I’d be happy to provide an estimate once we’ve diagnosed the fault/s and determined what remedial work will be needed.
That will, of course, require a careful and detailed inspection of your equipment, and avoid any unhelpful guesswork.
Assessment
Electronic equipment failures are typically ‘black box’ scenarios, meaning there are usually no obvious visual signs as to what has gone wrong. Contrary to what some imagine, failed components generally show no external signs of failure and ‘bulging capacitors’ are largely a meme created in forums, unfortunately.
Progressing from failure to remediation is where skill and experience come into play. The only solution is to test, measure, and get to the root of the problem/s. Asking a technician for a quote before they’ve looked at a piece of equipment is asking them to guess what’s wrong, what parts will be needed and how long the repair will take when they have none of that information.
Any answer will likely be wrong, so there is little place for guesswork in technical repair scenarios. It’s no different from asking a mechanic for a quote over the phone to fix a car with unknown problems or asking a surgeon for a quote on surgery before they’ve seen the patient. If these scenarios seem silly, then you’ve understood the point I’m making here.
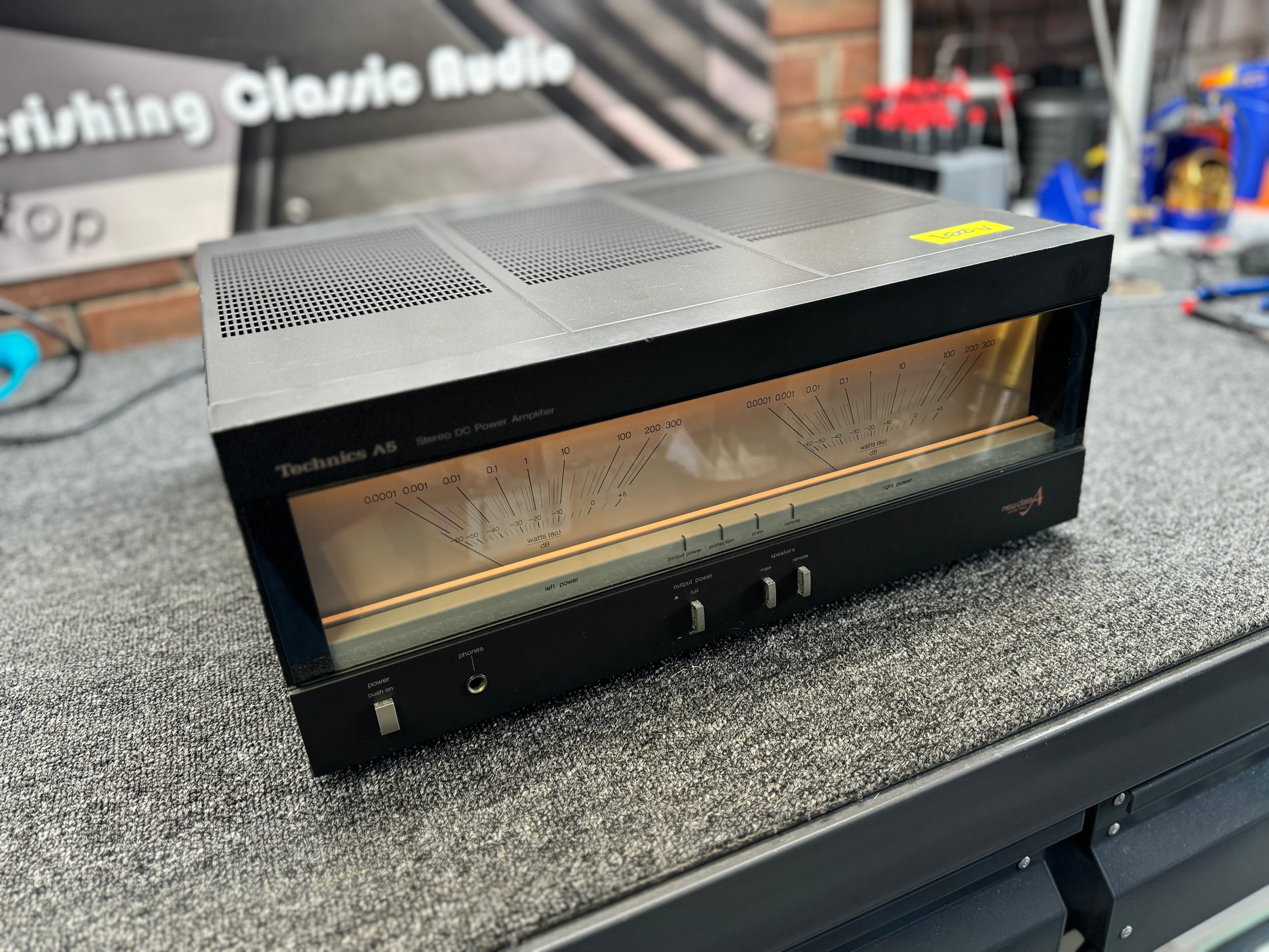
Six Steps
The correct approach involves a logic-based assessment of the equipment and its faults involving six steps:
- Collection of evidence
- Analysis of the evidence
- Location of the fault
- Determination and removal of the cause
- Rectification of the fault
- Checking, adjustment and calibration
Steps 1 to 3 comprise the assessment phase and generally have to be completed before a cost estimate can be offered. All steps require hands-on work with the equipment.
Other issues may become evident once work has commenced, which is why reputable repairers typically provide cost estimates.
Pretenders
So, why would anyone pretend to know what’s wrong and how much a repair will cost without first inspecting and testing the equipment in question? There’s a very simple answer to this: Because they need the business, and they’re prepared to take risks and mislead people to secure it.
Some folks expect sight-unseen quotes, and less ethical repairers enable this expectation because it brings them work from people who don’t know any better. It’s worth understanding that businesses that do this typically are those you would not want to use. We don’t engage in these sorts of practices, nor do we need the work.
I could never have guessed what was wrong and the hidden last fault with this Krell KSA-100S I repaired, for example. Similarly, an Accuphase E-303 that I repaired contained five unrelated, unguessable faults. One of the worst pretenders destroyed this beautiful Gryphon DM-100 class-A amplifier.
More…
Information regarding general service and repair costs can be found in this FAQ. Find out more with these repair-related FAQs:
- Liquid Audio’s charging structure
- Why equipment inspection is so important
- Why some equipment shouldn’t be repaired
- Why we are often fully booked
Discover more from LiQUiD AUDiO
Subscribe to get the latest posts sent to your email.