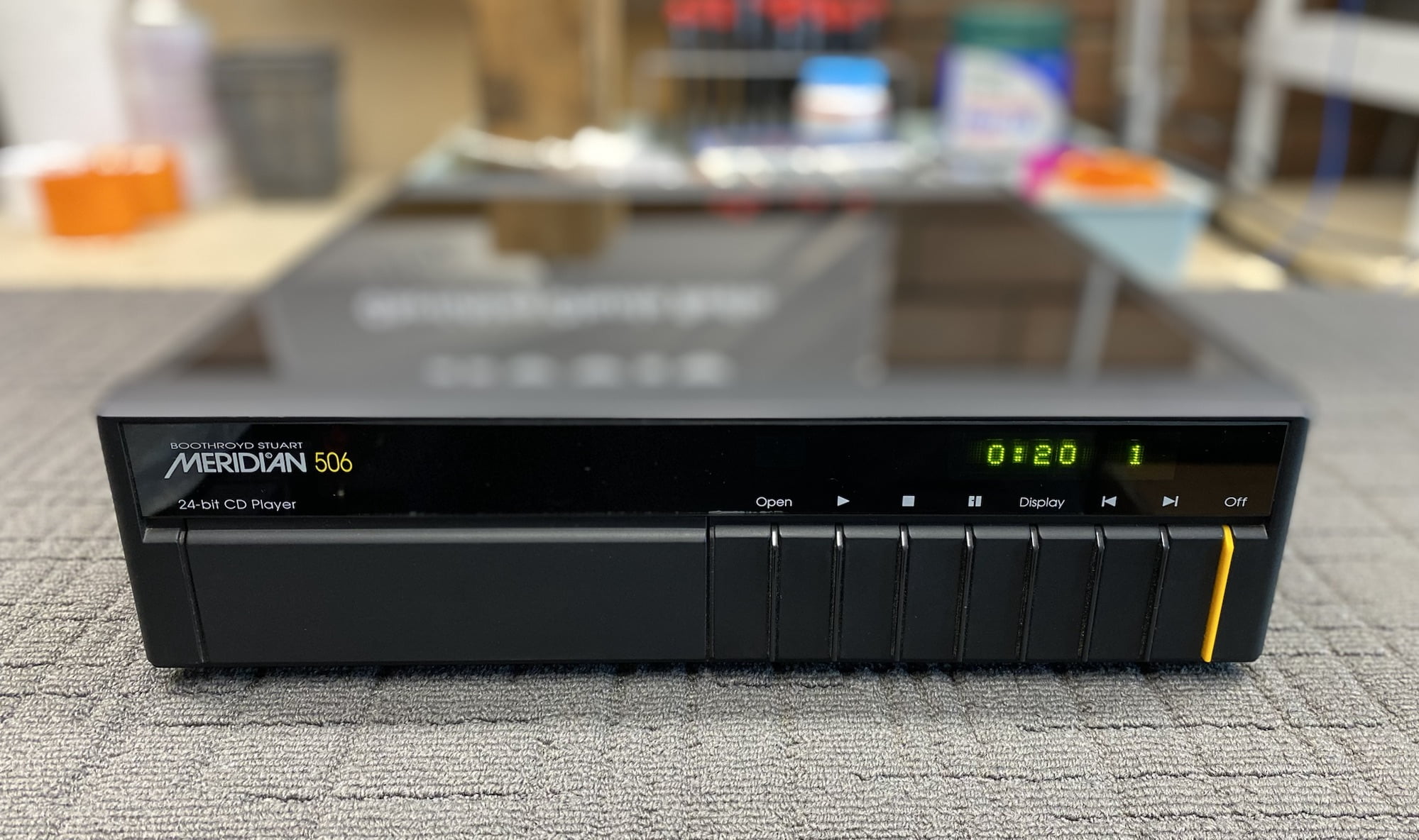
Bottom Line
Forget what you think you know in terms of CD transports and just know that transports sound different. These differences are more subtle at the lower end of the spectrum but paradoxically become more pronounced as you go up the food chain. I suggest that if you love Redbook CD despite its limitations as I do, you get yourself a really good transport, the best you can afford.
A great transport will be made by one of the great manufacturers, built like a tank and might even be quite old by modern standards. It will likely contain a classic Philips or Sony mech, or maybe a Sanyo in the case of some of the classic Krell CD players. Most importantly, a great CD transport will transform your playback of CDs, in a high-resolution system of course.
Again, I have nothing to sell you, no secret stash of Accuphase DP-90s, though I wish I did! Enjoy the journey.
Try these FAQs for more about CD players:
Read many other articles I’ve written about CD players and DACs:
Why do you have these FAQs?
The FAQs save everyone time, by addressing questions I’m most commonly asked.
Honestly, there are questions I’ve probably been asked hundreds of times now over the last 10+ years. Answering commonly asked questions like these takes a chunk of time and, without a good alternative, I’d almost never get any work done!
I write each FAQ and its answer based on something I’ve been asked recently, or previously. Writing carefully worded responses allows me to give you precisely the right information, in a way that saves your time and mine ultimately.
Yes, I invest a lot of my own time creating these often very detailed FAQs, but they generate a lot of goodwill too, so everyone wins!
I’ve read that I should replace any capacitors measuring 10% under spec – is this correct?
No, but this is typical of comments people find online.
NOTE: DIY electronic equipment repair attempts generally significantly increase the risk of damage, introduction of additional faults and electrocution. Stay safe and if in doubt, take your equipment to a professional.
Dunning-Kruger
The Dunning-Kruger effect is where people significantly overrate their knowledge of topics they’ve learned little about, and usually from a variety of untrustworthy sources. Public forums are a breeding ground for this and many come unstuck by relying on them.
One cannot expect to know much about anything, let alone a complex technical topic, after just a few hours of reading. Again, if in doubt, seek a professional, and note that professionals doing commercial work don’t hang out in public forums!
Example
Capacitors are one of many poorly understood topics in electronics, with ‘recapping’ being right up there. A reader’s comment on an article I wrote about the wonderful Kenwood KD-500 turntable prompted me to write this FAQ. Let’s examine this and then break it down a little:
A simple fix can be changing any electrolytic caps.. Always good to remove then and check there [sic] capacitance. 10% below should be changed.
Mark
Breakdown
Mark’s statement is incorrect. Not only will not help the original commenter fix his turntable, it will most likely lead to the owner damaging and devaluing his turntable, and it will still have speed issues after all that. I understand the causes of the speed issues with these turntables and they are not capacitor-related.
I replied as follows:
Thanks for your comment, Mark. I appreciate trying to assist others, but given that your comment highlights general misinformation regarding technical electronics repair and only encourages capacitor replacement rather than finding and fixing the issues, it’s helpful if I explain why.
Capacitors are much maligned and poorly understood. Capacitors should be checked, but rarely cause speed issues with these decks. New caps are typically specified to be within +/- 20% of rated capacitance, like these excellent Panasonic parts: https://industrial.panasonic.com/cdbs/www-data/pdf/RDF0000/ABA0000C1209.pdf.
A reading within +/- 20% is within new part specs and measurement error. Replacing capacitors that measure within 10% of spec is not only a waste of time and money, but it will not fix anything unless those parts also have a measurably very high ESR.
Most end-users also don’t have the test equipment needed to make these measurements accurately, nor the experience to interpret the results and therefore should not remove or change parts they cannot properly measure and assess.
Liquid Mike
Did You Know?
Did you know that brand-new capacitors typically measure low for C and high for ESR? There’s nothing wrong with them, they need to reform, the process that happens when they are first charged. According to the commenter’s theory, even brand-new capacitors that have sat for a while should be thrown away. This is, of course, incorrect.
Capacitors can fail and must be replaced when they do. They can also be replaced to significantly improve performance, depending on their role in a circuit. However, a 10% variance from rated spec does not constitute failure and may be within the measurement error of the typically ordinary test gear most owners will have access to.
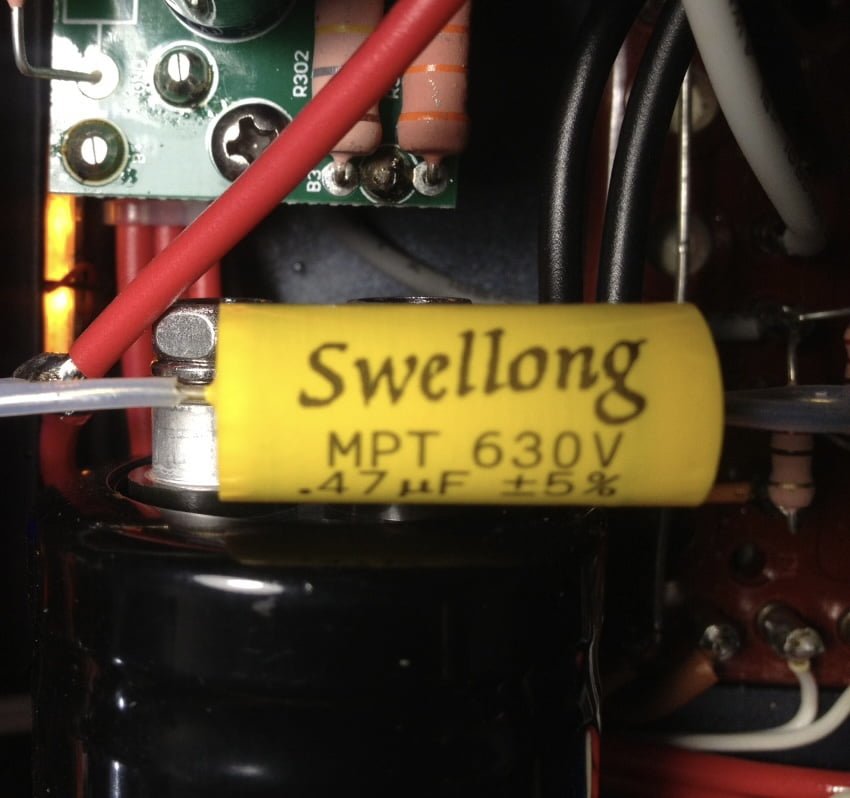
TLDR
All too often, people bin perfectly good parts and replace them with inferior parts, trying to solve problems that are not even caused by those parts. ESR is a more important parameter than C in terms of capacitor health. Proper lab-grade test and measurement equipment is needed to properly test capacitor parameters, equipment most people do not own.
Replacing parts can cause circuit board damage and introduce new faults. This is especially for those working with cheap soldering and re-work tools, ie people who probably shouldn’t be doing the work. Again, glancing through the Hall of Shame provides ample evidence of this flawed approach.
How much will my service or repair cost?
Only as much as necessary to carefully complete the work you’ve asked us to do, and no more.
Liquid Audio proudly delivers class-leading service, results and value. We’re honoured to have the hi-fi community’s trust, and we hope to assist you too!
Pricing
Our sensible pricing and approach mean we cater for a wide range of customers and equipment.
Job Type | Rate |
Small jobs to 30 minutes | $95- |
Standard technical work | $150/hr |
Consultation | $150/hr |
- Our $95 per-piece economy rate applies to work up to 30 minutes duration.
- Standard work falling within a 3-hour (or 4-hour for complex pieces) window generally proceeds automatically.
- We never require any upfront payment, all work is payable upon completion.
- Country, interstate and overseas customers should view these additional considerations.
- All work is billable, regardless of type or outcome. View our terms of service for details.
Quality
Liquid Audio is widely respected for excellence, professionalism, service, value-for-money and extensive contributions to the hi-fi community. Those looking for a ‘cut-price, cut-corners’ approach won’t find it here, though many such businesses exist, over-promising and under-delivering via predictably poor workmanship and results, ‘Swellong’ capacitors, devalued or destroyed equipment and court cases. Reviews, anti-customer rants, business name changes and court records tell these stories. Research is vital.
Mike … you, of course, are a gem. We are so lucky to have someone as passionate, intelligent, ethical and hardworking in little ol’ Perth.
David H
We take caring for our customers and their hi-fi equipment seriously. We charge only what is required to do a job carefully and to the highest standards. This adds value to cherished equipment, delivers the best results, and costs less in the long run. If this approach resonates with you, don’t hesitate to get in touch.
More
Check out these related FAQs:
Do you listen to every piece of equipment?
Of course!
When you run a business like mine, the reputation I’ve built based on care and attention to detail is no accident. Listening to every piece is an essential part of quality control and whilst some don’t, I do.
What are system resolution limitations and why are they important?
System resolution limitations or ‘bottlenecks’ are critically important as they define the maximum performance attainable with a given set of equipment.
This is actually the most critical thing to understand about any system. Think of it this way: You can have the best pair of speakers and the most amazing source equipment in the world, but if your amplifier can only support a certain level of performance, maybe it has a cloudy or opaque sound, limited power, limited bass performance or a shouty, edgy character, you will never be able to hear beyond that limit.
Everything you play will be defined and limited by the weakest link in your system. That’s why system optimisation as a whole is so vitally important. It’s also why this topic is one of the most requested for discussion by those utilising our advisory service.
Dirty Windows
Another way to think of this is using the classic ‘dirty window’ scenario. Imagine the sharpest, most detailed image in the world being held just behind a slightly dirty pane of glass. It doesn’t matter how good that image is technically, because you will only even be able to see the amount of detail limited by that dirty window and what can be observed through it. The only solutions are to clean the glass, replace it or remove it altogether.
This can manifest in different ways for hi-fi systems. For example, sometimes people upgrade elements of their system but don’t hear much of an improvement or cannot get the most out of the improved equipment. This is because of existing system resolution bottlenecks. The only way to substantially improve the system is to remove the bottleneck, or resolution limitation. This is why getting excellent advice about systems as a whole is so important.
An opposite example I can offer direct experience with related to my Yamaha NS-1000M speakers and my recently acquired Accuphase A-75 class A power amplifier. I heard an amazing improvement with this incredible new amplifier, because I have amazing source equipment, and because of those incredibly revealing and resloving Yamaha speakers. This is a finely tuned and well-integrated system as you might expect, where elements are very well balanced to allow each to perform to their best.
Examples
Examples of system resolution limits and being surprised the results aren’t better include:
- Fitting really good cartridges to average turntables
- Using high-end MC cartridges with cheap phono preamps
- Connecting high-quality sources to low-resolution amplifiers/speakers
- Connecting high-quality balanced equipment through single-ended connections
- Using an amplifier that is much better than a pair of speakers, or vice-versa
- Using any high-end gear in an untreated or poorly treated listening room
Know Your Limits
The key to removing system resolution limits like these is to identify that they exist, understand precisely where they are, and then devise a plan to mitigate them. Naturally, we can help with this.
You might be thinking: “Mike, this is obvious!” Great, but as obvious as this concept might seem to you, I promise that most people are not good at auditing their systems properly or identifying and eliminating system resolution limitations (you don’t know what you don’t know, etc).
My best advice is to seek advice from those who really understand this concept and avoid seeking advice from those with obvious conflicts of interest, including many folks selling new hi-fi equipment for example.
Can you contact me when you are accepting new bookings or put me in a queue?
Unfortunately no, though I promise I would if there was an easy way to manage a waitlist.
There are practical reasons why few businesses can do this, even those with multiple employees, but the simple explanation is this: The logistics of managing hundreds of people with enquiries and just one of me doing everything here, makes maintaining a waitlist of potential customers simply not viable.
The constant stream of local, interstate and even overseas enquiries, people buying and selling equipment and changing their minds about having it worked on, etc, means there’s no way to keep track of who wants to book what, and when. It’s neither practical nor sensible for me to try to keep track of all that, so I don’t.
The solution is our booking status table. It’s efficient because each enquirer need only check once in a while, and as guided by the table. It automatically filters out those who no longer require our services and saves me from sending hundreds of unnecessary emails.
I suggest people periodically check the booking status table based on the information provided in it. Feel free to send an enquiry even if we’re full because it gets the ball rolling.
What motorcycles have you owned?
A few of my customers ride motorcycles and this question always comes up, so here they are, in chronological order, with my rough year of ownership noted:
Bike | Model Year | Owned |
Motobecane 50cc moped | circa 1975? | circa 1984 |
Yamaha RZ250 water-cooled | 1985 | circa 1987 |
Yamaha RD250 air cooled | late ’70s | circa 1988 |
Yamaha RD400 air-cooled | late ’70s | circa 1988 |
Kawasaki KH400 | 1975 | circa 1989 |
Suzuki GSX1100ESD | 1983 | circa 1989 |
Suzuki GSX400 Four, London | 1981 | 1990 |
Suzuki GSX550EF, London | 1984 | 1991 |
Suzuki GSX1100EF | 1985 | 1992 – 1995 |
Suzuki Bandit 1200, purchased new, 1996 | 1996 | 1996 – 1997 |
Suzuki TL1000S (new) | 1997 | 1997 – 2001 |
Kawasaki GPZ750A1 | 1983 | 2001? |
Yamaha YZF1000R ThunderAce (new) | 2003 | 2004 – 2006 |
Kawasaki ZX12R (new) | 2005 | 2006 – 2009 |
BMW R1200R | 2009 | 2011 – 2018 |
Yamaha MT09 (new) | 2017 | 2018 – 2022 |
BMW R1250R (new) June 2023, damaged by Auto Classic in August, returned | 2022 | 2023 – 2023 |
Yamaha RD250 air-cooled | 2023 | 2023 – |
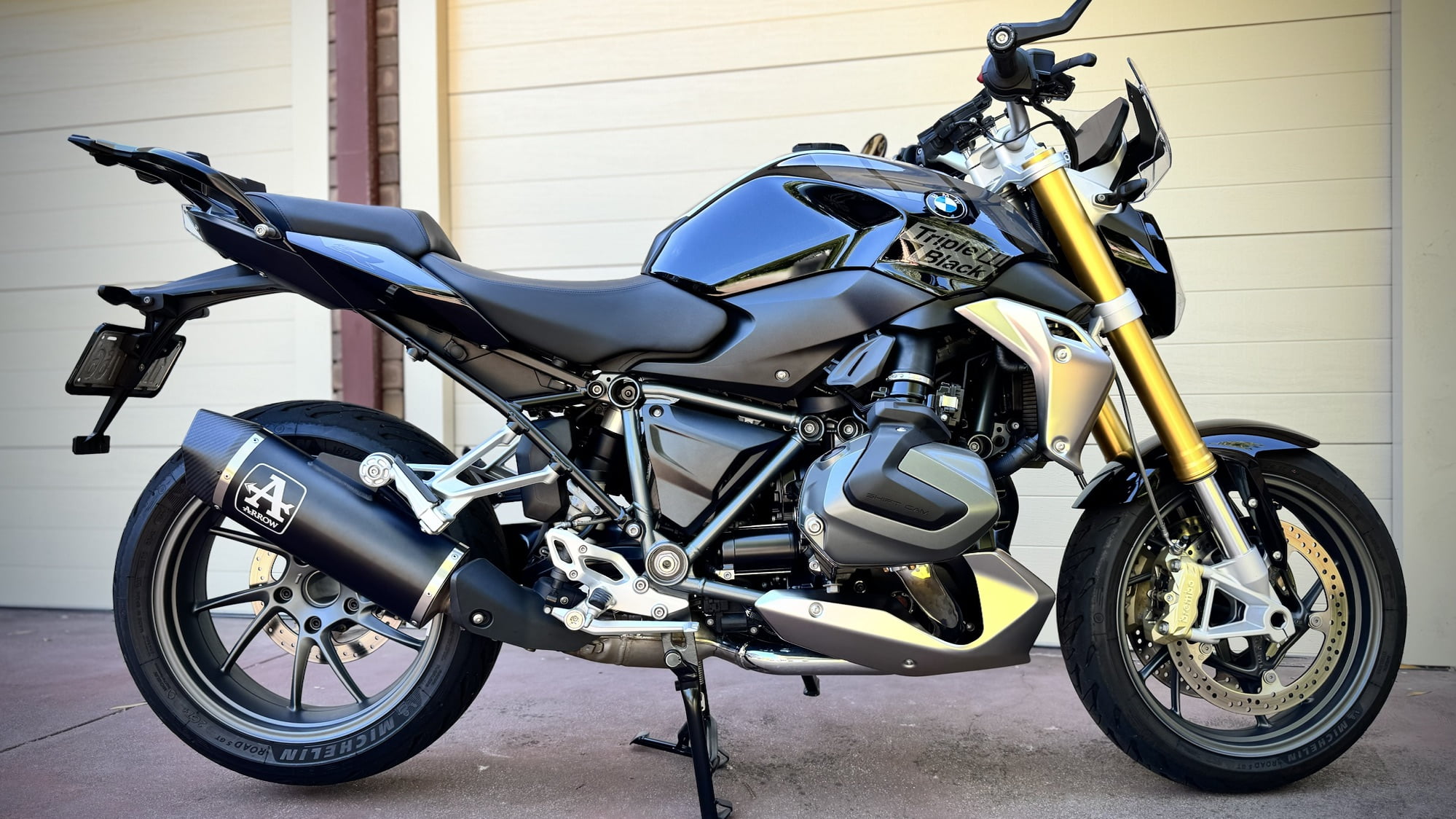
Why don’t you like working on equipment others have worked on?
It’s not all equipment, but in some cases, it will be compromised, damaged or even destroyed. It all depends on who’s worked on it; that’s the key.
In a nutshell, the picture below is why I often refuse equipment that has been worked on by the worst offenders:
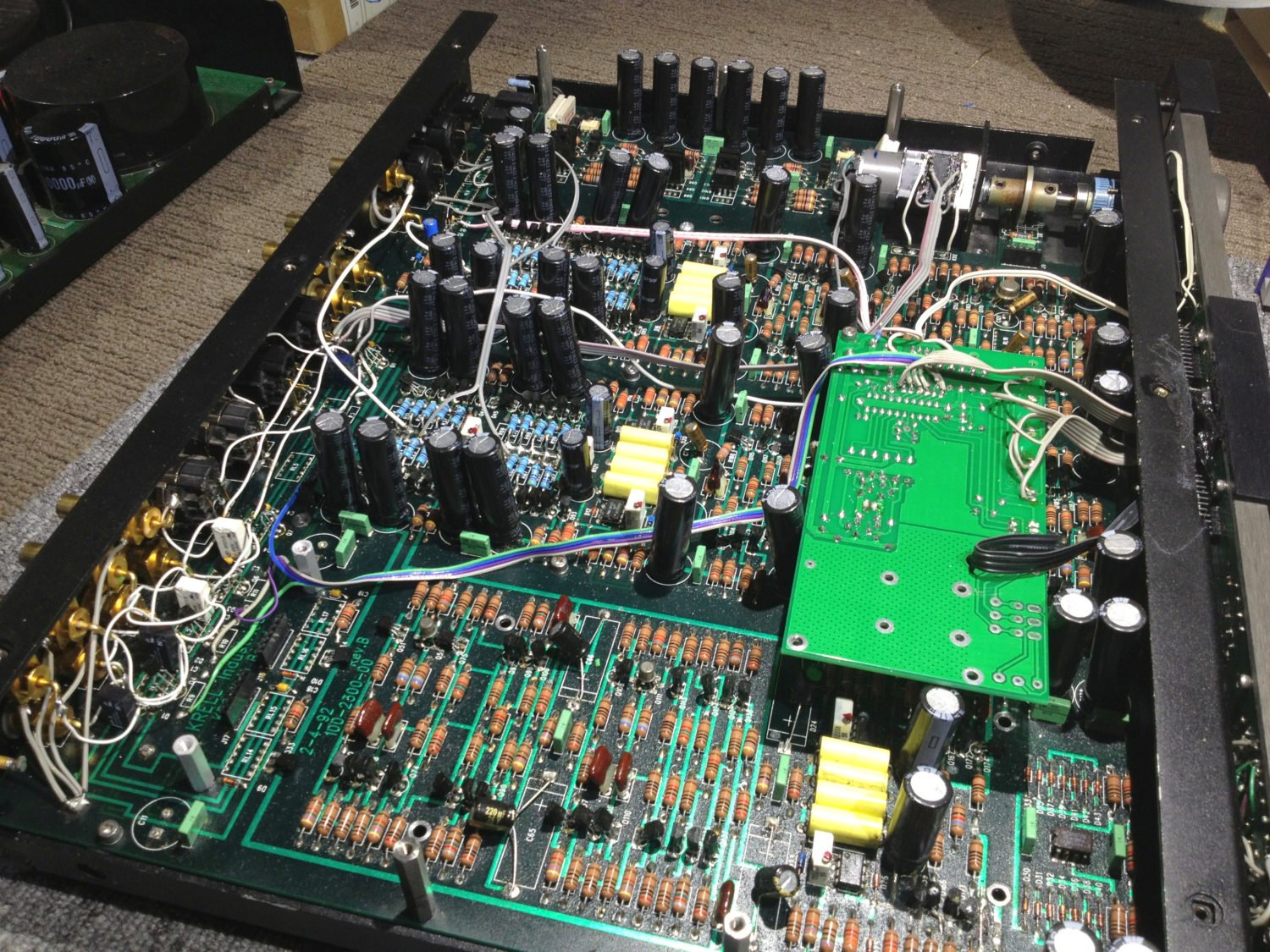
I don’t enjoy cleaning up mess left by others. The best hi-fi equipment is unmolested, perhaps dirty or even broken, but in original condition and ready for someone who understands how to care for it. I am happy to work on pieces that skilled technicians have worked on, but sadly, highly skilled professionals are few and far between.
Many DIY and commercial attempts at maintenance introduce faults such as damaged printed circuit boards and pads, compromised wiring and low-quality, incorrect or mismatched parts. This work not only does not resolve the original issues but these newly introduced problems can be terminal for the equipment.
Owners are then left with a mix of old and new faults and the need to find a skilled repairer who will take on such a case. Many won’t. A classic example of equipment I helped out my customer with was this Sansui AU-317.
There are industry parallels everywhere, by the way. Every mechanic, for example, knows the pain of working on a vehicle, only to find loose, broken, stripped or missing fasteners everywhere. The same scenarios occur with musical instruments like guitars and synths, poorly constructed buildings, etc. It is torture to work on anything bodged.
Undoing this stuff can be time-consuming, tedious and expensive, and when you’ve seen and tried to undo as much of this sort of thing as I have, you will understand why I generally avoid it.
Should I send my equipment overseas instead of to a reputable local repairer?
I hope the answer to this one is obvious.
A gentleman contacted me recently, annoyed that he couldn’t get his equipment in for immediate attention. He went on to tell me that he would no longer support local businesses and that he would instead send his equipment away for service. OK.
Nobody likes waiting, but waiting for a booking with a highly regarded, busy local specialist is almost always preferable to sending equipment overseas, to an unknown fate, with all the costs and risks that shipping entails.
Getting angry about local businesses being busy is one of the sillier attitudes I’ve come across in a long time, and I don’t mind saying so. Good repairers are busy for a reason and I would be worried if someone wasn’t busy!
Can you fast-track my repair if I pay more?!
No, all customers and equipment are treated equally here, with the only exceptions being some commercial jobs, and they don’t pay more.
I’ve been asked this a few times, with the imputation that these people would like to push their way to the front of my customer queue. I can must assume it’s worked before for these people, but I don’t run my business that way.
All customers are treated equally here and jobs are fast-tracked only where there are legitimate reasons, such as health concerns or mission-critical time constraints.
Telling me you will pay “A thousand bucks if I’ll look at it today” is not going to win me over. Call me crazy. No Hawaiian holidays for me, probably.
Is it safe to buy hi-fi equipment on Gumtree?
Generally no, unless you can have equipment inspected and you understand that PayPal offers no buyer protection on Gumtree.
You need to be careful when buying anything like expensive equipment on Gumtree, a local classifieds selling platform here in Australia. Did you know sellers can circumvent the buyer protection that normally exists when you use PayPal?
Suso aka Jackypl aka Jackpyl aka Jacky…
I wanted to purchase something recently and was dealing with the seller, a guy called Suso. He said he accepted PayPal. The item I was looking at cost around $4.5K AUD and when you buy something expensive sight unseen, you need all the protection you can get.
Interestingly, after what I’m about to describe happened, Suso then quickly changed his name to jackypl, jackpyl and later (currently as of 2024) to Jacky. Be very wary of sellers who constantly change their name, it’s a way of getting around bad feedback and poor reputation. There’s a reason I’ve used the same name on eBay and Gumtree for 20 years.
So, I asked ‘Suso’ aka Jacky if I could pay with PayPal. He took a long time to reply (warning #1) and then said I could, but that it would cost more (warning #2), despite the listing claiming that PaPayPal was accepted, at the asking price. Anyway, I reluctantly agreed and asked for the invoice to be sent. I was about to pay the PayPal invoice when I read the fine print:
NOTE: Buyer protection is not available on this transaction.
PayPal payment window
Buyer Protection
That’s right, you pay to use PayPal only to discover that the only reason for using it isn’t available on the expensive transaction you are about to complete! What’s the point did using PayPal if there’s no buyer protection? None.
I followed up with Gumtree who told me they didn’t offer buyer protection, and PayPal, who told me they did AND they didn’t (warning #3). One PayPal agent told me they did, as long as the seller invoices you a proper goods and services invoice rather than using the family and friends option. The other told me they didn’t offer buyer protection on any Gumtree transactions.
The seller stopped responding to me when I asked about this (warning #4). To me, this behaviour indicates he had something to hide and I decided the seller and his equipment were too dodgy. It seems he deliberately used the family and friends payment option that negated buyer protection.
I bailed on this transaction and imported other equipment myself, directly, which is my preferred methodology anyway. My advice is to avoid PayPal on Gumtree, and probably to avoid Suso / jackpyl / jackypl / Jacky. I will not use Gumtree for any serious equipment purchases in the future.
Should I work on my own equipment?
The answer depends on your skill level, access to tools, parts, etc. and understanding of the work required.
Working on your own equipment can be very rewarding and can save money and enhance the ownership experience. For some, basic maintenance may be quite straightforward and yet for others, the results can be disastrous, so as always, pick your battles!
Know What You Are Doing!
There’s a simple truth that I believe applies to all situations like this and is eloquently expressed by one of my favourite YouTubers:
If you know what you are are doing, you have a tendancy to KNOW that you know what you are doing!
Ed Ting
If you know that you know what you are doing, excellent. Be aware though that most owners do not know what they are doing and most dangerous of all, don’t know that they don’t know.
Skills
Working on electronics requires very specific knowledge, skills and tools that the average person simply won’t possess. The particular skill sets needed to do a job well take years to acquire. Desoldering, for example, is done poorly by most technicians, let alone first-timers. Bad re-work can quickly destroy a piece of equipment.
Tougher jobs, requiring access to mission-critical information, experience, tools and techniques can slow you down, increase the risk of inflicting damage and place you at the mercy of the forums and armchair experts. This is where things can really go wrong and one piece of bad advice can turn things upside down.
Horses for Courses
It’s sensible to get the best and most experienced person to do a job. This guarantees the best result, assuming you go to someone good, and it frees you up to earn money doing what you are good at. We all want to save money, yet paradoxically, attempting highly specialised work like electronics repair can often end up costing a lot more money in the long run.
Why does hi-fi equipment require specialist repairers?
Because hi-fi equipment is unique and quite different from appliances and other general electrical products.
Hi-fi equipment contains unique components and mechanical designs. A unique set of knowledge and skills accompanies working on this type of gear. General electronics repairers, musical instrument techs and whitegoods repair guys do not have the requisite knowledge, skills and tools to expediently and expertly repair this gear.
What are intermittent faults and why are they so tedious?
What
Intermittent faults are the most annoying type of faults one comes across when working on electronics. They are commonly found in the domain of electronics and can be a royal pain in the ar$e
Intermittent faults are best described as faults that:
- Come, go and are not always present
- Can be difficult to trigger or replicate
- Are modulated by triggers like temperature, voltage and humidity
Why
Intermittent faults can arise for various reasons:
- Solder joints degrade over time and may become electrically resistive and thermally intermittent
- Capacitors and resistors change as they age and as they warm up during operation, altering their performance
- Customer equipment set-up and use patterns may cause intermittent faults that are related to another piece of equipment, a cable, etc.
- Transistors and diodes may develop internal leakage, causing gain changes and noise. This may present as popping, rushing, crackling and whistling sounds, or even silence, which can be hard to trace. Semiconductor faults often cause variable DC offsets, tripping equipment protection circuits.
- Electronic parts don’t generally show obvious signs of deterioration as they age. They must be tested, usually under dynamic conditions, to establish functionality and health.
Which
Transistors are most likely to cause tedious intermittent faults, and some types are more prone to doing so. You don’t want to replace every transistor in the hope of resolving something like this. That’s a costly, wasteful process that may change the sonic character of the equipment and cause other issues when carelessly done, as it often is.
With the component-level repair necessary when working on older hi-fi equipment, one should always find the culprit/s and replace them, and others like them, where necessary. In other words, we always want to find and eliminate the cause of the problem. This is not the domain of recappers…
Paradoxically, even reworking dry joints associated with a bad transistor can sometimes ‘cure’ it for days or weeks, only for the problem to reappear, making finding them even harder. Fixing these problems is where we earn our money and lose our hair.
Fixes
Resolving these faults can be technically challenging, especially if the fault disappears as they do. There are ways and means of coaxing these faults out of hiding, but equipment will occasionally need a couple of visits for problematic intermittent faults to be exterminated.
Whilst intermittent faults are tedious, they are also extremely satisfying to resolve. Some of my best repairs have been when resolving intermittent faults, like with this Technics SE-A5 power amplifier.
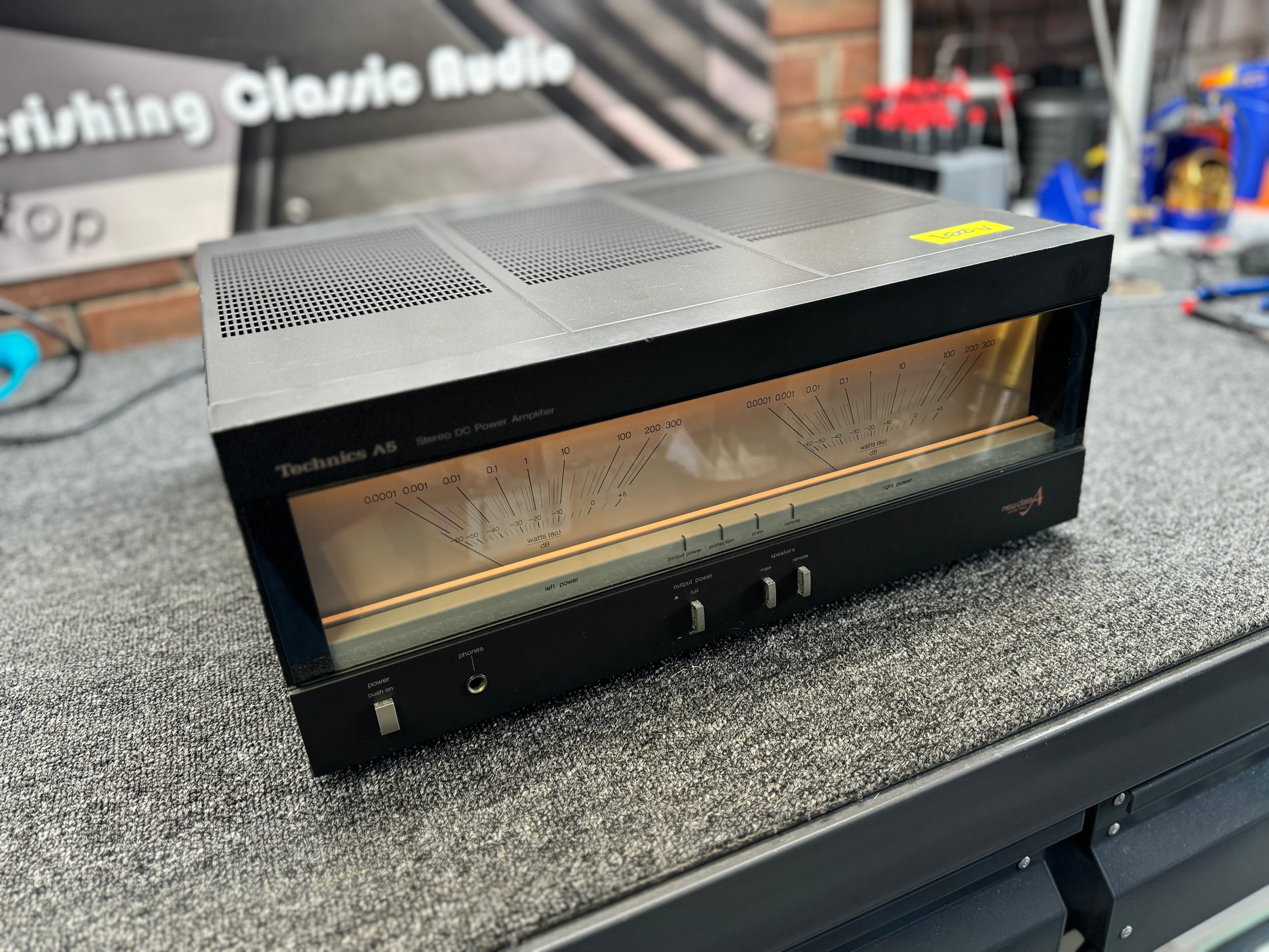
Just remember this, though, before you go nuts at your technician for not fixing an intermittent fault: These are tricky faults to find, and their intermittent nature is no more my fault than it is yours, or your mum’s! Customers need to work with their repairer to deal with the worst of these faults, so patience may be required sometimes.
How do I choose a better amplifier?
Amplification is the heart of any system and to improve it, I suggest you focus on three main areas.
These can be broadly grouped into: 1) reducing integration, 2) obtaining better-engineered/built equipment, and 3), getting better bang-per-buck, meaning pre-owned, older equipment. Let’s examine each of these in turn.
Integration
Integration refers to how many functions and therefore compromises are crammed into one amplifier box. In order of most to least integrated amplification, we have:
- All-in-one radiograms, lifestyle systems etc
- Receivers
- Integrated amplifiers
- Stereo power amplifiers
- Mono power amplifier
The simplest solution is called a radiogram, stereogram, 3-in-1 etc and we generally don’t consider these hi-fi, so I won’t cover them here.
Next, we have the receiver. Receivers are a power amplifier, preamplifier and tuner in one box. All consist of a series of many compromises, the smaller and cheaper, the more compromised.
Epic receivers like this Sansui G-8000 are less compromised but still compromised compared to a separate tuner, preamplifier and power amplifier.
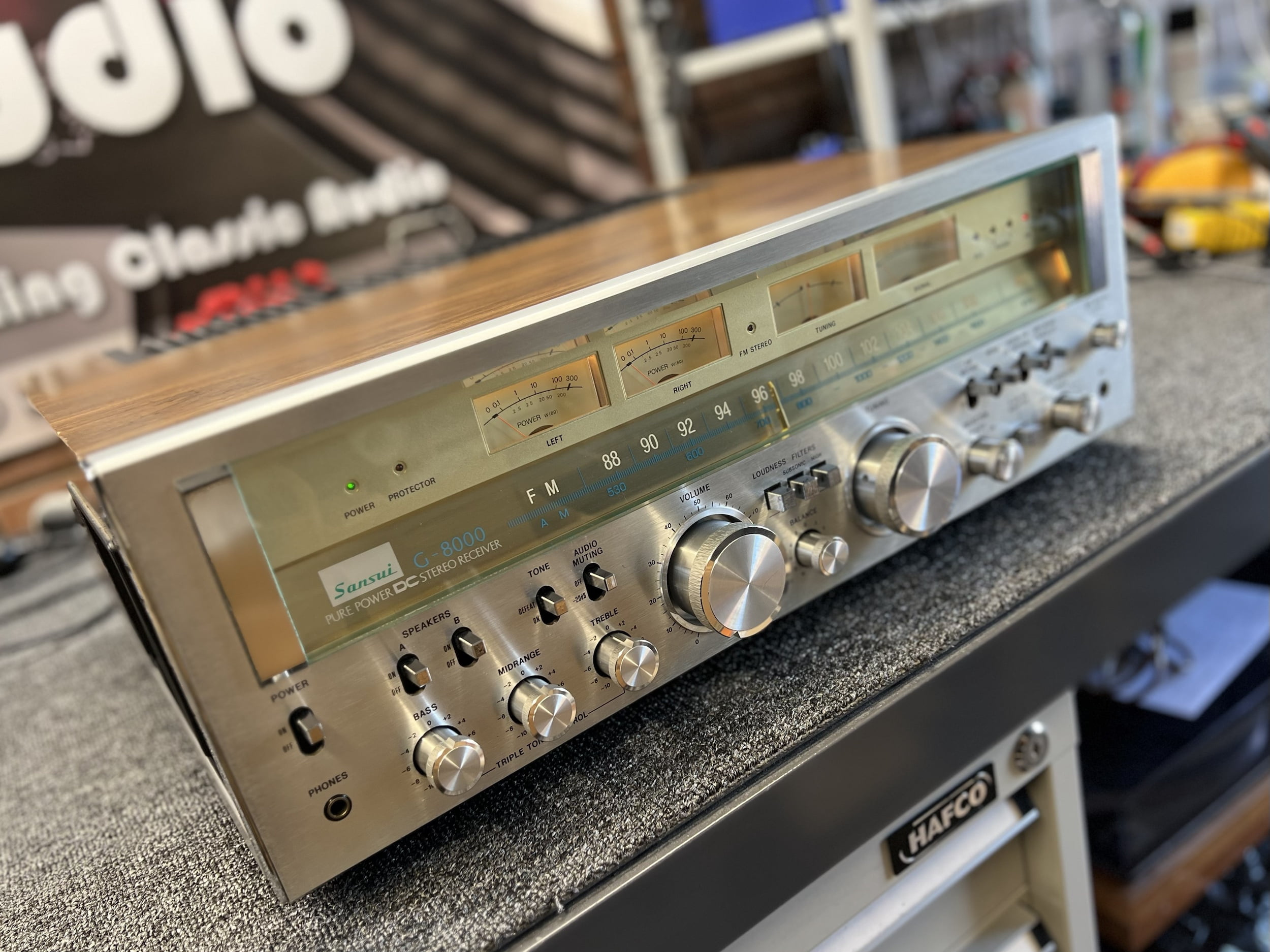
One level less integration involves removing the tuner from the box. Doing so leaves us with what we call an integrated amplifier, a combined preamplifier and power amplifier in one box. Examples include the stunning Pioneer SA-9800, Accuphase E-302, Technics SU-V8 and hundreds of others.
Integrated amplifiers work well for many and represent an acceptable compromise for those wanting to save money and have a decent-sounding system. They contain many compromises though, even at the stratospheric high end of integrated amplifiers, like the Accuphase E-800 class A integrated amplifier.
Separate components from the same company crush the performance of even this beast. How do I know? I own a complete system of high-end Accuphase components and I work on and listen to this gear every single day.
The least integrated and therefore best-performing amplifier solution comes in the form of separate preamplifier/power amplifier combinations, like my Accuphase C-290 and A-75, for example. The stereo power amplifier is the least compromised option many people end up with and it is a suitable stopping point for many in terms of increased performance.
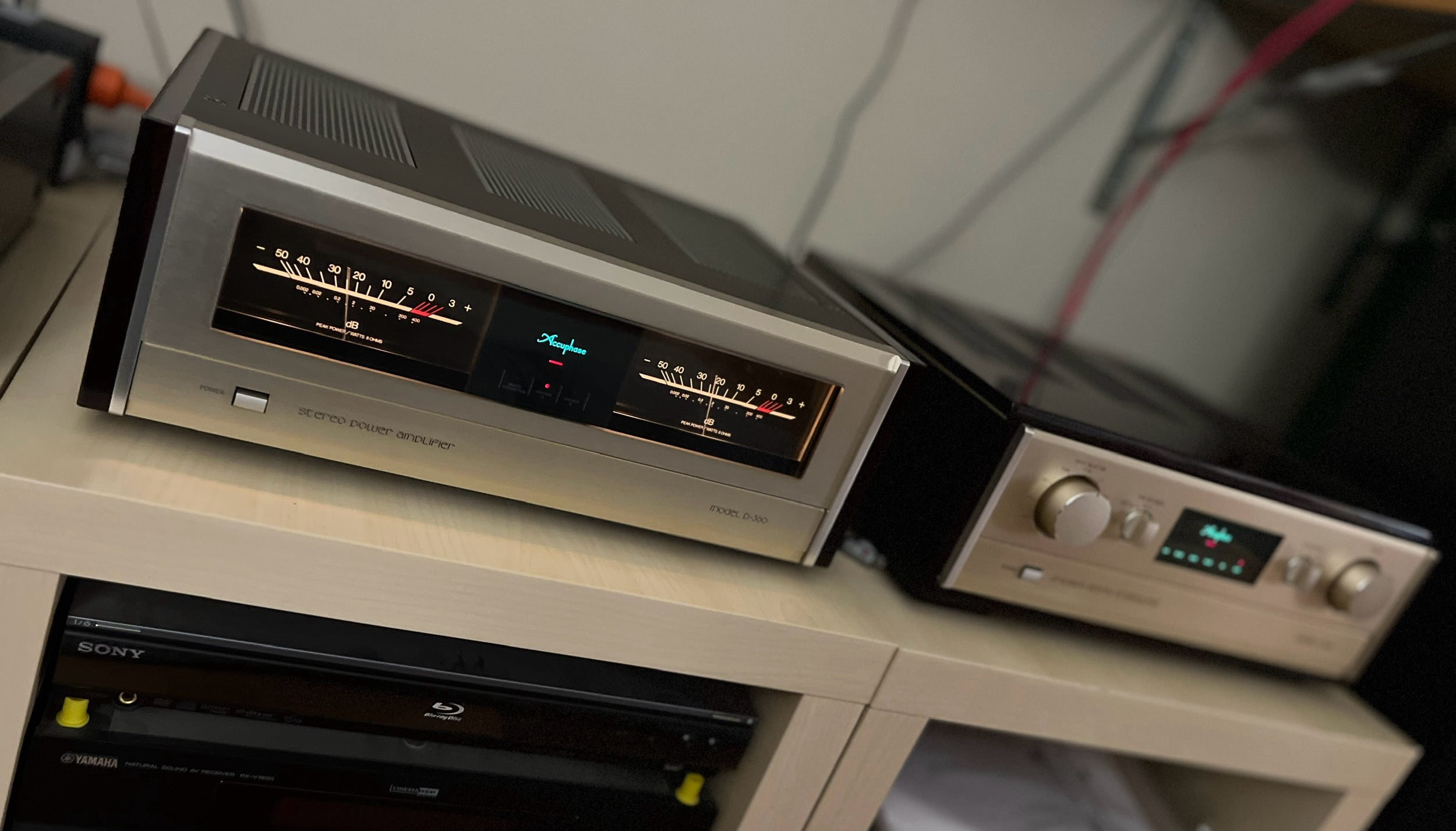
Even with a stereo power amplifier like the A-75, there are still compromises, just fewer of them. The ultimate power amplifier solution, other things being equal, is to have dual mono power amplifiers. In terms of Accuphase equipment, that would mean purchasing two Accuphase A-300s!
If there’s one takeaway here, understand that integration is the enemy of performance. The best solutions are the least integrated ones. So if you want to improve your amplification, reduce its level of integration.
Build & Engineering
I’ve written about this a lot over the years but there is no special new technology that makes a modern amplifier in 2023 any better than a vintage amplifier from the ’70s or ’80s. There are lots of reductions in build quality and engineering though that make the older gear often significantly more desirable, better performing and longer lasting.
In terms of design, engineering and build though, you want features like separate transformers for each channel, or even for different parts of the amplifier like the phono preamp for example. Output devices are important and MOSFETs often tend to sound warmer and smoother than bipolar devices, other things being equal. Balanced designs are preferable to single-ended ones and offer significant technical and therefore sonic advantages. Class A is also a highly desirable design feature and one I’ve written about separately.
Age
OK, so why do I go on about age in this context? Simply because back in the day, labour costs were lower, and engineering and manufacturing standards were less compromised by the search to build things more cheaply. I’m fortunate to have worked on most equipment from most of the major manufacturers over the years and without exception, I can draw a line through the changes in build quality and engineering and find a broad peak running from the mid-1970s through to the mid-1990s. In some cases, the design and quality were even higher back in the 1950s and 1960s.
Fidelity
Waveform fidelity can be considered the precision with which signals are amplified. Technically, this covers dynamic fidelity too, but it’s worth thinking of them separately, as it allows us to discuss great sounding low powered amplifiers, too. Waveform fidelity is ultimately determined by the quality of design and components used, how many corners are cut, or not cut etc.
Dynamic fidelity relates to the ability to replay the full dynamic range of the music and comes down to how many output devices there are and the rail voltages supplying them, amongst other things. To be able to reproduce the full range of sounds from soft to loud, within your listening envelope, and with the sensitivity of your speakers in mind as this is critical, a certain amplifier power output will be required.
Options
The easiest way forward for most owners of basic receivers and integrated amplifiers is to purchase a better integrated amplifier, like an Accuphase E-202 or E-303, Krell KAV-300i, Luxman L-550, Pioneer SA-9800, Sansui AU-919, Technics SU-V8, Yamaha CA-2010, and there are many, many others.
The very best way forward is a preamplifier/power amplifier combo, again, of which there are many. This will take up more space, but it is the ultimate solution and keeps small signal and large signal circuits largely separate. Wanna go super-ultimate? You’ll need two mono-bloc power amplifiers to go with your high-end preamplifier. The best bang per buck will always come from older gear.
Power
Regarding power, read this: https://liquidaudio.com.au/faq/are-low-power-amplifiers-acceptable-in-hi-fi-systems/ and this: https://liquidaudio.com.au/faq/how-important-is-it-to-match-amplifier-power-output-with-speaker-sensitivity/.
Power is important, there’s no getting away from that, but some of the very best-sounding amplifiers are lowish-powered class-A designs. They have dynamic limits that must be respected though and using one might require a tradeoff of improved fidelity for reduced dynamic capabilities, or more sensitive speakers.
Conventional speakers of around 87 – 89dB/Watt sensitivity will, in most cases, require around 100 Watts per channel to achieve moderate dynamic realism without clipping or compression in most environments. Low-level listening and high-sensitivity speakers change that picture, allowing for less power. Bigger rooms, less sensitive speakers and those that demand realistic sound pressure levels will require much more power.
Regarding amplifier types for different use cases, read this, and this.
The Best Amplifiers
I often tell customers that you can look at the design, engineering and execution and pretty much tell how good a piece of equipment will be in most cases. Sure, you need to listen to confirm that you like the sound, but good designs invariable sound good, and bad ones, bad.
In terms of what to look out for, this is heavily influenced by budget as this will include some features and exclude others.
- Avoid very low-powered amplifiers, except for low-level listening and/or very sensitive (ie non-standard) speakers
- Avoid very cheap amplifiers because you get what you pay for and good equipment is never cheap
- Avoid integration wherever you can
- Look for class-A, MOSFET output devices, and seriously heavy build
- Generally the heaviest, most expensive (when new) equipment is going to be the path to take. Nothing good is lightweight or cheap to buy, except something digital like a Wiim.
Regarding equipment you currently own, maintaining gear you love is always worthwhile and spending money on it will improve it if that work is done by a competent technician. Just keep in mind that, no matter what parts are installed, you cannot make a piece of basic gear into a high-end killer, no matter how many WIMA capacitors someone installs.
Most people should look to a significant equipment improvement, requiring a significant outlay. If budget is the overriding factor, I suggest saving and waiting until your budget allows for the purchase of equipment that offers significant improvement over what you currently own.
Summary
- Reduce integration, improve quality, engineering
- For sonic improvements, you have to move forward, not sideways
- To improve on a basic integrated amplifier, you need a better, more expensive design with less integration
- Good advice is critical to making the right decisions, bad advice leads to the wrong ones
Need More Advice?
This entire 650,000+ word website is free, and we offer more great information derived from actual hands and ears-on experience here than probably any other independent, specialist source. Check out other FAQs, reviews and so on for much more.
For those needing more specific, personalised assistance, we offer our highly regarded advisory service, where I tailor recommendations and improvements targeting your specific use-case, room, system, tastes and budget. You won’t feel bad for taking up my time because you are paying for it, exactly the amount you need, too.
Mike, what do you think of affordable, modern phono preamplifiers?
Do you mean those ‘affordable’ modern phono preamplifiers that cost $1000 or more, contain about $50 worth of parts if you’re lucky and sound ordinary? Not a lot.
You first need to understand that I’ve been spoiled by great phono preamps made when vinyl was at its peak. Much of the excellent equipment from that era is unsurpassed in terms of build, technical specifications and sonic performance. Cheaper, modern gear simply cannot hold a candle to it, despite all the hype and often impressive on-paper specs.
There isn’t a lot new in terms of analog circuit design and engineering that improves phono preamps. There are improvements in opamp design and miniaturisation though and these things save money. The very high cost of labour and the resulting increased production cost of gear these days mean that reducing construction costs is critically important.
These days we have affordable phono preamplifiers filled mostly with op-amps and cheap, miniature passive parts. Very few affordable discrete designs containing really high-quality parts exist.
Want a really good phono preamp? Get an older high-end preamp with a discrete class-A phono stage, coupled with a step-up transformer. Need advice about what to buy? Use our advisory service!
How good is the Denon DL-103 MC cartridge?
Better than many have heard but not as good as many think!
For those looking for the TLDR: The Denon DL-103 MC cartridge is probably the best available for higher mass arms like my Fidelity Research FR-64S at the low $400 asking price. The DL-103 is one of my favourite budget cartridges and great value for the money, with the right tonearm.
That said, the DL-103 isn’t well-suited to many turntables and tonearms, nor is it anywhere near as good as the very best carts available when we remove the price restriction.
Keep in mind that many who write about cartridges and turntables are relatively inexperienced and late to the party. A Denon DL-103 may be the best cartridge some have heard but this is often because they have very limited experience with a wide range of cartridges. In the overall scheme of things, this is a budget MC cartridge.
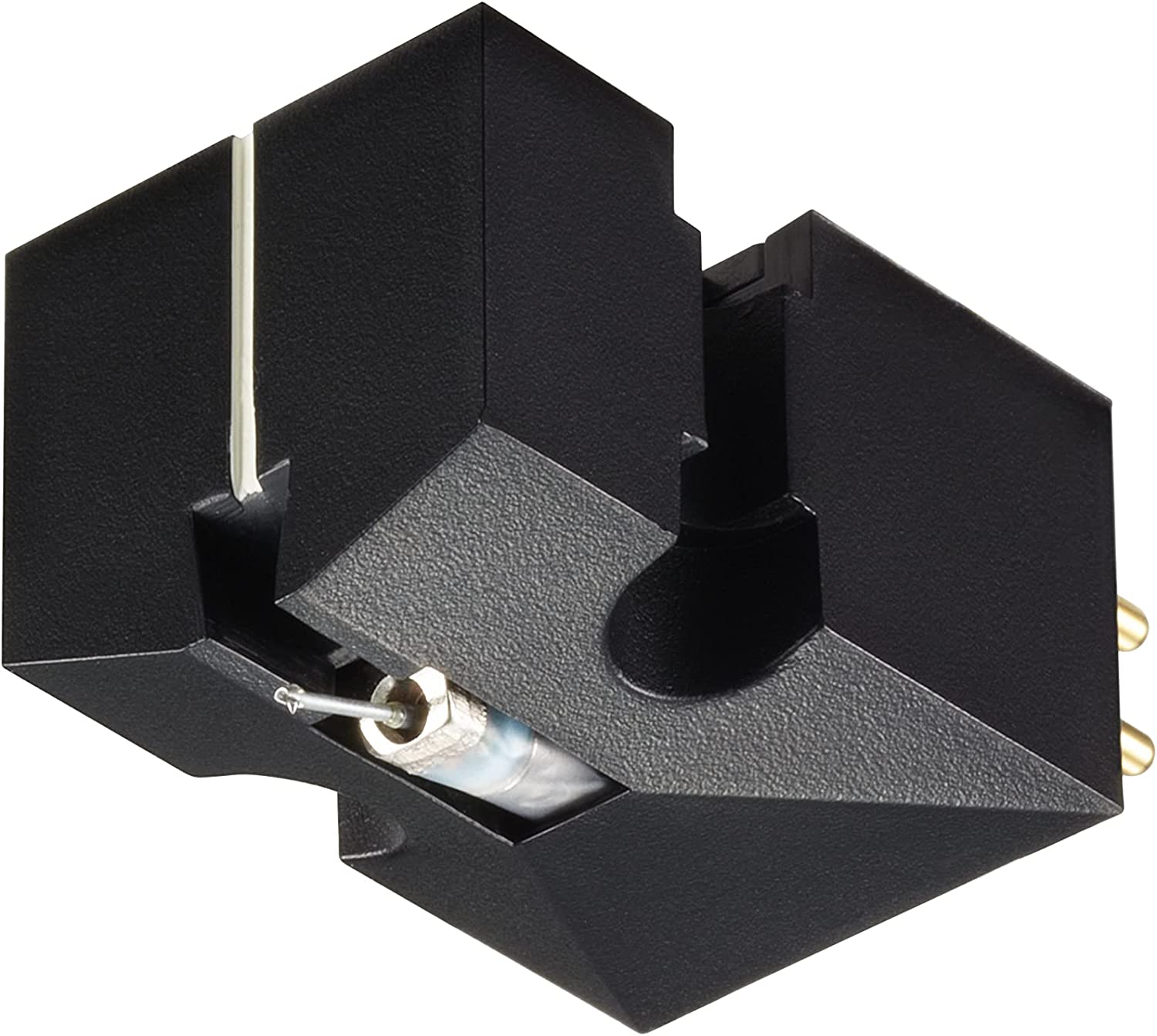
Physics
The Denon DL-103 was designed for longer, heavier arms, bolted to a nice heavy headshell. That’s because the 103 is an old-school low-output, low-compliance cartridge with a conical stylus, and was designed when higher-mass arms were common.
Understanding cartridge physics is vital to understanding how cartridges interact with headshells and tonearms. Cartridge-tonearm compatibility comes down to simple math and becomes intuitive with experience and a good technical understanding of the mechanics/physics involved.
Whatever else you do, make sure whoever supplies and fits your cartridge can explain a) why the DL-103 needs a higher-mass setup and b) verify compatibility with your equipment. Anyone telling you that “this isn’t important” or that “the DL-103 will work on any arm” or is “the best cartridge available” should be avoided because that’s the same as saying 1 + 1 = 3.
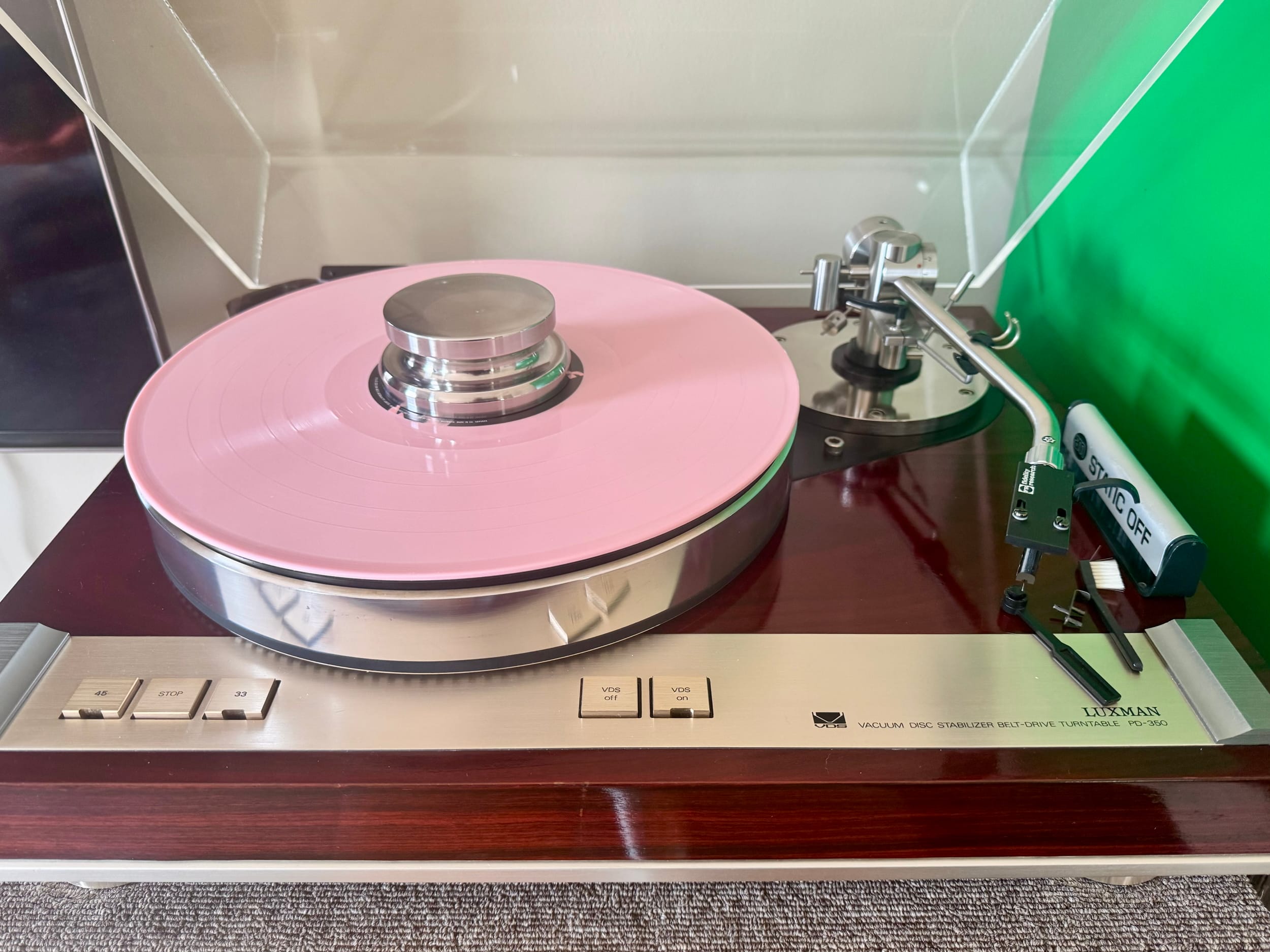
Perspective
The DL-103 is a beautifully made and presented low-output moving coil cartridge that sounds great in the right rig. It’s a classic-sounding cartridge because it was designed in a classic era. Tonearm design philosophies have changed since then though.
We’ve had the era of super low-mass arms, to which a DL-103 should never be fitted. We are now in a medium-mass tonearm era and the DL-103 isn’t very well-suited to many of these, but can be used with medium-mass arms as long as the resonant frequency is known and the necessary mass adjustments are made.
How Good?
How good is the DL-103 in the right set-up? It’s a very good cartridge for the low asking price. The Denon DL-103 sounds balanced, clean and powerful, with no obvious issues anywhere. The DL-103 offers higher resolution than similarly priced MM carts when partnered with a suitable high-gain phono pre-amp (critically important).
Overall, the DL-103 is better in most ways than similarly priced MM carts, except perhaps tracking, but perspective is critically important. I’ve heard people say they’ve never heard better than the DL-103 but that’s only because they literally haven’t heard any of the much better cartridges available.
I’ve fitted dozens of 103s and hundreds of cartridges. The DL-103 is a solid performer but there are significantly better-performing cartridges available. I think everyone loves the idea that a $400 cartridge with an aluminium cantilever and conical diamond might be as good as cartridges costing thousands, but this is just whimsy. If the DL-103 was as my Ortofon MC-A90, MC Jubilee, Supex SDX-1100D, or even my Fidelity Research MC-202 or FR-1 Mk3, I’d only use Denon DL-103s!
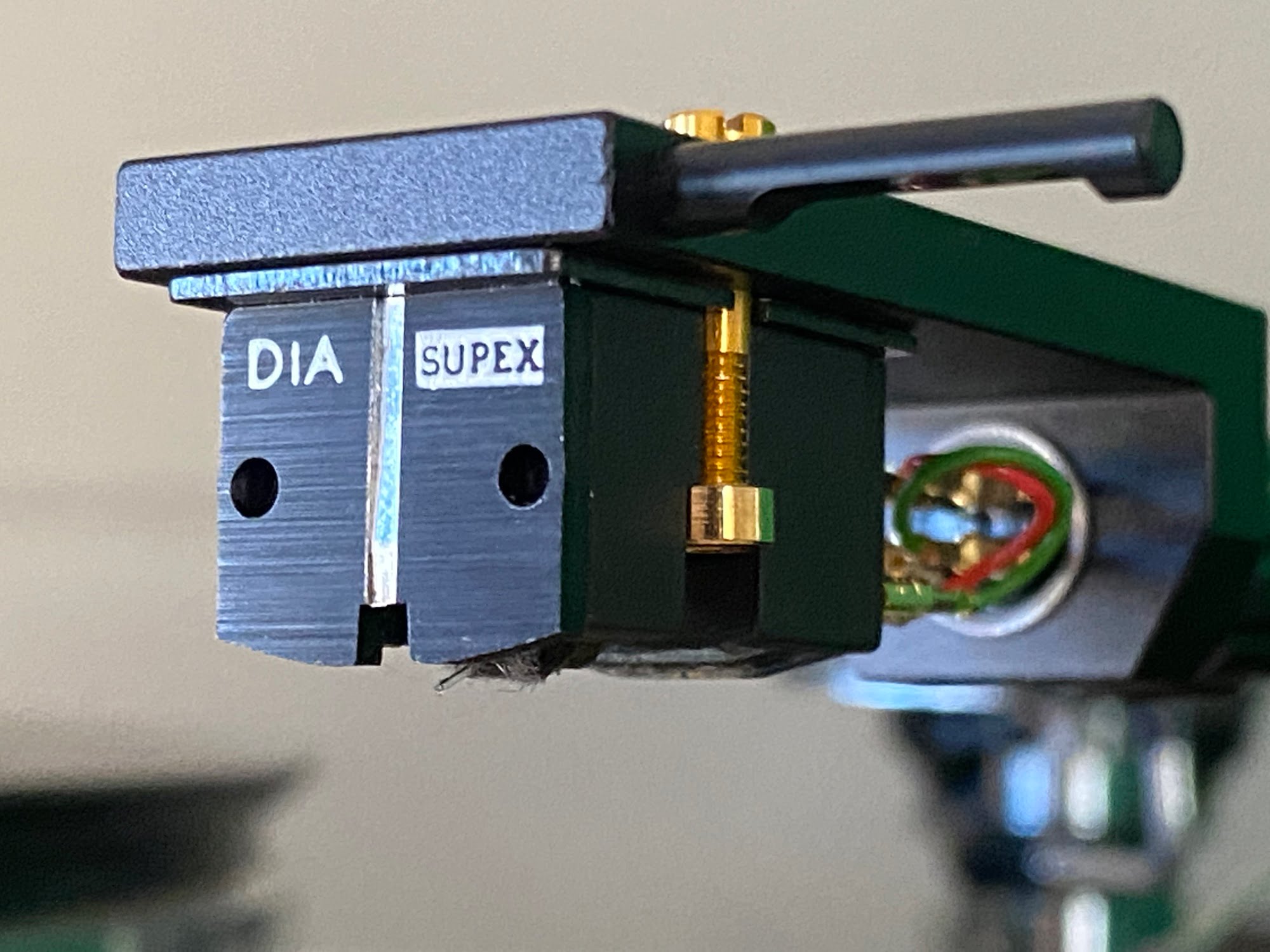
Variants
There are some specced-up versions of the DL-103 available, like the DL-103R for example. The DL-103R is certainly a better-sounding option for most people, though having heard most of the variants available, I think the best bang-per-buck version is the Denon factory original.
Other manufacturers dress up DL-103s in fancy aluminium or wooden bodies and charge hundreds more for them. Does that sound like great value to you? You can take a basic cartridge and wrap it in a fancy metal box, and it’s still a basic cartridge in a fancy metal box, so be mindful of this.
Salespeople NEED to sell you things, like DL-103s and plenty much worse. Once the sale is complete, in most cases that’s it. For many owners, even if the set-up is sub-optimal, the result will often be better than the crappy sub-$100 MM cartridge most are stepping up from, even if it’s still way out.
Whatever variant you buy, make sure that your retailer explains that the DL-103 is a very low-output moving coil cartridge, and the implications of this. If you’ve not been told that it needs a top-notch high-gain phono preamp and/or a step-up transformer, how much these elements cost, or how critically important they are in extracting the most from a good MC cart, then I suggest finding a different retailer.
The Bottom Line
The DL-103 will never be the most resolving, airy or articulate cartridge, but it is honest, beautifully made, and it will smack around Ortofon 2M Reds, Audio Technica VM95Es and worn-out old-school magnets and make them look as bland and uninvolving as they really are.
A DL-103 will deliver a better-balanced and more resolved result than many sub-$1000 MM carts, and even some coils. A $1500 cartridge like an Ortofon Quintet Black S for example, comprehensively bests the DL-103. Even at $699, Audio Technica’s AT-OC9XEN is better in most setups.
As good as the DL-103 is for the money, it’s a stepping stone for anyone seriously invested in vinyl playback and in advancing their playback performance. But, on the right turntable/tonearm and used with a quality MC phono preamp, nothing else retailing for $400 will touch a DL-103.
Why did you remove the phone number from your contact page?
So I could get more work done! UPDATE: I reverted this, legitimate enquirers want my number so it’s back up. I’ll filter calls more effectively.
Generally speaking, the only calls I want are from people booking our services and from folks who’ve purchased consult time via our advisory service. We have a great system for handling booking and advice enquiries via our contact form.
What’s better: a short tonearm or a longer one?
Other things being equal, a longer tonearm is always better, with one exception: linear tracking arms.
The reason you want a long conventional arm, or a linear tracker of any length, is to minimise or eliminate tracking error and therefore tracking distortion.
When a tonearm moves across a record, it does so in an arc, because the arm is fixed at a point that becomes the radius for arm motion across the record. Ideally, the tonearm would move in a straight line across the record. That isn’t possible, except in the case of the linear tracking arm, seen on decks like the Technics SL-10 for example.
For conventional arms, the stylus will scribe an arc across the record, the curvature of which is determined by the length of the arm. The longer the arm, the greater the radius, the gentler the arc and the lower the tracking error, and therefore distortion.
This is the single reason why many of the best tonearms are 12 inches long in the old money. Very good arms are usually 10 inches long or close to it, like my Fidelity Research FR-64S, and the standard length is around 9 inches. There are some excellent 9-inch arms, but this is about as short as you want to go before tracking error causes significant tracking distortion.
You’ll occasionally find turntables with short tonearms, mostly sold in department stores. I’ve worked on a few Gold Notes for example with teeny little 8-inch arms. Short arms allow for small turntables, but the compromises are too great and I strongly suggest you avoid anything with a less than 9-inch tonearm.
Are there customers you won’t work with..?
There are, but not many!
As one of Australia’s most trusted repairers, we attract great customers and have very few issues. As every business owner knows, however, you cannot please everyone, no matter how hard you try or how well you run a business.
Liquid Audio, in collaboration with several other Western Australian technicians and retailers, manages a (thankfully) short list of people who will not receive assistance from any of us. This protects the businesses in the group and minimises pain for us, the business owners.
The Blacklist
My customer database comprises well over 1000 individuals and I’ve only added around 10 people to the blacklist over a decade, so we enjoy excellent relationships with an overwhelming 99.99% majority.
It is a pleasure assisting normal, polite, respectful customers, but I choose to avoid aggressive, demanding, disrespectful, entitled, rude or otherwise unreasonable people. Unfortunately, there exists a small subset of people so unreasonable and problematic that attempts to work with them must be avoided entirely.
When these individuals cause problems for us, my colleagues and I apply a zero-tolerance policy:
Assistance is terminated, details are recorded and shared, and that person is blacklisted and perma-banned.
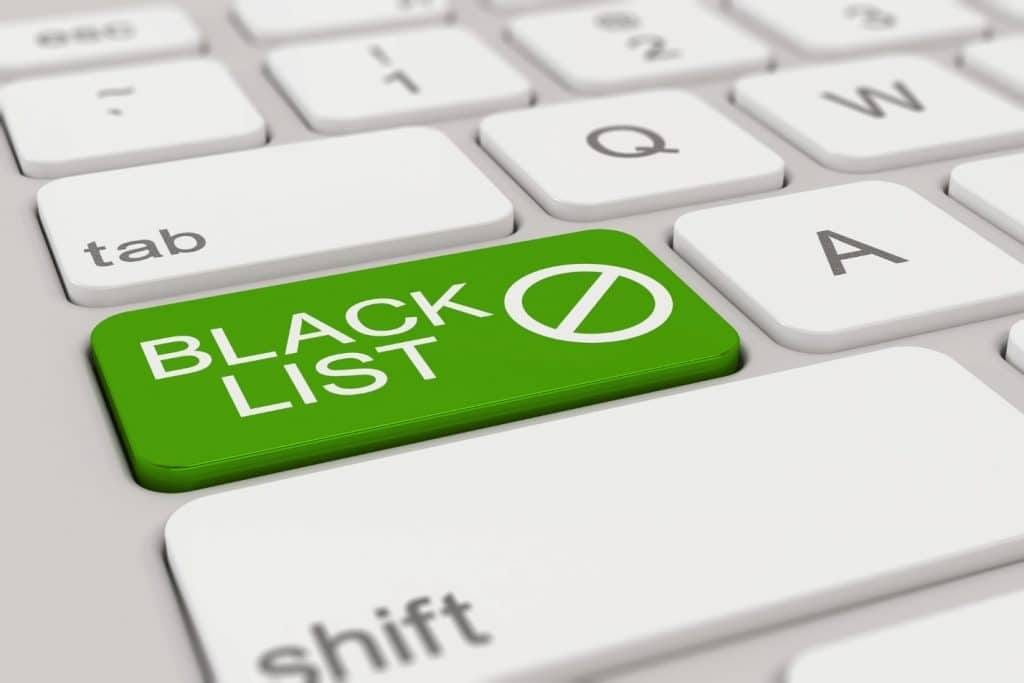
Rest assured, no reasonable human has been blacklisted nor will they be, but what does this mean for the few dozen individuals who have? Well, blacklisted individuals lose access to the most highly regarded technicians in Western Australia, forever and irrespective of which one they upset.
That’s a bad outcome for people who love hi-fi and care about its upkeep.
Admission
If you’re wondering how one makes it onto this list, in my case, do something like:
- Pound on my door like a loon for 30 minutes at 8 am on a Sunday in a pointless attempt to collect equipment when we are closed.
- Don’t pay your due-in-7-days account for a year, then forget to thank me for not selling your equipment and argue about the storage charges you’ve accrued.
- Accuse me (someone who’s been dedicated to helping the hi-fi community for more than a decade) of running a ‘scam’ after I’ve spent hours helping you, or of “stealing” 40-year-old, dead capacitors.
- Etc…
For anyone worried about being blacklisted, I can assure you that reasonable, respectful, folks have ZERO chance of this happening. Just be aware that the pathology leading to the examples above exists and we will protect ourselves from it wherever possible!
Are remastered records better than originals?
A great question. Some remasters are better, but often, original pressings are where the gold lies!
The answer varies according to the album and the pressing, due to many technical factors, but remastered records are often worse than excellent, lightly played original pressings, and in my experience, only occasionally better.
A Golden Example
A classic example of a good remaster being beaten by an even better original pressing can be found with one of my favourite records, New Gold Dream, by Simple Minds:
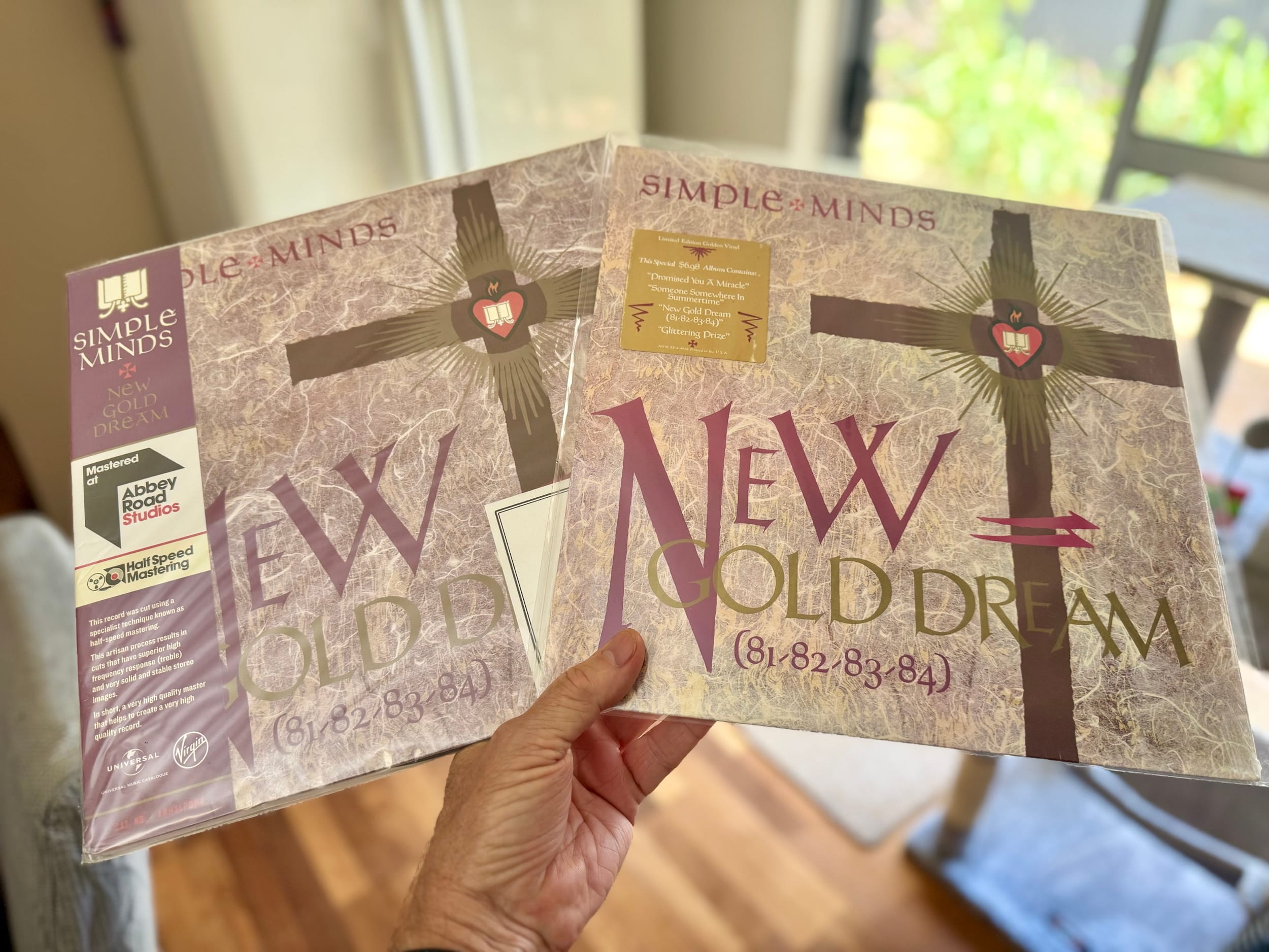
Here are two of my three copies of this great album. The one on the right is a rare gold and purple-coloured first release I purchased new and unopened from Japan. It appears to be nothing special apart from the gorgeous coloured vinyl. It’s a regular thin pressing, but it’s dead flat, very quiet, and from the year the album was recorded, or perhaps 1983, a year later, I’ll check that.
The copy on the left is a recent (a couple of years old) Abbey Road 1/2 speed mastered 180g ultra-hi-fi pressing that I purchased directly from Abbey Road. It is also a beautiful pressing: dead flat, concentric, quiet, and with great dynamics.
Here’s the rub: the original limited gold and purple edition from 40 years ago sounds better. This has been verified by several friends in my reference system and others have found the same. The early, thin pressing is quieter, has better dynamics, more air and detail, and more punch.
Who knew that older things could be bett… Oh, that’s right, I’ve been telling you this for years! 🙂
Age
Here’s what we know about analog recordings made on tape (as almost all analog recordings are): they offer the highest resolution of any medium, but deteriorate over time. The very best versions of the masters, mix-down masters, sub-masters and various analogs that make their way to the record pressing facilities are the ones made as close to when the original analog recordings were made.
What this means for records is that the early ones or those closest to the recording are often the best, all other things being equal. Better still, you want an early pressing from one of the first stampers made from the first mother – the moulds used to create the moulds used to press records. That’s because the moulds deteriorate every time they are used and the original master recording deteriorates from the moment they are made and every time they are played.
Add to this the fact that record plants, equipment, technicians and the people who operate the tape machines were all at their peak years ago, not right now, and the tendency for remasters to be produced too hot and you have a combination that renders modern remasters often disappointing. Don’t just take my word for it though, you can read more about this in many great articles online, like this good primer for example.
The Bottom Line
All that said, if you get the right album, remastered by the right engineer, in the right studio, with really good, intact analog masters as closely as possible to the originals, with good quality, clean vinyl that’s been well pressed, thick and flat, remasters can sometimes sound better than the originals, or at least as good. The problem is, there are not enough like this!
Mike – cassette decks – what’s the deal?
Cassette decks offer a ton of fun and a real ‘blast from the past’ user experience, but there are a few things to consider before you go crazy.
I love cassette decks and own several really nice ones. That said, cassette decks are amongst the most complex hi-fi gear and generally require the most maintenance due to their electro-mechanical nature, belts, gears, and motors. Think of the VCR you used to own, and you’ll not be far away.
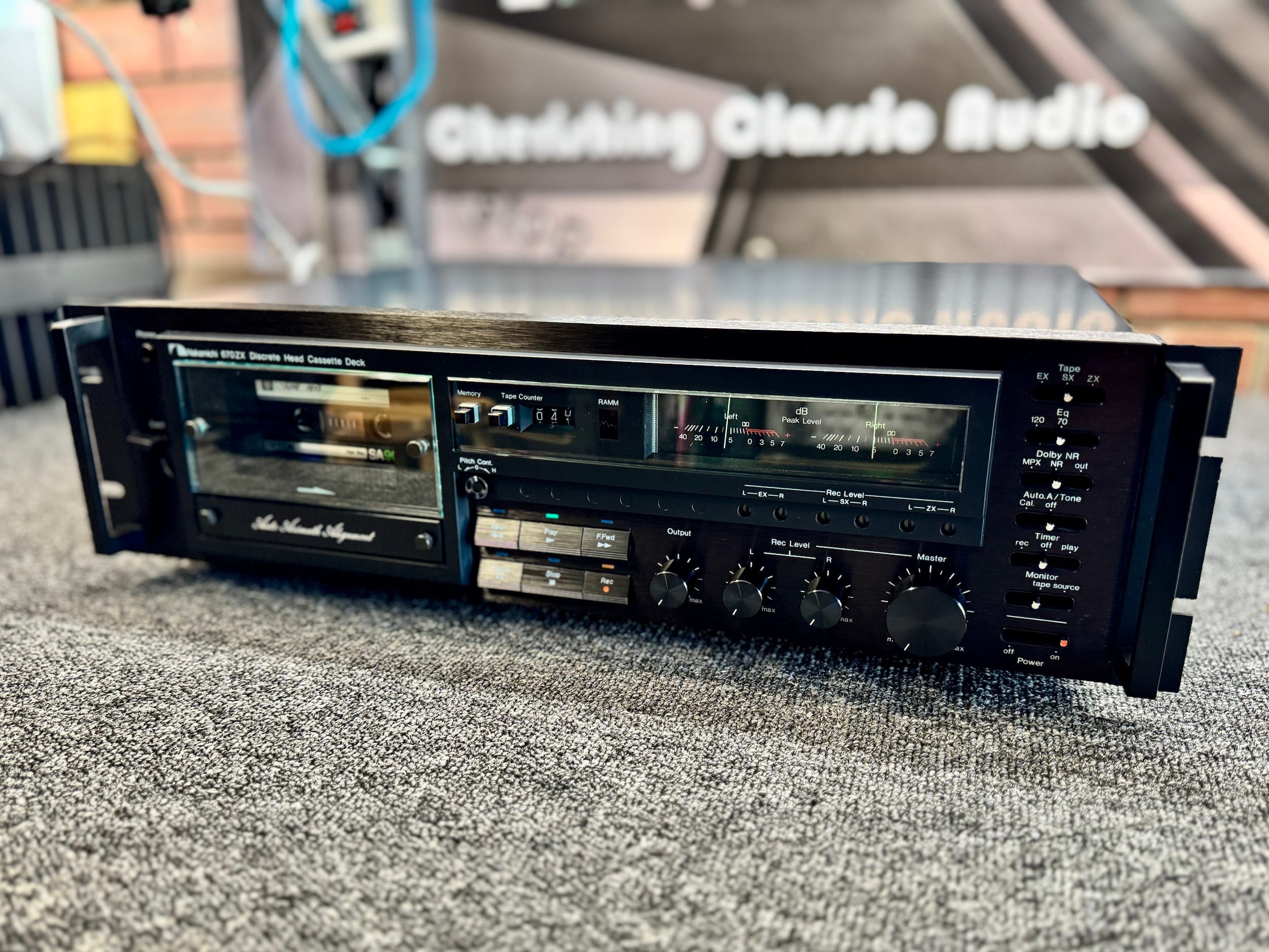
This maintenance is regular and periodic, with some necessary every 10 hours or so in the form of tape path cleaning. It’s also specialised, requiring special tools, lubricants, demagnetisers, calibration/test tapes and more. The work can be time-consuming and technical, much of which is way beyond most owners. So, the catch-22 with cassette decks is that as fun as they are, they can be costly to maintain.
I love playing tapes but remember that compact cassette, to use its correct name, was never intended to be a true hi-fi medium. It became one, and better decks with good tapes can sound excellent, but it’s more about the experience: warmth, VU meters, spinning reels and tactile interaction with these wonderful whirring machines.
If you want a cassette deck, look for a better, three-head, dual-capstan deck, from one of the bigger players like AKAI, Kenwood, Pioneer, Revox, Sony, TEAC, Technics, Yamaha and Nakamichi. Better decks cost more and are worth more, so the inevitable maintenance doesn’t feel so painful.
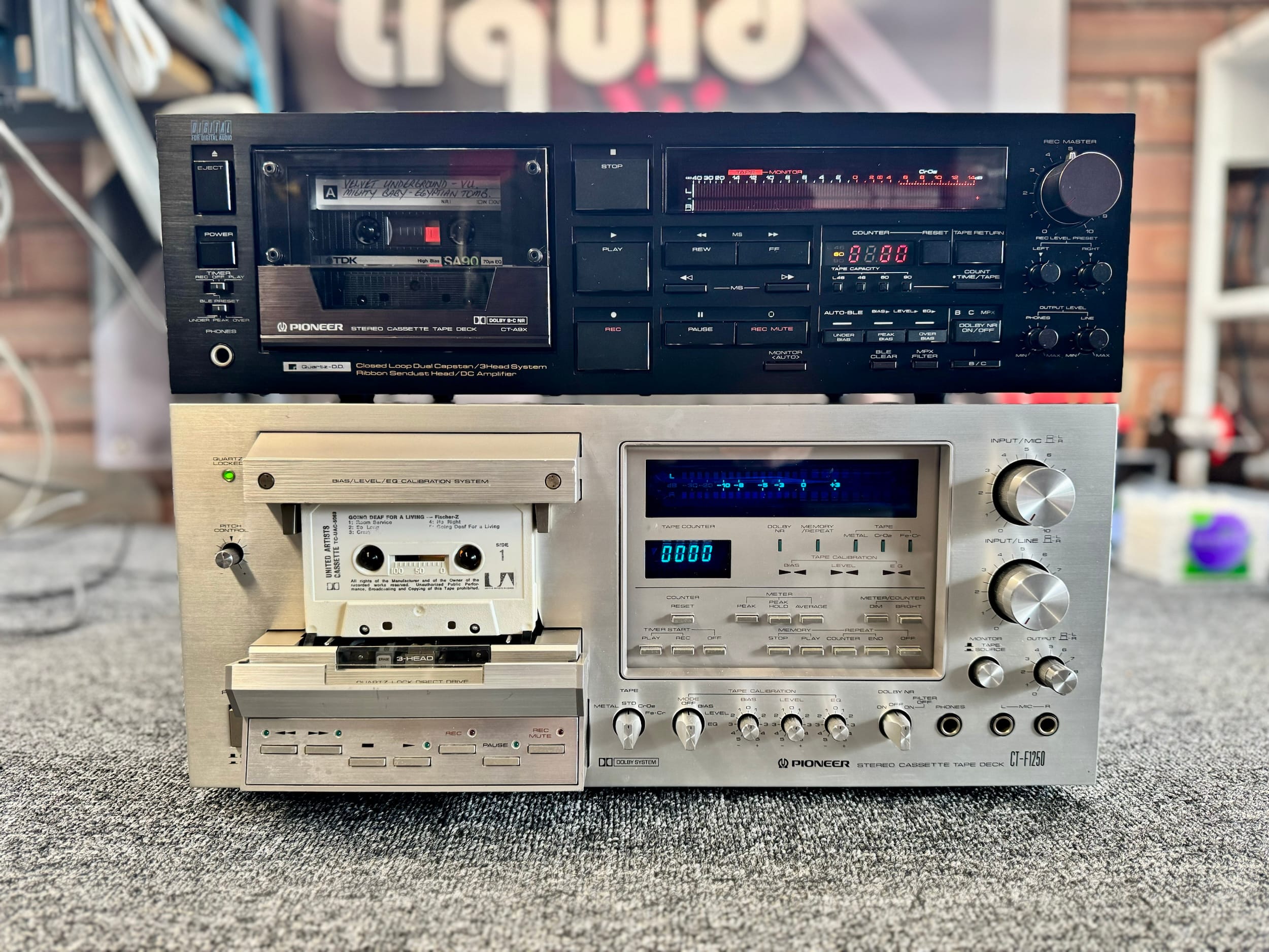
Full ‘mechanism out’ services have to be done periodically and take many hours. Many more hours can be spent on electronic adjustment and calibration. Most decks need major work at this age and the better decks are still very serviceable, but heads, pinch rollers and some other parts may be impossible to obtain, so choose carefully.
If in doubt, get good advice from someone who works on these wonderful old machines, and consider a specialist forum like TapeHeads.
Why didn’t you repair my equipment?
That depends on the circumstances associated with your piece of equipment, but there will always be good reason/s that I will carefully explain.
We focus on complex, no longer supported and often ‘unrepairable’ hi-fi equipment and fix almost all of it. This is important because:
- Much of it is complex, older equipment, sometimes lacking any available service data
- Much of it has visited others who could not effect repair
- It requires a technically-focussed component-level approach many cannot offer
Think of it this way: if these sorts of repairs were easy, there’d be no demand for our services, yet we are almost always fully booked, without advertising, and are known for fixing the really hard jobs that others often cannot.
There will be circumstances where repairs aren’t viable or possible within sensible bounds, though. There are also intermittent faults that may be challenging to isolate and resolve. These considerations are part of the challenges and rewards of working with complex electronic equipment.
Viability
In cases where repair costs are likely to exceed equipment value or customer budget, we may deem the work non-viable. We consider the condition, faults, value and work needed to properly repair a piece of equipment and even the customer when making this call. Let’s look at some examples:
- A customer doesn’t want or cannot afford to have the equipment properly repaired
- Critical parts and/or substitutes are no longer available
- A repair is unlikely to be viable or reliable for technical reasons
- A repair is not worth pursuing due to equipment condition, value, or customer issues
It’s important to understand that we are not responsible for equipment condition, faults, customer budget, parts or manufacturer support availability, or repair viability. These elements are beyond our control and are no more our responsibility than they are anyone else’s.
Example
I was contacted by the owner of an old amplifier, in poor condition, with various issues. The owner had emptied a can of WD-40 into it, it had been modified without documentation, tinkered with by several people, and was dirty, damaged and not well cared for. It was brought to us after everyone who shouldn’t have touched it had already.
After several hours of working through issues with the unit, I decided that further work was not viable due to the combination of issues, all of which were beyond our control, and the increasing amount of time that would be needed to resolve them, on a piece of equipment that was not worth much.
This doesn’t mean that amplifier, or another piece of equipment with a similar story, cannot be repaired, only that it cannot be economically repaired, given the issues, condition and type of equipment.
Despite doing my best to help this customer, explaining the issues and only charging our minimum, we were blamed for not fixing the amplifier, as though its problems were somehow my fault, with me being the last person to touch it! This was a valuable lesson about the importance of not trying to help everyone, and why I avoid equipment in poor condition.
Realistic Expectations
It’s like an 85-year-old visiting the doctor, wanting to be cured of arthritis. When the doctor examines the patient and determines that the required joint replacements and therapy are not viable or sensible, is that the doctor’s fault or responsibility? Should the doctor provide their time and expertise for free, simply because the patient doesn’t like the answer?! Of course not.
There are no miracles, but most equipment is viable to repair, especially if it’s in good condition.
My high-end amplifier has failed, how much will repairs cost?
I’d be happy to provide an estimate once we’ve diagnosed the fault/s and determined what remedial work will be needed.
That will, of course, require a careful and detailed inspection of your equipment, and avoid any unhelpful guesswork.
Assessment
Electronic equipment failures are typically ‘black box’ scenarios, meaning there are usually no obvious visual signs as to what has gone wrong. Contrary to what some imagine, failed components generally show no external signs of failure and ‘bulging capacitors’ are largely a meme created in forums, unfortunately.
Progressing from failure to remediation is where skill and experience come into play. The only solution is to test, measure, and get to the root of the problem/s. Asking a technician for a quote before they’ve looked at a piece of equipment is asking them to guess what’s wrong, what parts will be needed and how long the repair will take when they have none of that information.
Any answer will likely be wrong, so there is little place for guesswork in technical repair scenarios. It’s no different from asking a mechanic for a quote over the phone to fix a car with unknown problems or asking a surgeon for a quote on surgery before they’ve seen the patient. If these scenarios seem silly, then you’ve understood the point I’m making here.
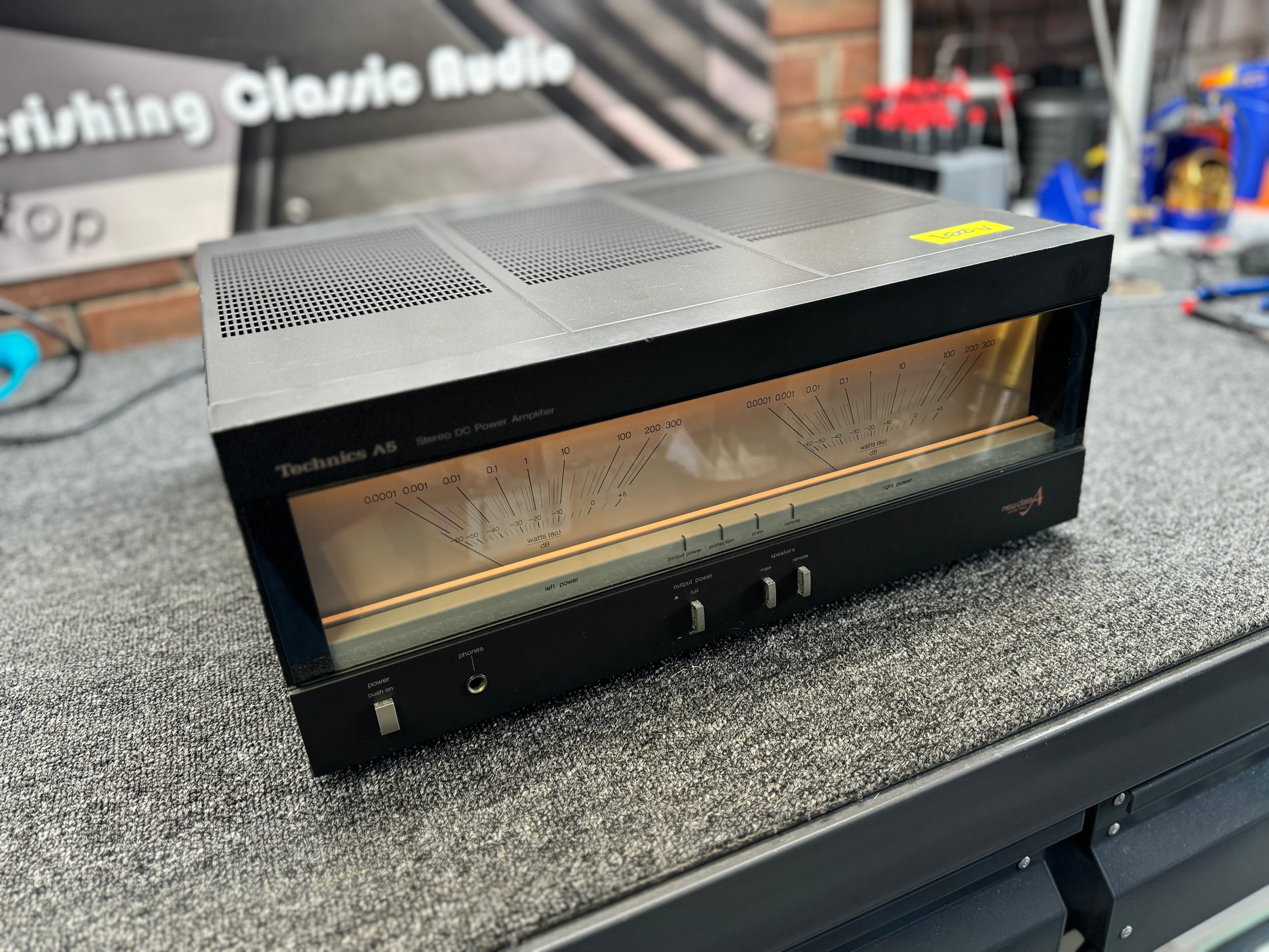
Six Steps
The correct approach involves a logic-based assessment of the equipment and its faults involving six steps:
- Collection of evidence
- Analysis of the evidence
- Location of the fault
- Determination and removal of the cause
- Rectification of the fault
- Checking, adjustment and calibration
Steps 1 to 3 comprise the assessment phase and generally have to be completed before a cost estimate can be offered. All steps require hands-on work with the equipment.
Other issues may become evident once work has commenced, which is why reputable repairers typically provide cost estimates.
Pretenders
So, why would anyone pretend to know what’s wrong and how much a repair will cost without first inspecting and testing the equipment in question? There’s a very simple answer to this: Because they need the business, and they’re prepared to take risks and mislead people to secure it.
Some folks expect sight-unseen quotes, and less ethical repairers enable this expectation because it brings them work from people who don’t know any better. It’s worth understanding that businesses that do this typically are those you would not want to use. We don’t engage in these sorts of practices, nor do we need the work.
I could never have guessed what was wrong and the hidden last fault with this Krell KSA-100S I repaired, for example. Similarly, an Accuphase E-303 that I repaired contained five unrelated, unguessable faults. One of the worst pretenders destroyed this beautiful Gryphon DM-100 class-A amplifier.
More…
Information regarding general service and repair costs can be found in this FAQ. Find out more with these repair-related FAQs:
What’s better: a good moving magnet cartridge or a cheap moving coil?
I don’t like either very much, but I generally recommend a good moving magnet cartridge over a cheap moving coil.
If you have say around $500 AUD to spend, and assuming you are chasing a medium compliance cartridge for a typical medium mass tonearm, there are lots of choices. Moving coil cartridges are technically better for a number of reasons. At this low price point, however, (yes, $500 is low for cartridges), moving coils are almost always high-output types and generally don’t sound great. An exception is the venerable Denon DL-103, but it’s not suited to lower-mass arms.
Cheap cartridges with aluminium cantilevers and spherical or elliptical styli don’t sound amazing, no matter the flavour. A nice moving magnet at this price probably has a better diamond and cantilever. It is going to sound warmer, punchier and probably a little easier on the ear, even if it lacks the resolution MC carts provide. There are no surprises here.
The MC Advantage
Much beyond $500, moving magnet cartridges don’t get a lot better because they are technically limited by the mass and therefore the inertia of their moving elements. Low-output moving coils start to come into their own at around the $750 mark. From here, the advantages of moving coils become critically important and this is why most cartridges I recommend from $750 are MC type.
The equally legendary but better Audio Technica AT-OC9, in affordable XEN configuration is available at this price point and crushes most similarly priced MM carts. The catch? You need a really good phono preamp to take advantage of the low output and higher resolution MC carts offer. Your Cambridge Audio 640P and iFi Zen are not going to cut it.
Almost all high-end cartridges are coils and all of my serious carts are or have been moving coils. Listen to any good system and you’ll hear it, but it creates that age-old equipment problem of wanting to spend more and more money! Do not forget or think you can sidestep needing an altogether better playback chain to get the most out of a low-output MC cart.
No Cheap Solutions
A classic rookie error involves listening to a good low-output MC cart on a phono preamp that isn’t good enough to extract the best out of these designs, and then deciding that there is no real difference. You’ll never hear what a good low-output MC cart can do because of the limited resolution of the phono preamp. The best solution is a better preamp and/or high-quality step-up transformer or premium active gain stage like the Accuphase AD-290, in my Accuphase C-290 preamp.
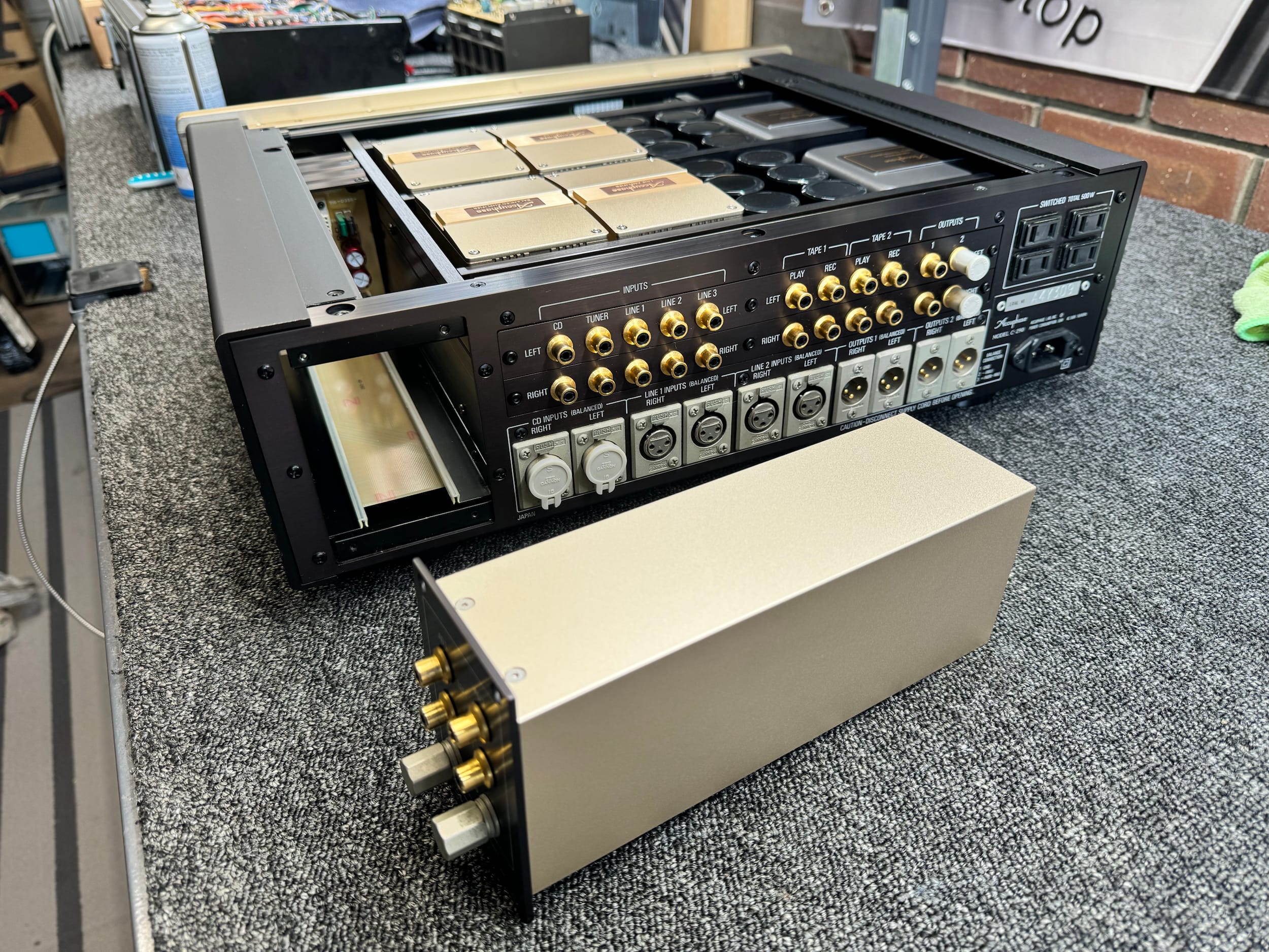
Mike, how do you feel about people seeking your advice but taking business elsewhere?
It happens and as long as they are OK with what it means down the track, I am OK with it.
Folks who’ve sought my advice and then used a corner-cutter repairer or bought something I’ve recommended elsewhere when they could have purchased it from me usually reach a point where they realise: “Geez, that Liquid Mike dude is the only one who can help me, I need to talk to him again!” At this point, they discover that this option is no longer available.
Mike, I bought a vintage Pioneer turntable you recommended, and bought the cartridge and headshell you recommended elsewhere. Can you tell me how to set it all up..?
No, but if you’d like to book your deck with us, I’d be glad to set everything up perfectly for you!
Trust
A lot of hard work has gone into building our trusted reputation and this half-million-word resource and because of it, we’ve had well over two million views here. People worldwide seek out and trust our advice. When you support independent, specialist small businesses like Liquid Audio, you’re supporting people doing the hard work to create unique resources like this one.
Online discounters ride on that wave of knowledge and interest, yet offer nothing other than products they buy in bulk and know nothing about. Corner-cutter copycat repairers steal ideas and then pretend they came up with them. Nothing original or good about any of that, unfortunately.
Mike I read your article about repairing xyz. I don’t want to bring my equipment to you but can you tell me what parts you used and where to get them..?
I have no interest in assisting someone who thinks asking this is reasonable.
Small = Better!
If you enjoy this website, if you’ve found inspiration here or if I’ve taught you something, you can say thanks by shouting me a drink using the donate button in the footer. Better still, grab some advice and support us by giving us your business and engaging us to work on some equipment for you.
By utilising small specialist businesses, you’ll be building a relationship with someone who rolls up their sleeves, contributes, educates, and helps, rather than just selling boxes and cashing in on other people’s hard work.
What’s the best moving coil phono preamplifier?
Either a good step-up transformer or an exceptional active gain stage.
There is no one best phono preamplifier, but almost nothing does a better job of taking extraordinarily small signals from a moving coil cartridge and amplifying them than a top-notch step-up transformer or absolutely first class active gain stage.
A Perfect Match
Technically there’s a bit to know, but step-up transformers are great because they are completely passive, require no power and have no electronic or moving parts to degrade sonics or add noise. They match the impedance of the cartridge to the input impedance of the next stage almost perfectly. They can also be chosen to provide a precise level of gain to suit the cartridge and following electronics.
These virtues combine to reveal a level of micro-dynamic detail and resolution you may have thought didn’t exist until auditioning a good step-up transformer in a high-resolution system. When I got my first transformer, a Fidelity Research FRT-3, in 2005, I was amazed.
Moving to an end-game Fidelity Research XF-1 after some very good advice from a friend was the game changer for me, and I’ve used, recommended and supplied many transformers since.
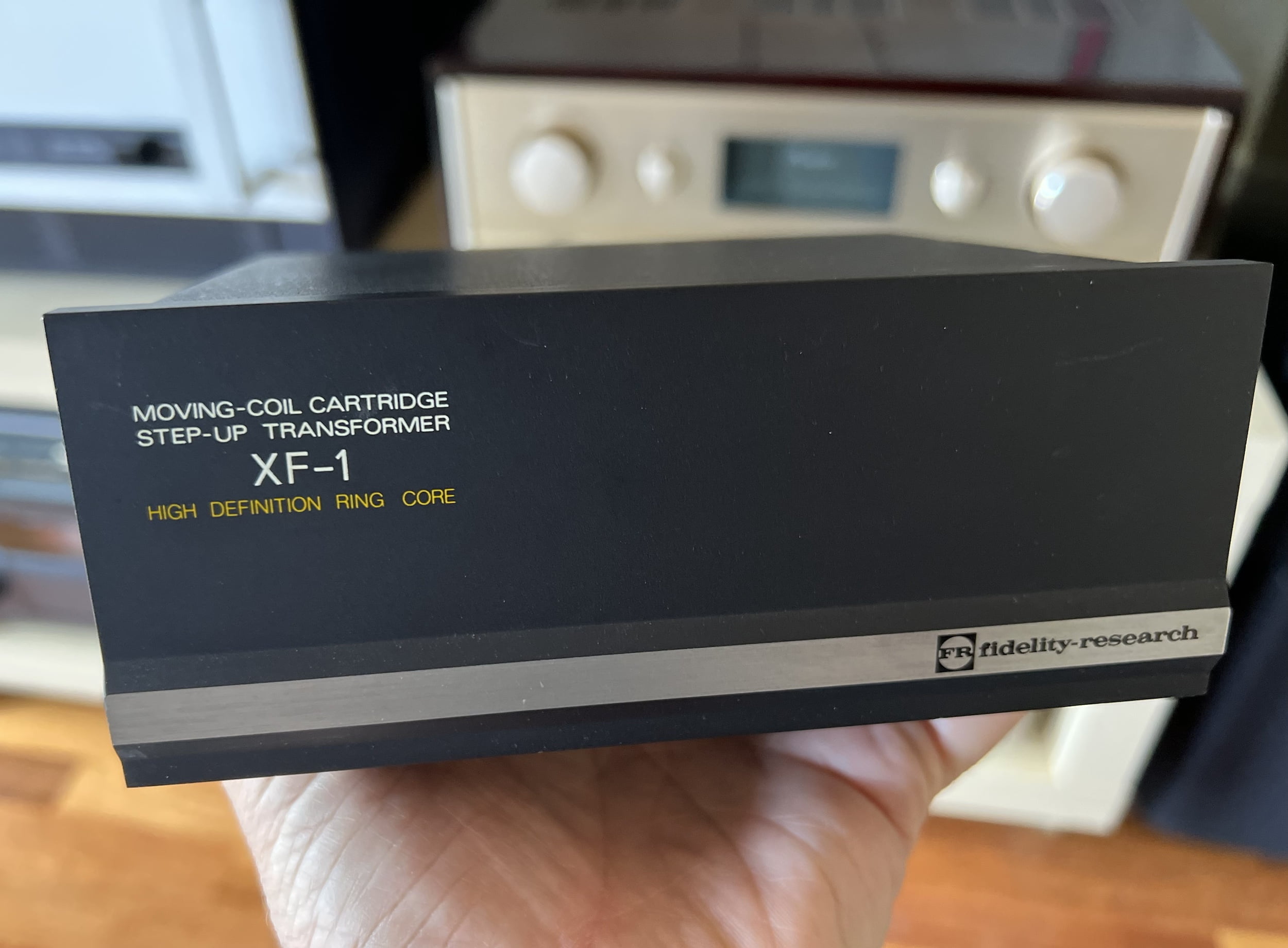
Some of the best phono preamplifiers, such as the Cayin Phono 1 I owned for a while, use transformers for their moving coil gain stages because they offer the best performance and lowest noise for sensible money.
Alternatives
Whilst good step-up transformers are ideal for most people in most cases, there are a few cases where alternatives should be considered. If you have or have access to an ‘S-tier’ all-active phono preamp, it’s worth comparing it to the best transformers.
A couple of years ago I acquired an S-tier Accuphase preamplifier containing a phono preamplifier so good it surpasses my various step-up transformers in terms of performance. Then I sold it and purchased an even better Accuphase preamp and phono preamp combo! Yes, I have a problem, but then don’t most of us?!
Mind you, my current Accuphase preamps cost as much as a car when new and many thousands of dollars even now, some 30 years later. I had to find and import them and there were many risks and costs involved, making this approach just too hard for most people, which I understand.
That’s why in many systems, and for many people, a really good step-up transformer is a great option, especially for those people who already own a good MM phono pre. But, if you can afford an Accuphase C-47 phono preamplifier, or an Accuphase C-280V or C-290 / AD-290 for example, this will be the very best option.
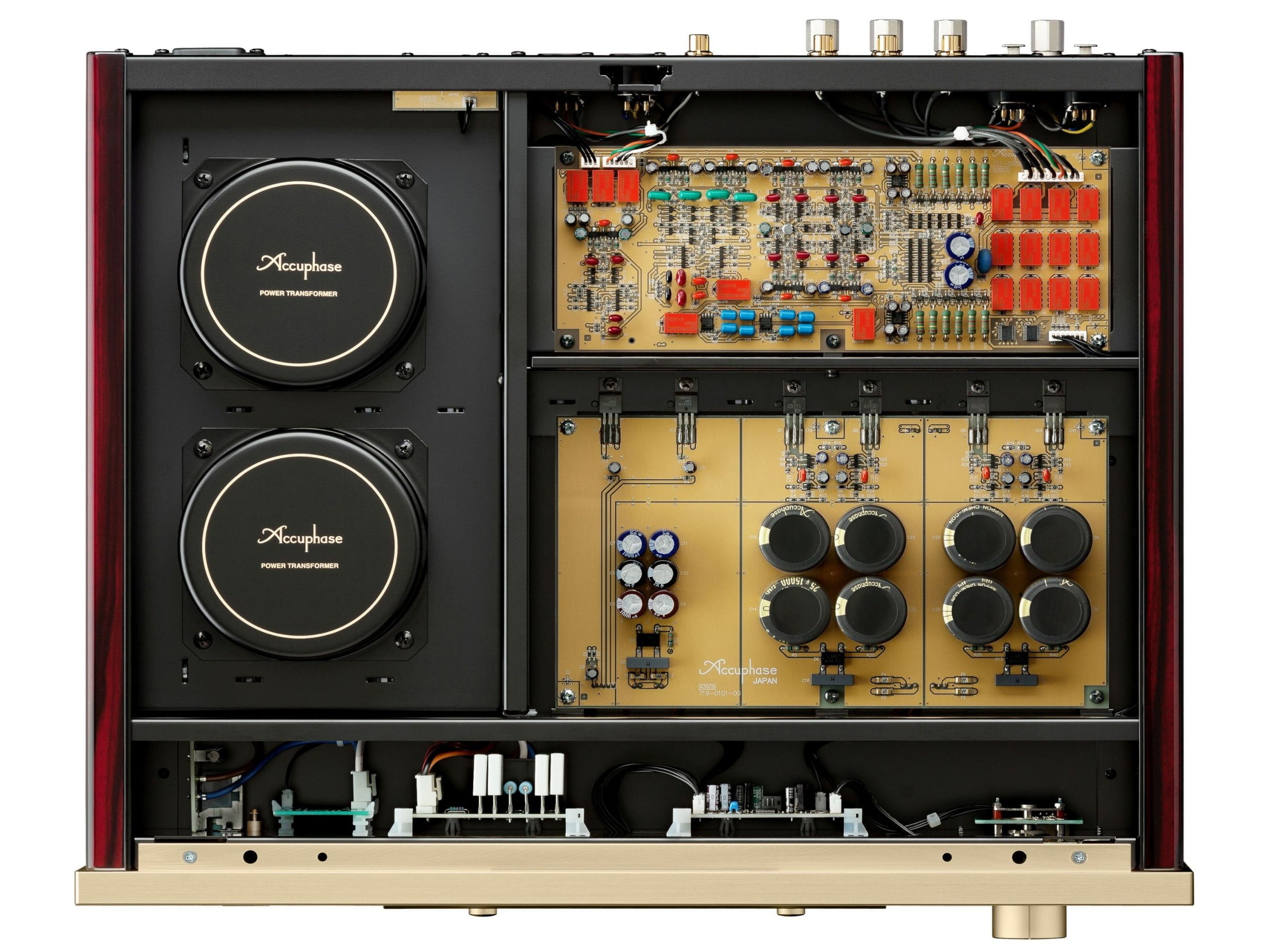
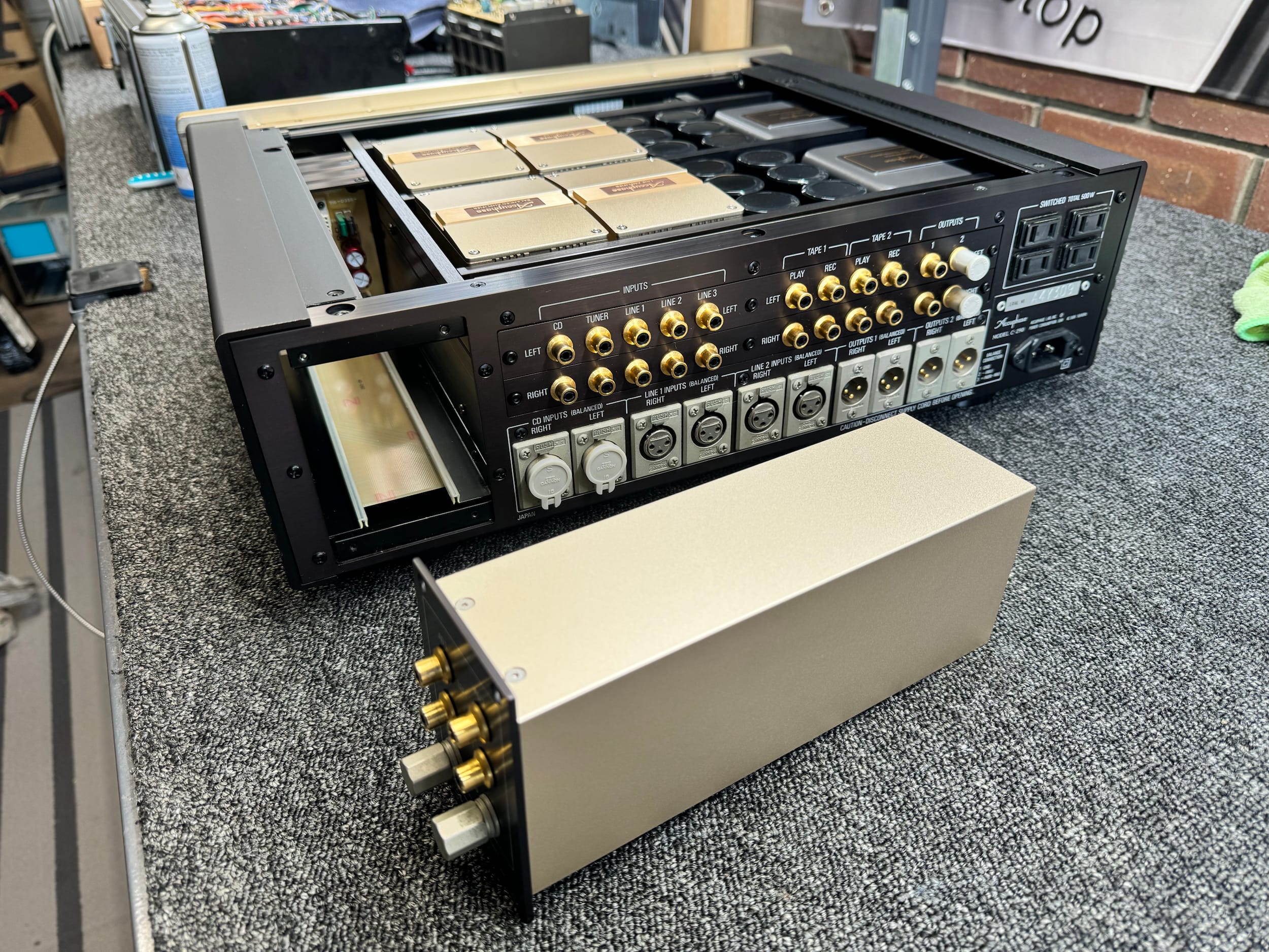
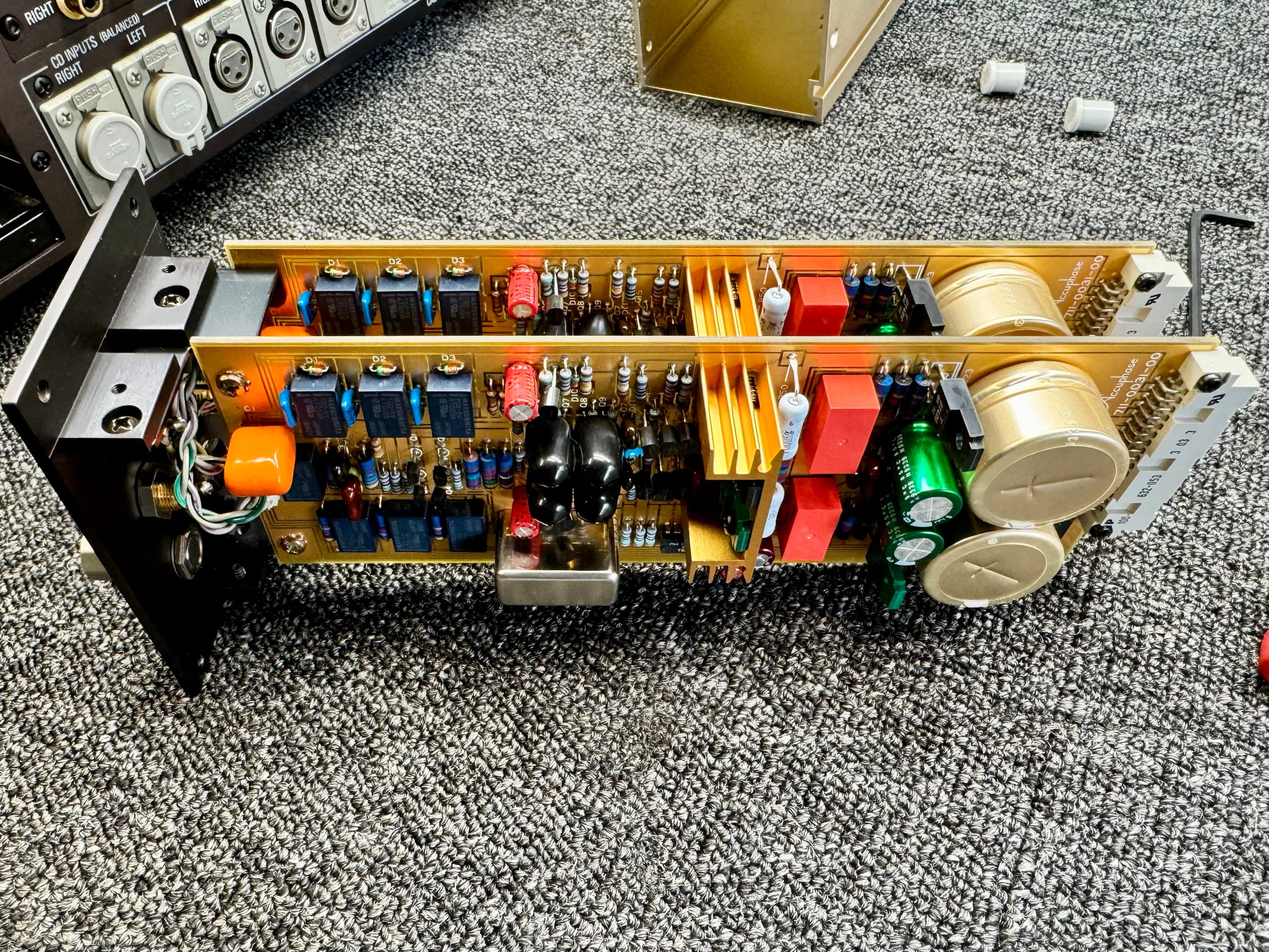
Knowledge
Deep knowledge and hands-on experience with step-up transformers and top-tier active phono preamps is scarce, something of a lost art or one that I’ve found was never acquired in the first place. Most people have never even seen a step-up transformer, let alone own several of them.
How many can say they’ve owned a Luxman C-03, Perreaux SM-2, Cayin Phono 1, Accuphase C-202, C-280V, C-290, AD-290, and Fidelity Research XF-1 L and XF-1M, Luxman PD-350 and Kenwood L-07D for example? I don’t know anyone else with this range of gear and I’m including friends and colleagues.
Retailers are generally only concerned with new gear they are selling, much of which is very ordinary. These days, many discover the almost mythic status of older equipment through sources like this website. I consult with customers via our advisory service. The customer who purchased this beautiful Ortofon ST-70 step-up transformer from Liquid Audio borrowed one of my transformers first.
Transformer Considerations
The pros:
- Lowest noise when partnered with low-noise MM phono preamp
- Exceptional resolution, micro-dynamic detail retrieval and relaxed presentation
- No parts to wear out, near 100% reliability, forever
The cons:
- Good new transformers are expensive, many of the best transformers are from the 1970s and 1980s
- They require careful matching and are generally only suited to a particular narrow range of cartridge impedance
- Needs a really good MM phono preamp, adding to the cost
Active Phono Preamp Considerations
The pros:
- Potentially the very best performance of all, but only at the real high-end
- The best options have great matching capabilities to suit a range of carts
The cons:
- The most expensive for the level of performance that matches or exceeds good transformers
- Electronics can and do fail, active preamps are not as reliable and will need maintenance
- Affordable (sub $2K) active gain stages tend to sound very ordinary
Do customers ever fail to pay for or collect their equipment?
Very rarely, but that’s just a couple of bad eggs.
Good People
Great customers combined with our high success and satisfaction rates, integrity, professionalism, sensible pricing and clear communication, deliver a non-payment rate of virtually zero for us. Operating ethically actually generates goodwill that typically shields us from would-be non-payers and undesirables. I also carefully filter enquiries and avoid assisting those who I think might be problematic. That said, I’ve had two non-paying customers in a decade, maybe three now given the most recent one in 2024.
Non-Payers
The first was a crooked real estate agent, let’s call him JVS… I repaired his turntable, but he failed to respond to emails about collecting it and my final warning after 12 long months stated that I would sell his turntable to recoup funds if he did not collect and pay for it immediately, no discussion. He suddenly wanted to collect his equipment..!
The collection was a drama, with a crying baby, a screaming wife with strange blue contact lenses and an odd, sweaty man attempting to wiggle out of paying the additional charges he’d accrued over 12 months of abandoning his equipment. Luckily I had witnesses happy to support me if needed. The guy is lucky I didn’t sell his deck after three months and is now on the blacklist.
I have some other very interesting stories about JVS because it turns out it isn’t just me he messed around. I’m sitting on those, for now.
The second non-payer asked me to service and repair his turntable as a high-priority job. I did that for him and had his deck running perfectly again, but he neither responded to attempts to contact him nor thanked me for fixing his turntable. After the mandatory warnings, we sold his turntable for considerably more than he owed. Another completely unnecessary waste of time and energy. Hello Mr John Messina!
The third is a gentleman who asked me to repair and refurb his Mitusbish pre/power amplifiers, to a maximum of $1000. I came in comfortably under that limit but when I sent the invoices he disappeared, ghosting me and has never replied, nearly 6 months on. I’m selling these two absolute classics, so keep an eye out for them in the store.
Hiring me and then leaving me in the lurch isn’t a great way to garner goodwill. I just hope it was worth burning the bridge.
Takeaway
There are some in this world who, no matter how much you try to help them, won’t or perhaps can’t do the right thing. My colleagues and I have a simple policy for dealing with people like this which places them on the aforementioned blacklist. I treat everyone kindly, professionally and respectfully, even the people in the examples above. They will however not be able to utilise our services again, which is their loss of course.
I’m having trouble aligning my cartridge, why does each tool seem to give a different result?
This is a really good question, variations of which I hear a lot. Let’s look at this in a little more detail.
Cartridge alignment is a technical process, but relatively straightforward, once you understand it. That said, cartridge alignment, along with tonearm-cartridge matching, are some of the most misunderstood concepts in hi-fi.
Given that alignment is based on math/physics, there’s not a lot of room for opinion, despite the nonsense you may read on this topic. It simply boils down to understanding geometry and the technical aspects of how to accurately measure and set things up.
I’ve written more about the key parameters involved in cartridge and tonearm set-up, so check that out.
Factory Alignment
Now, to the most important and yet most misunderstood point:
There is only one factory-correct alignment, and that’s one made to factory specifications.
Note: I’m not saying there is only one possible alignment, I’m saying there is only one factory-correct alignment, just like there is only one factory-correct wheel alignment for your car.
This concept must be understood by anyone working with turntables, yet astonishingly, many folks don’t. Why? It’s like anything technical. Very few people properly understand the details. As a former science teacher, it was my job to test people’s understanding of complex technical topics, including writing 3-hour exams!
There are many rabbit holes in the world of turntables. The Dunning-Kruger effect is ever present, yielding the classic: “A little knowledge is a dangerous thing”, “You don’t know what you don’t know”, and the Darwin Awards. There are folks out there who’ll tell you these manufacturer-supplied specifications are “wrong”. I’m interested in the science of hi-fi, and I’d never say I know better than the designers or engineers who created this equipment.
Details
So what is a factory or manufacturer-specified alignment? It’s an alignment:
- Done exactly as the tonearm/turntable manufacturer recommends
- Made to exact, recommended specifications
- Achieved using a manufacturer-supplied alignment tool, overhang gauge, or protractor, or one that accurately replicates the original design and/or measurement capability.
Factory alignment usually involves setting the correct overhang and cartridge offset at one or two null points. This is most often achieved by setting a stylus tip distance with respect to the headshell-arm junction, which is how Denon, Kenwood, Sony, Technics and almost all manufacturers do it. They achieve this by supplying an overhang specification and/or a paper or plastic gauge or protractor that is unique for the arm.
I use manufacturer-specified alignments and tools wherever possible because the design engineers knew what they were doing, and I like to honour those design decisions. In rare cases where the original set-up data and/or tools are not available, I’ll select (or make) an alignment tool appropriate for the job, based on the arm design, its specifications and experience aligning and calibrating thousands of turntables, tonearms and cartridges.
Confusion
Cartridge alignment involves setting the precise geometric and positional relationship of a cartridge in a tonearm. This ensures correct geometry as the stylus traverses the surface of a record. The stylus describes an arc of a precise radius as it moves, calculated to yield the best (or a particular) total area under the curve distortion result.
The factory-prescribed alignment is designed to generate the lowest distortion at a significant place on the record surface, often an outer track, or the inner grooves, where distortion tends to be higher. Change the radius or this arc and/or angle of the cartridge, ie its alignment, not to mention tracking force, anti-skate and VTA, and you will change the result, and how the turntable sounds.
I must mention that most owners shouldn’t be aligning cartridges. This is simply because it’s a technical process that requires some knowledge, tools and experience to complete successfully.
Generic Tools
When a cartridge is correctly factory aligned, it may appear misaligned when checked with any of the multitudes of cartridge protractors and alignment gauges available. If you align a cartridge with a Shure paper alignment gauge, for example, when you check with a factory tool, the alignment will very likely appear wrong.
Why? Because those others are the wrong tools for the job. The simple answer is that each tool delivers a different alignment. Don’t expect five different alignment tools and methods to get you the same alignment because they won’t. None of them may be correct for your deck.
A generic paper gauge “designed for every turntable” (which is technically impossible) cannot render the correct factory-specified alignment for many turntables. Generic tools deliver generic alignments, approximations based on a ‘generic’ tonearm length, unspecified alignment geometry, mounting distance and type of alignment. A factory-supplied template, tool or protractor, on the other hand, is designed to give the precise alignment specified for your deck/arm.
An example some might better understand would be getting a car wheel alignment done using data from the wrong vehicle. This happened to me years ago when I took my car to a supposed wheel alignment specialist who had no idea what they were doing. My car’s wheels were technically ‘aligned’, just to the specifications for a different model vehicle! idiots!
Generic protractors have a role to play in ‘quick and dirty’ alignments and work well in situations they were designed for, but there is no substitute for the correct factory alignment, tools, or a custom-made gauge specified with factory alignment parameters for your deck.
Multiple Alignment Syndrome
There are three common alignments – Baervald, Lofgren and Stevenson alignments – each yielding measurably different total ‘area under the curve’ distortion. Your arm will likely use one of these alignments. These alignments each sound different, some good, some not so good and random owner and retailer-made alignments can sound bad!
Which alignment is correct in your case? The factory alignment is technically the correct alignment, as the designers intended. It is always best set with a factory gauge, protractor or tool, or a precisely calculated and printed arc-type protractor. Other alignments are possible as we’ve discussed, but in my opinion, it’s preferable to stick with the factory-specified alignment.
Now, it’s technically true that one can improve on some alignments, in certain circumstances, but this is tweaker’s territory. Some alignments (Stevenson) are designed to perform best on 45s and on the inner grooves of 12-inch vinyl, where classical music crescendos often appear. Is it worth deviating beyond factory recommendations for most users, though? No.
I’m interested in getting turntables working perfectly for 99% of owners who are happy to go with a manufacturer’s recommendations. Of the 1000+ turntables I’ve worked on over the years, only a handful have been correctly set up. Every turntable leaves Liquid Audio correctly set up, per the manufacturer’s specifications.
Summary
- A cartridge must be correctly aligned for maximum performance
- Correct alignment refers to correct cartridge overhang and offset, azimuth, VTA, tracking force and anti-skate
- The best alignment in most cases is the manufacturer-specified alignment, made with the correct/supplied tools
- You should only change/set cartridge alignment if you understand everything so far and can accurately assess the current alignment and any changes made to it.
Need additional advice? For those needing more specific assistance, we offer an advisory service that provides information tailored specifically to you and your equipment. Better still, book your deck in for proper alignment and calibration.
View our FAQs, and reviews for more. If you appreciate FAQs like this one, you are welcome to shout me a drink using the donate button in the footer.
Do cables make a difference?
Yes, but there is much more to know.
Let’s get this out of the way: good cables always improve system performance. That said, there is more snake oil and pseudoscience in cables than just about any other aspect of hi-fi, and the hi-fi world is already filled with nonsense. You know my thoughts on nonsense, so let’s clear some up.
Audio ‘Jewellery’
One of the problems here is that buyers often have no idea what makes a good cable and many just want what looks cool. Big mistake.
Thicker is not always better. There are some ridiculously thick interconnects out there for example. Interconnects and mains cables 5cm thick aren’t better, they are just silly. They can damage or even break connectors and can cause serious harm to really expensive gear. I’ve repaired the damage caused by some only recently.
Ask the maker of the cable if they know the loading specifications for the RCA connector they want you to attach their cable to. People imagine thicker must mean better, but it just isn’t.
Likewise, prettier is not better and aesthetics have absolutely nothing whatsoever to do with electrical performance. Cable construction is what matters. Poorly made or incorrectly terminated cables can act as antennas and fry amplifiers and speakers.
The kookier and prettier a cable looks and feels, the more likely it is to sell. Add in a few meaningless marketing phrases like ‘super transconductance shield’ and ‘femto conductive polymer’ and combine them with the average shopper’s gullibility and poor grasp of science and you have a guaranteed seller!
It’s no surprise that there are so many ’boutique’ cable manufacturers out there. There’s a TON of money to be made in this segment of the market.
The Truth
So what IS a better cable? BETTER is better. Technically better, higher-quality cable stock, with higher-purity copper and silver conductors, better solder, better insulation, better shielding, fewer metal types, better connectors, and better construction.
Have folks who understand signal transmission put all that together and you have better cables. It’s pretty straightforward. It’s not expensive to make very good cables, hence the proliferation of excellent DIY cables out there.
Check out what’s used in Abbey Road or Air Studios, for example. You’ll find a ton of Canare and Mogami cable in mission-critical applications, and these manufacturers make cable stock for the boutique brands people spend big bucks on. I use Mogami and Accuphase cables in my system.
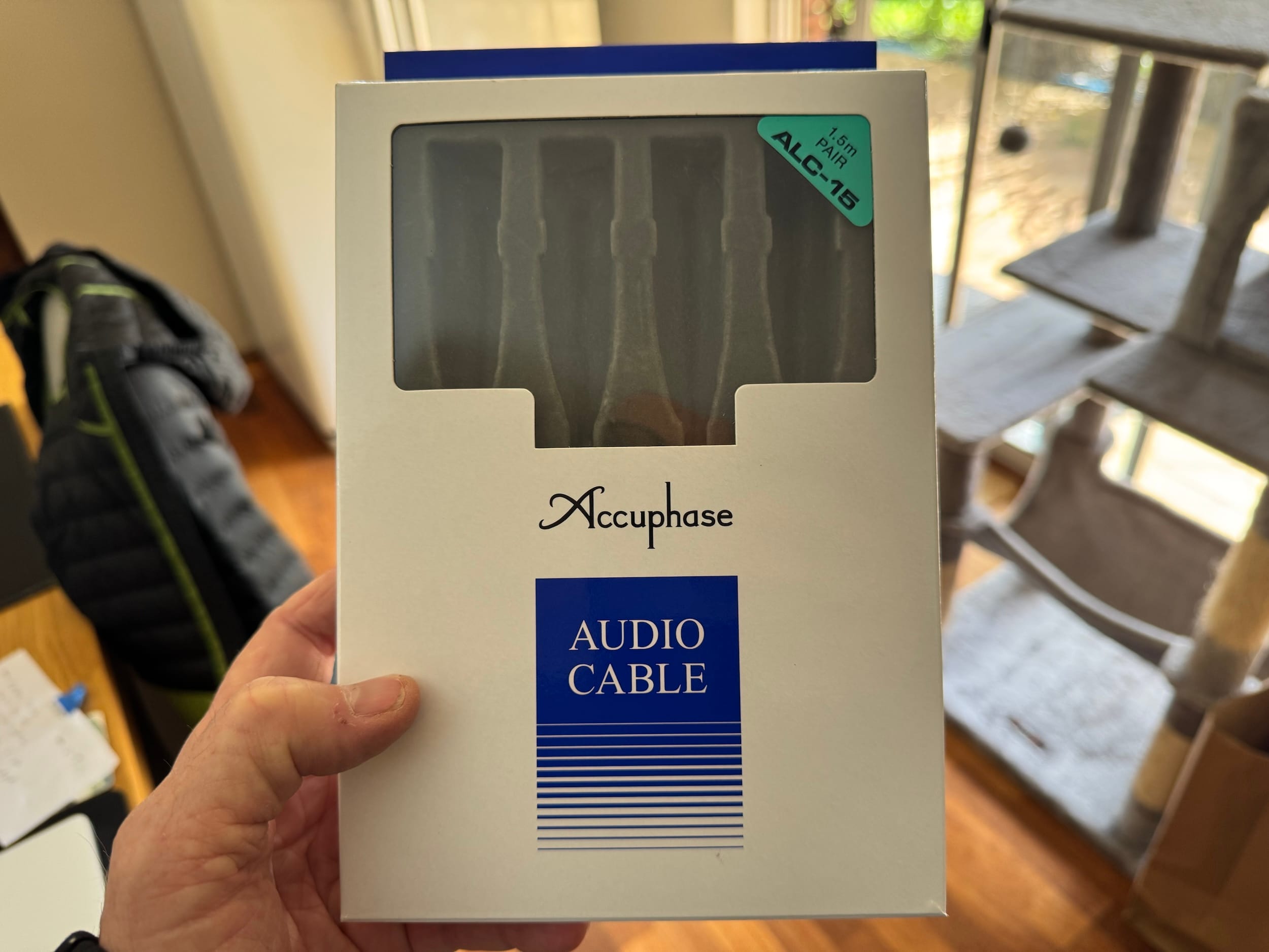
Directionality
Are cables directional? No, there is no directionality in properly designed cables or almost any cables for that matter. If cables were directional they’d act like diodes and that would be harmful to sound, rectifying the signal and introducing massive distortion, so you’d better hope your cables aren’t directional.
Surprised that this isn’t what your favourite hi-fi equipment reviewer, retailer or guru said? Don’t be. Have a look at who advertises in their publications, on their websites and the stock they are selling. That’s called a conflict of interest. Do you see me selling any cables..?
Nordost, one of the great science-based (rather than BS-based) cable manufacturers, states that cables have no directionality. That’s not just about their cables, they’ve stuck their collective necks out to state the truth about all cables.
But Mike, my cables are directional, it says so on the jacket and the salesperson told me they were.
Great, but they aren’t. ‘Directionality’ sells, so most cables are simply labelled as directional. The average salesperson’s understanding of the science here will be limited let’s say, so choose your source of information wisely.
Conclusion
Let’s sum up what makes a good cable:
- Premium conductor materials like high-purity copper or silver
- Premium insulator materials like Teflon and cotton
- Premium connectors, Amphenol, WBT or CMC for example
- Well designed shielding
- Cable symmetry, balanced or pseudo-balanced
- Silver and copper-based solders
- Minimising cable length
- Low cable resistance and capacitance
- Technically informed, properly engineered designs
Be especially wary of gurus selling cables. Choose carefully, from known quality manufacturers, based on good science, not what looks ‘cool’.
Can you sell me a belt for my turntable or an XYZ for my YYZ..?
Certainly, if it visits Liquid Audio for what will likely be much-needed TLC and expert maintenance.
Liquid Audio is not a retailer, so we don’t operate a retail storefront or offer retail parts sales though. Just as you wouldn’t go to your mechanic to buy a set of spark plugs, we don’t offer retail sales of bare service parts.
Liquid Audio encourages professional maintenance to address long overdue, ignored or poorly executed adjustments, calibration and maintenance of equipment like turntables. Many have never been set up correctly and almost all need work, used as they are, decades beyond their intended design life.
We stock thousands of parts to support this mission, but some don’t realise that selling small quantities of low-priced parts to the general public actually costs money for businesses not set up to do it at scale. One dumbfounded customer told me:
I don’t understand why you won’t sell me a belt, are you trying to be difficult?!
The “I don’t know how to install it”, “I chose the wrong part”, “I don’t know what part I need”, “I want advice about installing my part”, “My XYZ still isn’t running right” and “Let’s talk about my XYZ” conversations that accompany retail parts sales are not for me, but I salute all who enjoy such work.
We will, of course, gladly supply and fit the very best parts to your equipment when it comes to us for maintenance. Get in touch via our contact form 🙂
Why don’t all CD players sound the same?
A great question, so let’s discuss it.
Let’s start simply. A musician understands that no two guitars sound the same, even two of the same model. Likewise, two different digital camera models using the same Sony sensor will take different-looking pictures.
I can already hear people screaming “But Mike, these things are built differently!” Correct, just like CD players! There are so many elements contributing to the sound of a CD player that no two different players will sound quite the same. This is true of any piece of hi-fi equipment, and most other things, too.
Ones and Zeros
I think it’s useful to understand what a CD player does. A CD player does two important things: 1) digital data extraction from compact discs, and 2) digital to analog data conversion. Both processes are complex, and both produce data that will vary from one player to another. When you play a CD, what you hear is the sum of many complex electronic and mechanical elements working together.
A common misunderstanding concerning CDs is that:
“It’s digital, it’s all just ones and zeros, so things HAVE to sound the same.”
Whilst CDs indeed contain digital data in the form of ‘ones and zeros’, this statement indicates some missing knowledge in terms of how the data on a compact disc is converted into music you can hear, because you can’t listen to ones and zeros!
In terms of data extraction, CD players produce digital data streams that vary minutely from one player to another. These variances are measurable and occur before the data are converted into an analog waveform we can listen to, so they will impact what we hear.
Even different CDs of the same recordings don’t sound quite the same in some cases, a story for another FAQ. Likewise, CD transports only extract the digital data from the disc, yet they sound different, something which fascinates me.
Digital to Analog Conversion
Once we have the data stream from the disc, a complex series of signal buffering, decoding and processing steps have to occur before you can hear music from a CD. These steps and the digital-to-analog conversion contribute even more to the nature of the sound a CD player produces.
Converting digital data into analog waveforms can be done in many different ways, using different techniques, different chipsets, FPGAs, resistors and so on. Then there are output buffer amplifiers that deliver the signal to the next equipment in the chain. These lower the source impedance of the player, allowing the player to deliver a more robust signal, unaffected by cables and the load impedance presented by the following equipment.
The Devil is in the Detail… Again!
To summarise, to retrieve sound from a compact disc, data has to be read from the disc, error-corrected, filtered and anti-aliased, converted from a digital bitstream into an analog signal we can listen to, amplified and buffered for sending it elsewhere.
There is no one way to do all this and there are hundreds or even thousands of components between the disc and your ears, all contributing to the sound in subtle ways! Even Op-amps contain dozens of components and there may be several different op-amps in the signal path!
All of these steps and the different ways they can be achieved, variances in parts, circuit ‘luxury’, chipset types, connectors, wiring and more contribute to the distinct sonic differences between CD players. As with all things technical, there is much more to know than most realise and this is how misunderstandings originate. Do you seriously imagine that two different CD players ever would sound the same, knowing all this?!
It is worth noting however that CD players have less immediately obvious differences than some other sources and that it takes some experience to be able to describe these differences, at least initially.
An Example
My Accuphase DP-90 and DC-91 represent one the most expensive and predictably best-sounding series of designs/parts/decisions in terms of CD playback. This pair allows beautiful audio to be extracted from digital signals, the best I’ve heard. This cost as much as a good car when it was new and still cost as much as a decent secondhand car now!
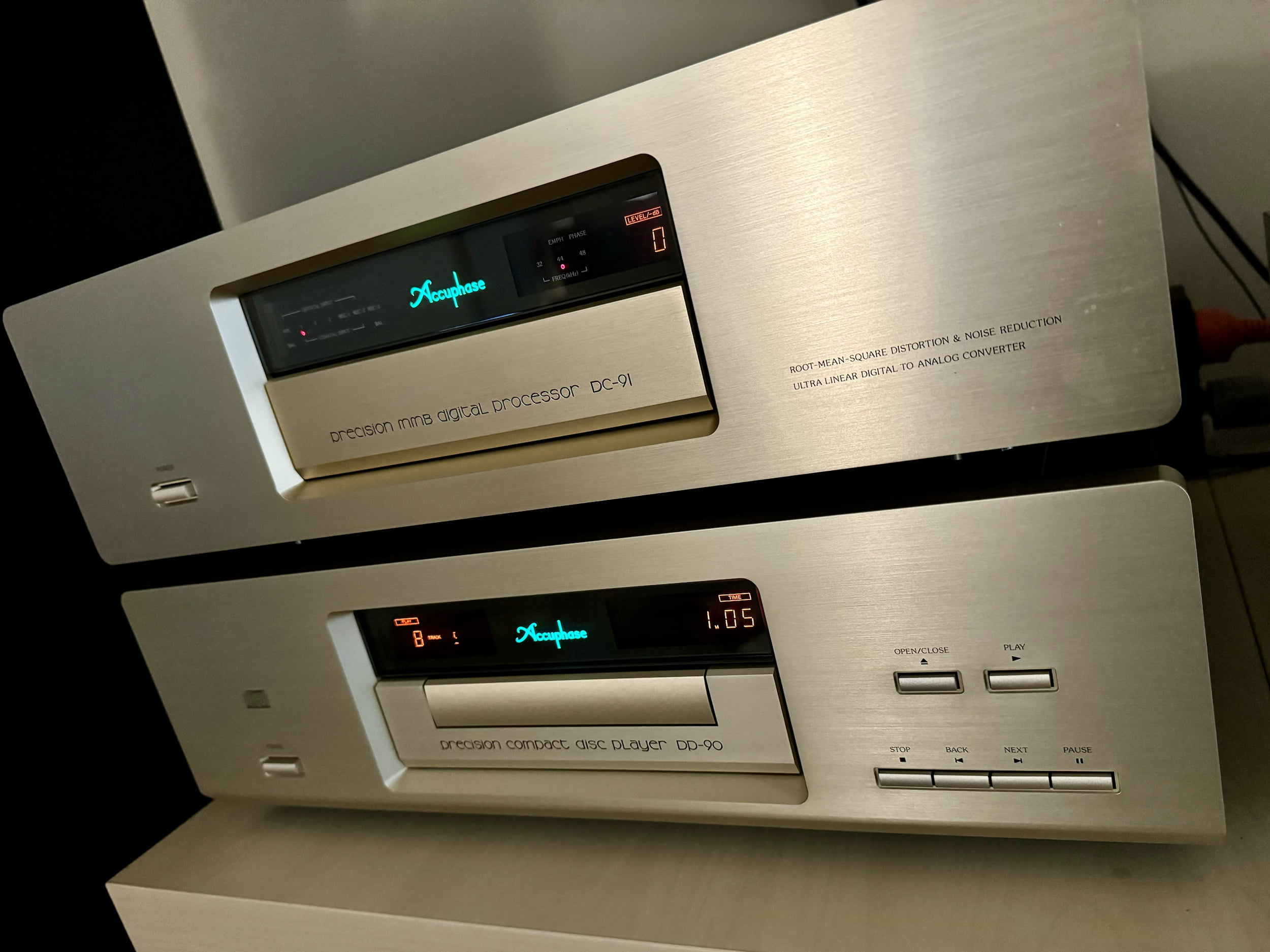
Even CD transports that lack a DAC can sound dramatically different from one another. I’ve written an entire FAQ about this topic!
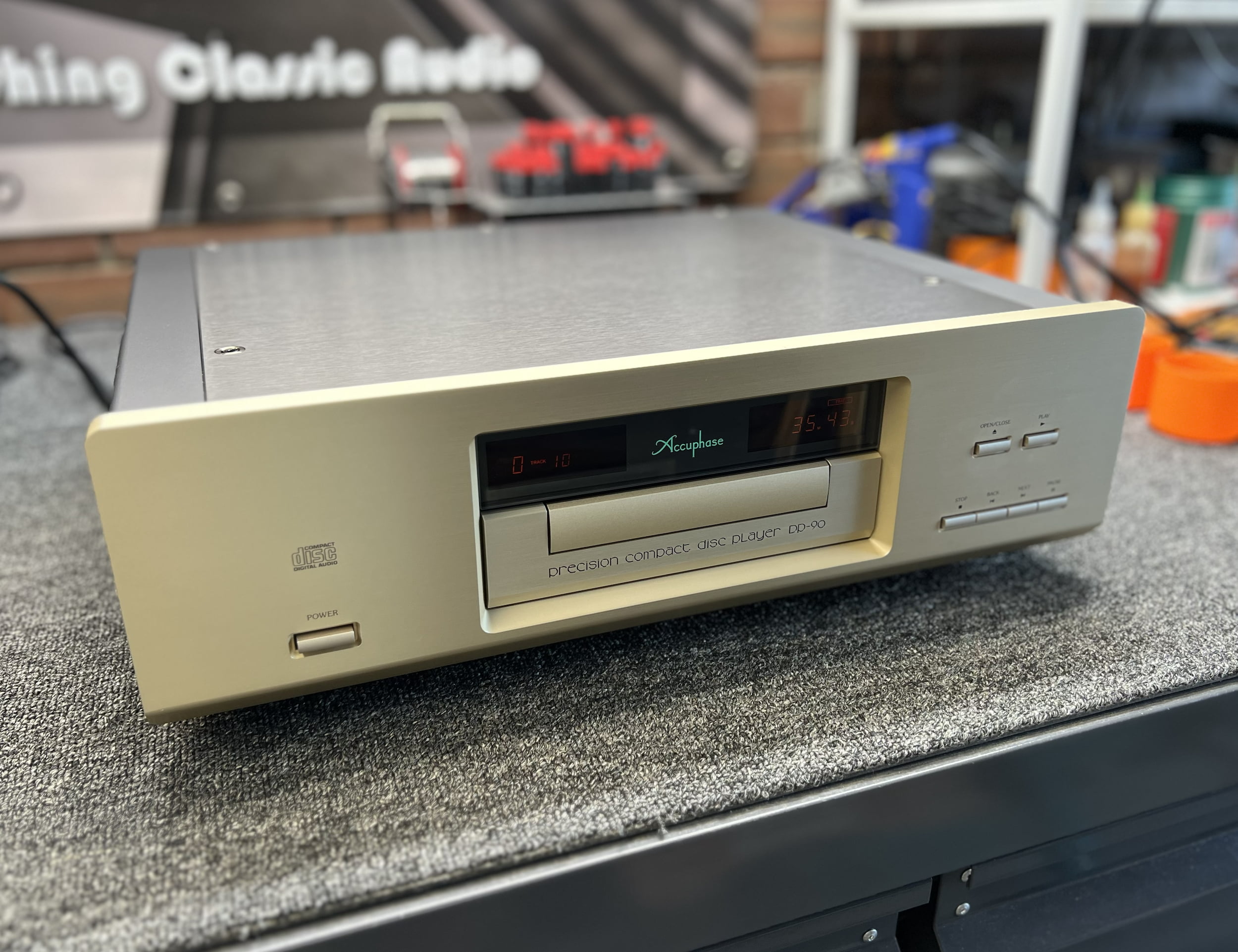
The Sum of the Parts
Each of these elements contributes to the sound of a CD player, along with others I’ve probably forgotten:
- The CD mechanism or mech, spindle motor and laser
- The hardware carrying the RF signal – shielded coax or unshielded wire, connectors, termination impedances and reflections
- DAC type and design – R2R/multibit delta-sigma/chip/discrete
- Analog and digital filter type and design – HDCD/FPGA/DSP/none
- Device firmware running the digital filters, PICs, FPGAs etc
- Inter-stage analog amplifiers and buffers, op-amps
- The all-important output buffer – discrete/op-amp/class-A/tube/transistor/transformer/balanced/singled-ended etc
- Power supply – linear/SMPS, filtering details, regulators, wiring
- Clock – frequency/PPM precision/drift/stability
- General layout, board design, wiring, shielding, parts quality
- Condition of the unit, laser power output/health, general state of service
- Vibration isolation differences between players and isolation hardware
CD players are complex mixed-signal (digital and analog) hardware devices. Unsurprisingly, they sound different, just as turntables sound different.
Is it OK to play CDs in my DVD or BluRay player?
Yes, but your CDs won’t sound as good as they can when played on dedicated CD hardware.
For the very best CD playback, you’ll need a dedicated Redbook CD player, or even better – a transport and DAC. In almost all cases, CDs will sound better played on good dedicated CD hardware than when played on even so-called ‘premium’ audio-visual or video hardware.
I’ve found they also usually sound better than files streamed at 16-bit / 44.1kHz and sometimes even better than high-res streamed files, where the player/DAC has the necessary resolution.
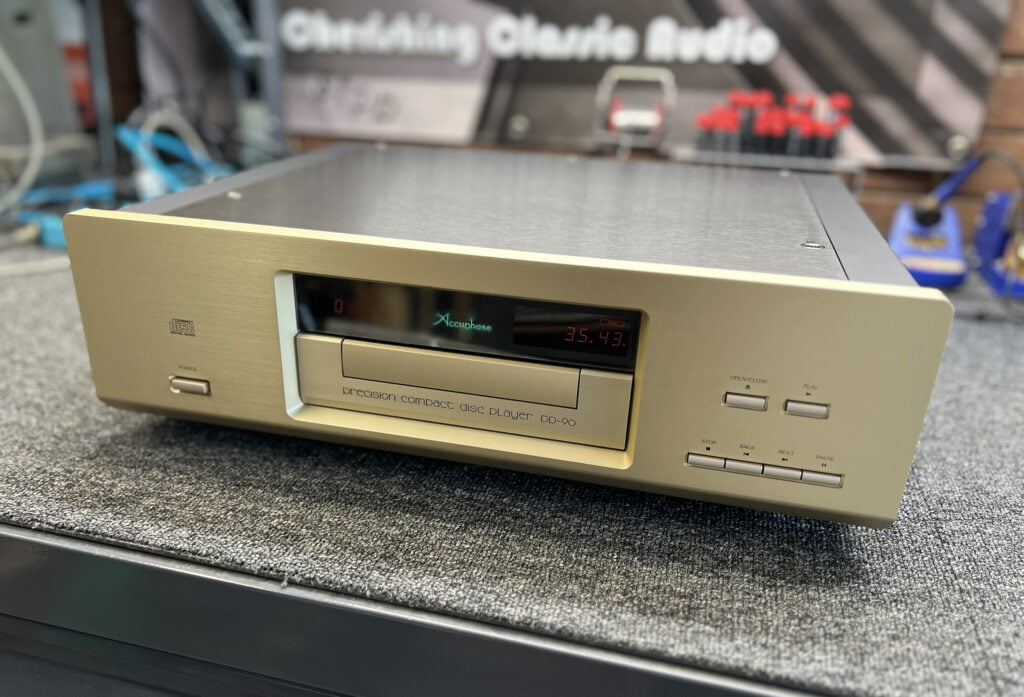
Wondering if this is all just audiophile nonsense? That’s healthy scepticism and I respect you for it because these questions must be asked. You should know that I have a science background and was a science educator for many years. I have absolutely zero interest in audio nonsense. I only pass on factual information I know to be correct, based on first-hand personal experience and knowledge.
Frame of Reference
“Mike, I’ve heard that all CD players and DVD players sound the same.”
Many people
I hear this sort of thing often and it comes generally from folks lacking broader experience with a range of better gear. There are BIG differences between CD players, so much so that I have a whole separate FAQ on this. CD players and disc players in general don’t sound the same at all, except in the very broadest sense. Heck, even the same CDs sometimes don’t sound the same!
Appreciating this comes down to experience and you can get that by listening to various machines in high-resolution systems. Understanding why they sound different requires a little technical knowledge though. Comments like “All CD players sound the same” generally stem from a lack of experience and/or understanding.
Experience
If you’ve never heard a great CD player in a high-resolution system, you need to. CDs sound ‘OK’ when played on cheap DVD players, but in a high-resolution system, the sonic differences between a good dedicated CD player and a cheap DVD player are night and day.
If you are listening through a Bluetooth speaker or Sonos, then of course, everything will sound pretty much the same, and bad, due to the resolution limitations of the system. Good hi-fi is all about clean, wide windows – i.e. high resolution. You can only get high-resolution from high-resolution equipment. Bluetooth, Bose and Sonos ain’t it, cheap plastic ain’t it and DVD players ain’t it either.
It’s a bit like beer, wine and coffee. All beer, wine and coffee taste the same when you’re 12, but are they the same? Of course not. As our appreciation and experience grow, we come to learn that no two beers, coffees or wines taste the same. This appreciation applies to audio in the same way it does to guitars, which don’t sound the same either BTW!
Differences
So, why are CD players better than DVD players for playing CDs? Briefly:
- DVD and Blu-ray players are generally not built with audio in mind. They are made almost entirely of plastic, built to last a few years only and use the cheapest, lowest-grade parts. If you don’t already know that cheap gear sounds cheap, you do now. People buying video disc players are generally not hi-fi enthusiasts nor as picky and manufacturers don’t waste money putting the good stuff inside machines they need to sell cheaply.
- Extracting and decoding the video signals from a DVD uses different technical solutions and higher processing speeds and frequencies than Redbook CD data. Each system needs to be optimised for its role and, from experience, no DVD or Blu-ray player I’ve heard sounds as good as a really good CD player.
Even the famously over-hyped Oppo BluRay players don’t hold a candle to good dedicated CD players. Yes, they are better than the cheap DVD and BluRay players that many buyers who raved about them were migrating from, but they’re not at the level of an excellent Redbook CD player or transport and DAC. How do I know..? I tested one in my system for several months. I was very disappointed, but I’m fussy and that’s what I’m talking about.
Find Out For Yourself!
You don’t need to take my word for it, just ask anyone who’s compared CD players, DVD and BluRay players and DACs in high-resolution hi-fi systems. No one who has will tell you that DVD players are the best way to play CDs. Better still, visit a specialist hi-fi store and ask to hear two different CD players and a DVD or BluRay player in a high-resolution system. Let me know if you don’t hear the differences between them!
Do you recommend new speaker terminals, RCA connectors and detachable mains cables?
In some cases, yes, and I’m happy to fit them, but people are often surprised to learn that there are usually many other considerations.
Many of these topics are plagued by misinformation and pseudoscience. Certain “improvements” are not actually improvements at all, and in some cases are retrograde moves. No retailer selling cables will tell you this of course, even if they actually knew or understood why.
Audio Jewellery
I’m interested in getting customer equipment sounding as good as it can, within their budget. I also encourage keeping equipment original, because that retains value. People are drawn to fancy cables and connectors, but there are almost always lower-hanging fruit that should be knocked off first. My question is:
Do you want fancy connectors or the best-sounding and running equipment with the highest resale value?
In other words, if you came to me and said, “Mike, I want you to spend two hours improving my amplifier,” I can tell you that those two hours would not be spent upgrading connectors in most cases. There will generally be much better ways to spend those two hours, and the improvements from this informed work will be far more significant.
Good Connections
Much of what people think they know about connectors is wrong because it’s based on marketing rather than science, so let’s clarify a few things. Good connections are critically important; good connectors might help us get there.
For example, did you know the best connections are no connections at all? Failing that, hardwired connections are always better, in terms of sonics. One of the best ways to improve an amplifier, for example, is to hard-wire a really good power cable to it.
The best connector is NO CONNECTOR. This can be inconvenient, though, so we need to be practical.
But Mike, this is sacrilege! Everyone selling cables and who’s spent a fortune on cables tells me that fancy detachable cables are the way to go!
I’m presenting well-understood basic science here. It doesn’t suit the retail narrative, but don’t shoot the messenger for that. Connectors are convenient and sometimes essential. Just understand that the fewer connections, the better.
Did you also know that the humble RCA connector is a really poor connector in terms of technical performance? There are many other connector types such as BNC, Camac, Cannon and others that perform measurably better.
I can treat connectors with a product that lowers contact resistance, and you’ll hear the difference that makes. I can replace speaker terminals, but it may be better to simply change cable-end connectors. If your speaker connectors are broken or awful, then yes, it makes sense to change them.
There are many possibilities that don’t make accessory manufacturers rich. Get in touch if you’d like to learn more.
Do Cables Make a Difference?
Yes, good cables are game changers, and I’ve written an FAQ specifically about this. Upgrading standard IEC inlets is a really sensible improvement. I can improve an existing IEC inlet with a premium hospital-grade filtered Swiss-made inlet module. They aren’t cheap but you can hear the difference they make. I can also bypass IEC inlets and hard-wire in some heavy-duty cables.
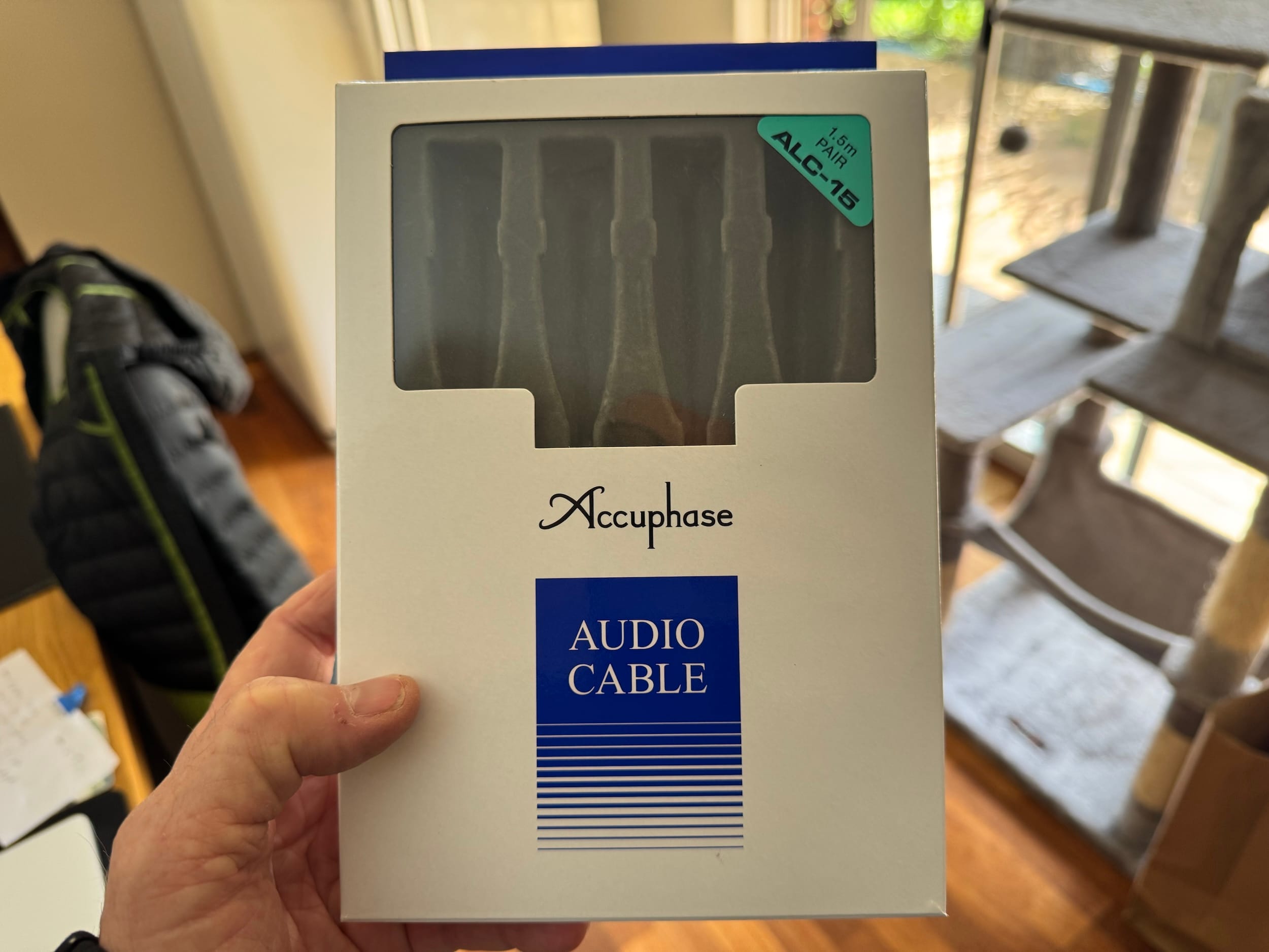
Some of the best-value and highest-performance cables are those sold as cable stock by cable manufacturers like Canare and Mogami, and then rebadged by boutique manufacturers. The best cables I’ve used in terms of build and sound quality are Accuphase cables, like the ALC-15 balanced cable, above.
Fancy-looking detachable power cables make retailers a ton of money and the biggest markups of all are on cables. If you want fancy detachable cables, no problem, just understand what you are spending money on.
Mini FAQ!
Yes, replacing bad RCA connectors can be very worthwhile when it improves connections. We often upgrade RCA connectors.
No, adding a heavy-duty or very fancy mains cable to a turntable will not make a difference. It simply can’t, because of that wonderful thing, physics. If you want to learn why not, ask me. Changing the signal cable can though.
No, using crazy-thick RCA cables is not a good idea. Want heavy-duty connectors and better sound? Go balanced. All the best gear is balanced and there are many technical reasons why it’s the better way to transmit signals.
How do I arrange a consult?
Simply choose the consult length below and click ‘buy now’.
Alternatively, you can do the same thing over on our contact page, in our advisory service information area.
Once you’ve paid, fill out the contact form and let me know what you want to discuss. I’m happy to chat by video or voice call and, if you are local, you can also visit for a consult with me in the Liquid Audio workshop. If we cannot assist you, we’ll issue an immediate refund. Zero worries, zero hassles. We’re here to help. If you like to find out whether we can assist you with a particular topic though before buying a consult, no problem, let me know.
What are your thoughts on buying equipment in poor condition?
I suggest avoiding equipment in poor condition, as a general rule.
My recommendation is always to buy the very best example of the equipment you are looking for, in the best condition, with the best service history, and a recent inspection and condition assessment, if possible.
Everyone wants a bargain, and buying equipment in poor condition, cheaply, is often perceived as such. However, there is no escaping the fact that equipment in poor condition tends to be less reliable and less repairable than similar gear in good condition. Equipment in poor condition also doesn’t hold value as well and is less collectible.
Poor condition outside almost always means poor condition inside, and poor maintenance in general. You don’t want sensitive electronics that have not been cared for. Corrosion is a good example. Once corrosion goes through equipment, it can cause endless problems.
Likewise, poorly cared-for gear is usually poorly serviced and maintained, even poorly repaired. Despite the best efforts of skilled repairers later, these issues are usually not reversible.
Should I clean my turntable with a cloth..?
No, not without taking a few precautions!
If you quite enjoy your current cartridge, let me give you a little bit of advice, from one long-time lover of all things vinyl to another.
Nothing ruins your day faster than an absent-minded dust down of your turntable with a soft microfibre cloth, that runs a little too close to your stylus. Please DON’T ask me how I know.
The worst thing is I know better, and I’ve lost count of how many customers have done something similar. Each time, it causes great pain and anguish, especially when something like an Ortofon MC-A90 falls victim…
To answer your question, I only suggest cleaning your turntable with a soft cloth with the headshell and cartridge removed.
You’re always full, can you recommend other repairers in Perth?
I’d be happy to.
Keep in mind that our booking status table, on the contact page, has booking statuses for different job types and suggested checkback dates to make things as easy as possible for potential customers. That said, if we’re fully booked and you can’t wait for a booking, get in touch.
If we can’t fit you in now or soon, I will recommend a colleague I trust, who also cares about the quality of their work and can perhaps assist in a more timely fashion. This is much better than having your equipment improperly repaired or potentially ruined.
If I don’t recommend someone, it’s important to understand why not. I will never recommend anyone I know to do substandard, damaging or dangerous work. There are quite a few who do, I hope you do not use one of them.
Are dual cassette decks worth repairing?
Often they are not, from an economic standpoint anyway.
Double Trouble
Dual or double-cassette decks have two cassette bays instead of the one more commonly found with better cassette decks. It’s important to note that dual cassette decks were the cheapest cassette decks of their time. Long-term usage and serviceability were not high on the designers’ list of priorities with these low-cost machines.
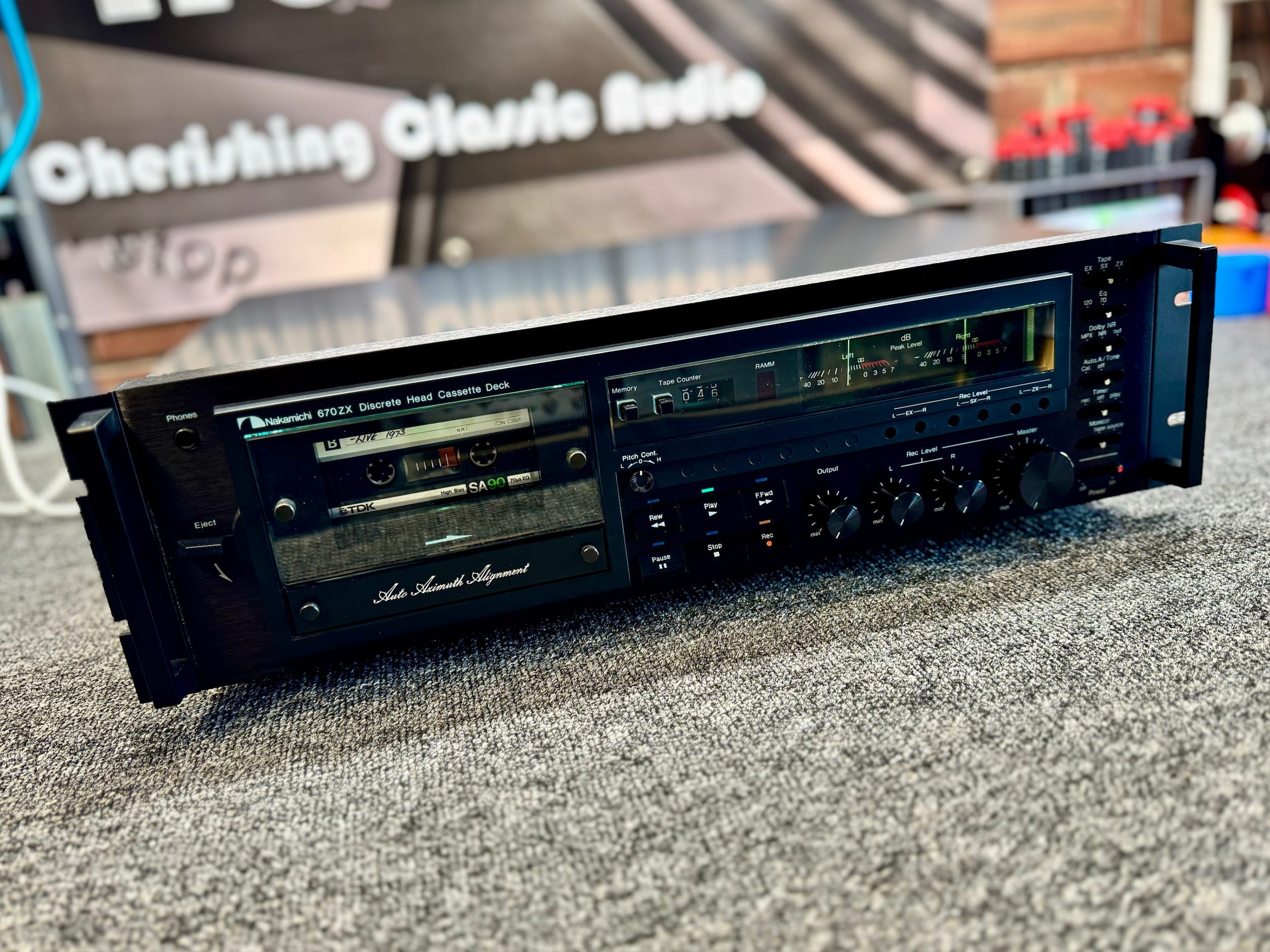
If you haven’t read any of my in-depth cassette deck maintenance articles, this can be some of the most labour-intensive work in hi-fi. Properly servicing one deck can be involved, so servicing two usually cheaply made mechanisms is generally work that needs to be done, yet isn’t economically viable/sensible to do for the level of equipment.
The doubling of mechanisms in dual cassette decks means double the heads, belts, capstans, and pinch-rollers. This doubles the cleaning and doubles the disassembly and reassembly. Doubling the already time-consuming workload usually means more work than these decks are worth. Too much doubling here and for these reasons, I generally avoid repair work on dual cassette machines. I DO offer light service work on them though.
Viability
If both decks in a dual-cassette machine need only light maintenance then this work done may be worthwhile. If both decks need repair in the form of idlers, belt replacement, or other deeper service work though, costs almost immediately exceed the very modest value of even the best dual cassette machines.
I like to keep my customers happy and generating large invoices for equipment worth very little isn’t a great way to achieve that. Most owners simply don’t want to spend hundreds of dollars on what is a low-cost and low-performance dual cassette deck. That said, some people will do this deeper dual cassette deck work and I am happy to recommend someone if it’s important to have yours running and you are OK with potentially high repair costs.
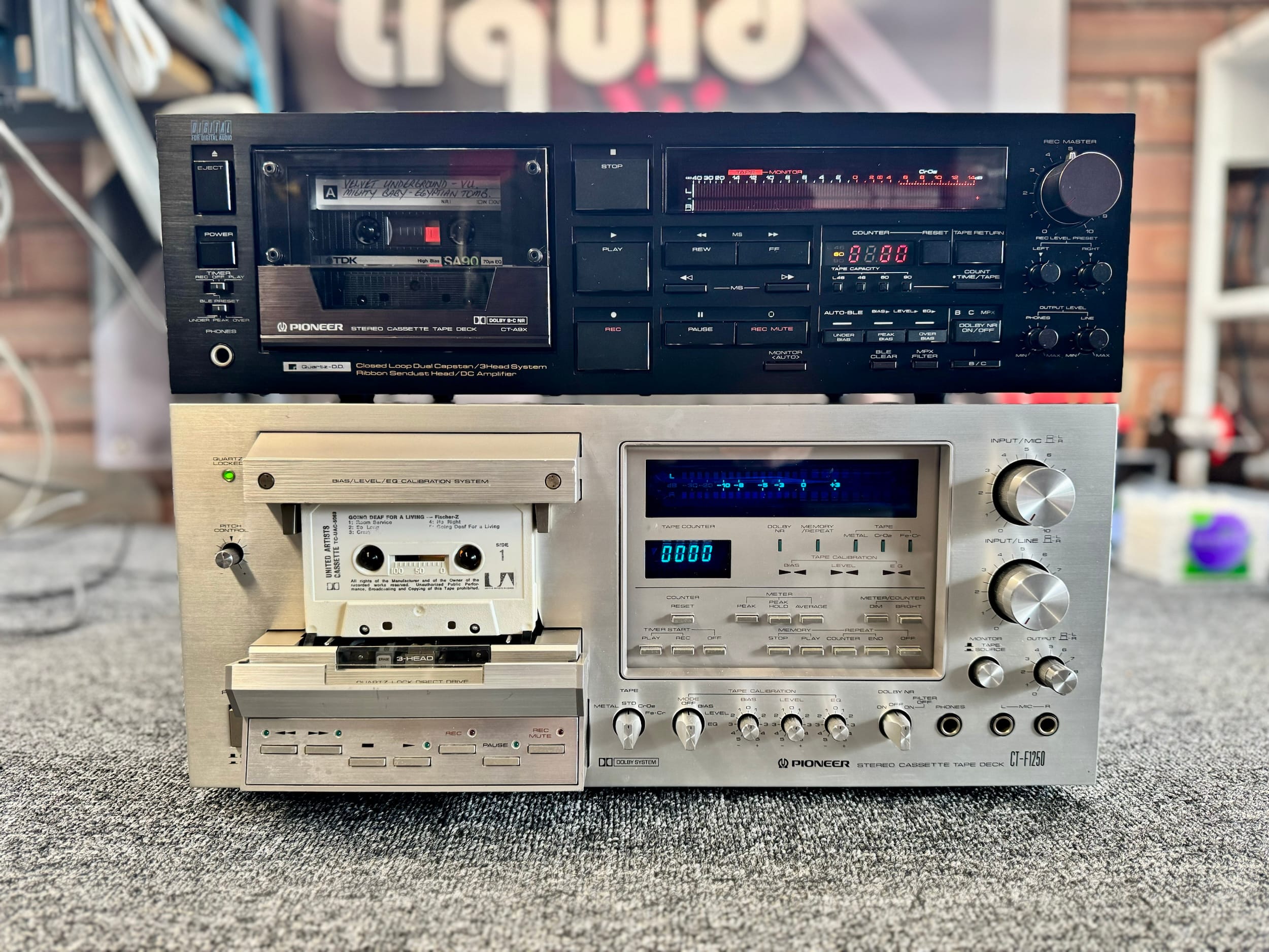
The opposite is true of good single-deck machines and I still work on those, like these two beautiful Pioneers, from my collection. Single-deck machines are built better, perform better and are generally nicer to work on. Decks like this are almost always worth servicing and repairing, but a whole day is sometimes needed for mechanical work on complex decks like these.
Do you repair equipment for hi-fi stores?
Yes, we do.
Some of Perth’s most highly regarded hi-fi stores direct customers to us and use Liquid Audio for their customers’ service and repair work. As an independent repairer, a large portion of our work is a result of direct customer engagement, but helping local businesses is very satisfying and something I’m proud to be able to do.
We’ve been approached several times with offers to be an official repair agent for some very well-known brands, ie an authorised repairer. I have declined these offers to this point though, as I want to remain truly independent and unaffiliated with any brand in particular.
Should I buy a cheap turntable belt on eBay?
If you are going to get a belt, a critically important part of how your turntable runs, at least get a good one.
How will you know if you’re getting a cheap turntable drive belt or a quality belt of the correct size or not? Well, if it’s very cheap, that probably answers your question!
To some, all rubber drive belts look the same. But really, all tyres kinda look the same don’t they, yet they are not. There are technical, sizing and quality aspects to consider that vary from belt to belt, even when belts are specified as being ‘correct’ for their intended purpose.
Fit
I’ve seen many eBay and Alibaba belts. Customers buy them thinking they will save a few dollars and sometimes hi-fi stores fit them, only for owners to find their turntables now run fast, slow or noisily. Owners then have to buy another belt of good quality and the correct size. This only wastes time and money.
Belt diameter, width and thickness are critical. Excessive tightness from belts that are too small is a common problem. Incorrectly sized belts place excessive force on the drive pulley and motor bearings, causing noise, poor running and excessive wear.
Material
Belt material and manufacture are also important. Poorly cut belts cause excessive wow in cassette decks. Poorly joined O-ring belts also cause speed issues. Poor quality belts don’t last either, some lasting only a year, vs up to 10 years for good quality rubber belts. Belts that are too thick or thin will cause your deck to run at the wrong speed. Did you know that?
You can avoid these issues by simply taking your deck to someone who sells premium quality, correctly sized parts that meet OEM specifications. When your belt is being fitted they can also give our deck a health check and perform any other service work or adjustments necessary to make your turntable run at its best.
Which Perth hi-fi retailers do you recommend?
Here are my favourite Perth hi-fi retailers:
Addicted to Audio
Dan is a great guy and knows his stuff, plus this store has some really interesting brands and loads of personal audio gear. In terms of store layout, quality, and hi-fi gear range, this is one of Perth’s top retailers. Dan and I do a bit of work together and he recommends us as needed.
Douglas HiFi
Chat with my friends Simon and Tony, ethical salespeople who won’t try to pull the wool over your eyes. These two have a wealth of hi-fi and home cinema experience. Douglas is ‘evolving’ back into what it always was – a proper hi-fi stereo store and one of the best. Douglas Hi-Fi also recommends us, for which I am grateful.
Frank Prowse Hi-Fi
Owner David Prowse is one of the nicest guys in audio and is ably assisted by great staff in one of Perth’s oldest and best-regarded proper hi-fi stores. I know the Prowse family well and even worked at the old location for a short spell. Frank used to help me when I was a hi-fi-crazed teenager, as did the wonderful John Negus of Audio Equip, in Myaree. Both were true gentlemen, and the industry needs more like them.
Revolution Turntable
Sadly closed, 2024!
My friend Pierre was the owner and a true old-school hi-fi industry stalwart. Pierre was also the official Australian Accuphase importer. We did a lot of work together and Pierre stocked a range of great hi-fi stereo gear, ably assisted by Jim, another great bloke.
Pierre had done this a long time and sadly, the retail grind and constant flow of odd-balls, tyre kickers and people wasting his time ‘discussing’ and demoing hi-fi gear, only to buy then buy it from zero-service online discounters who played no part in the sale, truly egregious and dipshit behaviour, finally caused him to throw in the towel. Retail is tough, and we need stores like this. Revolution Turntable will be missed!
Why don’t you require upfront payments?
Because I trust my customers.
Everything is upfront and transparent with Liquid Audio and as a result, we attract great customers who appreciate our ethical, professional operation. I don’t need to ask people to make upfront payments because they know we undertake work in good faith and I trust them to collect and pay for their equipment.
Naturally, people also want to collect their equipment after we’ve worked on it, so this just isn’t something I worry about. Occasionally though, someone will decide they don’t want to pay a bill. These are interesting cases!
Can you provide me with a service manual?
No, this is not a service we offer.
Many older service manuals are available online, and you don’t need my help to obtain them. Much of my service data, however, comes directly from manufacturers, distributors and other specialist sources, and is unavailable to the public.
Service data is intended for technicians and is provided in confidence, on the strict understanding that it will not be shared. Put simply, I am not permitted to share service data, manuals, schematics, etc that are not publicly available, and I don’t operate a file server for those that are.
No sensible professional would risk the relationships allowing them access to this critical data, so expecting me to, as Stephan from Germany did, is silly. When I politely explained to Stephan that I could not supply such data, he spat the dummy:
Thanks for nothing.
Stephan
I think what Stephan meant to say is:
“Thanks for your hard work and for the article that helped me repair my Krell amplifier; I’ll make a donation to support your work. I understand that you don’t need to publish anything, and I appreciate you replying and explaining this to me, despite having already explained it in the contact form I read and submitted.”
Sometimes, service data is not available, and in these cases, we must derive the necessary data by examining the engineering. This derived data and other proprietary solutions and intellectual property are also not up for grabs just because somebody wants them.
Should I buy rare transistors on eBay?
No, almost all rare transistor types on eBay are fakes.
The TLDR is that some parts are no longer available and that’s a certainty. If unavailable parts suddenly appear on eBay or other places selling to the general public, often in mainland China, walk away, unless you like throwing money away.
This point about retailers that sell to the general public is important because the commercial vendors I use for example don’t try to sell parts that we know are no longer available. You could say their customers are a bit better informed.
UPDATE, July 2024: I’ve been working on an Accuphase E-202 where the ‘repairer’ told the owner he had to order rare replacement transistors. Goodness knows why because there are more robust modern parts that should be used where the originals have died. Either way, I’ve tested them and they are standard Chinese eBay fakes. Be very wary of repairers telling you they are sourcing rare transistors from anywhere other than a reputable commercial vendor or specialist semiconductor supplier.
Dreaming
There are lots of parts that I wish were still available, but they’re not, so we move on and learn what to use in their place. Sure, an old guy in Poland may appear with an occasional box of special and otherwise unavailable parts, but you can usually pick these legitimate listings by looking for a variety of markers and other clues.
Everything else, like classic Hitachi 2SJ56 and 2SK176, VFETs, certain STK modules etc are fakes. I don’t mean that these parts are probably fakes, I’m saying with 100% certainty that they ARE fakes.
How do I know? I’ve been at this for a while now. I use a couple of specialist semiconductor vendors, and if they can’t obtain the parts I need, nobody can. I’ve examined and tested many fake parts over the years and have come to understand what is available, what isn’t and when genuine NOS parts do become available.
The Problem
Unscrupulous sellers know that people are willing to do almost anything to get hold of mythical, unobtainable parts. So, they take existing cheap parts and have them printed with whatever the unavailable part name is. The end-user/tinkerer/hobbyist/ill-informed repairer buys a few and installs them and they fail, or the problem remains… What then?
Are you going to return them to Shenzen? Good luck with that. How will you know, let alone prove that the new part is fake? How can you be sure there is not some other reason it failed? Would you even know if the new part or the equipment is performing correctly? Do you want to start an eBay dispute over fake transistors? You will be asked to have them professionally inspected and tested. For most, it’s just not worth going down this rabbit hole.
If you took your equipment to an expert, they could test it for you and let you know if the parts are genuine or fake, and what the problem is. This is why I generally avoid fitting customer-supplied parts. If the parts are not sourced from large commercial vendors or other specialist parts suppliers, you can’t trust them. It’s about eliminating variables. There are perhaps one or two good parts sellers on eBay, but that’s it.
Relax
In most cases, rare or unobtainable parts are simply not needed. I have stocks of, and access to, many rare NOS parts, parts that are unavailable to the average shopper. I also keep hundreds of modern replacement parts that work perfectly in most cases and I have an extensive database of tested substitutions that I’ve made over the years.
In the worst case where I have nothing available, I can design solutions to solve most semiconductor problems. This won’t involve eBay. Don’t fuel the fake parts industry or pay crazy prices for fake parts.
Can transistors in my vintage amplifier be replaced?
Yes, transistors can be replaced in almost all cases, with excellent results when done correctly.
As with anything technical, though, the devil is in the details, and people often get these details wrong. Part of the art of repairing electronics involves understanding what replacement parts are optimal in various scenarios and how to select the most appropriate substitutes when original parts are no longer available (NLA).
Good repairers stock a wide range of parts to accommodate most equipment/replacement scenarios. Good repairers do not source transistors on eBay. Read this FAQ to learn why.
Substitution
Transistors come in thousands of different types, sizes and ratings. Transistors are like spark plugs or tyres. They all serve the same general roles, but each type is tailored to a specific use case and set of parameters, like operating voltage, frequency response, gain, and power handling. Substitute the wrong types and the equipment may perform poorly, exhibit distortion, noise or high temperatures, or worse still, may catastrophically fail, taking other parts with it.
Transistor failures, in the form of noisy or drifty devices, dead shorts or open devices, are a common phenomenon in old and new gear. Resolving transistor failures is commonplace here at Liquid Audio, and getting this right, from a technical perspective, sets competent repairers apart. Look at case # 19 in the Hall of Shame, for example, to see how badly this can go wrong.
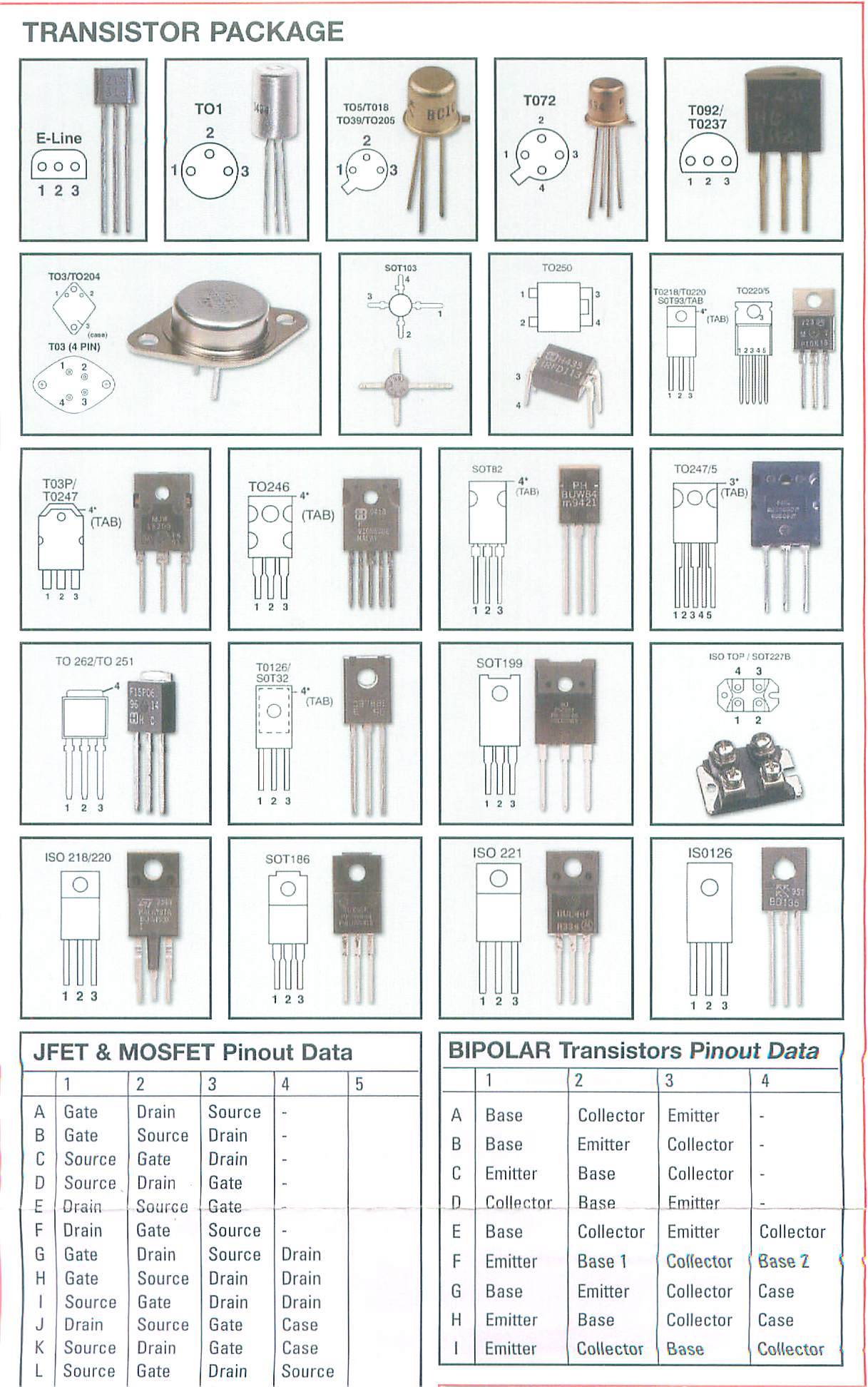
I’ve lost count of the number of pieces I’ve repaired where the problem was incorrect replacement transistors, rather than dead ones. Incorrect or poorly matched parts can lead to distortion, noise, overheating or premature failure. Therefore, a good working understanding of transistor specifications is critically important.
Stock
To ensure I have parts to suit most of the equipment we work on, I keep stocks of NOS and modern devices, including devices in TO-3 or TO-3P packages, TO-126, TO-220, TO-66 and TO-18 drivers, through to tiny little TO-92 devices, and everything in between.
Good repairers must have a range of such devices on hand, sourced through quality-assured supply chains rather than eBay for example. A quality-assured supply chain minimises warranty issues and maximises repair success rate. There is no point in taking chances here.

It gets trickier when we consider MOSFETs and VFETs, many of which are no longer available and lack any suitable replacements. That said, I’ve just repaired an amplifier with blown TO-3 MOSFETs and I used new parts from stock that worked perfectly. I have plenty more.
Data
Most older semiconductor devices can be replaced with modern parts, and I keep a regularly updated database of cross-references I implement. I also keep many old data books containing invaluable and otherwise unobtainable parts specifications, matching and substitution data. This allows the replacement of old devices with new and often better-than-original parts.
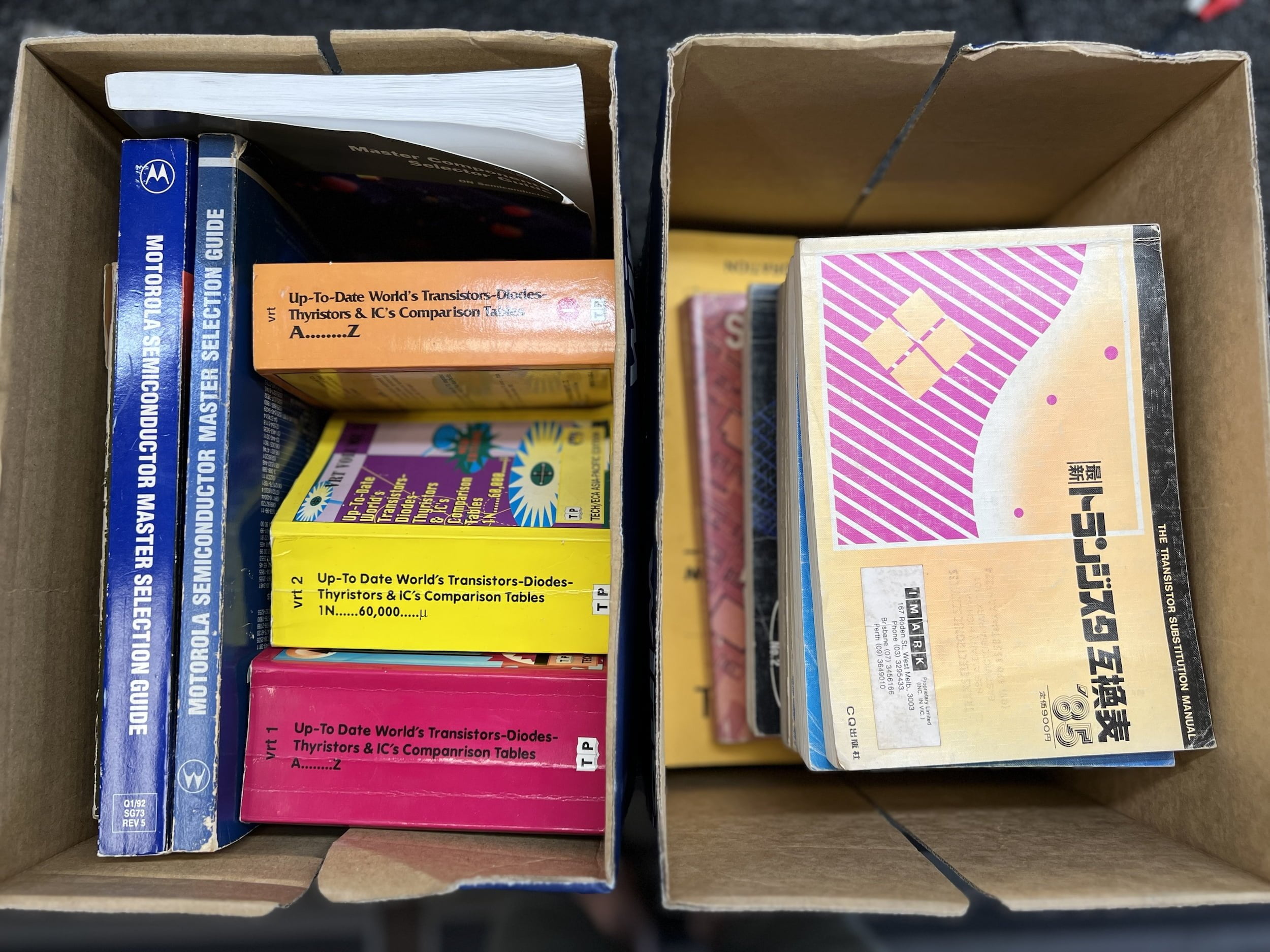
I stock replacements for the NLA TO-66 bipolar devices and unobtainable JFET small signal devices used in many older Accuphase amplifiers, for example. We also keep stock of probably thousands of transistors, including high-spec modern replacements for many vintage types that are NLA.
My technician told me cheap Chinese parts are perfectly OK, what are your thoughts?
Anyone offering this overall advice should not be taken seriously.
Cheap Chinese parts are everywhere and they have a place in very affordable equipment, Bluetooth speakers, soundbars etc. But there is a reason Bluetooth speakers and soundbars die after just a few years and I’d suggest that any technician telling you that cheap Chinese parts are perfectly OK in quality hi-fi gear is probably not someone you want to use.
“But Mike, Musical Fidelity uses cheap Chinese parts!”
Yes, they do, as do many manufacturers including Cambridge Audio, NAD, Redgum and many more. That doesn’t make these decisions good, it verifies why they are bad!
The single most important reason manufacturers use the cheapest Chinese parts is to save money. Many parts are now manufactured in China but not all of them fall into the super-cheap category. There is no good reason to fill boards with the very cheapest parts, other than to save money. That applies to manufacturers and repairers.
Do you offer radio and tuner RF alignments?
Yes, we have precision RF alignment equipment and are one of only a few still offering this service.
I’ve always held a strong interest in radio and keep a range of the most important RF test and measurement equipment, cables and connectors necessary to perform alignments of AM and FM broadcast band radios and tuners, and shortwave radios too.
Do you have cassette deck calibration tapes, head demagnetiser etc?
Indeed I do, you cannot do this sort of work properly without them.
In fact, I have some of the coolest cassette deck-specific tools available, custom-made for working with cassette decks and these are necessary tools of the trade.
My stash includes various calibration tapes including a custom Pioneer set for use with the CT-A9X and others, special mechanical tools, electronic test and measurement equipment, a TDK electronic tape head demagnetiser, and TEAC hand-held demagnetiser and a hand-made (by me) mirrored tape path cassette. I also have a range of hard copy original manufacturer service data and manuals.
Can you install LED lamps in my equipment?
In most cases yes, no problem.
We have stocks of incandescent and LED lamps, in the most common sizes, so you can choose what suits you. For the ultimate vintage goodness, incandescent lamps are the way to go. For a more modern look, LED illumination is great.
Can I use 100V equipment in Australia?
You can, as long as you understand some basic technical details and take a few precautions.
Basics
You can use equipment requiring almost any voltage, anywhere you like, as long as the specific voltage and current requirements of that equipment are met. For that, you’ll need to know:
- The operating voltage of your equipment
- Its power consumption, and
- If it needs to be / can be reconfigured for different line voltages
If you own 100V Japanese equipment that cannot be reconfigured for a particular local voltage, and many pieces cannot, you’ll need to select and source a suitable step-down or step-up transformer with the correct power rating and voltage. Such a step-down transformer should be sourced from a quality local manufacturer like Tortech.
A quality step-down transformer should be capable of delivering between 1.5x and 3x (or more) the rated maximum power consumption of the equipment drawing power from it. It must also deliver the voltage your equipment requires. A little less is OK, but no more.
Low-power devices are best to use with a step-down transformer because this avoids the need for a massive one. High-power step-downs are expensive, large, heavy, ugly things, and just another box you have to find a place for.
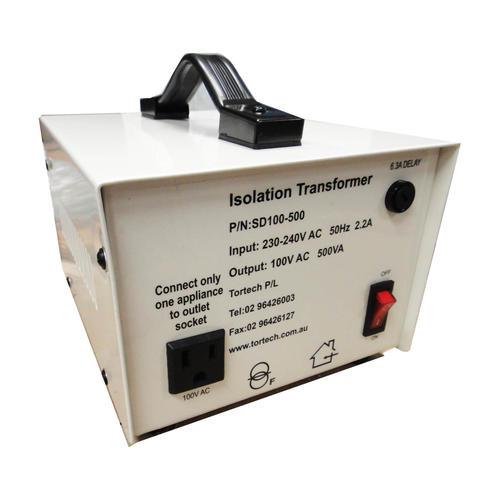
Note that 100V-rated equipment needs a 100V step-down transformer rather than the 110V or 120V offerings commonly available. Make sure you know which one you need, as indicated on the placard on the rear of your equipment.
Avoid cheap Chinese transformers as they are often incorrectly rated for voltage and significantly underrated in terms of the power they can deliver (VA), and their duty cycle. Remember, you get what you pay for.
Special Cases
If you have an amplifier, you’ll need a big step-down transformer, and these can be expensive. An amplifier rated for 500W maximum power consumption should be matched with a transformer rated for a minimum of 1 – 1.5kW at a 100% duty cycle, or more if possible. That’s a hefty transformer, and it won’t be cheap.
The high rating is necessary to minimise power supply source impedance and transformer core saturation. This will maximise amplifier performance and ensure the transformer does not overheat during normal use. Because hefty transformers are heavy and expensive, amplifiers are the least well-suited for use with step-down transformers; the bigger and more power-hungry, the less well-suited.
For low-powered equipment like turntables, DACs and preamps, smaller step-down transformers can work well. A moderately sized transformer will safely be able to run several low-power devices. Just make sure that the total continuous power consumption of all the connected equipment is comfortably exceeded (1.5x to 3x, or more) by the continuous maximum rating of the stepdown transformer.
Voltage
You may not realise that it is always best to run high-power, high-current devices like amplifiers on the highest voltage they can be configured for, ie 240V in most cases. There are two reasons for this.
Setting the highest voltage provides the greatest margin for overvoltage conditions, so there is some degree of protection in this configuration. Also, at 240V, the current requirements are less than half of what they are at 100V. Lower current draw means less voltage sag at the outlet, lower wire losses due to resistive heating and reduced dynamic effects associated with modulation of the power supply rails.
Many ‘extreme’ hi-fi systems in countries with 100 or 120V mains will have house wiring configured to deliver 220 or 240V for this reason.
Warnings
You must never plug equipment rated to run on 100V or 120V into an Australian 240V mains outlet unless it has been configured to run at 240V. Failure to adhere to this warning will almost certainly result in the death of your equipment. Worst of all, this death may be permanent. You’ve been warned!
Reconfiguring equipment may require internal adjustment, soldering, and replacement parts such as circuit breakers and/or fuses of a different current rating to suit the higher line voltage. This work must not be ignored, as it often is, because equipment may fail if a fault occurs once equipment has been converted to run on 240V if the correct current limits are not in place.
I’ve seen a recent influx of 100V equipment that has failed because people have a basic step-down setup and have temporarily forgotten that their equipment needs to be plugged into it! For this reason, it is imperative to have equipment reconfigured where it can be and to make sure any 100V zone is marked where equipment cannot be moved or plugged in elsewhere, with appropriate mains plugs.
PS
If you found this information helpful, there is a donate button in the footer and 140 other FAQs you might enjoy, plus hundreds of other full-length articles, all for free. Find another specialist doing even 1/4 of that and I’ll buy YOU a drink!
Can you provide me with a kit, parts list or BOM?
No, we neither use nor recommend kits, nor do we sell parts lists, BOMs, or parts.
Repairing and overhauling electronic equipment involves much more than swapping parts. For the average owner, attempting to overhaul a complex piece of hi-fi electronics via a kit is as silly as it sounds and usually creates more problems than it solves. Please don’t take this the wrong way, it’s for the same simple reasons that the average car owner shouldn’t try to rebuild their car’s engine.
I understand that people may want to take on this work, but this rarely saves money because most lack the skills, tools and experience needed to install parts correctly, diagnose and repair any remaining issues and ensure their equipment runs correctly afterwards.
Another problem with kits is that the parts usually have no traceable provenance or warranty. They may not even be genuine or the right parts for the job, which the average person has no way of knowing. If saving money is the goal, it’s usually better for most owners to do nothing than attempt major work on their equipment.
There are no magic kits or BOMs that will fix broken hi-fi gear. Each repair is unique, each must be assessed on its own merits and each will need a unique set of parts, and someone able to install them without causing damage and deal with any remaining issues.
I purchased equipment from Japan and it blew up, can you help?
I’d be happy to, but I hope you read this before needing my help!
If you are here because your equipment has failed, though, we will first need to establish what damage has been done. Careful inspection will reveal the answers.
Know Your Voltage
Different regions use different AC or mains supply voltages. For example, Japan uses 100V, the USA uses 110/120V, and Europe and Asia use 220V, 230V or 240V, depending on the region. Anything other than 230V or 240V presents a problem for people living in Australia, where we have a 240/250V supply.
Higher voltage AC supplies are better from a technical perspective; more on that another time. BUT – If you plug a piece of electronic equipment set to run on 100V or 120V into a 240V socket here in Australia, IT WILL FAIL, unless a fuse saves it first, which is a one percenter.
Electronic equipment doesn’t “automatically adjust”, as one enquirer who blew up his newly acquired equipment tried to convince me. Why he was trying to convince me of anything is a funny story in itself. Perhaps he was thinking of equipment with switching power supplies or SMPS, like phone chargers or USB power supplies.
The Problem
Transformers ‘transform’ or convert AC voltages proportional to the ratio of turns on their primary and secondary sides. Equipment set to run on 120VAC might contain a transformer that steps this down to 35VAC, which will be around 50VDC when rectified. When that transformer is fed 240V, double the input voltage equals double the output voltage. The internal 50VDC supply is now a 100VDC supply, which isn’t good if it needs to be a 50V supply!
100V will kill electrical components that were rated for 50V. Fast-acting fuses might save the day, but in most cases, the damage is more substantial, even terminal. It depends on the circuit and, to some extent, luck.
My 2024 repair of a gorgeous Pioneer PL-50L turntable is an example of a 100V Japanese turntable that died when plugged into a 240V outlet. There were no internal fuses here, and repair would not have been possible in the wrong hands.
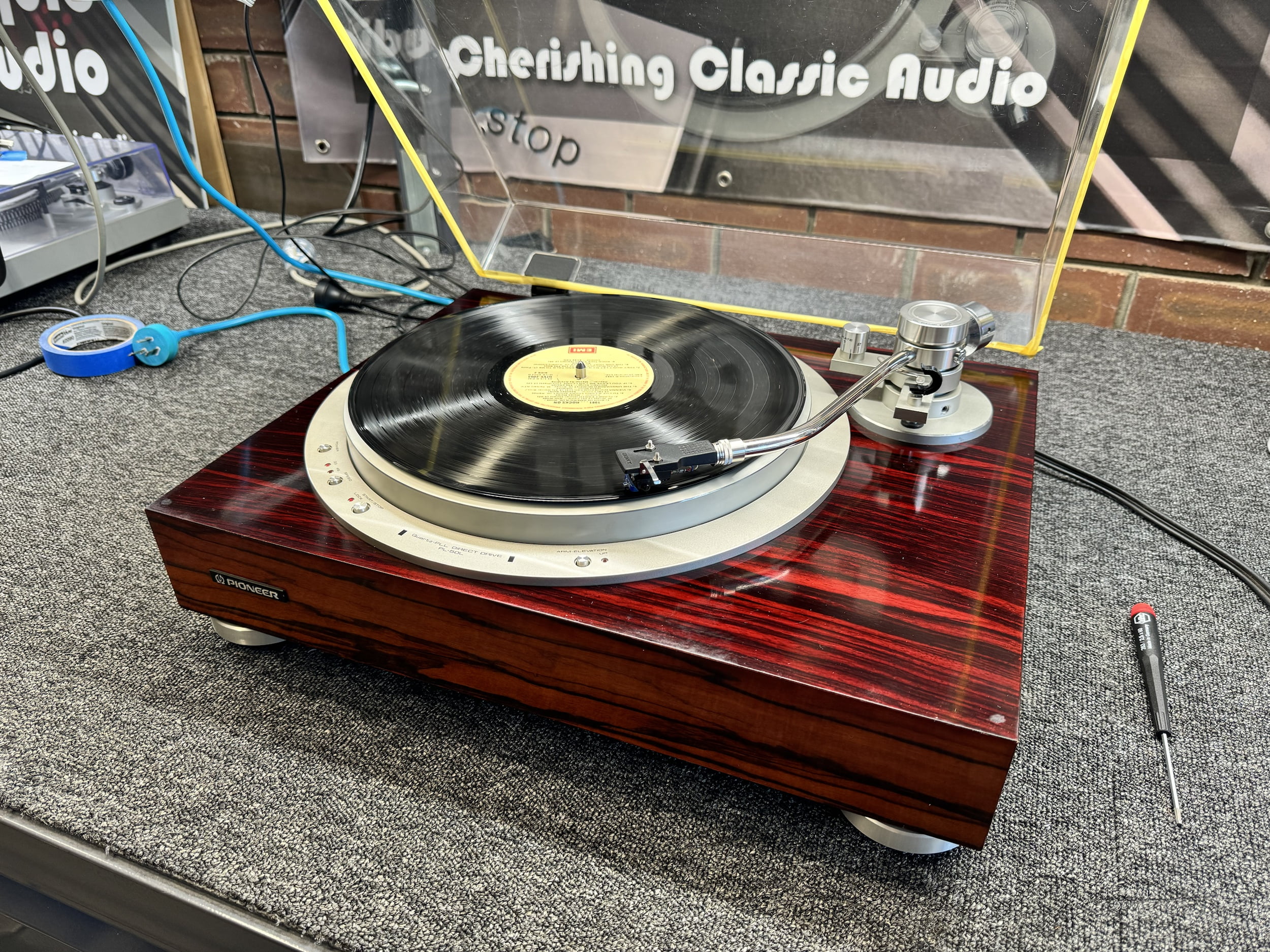
Configurability
Some hi-fi equipment can be set to run on various line voltages. Reconfiguration may be straightforward via an external adjustment or involve working inside a chassis to reconfigure taps, wires and unmarked jumpers. In some cases, new parts, like circuit breakers of a different rating, will be required. These are special order items.
Some equipment cannot be reconfigured, including lots of Japanese and North American market-only equipment. Over the years, I’ve become familiar with what can and cannot be reconfigured, but there are variations between examples of the same model that mean the answer often cannot be known until the equipment is inspected.
I’ve also seen locally supplied equipment misconfigured. The Mark Levinson ML-7 preamp I repaired and a pair of Accuphase M-60 amplifiers are two examples of gear set to 220V for a 240V environment. Therefore, a simple rule should be applied to all equipment:
Every piece should be checked by someone with the experience and knowledge needed to ensure it is correctly configured for the line voltage in your location.
False Economy
If you think it’s expensive to hire a professional to do the job, wait until you hire an amateur.
Red Adair
We all like to save money, but scrimping on the maintenance of rare/valuable/high-end things like hi-fi equipment is as ill-advised as you already suspect it might be. Nothing is saved by having the wrong person do an important job. An example:
In October 2024, I heard about a fellow with an Accuphase SACD player worth about $30K AUD who ended up with a lovely-looking $30K doorstop because he tried to save money and took it to someone who killed it. In desperation, he went to the forums, compounding his initial mistake with another.
Having equipment professionally inspected pre- or post-purchase is sensible and provides peace of mind that it is safe, clean, adjusted, and serviced. We almost always find things needing attention, so inspections pay for themselves when leveraged into price reductions, refunds, or avoiding the purchase of a bad example of a piece.
TLDR
I receive a steady stream of enquiries from people who’ve killed hi-fi equipment with incorrect line voltage. This failure mode is entirely avoidable by having equipment professionally assessed and configured. If the equipment cannot be reconfigured, a step-down transformer of the correct capacity/rating is required. More specific advice, as always, is available via our advisory service.
Should I buy an AM/FM tuner from Japan?
No, you should never do this.
Japan has a different FM band frequency allocation, spanning 76 – 90 MHz. The Australasian, European and North American FM broadcast band spans 88 – 108 MHz. That means that with a Japanese FM tuner, you’ll see a tiny 2 MHz overlap. You’ll be lucky if you can pick up one station in that slice and this often cannot be changed, especially in the older analog style tuners.
Does hi-fi gear really need to be serviced?
Yes, all electronic equipment needs periodic maintenance.
Pretty much everything made by humans needs some form of periodic maintenance or service, so this should come as no surprise. I regularly have to de-scale my coffee machine and kettle for example, but not everyone does or even knows they need to. Complex electronic equipment often containing hundreds of parts and operating decades past its intended design life is certainly no exception.
Design Life
Manufacturer-specified maintenance information is often found in the service documentation associated with a piece of equipment. The work needed takes the form of cleaning, electronic and mechanical adjustment and parts replacement necessary to keep equipment running reliably.
This maintenance is what was thought would be needed over the projected design life of the equipment though. When this equipment was designed and built, nobody imagined that it would still be working, let alone cherished and sought after, 30, 40, or even 50 years later. Incredible when you think about it and this certainly doesn’t apply to anything you buy new now.
There’s often very little maintenance information accompanying consumer-level gear like this anyway, a reflection of the nature of the equipment and its predicted lifespan. The extended life much of this equipment enjoys is usually well beyond its intended design life and the ongoing maintenance needs are simply not covered by any service data.
Keeping these pieces running requires experience and an understanding of how equipment ages. Many of these service procedures and techniques have been developed by Liquid Audio and other professionals in this space, over many years. I use service procedures, parts, lubricants etc that manufacturers didn’t disclose or that have become superseded. I’ve had to reverse-engineer these or develop solutions, as required.
Magic Smoke
Owners of hi-fi equipment are often unaware of maintenance requirements or that components degrade over time. Eventually, mechanical parts seize or fail and the ‘magic smoke’ is released from electronic components, leaving hi-fi equipment no longer functional. *
Having established that all hi-fi equipment needs maintenance, it may be intuitive that the more complex it is, the more maintenance it needs. Turntables and cassette decks are generally the most maintenance-intensive, followed by amplifiers, CD players, tuners, preamps and then things without knobs, like DACs, roughly in that order.
I’ve written more about how and why electronic equipment needs periodic maintenance here and here. Periodic maintenance reduces the likelihood and potential severity of equipment failure and dramatically improves its performance. Whatever you do, just have the work done by someone competent. Your equipment will eventually fail if you don’t maintain it.
* When magic smoke is released from an electronic part, that part is broken forever. Magic smoke cannot be ‘re-installed’, only new components containing their factory original magic smoke perform to specification.
Should I spray contact cleaner into my equipment?
In most cases, probably not.
If you have access to proper commercial-quality products, know how to use them, and that they are appropriate for the use case, go for it. But if not, or if you think that WD-40 and CRC 5.56 qualify as contact cleaners, then STOP, put the can down and s l o w l y back away from the equipment..!
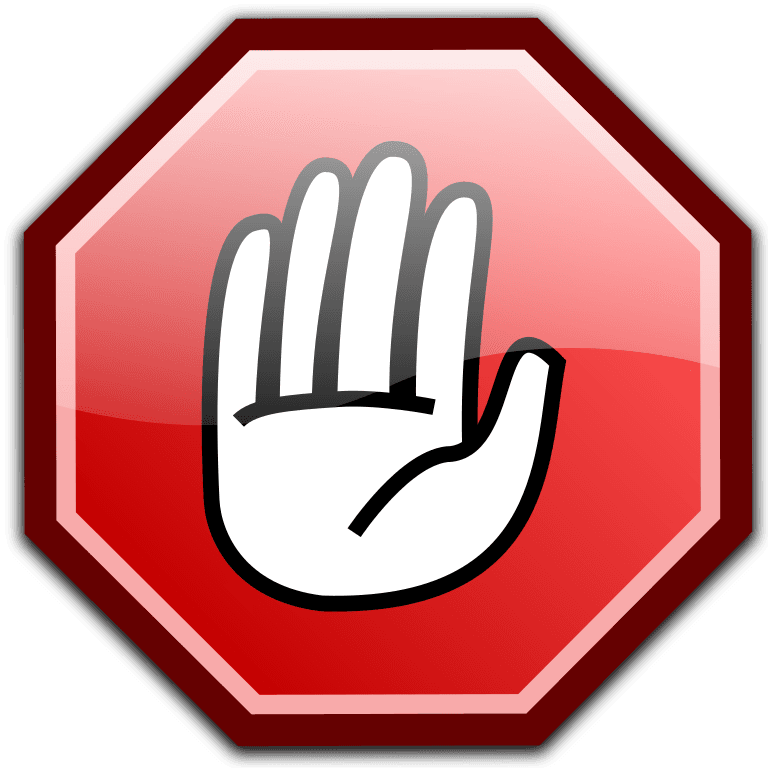
The contact cleaners and treatments I use are commercial/laboratory-grade products, often applied as part of a multi-stage deep cleaning and treatment regimen I’ve designed, specifically for equipment types long past their design life and where no official service procedures exist. These products are very different from those often found in hobbyist electronics stores that leave oily residues and offer only short-term relief.
WD-40
WD-40 and CRC 5.56 are aerosol-delivered, low-viscosity, penetrating lubricants, water dispersers and corrosion inhibitors. However, one of the issues with these products, especially WD-40, is that they are marketed a little like the old radium water was: good for everything, but in reality, not really!
These products consist of light oils suspended in volatile carriers that evaporate, leaving oily residues that protect metallic surfaces from corrosion for a short time. These residues attract dust and dirt, less important on nuts and bolts, but a very significant problem inside sensitive switches, relays and potentiometers with human hair-thin gold wipers, for example.
In these delicate structures, oily residues trap dirt, increasing friction and turning it into an abrasive paste, making such structures dirtier and less reliable over time. The use of pressurised aerosols containing oleophilic solvents can also flush out greases and oils that are part of the smooth mechanical operation of the switch/pot/etc. These must be replaced, and WD-40 cannot replace them.
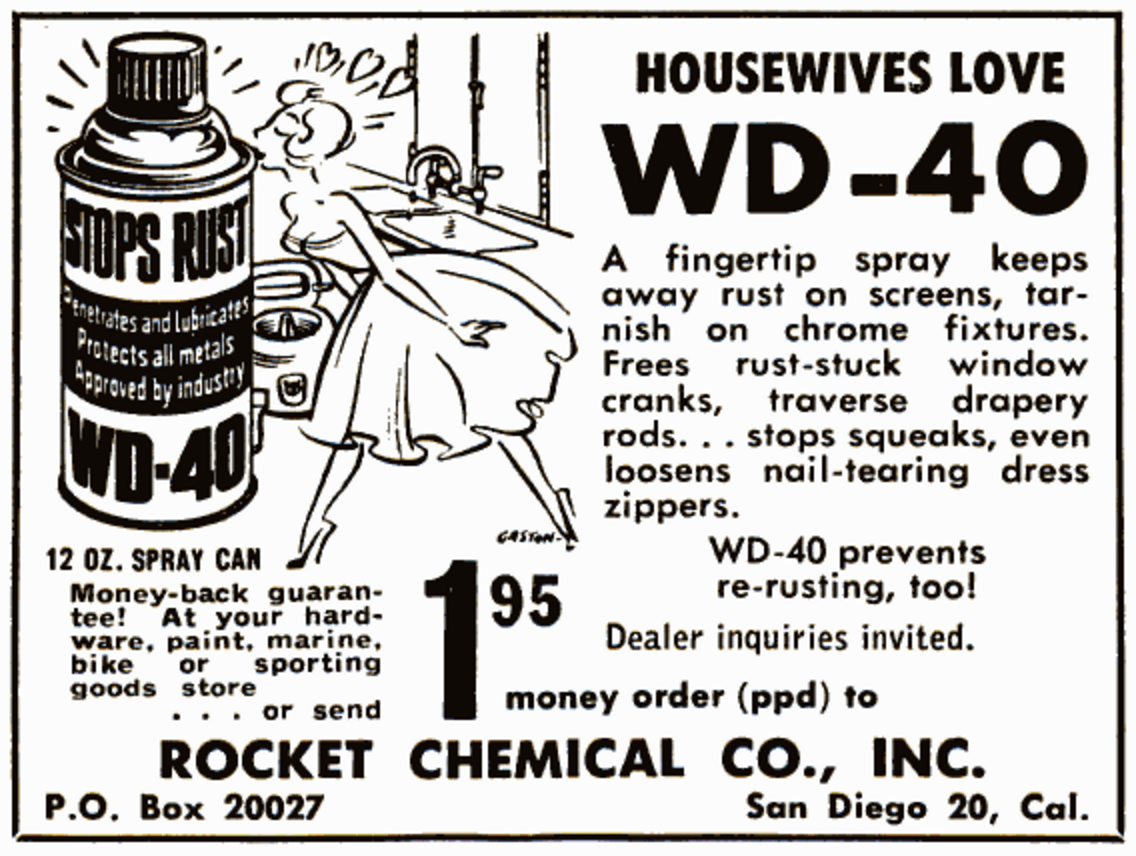
At some point after applying WD-40 or CRC 5.56, deep cleaning to remove these contaminants and re-treatment and lubrication will be needed to restore proper functionality. That is assuming permanent damage has not been caused through wear over an extended period of operation. This follow-up work is time-consuming and technical, and sometimes it’s too late.
But Mike, WD-40 was developed for NASA, for use on rockets!
So they say, and that’s just terrific, but it STILL IS NOT a contact cleaner or treatment. It’s like this: petrol is a great solvent, yes? Would you clean your carpets with it? How about electronics..? Lovers of WD-40 are welcome, even encourgaed, to spray that sh*t all over their equipment and even themselves if they wish. Just don’t bring it to me afterwards 🙂
How should I clean my hi-fi gear?
I use various cleaning techniques, depending on the equipment make and model, the parts I’m cleaning and how dirty it is, some of which I’ll briefly describe here.
Exterior
For most metallic, painted, and plastic exteriors, I recommend starting by carefully dusting the surfaces to be cleaned. Then, a microfibre cloth and mild detergent/water solution can be gently applied to areas needing cleaning.
Be careful with older gear, as logos and other markings are sometimes printed with ink that becomes fragile with time. Solvents other than water, and occasionally even water alone, can remove this fragile ink, so test a small inconspicuous area first.
Wooden exteriors can be cleaned with a soft cloth, wood soap, and furniture-grade oil or wax. I use fine furniture oil and beeswax for most wooden finishes. These work very well to bring out the grain and lustre of the wood.
Knobs can be removed and soaked in a mild detergent/water solution and then finished with a toothbrush and fresh water. Be sure to use the correct-sized flat-blade screwdriver or hex key to loosen any grub screws, where present. I’ve lost track of how often I’ve found these damaged when they should never be.
Plastic lenses can be dusted and cleaned with mild detergent/water and microfibre cloth. A little high-grade plastic or automotive polish with microfibre cloth can be used where lenses and bezels are dull and/or scratched. Again, avoid polishing printed surfaces as these may be degraded by this process. Be careful not to polish matt or satin finishes or they will end up glossy.
Be very careful with turntables, too. Turntables and cleaning cloths don’t mix well; many have learned this the hard way. Soft-bristled paint brushes work well in sensitive areas but as always, each case is different and care must be exercised when cleaning anything, especially tonearms, cartridges, etc.
Interior
Interior cleaning requires more care and should not progress beyond light dusting for most. There are electronic and mechanical parts to consider, and one must be very careful not to damage anything through the cleaning process. It is always better to err on the side of caution and not clean something than risk damaging it.
High-velocity air works well as an initial duster, combined with a very soft-bristled paint brush, but must be used judiciously. Care must be taken with raised components in order not to damage them.
Isopropyl alcohol and cotton buds or Q-tips work well to spot clean dirty components and boards. An old toothbrush is also a useful tool for cleaning boards, again with a little isopropyl alcohol.
Beyond this, I recommend deeper cleaning methods including ultrasonic and mild solvent cleaning, and deep chassis washing, both of which should only be carried out by someone familiar with these methods. Water-based solvent cleaning should be avoided unless the techniques are well-understood.
Avoid WD-40 and similar penetrants as they don’t clean electronics at all and leave oily residues that attract dust and dirt. This is especially problematic around high-impedance circuits like preamps, RF sections in tuners, phono stages, switches and relays. If in doubt, again, don’t touch it.
Technical Deep Cleaning
Beyond the basic cleaning I’ve outlined above, equipment often needs what I refer to as technical deep cleaning. Deep cleaning and detailing are specialised aspects of maintenance and I recommend booking your equipment with someone well-versed in this type of work.
Note that many repairers neglect this important aspect of maintenance for various reasons (it is hard, time-consuming, unknown techniques, etc), but dirt causes many problems with electronics.
I’ve developed deep cleaning regimens/techniques specifically to suit circuit boards, high-impedance circuits, switches and potentiometers, chassis parts, fascias and more. Some I’ve adapted from laboratory test and measurement and optical equipment cleaning procedures. Others I’ve created to suit the equipment I work on. These regimens can be considered proprietary and unique to Liquid Audio.
Technical deep cleaning typically involves specialist cleaning foams, liquids and tools, cleaning media, high-pressure air, ultrasonic cleaning, a drying oven, removal of sensitive parts to avoid contamination or damage, etc in combination with precise application of techniques applicable to the equipment in question. Whilst these techniques are very effective, they must be done exactly as designed or problems will arise.
I’m often asked for details of my technical cleaning regimens, step-by-step instructions, shopping lists, etc. but I don’t offer this proprietary information. Doing this properly would require written materials and training that I don’t have time to create, and my competitors would also love these details, in addition to what they already take from this website.
What’s the best-sounding amplifier design?
Class A is the gold standard and always used where cost is not a factor.
Based purely on performance and sonics, the highest-fidelity amplifier design is class A. Speaker sensitivity, combined with your amplifier’s power output, determines the system dynamic range, an important consideration not to be overlooked though.
No Compromise
Nothing sounds better than a well-designed, well-built class A amplifier. That’s because it’s the least compromised topology. This is also why you will always find class A designs where cost is no object, and in low-power circuits like preamps and headphone amplifiers, where highest fidelity is critical and class A circuits can be implemented without great additional cost.
For example, think about this: If class D designs were sonically the best performers, they’d be used everywhere, in preamplifiers, headphone amplifiers, phono amplifiers etc, especially given their efficiency and low cost. But they’re not. Why not when they are the cheapest amplifier designs to build?
Because nothing beats discrete, inefficient, linear, class A designs for signal purity and sonority. Engineers, equipment designers and manufacturers know this, of course. Engineering truths like this one can teach us a lot. Another interesting engineering fact is that cutting lathes are direct-drive… I wonder why that might be…?!
We can refine this further by stating that the very best solid-state class A amplifiers are generally MOSFET designs. FETs behave more like tubes than bipolar devices do. They are voltage devices, meaning tiny low-current signals drive them, making them very sensitive and simplifying circuit design and the signal path.
For this reason, cost-no-object class A designs like my Accuphase A-75, the Accuphase A-300 and many others including various BAT designs like this BAT VK-500 and the legendary Parreaux series including my Perreaux PMF-5150B use FETs.
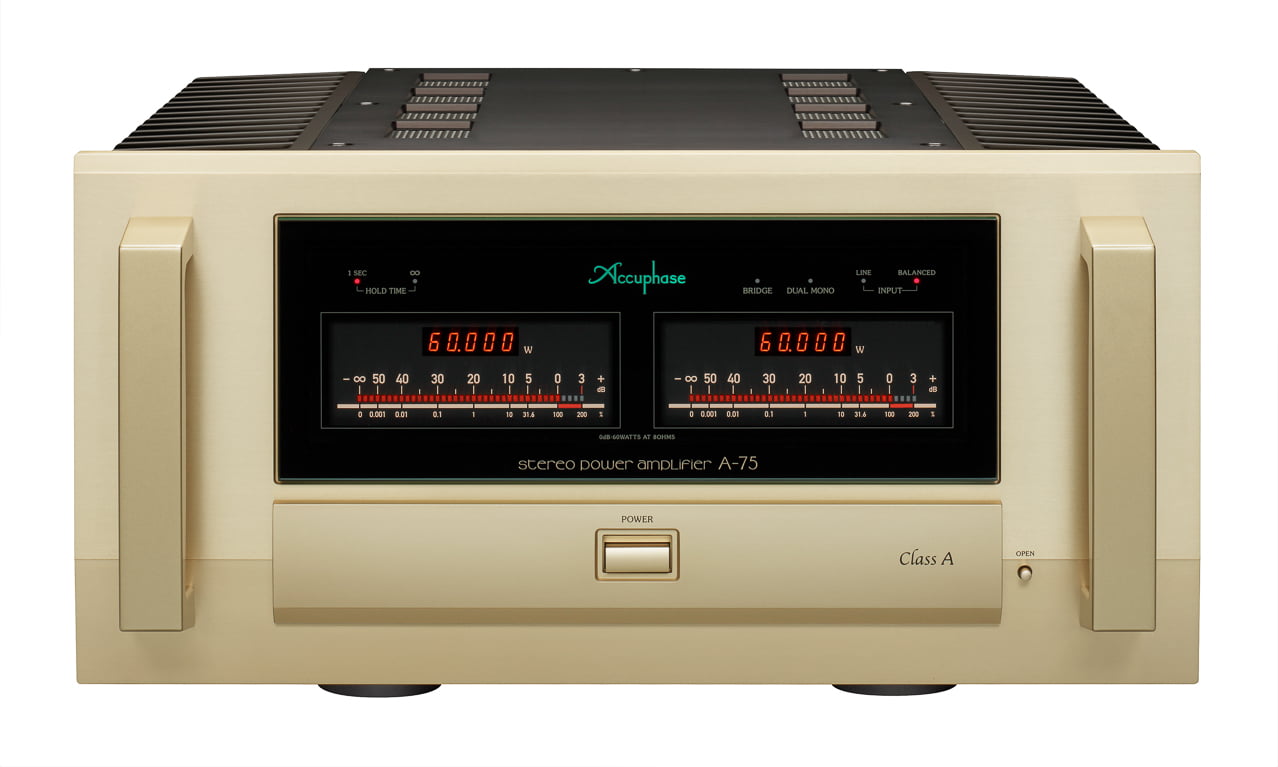
Drawbacks
Never a free lunch as they say and class A speaker amplifiers are hot, heavy and very expensive, because of their constant need to dissipate significant thermal power. For this reason, they’re often relatively low power, at least on paper, because of the need to make them somewhat affordable. Even low-powered class A amplifiers are heavy and much more expensive to make than equivalently specified class AB amplifiers.
High-powered class A amplifiers like my old Krell KSA-150 or the Accuphase A-100 monoblocks are crazy-heavy and expensive. But, when sound quality is priority number one and you have the free space to site a large, expensive, heat-generating amplifier, class A is the only way.
Oils Ain’t Oils
Note that being designated as a class A amplifier does not guarantee it will sound great. The plethora of cheap Chinese class A equipment bears testament to this. You do get what you pay for and there are many good reasons why an Accuphase A-75 class A stereo power amplifier costs $35,000 AUD and a Vincent costs $3,000!
There are of course Chinese ‘clones’ of Accuphase amplifiers, designed to suck in those who would believe that a $3000 cheaply constructed not even close rip off of a famous hand-made in Japan amplifier could ever approach to the real thing. These ‘Red Dot’ rip offs will always be the literal garbage that they appear, and they will always exist, appealing to the same people who buy a fake Rolex and imagine that they got a great deal!
Other Considerations
Keep in mind that dynamics and the ability to generate realistic sound pressure levels are as important as smoothness and low distortion in hi-fi terms. By these measures, some class A amplifiers may struggle with less sensitive speakers, simply because they lack power. Get the power/sensitivity match right though and you will be winning.
Also, keep in mind you can get nearly all the way there, and get better dynamic fidelity with high-bias class AB designs. These offer a small amount of class A power – anywhere from 3 – 15 Watts, and from there revert to traditional class AB. For most normal listening, these are class A amplifiers, but with the punch of something much bigger. They lack the fancy power supplies and MOSFETs though, in most cases.
What are the advantages of class B amplifiers?
For hi-fi purposes, none.
Class B is often used for radiofrequency broadcast amplifiers, where high power and low spurious RF emissions (sorry, no class-D in radio!) make it a great choice. On its own though, class B suffers from relatively high (crossover) distortion and is unsuitable for audio for that reason.
Combined with a little class-A though, you get the best of both worlds. When a little quiescent current is applied to the output devices, they are biased on past the zero-cross point, and you then have a class AB amplifier. This dramatically reduces distortion and is what most proper consumer-grade hi-fi amplifiers use these days.
What are the advantages of class AB amplifiers?
Class AB amplifiers offer many advantages that make them the most commonly found designs in the mainstream hi-fi space.
For example, class AB amplifiers offer lower cost and cooler operation than class A designs, with some of the finesse and high fidelity, but with some of the punch and brute force power of class B designs and no class D drawbacks, in a relatively affordable package. You get a little bit of everything here, but only up to a point.
Class B topology is not good for audio because of non-linearity around the output device crossover point, resulting in crossover distortion. However, class B designs offer more power, lower weight and lower cost than a class A design of similar power. All designs are a series of compromises. Class B is intended where extremely high power output and efficiency are critical and some distortion is acceptable, like RF transmitters.
Class A amplifiers have no crossover distortion and offer the highest fidelity and greatest sonic performance. The flip side is that Class A designs are heavy and run hot, even for very modest power outputs, because they dissipate their maximum rated power, all the time, even with no signal.
Class AB amplifiers operate in class A up to a few Watts and then revert to class B for the rest of the power envelope. At lower levels, you’ll have the sweet sound of class A. You’ll have the punch of class B for dynamic swings and higher volumes. The more class A power on hand, the better the sound, because the more of the envelope is reproduced via class A operation, other things being equal.
Almost all consumer-grade amplifiers operate in class AB because of this topology’s cost-effective, high-fidelity nature. That said, most consumer amplifiers run very little class A power, sometimes only a couple of Watts, or less! The best results, as always, come from pure class A.
What are the advantages of class A amplifiers?
The critical advantage of class A topology is superlative sonic performance.
Basics
Class A amplifiers deliver the smoothest, most euphonic sonic performance. That’s why class A is used in high-end designs despite its shortcomings and why the very best amplifiers are class A, where cost is no object. The best class A amplifiers are MOSFET or tube-based designs from my experience.
But Mike, I listened to a cheap Chinese class-A tube amplifier and it sounded like sh#t!
Indeed, so I’m excluding the myriad of cheap, low-quality Chinese and Indian designs that have flooded the market from Vincent, Willsenton and various other junk brands. This equipment sounds ordinary, is cheaply made, fails frequently and should generally be avoided.
Compromises
There are no free lunches in engineering though and, as per my FAQs on class AB, class B and class D, each topology has its pros and cons. Class A amplifiers dissipate their maximum rated power at all times meaning they run hot, constantly. The only way to deal with this heat is to use the very best parts and engineering, big chassis and heatsinks, etc. The best parts and engineering always mean one thing: m-o-n-e-y baby!
Now, if the required power output is very small, such as a headphone amplifier or preamplifier like my Accuphase C-290, class A is no problem and less expensive to implement. Dissipating low power is relatively easy. Power amplifiers running in class A have to be large and very substantially built to cope with this constant high power demand, 100% duty cycle and high heat dissipation, however.
Such class A power amplifiers are big, heavy and need excellent ventilation. Some environments/use cases won’t be well suited to class A amplifiers. My Accuphase A-75 class A power amplifier weighs 45kg and delivers a very conservatively rated 60 Watts per channel into 8 Ohms (measures over 120 Watts/ch). Good A/C is essential when running class A amplification like this!
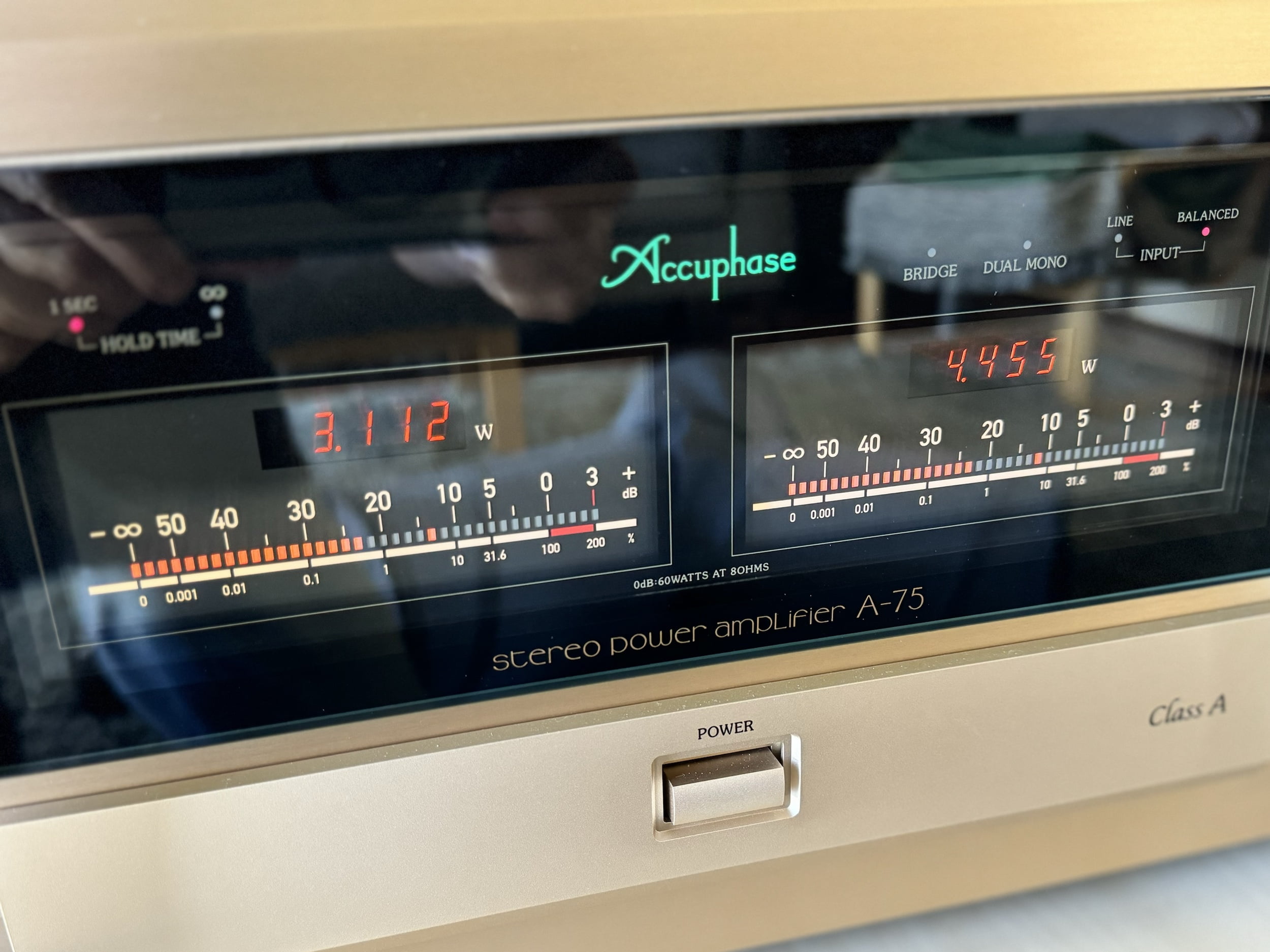
Bottom Line
With these overbuilt designs come advantages though, like massive power supplies and premium, heavy-duty parts that can cope with the load. These build factors also deliver sonic advantages of their own, so class A amplifiers tend to just be better all around. The best-sounding ones are the MOSFET types, like the A-75.
The disadvantages of class A design such as high cost, high power dissipation, increased electricity bills, and large size and weight must be taken into account. Class A amplifiers have the highest $/Watt ratio and are therefore not found at the lower end of the consumer spectrum.
Because powerful class A designs cannot be implemented cheaply, cheap Chinese solutions, like the ridiculous Mumysys/Musymys/Mumsymys (LOL) Chinese designs that look a little like an Accuphase something A-75 are literal garbage and should be avoided.
For the best sound, whether tube or solid-state, class A is the gold standard.
What are the advantages of class D amplifiers?
Class D offers advantages in efficiency, size and cost, allowing a proliferation of small, powerful and cheap amplifiers.
Pros & Cons
High power and low cost are desirable amplifier traits and help explain the popularity of class D amplifiers in the low-cost, high-value sectors of the market. Class D delivers very high efficiency compared to class AB amplifiers, meaning more Watts per $, less heat and smaller amplifiers. Class D also simplifies construction and allows fewer and smaller parts, reducing build costs.
There’s no such thing as a free lunch though and class D trade-offs traditionally revolve around performance or in this case sound quality. Class D amps historically have measured poorly, including higher distortion, noise and unwanted RF byproducts caused by the high-frequency switching inherent in these designs.
Class D amplifiers also often don’t perform as well when driving really low-impedance loads of 2 or even 1 Ohm. That said, there have been many improvements in class D designs in recent years and some of the latest class D designs perform well on paper, even spectacularly well in a few cases. Note that spectacular on-paper performance does not automatically translate into spectacular sonic performance, however.
The TL;DR: For the ultimate sonic performance, class D has never been the best choice and this remains the case. That mantle, as always, goes to class A. Note that this is not an opinion, it is an engineering reality.
As with all things technical, there’s a bit to understand, so let’s dig in.
Conflicts of Interest
Some will try to convince you that class D is inherently sonically superior to class A or class AB, but there is nothing from a technical perspective that makes class D sonically superior. Class D is cheaper and more efficient though, so it suits one-box solutions – Bose, B & O, Devaliet etc – and it works very well for less critical home cinema, AVR and subwoofer duties.
Engineers and experienced audiophiles understand this but manufacturers and retailers need to sell new equipment, creating a ridiculous conflict of interest ever-present in audio. Imagine taking your old car to the dealership and asking the salesperson if they think you should keep it or get one of the fancy new ones they sell. Do you honestly think you’d receive impartial, technically informed advice from people whose livelihoods depend on selling these new cars?
But Mike, if class D is no good, why do manufacturers use it?
This is the right sort of question to ask. Class D works very well in certain use cases and offers big cost savings, which means greater margins and therefore bigger profits for manufacturers.
Use-Cases
Class D is a bit like plastic. Given the choice, most things would be built out of metal and wood rather than plastic, because these are more beautiful, more durable materials. You can make some fancy and cheap parts out of plastic, though. Plastic = lighter, faster, cheaper. Class D = smaller, more powerful, cheaper.
Class A is the best option in amplifiers where cost is not a factor, but cost is always a factor. You can’t build 500-Watt class A PA amplifiers because they would cost $100,000, weigh 200kg each, and nobody would buy them because nobody in the nightclub gives a sh*t about better sound that you can’t hear through the garbage PA speakers when you are drunk!
Is class D ever the best choice? Class D is perfect where high power, small size and low cost are needed, like subwoofers, home cinema amplifiers and receivers and low to mid-priced power amplifiers. All-in-one amplifier/DAC/streamer things, sound bars, subs, PA amplifiers and AV receivers use class D amplifiers for one set of reasons: low cost/small size/high power/high efficiency/high margins.
Manufacturers like NuForce, B&O and Hypex have produced class D amplifiers and amplifier modules for the hi-fi market. B&O’s ICEpower class D modules find use in concert, club and live venue environments where high power, efficiency and ruggedness are more important than absolute sound quality. In these roles, class D performs well.
Bull$hit
Consumer (mis)understanding of the technical aspects of hi-fi engineering generally comes from marketing materials and retailers. The problem again is the conflict of interest and the poor technical literacy of these sources.
Here’s the bullsh*t HiFi+ spewed about the ‘new’ class D amplification in NAD’s plastic C-298 power amplifier, for example, with nonsense highlighted:
NAD has moved away from the old-fashioned and very power-hungry linear power supplies and class AB output stages that waste nearly half of the energy consumed, producing heat rather than sound. Instead, the company has developed even better performing circuits based on switch mode (sic) power supplies and class D output stages. Once thought to be inferior to traditional topologies, NAD’s advanced work in this area has created some of the best-performing amplifiers regardless of basic design principle. These new designs are very linear over a wide bandwidth and provide consistent performance into all speaker loads, providing a dramatic advance over previous models.
HiFi+ ‘staff’
HiFi+ needs to do better, so here’s my translation:
NAD has abandoned proven, high-performance but more expensive to manufacture linear power supplies and class AB output stages. These are less efficient because they deliberately use some energy to improve sonic performance. Instead, the company has recycled existing, poorer-performing but cheaper to make circuits based on switching power supplies and class D output stages. Known to be inferior but currently trending in hi-fi land, NAD has used old designs from the ’50s and ’60s to save money on transformers, parts, metal and therefore production, weight and shipping costs. These designs provide no real advancement over previous A and AB models except increased margins and profitability, which helps NAD.
Liquid Mike
The High-End
Class D was the flavour of the month in the naughties when people like Srajan Ebaen at 6 Moons endlessly pumped brands people had ever heard of and now cannot remember. Many turned out to be unreliable due to their use of cheap, off-the-shelf modules and low-cost build and manufacturing. Class D has come a long way since then, but you only need look at really serious gear and things become clear.
True high-end gear doesn’t need to be small, lightweight, efficient or affordable; it just needs to sound and perform THE BEST and be incredibly well-made. At the real high end, there are no advantages to using class D and many advantages to using the gold standard, class A. For this reason, you almost always find class A in high-end products, without exception.
Note that the real high-end does not include NuForce, Bakoon, B&O, NAD, Bel Canto, etc. This stuff is, almost without exception, junk, dressed up to look good. The Mark Levinson No 53 class D monoblocks are a rare exception, and Stereophile bravely described them as “disappointing and flat-sounding” despite their extraordinarily high cost.
Bottom Line
But Mike, lots of hi-fi gear is class D and I’ve read that it’s just fantastic.
Be wary of your sources, their conflicts of interest and clickbait like “Build the best amplifier in the world for $500”. I don’t know anyone who doesn’t want a $500 class D amplifier to be better than a $35,000 class A amplifier like my Accuphase A-75. The problem is, this is like wanting a Hyundai to be Ferrari.
Class D has come a long way in very recent years and better designs are coming to market all the time. Class D is a useful topology, but just know and understand why there are better choices when it comes to the best amplifiers. Science has the answers, always.
What parts wear out in hi-fi electronics?
Both electronic and mechanical components experience wear over time.
Electronic Components
Many will know that capacitors degrade over time, specifically wet aluminium electrolytic types. Wear rates vary according to type, quality of construction, thermal loading, age and hours of use. I’ve seen capacitors fail after 5 years and older parts that are still perfect after 50 years, which is extraordinary and common for Elna capacitors for example.
There is a ton of nonsense written about this and promulgated in forums, so choose your source of information carefully.
Transistors, diodes and resistors also deteriorate at different rates depending on the type and how they are used in a circuit and can fail, sometimes catastrophically. Failure tends to follow certain types, scenarios and the old nemesis – heat.
Some resistors are prone to increasing in value or becoming noisy. Likewise, certain small signal transistors and diodes are ‘fragile’ and commonly fail, others fail when pushed close to their voltage or thermal limits.
Testing is the only accurate way to determine whether deterioration has occurred and if so, how much. Parts can be tested, measured and replaced with new ones that meet or exceed OE specs in most cases.
Mechanical Components
Belts, gears, switches, potentiometers, knobs, meters and connectors are the most common mechanical parts that suffer from deterioration and wear. This includes rotary and linear controls and switches, speaker terminals, RCA connectors and so on.
Many of these components can be replaced and others are serviceable and can be brought back from non-functional to working perfectly, with the correct service techniques. Other parts like connectors can be replaced with new parts.
Is buying old hi-fi gear hi-fi risky?
There is some risk associated with buying anything, whether old or new.
I would argue that it can be even riskier buying modern, firmware-driven, plastic, made-in-China equipment that will likely fail within 5 years and at that point be completely unrepairable.
As long as you mitigate your risk, buying older hi-fi gear should not be any riskier than buying new equipment. It can be less risky to buy well-cared-for older gear than newer stuff in terms of long-term reliability. Now, do the manufacturers or stores want you to know that..? Of course not.
Much of the equipment I work on was made in the ’70s and ’80s and hasn’t failed catastrophically. Yes, it might need cleaning, service and adjustment, but everything does eventually. A lot of newer gear (Cambridge, Marantz, NAD etc) fails after such a short time that it’s embarrassing, for everyone.
You need to know what you are looking for and how to test older gear of course. This will involve listening to it and operating it. Beyond that, an inspection either pre or post-purchase is a very sensible idea and can potentially save a lot of money.
There are, unfortunately, people knowingly selling faulty gear, especially on GumTree. Be very careful and if in doubt, seek advice.
Do headshells, wires and mounting hardware make a difference?
They do, everything in the signal path and attached to a transducer like a cartridge makes a difference.
Materials and construction improve as one spends more on headshells, wires and mounting hardware. This translates to better detail retrieval and micro-resolution. Naturally, the higher your system resolution, the more noticeable these differences will be, which is why I focus on improving system resolution in consults with customers for example.
Wire
If you are spending decent money on a cartridge, you ought to put it on a decent headshell, with premium wires and have it perfectly, and correctly aligned. Note that these are not the same thing. I’ve found headshell wiring to be especially important and currently use SME silver headshell wires. They are the best I’ve found out of trying various Litz, 99.9999.% pure copper, and other wires.
Silver wire is generally a game changer wherever you use it, but it is costly. Other wires work well too, like Ortofon’s silver wires, Jelco’s Litz wires and some Audio Technica wires. I supply basic sets of wires that work very well, through to high-end wires, whatever you might like to use with your deck.
Headshells
I always suggest using the best headshell you can afford and ensuring that it matches the mass of the tonearm and the range of cart/headshell weight that your arm can support. Headshells are made from a variety of materials, some of them good and some not so good.
Ideally, you want materials that have a high stiffness-to-mass ratio and that can be perfectly accurately machined. This is why various alloys of aluminium and magnesium are commonly used and excellent materials for the job. Wood on the other hand cannot be precisely machined at these dimensions and has a poor stiffness to mass ratio. It is, therefore, a silly material for a headshell, but popular with hipsters.
Want to see what the best headshells are made of? Find some of the best headshells from the golden age of vinyl and see if you find a wooden one…
Fasteners
Fasteners and even the rubber gaskets at the headshell/tonearm interface are important and all of them contribute to the final result. There are two common materials for the fasteners: aluminium alloy and stainless steel. The materials have different densities and so fasteners of the same dimensions will have different masses.
This becomes important when looking at headshell mass and cartridge-tonearm matching. Part of my precision turntable setup process involves assessing the fasteners and replacing them with typoes better-optimised for the turntable and tonearm in question.
Structural Stuff
The general condition of the fixings, arm-headshell interface, turntable feet, miscellaneous screws, fasteners, cable dress, nearby equipment etc all play a part in overall performance, so these things should be considered. Likewise, the record-turntable interface is important which is why I recommend a quality peripheral record clamp, and central collet or mass-style clamps.
Advice
Good advice ties all this together as part of the system as a whole. There is so much pseudoscience and misinformation especially in the turntable space because many are new to it, even some of those working with turntables. Many turntables are hobbled by poor cartridge-tonearm matching, poor headshell, wires and fasteners, and of course poor setup and calibration.
How important is cartridge-tonearm matching?
Cartridge-tonearm matching is very important!
In fact, the match is so critical that improperly matched elements can lead to a dangerous condition that can damage vinyl and even potentially break a cartridge.
Why are there so many new belt-drive turntables?
A smart question to ask, belt-drive turntables are much cheaper to make.
Even small manufacturers can tool up to make a basic belt-drive turntable. You could just about make your own at home and that’s how many small manufacturers start out.
Direct-drive turntable manufacture is quite different though. It requires considerably more engineering and capital investment. Motors tend to be custom-made and need more than just a capacitor to drive them. There are benefits of course, but to the average person wanting a cheap turntable, these extra costs don’t make for cheap turntables.
Are low-power amplifiers acceptable in hi-fi systems?
It depends on the system, sometimes yes, usually no.
The sound pressure levels achievable with a hi-fi system come down to two parameters: amplifier power output and speaker sensitivity. Low-power amplifiers can create realistic sound pressures and dynamics, but only when partnered with sensitive speakers.
This all comes down to simple physics. A 20W or 30W per channel amplifier can’t offer high-fidelity dynamics and sound pressures with ‘normal’ sensitivity speakers, that is speakers with around 89 – 91dB/Watt sensitivity. It’s not physically possible. Hi-fi listening at low levels may be possible here, but scale and gravitas will be missing.
However, when you partner up a high-quality, low-power amplifier with high sensitivity speakers, say 93 – 98dB/Watt, then you can achieve real heavyweight dynamics and punch, so it’s a sliding scale. Trade one and you need another.
Likewise, traditional lower-sensitivity studio speakers will need a more powerful amplifier to drive them properly. Speakers with 85dB/Watt sensitivity for example will need a seriously beefy solid-state amplifier to drive them. This is inescapable.
This FAQ covers the concept in more detail.
Do you charge to install cartridges?
That depends on the circumstances.
Properly installing and setting up a cartridge with the right hardware and precisely calibrating overhang, azimuth, tracking force, anti-skate, VTA, arm lifter position and height using the correct tools is never a 5-minute job. It can take significant time with a complex deck/installation but no matter what the scenario, doing this work properly takes time and expertise.
With this in mind, we cannot fit and precision align all cartridges or customer-supplied cartridges for free. Doing so would cause us to lose money and that’s not sensible. We have a system that works well though.
We offer free precision installation and alignment of cartridges we supply with an RRP of $300 or more when you book your deck for any kind of maintenance. We absorb the cost of the installation and alignment, giving customers a better deal and encouraging the precision fitment of better cartridges. Try getting that from an online discounter!
We charge to install customer-supplied and low-cost cartridges we supply but you get a precision alignment and an opportunity to have your deck carefully inspected and precisely serviced and adjusted if you so wish, something that may never have been done before.
Keep in mind that many retailers cannot correctly install and set up cartridges and tonearms. I’ve lost track of the number of turntable set-ups I’ve corrected after being set up by major retailers.
I like your approach, you seem unafraid to call things as they are.
Not really a question but I genuinely appreciate the feedback!
I honestly believe life is too short to be anything other than authentic and decent. It’s definitely too short to be afraid of what others think of us.
A long time ago, I realised that I didn’t need to worry about trying to keep everyone happy or appealing to everyone. Instead, I embrace what I’m good at, that’s likely why you are here. I’ve also learned that none of us need tolerate with rudeness, disrespect or ingratitude and I embrace that philosophy in dealing with people.
People seem to appreciate this ‘straight shooter’ approach and I’m glad they do. It seems to attract decent visitors and amazing customers and out of 1000+ actual customers, there have been just a handful of doozies. I’m also pretty good at filtering people. I’m really only interested in what sensible, respectful people who appreciate my approach have to say. Others, I really don’t care!
I value feedback and overwhelmingly, people tell me they love the website and my approach to business. This helps me to improve the content and create things that I know people will appreciate. Running an independent business and having strong partnerships with other local businesses also means I can call out BS and nonsense where I find it, without fear or favour.
This site is an advertising/favour/marketing-free zone. Manufacturers don’t offer me products, I deliberately don’t do any warranty work and nobody tells me what to write, what to say or who to speak to.
Are second-hand cartridges worth buying?
Many of the best cartridges ever made hail from the golden era of analog, so yes, the right carts are definitely worth chasing down.
Types
To recap, there are two main types of cartridges: moving magnet and moving coil. The best cartridges tend to be moving coil designs and these are usually more expensive and better sounding. There are some great moving magnet designs too, but these are generally less worth a hard chase if you know what I mean.
Retipping
Cartridges wear out, so you need a way of establishing their current state of wear. That way you’ll know whether you’ve found a good deal or not. We inspect cartridges and an inspection and deep clean is often a great starting point.
If it is a moving magnet cartridge, can you still get a new stylus? Many stylus types haven’t been available for years. Old styli can be retipped, but this is less common with magnets.
Retipping starts at around $300 and goes up from there. Moving magnet cartridges are often worth less than this, so the availability of styli has always been a critical factor with moving magnet cartridges.
It’s a little different with moving coil cartridges. These must be retipped to rejuvenate them, they don’t have removable styli. Most MC carts are worth more than $300, new or vintage though, so the retipping becomes much more viable, especially when you consider that some moving coil cartridges cost as much as a car.
Cartridge suspensions also age and the rubber elements can harden. When this happens, that stylus (MM) or cartridge (MC) is finished. At that point, current manufacturers can rebuild the cartridge, with a new suspension, cantilever and stylus, for around 75% of the new replacement cartridge cost.
Value & Chasability
Because of their less disposable nature and greater purchase price, MC carts tend to be better made and it’s less common for their suspensions to harden with age, making vintage coils generally more viable prospects and well worth hunting down.
Not only that, but better MC designs tend to feature line contact, Microline or Shibata-type gems that last much longer. Putting all this together, MC carts are likelier to have life left in them. They are more worth re-tipping when they wear out. They last longer when they are retipped.
As an example, I own and use moving coil cartridges from the 1980s that work perfectly and sound amazing. Vintage cartridges came from the golden era of cartridge design and manufacture, so it’s worth considering that some of the very best cartridges of all time are those really good ones from the ’70s and ’80s.
Are second-hand records worth buying?
You bet, there are some awesome second-hand bargains to be had!
Sadly though, the golden days of $1, $2 and 5 records from the smoky second-hand record store in North Perth are long gone. Yes, you’ll still find $1 Engelbert Humperdinck records, but you’ll come across all sorts of other bargains second hand. Some will be relatively new releases, on heavy vinyl, from the record and hi-fi stores, and online sellers. Others will be older, lightweight pressings, but don’t let that put you off. Some of the best records I own are 120-gram pressings from the last 50 years.
Don’t make the mistake of thinking remasters are the only or best way to go either. Early pressings, from close to the original album release date, when all the copies in the analog chain were freshest, are often the most sought-after and best sounding of all.
What you want to do is check second-hand records carefully for scratches, flatness and clean them in most cases. Warped records can be flattened. Dirty records can be cleaned. How should you clean them? That’s the topic of another question..!
What are your thoughts about audio gurus?
I advise you to slowly back away from any guru implying they possess magical powers in relation to designing/repairing/improving audio gear, and run when safe to do so!
Magic
Audio gurus are generally associated with pseudoscience and nonsense, often claiming magical powers through ‘secret’ wiring skills, ‘special’ ultra-bad construction techniques and dollops of mystical horse-$hit. Goodness knows there’s enough bogus nonsense in this world. What’s needed is sound, reliable, fact/experience/science-based sources of information.
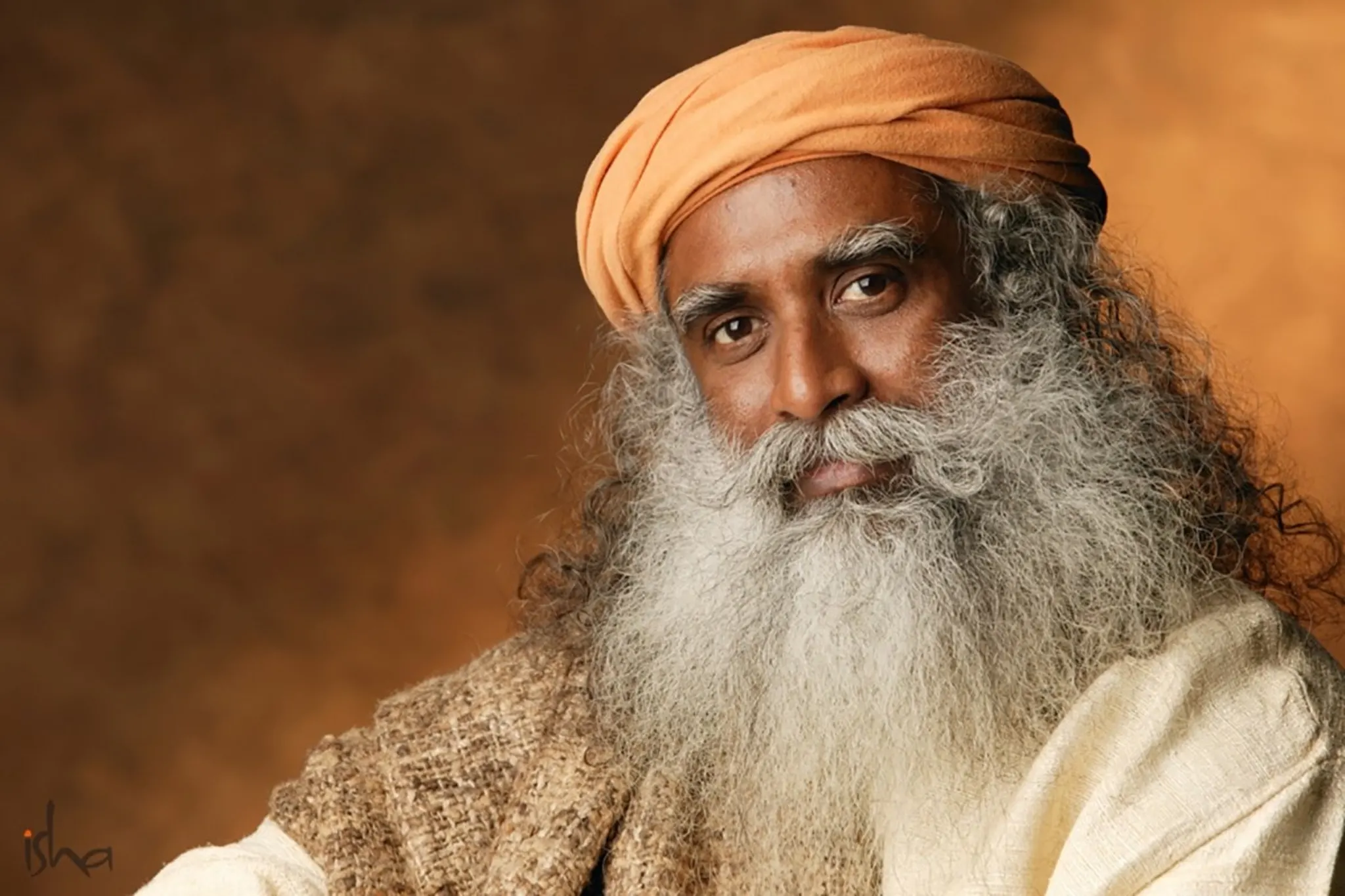
A customer very kindly told me that he thought I “work magic on turntables.” This is lovely feedback (thanks Rod), but nothing I do is even remotely magical. I’m anti-guru, anti-BS, pro-science and pro-expertise.
The results I achieve come from a scientific foundation and an understanding of what to do and how to do it. There’s no magic, snake oil, or white beard (yet). You might consider me knowledgable or skilled, but I have no special powers, I’m not a guru, and I don’t claim to be better than anyone else. I’m competent in my sphere of operation and learning all the time. There’s a big difference.
Audio Guru BS
There are self-proclaimed audio gurus everywhere. They generally propagate snake oil, nonsense and badly made hi-fi gear. If you want to buy a homemade valve amp or guru-made cables, that’s OK, but don’t expect a competent technician to look at them when they break or break something else in your system. I’ve been there, but never again, I refuse all such products now as a blanket rule.
Let me help you identify these people so you can save yourself time and money. These audio guru – ie audio numpty – utterings should ring alarm bells:
- Precision instruments, tools, soldering equipment etc are “unnecessary”
- Technical documentation is unnecessary
- Cables either don’t matter or matter more than life itself and must be made by gurus
- Neatness and precision are “over-rated”
- Build quality is also over-rated
- Build quality does matter, but our gear looks so bad because it has been “modified by someone else”
- Engineering, science, measurement etc are overrated
- The more terribly wired something is the more skillfully wired it is
- Properly engineered, name-brand products are no good or part of a “conspiracy”
- Calling out poorly made equipment or terrible repairers is somehow “bad”
- The best cables are directional and need special magic supports
- Guru-made gear is essential to reach audio nirvana, etc, etc
You’ll note the pattern of ‘guru thinking’ here: all the critically important things like care, effort, neatness, knowledge and skill, don’t seem to matter to these guys, and yes, they are always guys. This thinking is beyond stupid, it’s idiocy. I won’t share details of the conversations my colleagues and I have about such things, but you can guess the gist.
Ask anyone with real expertise and skill if quality parts, tools and neat work are overrated. Ask someone working in the aerospace industry if wiring neatness and tool quality “matter”. I don’t know how those pedalling BS like this survive, but people are gullible and these gurus prey on folks like this.
How can vintage audio gear and formats sound so good?
I’d like you to consider something: we put men on the Moon in 1969, more than 55 years ago.
There are three key points here:
- Men
- Walking on the moon
- in 1969..!
Take a moment to process that. Do you reckon we could do it now..? I seriously have my doubts, but either way, it tells you a great deal about the state of design and engineering in the ’60s and ’70s.
I should add that Voyager space probes with their gold-plated records have already left the solar system. One of these probes still works, sending signals back to Earth from nearly 20 BILLION km away. Probes also landed on Mars. In the ’70s…
Think about these achievements. Ponder the materials, science, electronics and all-around engineering genius necessary to achieve these feats. Analog audio is fairly straightforward by comparison and a quick scan of the annals of hi-fi history shows that some spectacularly good equipment came out around this time and even earlier.
You see, people often incorrectly assume that all the technological improvements we’ve made since we put people on the Moon directly correlate with improvements in audio. Some do, but many, even most, don’t. We had the technology and engineering to make extraordinary equipment and recordings, way back in the 1950s.
Some of the very best recordings were made with valve microphones, direct-to-tape in the ’50s and ’60s. The audio spectrum is quite narrow and technically not that hard to reproduce. Dynamic range is where things get trickier, but magnetic tape running at 15IPS can do it and vinyl does an admirable job of reproducing it.
Sure, consoles and equipment have continued to improve, but the formats – reel-to-reel tape and vinyl – remain as good as they always were. Arguably the hardware, ie tape machines, valve microphones, cabling etc was better then.
There have undoubtedly been some major improvements in transistors, integrated circuits, DACs and so on. But there have also been increases in wages and conditions which have seen the need to automate and simplify production and move away from expensive metal and glass construction, in favour of cheaper plastic-based materials and machine assembly. Stuff costs less but doesn’t last as long either.
I’m not for a moment saying all old gear and formats sound better, because they don’t. The Compact Cassette is a good example. It’s fundamentally flawed and really only sounded good towards the end of its life. Vinyl on the other hand has always sounded great and always will, because of its inherently high resolution.
I have a few of my Mum’s records from the ’50s and they are some of the very best recordings I own. Again, think about that. My system sounds unbelievable and some of my best recordings are from the 1950s. Extraordinary, but true.
High-resolution digital is where things have really come a long way, but even good old Redbook CD can sound excellent, outstanding even, with the right equipment.
What’s the highest fidelity, highest resolution music source I can access at home?
As of 2023, it’s either magnetic tape running at 15 IPS, an excellent vinyl playback system, or the best hi-resolution digital files played back through seriously good DACs.
People are often upset to learn that their favourite digital files were originally recorded onto analog tape, but there is more obscuring of the provenance of digital files than just about anywhere else in hi-fi. Why? Because there is money to be made by people NOT understanding this point. Do I need to mention the Mofi lawsuit to jog people’s memories..?
Digital sound involves sampling, whereby resolution is lost when a digital copy is made of an analog file. The highest resolution source you can access is the highest quality non-sampled analog source file. The highest-resolution analog medium is high-speed reel-to-reel tape, closely followed by vinyl.
Reel to Reel Tape – The Ultimate #1
Not cassette tape, I’m talking proper reel-to-reel tape running at high speed. Let’s not forget that most of your favourite recordings were made on tape and the very best recordings of all time were made on tape. Anyone who’s ever heard a good reel-to-reel tape played on a good machine will know what I’m talking about. There’s a richness, fluidity and power in the tape that has to be heard to be believed. Once you’ve heard it, you’ll immediately understand.
Herein lies the problem though – how do you hear this? You need a high-quality reel-to-reel tape machine and some extraordinary and very expensive Tape Project tapes, or similar. There are very few tape releases available and really, this is almost a dead end unless you can access the tapes. So for most people, this is a dead end.
Vinyl – the Ultimate #2
The second top-tier source is vinyl. Vinyl is another analog medium, ie it presents a copy of the original file, not a sampled version. Good vinyl played on a great turntable, arm and cartridge is close to reel-to-reel in terms of resolution and detail retrieval. The limiting factors are the hardware and pressings. With analog sources and gear, you get what you pay for and it’s a sliding scale. The resolution possible with a good vinyl set-up though is incredible.
Hi-Res Digital – the Ultimate #3
Some readers will be bemused by the fact that I’ve listed this as the third level of ultimate, but that’s only because source files are so variable and their provenance so guarded that one often doesn’t know what one is getting. It’s also because the sound of these files is very hardware-dependent. That being said, high-resolution digital files can sound excellent or even outstanding and hard on the heels of analog. By high-resolution, I’m referring to files with 24-bit/192kHz, DSD, SACD resolution or greater and MQA encoding for example.
Lossless is a misused term, however, because all digital methodologies involve some loss, through how they sample the original. Most streaming services like Apple have switched to lossless for their entire catalogue and many files are now also offered at high-res lossless quality. Whilst it’s unclear what constitutes ‘high-res’ over at Apple, we can assume it to mean source files where the data is encoded at greater than Redbook CD, ie 16-bit 44.1kHz resolution.
Redbook (CD)
Next comes Redbook CD. Not quite an ultimate source, CD still has a lot to offer and I’m amazed by how much one can get from 16-bit / 44.1kHz files. I have some superb-sounding CDs and played on a good transport and DAC, they can sound fantastic. Many would argue, myself included, that CDs played back via a really good CD player and or DAC sound better than many/most streamed hi-res files. If you haven’t done so, this is worth investigating and CDs are becoming quite collectible for this and other reasons.
Cassette & FM Radio
Compact cassette tapes and analog FM radio are probably the last in terms of being real hi-fi. Both offer good to excellent performance but are very hardware-dependent. A good FM tuner can sound fantastic though.
What should I look for when buying second-hand hi-fi gear?
Mostly its overall condition, control functionality and service history.
It might sound obvious, but the physical condition of a piece of second-hand hi-fi gear tells us a lot about how it’s been looked after. Gear that has been well cared for is almost always a better bet than gear that’s been neglected, other things being equal.
This extends to service history. All equipment needs periodic maintenance and parts replacement. Can the seller show you any records or invoices for past work? Has this work been done by a reputable technician? Older gear can need extensive maintenance. Don’t let this put you off, it’s still often much better value than buying new, but the work HAS to be done.
Performance – I suggest almost never buying something you can’t see and hear running. Anyone who says they can’t show you something running should be avoided – like the plague. Are you going to just take the word of a random seller that the equipment works well..? I wouldn’t.
Does the equipment turn on and run smoothly? Does it sound good? Do all the controls and switches work as they should? These are all things that can be checked prior to purchase. How about a warranty? If buying from a business, there will be some kind of warranty against defects. This can be very helpful. Some non-business sellers will offer returns if there are problems but this is rare.
Hi-fi equipment purchases should be made with a cool head. It might be rare and collectible, but if it’s broken, it might also be the world’s most expensive doorstop, and we don’t want that!
Why are you often fully booked?
I’m frequently told that our reputation, professionalism and trusted approach to working with classic hi-fi equipment are responsible.
It’s also because we are a specialist small business, working diligently to preserve classic hi-fi stereo equipment, in a small industry, with few genuinely respected operators.
Reputation
I’m honoured to assist customers Australia-wide and beyond, incredibly proud of the hi-fi community’s trust in us, and thrilled to be entrusted with so much beautiful hi-fi equipment. Some of Perth’s best hi-fi retailers recommend/use Liquid Audio. We’ve also been offered several service partnerships for prestige brands, which I’ve so far declined. *
Liquid Audio is widely respected for benchmark attention to detail, professionalism, service, value-for-money, consumer advocacy and contributions to the hi-fi community. A reputation like this can’t just be ‘crafted’ though; it must be earned, something we’ve done with hard work, original thinking, professionalism and dedication to excellence since 2009.
Strangely, we are respected as much for what we don’t do. Some technical businesses ironically do awful work. Our consumer advocacy outing such businesses has saved countless others from falling victim. NOT accumulating terrible reviews, court cases, multiple business name changes, a long list of destroyed equipment, ranting at customers, stealing work and ideas, spewing nonsense, and having little education or technical skill certainly helps Liquid Audio stand out!
Our successful approach is, unsurprisingly, often emulated. I’ve spotted my designs/words/repairs/style in many places over the years, without acknowledgement. You’ve likely seen various examples without realising it. Creating and doing everything yourself is hard, but that authenticity cannot be replicated. Content can be mimicked, but creativity, integrity, professionalism, and workmanship cannot. **
* With the benefit of hindsight, I possibly should have accepted one famous UK brand repair partnership.
** The copycats know who they are, as does the Wayback Machine 😉
Difference
I designed Liquid Audio to deliver what many others can’t. Growing up, I longed for a hi-fi repair business with a skilled, passionate owner who knew his stuff, but there weren’t any. Fuelled by my passion for music, hi-fi, electronics, all things technical and my unhealthy obsession with detail, my goal was to offer just that: a specialist business with the flair, skill, passion and professionalism so often missing in the electronics repair space.
It still amazes me that my tiny Perth-based specialist business is overflowing with local and interstate work, despite the costs of shipping it here, and with no advertising or paid-for ‘reviews’. This high customer engagement and loyalty demonstrate that people appreciate what we’re doing. This site was visited nearly 400,000 times in 2024, and we have five million views here and on YouTube. These would be great numbers for a large business, let alone a one-man operation!
Authenticity and professionalism are key. You’ll NEVER find me ranting at customers or arguing with people online. Nothing is ever farmed out, as one notoriously bad Perth repairer does. Everything you see here, including this entire website, is done here, by me, nobody else.
Despite all this, we don’t please everyone, nobody can or should try.
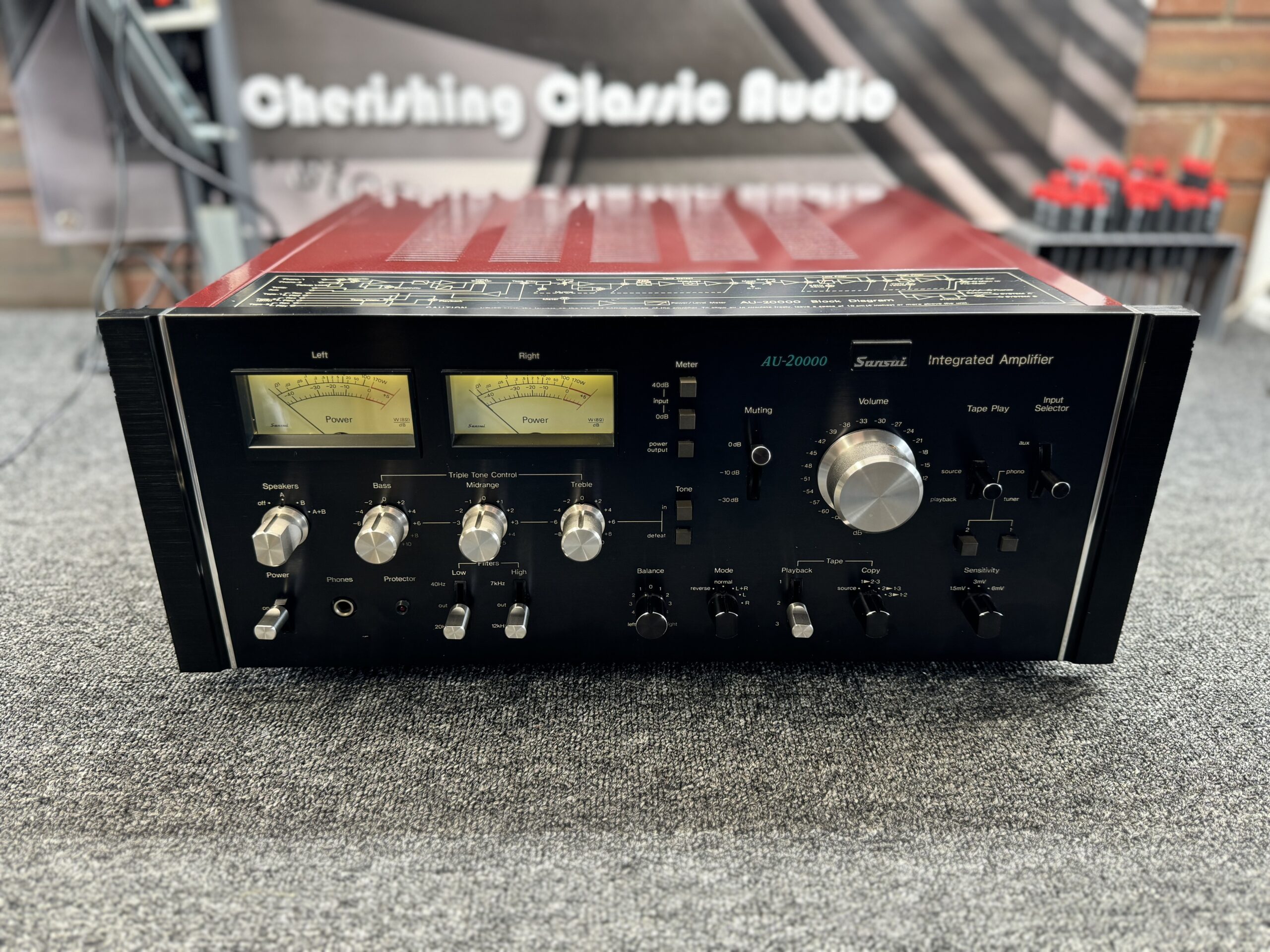
Best Practice
The following aspects of our approach seem to resonate with people:
- Our mantra: create, inform, add value, never harm
- We’ve served the hi-fi community under the same name since 2008
- We are dedicated to technical excellence
- We inspect equipment rather than guess about its condition/faults
- We advise when equipment is damaged or not viable to repair
- We recycle dead hi-fi equipment to be enjoyed again by others
- We champion integrity, professionalism, quality and value
- We care for Akai and Accuphase to Kenwood and Krell
- We specialise in component-level repair
- We advocate for improved industry standards
- We build long-term relationships with customers, distributors and manufacturers
- We created a unique, free 650,000+ word, 500+ article and video resource
- I’ve spent a lifetime in science and I love, live and breathe electronics, hi-fi, music and all things technical!
My Apologies!
Doing things differently means we will always be busy, and I apologise for any delays this may cause. I genuinely appreciate your interest in our services and encourage you to use our booking status table. Don’t hesitate to reach out if you have questions.
I’m thinking of using the cheapest repairer, what are your thoughts?
Well, like most people, I understand that cheap rarely equates to good.
Cheap builders, cheap Chinese motorcycles, cheap hi-fi gear, cheap professionals and technical personnel – adages like “the poor man pays twice” exist for a reason. Growing up, my Dad always used to tell me:
You get what you pay for, Mike.
AJ Fitzpatrick
Dad was right and those wise words have stayed with me, influencing my decisions to this day and embedded in the way I run Liquid Audio.
A much better question to ask is:
Do you want a job done cheaply or do you want it done well?
You certainly don’t have to pay a fortune or seek out the most expensive repairer, for example, to ensure work is done well, but seeking out the cheapest ones almost guarantees that it won’t be. That’s the takeaway.
False Economy
Cutting costs means cutting corners and cutting quality. The people who think corner-cutting is OK are neither the customers I serve nor the people you want doing mission-critical work on cherished hi-fi equipment, someone’s brain, legal documents, aircraft or a Rolex watch. It is that simple.
We see this play out with dodgy builders, mechanics and botched cosmetic surgery; it’s everywhere and always produces the same results. People looking for the cheapest way to do something inevitably realise that the cheapest way is usually the worst and most expensive way to do something.
This premise is well-understood, yet the temptation of blind quotes and the lowest price often sucks people in, without any critical thinking around what they might actually mean. Blame must, unfortunately, be apportioned not only on the perpetrators but also on those driving this ‘lowest price’ mentality.
Real Value
Equipment like the AU-317 above that visits the cheapest repairers usually needs to visit others for rectification. Seemingly cheap repairs deliver predictable results: shortcuts, BS and poor workmanship, ‘Swell-Long’ capacitors (I’m serious), devalued, damaged, or destroyed equipment and sometimes even court cases. Thankfully, none for me in 15 years, and there’s a reason for that.
All this is amusing, maybe, until you or someone you know falls fall victim. Worst of all, it’s always more costly than simply having the work done properly in the first place. The bad reviews, crazed responses, changing business names and court records tell the story. It’s all out there. Buyer beware.
Quality, professionalism and results are things most customers remember long after they’ve forgotten the cost of a repair. This constitutes real value. My approach is often copied because even the worst corner-cutters eventually learn the value of a quality-focused approach and most grow to hate the court cases..!
Are there any decent, affordable new turntables?
Yes, though this answer depends on what one considers decent and affordable.
Those looking for new high-performance machines for under $1,000 will find very little of interest. High-performance turntabling can’t be done for $1K new; spend a little more, though, and things start to improve. If you broaden your horizons to include pre-owned equipment, then $1,000 gets you something much more interesting.
Decent, New
- The Pioneer PLX-1000, at around $1100 and 15kg, is a good value new option. No, it’s not high-end, but it’s a little over a grand. It’s cheap and cheerful, like some of the Audio Technica decks.
- You might find the occasional Technics SL-1200 Mk7 on special from online sellers, though by now these have probably dried up. For around $1600, this is the best deal up to about $3K.
- A new Technics SL-1210GR at around $3,000 AUD is good value if you want a new deck. Just keep in mind that you will get a far better machine on the secondhand market for the same money.
- The new Technics SL-1500 is worth considering at around $2,000 AUD, discounted to $1,500. It’s a basic deck, but solid value, though the plastic tonearm base irritates me at the price.
- The MoFi StudioDeck for around $2,000 is also a decent value. Be careful of the loose bearings I’ve found in a few of these now though.
- The MoFi UltraDeck is a much better turntable, though perhaps not what most consider affordable.
- The Rega Planar 3 is a belt-drive classic for around $1,500. This is a solid value, not a high-precision deck by any means but they sound decent. Don’t go lower than a Planar 3 in Rega’s lineup, though.
- If you are on a really tight budget, you might consider the Audio Technica AT-LPW40WN, what a mouthful, but I wouldn’t go any lower than this, new.
- Better from Audio Technica would be the direct drive AT-LP140XP. This deck crushes cheap sub-$500 junk.
- Sub-$500 ProJect, Thorens, Denon and other cheap turntables are generally not worth buying, especially when you consider that you can buy a decent golden-era deck for $500.
- Crosley, Marley and other plastic junk should be avoided if you care about your records and how they sound.
Best Options
The only new deck I could live with here is the SL-1210GR. Spending around three grand gets you a heck of a lot of second-hand golden-age vinyl goodness, so keep this in mind. You could find a Kenwood KD-650 for much less than that or even a Yamaha GT-2000 for that money, and these are altogether better options. The real value, as always, is on the second-hand market.
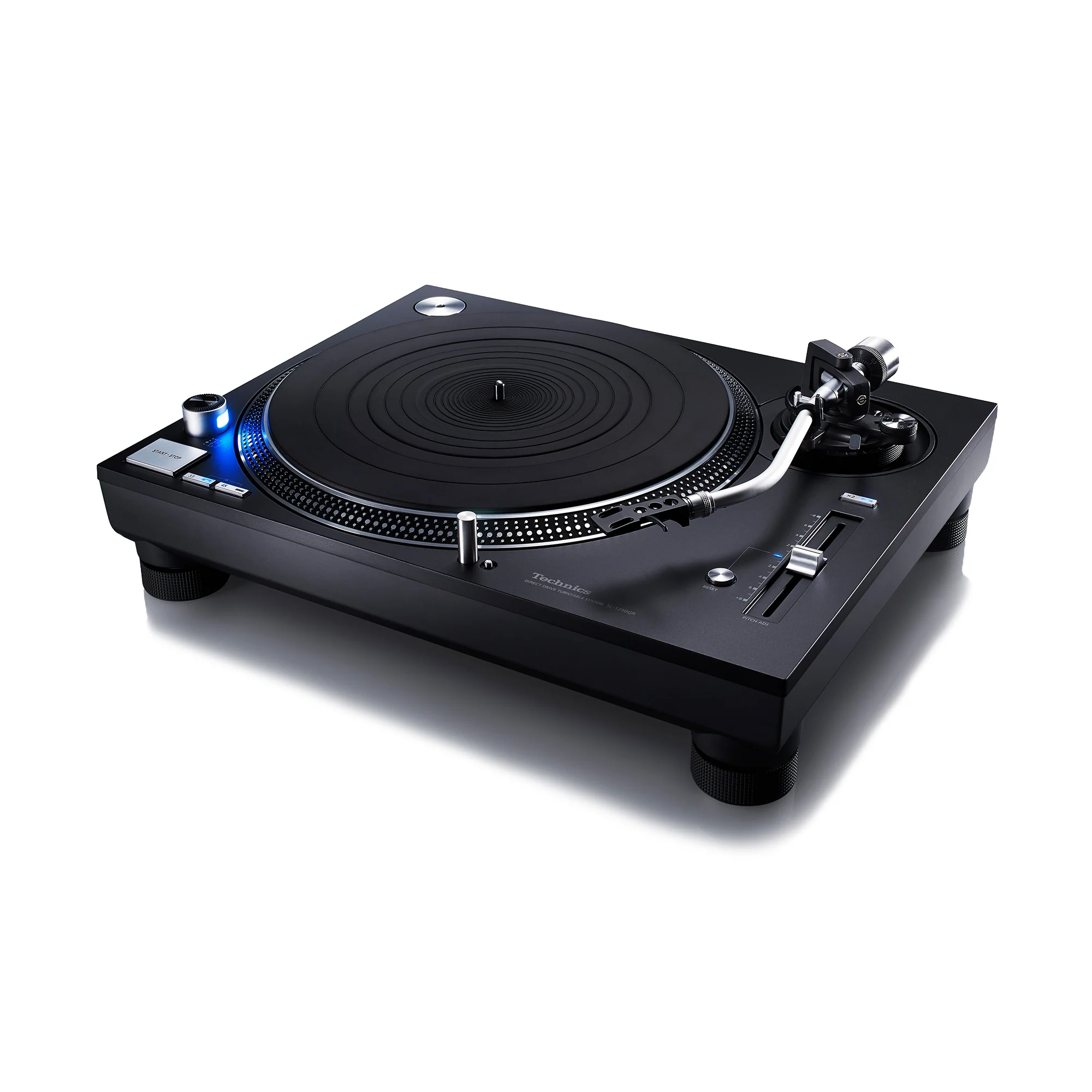
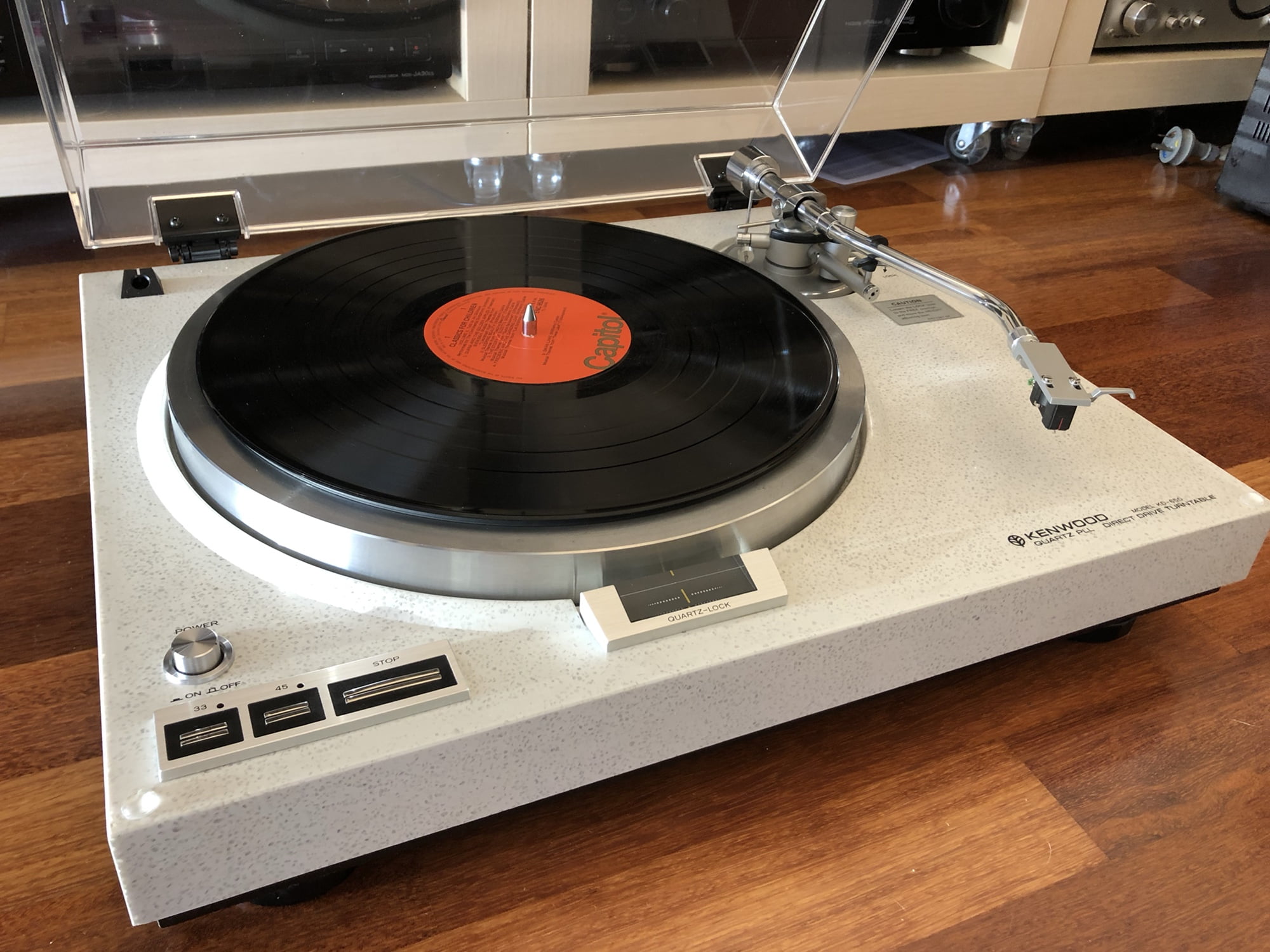
What do you recommend in terms of power supplies for hi-fi gear in older premises?
Power can be a real issue in older houses, so here are a few suggestions.
The first might seem obvious, but have everything checked and tested by a qualified electrician. This can identify and rectify wiring and ground issues, broken outlets etc. Power outlet testers like this one allow end-users to identify miswired outlets, ground problems and so on and are a good starting point.
Next, assuming you have safe, correctly wired outlets, you need quality power distribution. Multiple wall outlets are best, so ask an electrician or your landlord if this is a possibility. Failing that, I suggest the best powerboard you can afford. One bigger one is better than daisy-chaining them, which should be avoided.
Amplifiers and other high current equipment should ideally be plugged into the wall directly, rather than through a power board, where possible. Older gear may have grounds/earths lifted or removed, so this must also be carefully checked for safety and performance reasons.
Mains filters are useful in some cases and can be purchased from hi-fi stores. These may reduce noise and improve system performance. Regenerators offer the best performance but are also very expensive and usually not suited to high current devices.
How long does a stylus last?
Anywhere from 200 to 2000 hours, depending on the cartridge design and stylus profile.
I’ve written about this elsewhere, but the increased contact area of line contact gems leads to lower contact pressure, less friction, lower wear and better sound. The best line-contact types can last 2000 hours or more, but line-contact styli are more expensive to manufacture, so there is a price to pay. By contrast, cheap spherical/conical and elliptical styli generally only last for 200 – 300 hours. So you could get 5 – 10 times more life from a really good cartridge/stylus, which can more than offset their increased cost.
Other factors must be considered, including poorly designed, low-quality turntables and older types with excessive tracking force. These can experience more rapid stylus wear, and cause accelerated record wear. Even the best cartridges, tracked at lower than recommended tracking forces, can experience accelerated record and stylus wear.
It’s important to replace a stylus before it becomes worn or it will destroy your records. For moving magnet cartridges, this is fairly straightforward, as long as a quality replacement can be sourced. I often supply quality Japanese JICO and Nagaoka styli for older cartridges.
For moving coil cartridges, stylus replacement involves bonding a new diamond to the existing cantilever or installing a new cantilever and diamond. Several vendors provide this service.
Does hi-fi equipment need to be overhauled?
Eventually yes, if you want to keep it running.
Watches, power tools, motorcycles and electronic equipment all eventually need to be overhauled and/or restored, and this applies to everything built by human hands. This is not to say YOU need to have your equipment overhauled, but eventually, someone will, assuming they see the value in keeping the equipment we love alive and well.
Older hi-fi gear is generally reliable and longer lasting than newer gear. However, there is no escaping that eventually, someone HAS to spend money to have it overhauled or restored. That should preferably be done before it fails, taking out speakers, output devices, catching fire etc. If you love a piece of equipment, consider giving it some TLC before that happens!
Why don’t you repair home cinema equipment?
Very simply, this type of equipment is often almost worthless after just a few years and therefore not worth repairing.
If you add in poor serviceability and poor audio performance, compared to even modest hi-fi stereo gear, you end up with very few reasons to repair this stuff and why mjuch of it is simply thrown away when it breaks. Don’t shoot the messenger, these are facts.
I always ask one critical question about equipment being considered for repair:
“Is repair economically viable?”
Even some of the cheapest hi-fi gear from the ’70s is sought after for its performance, reliability and serviceability. The same cannot be said for the plethora of average sounding, cheaply-made and obsolete home cinema equipment from the last 30 years or so.
Most of it is essentially worthless after just a few years due to useless feature creep and poor serviceability which kill retained value and therefore repair viability. Most of this gear is at best only marginally serviceable, because:
- Much of it is so cheap or now worth so little that it’s barely worth opening, let alone repairing
- Critical parts are often no longer available and SMD chip-based boards like HDMI controllers are not designed to be repaired
There are some notable exceptions, but generally, I’d suggest you forget about repairing home cinema gear.
Are analog AM/FM tuners still a viable hi-fi source?
They definitely are in the case of analog FM, but there are four key considerations.
The first and most obvious one is the contingency that broadcasters continue to use the analog 88 – 108 MHz FM band in Australia and elsewhere. Once these broadcasts cease, that’s it.
The second is less obvious and that’s source material quality. With good, uncompressed source material, the quality achievable with really good FM tuners is extraordinary. Stations like ABC Classical and some of the smaller independent stations playing CDs and records can deliver excellent sound quality via a quality analog tuner, much better than the compressed, lossy streams on DAB or digital radio.
My beloved Marantz 125 tuner never ceases to amaze me with its richness and space, playing stations like these, even when they are sometimes digital streams being re-broadcast. It has a lot to do with how they are produced. However, many commercial stations, run compressed, thin-sounding streams that sound bad on whatever you play them – DAB or analog FM.
Third, the antenna is critically important with analog FM tuners. A proper roof-mounted FM antenna will boost signal strength, reducing distortion, multipath signal issues and noise for the cleanest reception and best sound quality. Without a good rooftop antenna, you will not achieve full quieting and maximum noise and distortion performance.
The fourth consideration is tuner alignment. AM/FM tuners often have between 10, 20 or even 30 separate alignment stages that require high-performance RF alignment equipment, and a deep knowledge of how to use it. These alignments need to be done periodically, say every 10 – 20 years, as components age and change.
Good tuners, properly aligned often have 0.1% distortion or less. If you haven’t heard a really good, well-aligned and well-fed analog FM tuner playing a good broadcast, you need to before it’s too late! As you might expect, being a radio nut, I have this equipment. The work is involved though and utilises some fairly kooky test and measurement gear. Whilst I have most of what’s needed in most cases, I may not be able to align every tuner.
Can I get hi-fi sound from streaming services like Apple Music and Spotify?
Not from Spotify, but with Apple’s new Lossless services, yes you can!
Apple has finally updated its streaming music service and released Apple Lossless files across the board, with at least CD quality uncompressed, lossless 16-bit / 44.1kHz files, with some offered at up to 24-bit / 192kHz. You can now get hi-fi sound from streaming services without any additional cost in Apple’s case.
You’ll need wifi and/or a hard-wired connection to a phone or streamer to access the high-resolution files. A streamer, computer/DAC or phone/DAC combo as I use will work well. Bluetooth won’t pass these high-resolution files due to the bandwidth limits. Bluetooth sucks anyway, best off to use a hardwired connection I reckon.
I currently use my iPhone 13 Pro Max connected to a Gustard A26 High-Performance DAC with MQA decoding. This combo sounds phenomenal, as you might expect. Many are still surprised to learn that lower-resolution 16-bit / 44.1kHz Redbook files can sound better than streamed high-resolution files, but discovering all this is part of the fun. If you access really good high-res files though and have a DAC capable of extracting that resolution, and many are not, the results can be amazing.
Tidal High Resolution also offers true high fidelity, though it’s a bit more expensive. The standard 256kbps files you’ll find from providers like Spotify are not hi-fi. Their limitations are obvious, sounding thin, grainy and lifeless.
Do you offer in-home auditions on equipment for sale?
Generally not, though it depends on the circumstances.
Much of the equipment in the Store is on consignment and, as you might imagine, I look after such equipment very carefully for my customers! That being said, every case is unique and there is some room to move with equipment you are seriously considering purchasing, where an in-home audition is important and where payment is made upfront.
What’s the deal with inner groove distortion?
Without getting too technical, as a cartridge mounted to a radially tracking tonearm moves across the record, playback distortion characteristics change with changing tracking error.
Generally, the highest distortion is found playing the innermost grooves of a record. There will be two points with the lowest distortion, where the radial arc traced by the arm intersects a radius from the centre of the record. On either side of those two points, distortion will rapidly increase.
What you may not know is that certain stylus profiles and cartridge alignments minimise inner groove distortion. In fact, you can ask me to specifically align your cartridge so that it minimises inner groove distortion, though I generally recommend using the manufacturer’s specified alignment in most cases.
Note that linear tracking tonearms don’t suffer from this positionally variable distortion as they don’t trace an arc as they move across the record surface. This is a key benefit of linear tracking arms. It’s also why longer tonearms are preferable. The arc they trace has a greater radius and is, therefore, closer to a straight line, leading to lower variation in distortion across the record.
Can I bring my equipment to Liquid Audio if it’s already been to other repairers?
In most cases, yes, but it comes down to whether your equipment has been damaged, and if it has, how badly.
Unfortunately, certain repairers do such poor work that I may decline to look at the equipment they’ve touched. Why? Because the damage inflicted by certain individuals often renders further work difficult, not viable or even impossible in the worst cases. It’s not reasonable for these issues to become the next well-intentioned repairers problem and unfortunately, all good repairers will know exactly what I’m talking about.
Take a look around the Hall of Shame to better understand what I mean. All of the equipment featured there was very repairable before someone ruined it. If circuit boards have been destroyed, for example, I will often decline to work on a piece of equipment.
What’s better: a vintage turntable or a new one?
Assuming you have around $1000 to spend, this gets you a far better vintage turntable than a new one, assuming the vintage deck is in good working order.
There actually isn’t anything I can strongly recommend for $1000 new, unfortunately. But, that same amount of money would get you a decent Technics SL-23, SL-120, SL-1200, SL-1300, SL-1500, Kenwood KD-500, KD550, Sony PS-4750, maybe even a PS-6750, Sonab 85S, Yamaha YP-701, Rega Planar 3 with decent cartridge, and on it goes.
As I often tell people, the golden age of vinyl has already happened and, even though there are some great new turntables and vinyl coming out, the real value is in these classic and beautifully made vintage machines from years past. For now anyway!
What’s better: an older CD player or a new one?
A VERY good question, with an answer that depends on what you value, but for most people, it will be an older CD player.
Let me instead ask you this: What’s better: a CD player that is beautifully built, reliable over decades and sounds great, or a player that only sounds great, but lacks the beautiful build quality of older machines and will almost certainly fail after only a handful of years?
Carefully consider this question because, in a nutshell, it reflects where we’ve arrived in consumer CD player land. Even two grand these days buys you fancy-looking plastic garbage, so deciding what’s better for you means understanding what’s changed. You ain’t going to get that from a salesperson, unfortunately, so as we do here @ Liquid Audio, allow me to assist.
I realise that CD lovers have become aware of this article via the renewed interest in CDs and perhaps because this article has been linked somewhere on the interwebs. This article and others like it are written specifically for people like you who appreciate these enduring little silver discs and the hardware that plays them.
The Golden Era
In terms of build quality, serviceability, service life and ‘vintage goodness’, older CD players are almost always better and nicer to own than new ones. Even in terms of sound quality, older players often sound superb, sometimes better than expensive new ones. When you consider that CD playback technology was matured by the naughties, this is not incredibly surprising.
Just as I keep saying that you want a turntable from the golden age of analog, you should try to find a really good CD player from the golden age of CD. It makes sense when you think about it. And when is the golden age of CD? For me, it’s a roughly 20-year period from the late ’80s through to around 2007.
Newer players can sound great if you spend decent money. This is mostly due to improvements in DAC architecture, but that’s about all that’s improved in terms of Redbook CD playback. It’s not easy to find great-sounding affordable players, and I’ve noticed that many newer players sound thin, etched and lack body. There’s nothing worse than a thin-sounding source, even if it is as smooth as you like, so keep this in mind.
Whether old or new, a CD player + stand-alone DAC are almost always the best way to go anyway. Other things like lasers, power supplies, loaders (mechanism), build quality, and serviceability are critically important in a CD player. These elements are rarely as well designed and implemented as they were in older players. Newer CD players often don’t last much more than five years, vs. sometimes 40 years for players I work on that still run well and herein lies the point: older players are generally much better built, more reliable and longer-lasting.
Let’s look at a few examples:
A Modern CD player…
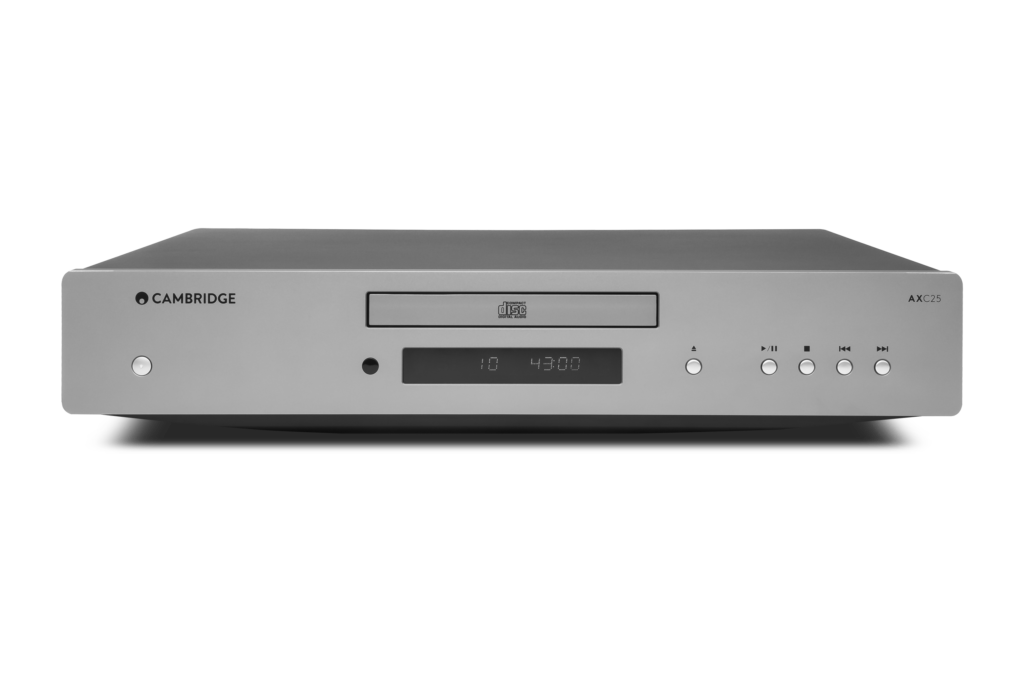
THIS is a CD Player:
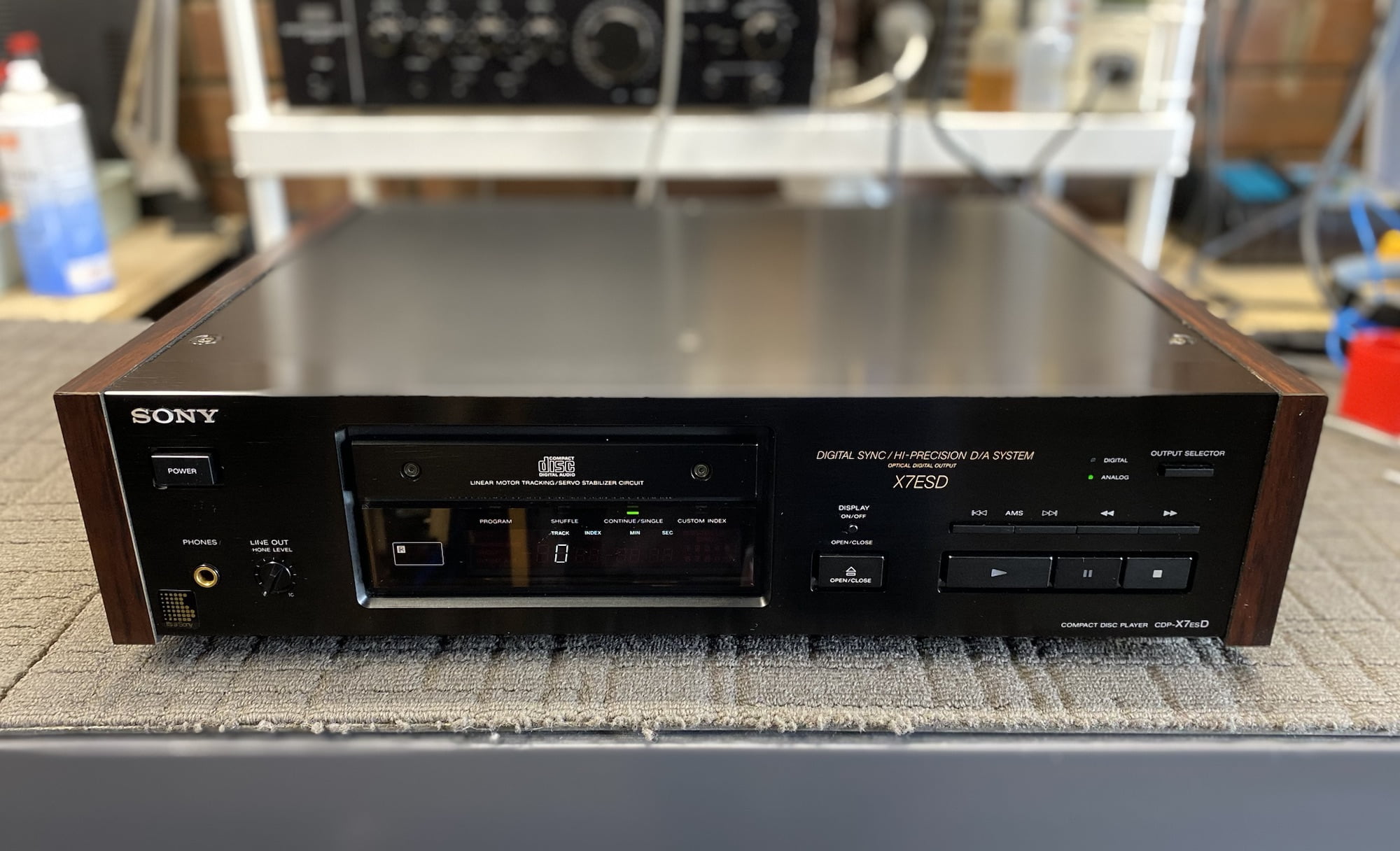
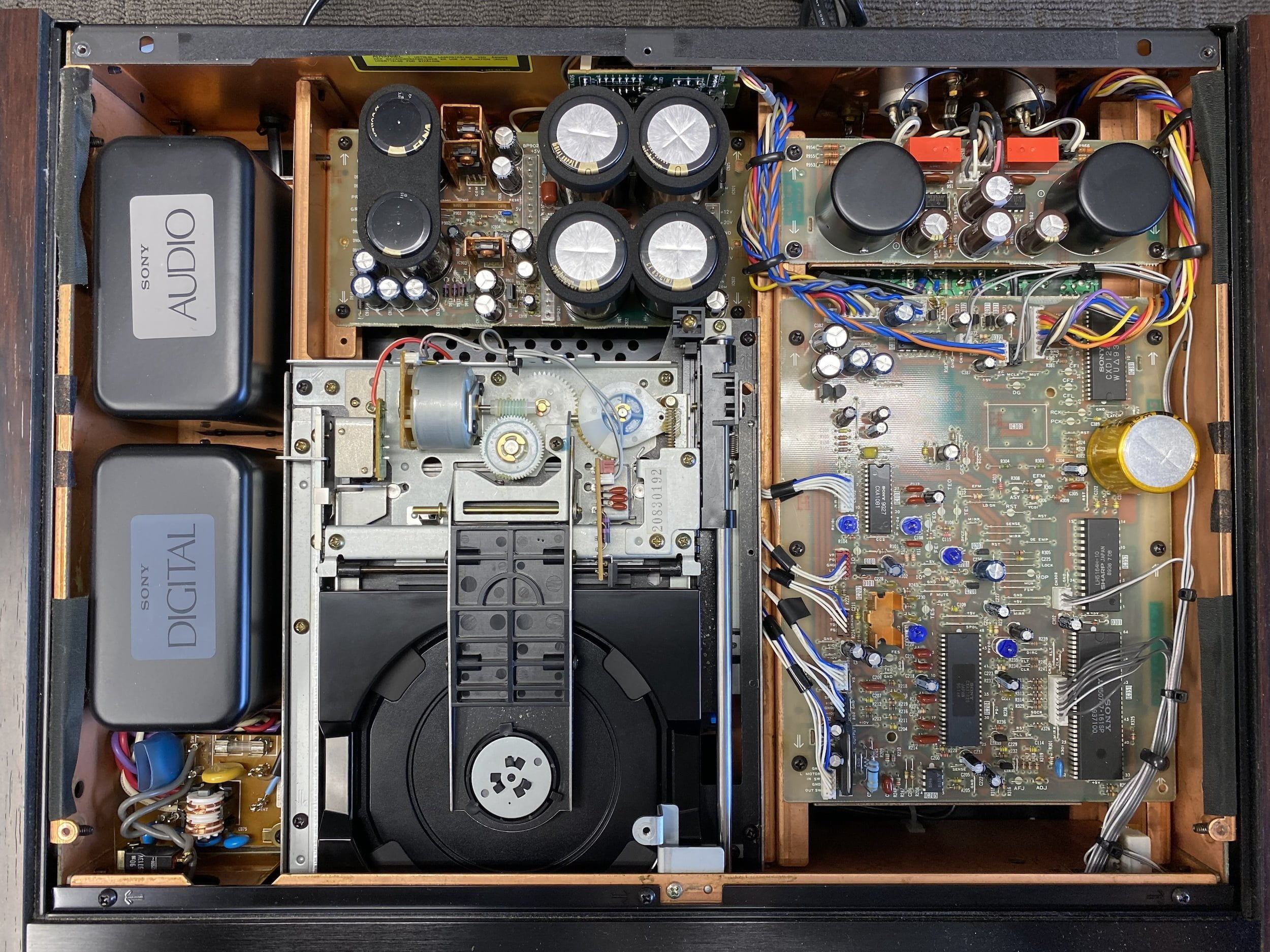
The Sony CDP-X7ESD features transformers for balanced audio outputs, separate analog and digital power transformers, premium parts and metal construction. It is fully serviceable and still runs perfectly, all these years later in 2024. This was a high water mark and I assure you that NO modern players are built like this. They don’t manufacture bespoke laser mechanisms like this anymore.
It’s worth noting that when used as an integrated player via its onboard DAC, it sounds veiled and lacks resolution compared to the best Redbook CD equipment I’ve heard. These limitations are easily resolved with a nice modern DAC though. See how easy this is?!
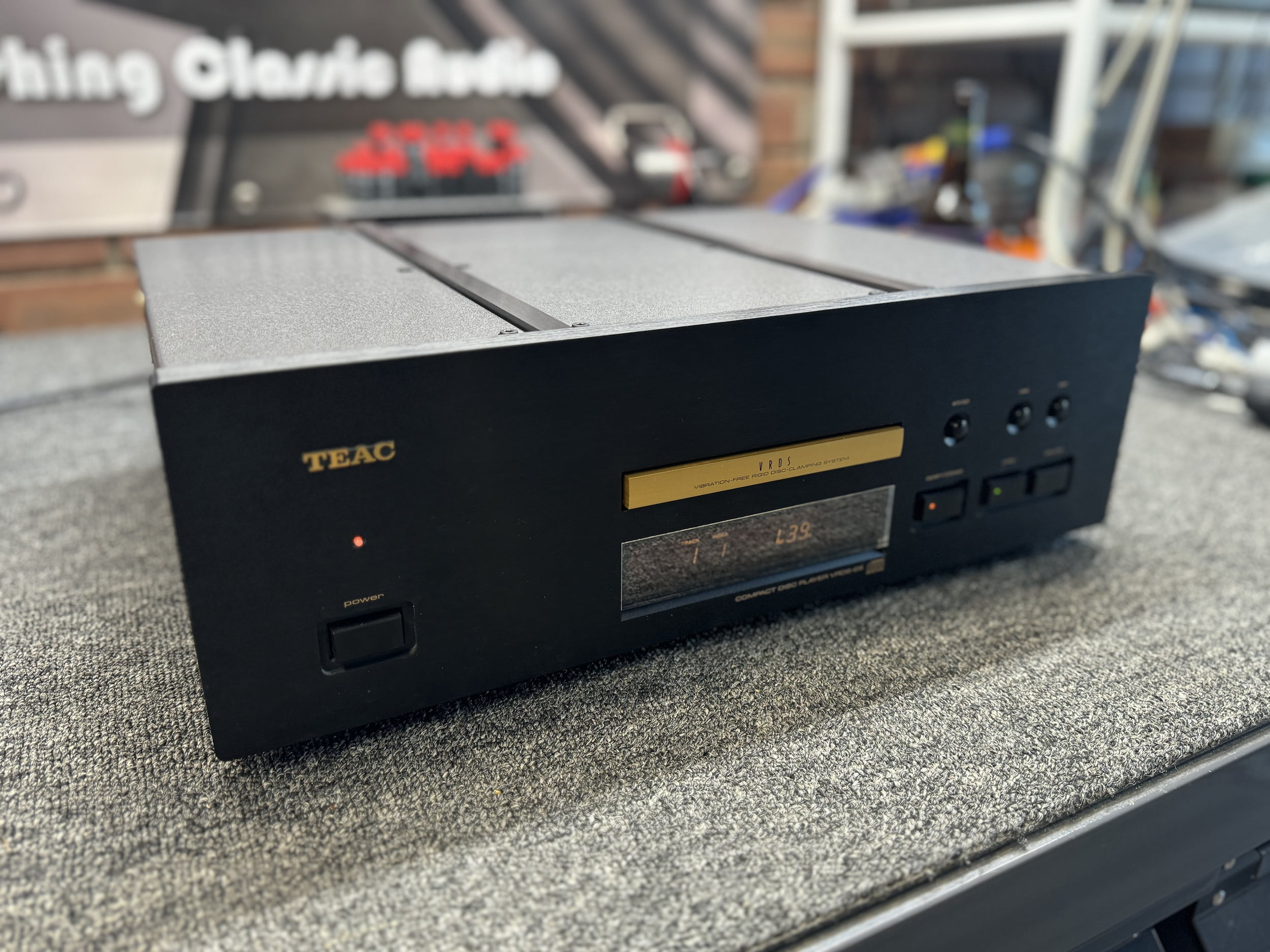
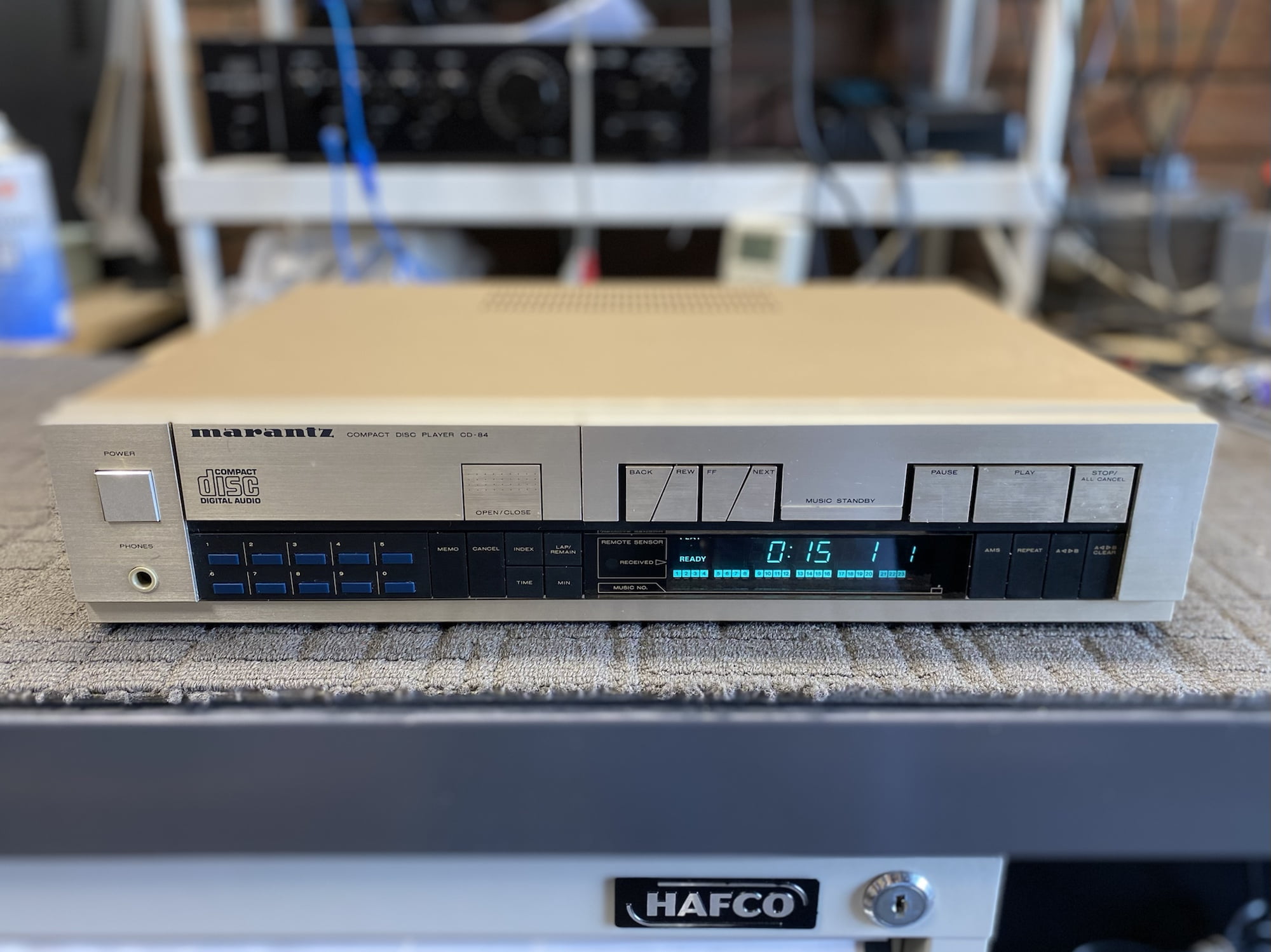
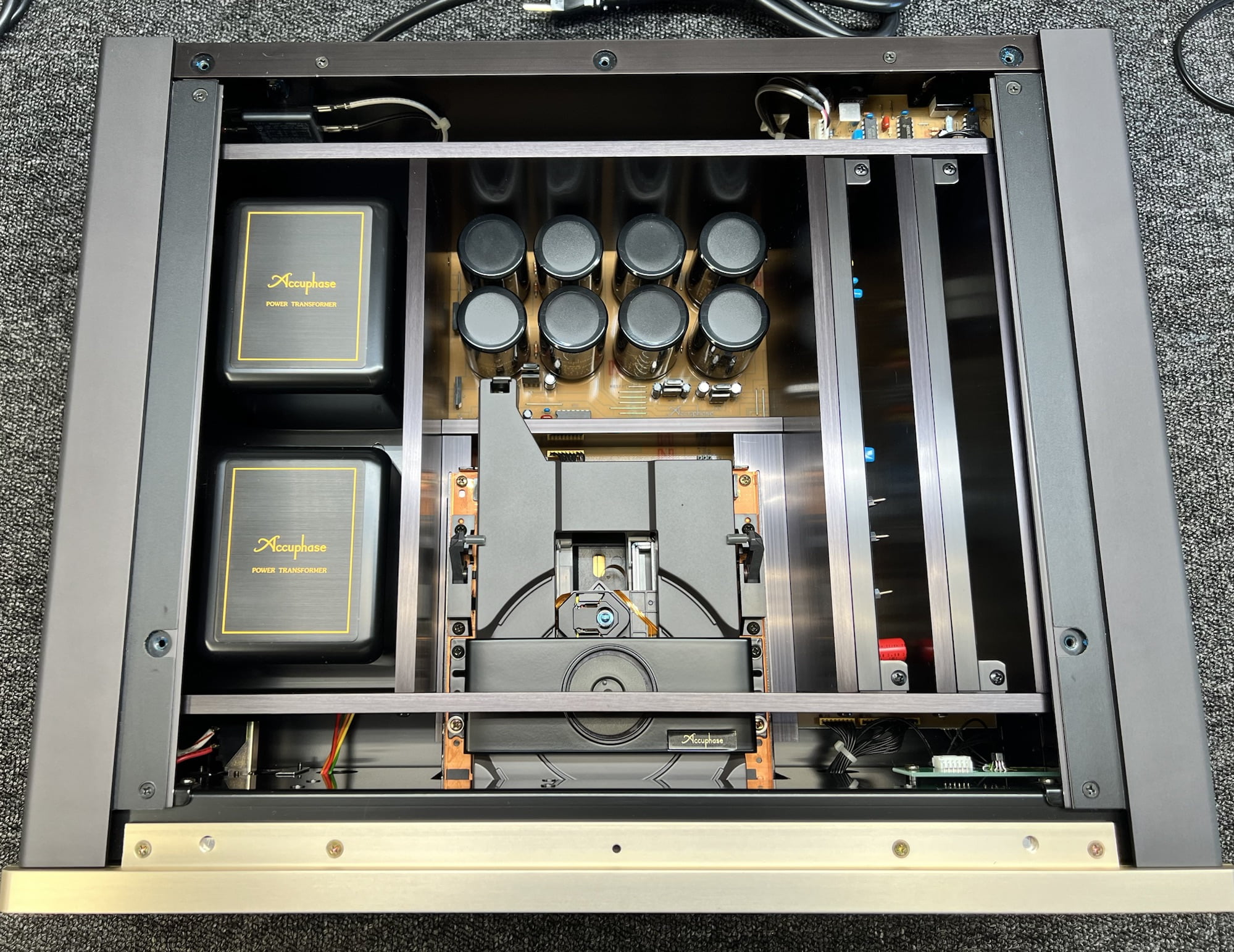
Look at these examples of wonderful older CD players and try to convince me that modern players that fail after three years are better.
But Mike, my Cambridge Audio whatever CD player has a Wolfson DAC!
Someone…
Great but tell me what good is that Wolfson DAC in a player that can’t load or read a disc any more because the junk plastic mech failed? It’s a serious question because I hear variations on this all the time. Who cares what DAC chip it uses if it’s made of the worst plastic and uses a switching power supply filled with Long Dong capacitors?
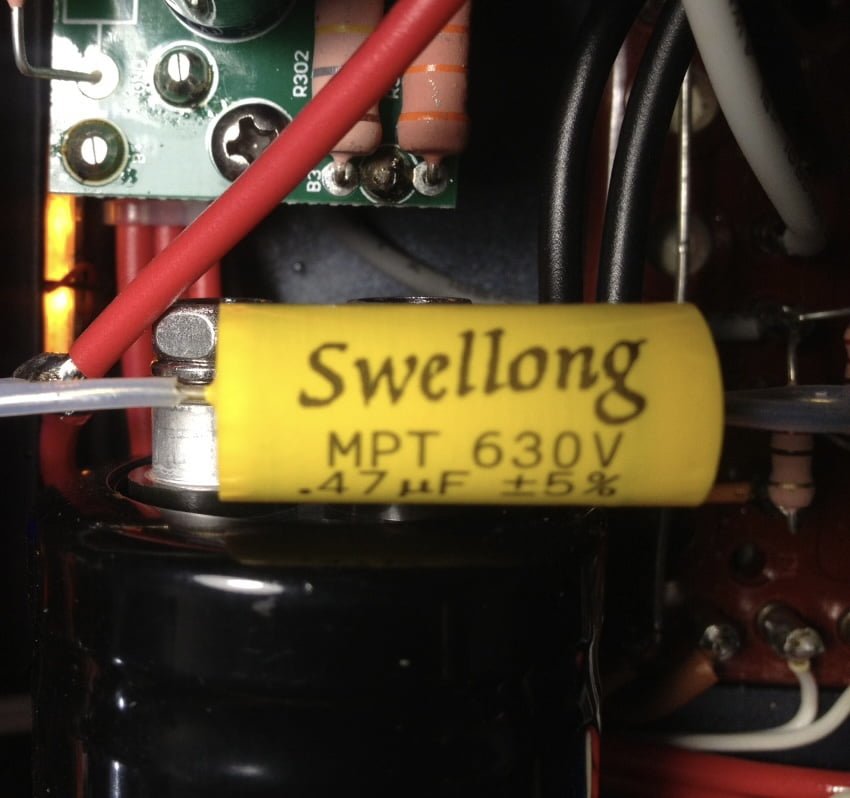
Decreasing Build Quality
I’d never thought I’d be saying this but, just as the golden age of turntables passed long ago and almost all the best turntables are the ones already out there, so it is now with CD players. Modern players are cheaply built with lasers that don’t last long. Some players need a new laser after just a couple of years, which is unacceptable in my opinion.
I constantly service CD players from the ’80s and ’90s, running their original lasers. Yes, some of them need repair, but for reasons often relating to their 30+ year vintage and failing capacitors and mechanical issues rather than lasers. I work on modern players too and I’ve replaced lasers and entire mechs that are three years old or less. THREE YEARS! This is how far we’ve come with all that “new technology”.
New technology isn’t much use if the device containing it is made of the world’s shitiest plastic. I’ve had customers tell me they wanted to throw their new CD players in the bin when they’ve failed after a few years. Do you think hi-fi store sales staff are going to tell you about this? They NEED to sell this junk to put food on the table, a real conflict of interest.
Let me know if you’ve ever walked into a hi-fi store and the salesperson told you that the classic CD player you own is much better than any of the new affordable junk they have in the store because that person and the store they work in deserve medals!
Compromise
The sound of a CD player depends on many elements: the CD drive used, error correction, power supply, analog output buffer design, internal layout, build quality and DAC architecture all contribute to the sound. This is how some older players can sound better than newer ones despite DAC architecture improvements – it’s not only about the DAC, and I’ve written about this.
Don’t get me wrong though, a good modern CD player, like the Accuphase DP-450, is a stunning-sounding machine, better than most older players, for sure. They also have multiple digital inputs which enhance flexibility and, being an Accuphase, this one is certainly well-built. But it’s also $11,000 AUD.
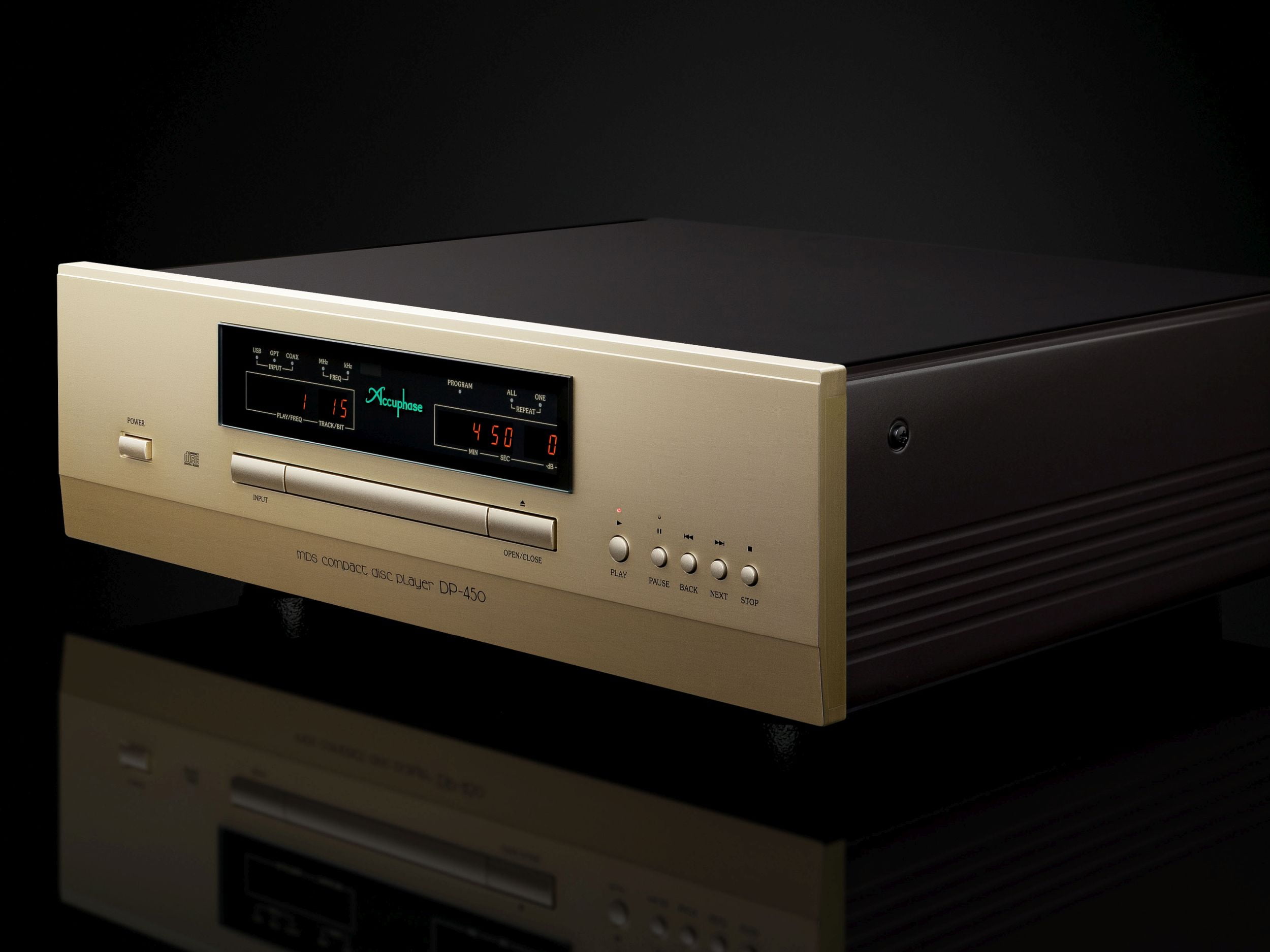
That being said, an older Accuphase CD player like the incredible 20kg Accuphase DP-75 for example is even better-built and probably sounds nearly as good.
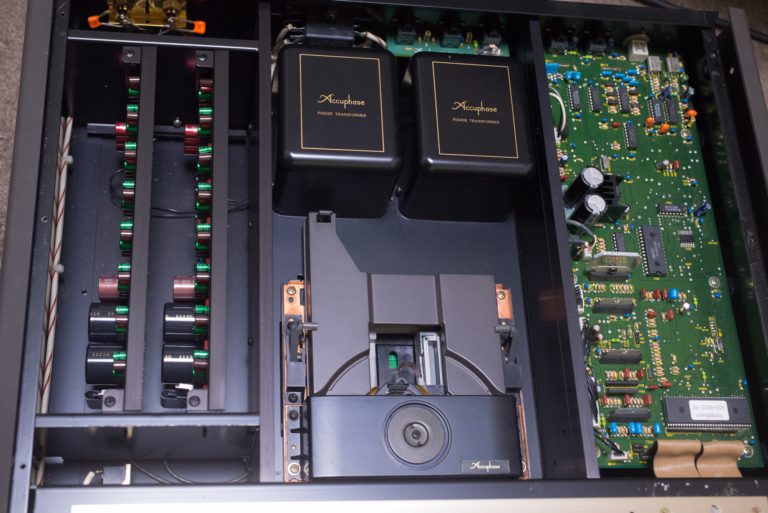
Best of Both Worlds
Integrated CD players, ie players containing both transport and DAC are always a compromise, in the sense that anything integrated is. A good, modern DAC, where the focus is more on the DAC itself, the power supply and the output buffer can significantly lift an older player that might have outstanding build quality, laser and mechanics but a dated DAC architecture. Want the best of both worlds? Get a classic player and a really good standalone DAC.
That’s what I’ve done with my Redbook CD and digital source playback chain and it’s breathed wonders into old and new source material. I use my Accuphase DP-90 (previously my Sony CDP-X7ESD) and iPhone 15 Pro Max as file sources or ‘transports’ and a superb new stand-alone DAC based on the AKM AK4499EX chipset, with discrete, balanced outputs.
This combination comfortably bests my previous Sony CDP-X7ESD as a stand-alone machine or used with the DAC. It has transformed my digital playback, and I still get to use an incredible classic CD player. It’s a win-win!
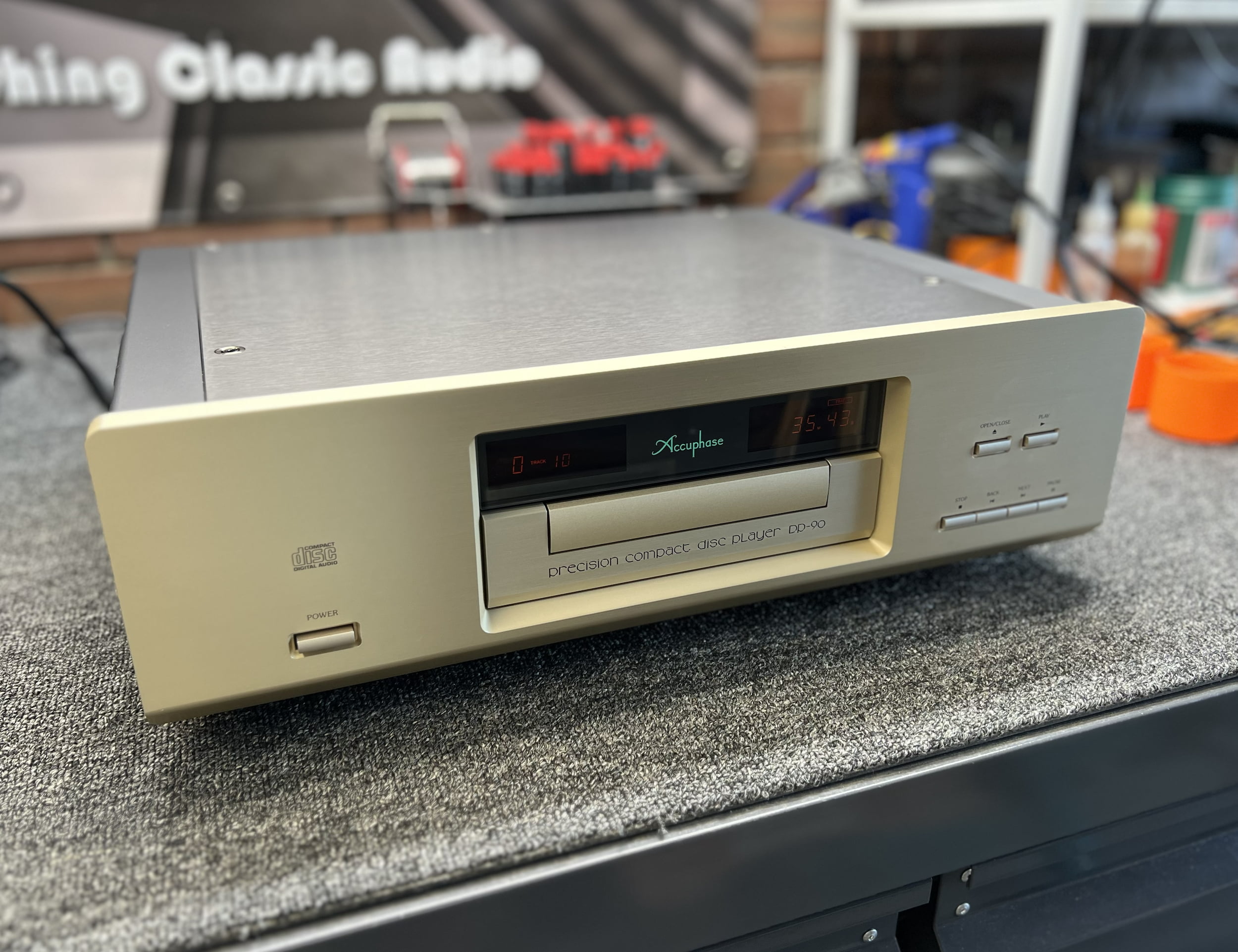
The Bottom Line
So it depends on what you want. Most people want something that will last – is that a new Marantz CD-6006 like the one I re-lasered in 2021 after just over two years of service? Or is it a 25-year-old Sony CDP XA-20ES for example, that still plays a disc as well as it did when it was new? I know which I’d rather own.
More
Read other FAQs I’ve written about CD players:
Read other articles I’ve written about CD players and DACs:
How important is it to match amplifier power output with speaker sensitivity?
Critically important for proper hi-fi performance and dynamic range.
This combination of technical parameters determines the actual sound pressure level you can attain without distortion and also tells us a lot about the system’s dynamic capabilities. As usual, science provides the answers.
Low Power
For example, let’s say you have a low-powered amplifier up to around 30 Watts per channel. To achieve realistic dynamics and sound pressure levels, you’ll need sensitive speakers rated at over 90dB/Watt sensitivity, preferably a lot more, to be able to play loudly and with realistic dynamics.
If that 30-Watt amplifier is matched up with speakers with relatively normal sensitivity, the result will be a system that sounds strained and lacking in bass control and dynamics at anything other than very low levels. This combination can work, but only just, and in the right context, with mellow music, a small room, and no desire for realistic sound pressures.
High Power
Conversely, let’s say you have a very powerful amplifier, something like 200 – 500 Watts per channel. This gives you a lot more headroom and means you can use speakers down to relatively insensitive 83 to 85dB/Watt, which are often some of the better sounding options. ATC and B&W designs spring to mind.
This gives you more choice and allows crushingly high sound pressures and dynamics with regular speakers of 88 – 90dB/Watt sensitivity or more. It also gives you dynamic range and headroom, allowing your amplifier to almost always coast rather than strain at the limits. Coasting tends to sound good; straining, not so much.
What’s Better?
Is one approach better than the other? Not really, both have merit, but for most ‘normal’ speakers and rooms, higher power is certainly preferable.
I currently (2025) use a high-current class A amplifier (around 70 Watts/channel) to drive speakers of ‘normal’ 89dB/Watt sensitivity. This allows for a good mix of everything: micro dynamics, punch and bass control and high sound pressure levels if needed.
I’ve also heard amazing sounds from super low-powered valve amplifiers of around 5 – 10 Watts/channel and sensitive horn speakers of 98 – 100dB/Watt. This can yield similar or even greater dynamics in some cases, and often better micro-resolution, because sensitive speakers tend to give you that.
Then again, sensitive speakers are also often more coloured, so swings and roundabouts. What you don’t want is a low-powered amp driving speakers of average to low sensitivity. This is always an unfavourable marriage.
Why are good phono preamplifiers expensive?
Because in order to faithfully amplify the minuscule signals generated by a phono cartridge, they must have the highest precision and lowest noise of any amplifier in your system.
It’s no mean feat to take a 0.3mV signal and amplify it to the level needed by a regular line-level preamplifier. One millivolt or 1mV is one one-thousandth of a volt. Moving coil cartridges typically have outputs of less than 1mV, a tiny signal.
This has to be amplified up to a volt or so, that’s a gain of over 1000x. This amplification has to be made whilst adding as little noise and distortion as possible. The phono preamp also has to EQ the signal to RIAA specs, reversing the EQ applied to the signal embedded in the record grooves.
Audio Microscopes…
I studied botany and zoology at uni and am well-versed in microscopy. The microscope is a perfect analogy in optical terms, to a phono preamplifier. Ever used a bad microscope? The image is distorted, lacking resolution and opaque. It’s exactly the same, only in sonic terms, when you use a bad phono preamp.
The job these instruments do requires not only huge gain (magnification in optical terms) but ultimate precision in terms of parts, circuit design, layout and adjustment (lens quality and figure, low optical distortion). This is why there is such a gulf between cheap op-amp-based phono preamplifiers and discrete class-A tube-type phono preamplifiers. Its also why a kid’s microscope is $50, vs tens of thousands for a really good one.
Step up (no pun intended) to a good moving coil step-up transformer for example and the price hike is considerable, likewise, to a good class-A phono preamp, or a really good microscope. Parts like JFETs, big film capacitors, precision resistors and premium wiring all add to the cost of these instrument-grade amplifiers.
I should mention that some of the op-amp-based solutions aren’t even that cheap, but moving to a precision, discrete design always improves things. Likewise, ramping up parts quality and grading has a profound effect on performance. Using 1% silver mica and polystyrene film capacitors vs using 5% green caps and other cheap types greatly affects the final result’s accuracy. When you are dealing with such small signals, you need accuracy.
The best phono preamplifiers use MKP (polypropylene film), silver mica, polystyrene film, discrete transistor networks and tube gain stages. The very best use transformers for the critical job of boosting moving coil signal levels.
Should I buy a cheap phono preamp?
Only if you understand the fairly linear relationship between price and performance with phono preamplifiers and the limitations cheap phono preamps impose.
There is enormous variation among phono preamplifiers. Cheap phono preamps really only serve one purpose and that is to add vinyl playback to affordable systems that don’t already have it. It goes without saying that one cannot care too much about sonic performance with said cheap systems.
That use case does not reflect most of my customers or their scenarios though. If you DO care about the sonic results, cheap phono preamps are never a good idea. They tend to be coarse, grainy, noisy, thin, unrefined, veiled, lacking dynamics and possess narrow soundstages and poor imaging.
What constitutes ‘cheap’? For me, anything under $1000 new for a phono preamplifier is on the cheap side. Between $2K and $4K, things get better and continue to improve from there. Pre-owned gets you orders of magnitude better value, of course.
There are good reasons why the best phono preamps are expensive. The quality of parts used in the best phono preamplifiers and attention to design and execution are extraordinary, and they need to be, given the extraordinarily small signals and high gain needed.
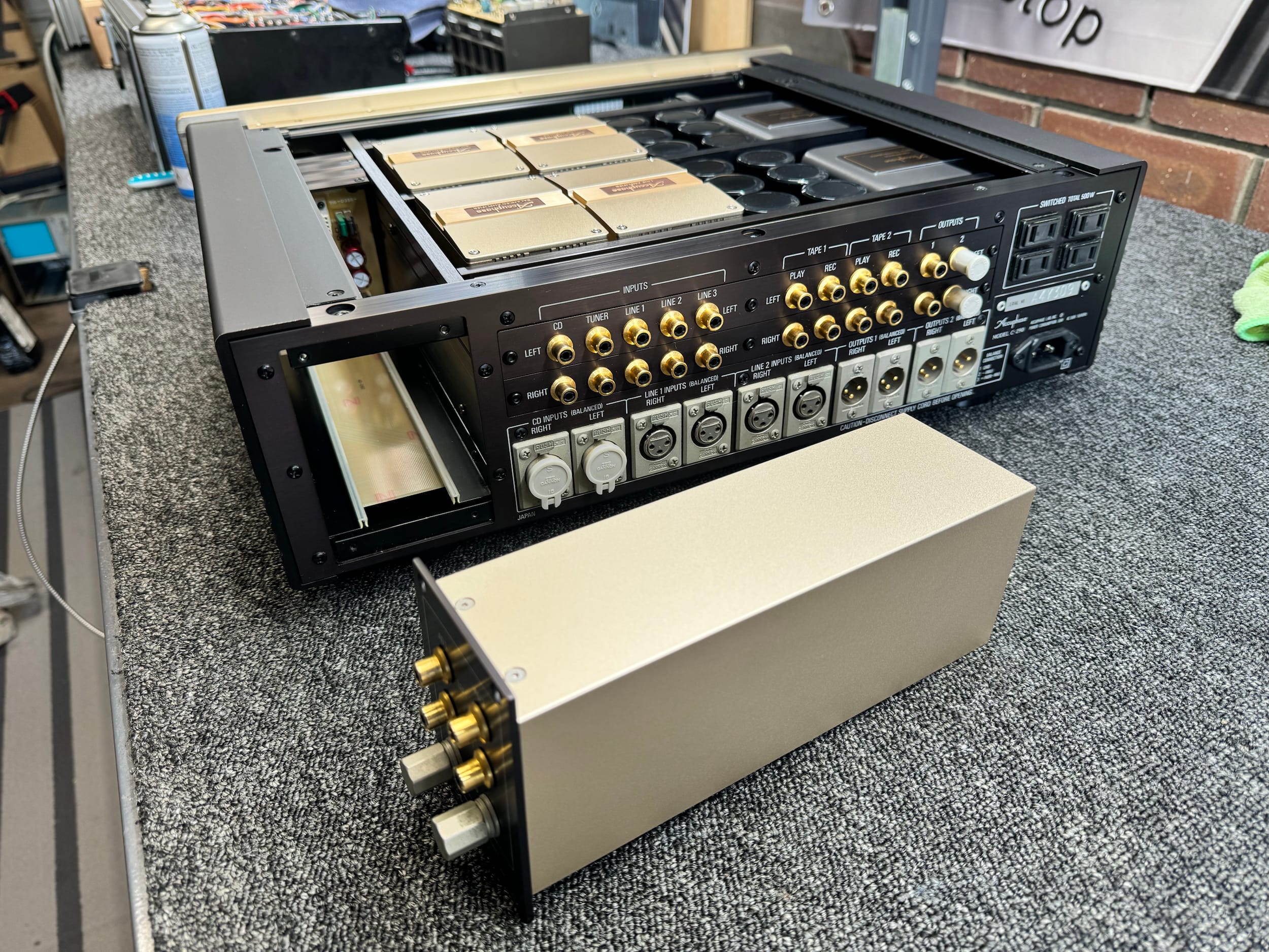
OK, I know you want to see inside…
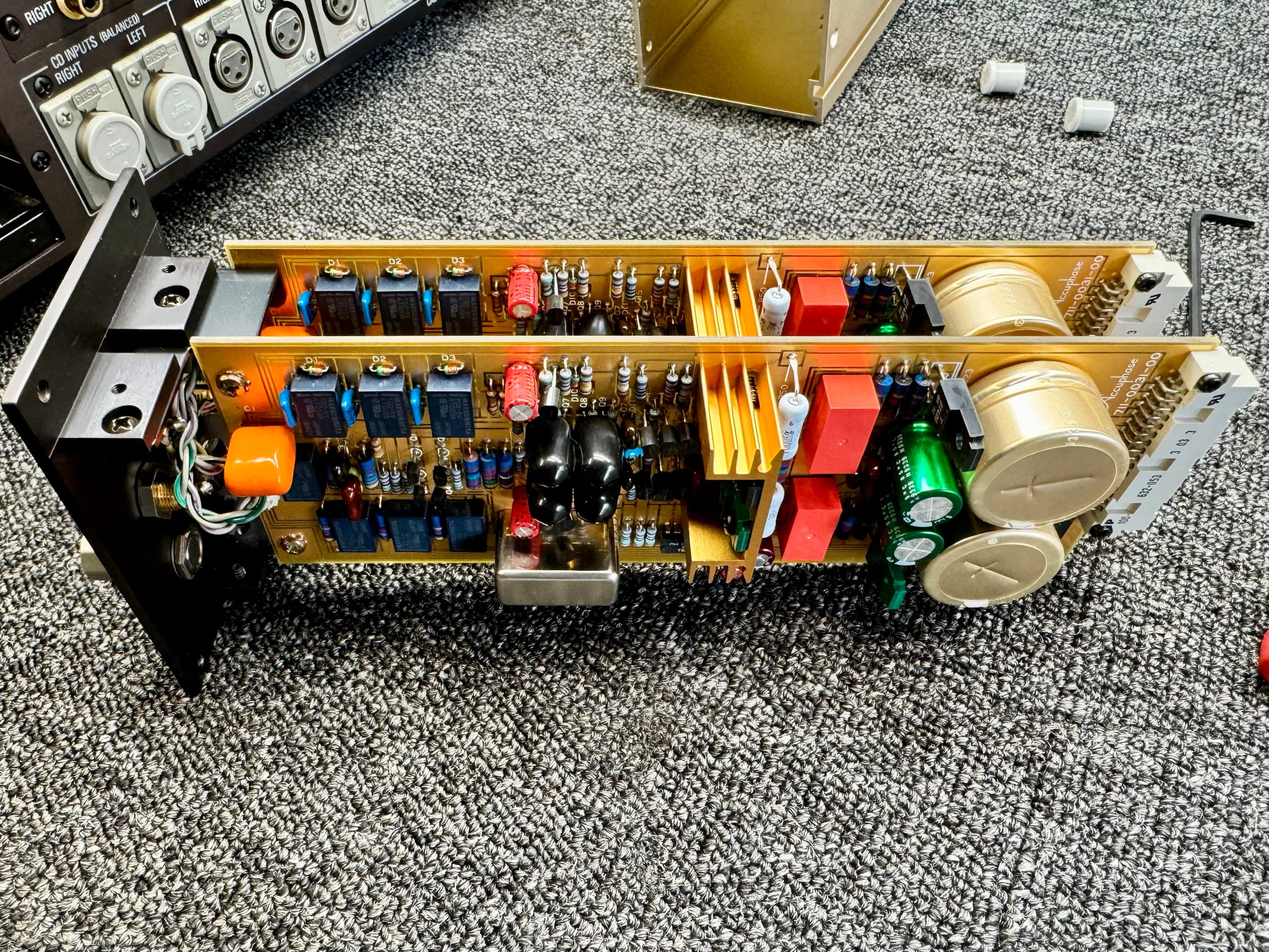
Here’s a look at a later Accuphase AD-2820, from around 2011:
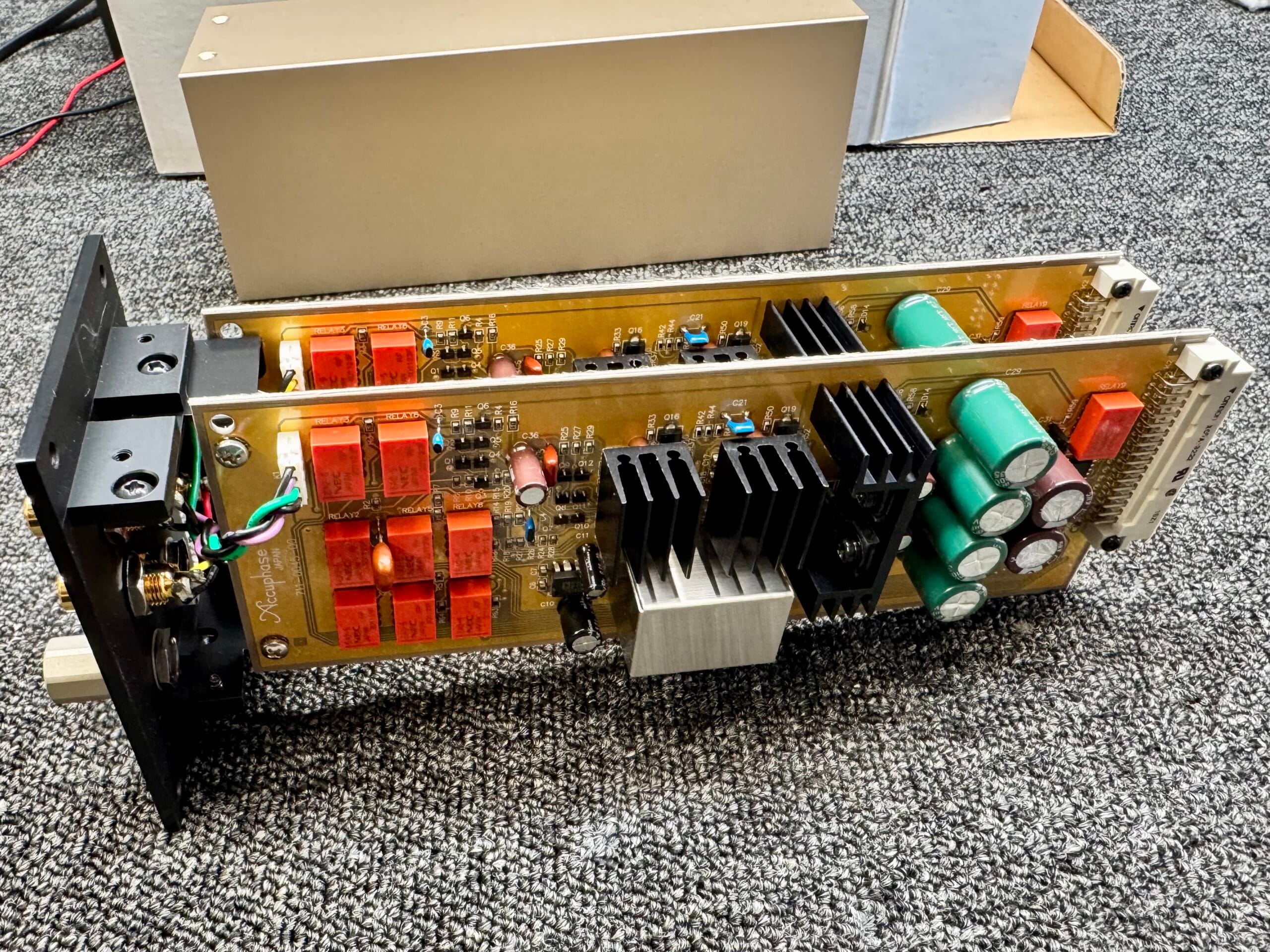
Wanna see a better phono preamp? Try the new Accuphase C-57:
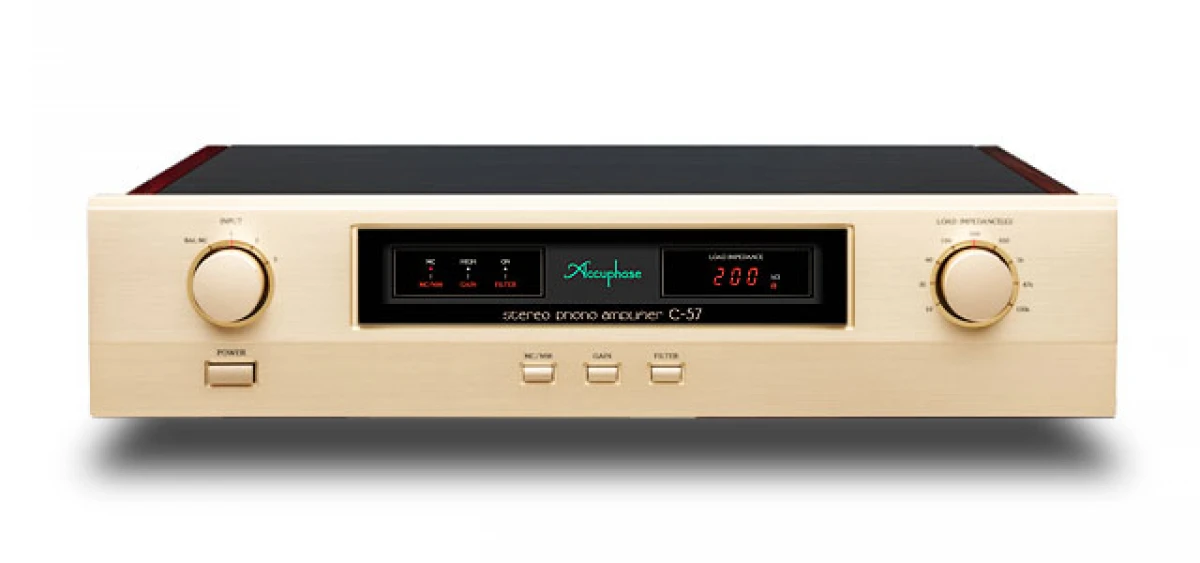
What are the important adjustments to make when setting up a cartridge?
A number of critical adjustments must be made each time a cartridge is fitted to a tonearm.
These adjustments are vitally important in getting the most out of your records and stylus. Let’s look at them in the order I normally set them, this is a sequence I apply to all turntables that visit the workshop.
Note: most end users and many retailers don’t have the necessary alignment tools or knowledge to correctly set up cartridges. This is not a judgment, merely an observation and something to be considered if you wish to extract the highest possible performance.
Cartridge alignment can be thought of as optimising two sets of parameters: geometry and forces at the stylus tip.
Geometry
The first adjustment is called overhang, which describes the location of the stylus tip with respect to the tonearm mounting point and the spindle. This specification is provided by the tonearm manufacturer and measured, on deck, with either a headshell gauge or an on-platter overhang gauge.
Next is the cartridge offset angle when viewed from above. This is usually specified as correct when the cartridge body, and/or cantilever, are parallel with the headshell’s long axis when the correct overhang has been set.
Azimuth describes the parallel alignment of the cartridge with respect to the record surface when viewed from the front. This is typically measured with a mirror under the stylus, viewed from the front.
Vertical tracking angle or VTA affects the angle of the stylus contact point with respect to the record surface. It can be thought of as approximating the angle between the cantilever and the record surface. It’s usually measured with a VTA gauge and set initially so that the headshell top surface is parallel with the record surface when viewed from the side. This is the starting point and adjustment from there is by ear.
Forces
Lateral balance is a feature offered on some tonearms and should be set at or around this point in the process.
Tracking force, which describes the downforce at the stylus tip. This is typically measured with a digital stylus ‘pressure’ gauge. Note that this isn’t technically a pressure measurement, the common name is incorrect, strictly speaking!
Lastly, anti-skate is a counterforce to the asymmetrical forces that pull the stylus tip toward the centre of the record and place added force on the inner groove wall. It is set to counteract that force as closely as possible.
There is some iteration in the set-up process and I generally go back and check everything again as some adjustments will slightly affect others.
Is it normal to hear hum when playing records?
No, a good, well-set-up vinyl playback system should be almost silent and exhibit no audible hum.
This is one of the great revelations about vinyl that folks discover on the typical journey from basic equipment to more aspirational gear. The short version is that, if you haven’t listened to a serious vinyl rig, you need to, if only to have a reference point.
What is Hum?
The term ‘hum’ describes continuous low-frequency tones of a constant frequency or pitch, usually centred around 50/60Hz or 100/120Hz. Hum can be mechanical or electrical in origin and usually indicates a problem in the playback system. Whatever the origin, hum should be tracked down to the source and eliminated or minimised.
Various types of low-frequency noise can be attributable to hum.
Electrical Hum
Bad or missing earths or grounds are a common cause of electrical hum, especially in vinyl playback systems. The high sensitivity and gain of a vinyl playback chain will take tiny ground currents that cause hum and amplify them to the point where they will become an audible problem. Any currents flowing in the ground system will be audible, and so we want to eliminate those ground currents.
By definition, current flows between two points with a different potential or voltage. Ground currents that cause hum flow where two elements in the playback chain reference different grounds and therefore sit at slightly different potentials. Bad cables can play a part here, as some do not have an effective ground linking both ends of the cable structure.
Therefore, the trick to ensure a quiet system is to ensure the turntable/pre-amp/amplifier combination is effectively grounded together and that at least one piece is system ground-referenced. All grounds must be of a low impedance, made using clean, quality wire and connectors.
Mechanical Hum
Mechanical hum can originate from turntable motors and mains transformers. The hum from both sources can often be resolved with the right attention and some new parts, with specific attention paid to damping and isolation.
Cheap phono preamps, cartridges and cables will always be noisier than good ones, and active preamps will always be noisier than transformers. An English brand of turntables that shall remain nameless opts not to use a separate headshell/arm ground. These decks are generally noisier than turntables with better, separated ground arrangements. Equipment type, set-up and installation can all contribute to hum.
Acoustic Feedback
Mechanical vibration from the turntable itself or other equipment can be coupled through a turntable, back into speakers, creating what’s called a positive feedback loop. These loops can occur through shelving, for example shared by speakers and turntables, wooden floors and other resonant structures.
In these cases, the hum makes its way to the speakers, which energises the turntable, arm, and record at the hum frequency, which is then fed back into the signal chain and further amplified, creating what we call a positive feedback loop.
Positive feedback loops can very quickly go out of control and destroy speakers and even amplifiers, so if you have a hum that appears to be coupled through your turntable, resolve it or seek expert help immediately!
Rumble
Rumble is another source of low-frequency noise generated by a turntable’s spindle and/or motor bearings. This is typically a broader-spectrum LF noise than hum and may consist of several fundamentals or tones, and their harmonics.
Rumble intensity is generally inversely correlated with turntable price. In other words, the cheaper the turntable, the greater the rumble, and vice versa. This is because cheaper decks have poorer mechanical quality, looser bearing tolerances and greater bearing surface roughness. Consequently, cheap turntables are often rumbly.
More expensive machines have bearings machined to tighter tolerances, better bearing surface finishing, higher quality motors and other parts, heavier chassis, better lubrication, and so on. These elements contribute to lowering the noise floor of better gear, such that it becomes essentially inaudible.
Quiet
In well-set-up vinyl playback systems consisting of quality components, there is no audible hum. The predominant noise in systems like this is groove noise, a residual component of the cutting lathe, the friction between the stylus and the groove itself.
There will also be some phono preamplifier noise in the form of a soft and gentle ‘rushing’ sound that will be inaudible during normal listening. Some white noise is present in all systems, but hum is absent from all good ones.
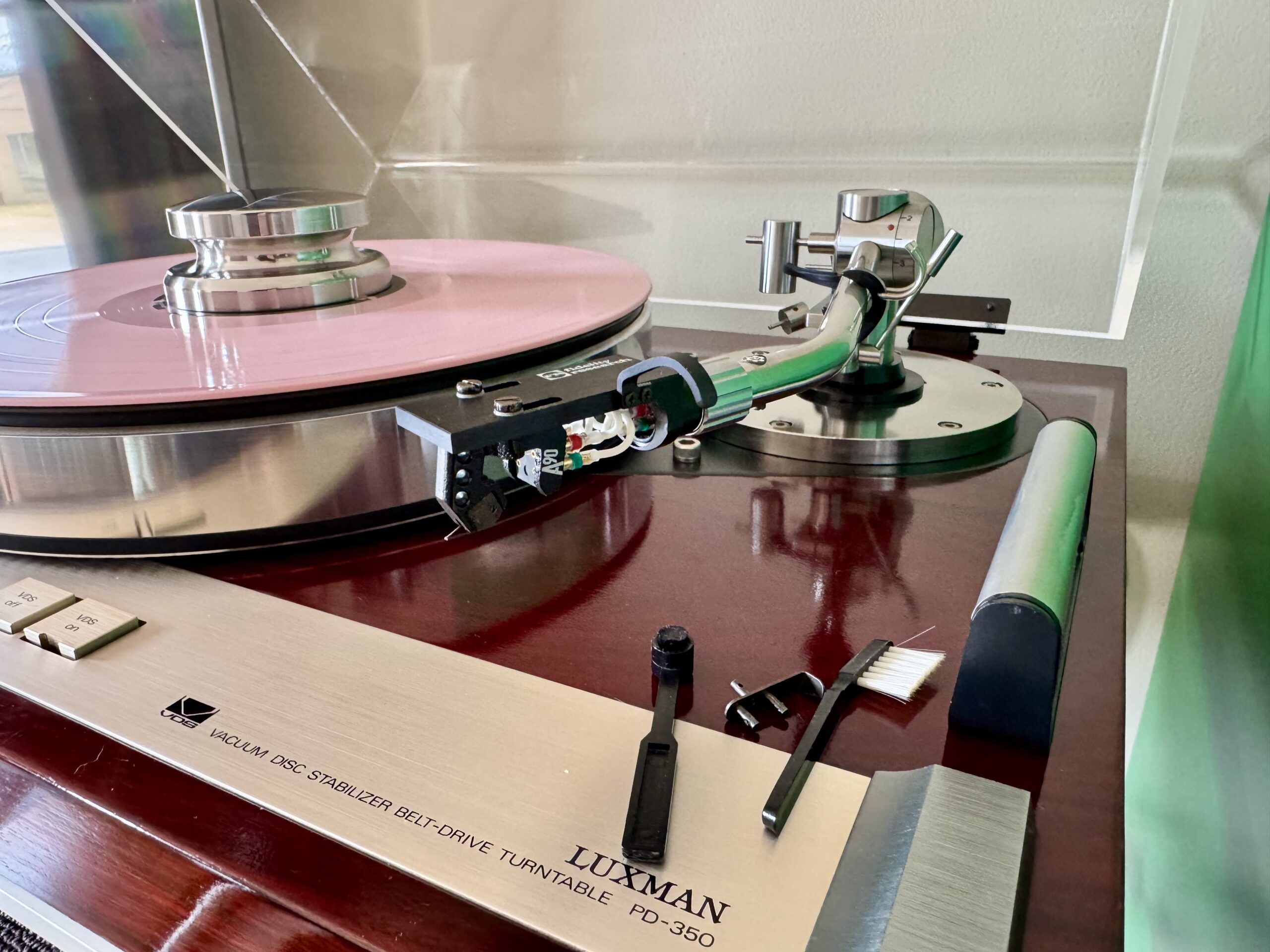
There’s absolutely no hum in my reference set-up (above) consisting of a Luxman PD-350, Fidelity Research FR-64S, RS-141, Ortofon MC-A90, feeding my Accuphase C-290/AD-290 and Accuphase A-75.
Mike, by “no hum” do you mean just a little hum..?
No, I mean no hum – NONE! There will be no audible low-frequency components in a good vinyl setup in a properly placed and set-up system.
If you are curious about how quiet a vinyl playback system can be, let me know, and if I’m not too busy, you may be able to hear my reference set-up so that you at least have a sonic baseline from which to make comparisons.
Should I play my records on radiograms and stereograms?
Not if you care about sound quality and preserving your vinyl!
Funky Furniture
Radiograms and stereograms, with few exceptions, are not hi-fi equipment. These are furniture pieces that play music. This was their original design intent, and they work well in this role but don’t expect more of them.
The problems are varied, but generally speaking the turntables in these units range from bad to terrible. They usually use ceramic cartridges that run very high tracking forces and conical stylii that don’t treat records well. This combination causes accelerated record wear and will result in noisy, distorted-sounding records after not very many plays.
The electronics and speakers are designed to fill the room with a warm, ‘easy listening’ sound, typical of AM radio stations of the day. There’s nothing high-resolution about systems like these so you’ll never hear most of what’s on your records. If this is your jam, cool, but if you care about your records, there is still a significant problem.
Vinyl Care
But I play all my records on this and I don’t care!
Owner of the worst one-box unit I’ve ever seen
Someone told me this recently after I reiterated my general advice on this topic, and which he didn’t seem to understand. Not everyone cares, I get that, but thankfully most do!
Almost all record owners should avoid playing precious vinyl on radiograms, stereograms and cheap integrated music systems. If you own precious vinyl or even a modest record collection you care about, get a decent hi-fi turntable with an elliptical stylus, or better. The reduced tracking force and better stylus profile will extend the life of your records and produce far superior sound quality when combined with a decent amplifier and speakers.
Why does vintage hi-fi gear last longer?
This is a good question with a simple answer: it was designed and built to last longer.
We need to start this brief discussion by acknowledging the shift in product design life and public expectations around this. Back in the day, people saved and bought hi-fi gear, with a view to keeping it for a long time. Manufacturers built gear to align with this general philosophy.
The longer life of older equipment generally comes down to better mechanical design, use of higher quality switches, longer-lasting through-hole capacitors, greater serviceability through component level board repairability and so on. I often see equipment from 1970 with a full set of electrically perfect Elna electrolytic capacitors. Fifty years from what are nominally 2000 hour-rated parts is extraordinary, and yet this is common.
Modern capacitors found in affordable new equipment rarely last this long. Good modern capacitors are excellent, but you need to spend a lot to get an amplifier filled with good Nichicon, Nippon Chemi-Con or Panasonic capacitors. Add to this the through-hole nature of older caps and other parts, which were designed to be serviceable.
Then there is the physical build quality. Older gear tended to use less plastic, heavier grade metal, metal switches and so on. These parts tend to be serviceable. If metal bends, for example, it can often be bent back. Plastic breaks and becomes brittle with age.
The simple fact is that older gear from the ’60s, ’70s and ’80s was designed with serviceability in mind. Production values and the way we view our equipment have changed. Modern gear is often designed to be thrown away rather than serviced when it fails, so it often cannot be viably kept running.
Home cinema equipment and modern TVs are classic examples of this. Ever wonder where all the old TV repairers went? It’s not that modern TVs don’t fail, they do, but try taking your 65-inch TV anywhere if it breaks.
Why does electronic equipment need to be serviced?
Because all hi-fi equipment and electronic devices contain parts that change over time, wear and need periodic cleaning, lubrication and adjustment.
When you combine the sometimes hundreds of electronic parts with mechanical components like the levers, switches, belts, gears, pulleys and connectors found in many types of hi-fi gear, you have a combination of parts and systems that wear and need periodic attention and maintenance, over time.
Mechanical linkages, pulleys, gears, idlers, pinch rollers and motors need cleaning and lubrication and this is fairly easily understood. But electronic parts also change over time, most notably electrolytic capacitors, some semiconductors and resistors. One thing is for certain though: your hi-fi equipment will need money spent on maintenance if it is to keep running reliably.
Proper periodic maintenance prevents premature failure, improves performance and reliability and therefore enjoyment of your equipment. It’s a quirk of human nature that we sometimes purchase things and expect that they will run without attention. This isn’t even true even for a kettle, let alone complex equipment like turntables, amplifiers and cassette decks.
How do I find a good technician?
This is a question I am asked more often than almost any other by folks who don’t live in Western Australia.
Above all else, I suggest you try to find someone technically focused, able to provide evidence of their work, who solves problems and who has positive feedback, without the crazed rants a few of my competitors like to leave for people who aren’t happy with their services. You’ll never see me ranting at anyone, no matter what I think of the customer.
Try to:
- Find out who’s busy and recommended by other reliable sources, like good retailers.
- Look for the best technicians rather than the lowest rates, because you get what you pay for.
- Avoid sight-unseen quotes; nobody can know exactly what your equipment needs without seeing it.
- Look at reviews, read the good and bad ones, and the responses to them.
- Avoid recappers; recapping rarely fixes things, and problem-solving is key.
- Remember, there are no miracles, only skilled individuals with a technical approach doing good work; everything else is hot air.
Ask Retailers
One useful piece of advice I can offer is to find the best hi-fi store/s in the largest city near you. Ask an experienced staff member who they use/recommend to service and repair the type of equipment you own. Good retailers use technicians they can rely on. Experienced staff should be able to recommend someone who can assist you or perhaps even arrange the repair through their store. Shonky retailers use shonky repairers.
Keep in mind that retailers add a charge for dealing with and arranging such work. This is quite reasonable, given that it takes a real person time to book in and arrange a repair job, and this will be an addition to the raw repair cost charged by the technician.
Other Considerations
Good technicians inspire confidence and won’t try to quote you on a job without inspecting and testing the equipment. It may be tempting to go with a ‘magic blind quote,’ but ask yourself how a technician knows what’s wrong with your equipment or what condition it’s in before parting with your money.
Recapping is a fad that is often unhelpful in solving problems. Many or even most faults are not capacitor-related. Replacing lots of old parts might sound like a good idea, and it can be, but this is best done after figuring out what is wrong with a piece of equipment and fixing it, for hopefully obvious reasons.
It’s a bit like this: your engine makes a noise, a mechanic looks at it, you pick it up later, and he’s rebuilt the entire engine when it was just a noisy pulley. Sensible? Smart? Logical? No. Does it even enhance the value of the car? Not if the work has been poorly done.
Tracing and resolving electronic faults is technically challenging, that’s why not many are really good at it. Look for someone who understands this and expresses it, and who is interested in finding the cause of a problem and resolving it.
Can I pick your brains for advice, tips and recommendations?
Yes, I’m always happy to assist advice-seekers.
We have an advisory service specifically for these sorts of scenarios where people want expert advice. Just select a consult that best suits your enquiry and complete the contact form with your questions!
Does a cartridge really affect the sound of a turntable?
Yes, cartridges are a critically important part of the chain, just as important as the turntable itself.
Cartridges are transducers, like microphones, headphones and speakers. You may already realise just how much each of these contributes sonically.
Precision
Cartridges do incredible work, converting minuscule groove modulations, via the stylus and cantilever, into tiny electrical signals, via magnets and wire. These tiny electrical signals must then be amplified in a linear fashion in order not to generate distortion, which is another incredible story.
This work requires a staggering level of precision and materials engineering. That’s why my Ortofon MC-A90 for example is so bloody expensive! You get what you pay for with anything that relies on this level of precision and expensive materials. The cost vs. performance correlation is fairly linear; the more you pay, the better the results and this applies to camera lenses, speakers, musical instruments, and cartridges.
Performance
Cartridges cost anything from $10 to $10,000+ and their performance varies from unlistenably bad record-destroying to sublime! I always recommend people spend as much as they can on a good cartridge as it’s a huge part of the sound of a turntable.
Better cartridges give the added benefits of preserving precious vinyl and longer life. The larger contact area of a Shibata or line-contact diamond exerts lower pressure at the interface between the stylus and vinyl groove. This causes less friction, and therefore less heat and record wear. Quality cartridges/styli provide anywhere from 1000 – 2000 hours useful life, compared to just 200 – 500 hours for a cheapy.
Cheap vinyl playback systems like Crosleys and other department store junk will wear away your records before your eyes! Don’t EVER play your records on something like this if you care about them.
Should I buy a Crosley?
No!
Never buy or use Crosleys or other cheap plastic record players if you care about your records and how they sound.
Cheap plastic turntables like Crosleys destroy vinyl due to their crude engineering and super-low-quality cartridge. The gems in these cheap styli – diamond or sometimes sapphire, have terrible profiles, are often poorly polished and rely on high tracking force to even play a record.
Then have you heard one of these things? They sound appallingly bad and really are a complete waste of money, even as a child’s gift. You are much better off saving for a decent secondhand or cheap new hi-fi turntable. You can pick up $50 secondhand turntables that are better. Almost anything is better than a Crosley!
Do I feel bad about bagging these things out? Nope, not at all. The manufacturers of these things are cashing in on the vinyl revival and preying on the average buyer’s lack of knowledge. That’s bad.
What’s the best turntable?
There isn’t one best turntable, just the best one you can afford.
All the really good machines are heavy, for various engineering reasons. Therefore, aim for something solid, well built, preferably costing over $1000AUD new if you want a good first turntable. Alternatively, you’ll get better performance in almost all cases from a second-hand classic turntable from the 1970s and ’80s.
Remember, for many years, vinyl was the highest resolution source that most hi-fi lovers had easy access to. One could argue this still is the case. This is important because the golden age of vinyl and record players was the ’70s and ’80s, so that’s when some of the greatest machines were made.
What’s better: belt-drive or direct-drive?
There is a long-standing myth amongst an admittedly ever smaller cohort these days that belt-drive is a superior drive methodology for turntables. It isn’t.
There’s a bit to know of course, but the TLDR is that the drive method is only one of many factors determining turntable performance. Direct-drive (DD) has many advantages, as does idler-drive, but DD is also more expensive and if you read no further, that’s the end of the story.
Science (Myths vs Facts)
I have a direct-drive washing machine and it’s a much better machine than the belt-drive washer it replaced, but, like a washing machine, a turntable’s performance is the sum of many parts and systems working together, and there are great examples within each drive type.
The notion the belt drive is inherently superior is perpetuated by certain manufacturers who are so ensconced in propagating this myth that they simply cannot now say anything different. The technically uninformed mainstream media and equipment owners swallow this up like gospel, fuelled by a desire to support these manufacturers who pay for spots in these media. All of this, compounded by a general lack of experience on the part of the hi-fi-consuming mainstream leads to the misinformation you’ll often find regurgitated in forums and elsewhere.
One critically important goal of any good turntable is to spin the platter as close to the perfect speed as possible, with as little variation and vibration as possible. Belt-drive offers no inherent advantages in any of these areas and disadvantages in most cases and implementations. It IS cheaper to implement though and this is, without a doubt, why it’s so widely adopted.
The best performers by these metrics are direct-drive turntables. This is science and the data is measurable. That being said, there are exceptional belt-drive and direct-drive turntables. I’m lucky enough to own an end-game example of each and I can confirm that the drive method is not the most important factor to consider.
Costs
Design and manufacturing costs are the overriding reason why you don’t see many new direct-drive machines these days. It’s cheaper to make decent belt-drive turntables and this is why most affordable decks tend to be belt-driven. This suits small manufacturers who can build a belt-drive turntable using readily available, low-cost motors. It also suits the buying public who generally don’t want to spend $20K USD on a turntable, hence the preponderance of good reviews of cheap belt-drive machines.
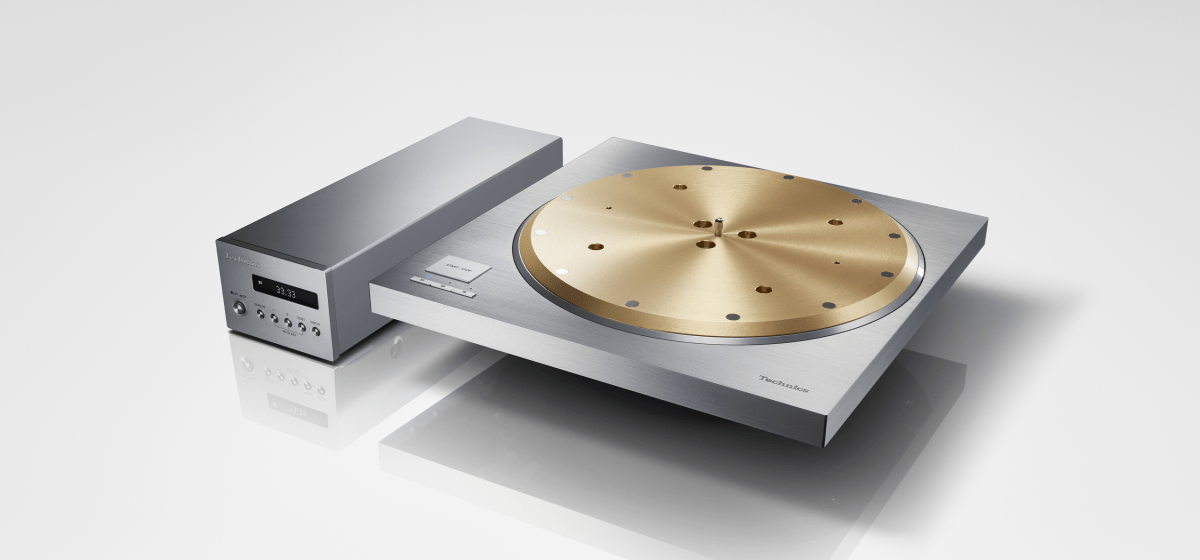
Direct-drive machines are much more expensive to design and manufacture, but direct-drive has advantages in terms of torque and speed consistency, so where cost is no object, you’ll generally find direct-drive. The performance advantages of direct-drive systems explain why some of the best and most expensive turntables, tape machines and cutting lathes utilise direct-drive. That being said, there are some killer, high-end belt-drive turntables from the golden era and they shouldn’t be discounted.
The bottom line is that you get what you pay for, always. A good turntable, no matter what drive method, is expensive, like all good things.
Apex Use Cases
As I mentioned, most of your records were recorded, mastered and cut on direct-drive tape machines and cutting lathes. Did you know that? Have you thought about why that is? Ponder it for a moment because it vapourises arguments about which drive type is preferable.
People far smarter than you or I choose what’s best in cost-no-object scenarios like record-cutting lathes. It’s their job to pick the best option. Record-cutting lathes are direct-drive for several very good reasons that apply not only to making records but to playing them, as is hopefully obvious.
Superior methods are always used where performance is critical and cost is no option. This explains why many of the great turntables are direct-drive and why those machines are so highly sought after.
Some folks get upset about this, but most of them haven’t owned or even heard a genuinely high-end machine like an L-07D, SP-10/SL-1000 or GT-2000. My perspective, being only interested in what’s best and having worked on and listened to thousands of turntables over the years is simple: show me an excellent turntable and I’ll enjoy it, belt, idler or direct-drive.
My current working reference is a belt-drive Luxman (Micro Seiki) PD-350 and it’s a phenomenal turntable, as you’d expect of something weighing 30kg and costing as much as a motorcycle when new. My best turntable is my direct-drive Kenwood L-07D though.

The Sum of the Parts
As I’ve mentioned in other FAQs, the performance of a piece of equipment is rarely defined by just one part of it. This is certainly true with turntables where the drive method is rarely the defining factor in turntable performance, but merely an element of it.
One must look at all factors, including drive method, chassis construction, platter and tonearm mass and design when evaluating a turntable. Great turntables come in various flavours, belt-drive and direct-drive. You need to choose which aspects of the design and performance matter most, to you!
But the record store guy says belt-drives are better!
Ah yes, the record store guy, who usually knows a lot more about records than record players!
With the greatest respect to record store guys, this is merely an observation based on experience. Several of my customers are record store guys, one owns a large record store here in Perth. Nice people, good taste, interested in record players and vinyl, but very rarely experienced with serious equipment to be able to offer opinions like this, and the ones I know would – or should – declare that.
This is true of most of what you’ll read and hear on most topics. What you need is to speak to someone who perhaps owns an end-game example of each type of turntable and then ask the right questions. Now, I wonder who does, and who’s listened to hundreds of such machines..?!
There are excellent belt-drive and direct-drive turntables. It’s not the drive method alone or even mostly that determines system performance. Unfortunately, most people aren’t interested in the technical details, nor have they been exposed to the range of equipment necessary to form a valid opinion on this important point.
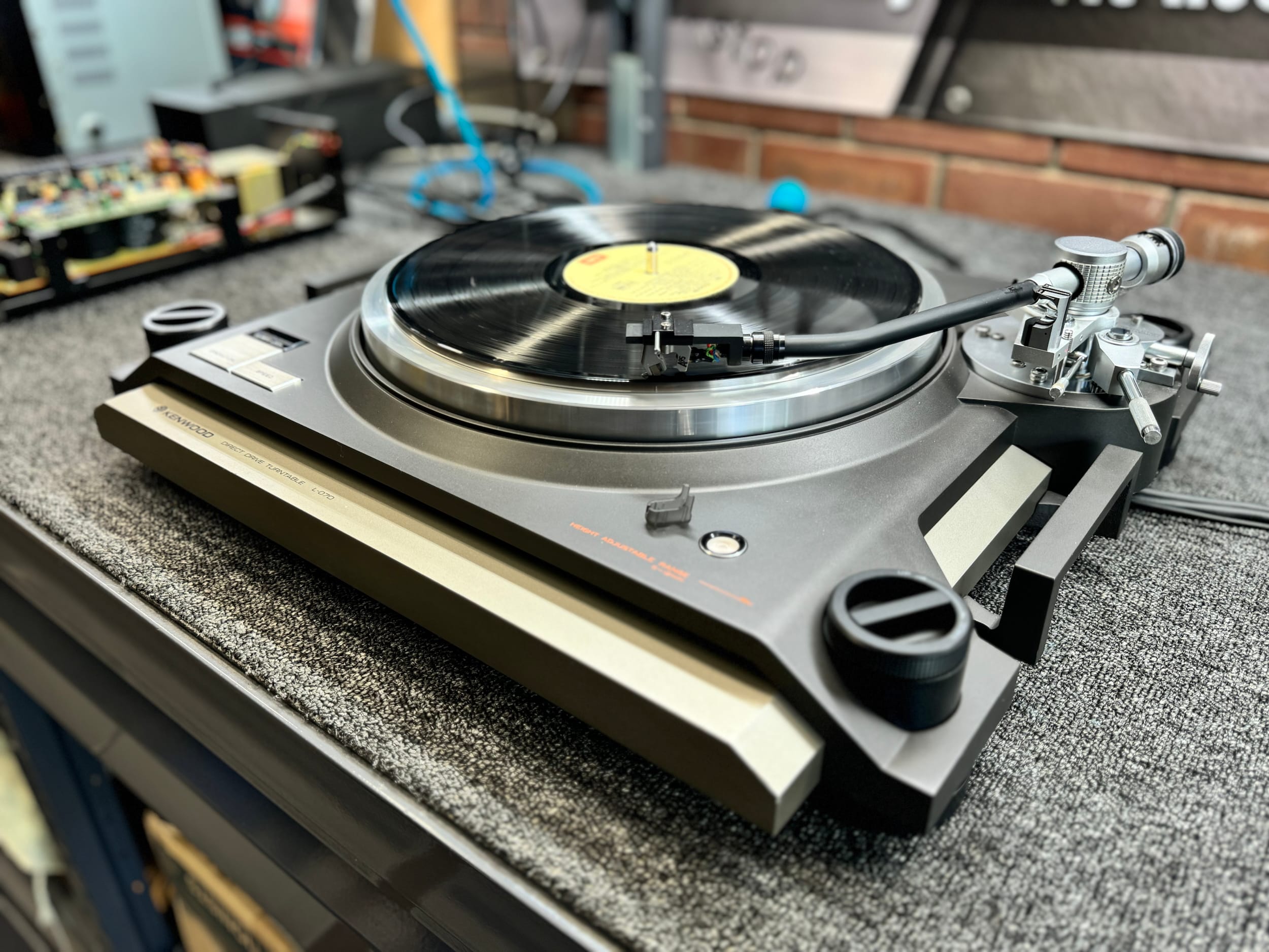
How many record store guys do you think have listened to an SL-1000, PD-350 or L-07D, for example, let alone owned several of these grail machines? Simply put, most people will never hear an end-game turntable, and this lack of experience and knowledge lies at the heart of all misinformation, on this topic and others.
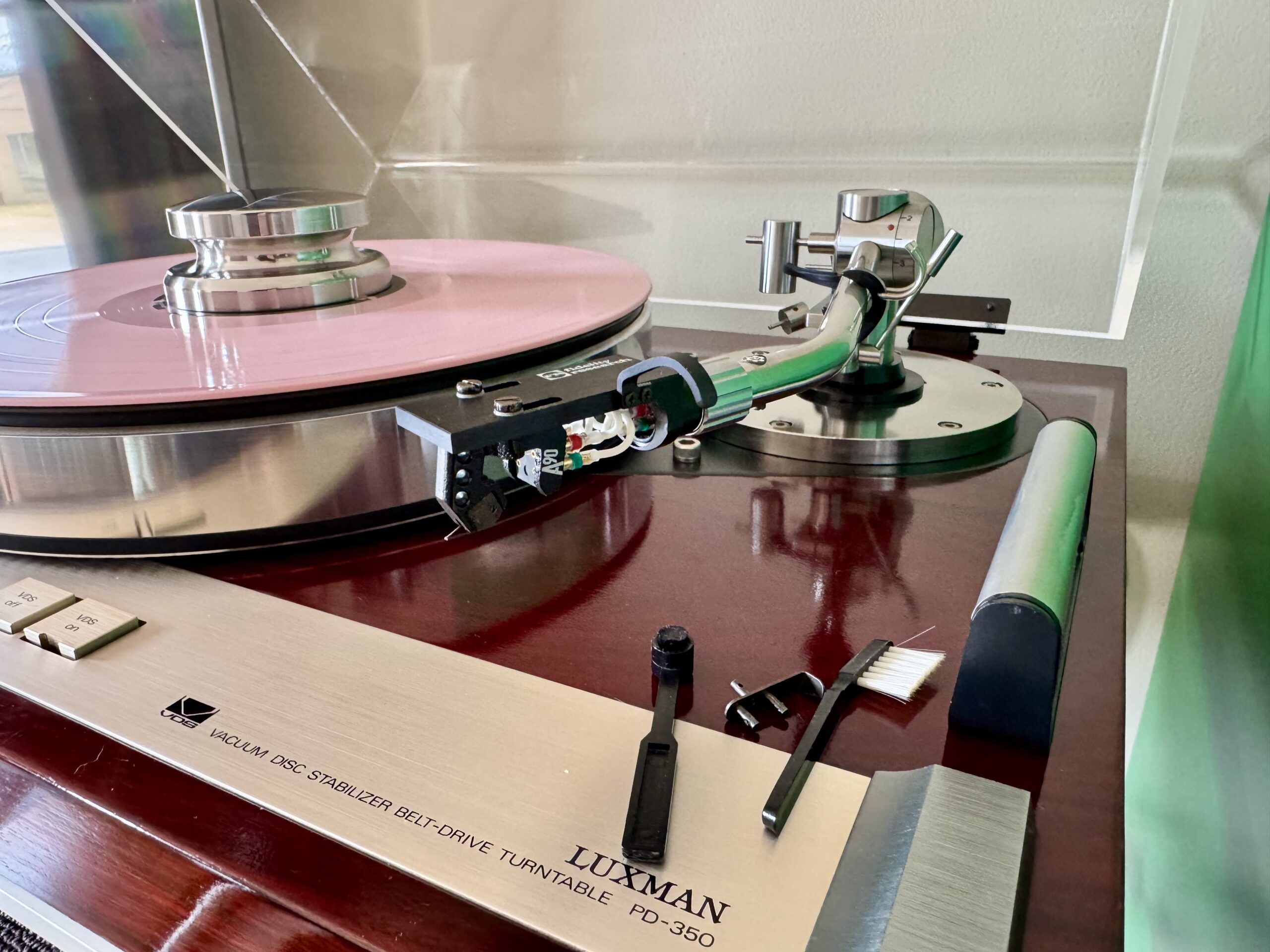
As we always say at Liquid Audio: knowledge is power. Want the truth? Speak to someone who knows what it is!
Do you dislike belt drive turntables?
No, I dislike cheaply made, overpriced, underperforming turntables, 95% of which happen to be belt drives.
There are many amazing belt-drive turntables out there. One of my two reference turntables is a golden-age, end-game Luxman PD-350 (ie Micro Seiki) belt drive turntable. Yes, the other is a direct drive machine, but I wouldn’t own or still be using the PD-350 many years after acquiring it if I didn’t like it, trust me on this!
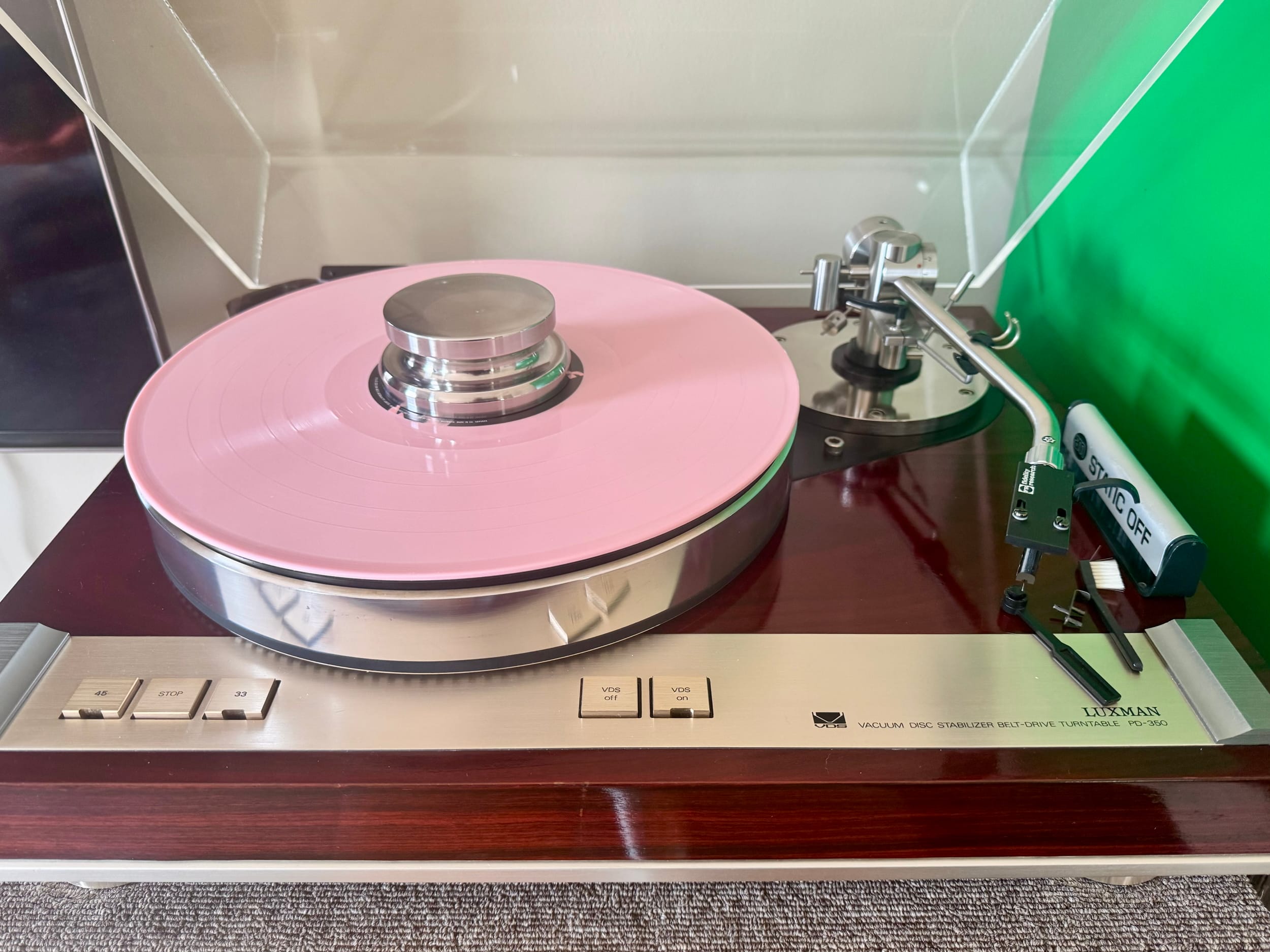
That being said, the Luxman PD-350 isn’t your regular belt-drive turntable, and this is important. Good belt-drive decks are excellent, but many are ordinary and far surpassed by direct-drive machines. Far too many people have spent far too long reading about hi-fi rather than experiencing it, and as a result, they have no clue about what’s actually good.
I enjoy the honesty and simplicity of older Rega Planar machines. I love decks like the Pioneer PL-514, Technics SL-23 and Kenwood KD-2055, just to name a few. What I don’t like is crappy turntables, no matter how their platters are driven.
This especially extends to modern overpriced underperformers; unfortunately, most of those are belt-driven, many of the famous brands you’d be familiar with…
What’s better: moving magnet or moving coil?
Ultimately, moving coil, but it depends on how much you have to spend. If your limit is $150, a moving magnet is all you’ve got baby!
That isn’t to say there aren’t some great moving magnet cartridges, especially vintage models. Rather, the best solution – technically – is the moving coil design, because of its reduced moving mass and therefore greater linearity and micro-dynamic accuracy.
Lower mass means lower inertia and therefore better transient response and high-frequency performance. All of that translates to better dynamics, detail, lower distortion and more of that elusive ‘air’. I’ve written quite a bit about this here.
Marketing departments everywhere have tried to convince people that lower-cost moving magnets are “as good” or “nearly as good” as moving coils, but the fact that they even need to try to convince people of this tells you something. They still have these inherent design limitations and speaking from experience, they simply aren’t as good.
Because coils are technically better, manufacturers also tend to spend more on these designs, using better diamonds, more expensive boron or even diamond cantilevers and better coil wire. This means you can spend a ton on a good MC cartridge, but remember that a really good moving magnet cartridge will be better than a cheap moving coil. You get what you pay for.
The caveat here is that because moving coil designs generally have much lower outputs, you need higher quality electronics and even a step-up transformer to get the most from them. People who audition really good MC carts in systems limited by a basic phono preamp might say something like “it didn’t sound that good” or similar.
Don’t expect a really good moving coil cartridge to sound its best on a built-in or cheap external phono preamp. You’ll need a step-up transformer to get the most from a moving coil cartridge.
What equipment do you work on?
We care for discrete hi-fi stereo equipment, the kind you find in good hi-fi stores.
This includes quality Australasian, European, Japanese and North American discrete (non-integrated) hi-fi stereo (two channel) equipment including integrated amplifiers, phono preamps, preamplifiers & power amplifiers, single cassette decks, CD players, DACs, receivers, tuners, some shortwave radios and turntables manufactured from 1970.
We cater for most good brands including Accuphase, Akai, ARCAM/Cambridge, Denon, Esoteric, JVC, Kenwood, Luxman, NAD, Onkyo, Naim, Mark Levinson, Pioneer, Quad, Rotel, Sansui, Stax, Sony, TEAC, Technics, Yamaha, and more.
We focus specifically on amplifiers, CD players and turntables. A spread of other components fills out our usually full booking schedule.
We cannot assist with:
Home cinema, multi-channel, AVRs/HTRs, Blu-ray, DVD, Laserdisc, VHS, PA, DJ, portable, car audio, record changers (BSR, Garrard etc), Bluetooth turntables (Crosley, Marley etc), soundbars, micro/mini/midi/shelf systems, 3-in-1s, radiograms, stereograms, lifestyle systems (B&O, Bose, Sonos etc), 4-track, reel-to-reel, headphones, speakers, musical instruments/amplifiers, most tube equipment, or equipment manufactured before 1970.
Why do you need to inspect equipment before providing repair cost estimates?
Because anything else involves guesswork based on incomplete information and that’s not how we gained the trust and respect of the hi-fi community.
I’m immensely proud of our reputation and the trust people have for Liquid Audio, but it’s no accident. Diagnosing what a piece of equipment needs is part of our process and creates happy customers and guesswork plays no part in it. Everything we do is determined by careful, hands-on assessment, testing and measurement. That’s how it should be done.
Guesswork
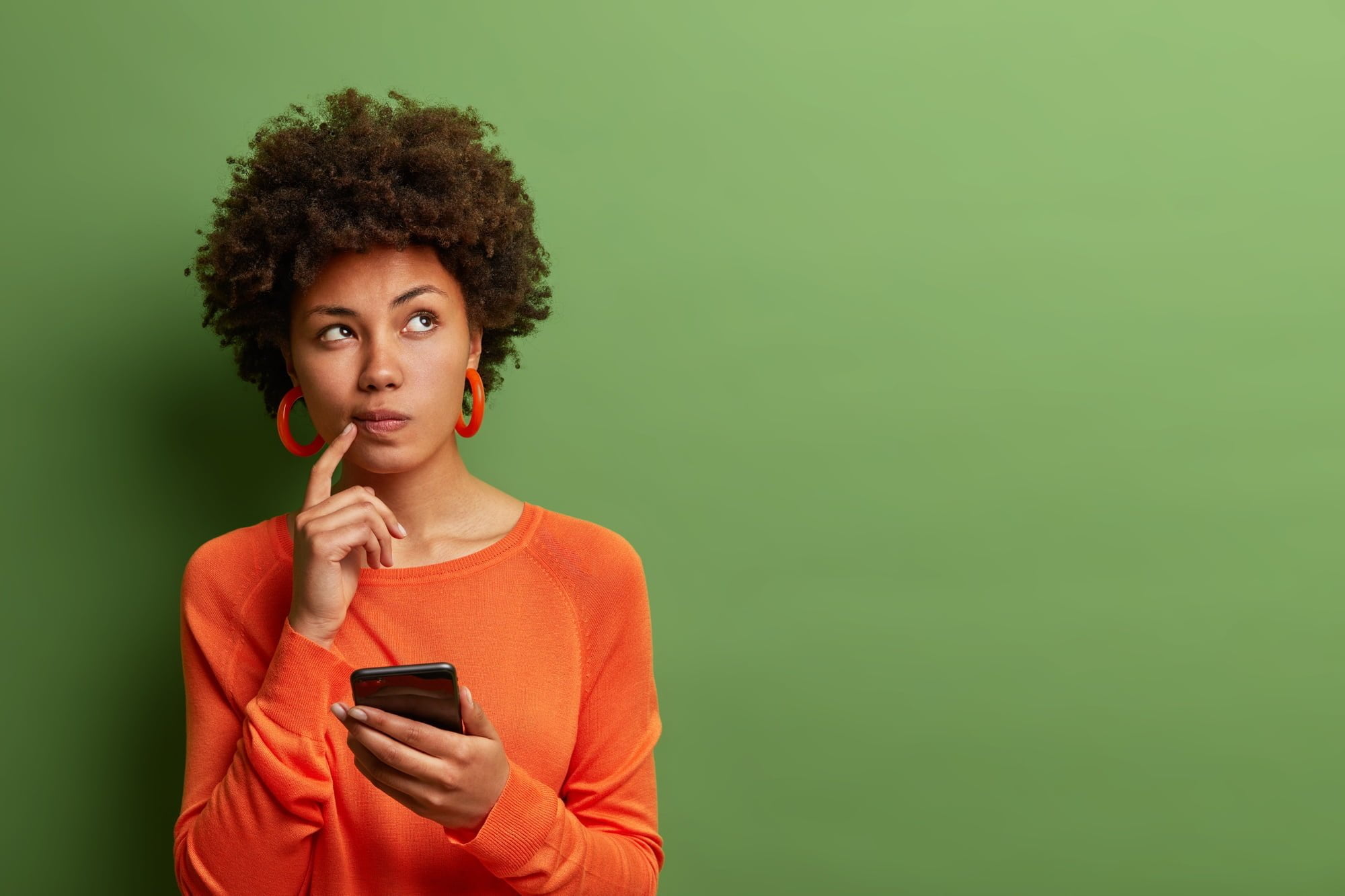
Say your amplifier won’t turn on. Why not? There is no way to know without inspecting it. The repair costs vary enormously depending on the failure mode so this isn’t something you’d want to guess about. What if your turntable won’t play records? Does it need a new idler wheel, belt or repair to the drive circuit? Who knows, but know this – nobody can know without seeing it.
How would you feel if you threw away a perfectly repairable piece of equipment because of an incorrect guess? Well, that’s exactly what happened with this Sansui AU-317 integrated amplifier:
The same technician deemed a Marantz CD-52 I recently repaired “Unrepairable and should be thrown away”. Both repairs were technical, though straightforward and affordable, saving both pieces when they were going to be thrown away. Nobody knows exactly what your equipment needs without inspecting it. Some folks don’t know even when they HAVE inspected it!
Estimates vs Quotes
Despite this logic, some expect blind quotes (rather than estimates) before a technician has assessed a piece of electronics. Delivering the lowest ‘quote’ on work one hasn’t even seen, to customers who will go elsewhere unless you do, is highly problematic and a driver of poor work across all sectors.
By definition, work driven by the lowest cost will deliver corner-cutting, poor workmanship, and poor results. Those driving this quest for the lowest price will ironically be unhappy when cut-price work hasn’t been done properly. This low-quality death spiral is entirely avoidable by simply understanding that there are far more important considerations.
Despite the silliness of blind quotes, businesses provide them because they bring in work with a certain type of client. I’m in the fortunate position of never needing work, partly because I do not cut corners, an irony that I hope is not lost on readers. On principle alone, we never provide blind quotes and because of our focus on quality, we are better served assisting customers who don’t expect them.
Estimates are quite different. They allow for the variables that affect the cost of a job including discovery factors like condition and service history, fault analysis, customer requests and parts required in each unique case.
We provide estimates where requested, usually after having assessed the unique requirements of a piece of equipment, and its owner. Customers trust us to charge fairly for the work we do, something we are known for.
Mike … you, of course, are a gem. We are so lucky to have someone as passionate, intelligent, ethical and hardworking in little ol’ Perth.
David H
More…
Find out more with these repair-related FAQs:
Everyone has a different opinion, where can I find informed hi-fi advice?
You need to find sources with a) the fewest conflicts of interest and b) the most accurate information.
Information vs Opinion
As the great Plato once said:
Opinion is the medium between knowledge and ignorance.
Opinions are everywhere and, quite honestly, most aren’t worth the ‘paper’ they are written on. I often speak with advice seekers who tell me:
“Mike, I read in a forum that I should buy XYZ, what do you think…?”
The overwhelming problem is that most folks in forums a) can’t help you, but b) think they can, leading to rabbit holes of wasted time, energy and money. It’s worth knowing that real experts and specialists rarely get involved in public forums related to their work. The vast majority of commenters lack the knowledge and experience to help themselves, let alone others!
As a result, forums are often filled with subjective, regurgitated, conflicting opinions, technically incorrect ‘facts’ and pseudo-scientific nonsense. I avoid them entirely, except for private, technical forums I’ve been part of for years.
Then there are retailers, often blinded by marketing, unable to parse the technical facts and heavily conflicted by the need to sell you equipment. This isn’t a judgment, merely an observation that I challenge anyone to refute honestly.
There are a few good retailers, but most don’t know which information is important/right/wrong. They all sell competing products, many of which they know to be junk, leading to more rabbit holes of wasted time, energy and money.
This conflict of interest is a huge problem, the elephant in the room, yet people turn to retailers for advice, which is ridiculous when you think about it. It’s like visiting a car dealership, asking what brand of car they think you should buy and expecting an unbiased response. Silly, right?!
Good Sources
Finding the best advice is quite easy when you understand that this relies on finding the best sources of information. There are a couple of things one needs to qualify as a good source:
- The fewest conflicts of interest. No retailer who sells products can genuinely offer you impartial advice about equipment they don’t sell and are not trying to sell you. They need to sell products they offer, a fundamental show-stopper in terms of conflicts of interest.
- The most real, hands-on experience with the equipment you are interested in. There’s a reason I own and have owned a range of high-end digital and analog sources, amplifiers, speakers, etc and I work on this stuff every day. That means I own and listen to equipment most have only dreamt of owning and listening to. I don’t get my information from anywhere other than direct hands-on experience. This is extraordinarily rare.
These filters rule out most sources of advice as useful, trustworthy ones, so be careful. Our advisory service is one widely respected, dependable source. There are others, but there just aren’t many.
The reasons are simple: I’m a technical specialist, not a retailer. I have no conflicts of interest in recommending hi-fi equipment and discussing how to improve your hi-fi system because I receive no commissions or kickbacks and I don’t need to sell equipment at all. I also don’t need people to seek my advice as this is a tiny fraction of my business.
Yes, you must pay for my time in the same way you would other specialists such as a doctor or lawyer, but you get a completely different calibre of information that satisfied customers from around the world greatly appreciate.
Can you help me fix my equipment without me bringing it to you?
In most cases, unfortunately, not.
I love helping people – I was a science teacher for 15 years – but remotely guiding people I don’t know through complex technical work that I’m not formally engaged to undertake is not a service I offer.
There are four main reasons:
- I don’t want to guide anyone into a situation where they hurt themselves or their equipment. Attempting to describe concepts/processes, assess/measure parts, and use test and measurement equipment and soldering tools while keeping someone who likely doesn’t understand the dangers of electronics safe is simply not sensible.
- Most equipment owners (not all) lack the equipment, knowledge, parts and experience needed to undertake electronic work, guided or otherwise. Better to take it to a specialist.
- People often don’t realise that electronics repair can be time-consuming and expensive. It will almost certainly be MORE time-consuming and possibly expensive using the guided DIY approach, especially if there are issues created by this approach, which there usually are.
- The equipment owner has to pay for the guidance/time, but may not be capable of repairing their equipment. What then?
- I need to safeguard my IP and proprietary solutions, many of which I’ve developed from scratch, for maintaining hi-fi equipment. My work is already copied, without attribution or remuneration, and often for commercial gain and I often receive requests like this from/for other commercial repairers. I like helping people, but my competitors, not so much!
I encourage local, hands-on specialist assistance as the best option in most cases, where such individuals exist. For those needing assistance who cannot bring equipment to me and cannot find any local specialist help, our paid advisory service may be able to help. I make no promises, but you are welcome to ask.
Note that I am unable to provide service data, more on that here.
Can you sell me service parts?
No, we don’t operate a retail store or sell service parts like belts, integrated circuits, and capacitors directly to the public.
We do however stock thousands of electronic parts, belts, cartridges, headshells and turntable mats. We fit these parts as needed when you book your equipment in for service, repair or improvement.
How is Liquid Audio different from other repair businesses?
Many aspects of our approach make us different from other outwardly similar businesses.
Quality and attention to detail are our focus and businesses championing professionalism and quality over making a quick buck are sadly rare these days. Folks looking for a ‘cut-price, cut corners’ approach won’t find it here, though such businesses exist, delivering predictable results: sight-unseen ‘quotes’, shortcuts, poor workmanship, ‘Swell-Long’ capacitors, devalued or destroyed equipment and even court cases.
There are a heck of a lot of pretenders and copy-cats out there, but go back to my oldest articles and you’ll see how long I’ve been doing this work. Even better, do a Google search for text from my site and see where that text originates. Right here, all of it, every single image and word is straight from me.
Everything from our premium tools and test equipment to the way we approach things is different. But it’s not just this. I’m old-fashioned, I believe in courtesy, professionalism and being straightforward with people. I have a genuine love of hi-fi gear. I love working on it, love the history and classic designs and find it incredibly satisfying to focus on the tiny details necessary to have it running at its absolute best.
I own this business and I service and repair everything, run the website and write the articles. I’ve been contributing to the hi-fi community for more than a decade. These are just some of the things that make Liquid Audio different and so busy!
We take our goal of quietly preserving hi-fi equipment and bringing enjoyment to its owners seriously. We charge what it costs to do a job carefully, to the highest standards, adding value to cherished equipment and delivering the best results for customers who care about the details as we do. If our approach resonates with you, don’t hesitate to get in touch.
You take on some big jobs, are there any you won’t take on?
We generally avoid equipment in poor physical condition, damaged by other repairers, heavily modified or equipment that isn’t serviceable.
Don’t get me wrong, the challenging jobs can be very rewarding, but we’re not interested in trying to make a silk purse from a sow’s ear or charging you for trying to.
These days we filter equipment in poor condition because it becomes a problem for us this shouldn’t really become our problem if you think about it. We’re here to help, but ultimately we also want good outcomes for everyone and that means not taking on jobs where the odds are stacked against all of us.
Do you sell pre-owned hi-fi equipment?
Yes, we sell quality, pre-owned hi-fi equipment via our popular store.
Current inventory is viewable in the store along with equipment in our sold equipment galleries 1, 2, 3, 4 and 5.
Purchasing quality pre-owned hi-fi equipment from Liquid Audio has many benefits:
- Equipment is expertly inspected, tested, cleaned, detailed and serviced
- Most pieces come with a 3-month peace-of-mind warranty
- We carefully select and stand behind every piece we sell
I hand-pick every piece and I’m very selective about the equipment I make available for sale. You can purchase equipment from our store knowing that it comes from one of the most respected businesses of its type.
Visit our store for current inventory and feel free to browse our sold equipment galleries 1, 2, 3, 4 and 5.
Why should I purchase a consult?
Expertise
People generally consult specialists because they’re seeking the highest calibre of expertise and insight, which maximises results and minimises wasted time and money. It’s why we engage accountants, doctors and lawyers, rather than relying on Google or Dick next door. This is always the best option, though many only learn this after much time and money have been wasted. A better question for those seeking the best assistance is: Why wouldn’t you consult with a specialist?
Get the best advice you can find from Mike, and please, stop quoting forum posts as authorities. Only the guys who actually work, live and breathe this stuff really know.
Jon S
Entitlement
Our advisory consults are a great example of a specialist professional service, delivering expertise and factual information without retail conflicts of interest. It brings many benefits to those seeking our guidance, but also requires constant time and energy input, and time + energy = money.
It’s unfortunately not possible to engage with all the requests for advice I receive without utilising a standard pay-per-use framework. Most immediately understand this, but some mistakenly believe they are ‘entitled’ to assistance/time/energy, which is, of course, as ridiculous as the idea that those individuals work for free.
Consults pay for themselves and so are effectively free anyway, but 15 years of ethical business, tens of thousands helped, 5+ million views, and over 650,000 helpful and completely free words confirm: We don’t owe anyone. Anything.
Examples
G: ‘G’ sought technical assistance with his expensive Sansui amplifier after enjoying my free content. When I suggested he purchase some discussion time, G exploded: “F*** you, I’m not going to pay you.”
K: ‘K’ read my KD-600 turntable articles and sought improvement advice for his KD-600. When I suggested he purchase a consult, K threatened that he knew “Someone in the Australian Tax Office”. K sneakily tried to obtain my help some years later, hoping I’d forgotten. I haven’t.
M: ‘M’ purchased a 30-minute consultation, which yielded outstanding results and a game-changing amplifier purchase. His mistake was to angrily claim he’d “Paid for 60 minutes but only received 20” before checking his records. I sent proof of his 30-minute purchase and 50-minutes assistance, yet received no apology.
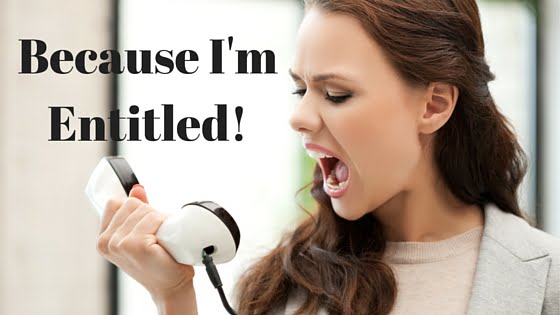
Exchange
With our pre-paid advisory service, advice seekers pre-purchase consults tailored to their needs. This is a fair, flexible approach, aligned with our core values of maximum quality and value, and minimum wastage.
Mike … you, of course, are a gem. We are so lucky to have someone as passionate, intelligent, ethical and hardworking in little ol’ Perth.
David H
Paying for a product or service is a fundamental aspect of commerce. It supports hard-working specialists and small businesses, properly values a specialist’s time, reduces time/energy/goodwill-draining interactions and fosters positive, mutually beneficial exchanges with good people.
Expert advice also pays for itself, saving time and money and delivering the best results, making it one of the most sensible purchases most can make.
Do you sell belts, styli and cartridges?
Yes, we keep thousands of parts in stock and have speedy access to many more.
We don’t operate a retail shopfront though, so we don’t sell bare service parts for example. Instead, we supply and fit them as part of the services we offer.
How long will my repair take?
This depends on your equipment, what’s wrong with it and how many jobs are in the pipeline.
Each job will be done in turn and according to workflow considerations. All jobs are in a queue for attention and some take longer than others to process. Some jobs require parts to be ordered and some suppliers take longer than others to deliver.
Do you offer hi-fi equipment inspections?
Yes, we offer pre and post-purchase hi-fi equipment inspections, cartridge inspections and more.
A Liquid Audio report can save people hundreds or even thousands of dollars and a great deal of pain.
Imagine for example having an expensive amplifier inspected prior to purchase. I find that many hundreds of dollars of work and repairs are needed. You take my detailed report to the seller and negotiate a fair price, based on my findings, that saves you far more than the cost of the inspection. This is a great result.
Is my equipment repairable?
Probably, but this always comes down to what your equipment is and exactly what’s wrong with it.
Various factors come into play here, including the make and model, its general condition, fault/s, your budget and so on. Most faults are repairable, but some combinations of equipment/fault/condition may render repairs difficult, or non-viable. Inspection is the only way to know that and, naturally, as soon as we know, we will let you know!
Do you provide a warranty?
Yes, we offer an industry-standard 3-month warranty on parts and workmanship.
In the rare event that you experience an issue related to any of the work we’ve done for you, we will fix it, where it’s viable to do so or refund you where it’s not.
Why repair vintage equipment when I can buy new?
Because the vintage gear you already own is almost certainly better than any decent new gear you can afford!
Nothing you can buy for sensible money now is built like vintage hi-fi equipment, or made in Japan. Nor is much of it very sonically inspiring either, something those of us who don’t make a living selling new hi-fi gear are not afraid to tell you.
I regularly see 40-year-old hi-fi equipment that has come in for its first maintenance. Do you think your BOSE or Sonos ‘thingo’ will be working in 4 years time, let alone 40?! No, and I can guarantee the crappy dock, soundbar or Bluetooth whatever doesn’t sound as good as proper vintage hi-fi gear either.
Experience shows that $500 vintage amplifiers regularly crush $2000 new ones in terms of build and sound quality. If your vintage amplifier only needs some routine maintenance, why wouldn’t you get that done?!
The the hi-fi store guy promised a new turntable would kill my classic deck, is this true?
Ah, this old chestnut. No, generally these statements are made simply to sell you new equipment.
Manufacturers, retailers and salespeople need to sell you stuff to stay in business. It makes sense right? Imagine walking into a hi-fi store, telling them what you have and the sales guy saying:
“Wow, your turntable is awesome, probably better than anything here up to around $3000!”
Rare honest salesperson
Sales staff are generally paid a commission. This reward for selling creates a very real conflict of interest inescapable by all but the most ethical salespeople, strangely often overlooked or not even considered by consumers.
Remember, there is NOTHING new in turntables except styling. The very best turntables have mostly all been made, somewhere between 1970 and 1985. There are a few notable exceptions, but you get my point. The industry needs you to believe that new gear is better, otherwise, everyone’s out of a job.
Consider this: I don’t have a turntable to sell you and I don’t operate a retail shopfront. In fact, I’m not trying to sell you anything, nor do I mind whether or not you believe me. I fix and service equipment, old and new, that’s my core business. But others are trying to sell you something, aren’t they? Do they have new turntables to sell by any chance..?
By the way, I’m not suggesting that all salespeople are dishonest. Ethical salespeople exist, like my friends Simon and Tony @ Douglas Hi-Fi and Pierre @ Revolution Turntable. Make sure you ask your hi-fi store guy what turntable he owns. This will help ensure there’s some credibility to the advice you are being given.
But surely new technology must sound better?
What new technology? Modern analog gear uses the same classic circuits, but often with lower-quality parts and construction.
There is very little ‘new technology’ in analog audio. Most analog electronic circuit designs date back to the earliest days of tubes and transistors. Even things like class-D and class-T amps are not new, nor are they designed to produce the highest fidelity.
Yes, there are some superb new op-amps, transistors and circuits that utilise them, but premium parts and circuits are found in premium equipment. A strong argument can be made for the fact that the best analog audio engineering is all discrete component design, though, with as few op-amps as possible.
My Tektronix SG505 ultra-low distortion audio signal generator that I use in the workshop is a great example. This wonderful piece of gear dates back to the 1980s and yet boasts < 0.0008% distortion, using ‘old’ NE5532 and similar op-amps! This thing is an order of magnitude better than most gear I ever test, but it uses old technology!
High-end gear often contains tubes and… oh that’s right, all the best tubes are old ones, from the ’50s and ’60s. They certainly aren’t new. Actually, this ‘new technology’ thing is grossly overstated and misunderstood.
Digital is different. As an emergent technology, things are improving, at least on paper. It’s still all about the execution though. My end-game Accuphase DC-91 DAC from the 1990s still sounds better than any other DAC I’ve heard, old or new. That is mostly because of the design, engineering and execution, not the DAC chips (16 of them) used inside.
Where this is more important is in affordable new gear. Cheap new DACs often sound better than cheap older ones. Cheap new amplifiers though, from experience, do not.
I’ll leave you with one final thought, from an old ex-science teacher: We put men on the moon in 1969, with old technology. Do you think we could muster up the same effort now? I’m not convinced we could.
Doesn’t your hi-fi system contain lots of new gear?
No, it doesn’t!
I own a tuner from 1975, cassette decks from 1979 and 1983, a CD player, DAC and preamplifier from around 1995, step-up transformers from around 1980 and my cartridges range from 1980 – 2009. My two pairs of speakers are from the late 70s and 2003, though my cable is relatively new. The newest thing I own is my power amplifier, from 2021.
So, my system consists of mostly older or even vintage gear, but it’s a mix and constantly evolving as most people’s systems do, if they are actively seeking to improve them.
So the retail machine is designed to get people to ‘trade-up’ to new equipment?
Of course, but are you honestly surprised..?
Ask owners of newer gear how they feel about their expensive “superior modern equipment” that often dies just outside of warranty and is then deemed non-viable to repair. Read the reviews. Every new piece of gear sounds “significantly better” than the one preceding it, right? OK, so how then is it possible for a 40-year-old amplifier to sound better than a new one?
Seriously, explain that. If each year brought significant improvements, older gear would sound awful compared with gear with 40 years of continuous improvement. But it doesn’t and anyone with decent rears and experience will confirm this. Unfortunately, many tricks are played on the average consumer.