The beautiful and iconic Kenwood KD-650 turntable is one of the very best decks of its era. Come with me as I repair an elusive fault, overhaul and review this classic deck.
It’s no secret that the Kenwood KD-600 is one of my favourite turntables. I’ve owned a KD-600 for many years and this is how she’s currently set up, with Jelco arm, FR cartridge, headshell, and Kenwood TS-10 ceramic platter mat. The Kenwood KD-650 you see here comes factory-fitted with an excellent Kenwood tonearm.
I’ve written about servicing and repairing the KD-600 and 650 before, though this is my most comprehensive article on these decks to date. Before we get further into the article, check out my video covering the overhaul and repair of this deck.
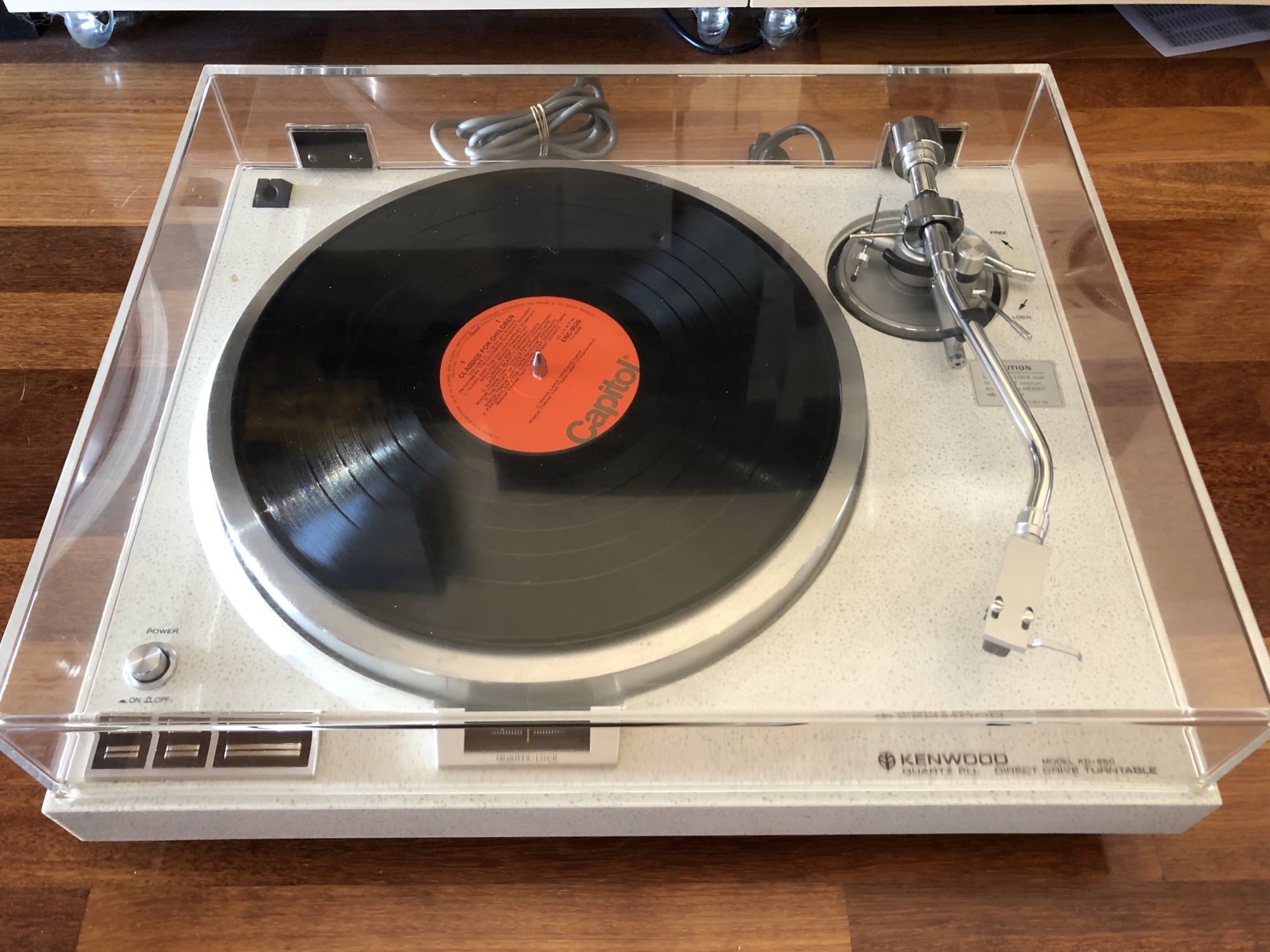
As mentioned, the Kenwood KD-650 and KD-600 are identical, aside from the aforementioned 10 inch Kenwood tonearm of the 650. The decks feature beautiful, slim styling and an unusual synthetic granite/marble chassis that looks cool even now. I particularly enjoy the way the light coloured chassis contrasts with the black base panel and light blue Kenwood TS-10 ceramic platter mat.
The fact that Kenwood sold a lot of KD-600s and 650s should be of no surprise. Heavyweight build and sound quality, state of the art specifications and high-tech materials combined with a sensible price-tag, created an instant classic for the company. Kenwood utilised high-quality materials that hold up very well over 40+ years. Add all this to excellent reliability and you’ll see why these decks have become almost unobtainable on the used market.
The KD-600 and KD-650 are technically better and better sounding decks than the much-loved KD-500 and KD-550, and original retail and current market prices reflect this. Their rarity and the reluctance of owners to part with them now, means they sell for big money if you can even find one.
Features
The Kenwood KD-650 features a brushless and slotless direct drive motor, quartz referenced phase-locked speed control, high-inertia machined and balanced aluminium platter and heavy rubber mat. The S-shaped tonearm is longer than normal, at around 245mm, or nearly 10 inches.
The chassis is made of Kenwood’s proprietary Anti Resonance Compression Base or ARCB synthetic granite/marble material. ARCB spawned many imitators, but this is the original and best. The deck is started and stopped with very cool touch sensors that respond to the lightest touch.
Just like the incredible Sony PS-8750 I wrote about recently, the KD-650 has proper quartz crystal speed control, here with the crystal contained in a thermally insulated box, for maximum accuracy and minimum drift.
Space-age engineering like this contrasts starkly with lightweight chassis, belt-drive, wobbly suspension and clock motors indexed to mains frequency offered by other manufacturers. As if 50Hz is a reference frequency one should use for a turntable! It’s little wonder the market flipped when decks like this, the PS-8750 and the Technics SL-1200 appeared.
Sadly, not much is made like this anymore, because it ends up being just too expensive and sitting on store shelves. One of the only modern equivalents is Technics’ SL-1200GR, a lovely deck, though not as good as a KD-600 / 650 and selling for a cool $5000 AUD, with a nice cartridge, from a reputable dealer!
Kenwood KD-650 Specifications, courtesy Vinyl Engine
Have a good look at these specs, they’re state of the art, even now. The 600 / 650 hailed from an era when these machines were the pinnacle of hi-fi audio reproduction. Wow & flutter of 0.025% WRMS is a superb spec. Most ultra-expensive new decks can’t beat this, except maybe the stunning Technics SP-10R. If pitch stability matters to you, and it should, look closely at decks like these.
Drive: quartz PLL direct-drive system
Motor: 20-pole 30 slot brushless DC servo motor
Platter: 33cm, 2.6kg aluminium alloy die-cast
Speeds: 33.33 and 45rpm
Wow & flutter: less than 0.025% WRMS!
Signal to noise ratio: more than -75dB
Tonearm: static balance type, s-shaped pipe arm
Effective length: 245mm
Overhang: 15mm
Stylus pressure range: 0 to 3g
Usable cartridge range: 2 to 12g
Dimensions: 490 x 165 x 460mm
Weight: 15.4kg!
Year: 1978 – 1981
Problems
My customer bought his Kenwood KD-650 for a very fair price, but it came with a critical fault. An electronics repairer owned it for years and had not been able to get this KD-650 to spin. It powered on but was completely unresponsive to the touch sensor. It turned out that one of the CMOS logic chips was broken and finding this fault was very satisfying.
In addition to a repair, the deck needed my standard KD-600 / 650 service including touch sensor deep clean, which I now do on all these decks. After completing other service elements, a KD-600 / 650 should be carefully set up and adjusted, using an oscilloscope and digital multimeter. There is no shortcutting this process, so let’s go!
Overhaul
The first steps involve servicing the switch and replacing some capacitors. As I often explain, the original capacitors were fine, but my customer requested I replace them as part of this overhaul, a perfectly reasonable request.
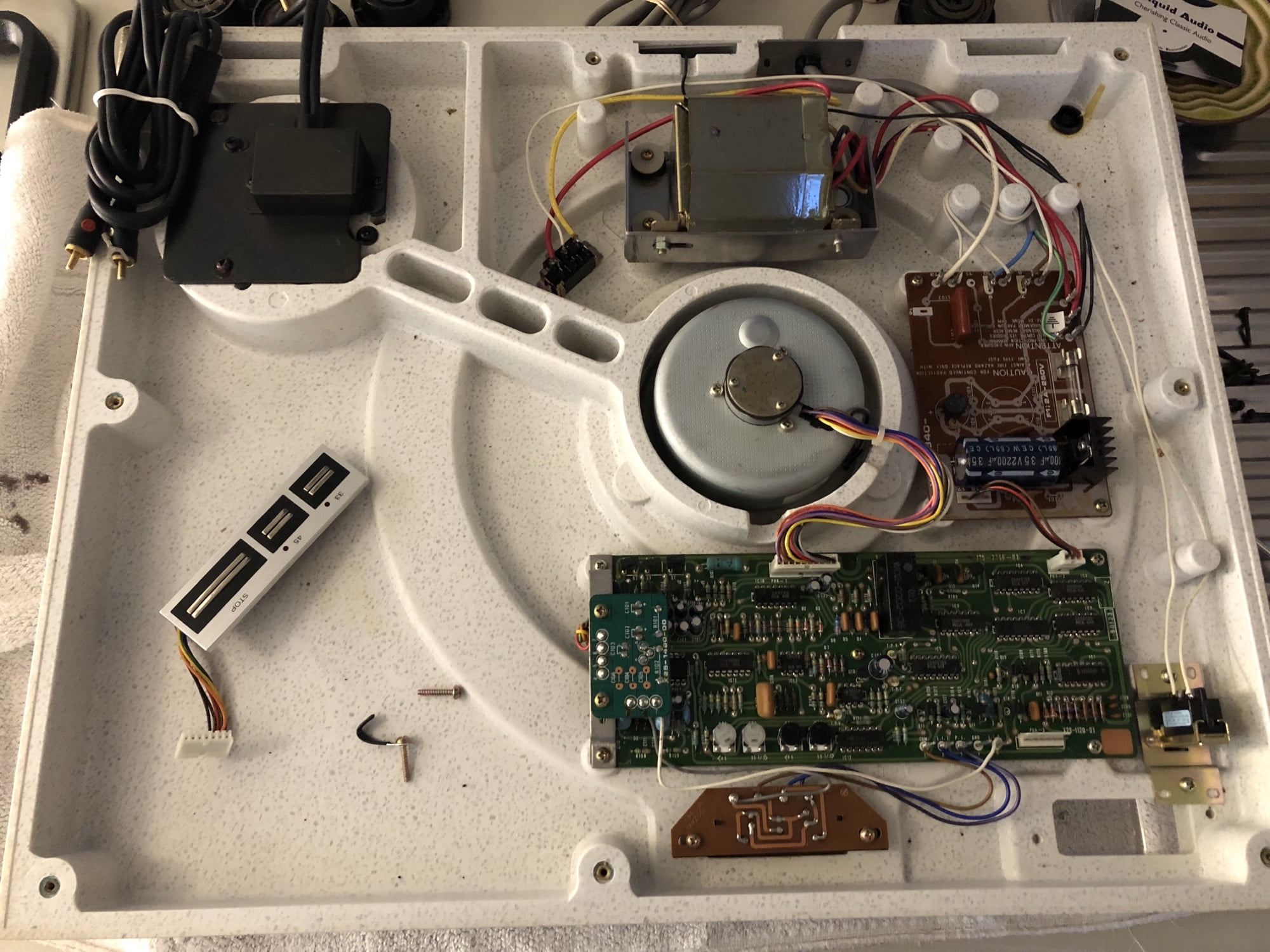
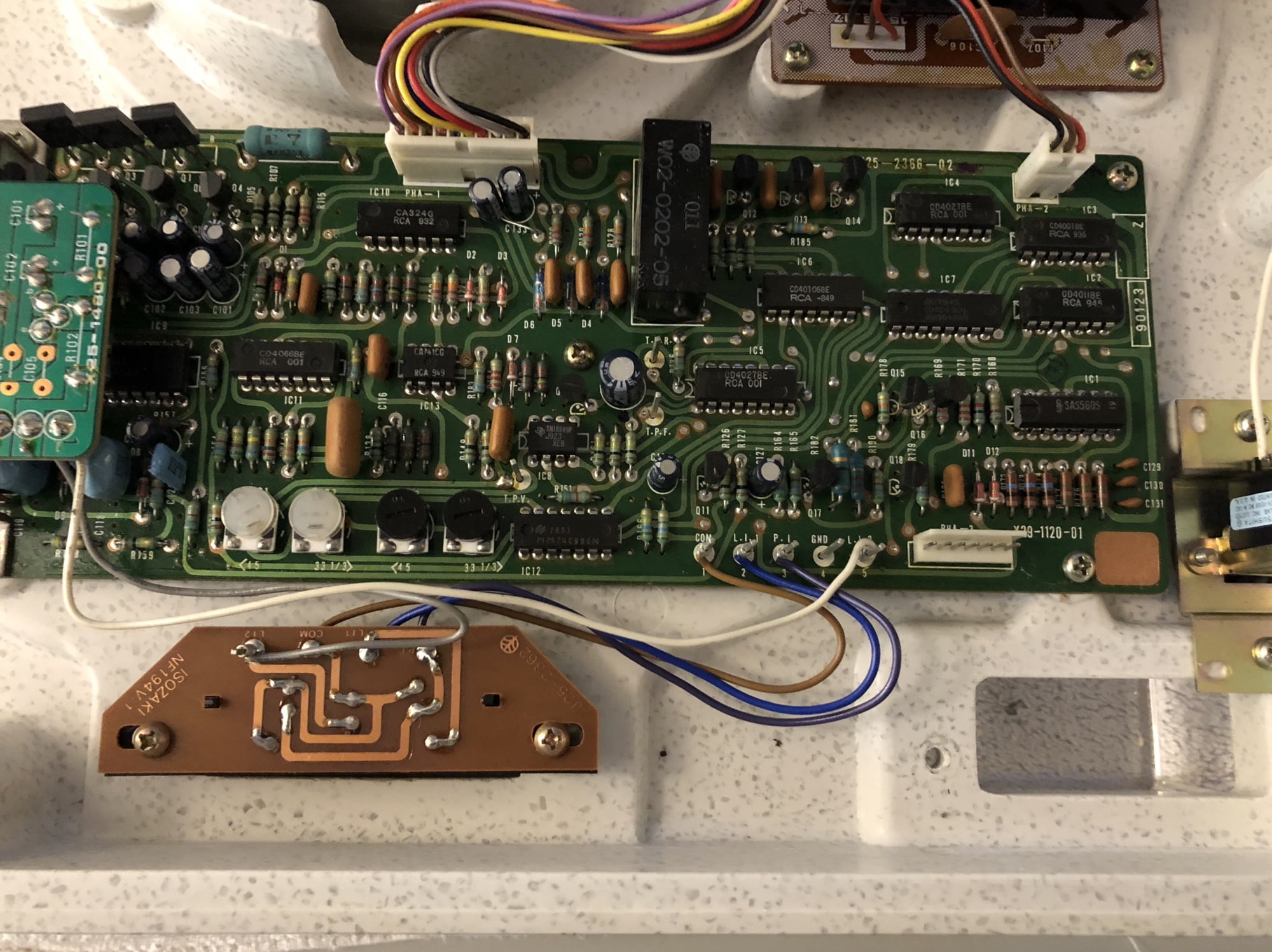
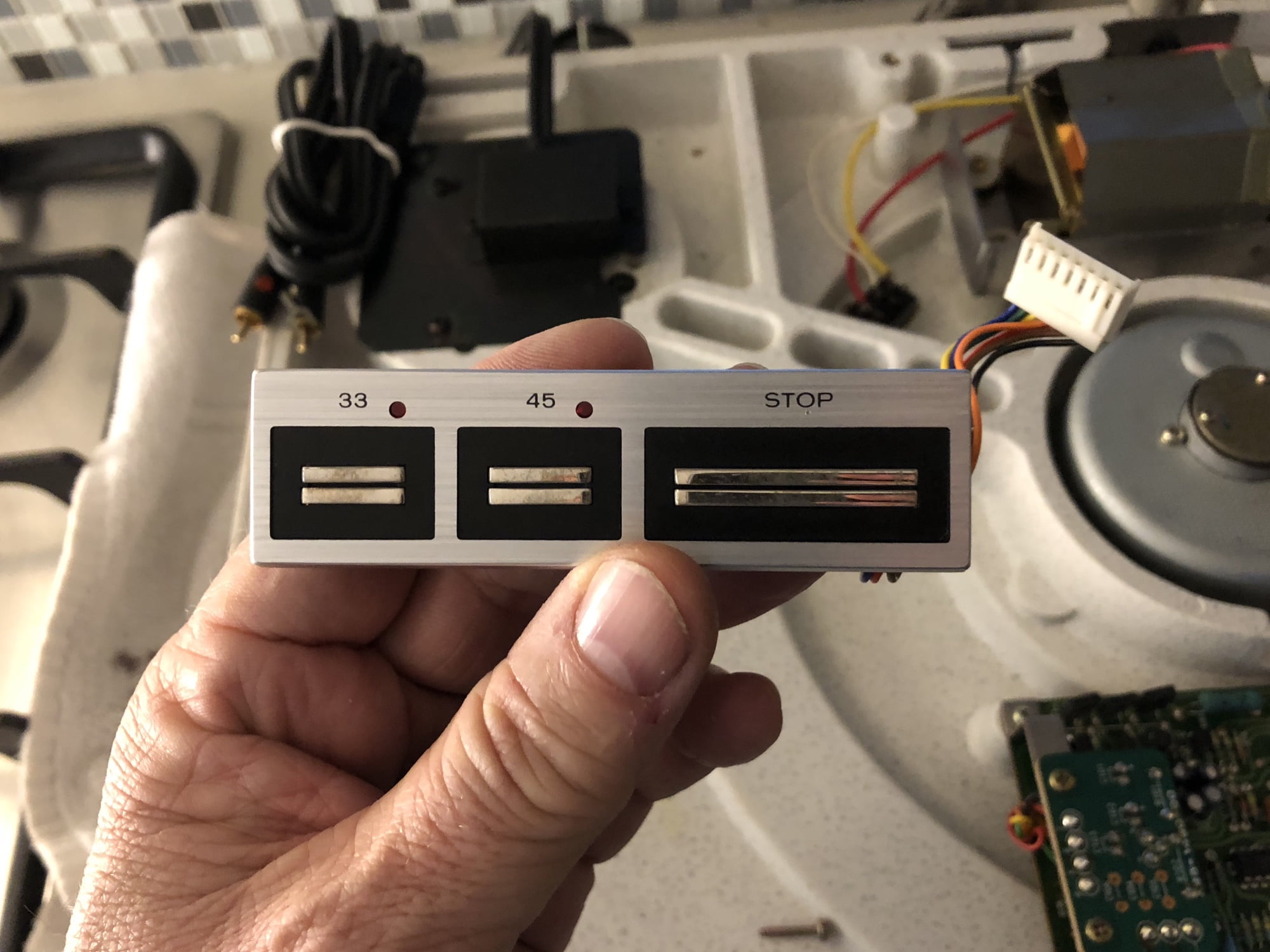
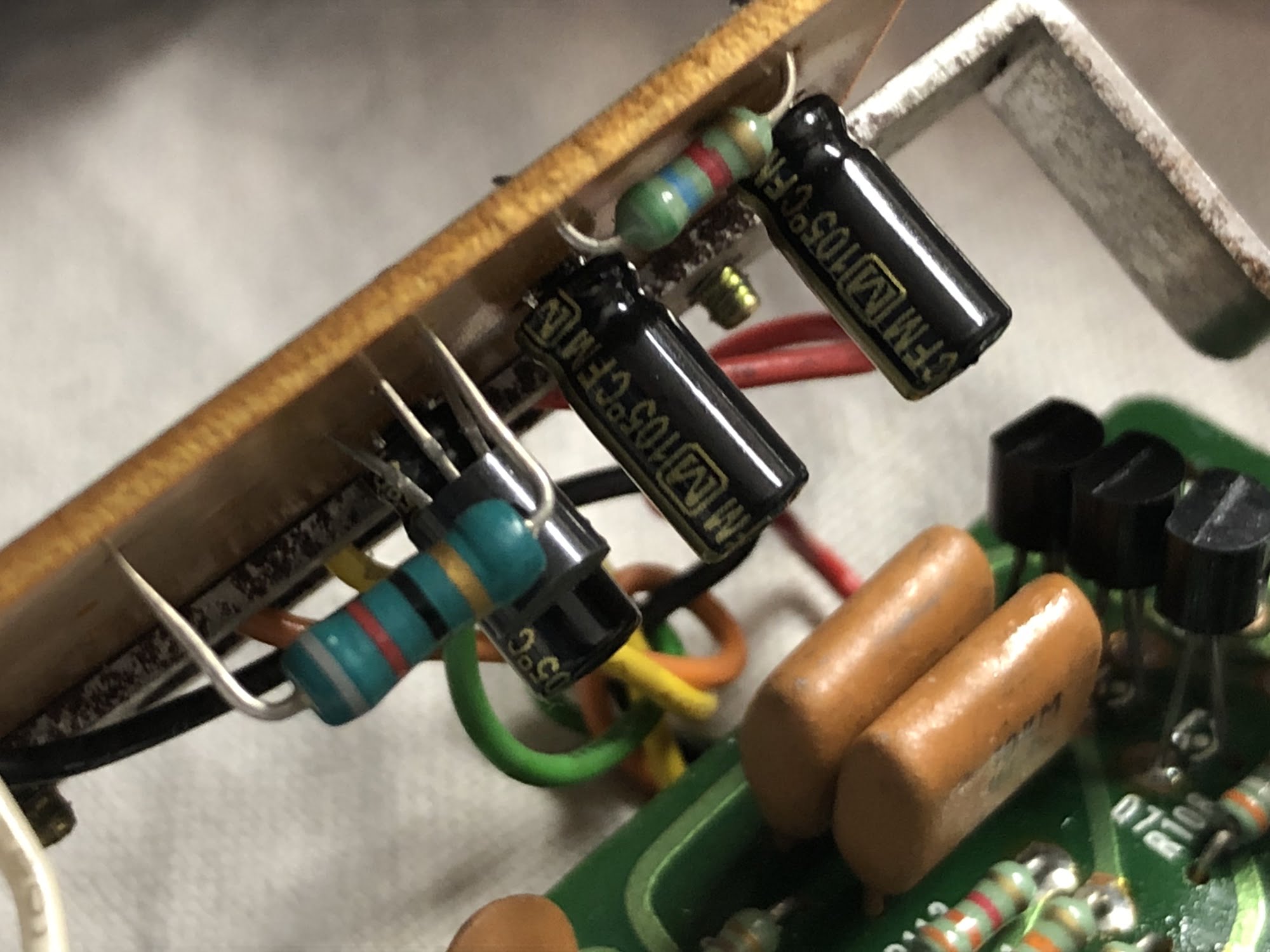
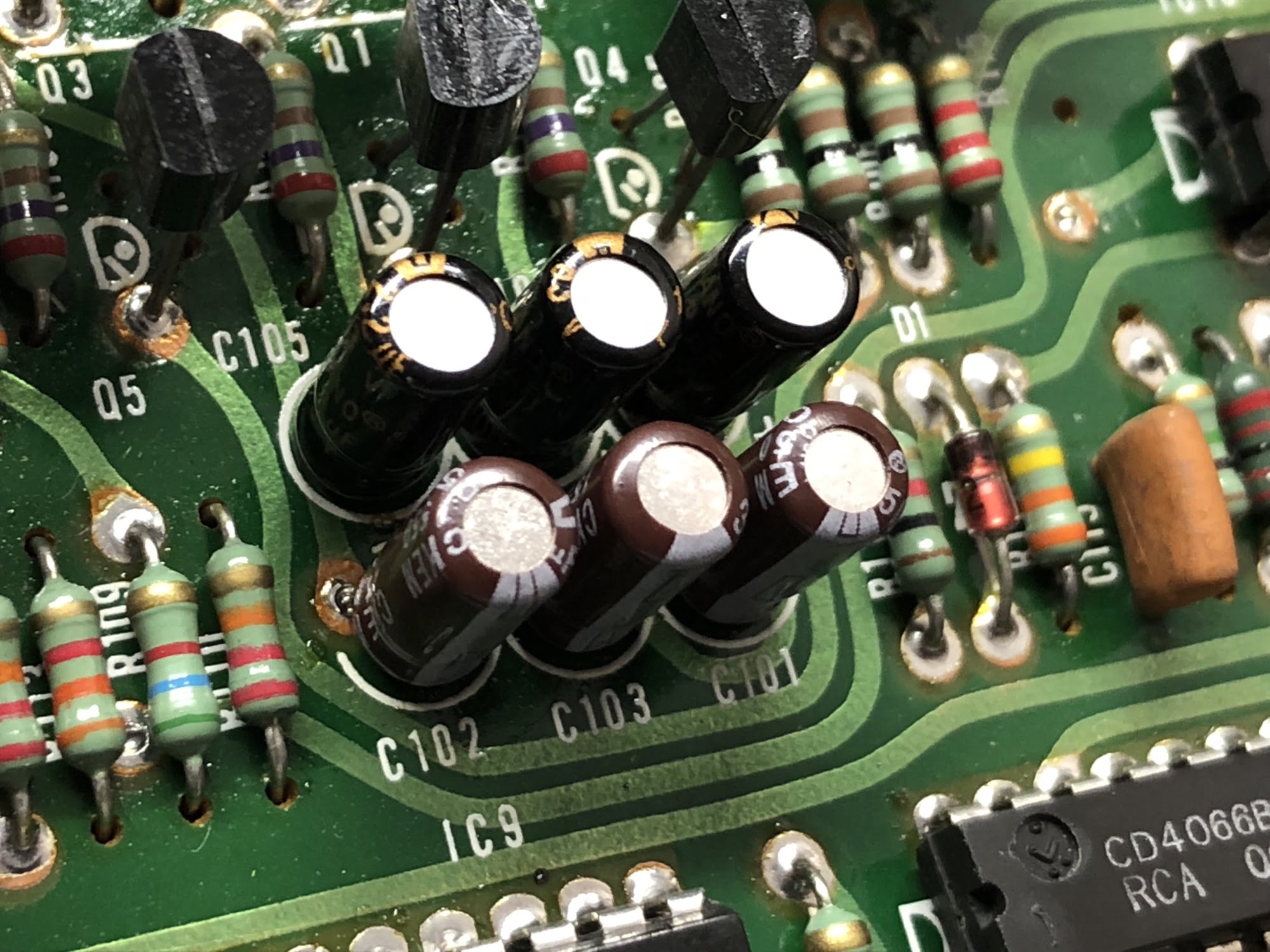
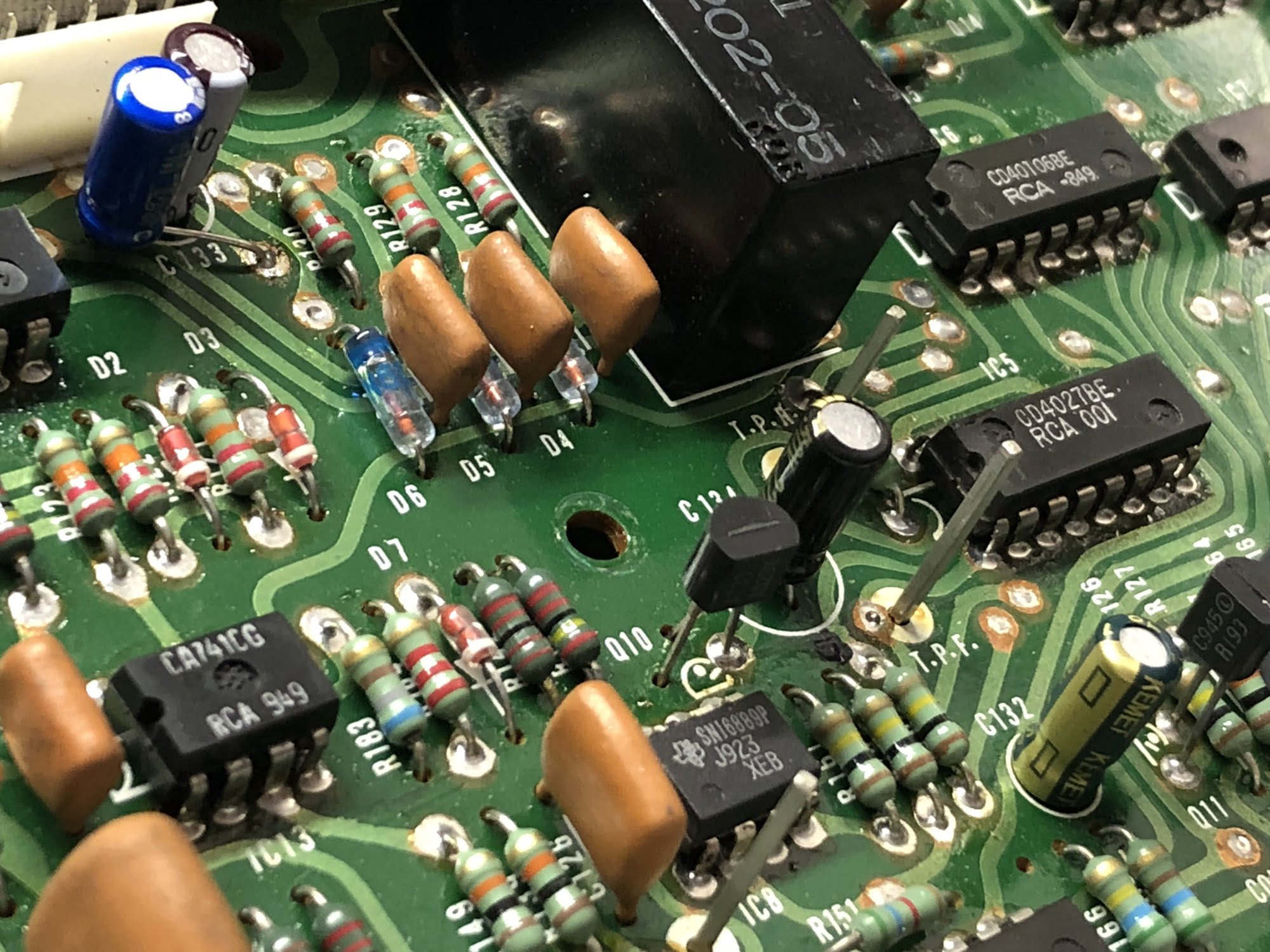
Repair
Time to find and fix this weird Kenwood KD-650 control issue.
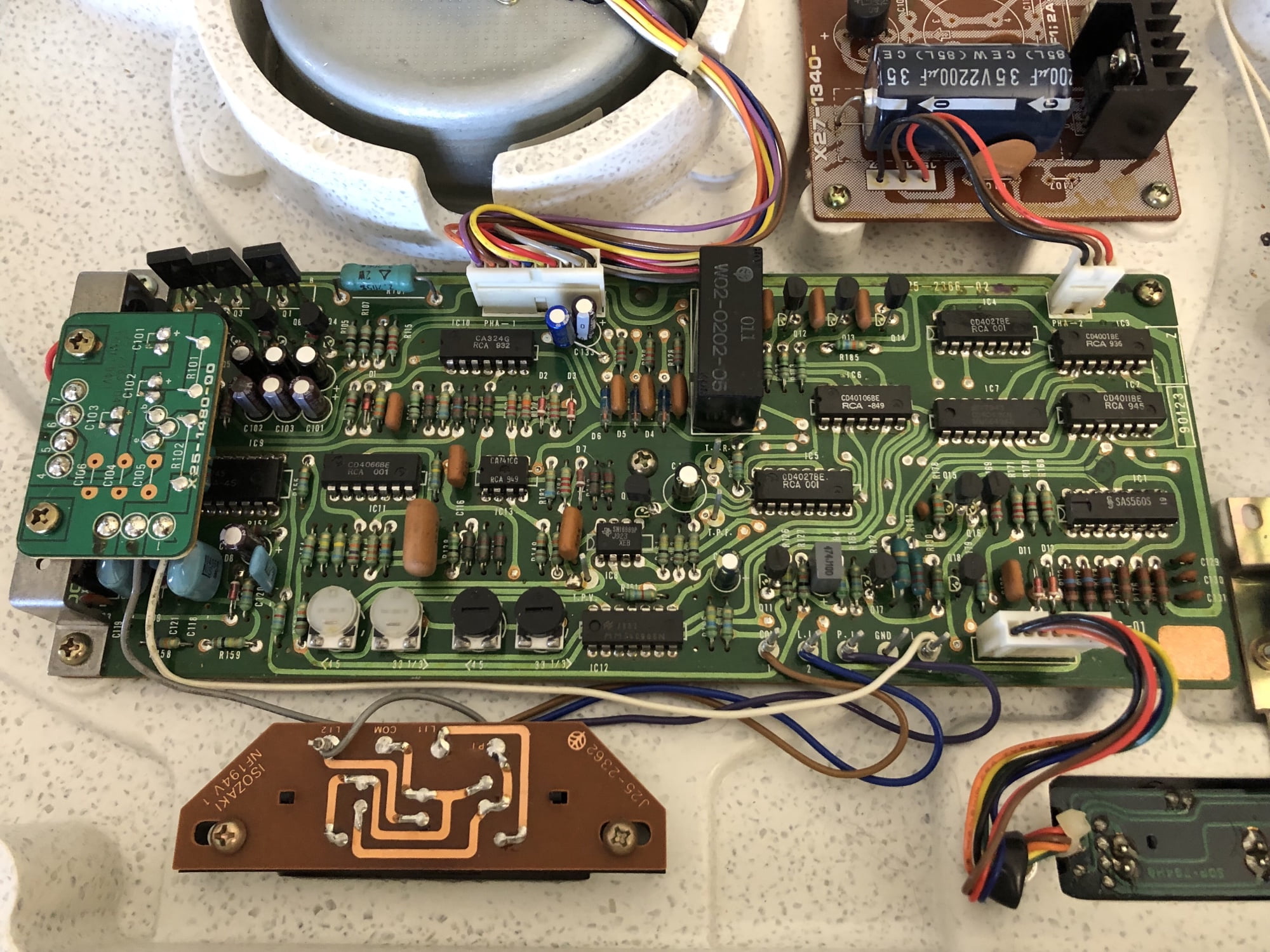
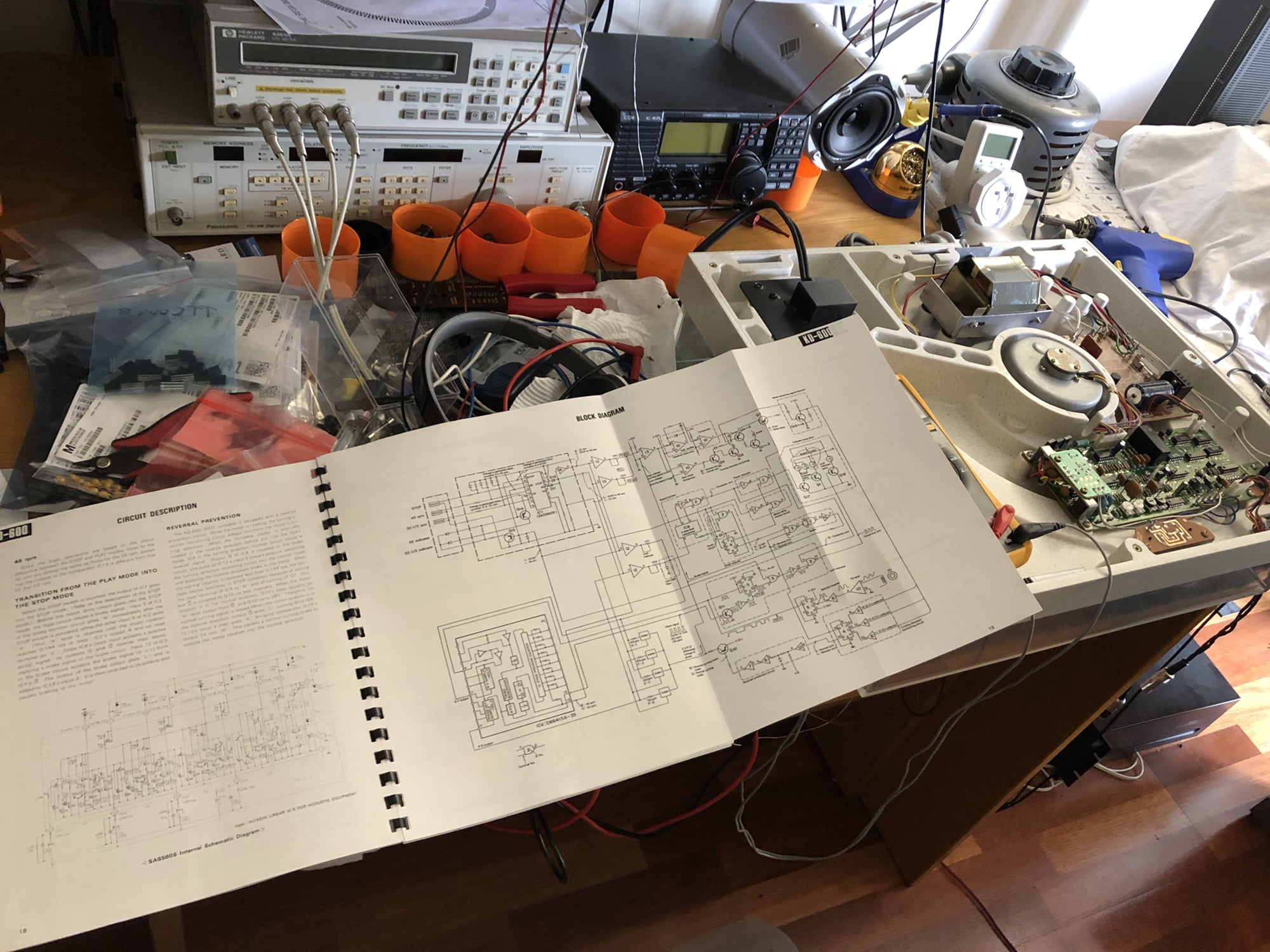
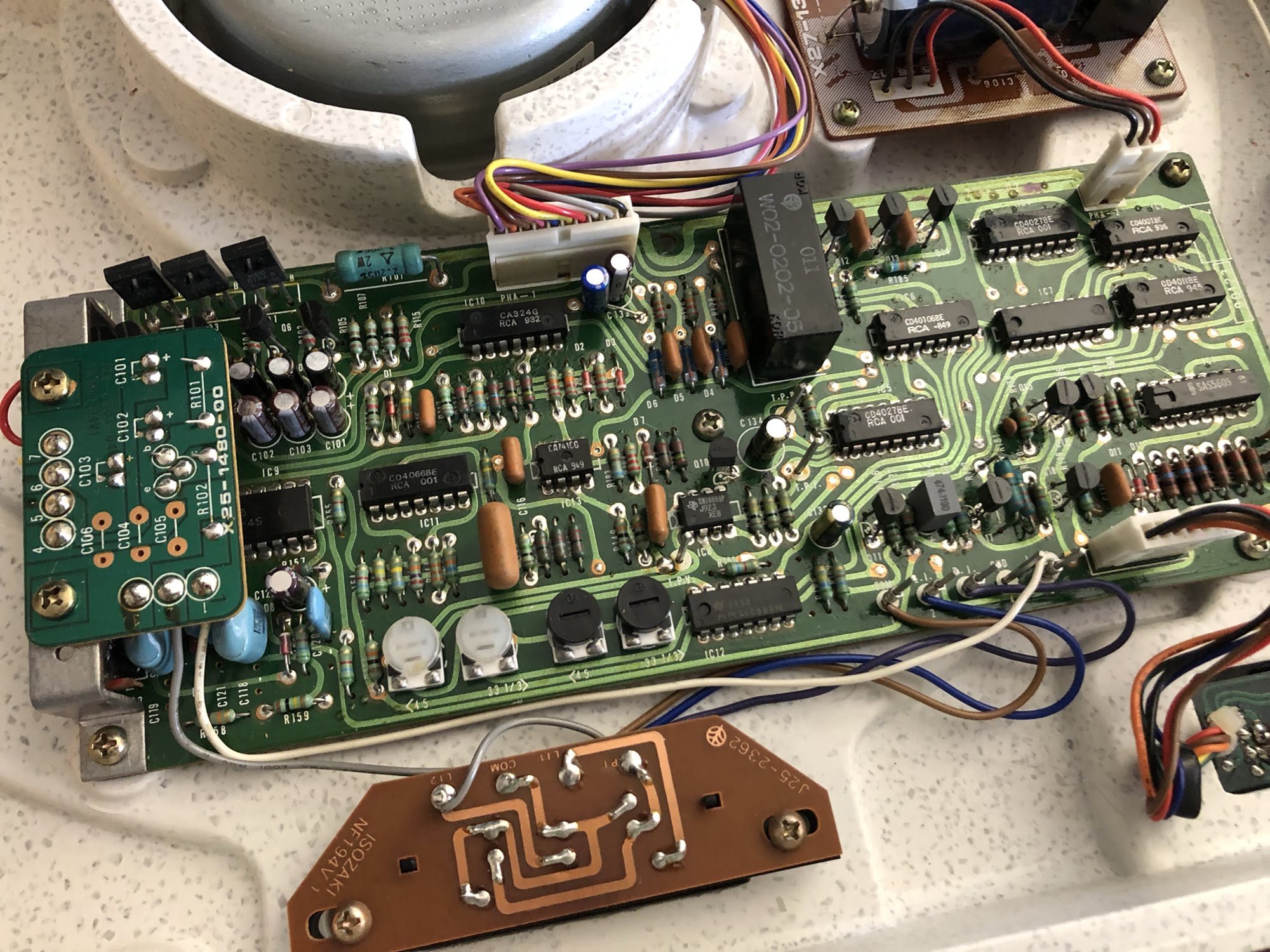
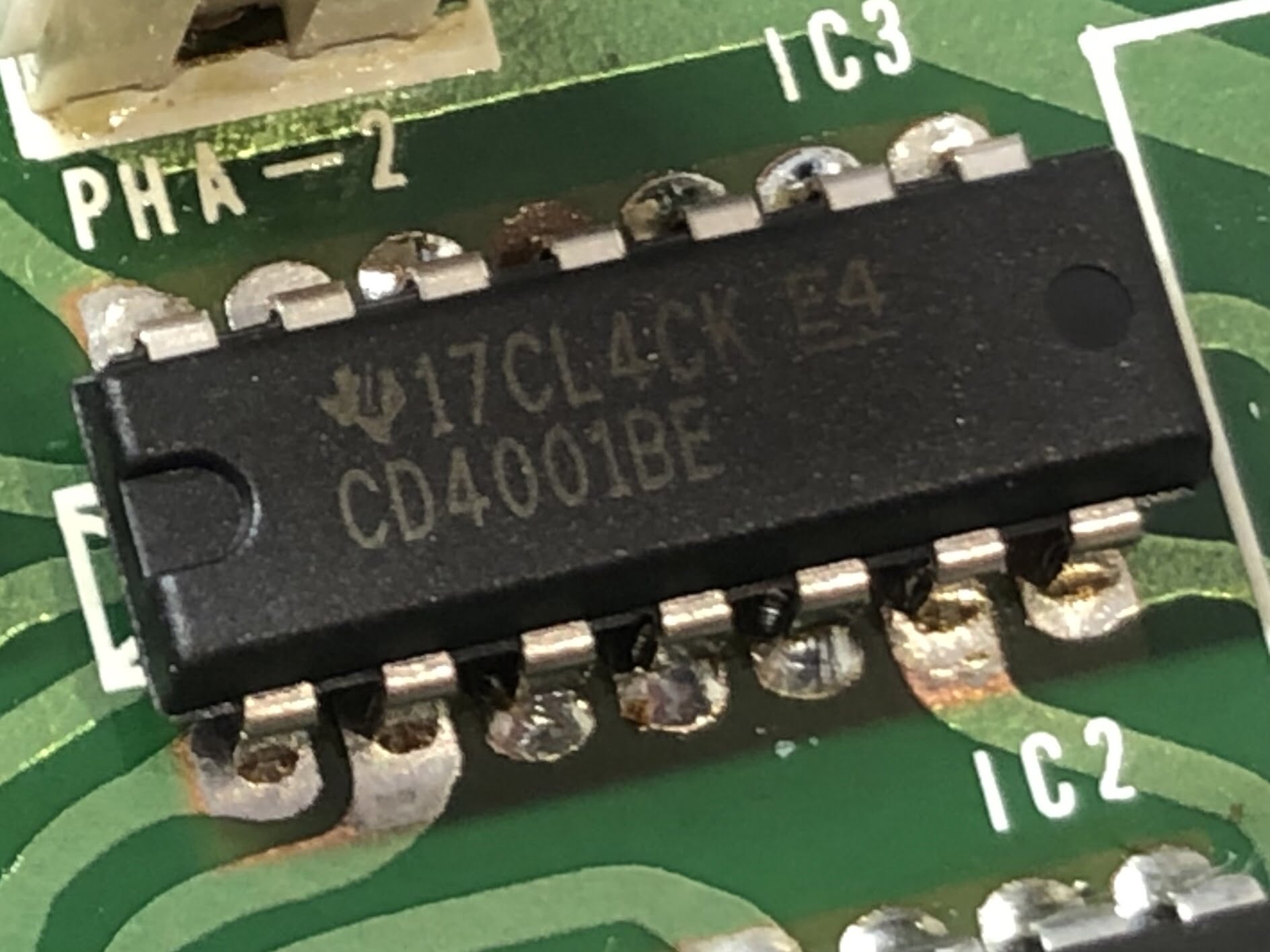
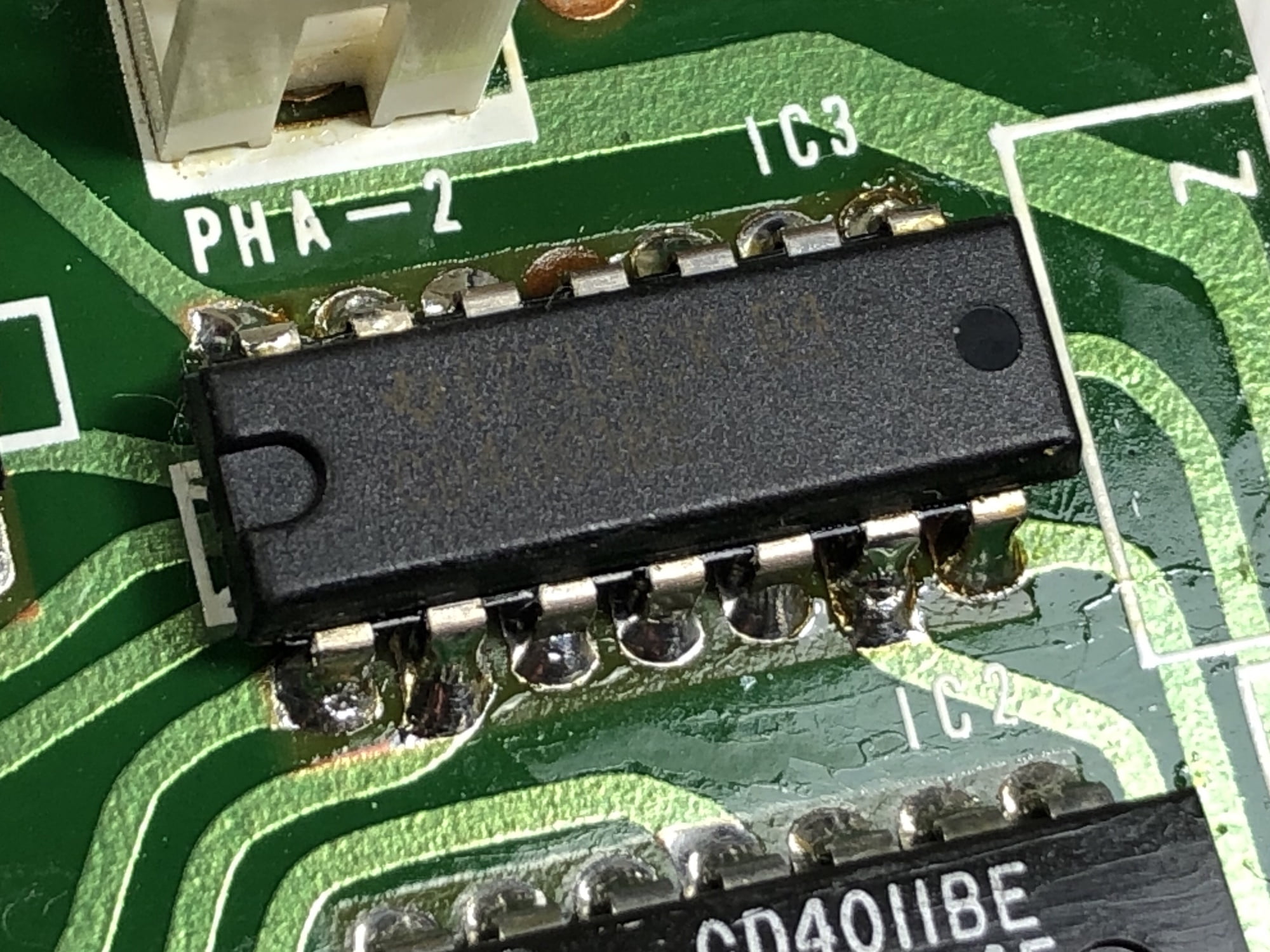
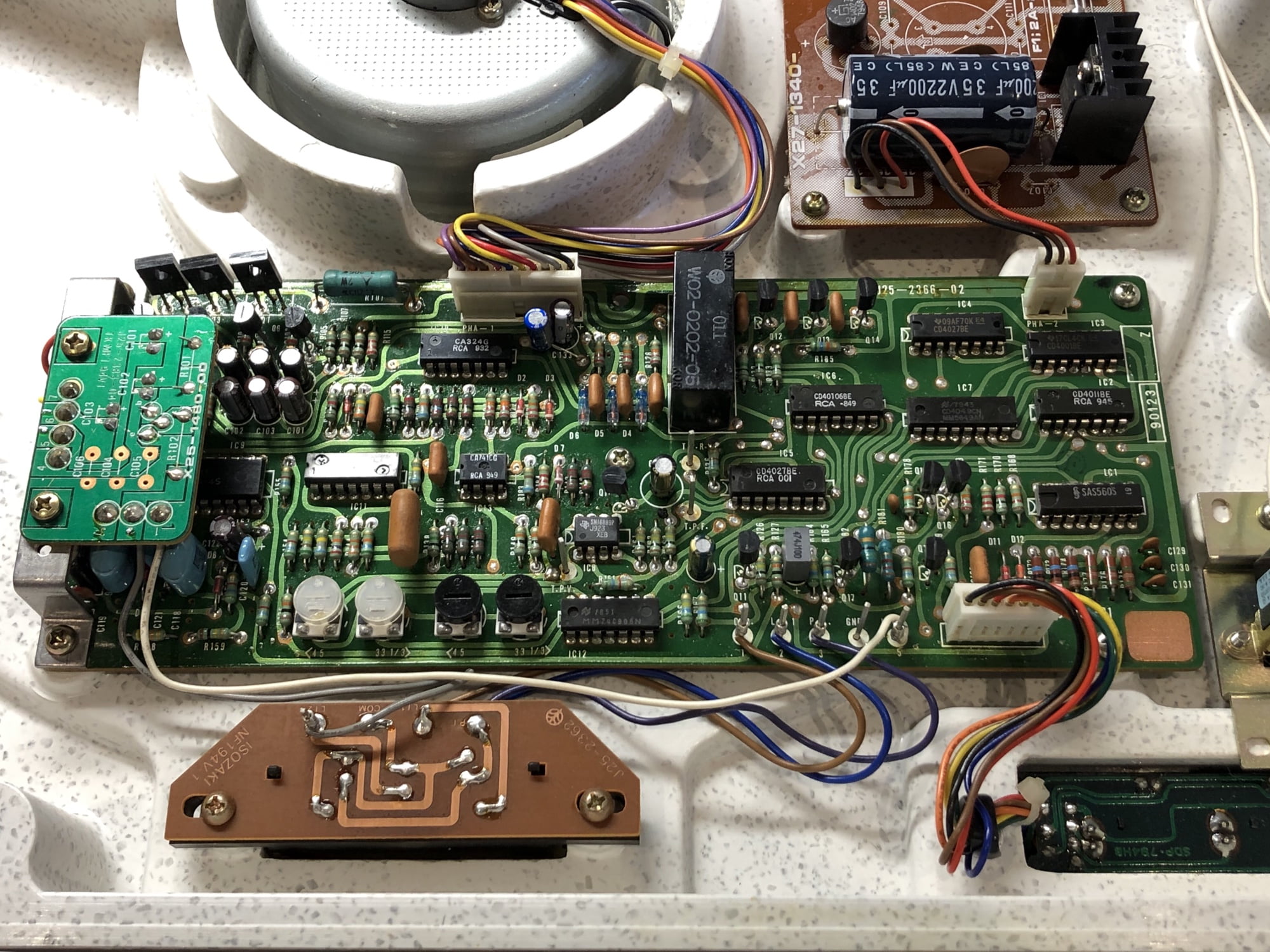
Motor Service & Adjustments
The next step in the overhaul of a Kenwood KD-650 or KD-600 involves a bunch of adjustments. Don’t be tempted to ‘twiddle’ trimmers if you don’t know what you are doing or you’ll end up with a deck that doesn’t work. A dual-channel oscilloscope, probes and an accurate multimeter are needed for these next steps.
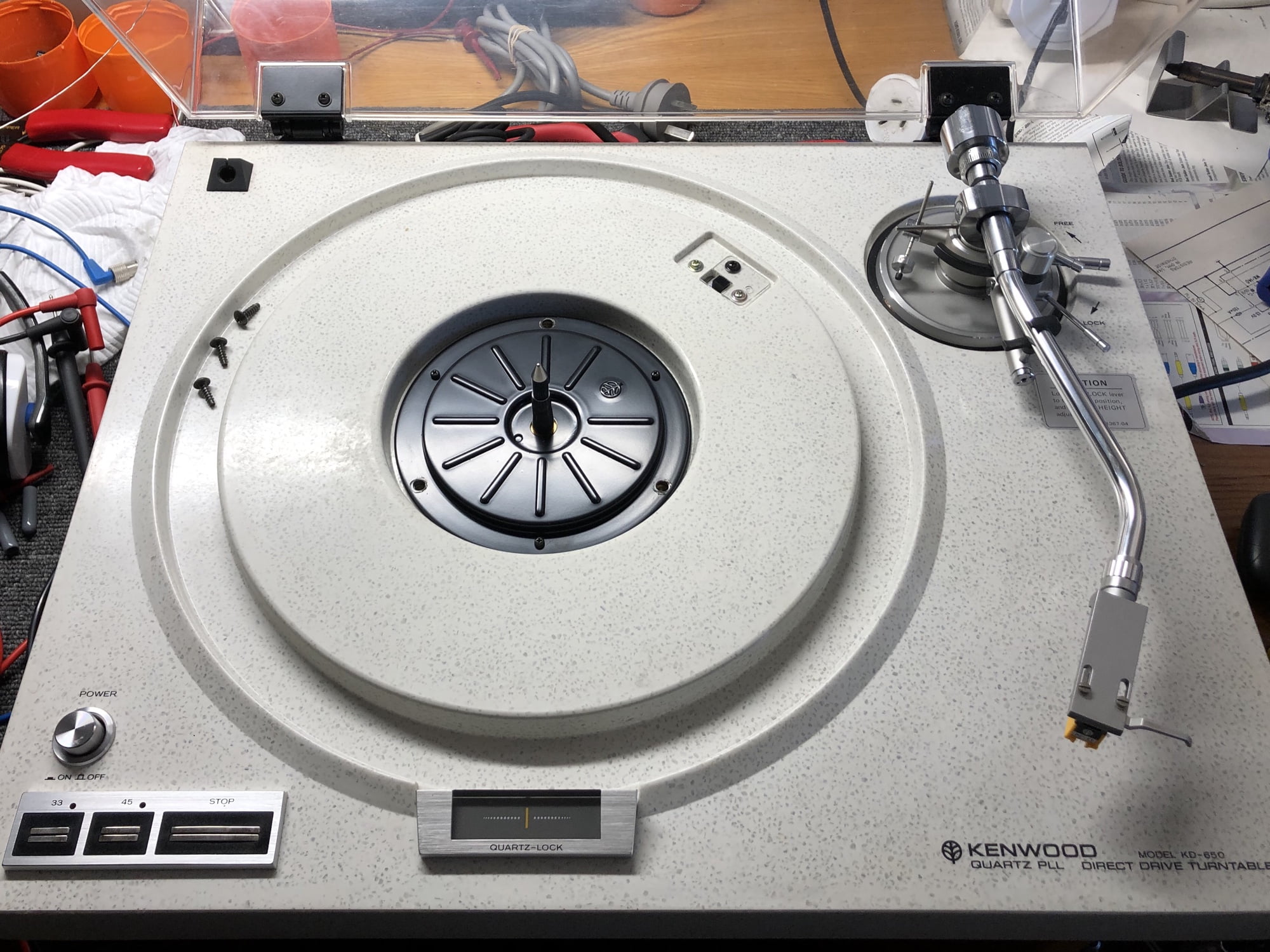
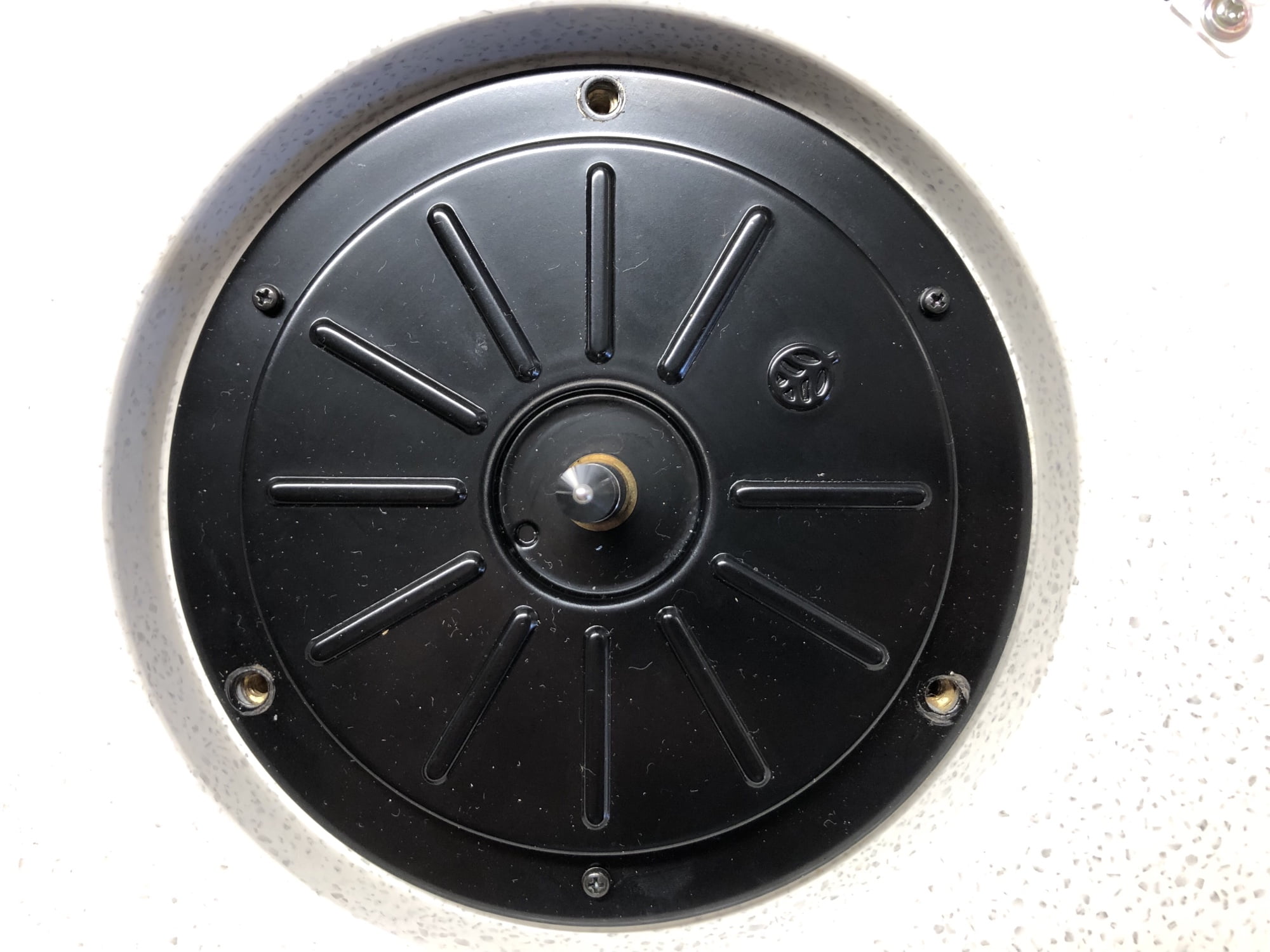
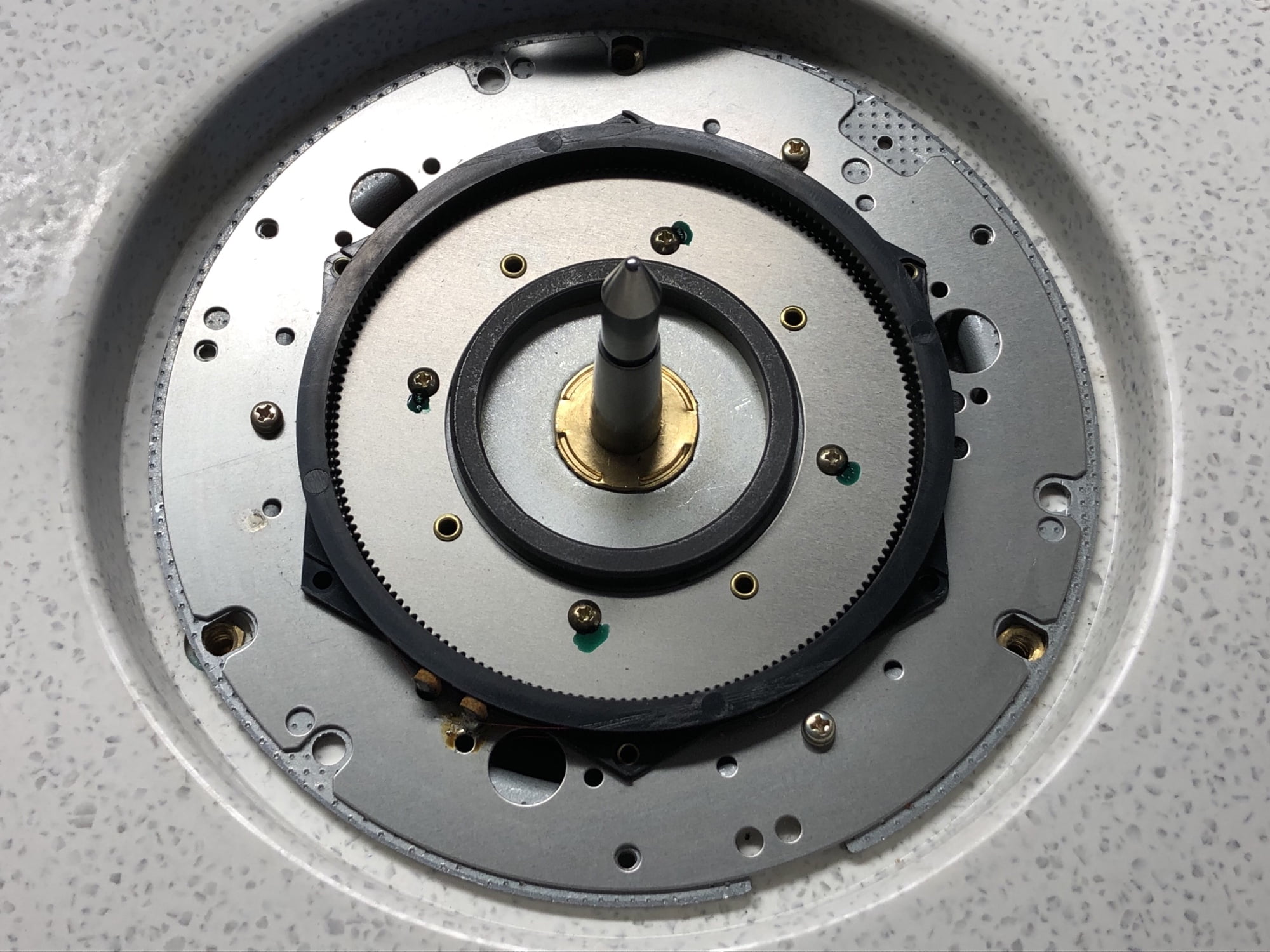
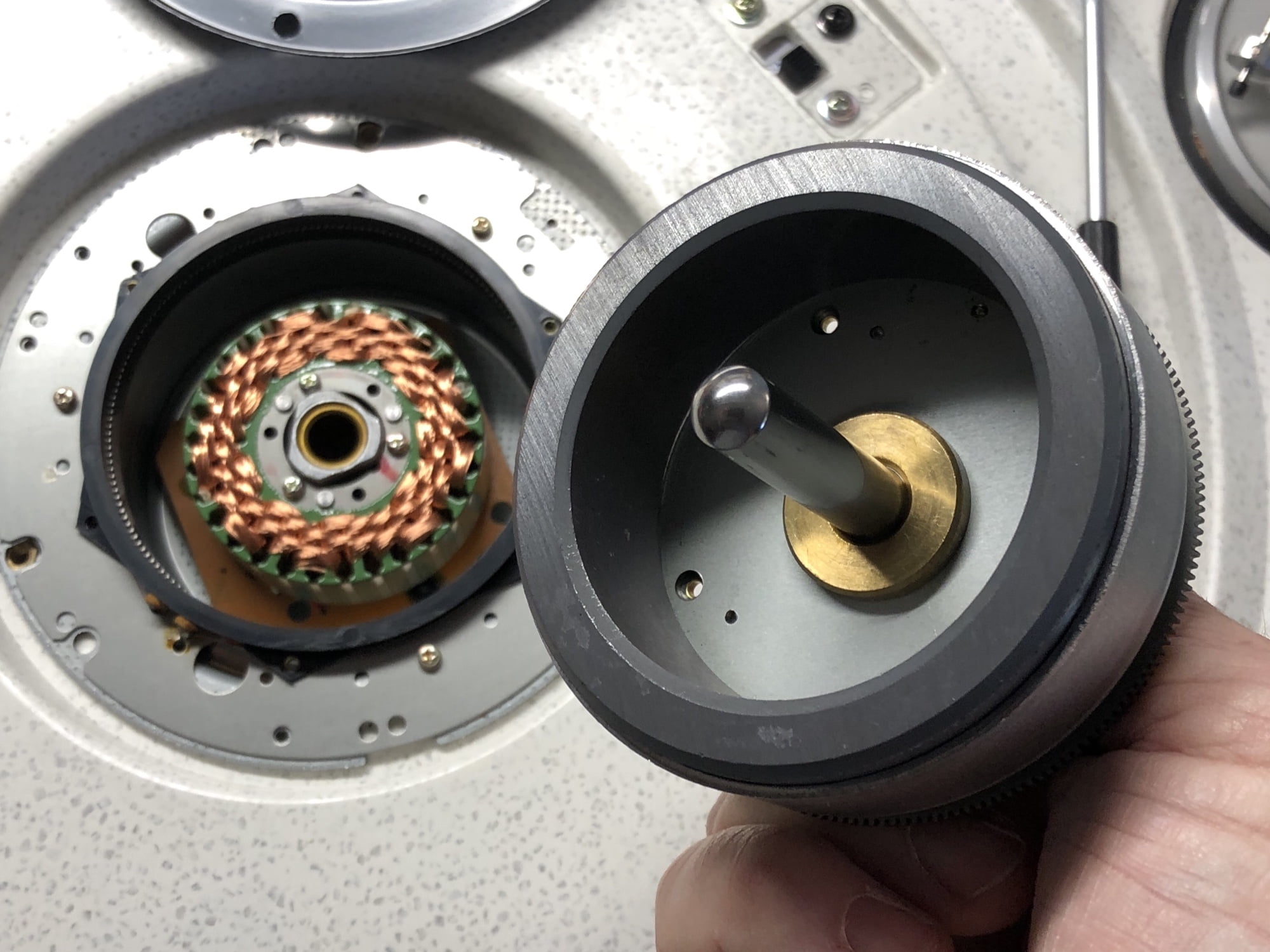
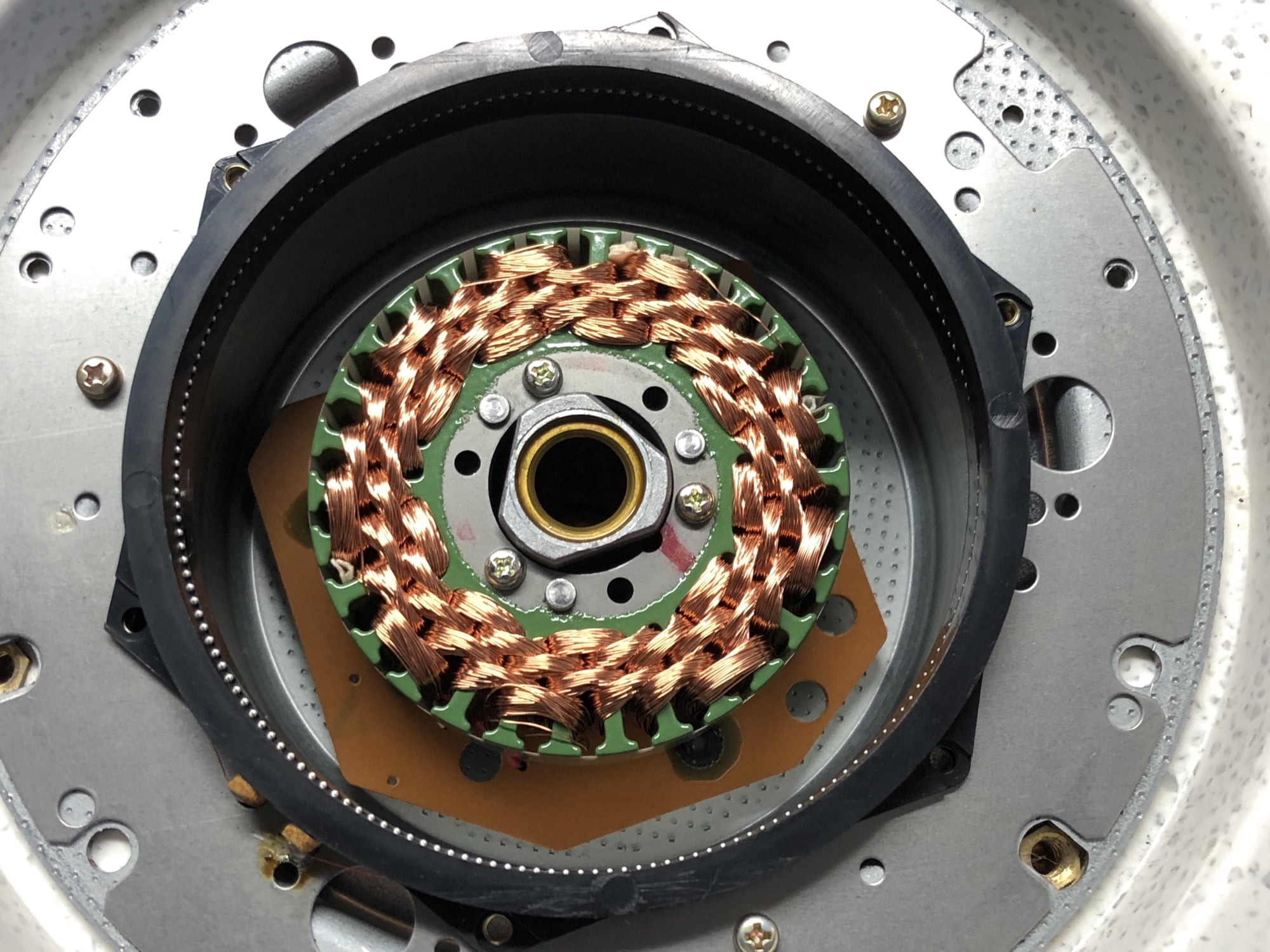
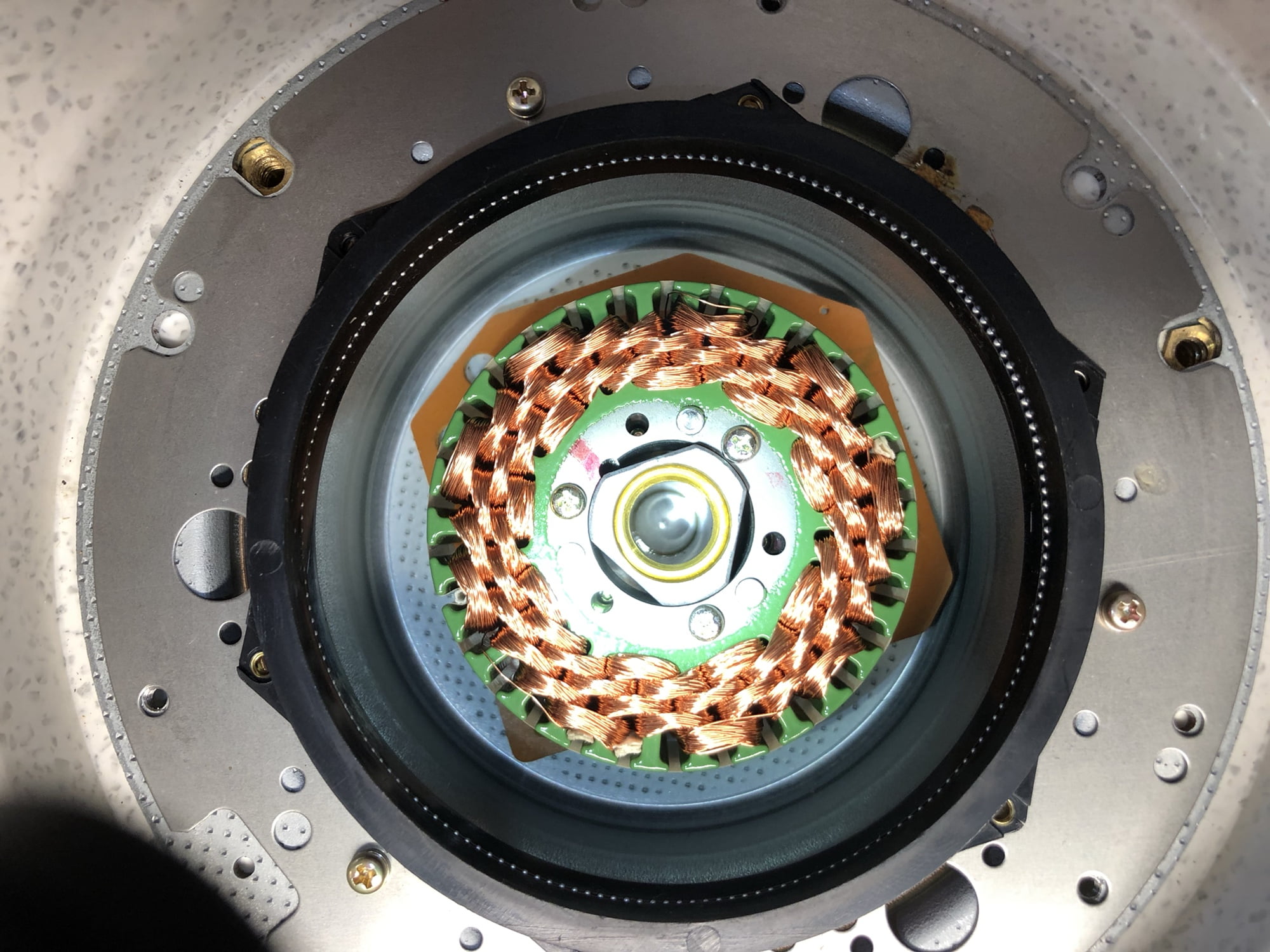
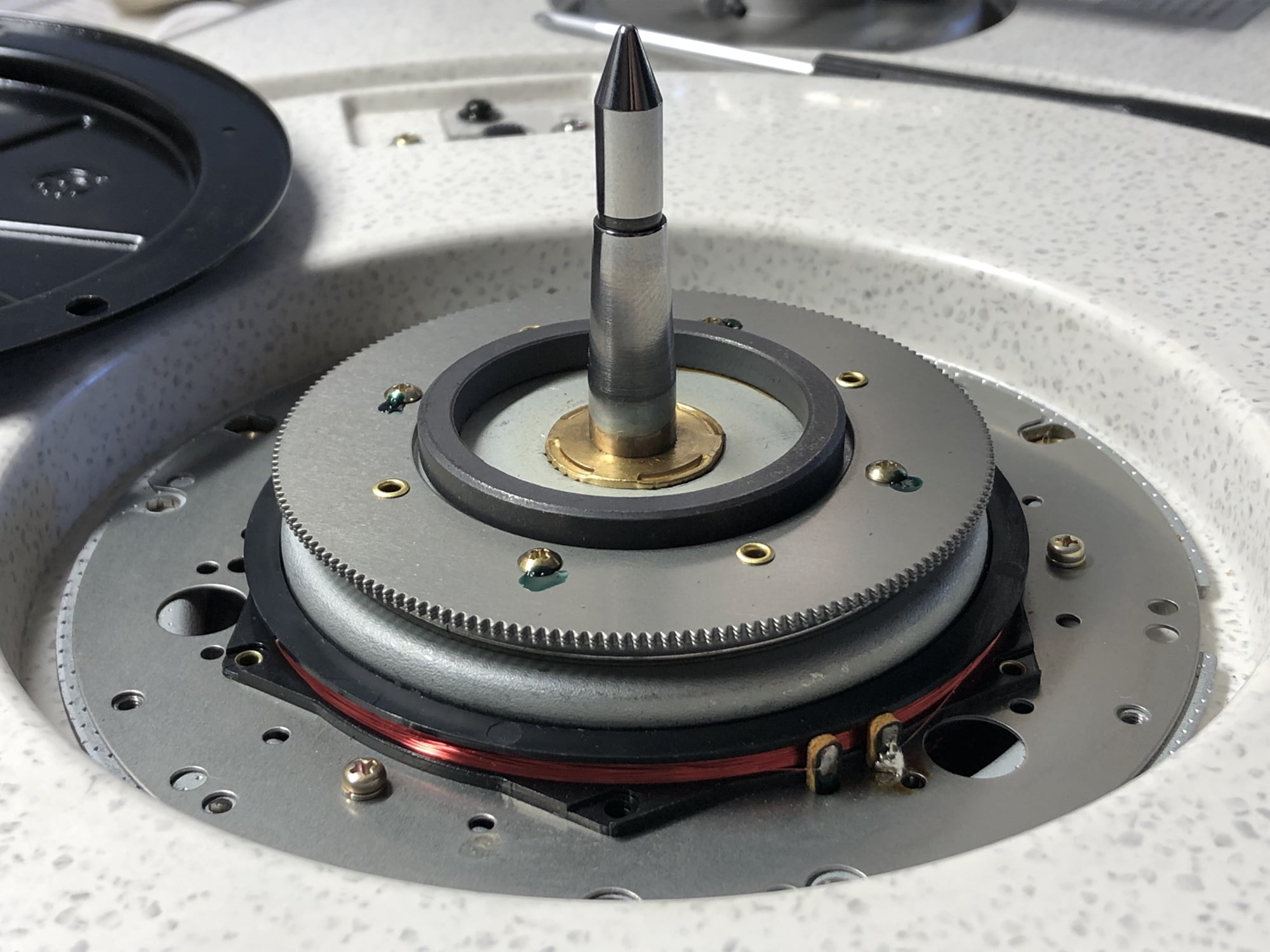
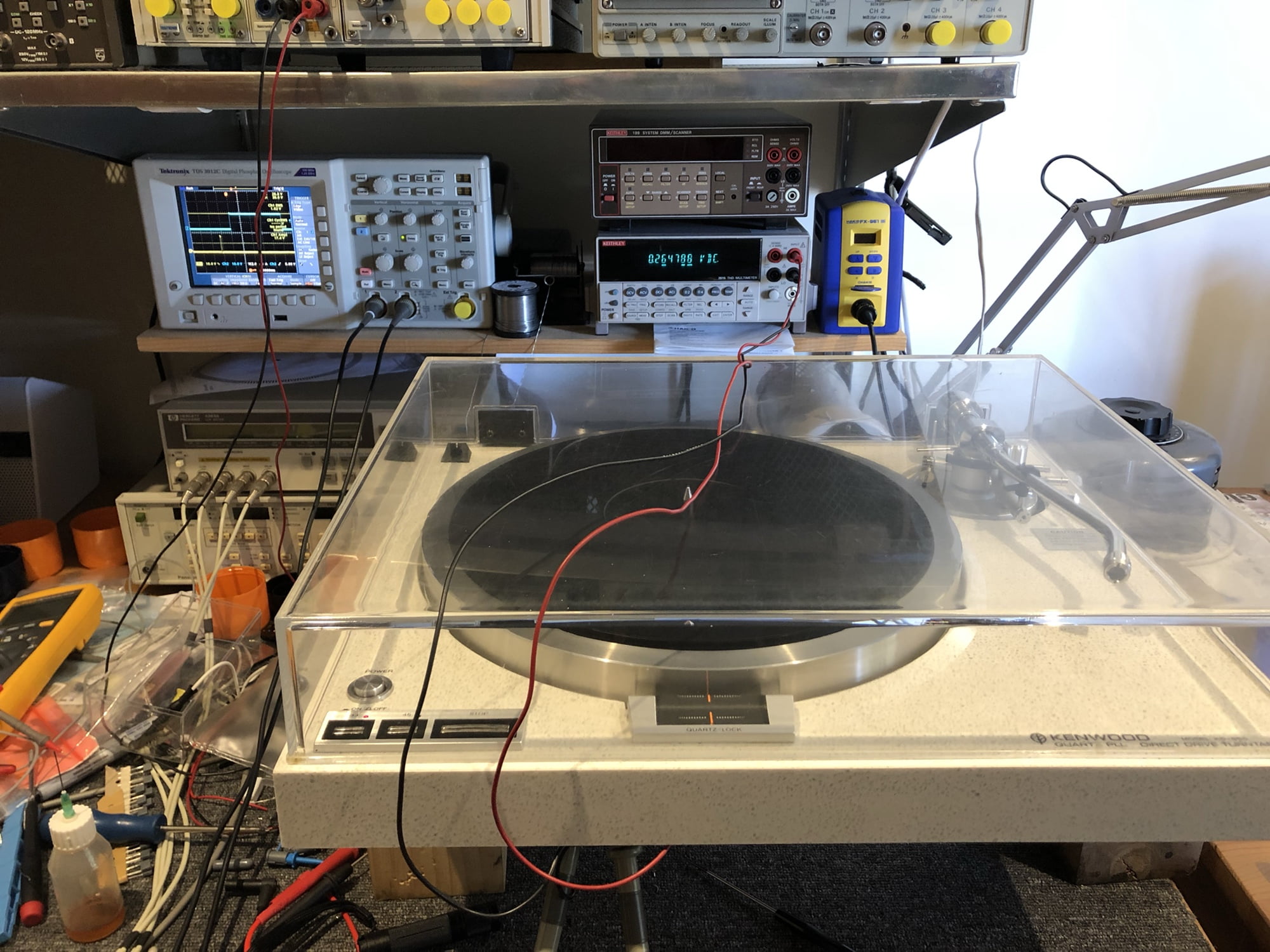
Cartridge Installation & Set-up
The second last step involves the installation of a new cartridge, and carefully setting overhang, azimuth, tracking force, anti-skate and ride height.
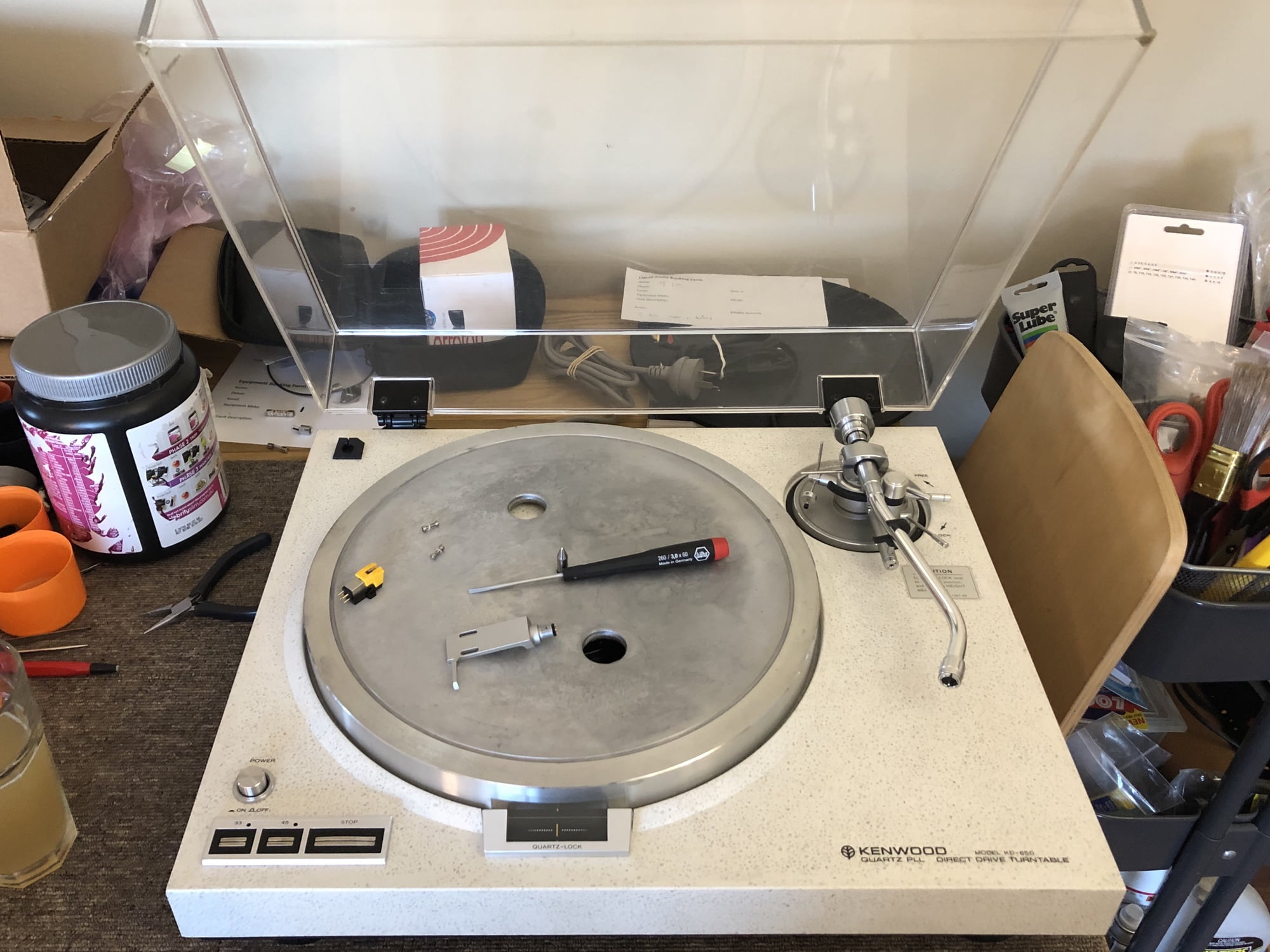
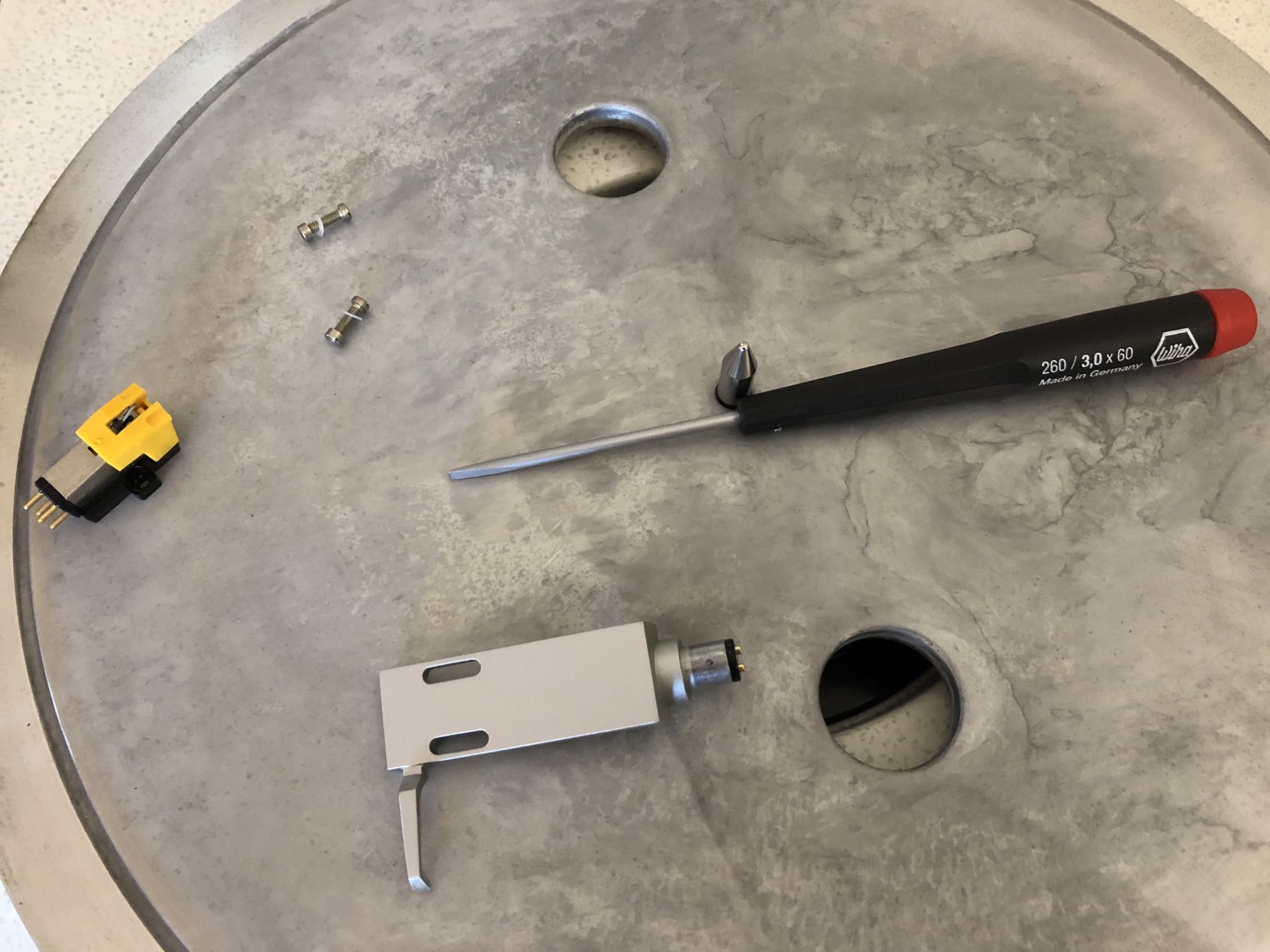
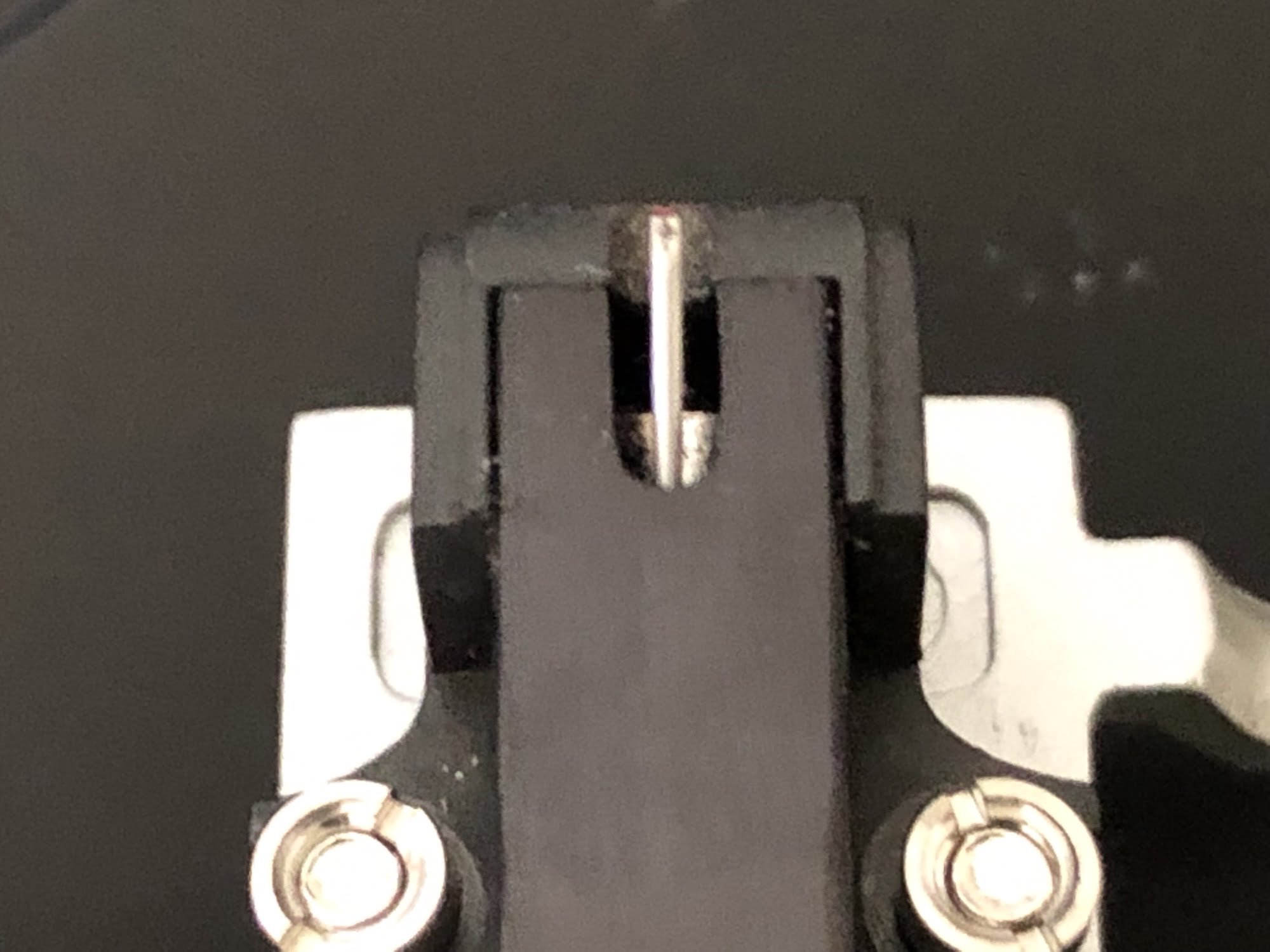
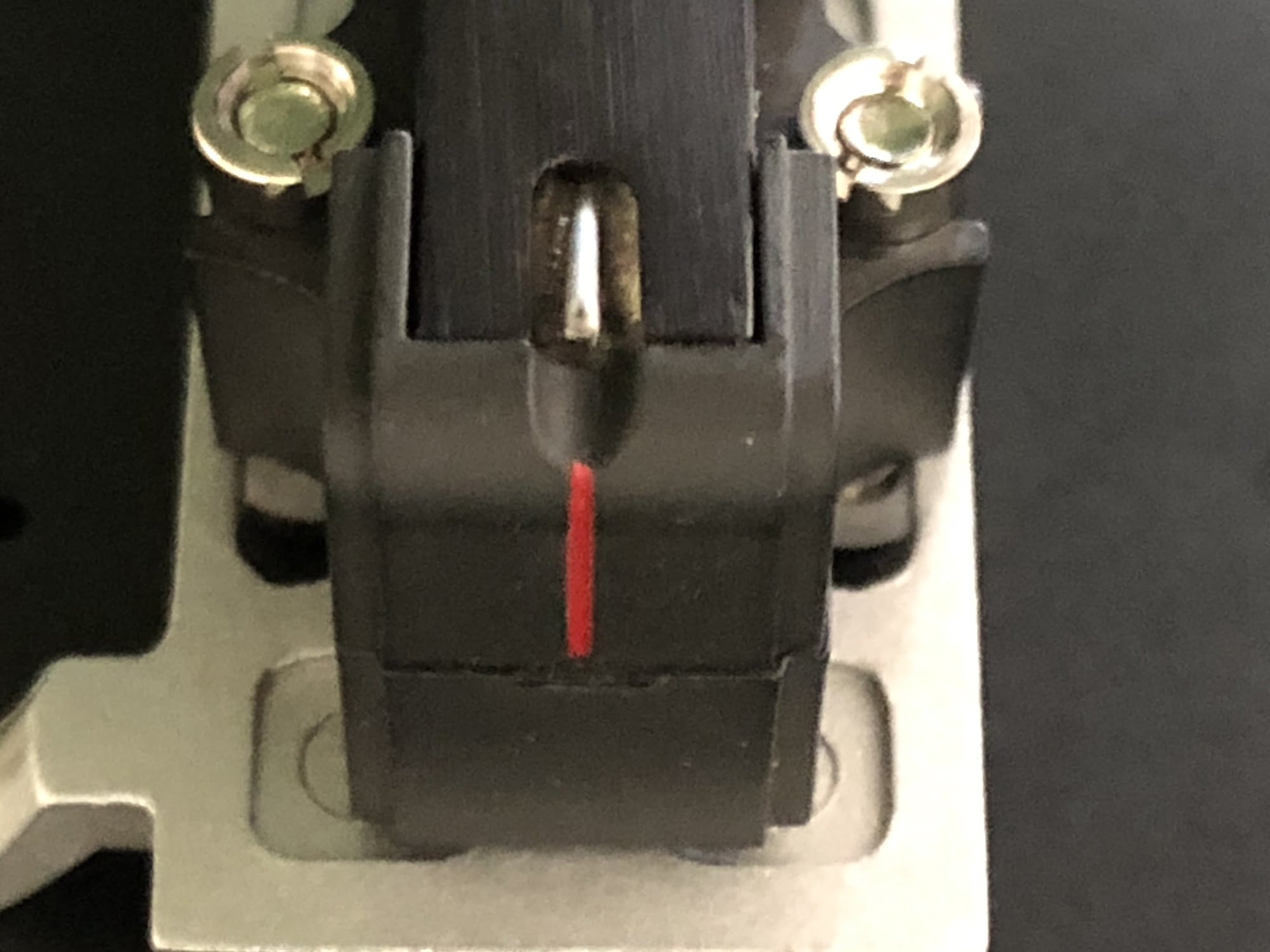
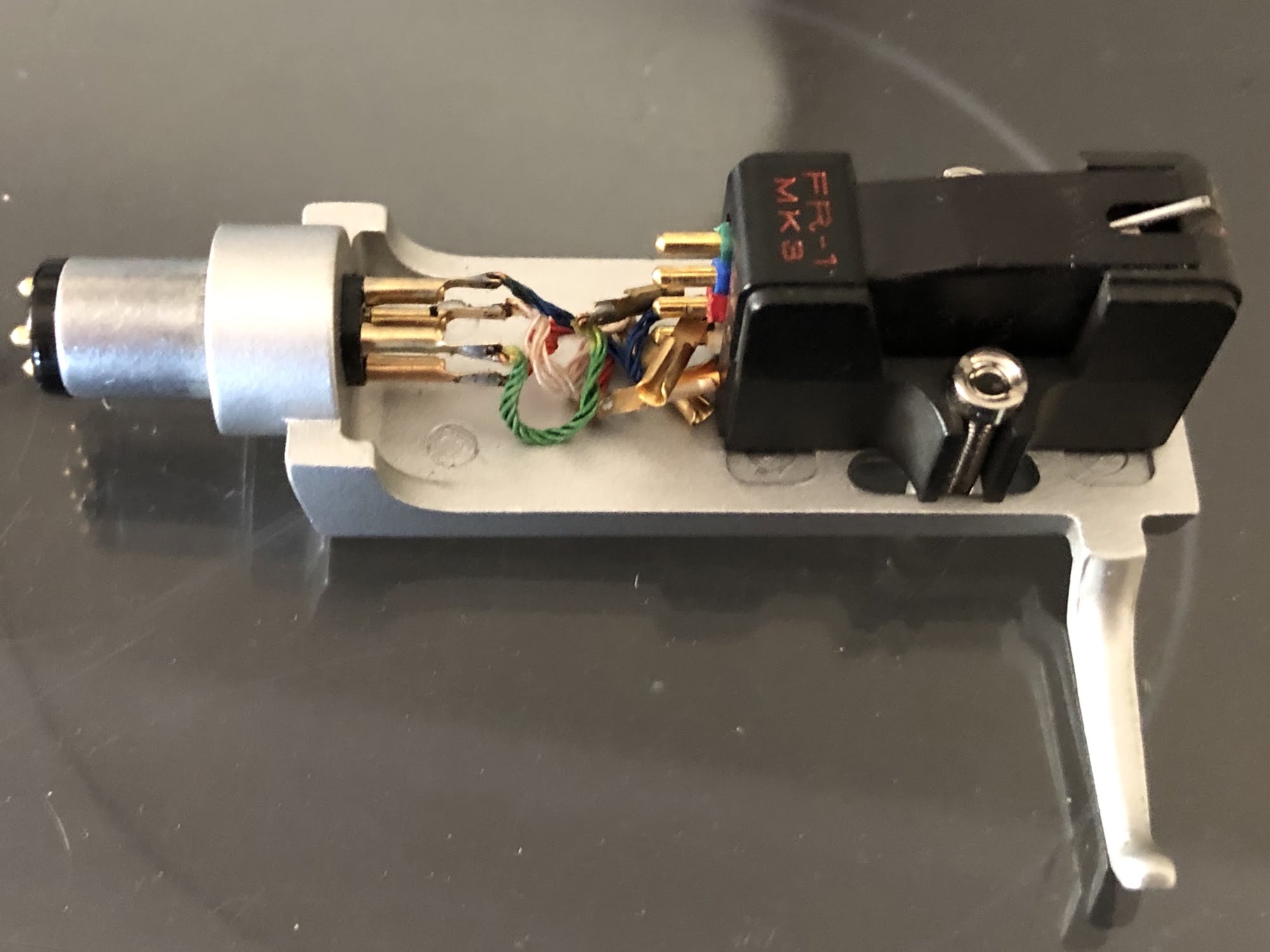
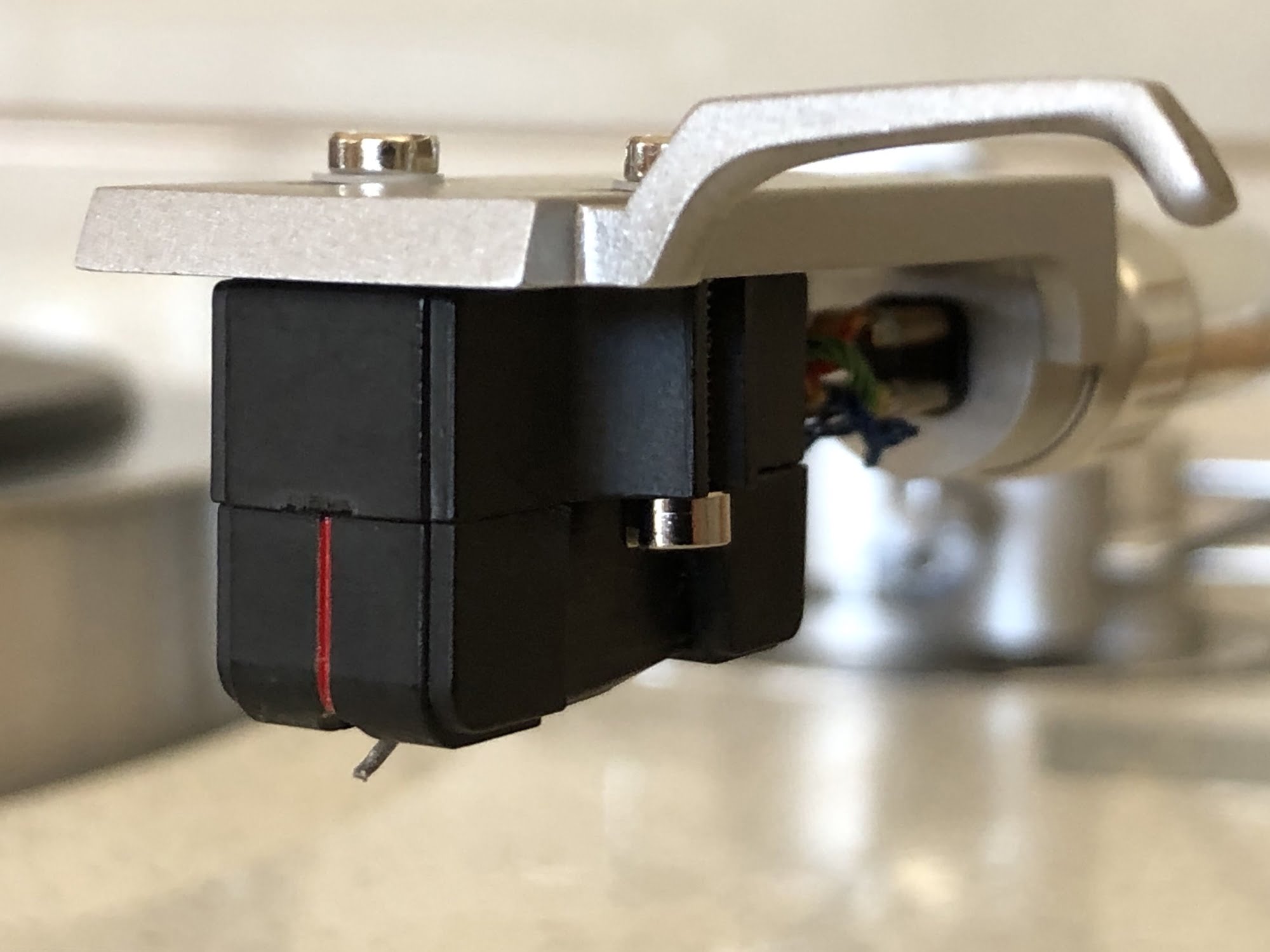
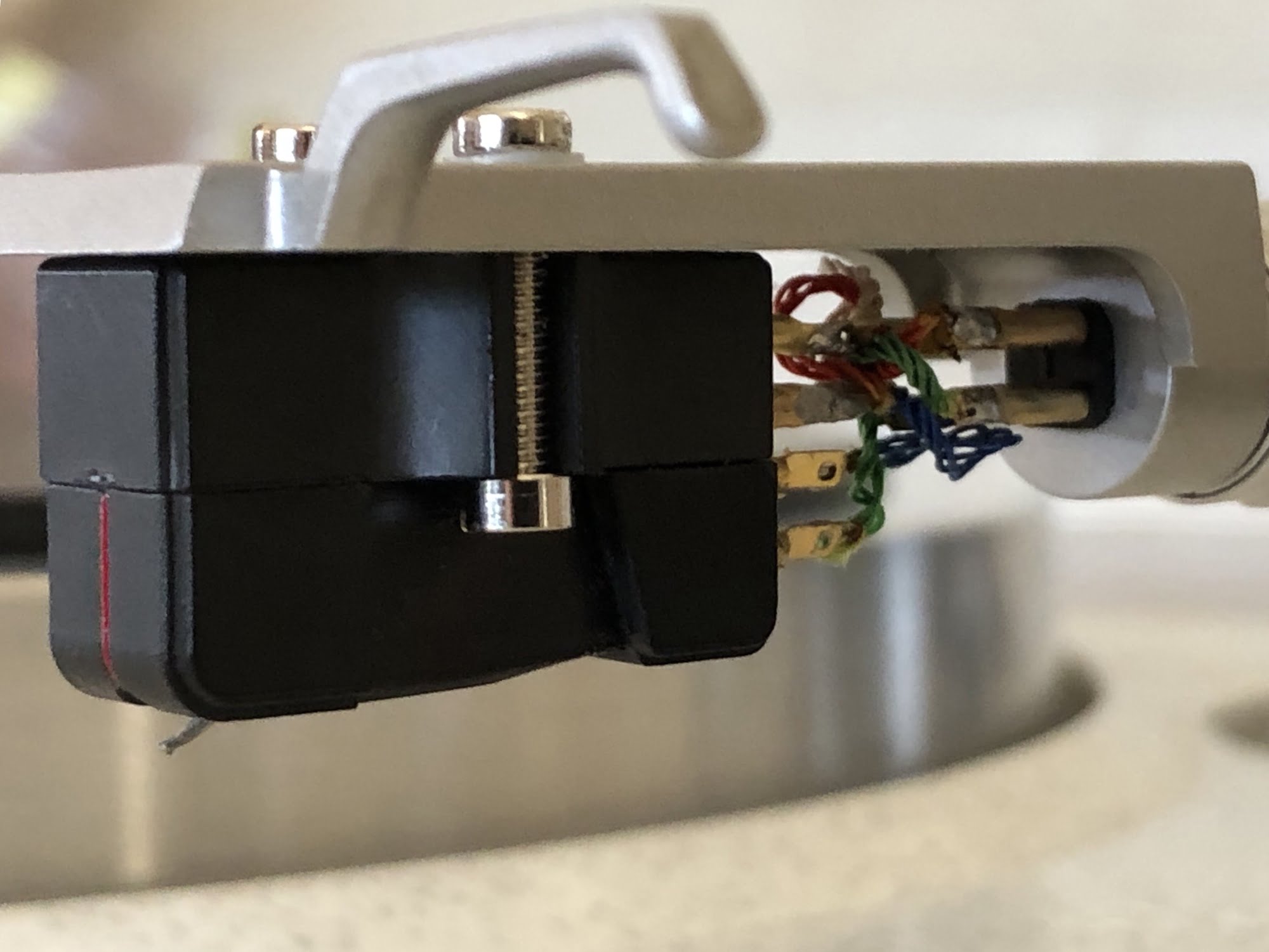
Cleaning & Finishing Touches
I always thoroughly clean equipment that visits the Liquid Audio workshop as a part of the service.
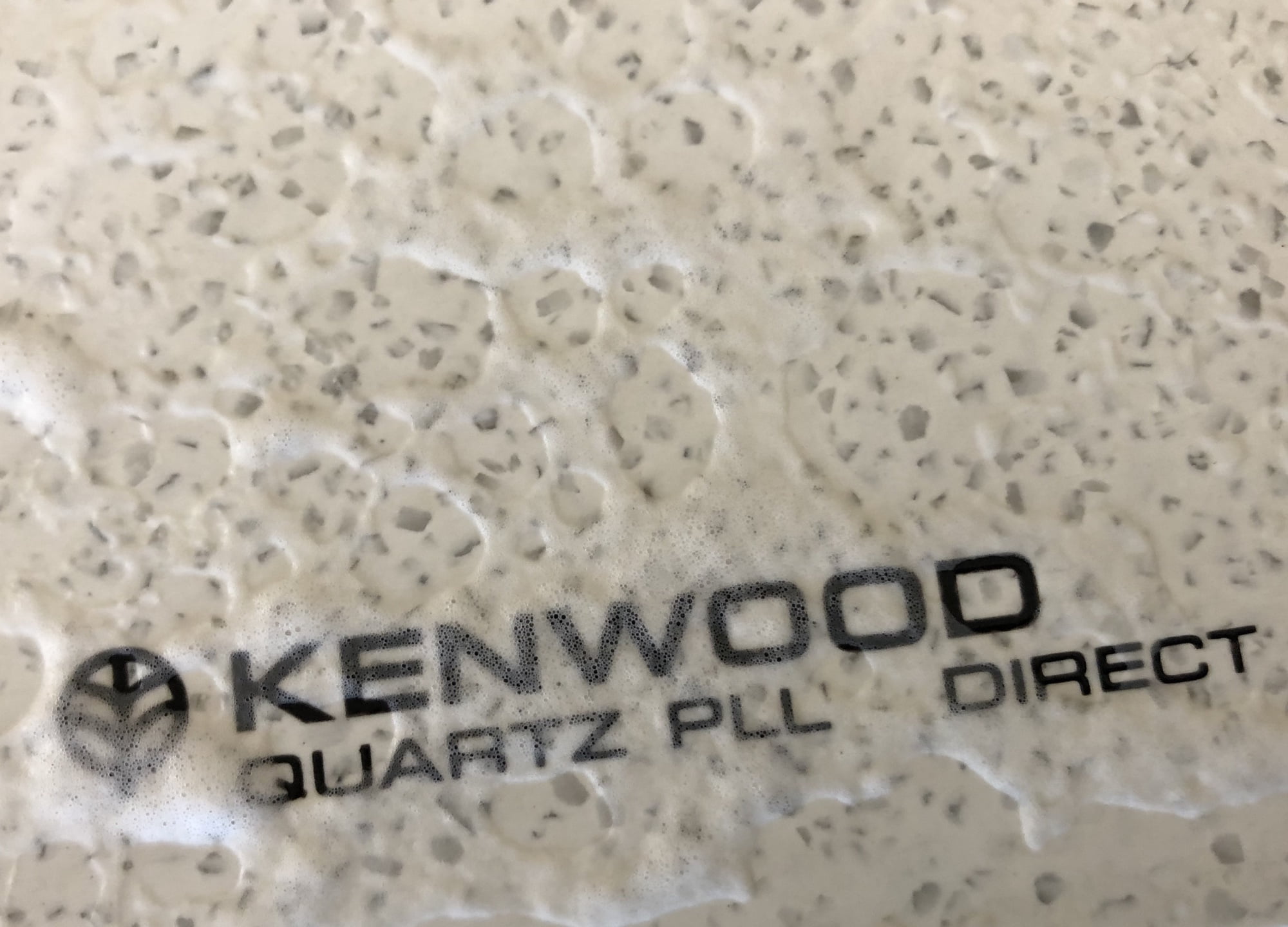
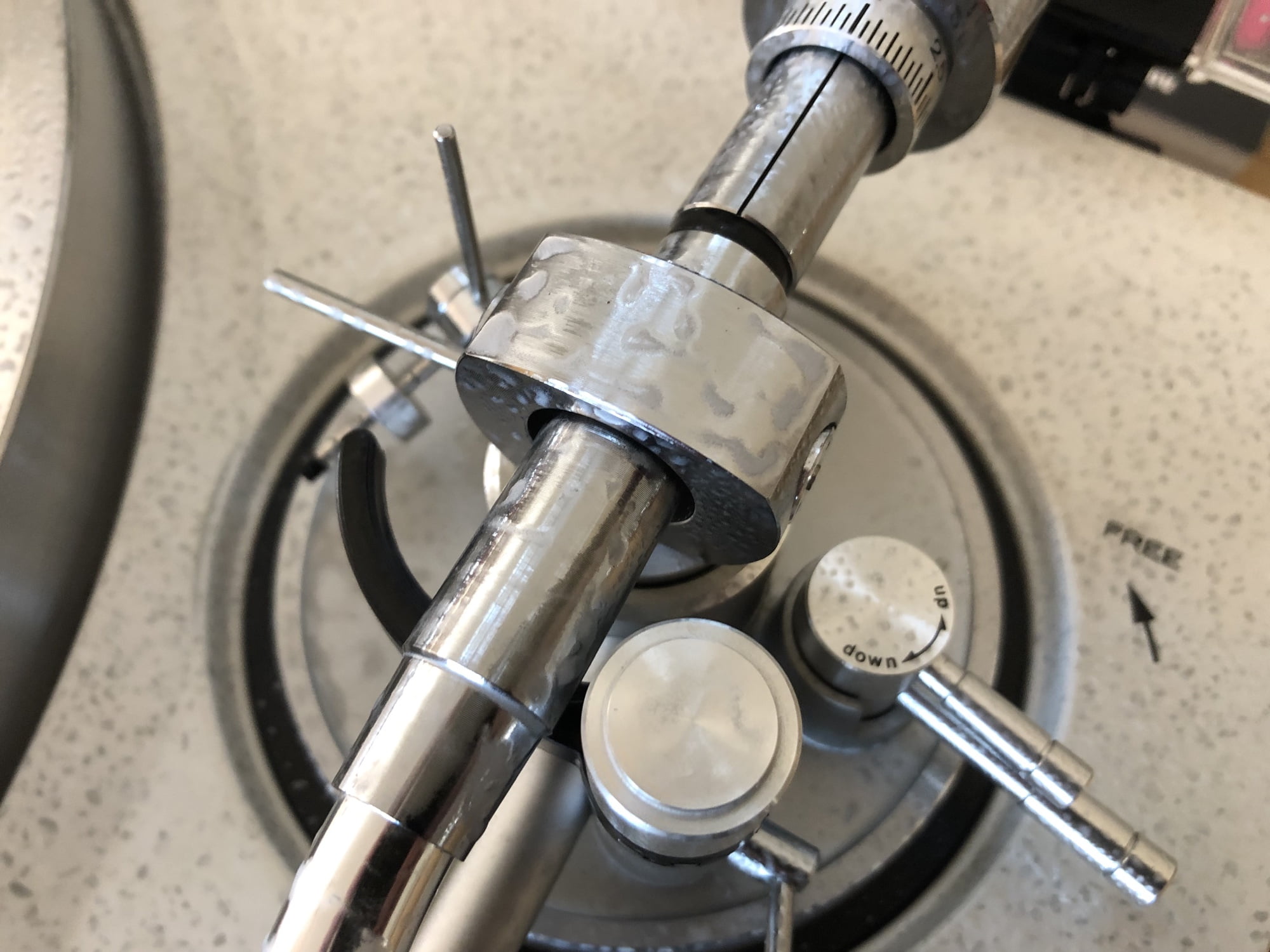
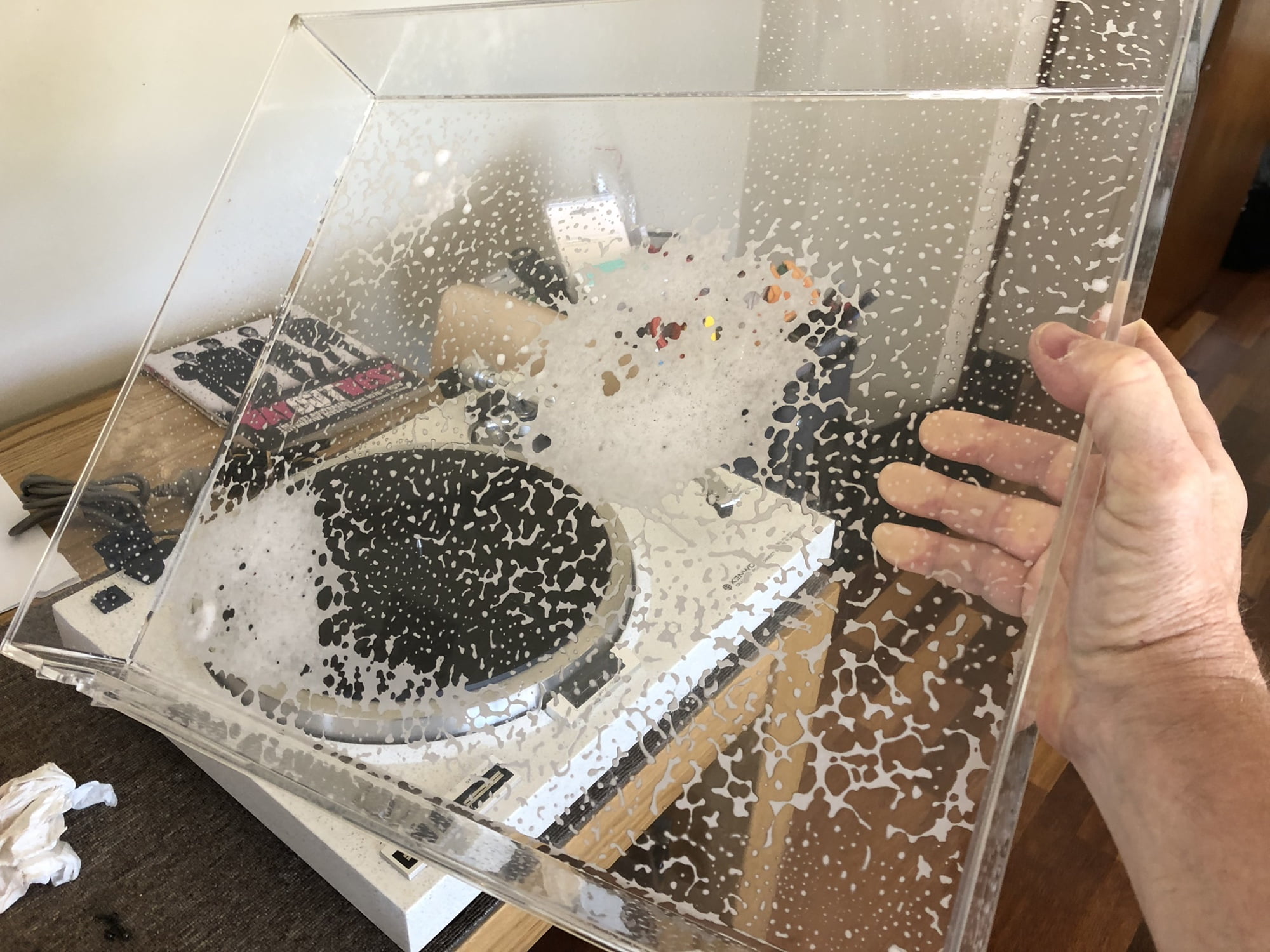
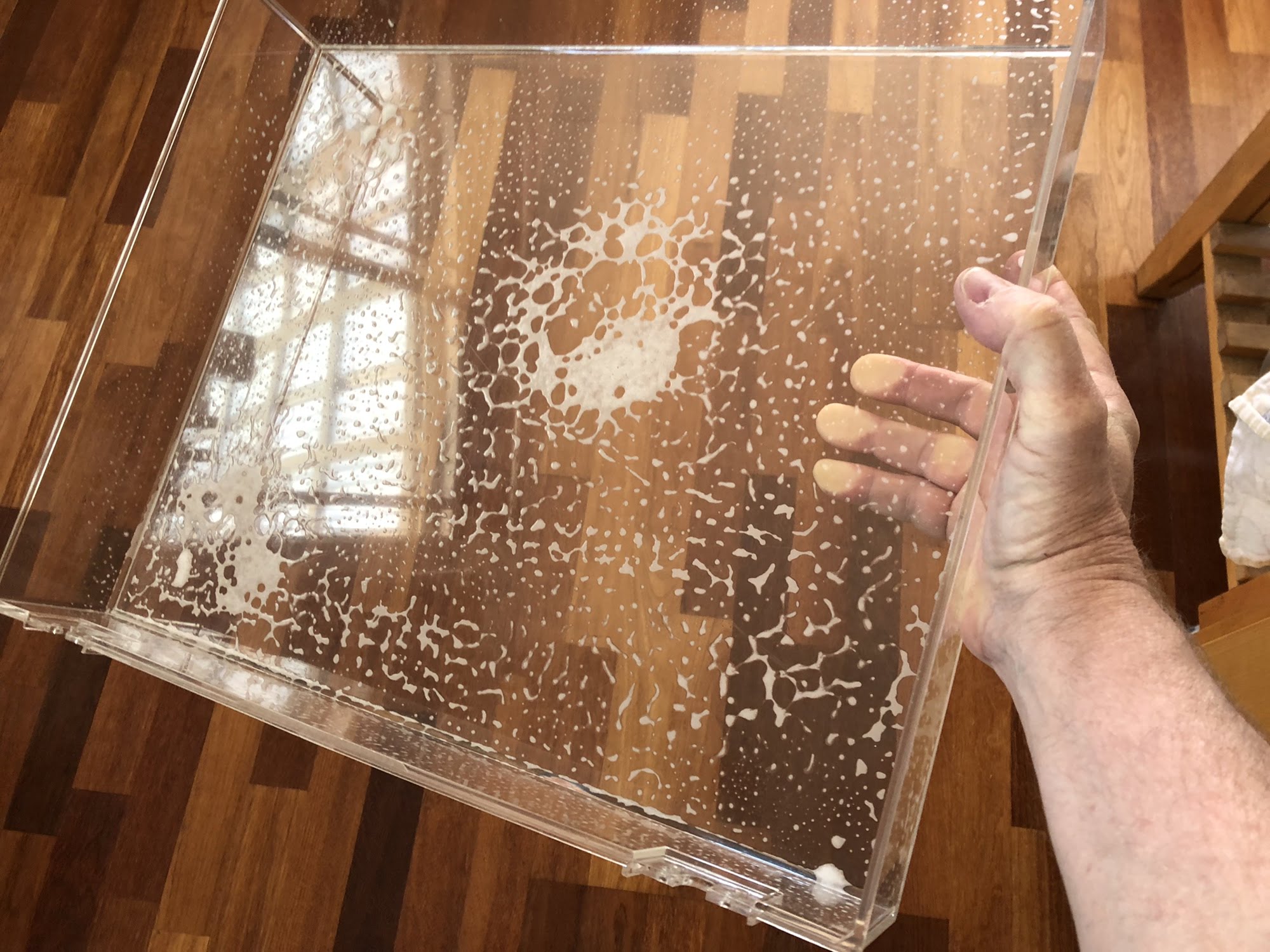
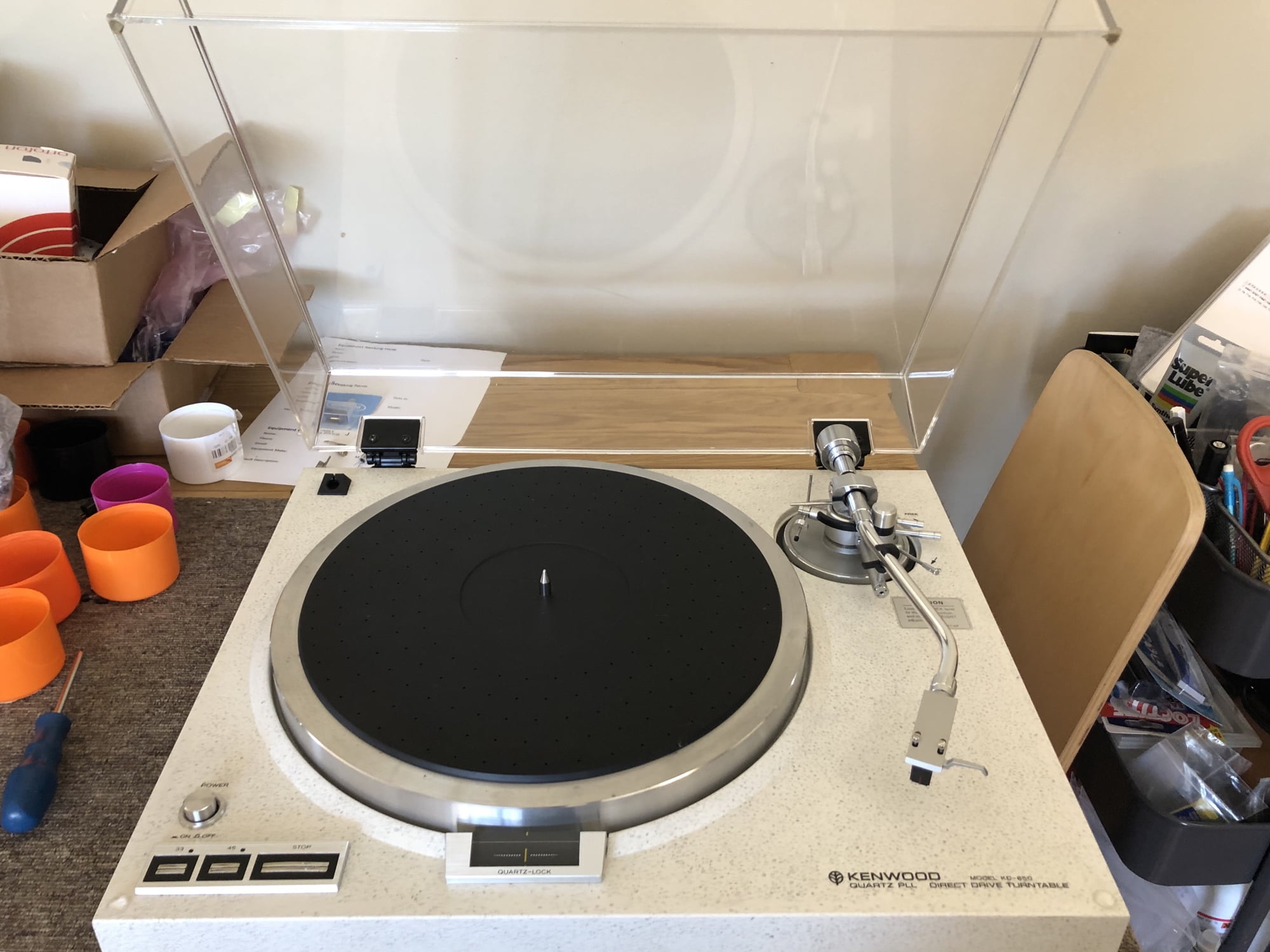
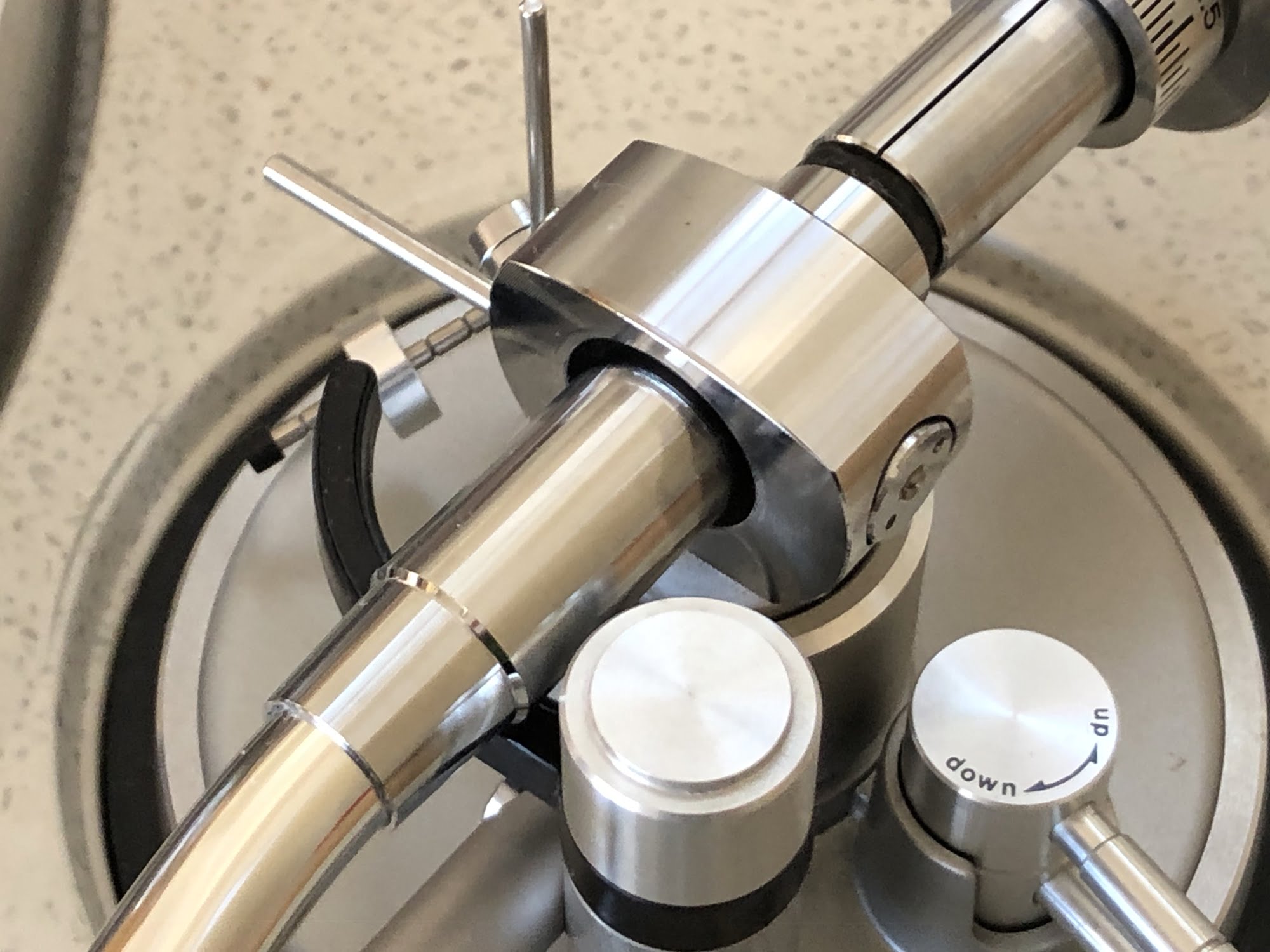
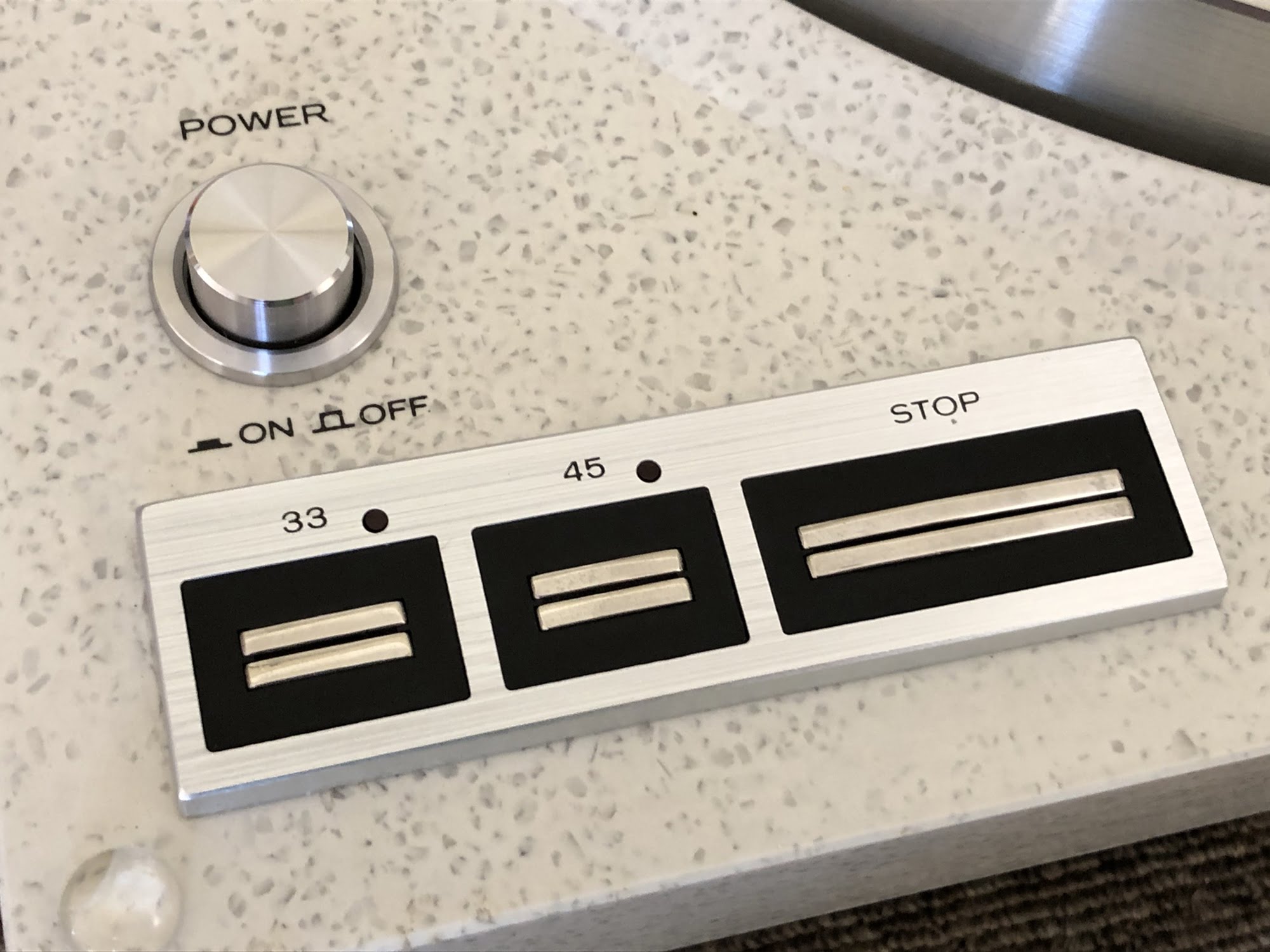
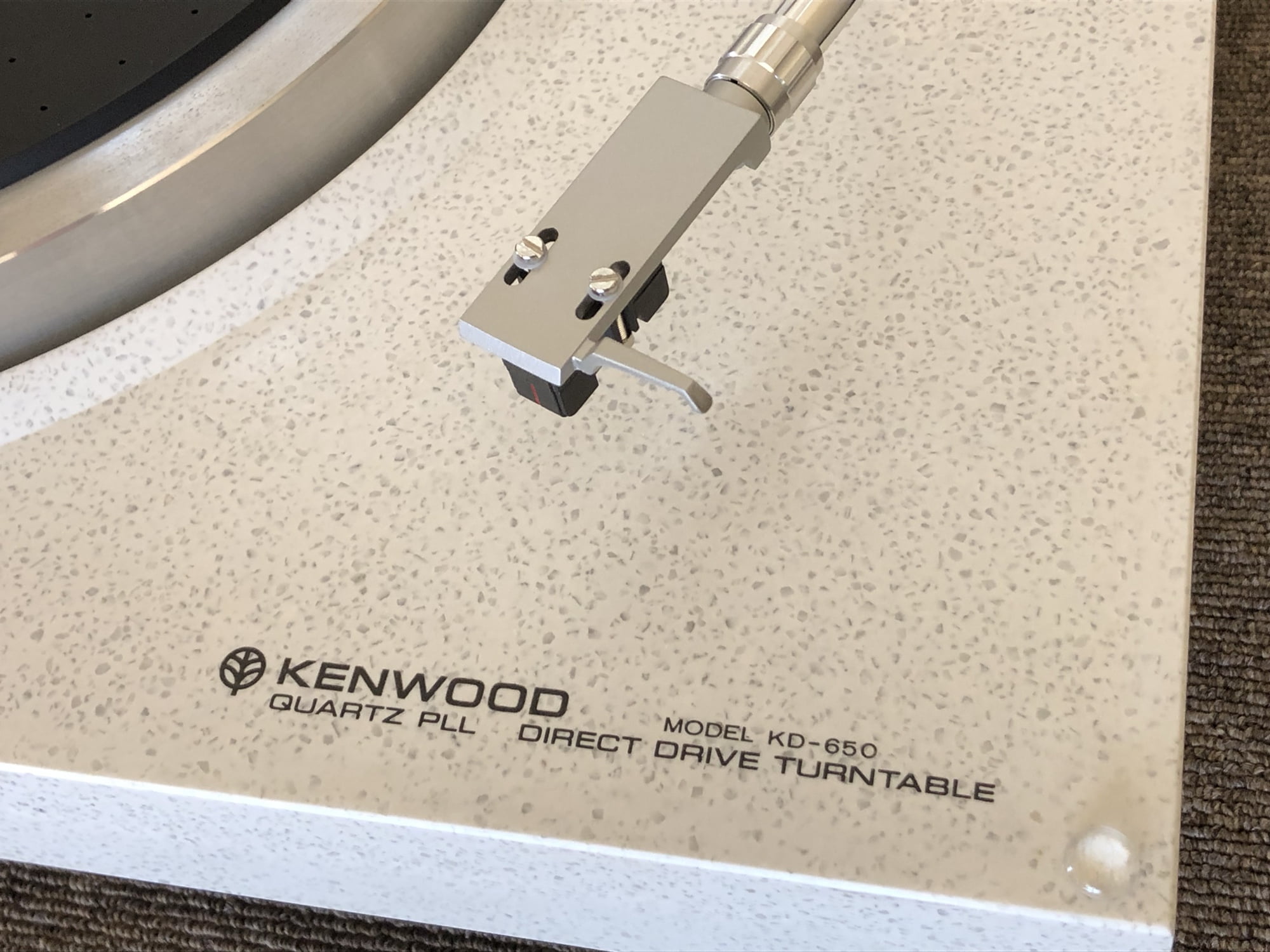
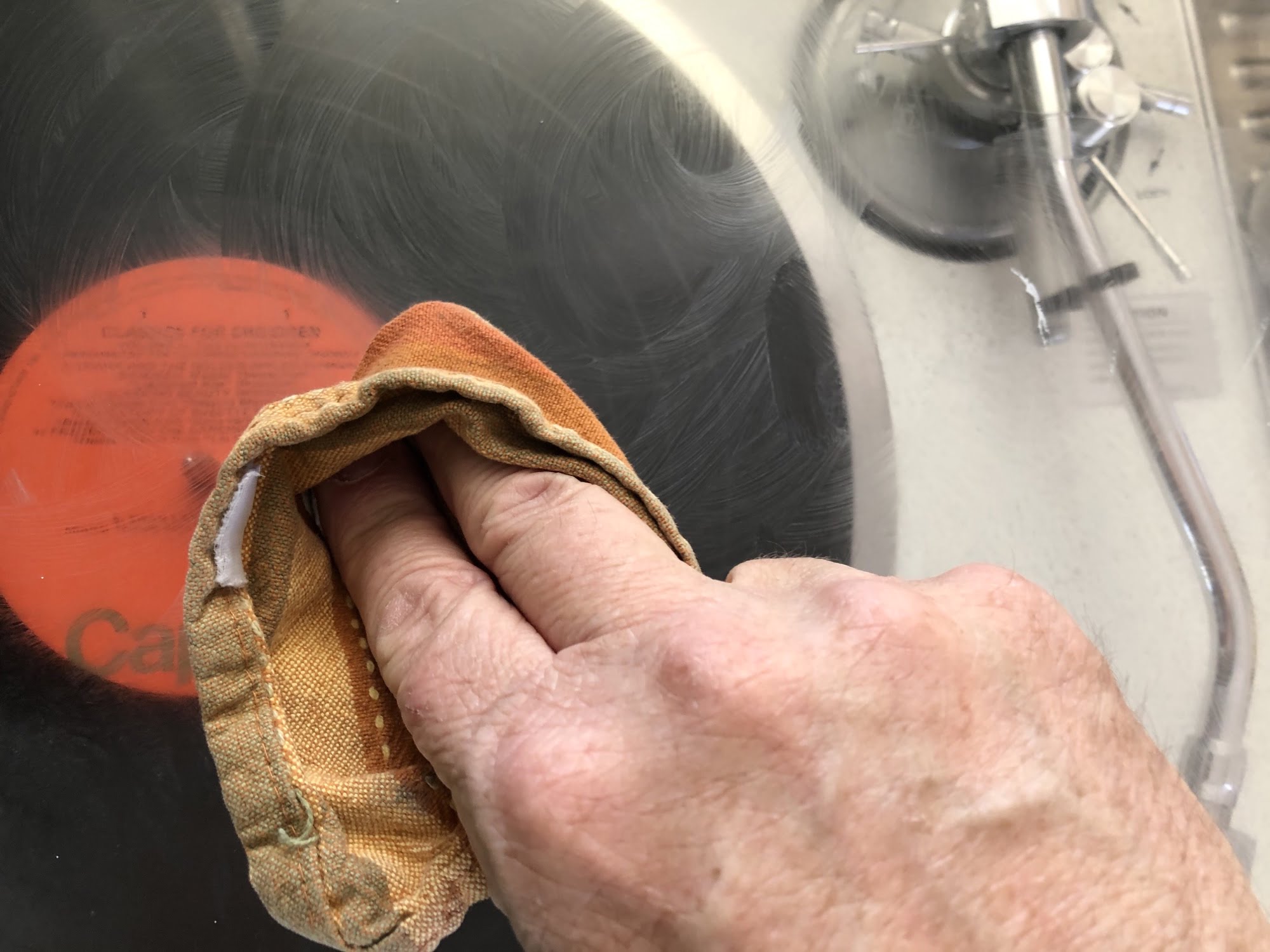
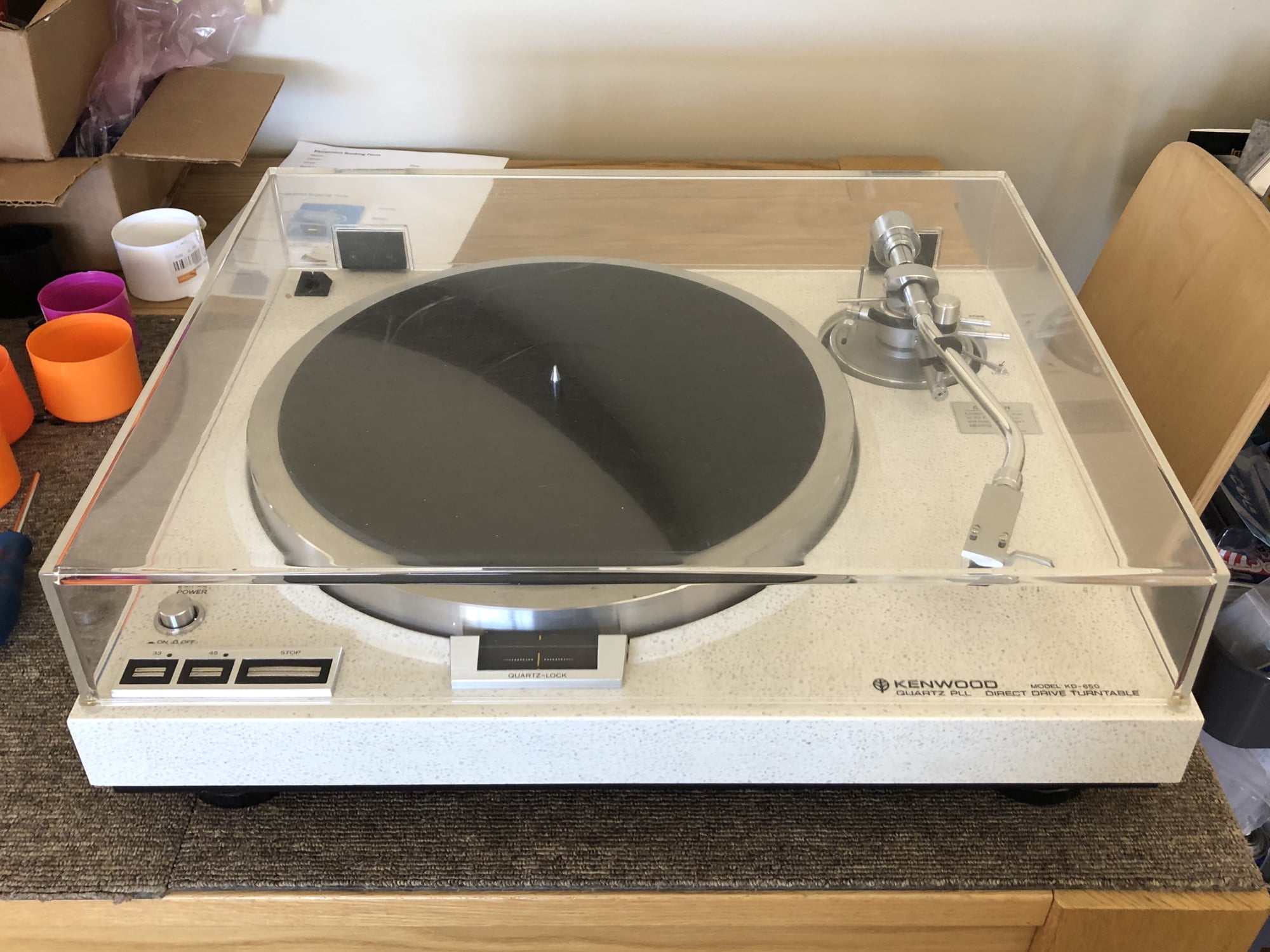
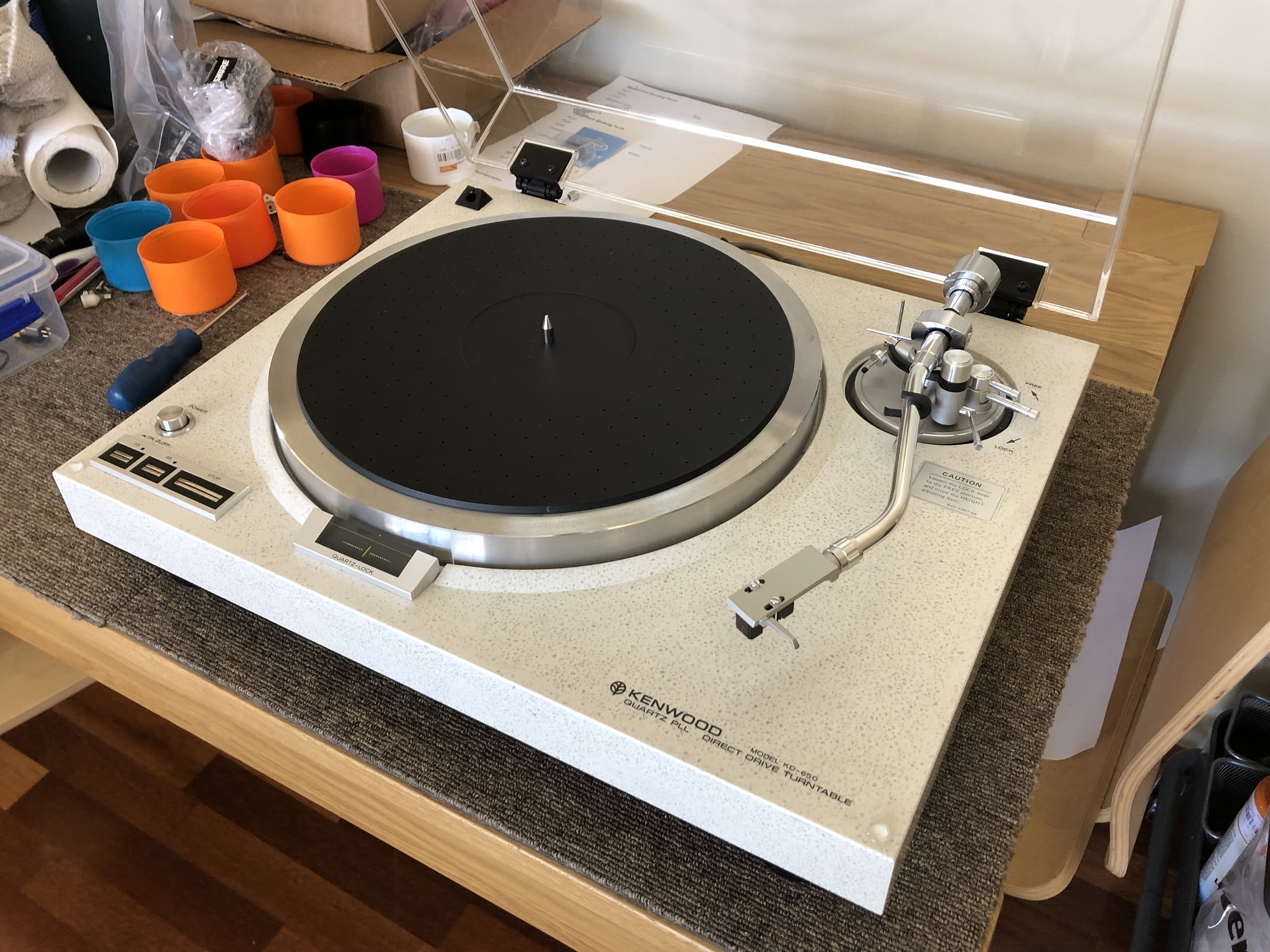
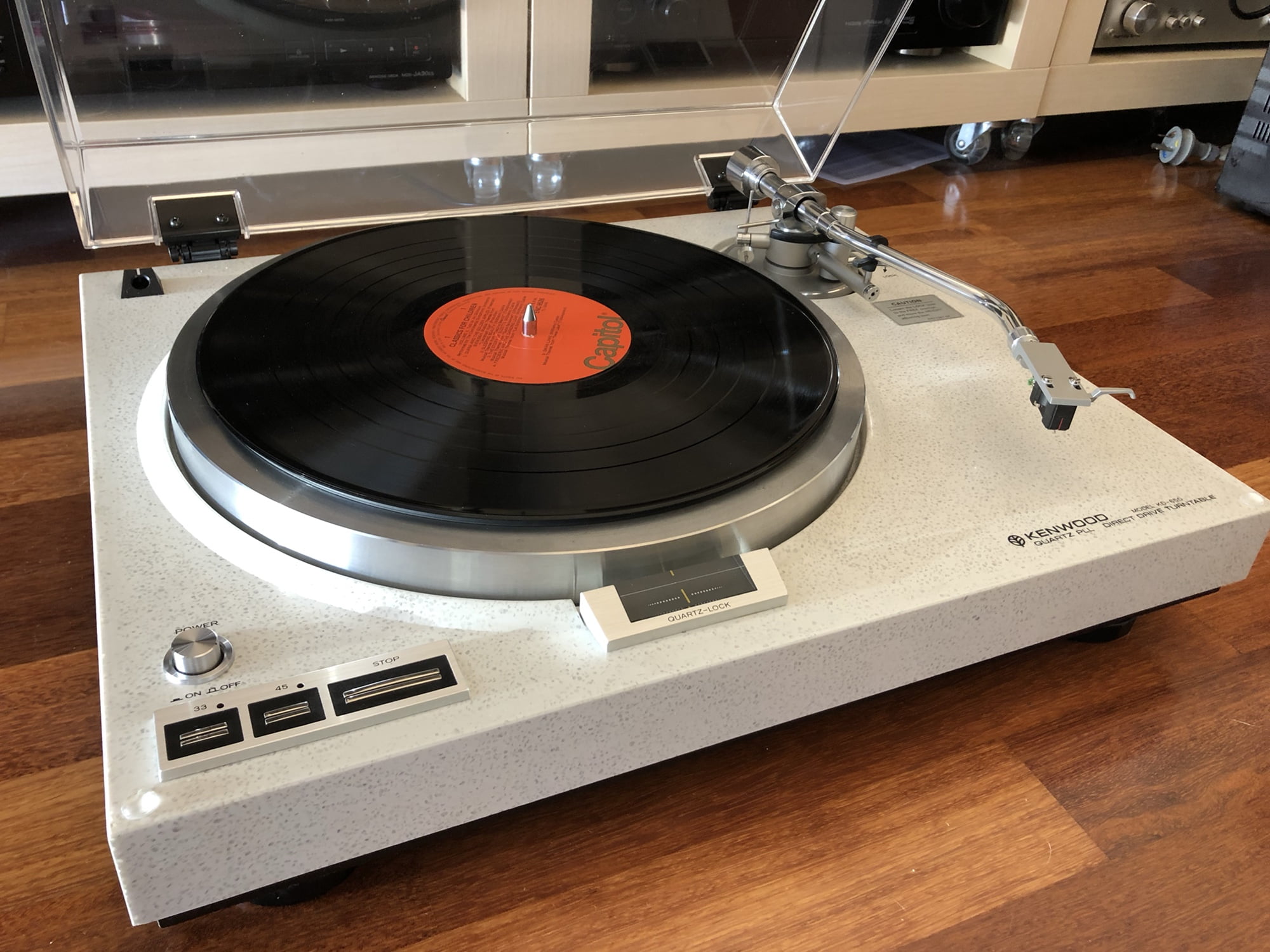
Sound Quality
A high-quality direct-drive deck like this Kenwood KD-650 will always sound good, especially in terms of pitch and timbral accuracy. Add in the superb chassis, platter, motor and tonearm you get with the KD-650 and you have a real heavy hitter. Even the lid is one of the thickest and heaviest available.
The over-engineered motor provides vanishingly low wow & flutter and very low rumble. This lowers the noise floor, enhances dynamics and improves realism with acoustic instruments. The longer tonearm lowers tracking distortion when compared with regular 9-inch arms.
Seriously, nothing new for sensible money can touch the performance of a well-set-up KD-600 or KD-650, especially with an FR-1 or similar high-performance cartridge. For example, the KD-650 is definitely a better turntable than Technics’ new SL-1200G, which sells for $6500 AUD…
Bottom Line
This is 15kg of pure, unadulterated Japanese engineering, the sort that makes other manufacturers who can’t build arm height adjustment into their decks say “arm height adjustment isn’t important.” Yeah right!
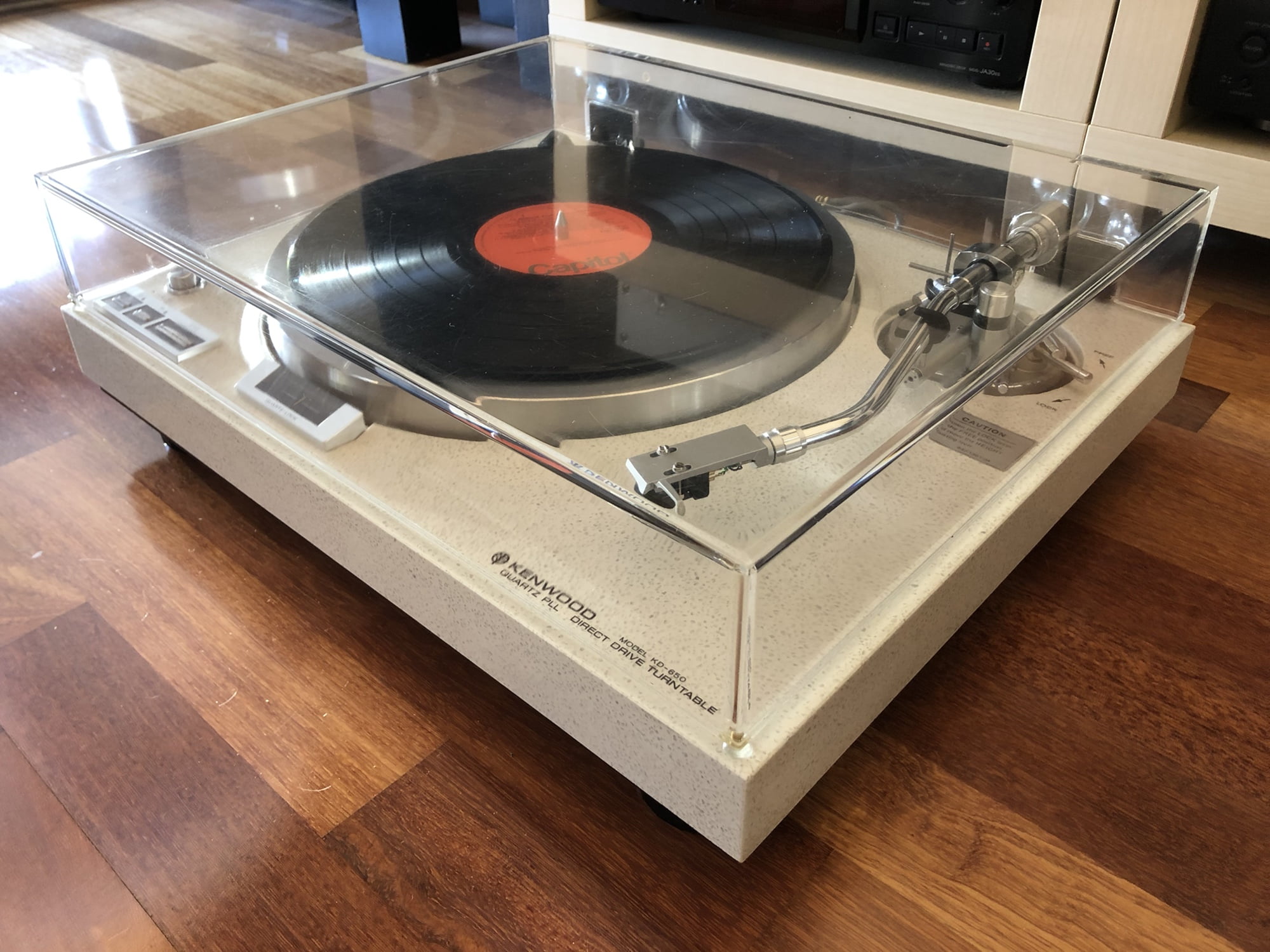
If you’re looking for an amazing vintage deck, or are perhaps stepping up from a belt-drive or lesser direct-drive and don’t have the many thousands of dollars needed to attain this level of performance in a new deck, I strongly suggest a Kenwood KD-600 or KD-650.
Of course, if you’d like Liquid Audio to repair or service your Kenwood KD-650 or KD-600, you need only contact me to book an appointment.
Discover more from LiQUiD AUDiO
Subscribe to get the latest posts sent to your email.
Awesome! I myself have a KD 600 & 650 due to Mike’s previous posts about them & can testify to the absolute truth of his remarks on their amazing sound quality. I had been a vinyl enthusiast for 40+ years prior to obtaining the Kenwood decks & they are hands down the single biggest upgrade to my record listening experience. It fills me with joy to see that yet another of these vintage decks will still be going strong after all these years. Thanks again Mike for being a beacon in the darkness for vintage audio enthusiasts everywhere!!
Thanks Tim and glad you enjoyed the article!
Fabulous repair and information. I discovered this after purchasing a KD-650 a couple of moths ago. The PLL was initially ok but wandered after a few weeks. Upon opening it, the pcb had been butchered by a cowboy, removing most of the pcb pads from the TC4027 flip flop. Removing excess solder that seemed to have been applied by Stevie Wonder and bypass wires suitable for mains, I am back to a good starting point.
I am replacing the trim pots and capacitors as the problem only arises after a couple of hours playing. The VTA was non functional as the muppet had put the fixing cam bar in back to front, damaging the height adjust gear. Work in progress, regrettably I’m in the uk otherwise this would have been sent to you.
I also own a pristine Tri-Vista DAC, so your information about that was also very interesting.
Hi Steve and thanks so much for the feedback, very much appreciated!
I have the KD-750, the next one up the chain. It’s odd that the overall design of the 650 looks more modern and refined. The control board in the 750 looks a bit more dated by comparison.
I recently repaired mine since it developed the dreaded speed control problem. After hours of studying the service manual and troubleshooting, I finally found the problem. IC13 (TA7179P) is supposed to supply -15VDC and +15VDC to a quad op amp, which wasn’t getting the -15V. Had to get a NOS one from China. I tell you, that chip gets HOT. Kinda surprised it lasted 40+ years. I have spares now!
Thanks for your write-up. The part about changing the bearing oil prompted me to do the same thing on my KD-750. Looks to be the same motor. I noticed an improvement – my quartz lock light doesn’t flicker anymore when coming up to speed.
Hi Jamie and thanks for your comment. The KD-750 is a very nice machine and very similar to the 600/650. You’ve done great work there to resolve that speed issue. The whole series is prone to failures that cause speed issues. Can I ask what symptoms yours exhibited?
Ok, so there’s more to this story. I actually have two KD-750s. My first one that I’ve had for 20 years began having intermittent speed control problems. It would lose quartz lock briefly and recover. Problem became more frequent. I recapped it and the problem went away for months. Then, I started it up one day and the platter spun at high speed.
I took it to a stereo shop, they couldn’t figure it out. I found a beat-up “working” parts unit and swapped the boards. It worked for a week with the recapped (Nichicon PW) donor board until it failed. It would lose speed lock, recover, lose it again, and would finally coast to a full stop. Then it would start itself back up and repeat. Well, crap. Two dead turntables. I really studied the service manual and did more troubleshooting.
That TA7179P ended up being the problem in both units. The one that lost the -15V rail had the runaway speed issue. The other one had lost the +15V rail and it had the coasting to a stop symptom. Oddly, I could cure the problem by spraying the IC with freeze spray. Once it warmed back up the problem returned.
Now I have two working ‘750s. The “parts” unit just needs a dust cover and some hinges.
Just curious, what kind of oil did you use to lubricate the motor bearing? I just used some full synthetic 10w30 in mine
Hi Jamie, interesting and thanks for the update. Recapping is rarely the solution, finding the cause of the problem as you’ve done here is the way to go, so well done. The 10/30 oil you’ve used will be fine in this application.
Mike,
Great article. I’ve had my KD-650 since 1982ish? At times my sych light doesn’t come on and the speed doesn’t lock. I’ve found that if I remove the platter cover, lift the the platter and gently replace it the unit will lock at 33rpm again. Seems to happen a lot. Any suggestions on a fix for this would be greatly appreciated. I live in the US or I’d ship it off to you. Thanks
Gary Grobson
Hi Gary, glad you enjoyed the article. These are signs that your deck needs service and electronic adjustment. It can also be an indication that one of the chips in the control circuit is on the way out, one type of chip suffers a ‘soft’ failure of one or more of the gates, leading to symptoms like this. I suggest a proper service first and see if that improves things. This must include electronic adjustment, so you need to find someone who really knows what they are doing as this part is easy to get wrong.
Any idea were I can get replacement hinges for the KD 650.
Thanks, Darren.
I sell and fit them when decks come in for service. They aren’t an exact replacement but better than no hinges. I can’t help if your aren’t local though, my apologies.
Hi, I read through this and was wondering how you clean the switch?
“Here I am about to service the speed control touch sensor. I’ve developed a process to service these switches that eliminate some of the operational issues that arise as they get older.”
Hi Chris, thanks for your question. My exact methodology is proprietary and I try to keep it that way mainly because of the commercial nature of my work and the fact that many competitors snoop around and try to ’emulate’ what I do, bless ’em! That being said, I can apply all the tricks I’ve developed to your deck as part of routine maintenance, or you could send me the switch. Either way, the switch has to come out of the machine for what I do. Feel free to enquire via my Contact page if you have specific questions.
Hello.
First of all congratulations on the review, it’s really great and can help a lot of people with devices like this. Well done!
If you could give me some help here I would appreciate it.
I recently acquired a KD 650 with problems.
In 33 everything is perfect but when I change to 45 the turntable starts spinning backwards, yes, backwards, at an uncontrolled speed.
Any clue what it could be?
Hi Lucas, thanks for your comment and I’m glad you enjoyed the article. I’ve been writing about and repairing these great decks for many years and never get tired of working on them. These are complex turntables though and really expert attention in cases like this, and even for general service. The drive circuit is responsible for keeping the platter turning in the right direction, at the right speed. Logic controls these functions, with analog speed feedback and comparison against a reference. This will likely be a logic issue, but beyond that, actually tracing the fault and diagnosing it will require hands-on time with someone very familiar with these machines. Forget recapping or shotgunning parts, someone really familiar with these will be able to trace the likely fault in the logic circuits that control the deck and fix it. If you were local I would be happy to assist but I’m guessing you are not. Do you have a specialist repairer familiar with these machines you can visit?
Hello and thank you for the reply.
I’m in Portugal… Very far away…
I have no one to turn to for now but myself, I’ll do some measuring tests on the IC’s and look at the manual to see if I can figure out what’s going on.
Given your experience this problem could have already passed through your hands.
Thanks anyway.
Hi Lucas, no problem and yes, I’ve seen virtually every possible platter/control scenario including spinning forwards, backwards, fast, slow and not at all. They each have different and sometimes various causes. It’s never a case of “replace part X and the problem will be solved” with electronics repair, especially a mixed signal control circuit like this. The service manual is great in terms of explaining the deck logic though. Start by looking at the logic and gates involved when activating 45 rpm mode and then test those gates with the deck running to validate logic truth.
the service manual that circulates online is of very poor quality which makes the situation even more difficult.
do you think it is possible to scan your manual and send it to me?
pages 18, 23, 30 and 31
Hi Lucas, I cannot assist with a scan unfortunately, but the widely available electronic copy is useable, if not the best scan. Pages 30 and 31 are very useful and the voltages are all legible as far as I can see.
Hello
You do superb work, I own a Kenwood KD 850 turntable. Unfortunately I hadn’t turned in on for a few years. When I attempted to, it powered on, spun, then died. It will not power on anymore. Any idea as to what the cause can be. I reside in the United States and would have gladly brought it in to you since you do impeccable work.
Hi and thank you for your question, glad you are enjoying the site. Unfortunately, without the gear in front of me, there is no way to know what has gone wrong here. Rather than speculate or attempt anything at home, my best advice with anything like this is to find a turntable specialist you can take the deck to, as you would a car, watch, etc. A good way to find someone decent is to call the best hi-fi stores in the biggest city in your state and ask who they recommend for direct-drive turntable repairs. Best of luck, these are lovely machines that need to be kept running.
Hey! Can you give me a recommendation on how to clean my KD-600? I recently had it repaired, but the service did not include any cleaning. The example here looks crisp, so I would love to get mine in a similar condition in the safest way possible.
Hi, glad you enjoyed the article, I have FAQs for many questions like this, so try this one on cleaning: https://liquidaudio.com.au/faq/how-should-i-clean-my-hi-fi-gear/ . Beyond this I use proprietary cleaning regimens, but careful use of a soft microfibre cloth and mild detergent solution is a great starting point. Note that the touch switches with their super-high impedance are sensitive to moisture, ie humidity, etc. Enjoy that lovely deck!