It’s not all equipment, but in some cases, it will be compromised, damaged or even destroyed. It all depends on who’s worked on it; that’s the key.
In a nutshell, the picture below is why I often refuse equipment that has been worked on by the worst offenders:
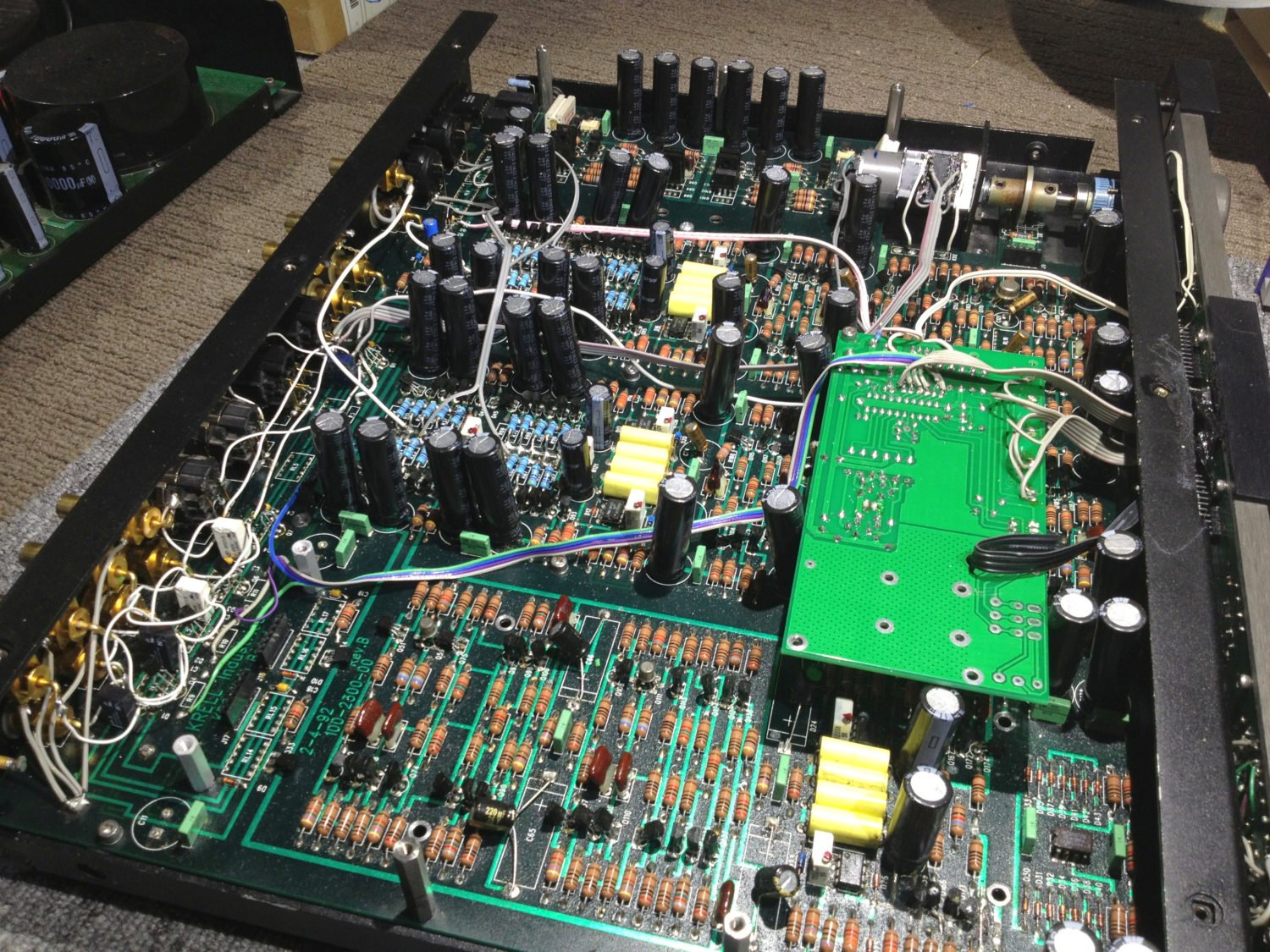
I don’t enjoy cleaning up mess left by others. The best hi-fi equipment is unmolested, perhaps dirty or even broken, but in original condition and ready for someone who understands how to care for it. I am happy to work on pieces that skilled technicians have worked on, but sadly, highly skilled professionals are few and far between.
Many DIY and commercial attempts at maintenance introduce faults such as damaged printed circuit boards and pads, compromised wiring and low-quality, incorrect or mismatched parts. This work not only does not resolve the original issues but these newly introduced problems can be terminal for the equipment.
Owners are then left with a mix of old and new faults and the need to find a skilled repairer who will take on such a case. Many won’t. A classic example of equipment I helped out my customer with was this Sansui AU-317.
There are industry parallels everywhere, by the way. Every mechanic, for example, knows the pain of working on a vehicle, only to find loose, broken, stripped or missing fasteners everywhere. The same scenarios occur with musical instruments like guitars and synths, poorly constructed buildings, etc. It is torture to work on anything bodged.
Undoing this stuff can be time-consuming, tedious and expensive, and when you’ve seen and tried to undo as much of this sort of thing as I have, you will understand why I generally avoid it.
Discover more from LiQUiD AUDiO
Subscribe to get the latest posts sent to your email.