If you love beautiful, well-maintained hi-fi gear, you’re not going to love the Hall of Shame…
I think most people would prefer to learn about poor and unethical operators – bodgy builders, egregious electronics technicians and maladroit mechanics, for example – before they damage the things we own and love. This simple premise, and my passion for truth, fairness and improving standards within our industry, led me to create my now widely emulated Hall of Shame. Welcome!
Liquid Audio’s Hall of Shame, or ‘HoS’, sheds critical light on hi-fi equipment that has been damaged, devalued, or destroyed by individuals and businesses claiming to repair and improve it. We do this not with any sense of pleasure, but because it needs to be done, as uncomfortable as it is. Each case includes photographic evidence and a detailed analysis to educate and empower people to make more informed choices about their technicians.
Hi Mike,
Just wanted to say you’re doing an amazing job bringing things like this to light and putting the offenders on display!
Keep it up mate, it definitely makes me squirm to see and read, but can’t deny the catharsis of it not being my problem! 😉
– Mason
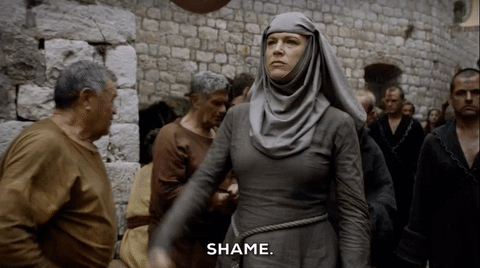
This resource never criticises legitimate, professional businesses and technicians. I have nothing but respect for my colleagues and anyone who takes their job and responsibilities seriously. The cases presented here undermine diligent, hard-working technicians everywhere. Those responsible should be ashamed of themselves, seriously.
Ethics
I’m guided by a golden rule of ethics summarised by this quote:
“If you see fraud and do not say fraud, you are a fraud.”
Nassim Nicholas Taleb
Many of these perpetrators continue to ruin hi-fi gear because people who know about it say/do nothing. Turning a blind eye only helps perpetuate the problem, and I have a problem with that. I’ve even lost customers over this, people I’ve insisted need to follow up on ruined equipment, to at least help others, and I make no apologies for this position.
If you’ve had equipment damaged by one of these bad businesses, you owe it to others to do something about it. It is your responsibility to do so; don’t rely on people like me to do that work.

Qualifications
One of the worst perpetrators in the HoS claims to be an engineer but has no engineering degree, nor anything even remotely resembling one. He’s barely literate. That’s not to say qualifications or literacy tell us anything about the quality of someone’s work; they do not. I’ve seen good and bad work at the hands of engineers and non-engineers alike, but one should not lie about qualifications.
I have an Honours Degree in Science and a Post-Graduate Diploma in Science Education from one of the best universities in the Southern Hemisphere. I was a specialist secondary science teacher for 15 years, worked for the Department of Education, and mentored/trained thousands of pre-service secondary teachers as a mentor teacher and later at Curtin University School of Education. I’ve also run Liquid Audio for 15 years. Blah, blah.
You may or may not care about that, and maybe it doesn’t matter, but it certainly tells you a couple of things about my intellectual abilities, dedication to learning and science, and my professionalism. Five years at a difficult-to-enter university is very different to an online course that literally anyone can take. It doesn’t tell you anything about the quality of my work; only my work does that. Remember this point.
Cheap = Expensive
If you think it’s expensive to hire a professional to do the job, wait until you hire an amateur.
Red Adair
Choosing the cheapest business to undertake work requiring the maximum skill and attention to detail is always a bad idea. Let’s examine cheap vs. quality electronics technician workmanship using a benchmark piece of equipment: the legendary Quad 405-2 power amplifier.
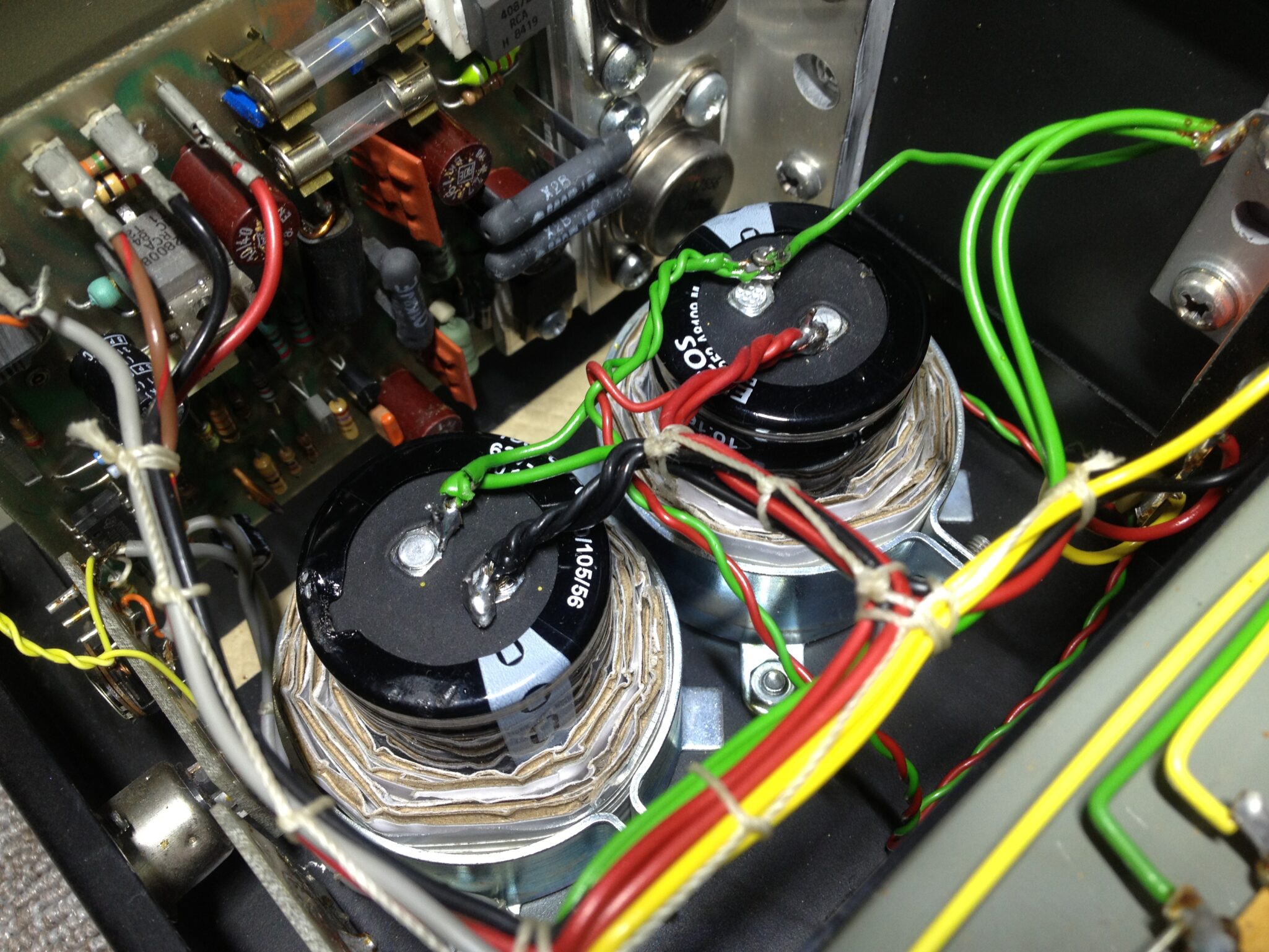
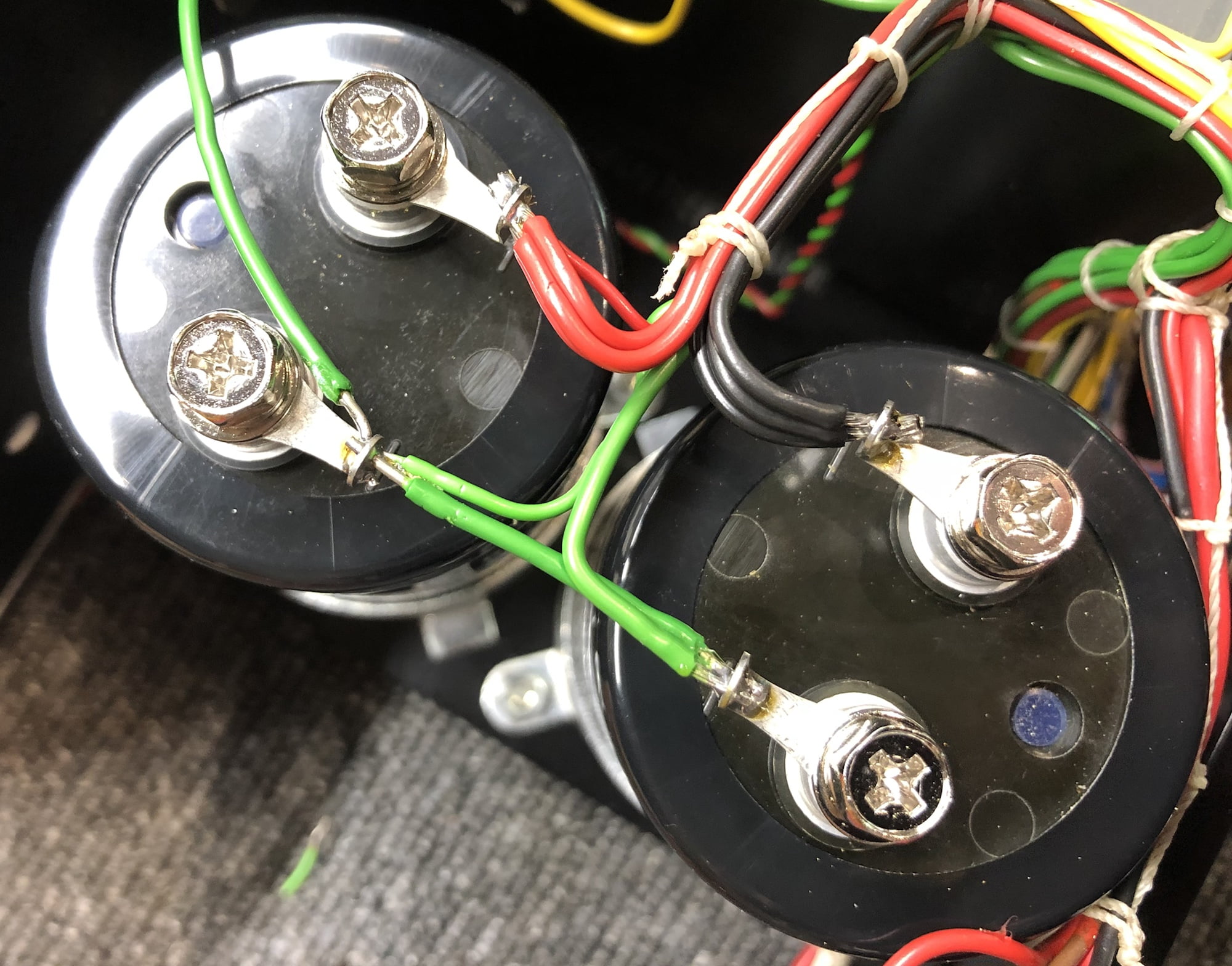
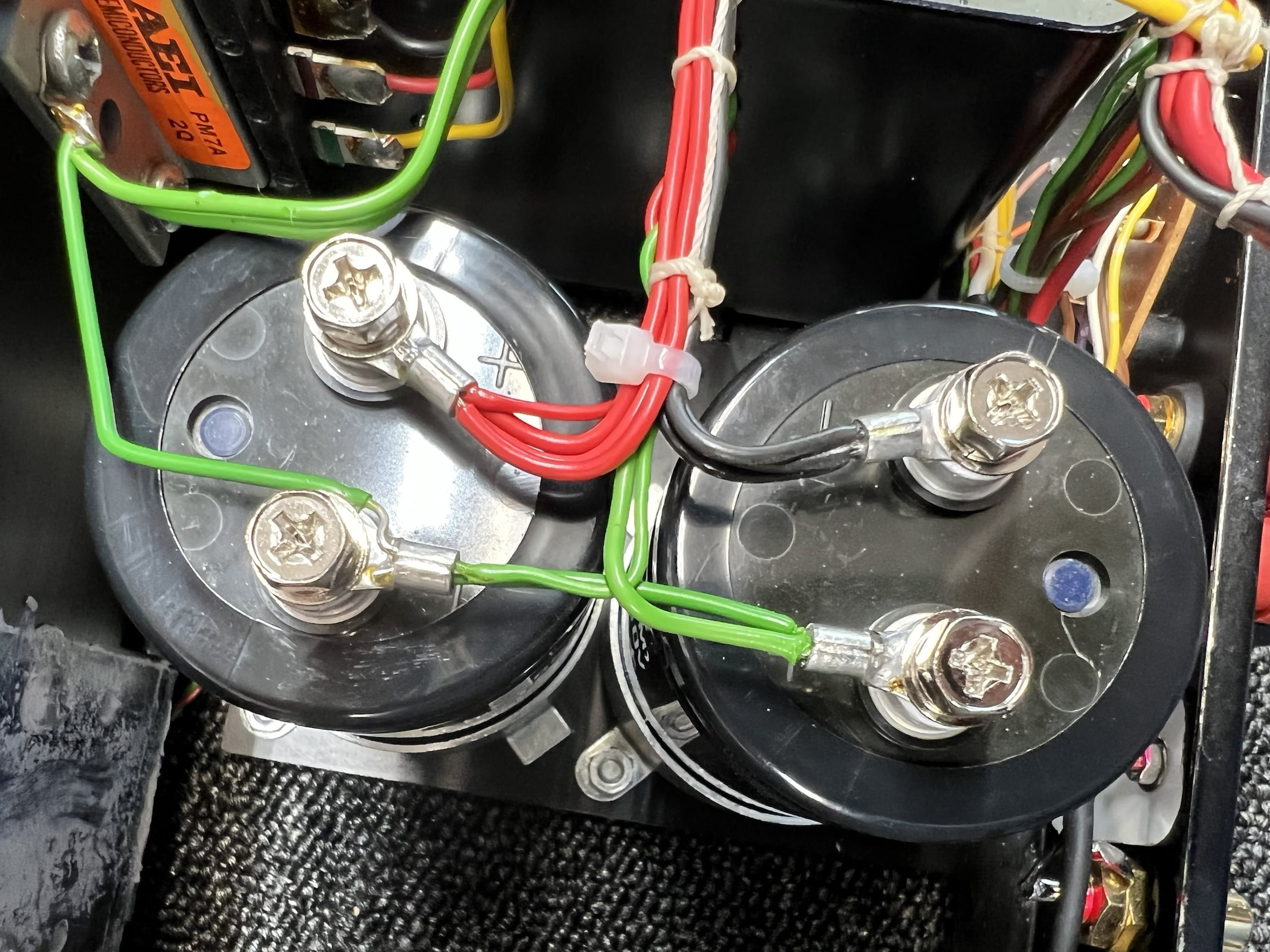
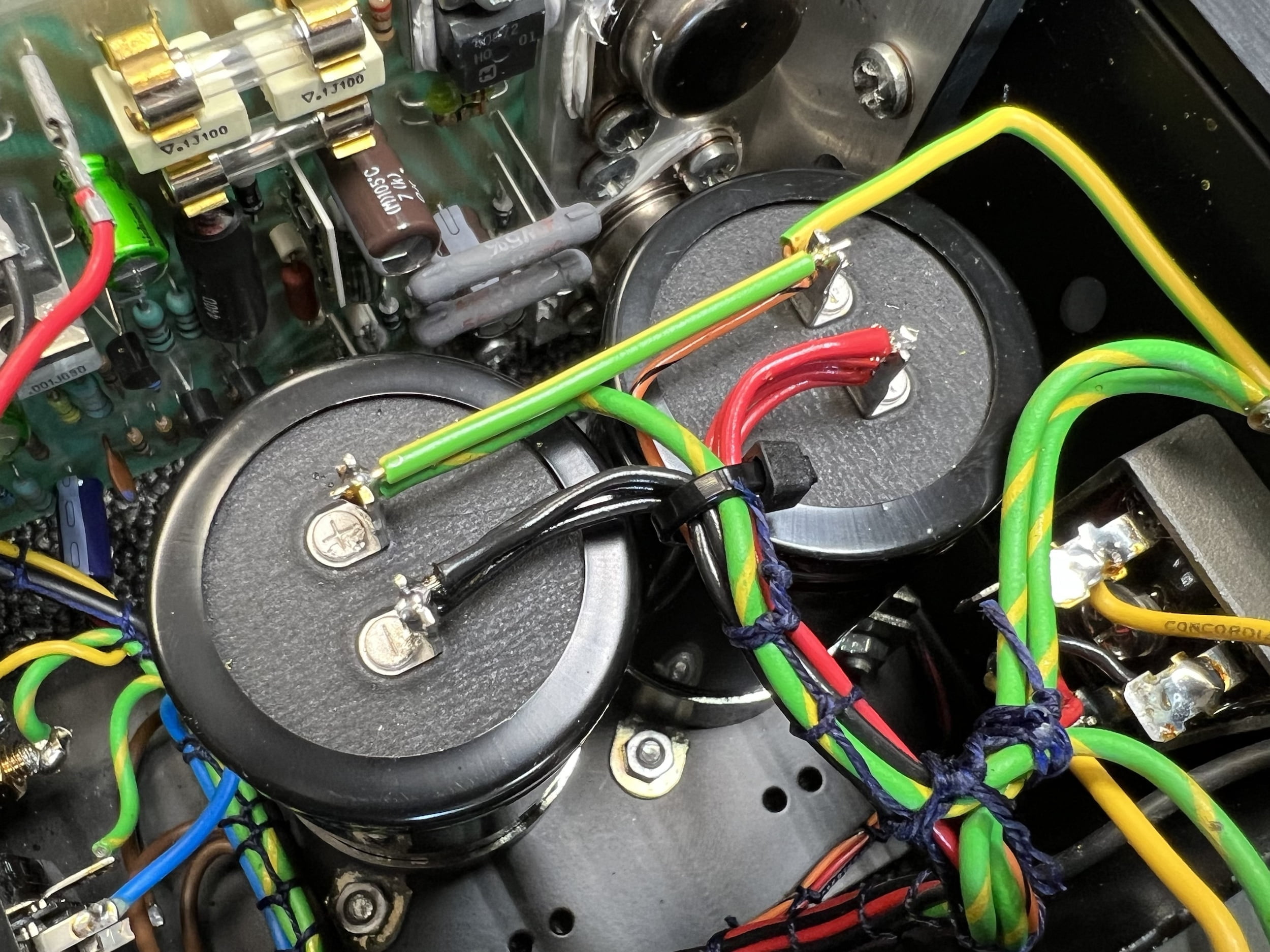
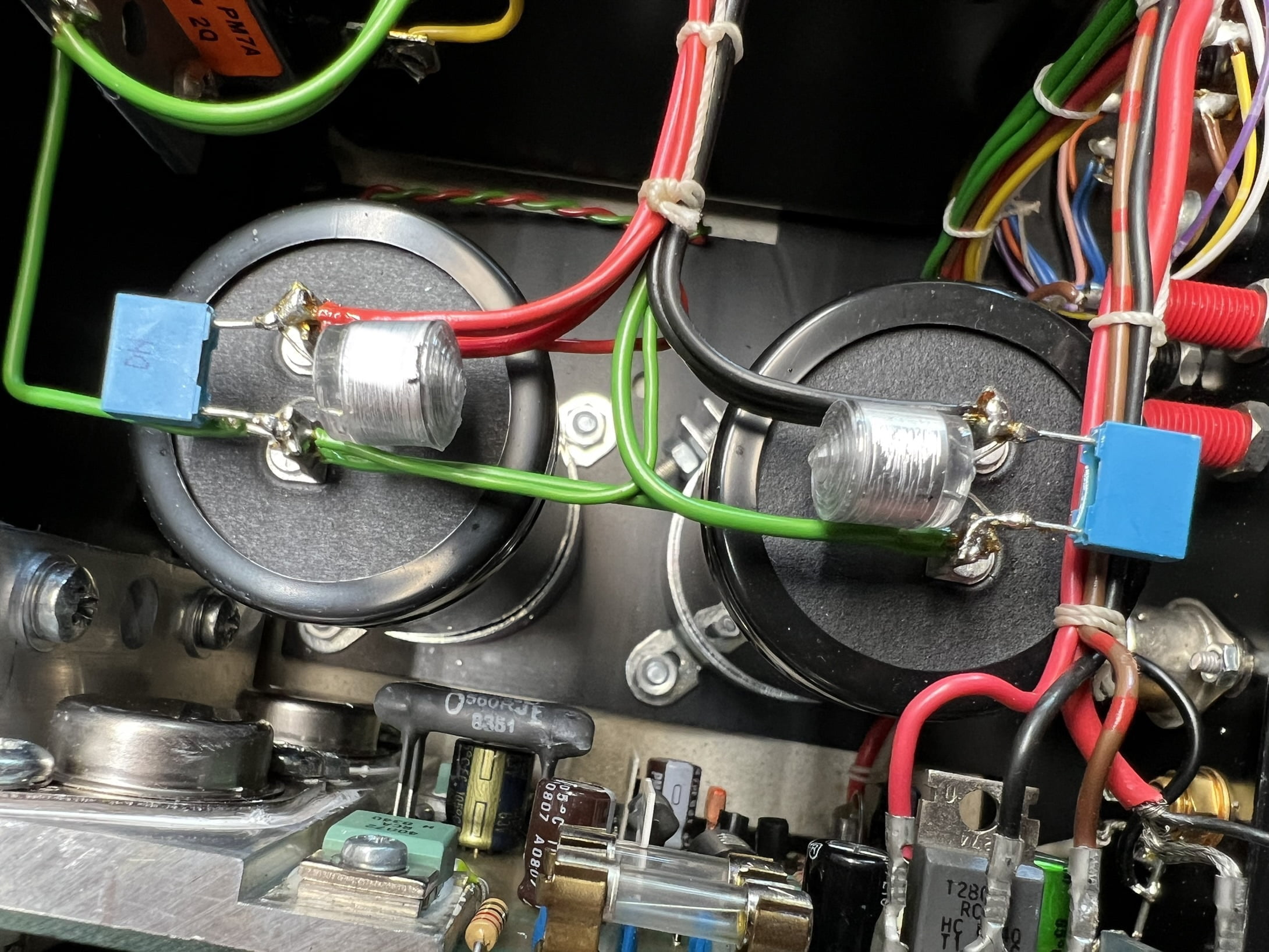
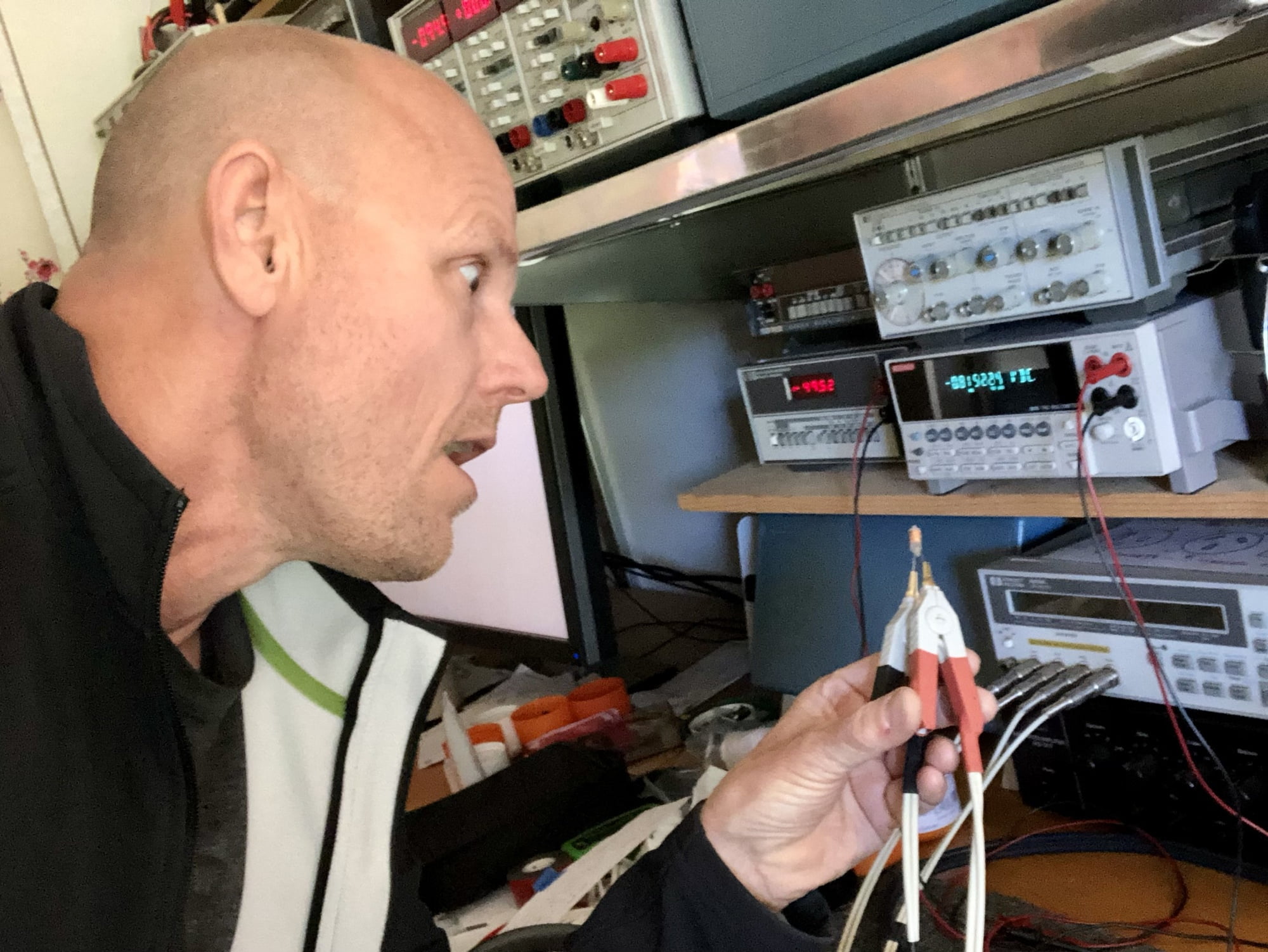
Professionalism
I’ve been thanked many times for building the HoS, but I’ve also been abused, gaslit, threatened and accused of running a “hatchet job”. I mean, you’d think there could only be praise for reporting on terrible work and helping people, right…?
It turns out that lots of people don’t want you looking at these cases. These people would rather the HoS disappear so you don’t hear about the pain and anguish, financial losses, court cases, irate emails and wasted time and energy the owners of such equipment go through. That says a lot about those people. I can’t imagine a more unethical stance.
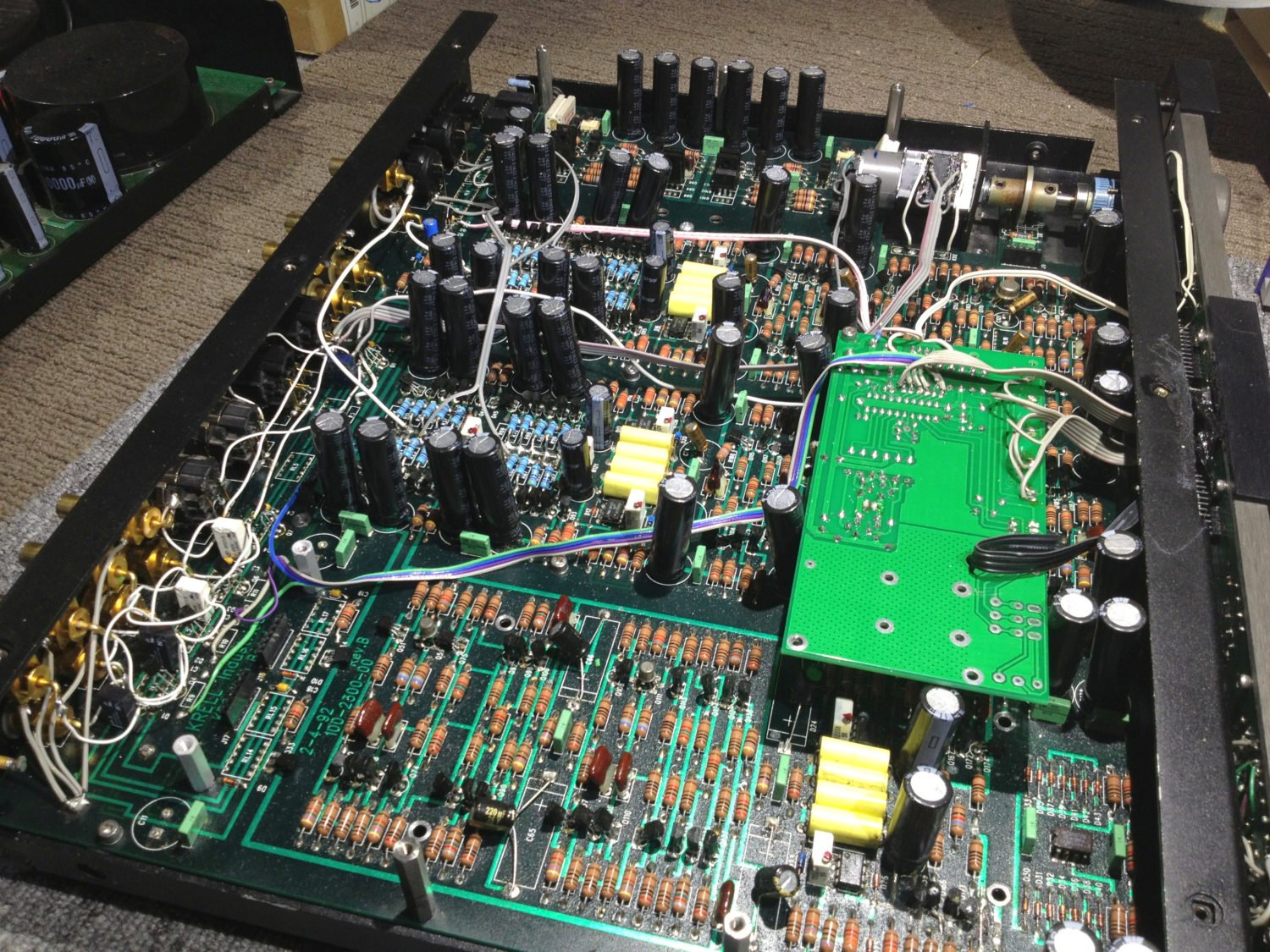
It’s not only me who’s been attacked by the way. Take this example, courtesy of the most featured business in the Hall of Shame and loser of a significant 2024 case in Joondalup Magistrates Court:
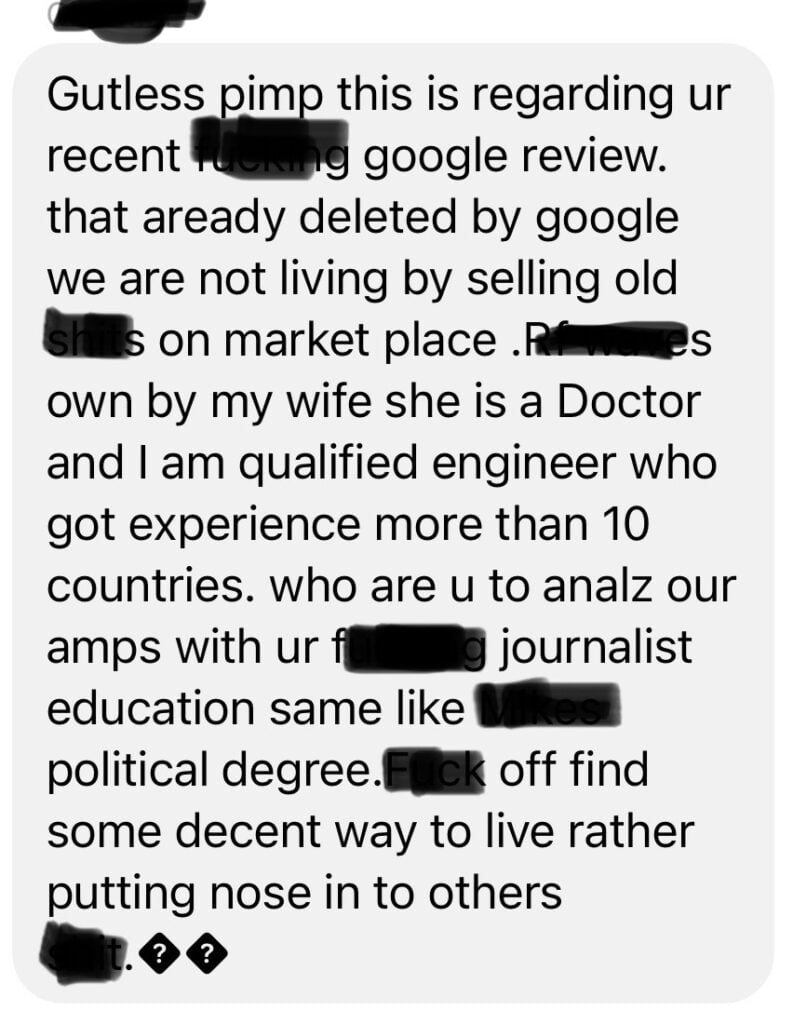
Mr RFW sells mains-powered equipment that has not passed ADRs and cannot legally be sold here in Australia. He regularly rants at unhappy customers and sent this rant to a state senator. This uber-offender has recently (2025) started to tell anyone who’ll listen that there is “a conspiracy” against him, led by yours truly! I wasn’t even the expert witness who gave evidence against him in the Joondalup Magistrates Court case he lost in 2024, though I did take some of the images used by the expert witness in that case.
For those who don’t know, I do my own thing and run Liquid Audio in my unique way. Thankfully, this approach is popular with intelligent customers, and the opposite of that which leads to ruined equipment and court cases. This is no accident BTW. I was also fortunate to inherit honesty, integrity and professionalism genes, and I’m focused on doing good work and supporting my customers. Conspiracies are stupid, there is no conspiracy.
What there is, however, is the reality of terrible work and damaged or destroyed equipment. These people don’t want, or simply cannot bring themselves to accept responsibility for it, because it reflects so badly upon them. Instead, they would have you believe that, rather than their poor workmanship, terrible reviews, lost court cases, and incoherent, unprofessional rants at customers, generating their poor reputations, it’s me. And yes, these are adults…
Moving Forward
Two businesses featured in the HoS lost court cases in 2024. One of these businesses has had at least three business names in the time I’ve been running Liquid Audio. It doesn’t take a rocket scientist to know why businesses frequently change names. That business, which features here, is not the worst.
It’s important to understand why these types of businesses exist:
- Low prices; it always starts here. Too many mistakenly equate the lowest price with the best deal, only to learn that the best deal is a blend of factors rarely correlated with cheap.
- Many budget businesses ‘borrow’ design, style and content ideas from professional competitors with excellent reputations, to attempt to lead others to assume they offer similar levels of quality and technical excellence.
- Cheap work attracts less informed, less fastidious customers who are less likely to realise they’ve been had
- Many are afraid to take action because of aggressive retaliation from business owners. Customers have told me they’ve been screamed at and even pushed and shoved in one recent case with a dodgy southern seller.
- Bad reviews are often removed via bribes and refunds, and fake positive reviews are purchased, skewing ratings and painting an unrealistically positive picture.
Prospective customers and the hi-fi community can help by keeping the following in mind:
- Finding an expert, trusted technician should drive decisions about who to use
- Quality is more important than any price or a blind quote. The result is what matters; cost-cutting = corner-cutting.
- Support and promote ethical businesses that positively contribute to the hi-fi community
- Research business name changes, review scrubbing, negative reviews and business owner responses
- Leave honest reviews for good and bad work without fear or favour. If you’ve had equipment damaged or destroyed, you have a moral responsibility to let others know.
Two local businesses lost major court cases in 2024 because of diligent equipment owners who said enough is enough and did something about it. People rely on me and the HoS, but I cannot do all the heavy lifting here; it’s exhausting.
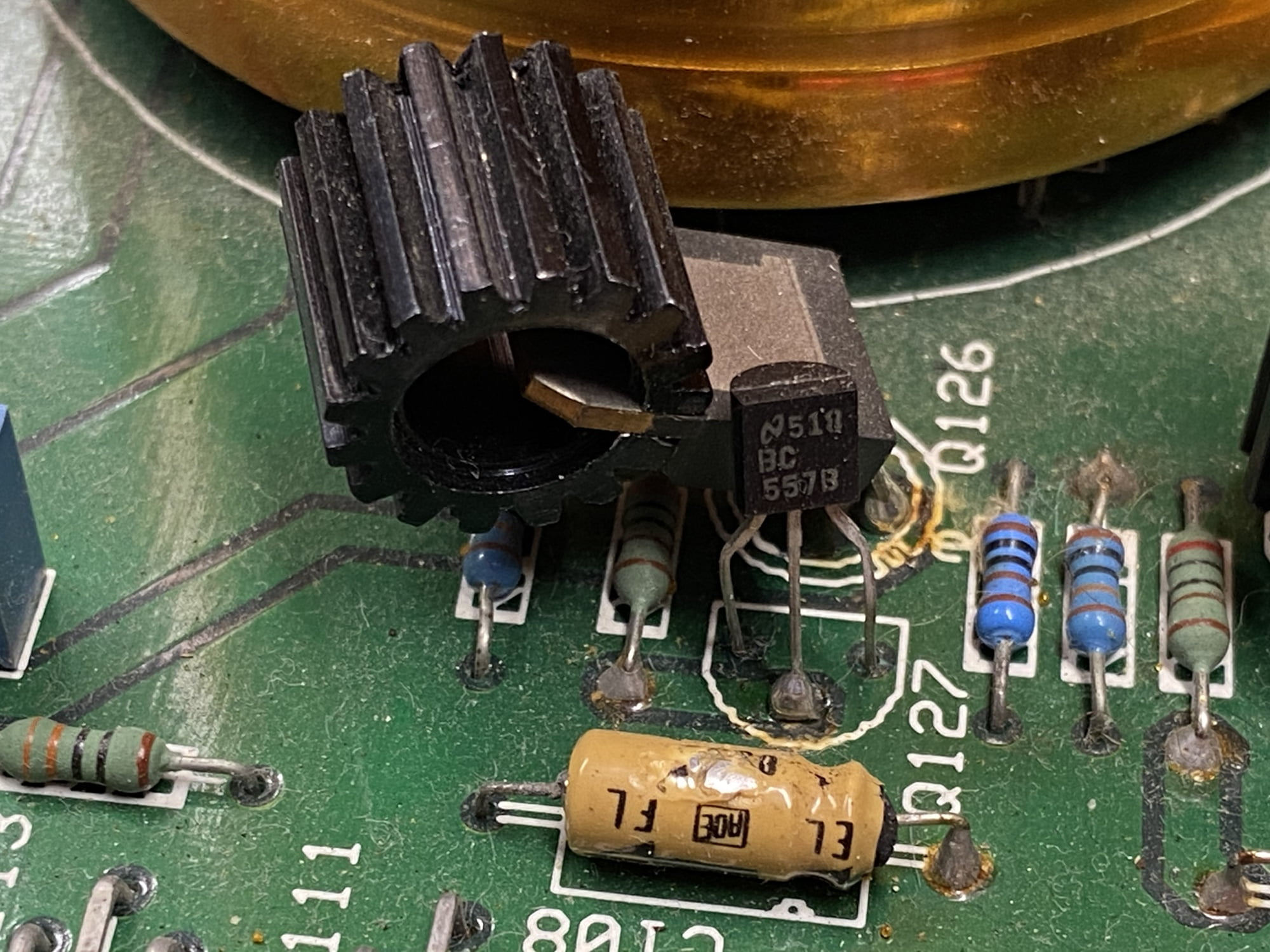
HoS FAQs
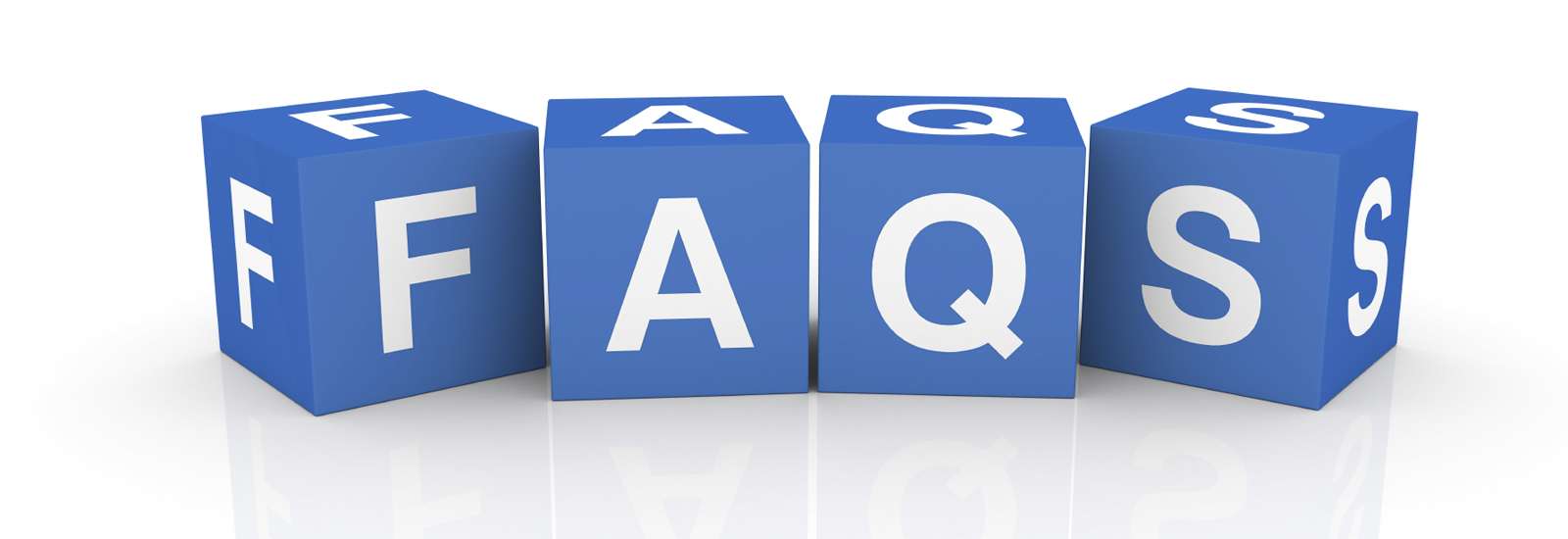
Q: Mike, what’s the purpose of the Hall of Shame
A: To save people and their equipment from businesses pretending to do high-quality work.
Q: Surely these are simple mistakes anyone could make?
A: No, everything you see here demonstrates a profound lack of care, skill and technical knowledge/ability.
Q: Mike, one of the worst of these guys claims this is all a consiracy by you to ruin his business!
A: I’m not interested in ruining anyone, only in saving people’s cherished hi-fi equipment and exposing folks who ruin it. There is literally no other motive. I don’t need work, I don’t know the guilty.
Q: Mike, but one of these guys claims to be an engineer!
A: He does, and in a 2024 court case, this was found to be untrue by standard definitions of the term. This is deliberately misleading at best.
Q: Mike, you’re not a ‘real’ engineer either.
A: Correct, I neither studied engineering nor ever claimed to be an engineer. Most importantly, I don’t need to be an engineer to be an expert in my field. I have an Honours Degree in Science and a post-graduate Diploma of Science Education, five years of full-time, in-person study at one of the world’s great universities. I don’t know of any other local technician who can make that claim. How bout dat!
Q: Isn’t the Hall of Shame here “Just to make you look clever?”
A: No, Liquid Audio established a reputation as a highly respected repairer before creating the HoS.
Q: Mike, who gave you the right to judge this work?
A: Everyone has that right, though I am especially well-positioned to assess them and have inspected all of them.
Q: Who cares what you think about these cases?
A: Many clearly do, but you must make up your mind.
Q: Mike, do you “have it in” for bad businesses?
A: No, I have no interest in any of these people and I’d rather not have to document these cases.
Q: Mike, do you get annoyed when people bring equipment to you after it’s been destroyed by others?
A: I politely explain that I’m not here to clean up the mess left by others.
Q: Mike, you’re just negative.
A: What I present here is information; it cannot, by definition, be negative or positive.
Q: Mike, aren’t you trying make out that you’re better than everyone else?
A: No, I don’t believe that, nor am I trying to promote that idea.
Q: Mike, isn’t it unprofessional to highlight others’ poor work?
A: No, I would argue that it’s part of my professional responsibility to do so.
Q: How do people behave when called out?
A: Most react badly, even screaming, ranting and becoming physical with people who mention it.
Q: Mike, have you ever met any of the people featured in these cases?
A: Only one, from case #15. I’ve spoken to Trevor Lees from case #6, and the owner of the business in case #16.
Q: Mike, are you legally entitled to name people?
A: Yes, in Australia it is neither defamatory nor illegal to factually report information, or express opinions about people, businesses, places and products.
Q: Mike, has anyone tried to force you to remove a case?
A: Yes, Trevor Lees from case #6 and the business owner responsible for case #16 both threatened me with legal action if I didn’t remove their cases. A professional conversation would have been much better, threats tend to make me dig my heels in.
Q: Are you worried people will try to force you to remove these cases?
A: No, nobody will ever force me to do anything I don’t want to do.
Q: How can people do such poor work?
A: Delusion, greed, the Dunning-Kruger effect, there are many reasons.
Q: Mike, how can you be sure the people did the work attributed to them?
A: Verification is achieved via my firsthand inspection of equipment and interviewing the owners.
Q: Mike, thanks for making this resource, but it’s a fair weight to carry. Are you OK doing this?
A: Thanks for your concern, and yes, it is a little ‘heavy’ at times, but someone has to do it. Many owners who’ve been burned frustratingly do nothing. Life’s short, and it’s worth standing up for what you believe in.
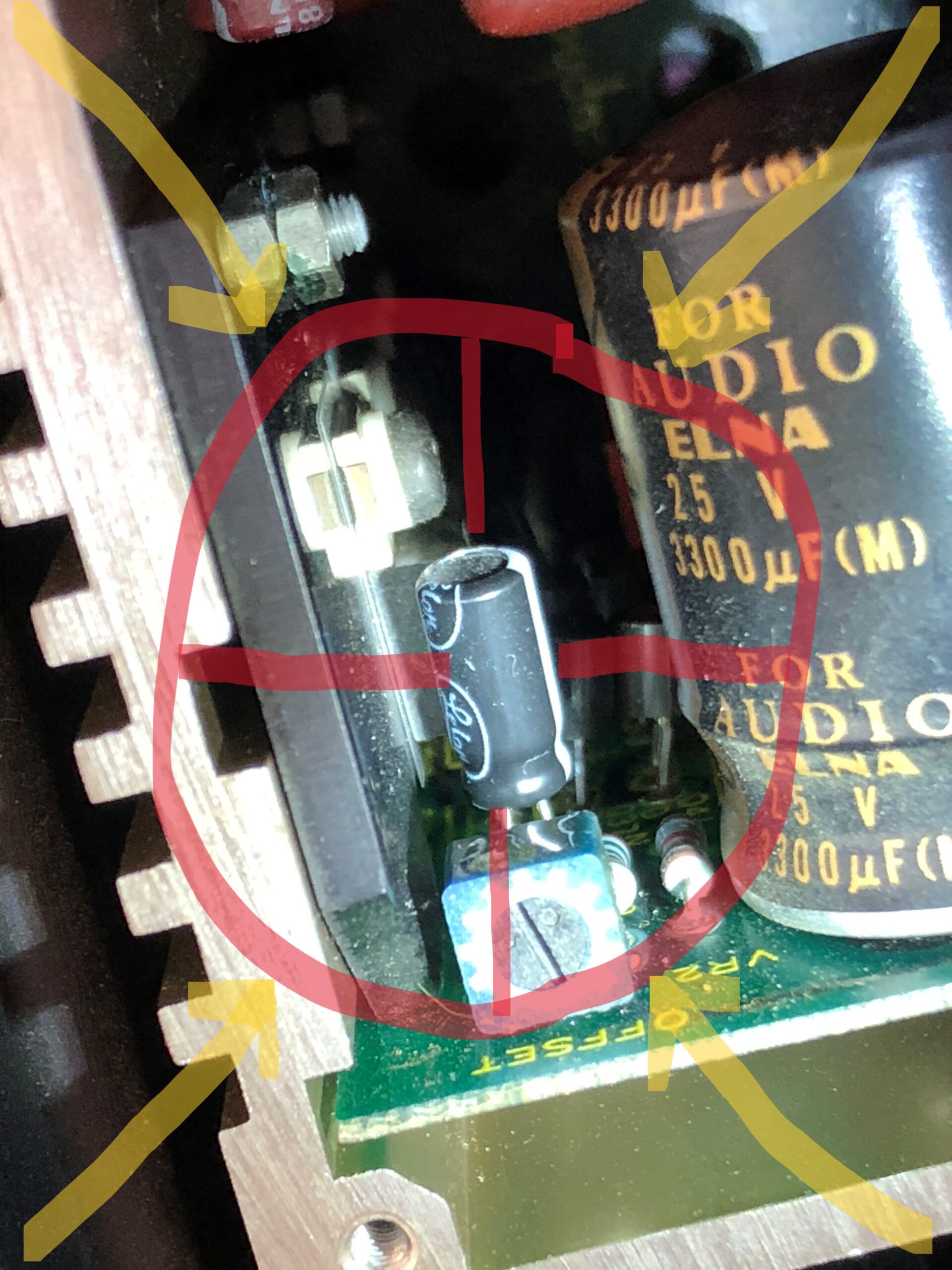
Hall of Shame Case Files
Important Case Updates
Update, December 2024. I have the transcript for the RFW court case and there is some very amusing content!
Update, April 2024. Two of Perth’s worst repairers have recently just found themselves in Magistrates Court and both LOST, both being found liable for damages. One didn’t even turn up to court, a sign of the respect he has for the legal process. People are taking action, WELL DONE to both brave individuals for standing up for themselves, bringing their cases and winning!
Update, March 2024. The individual responsible for so much of the carnage on this page including cases # 1, 10, 13, 14, 18, 19, 20 and others was recently taken to court over the destruction of multiple pieces of equipment worth many thousands of dollars by a brave victim not prepared to let it go. His case was heard on 12 March 2024. Mr RFW LOST THAT CASE and was found liable for all damages.
Update, 16 May 2023: We won, everything stays, see case #16 for the details. See the case #16 deeper holes postscript for the latest.
Update, 10 May 2023. The manufacturer of the equipment in case #16 has threatened me with a lawsuit in an attempt to force me to remove his case from the HoS. We now have confirmation he built the equipment and my guarantee that the images will remain visible.
Disclaimer
- All cases come from customers of Mike @ Liquid Audio and Jason @ The Speaker Doctor
- The opinions expressed are my own and the content here may not be re-used without my permission
Case Index
- Ortofon 2M Bronze moving magnet cartridge
- Luxman 5L15 integrated amplifier – coming soon
- Sansui AU-505 integrated amplifier
- Kenwood KA-9150 integrated amplifier – coming soon
- Marantz 2270 receiver bodges
- ‘High-quality’ Western Australian tube preamplifier
- Yamaha CR-600 receiver
- Naim amplifier death – coming soon
- NAD 218THX power amplifiers + speaker death
- Accuphase C-280 Preamplifier
- Denon PMA-1060 Integrated Amplifier
- Gryphon DM100 Class-A Power Amplifier
- Pioneer PDS-507 CD Player
- MAS Solitaire Power Amplifier #2
- MAS Solitaire Power Amplifier #1
- Krell KSA-150 Power Amplifier
- Marantz CD85 CD Player
- Krell KRC HR Preamplifier
- Harman/Kardon PM-655 Integrated Amp
- Perreaux PMF 3150 Power Amplifier
- Kenwood KA-5700 Integrated Amplifier
Case 21 – Ortofon 2M Bronze Moving Magnet cartridge sold to a buyer with “only 20 hours” use…
Space here in the HoS is generally reserved for shonky technicians, but occasionally, with particularly egregious cases, I will feature shonky sellers, like this one from Tasmania.
The “only 50 hours” cartridge use/wear meme has been part of the hi-fi community and forums for decades. It’s where someone selling a cartridge typically dramatically understates the number of playing hours a cartridge has seen to tempt buyers and get a better sell price. It’s like winding back the odometer on a car – a dog act.
Wear
Cartridges wear out, based on playing hours, condition of your vinyl and other factors like stylus shape and tracking force. I’ve written more about stylus life in this FAQ.
Therefore a typical cartridge-for-sale ad might read:
“Ortofon MC Jubilee moving coil cartridge for sale, only 50 hours!”
50 hours is almost like new for a good line-contact type stylus, perhaps only 3 – 5% worn. The ‘funny’ part, for those who think being ripped off is funny, is that people are rarely creative in terms of their usage estimates. Folks invariably settle on the 50-hour estimate, no matter how ridiculous or implausible it is that every cartridge has only 50 hours of use! Wear and usage can of course be estimated, a specialist service we offer.
Example
One should probably use a 10x multiplier with many of these listings, based on what I’ve seen over the years. Take this example from a seller in Tasmania, advertising on StereoNet here in Australia.
This Ortofon 2M Bronze moving magnet cartridge, a transducer I’m very familiar with, was listed as having only 20 hours of use, in supposedly excellent condition. One of my customers purchased it and asked me to install it on his Pioneer PL-71 direct drive turntable, after servicing the deck for him.
I realised after closely inspecting the cartridge that it was damaged and the suspension was shot. It actually looked more like it had seen 200+ hours, perhaps many more, tying in with my 10x multiplier advice. It might look like this after 20 hours playing my garden beds, but not playing good, clean vinyl.
The seller’s photos were poor and/or misleading because they lacked the resolution, detail and angles needed to clearly see the condition of this dud. Unhelpfully, the seller did not respond to my customer when he raised his concerns. This says a lot.
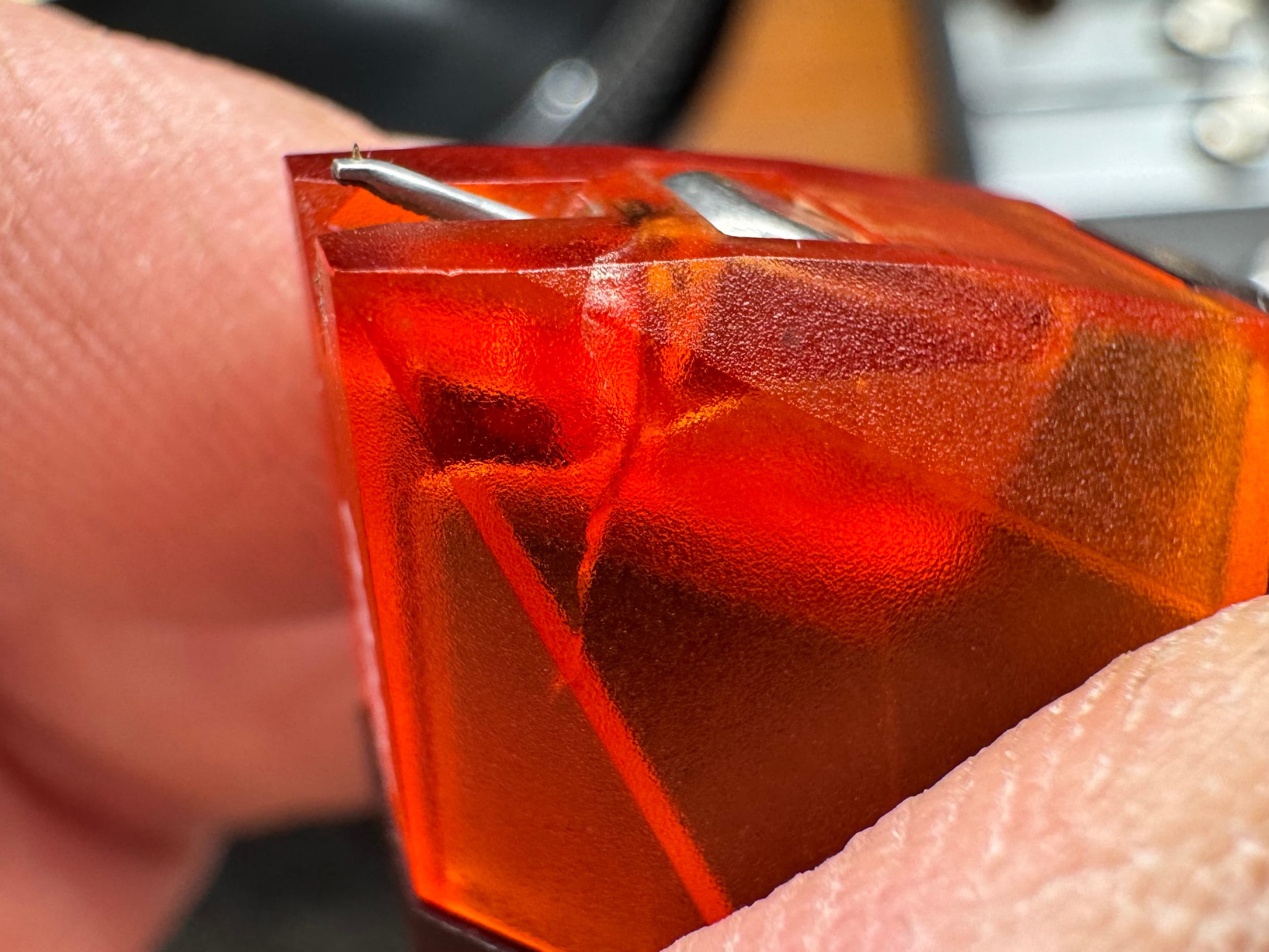
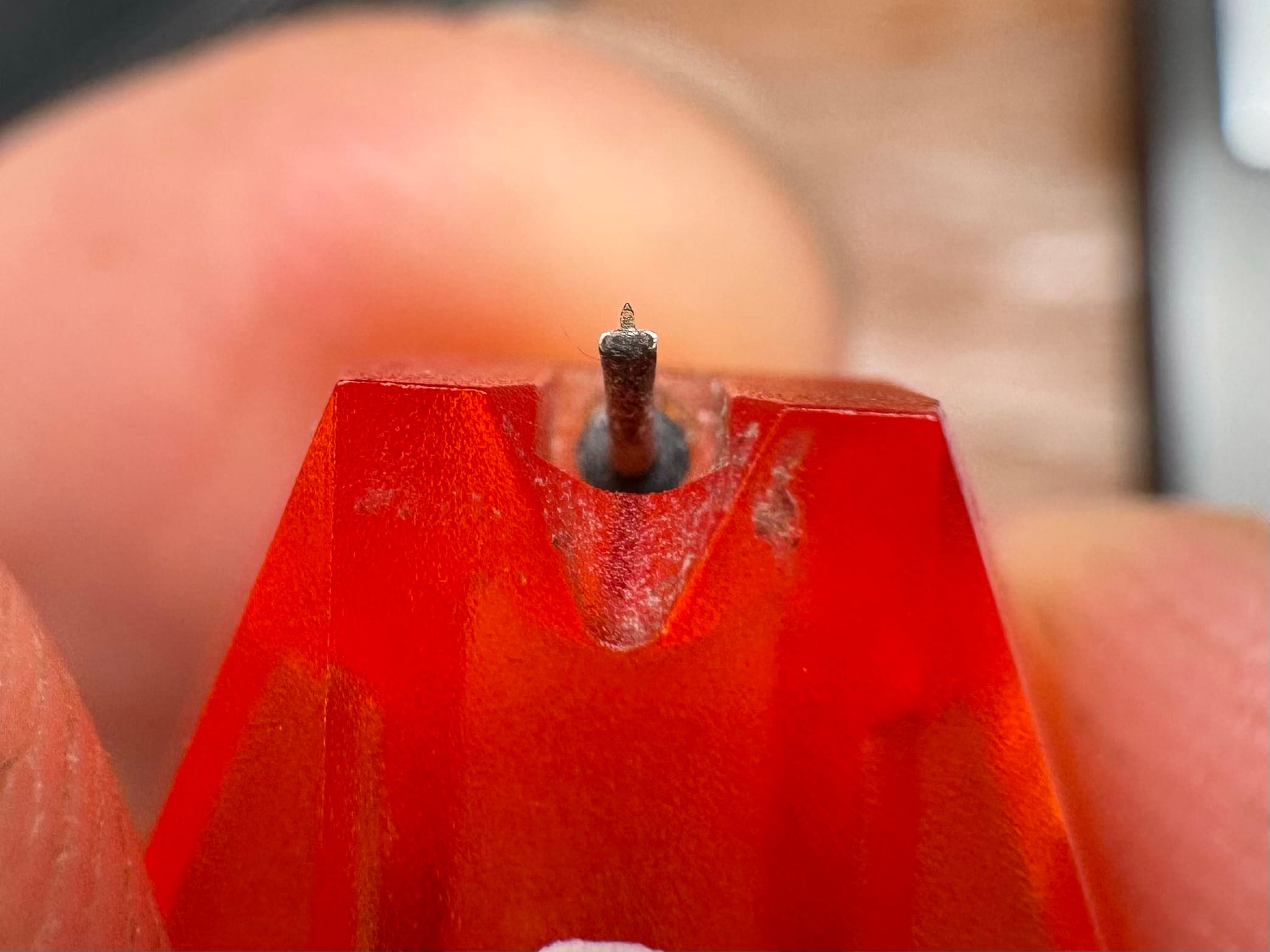
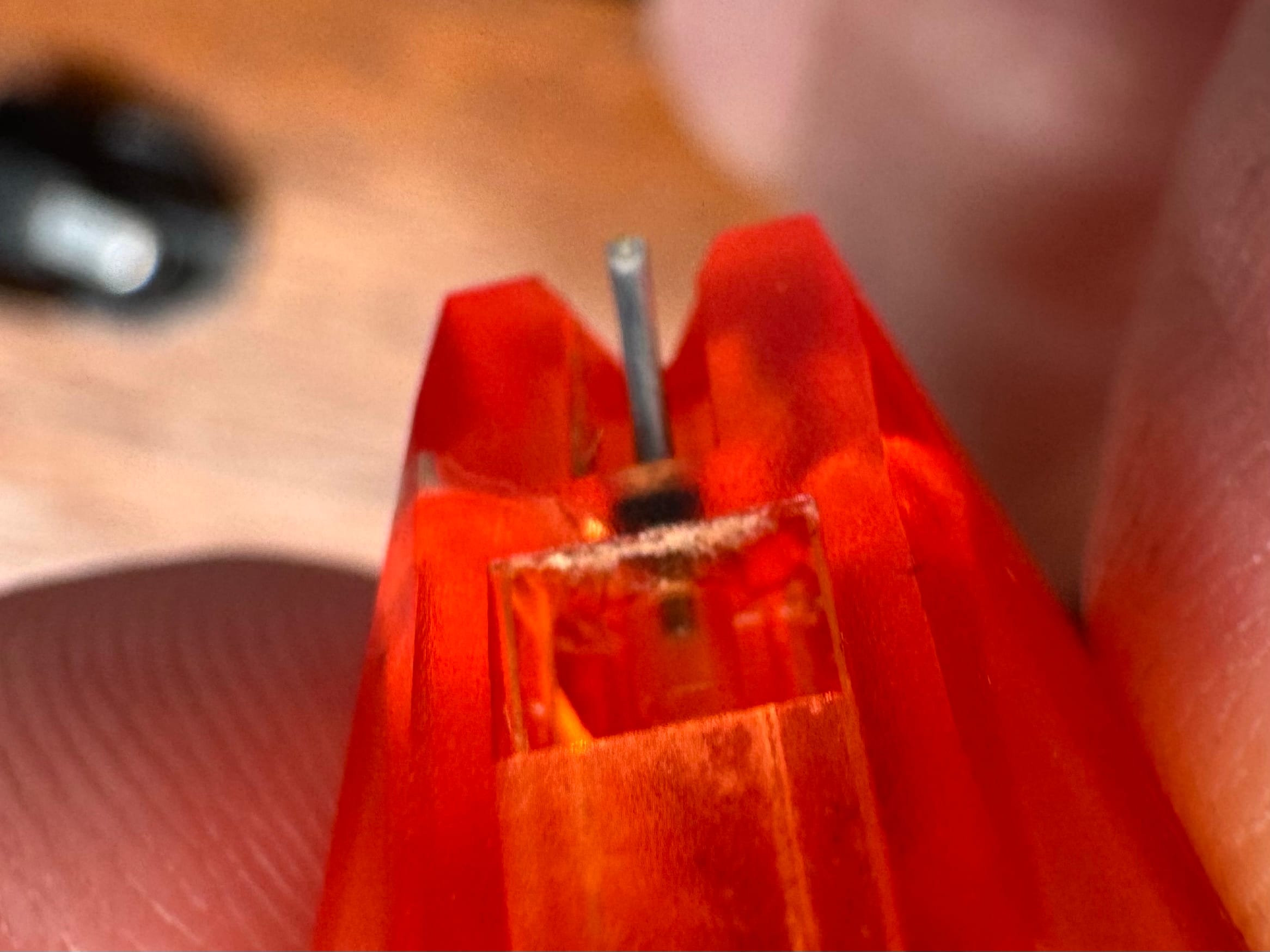
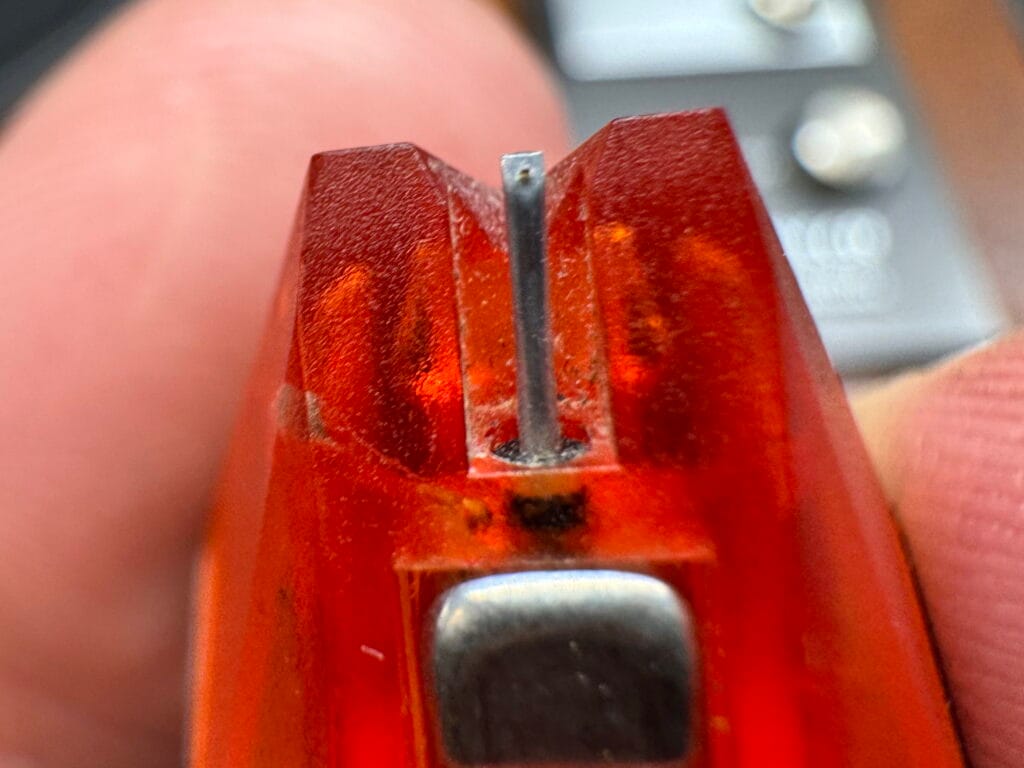
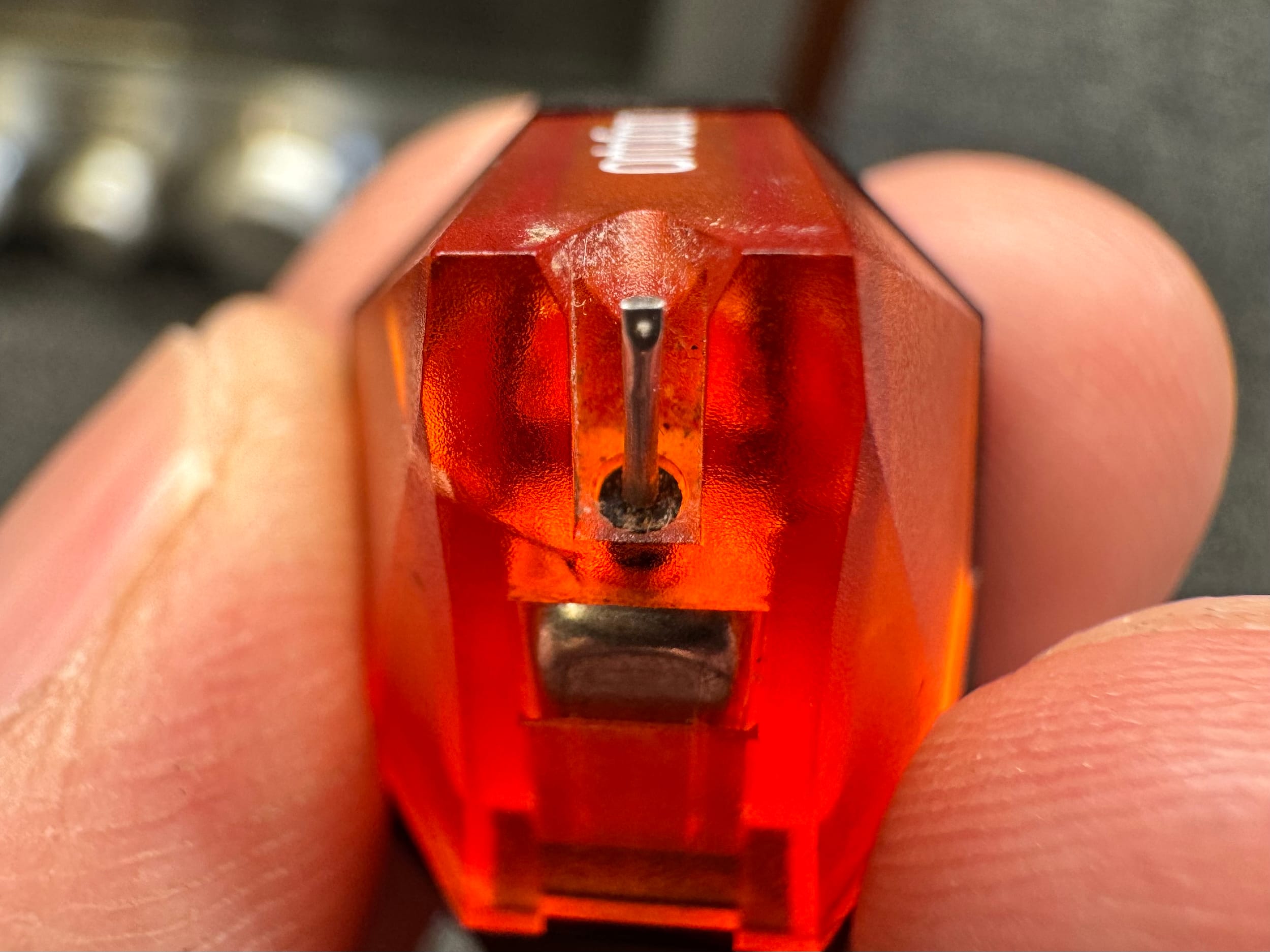
Moral
There is no doubt that legitimate sellers will list cartridges with “only 50 hours” use, and various other low hours numbers. Just know that near-new cartridges will look near-new – no surprises there. By and large though one should be extremely wary of these sorts of very low-hours claims.
Many sell cartridges that are damaged, with bent cantilevers, or with much higher than stated wear. They do this by obscuring details and many buyers lack the experience to know better. High-resolution inspection will, of course, tell the story. We offer this service, as do others. Just be careful and be sure to ask lots of questions, especially with much higher-priced “50-hour” carts!
Case 20 – Stunning Luxman 5L15 integrated amplifier dramas & great result
Welcome back friends and once again, we see a case involving our friend Mr RFW. Don’t ask me why this keeps happening, but I can say that there are many lovely, trusting people out there getting much less than they deserve. That being said, not all of these cases end badly and this is a classic case in point. I was able to rectify his mistakes and the amplifier runs beautifully once again. Winning.
I was asked to work on this amplifier as it had been to Mr RFW and the problems remained, despite large-scale parts replacement. This is a very common outcome when dealing with this repairer because, as I’ve said many times, shotgun parts replacement rarely solves a problem and only increases the risk of creating further problems. Such was the case here and it doesn’t matter how qualified the guy is or thinks he is, it’s only the work he does that matters.
Thankfully, my astute customer brought the amplifier here for attention. We were able to resolve the actual issues deep in the amplifier’s circuitry and restore normal operation, a great result.
More soon!
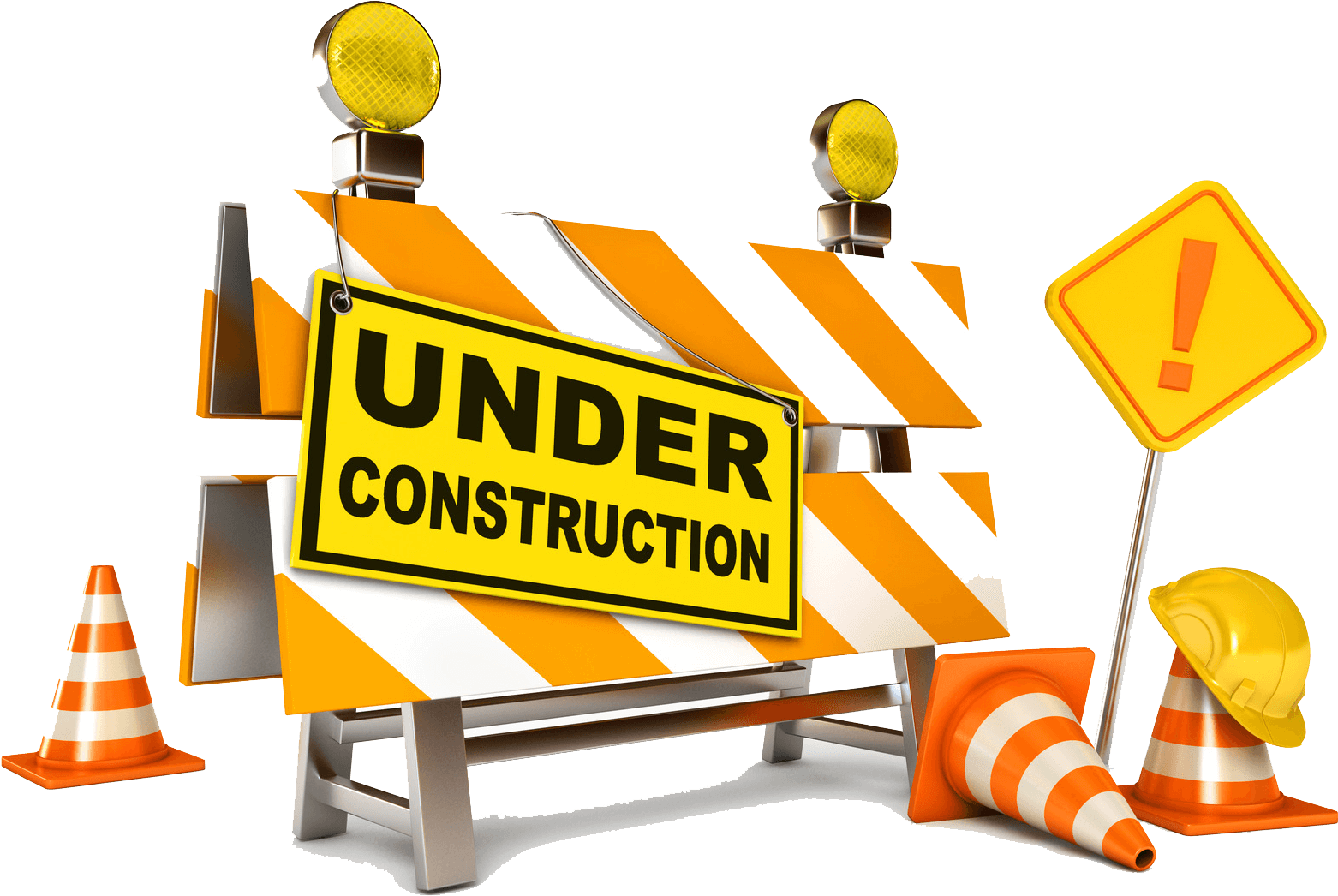
Case 19 – Gorgeous Sansui AU-505 integrated amplifier ruined
After writing about these HoS cases for 6+ years, a customer brought in a piece of equipment he’d had with one of the worst repeat offenders in the Hall of Shame, a Perth repairer, unfortunately, who seems to believe that a ‘qualification’ is all you need to become a proficient repairer. I told my customer this would probably be a bad one, but it was worse than even I expected.
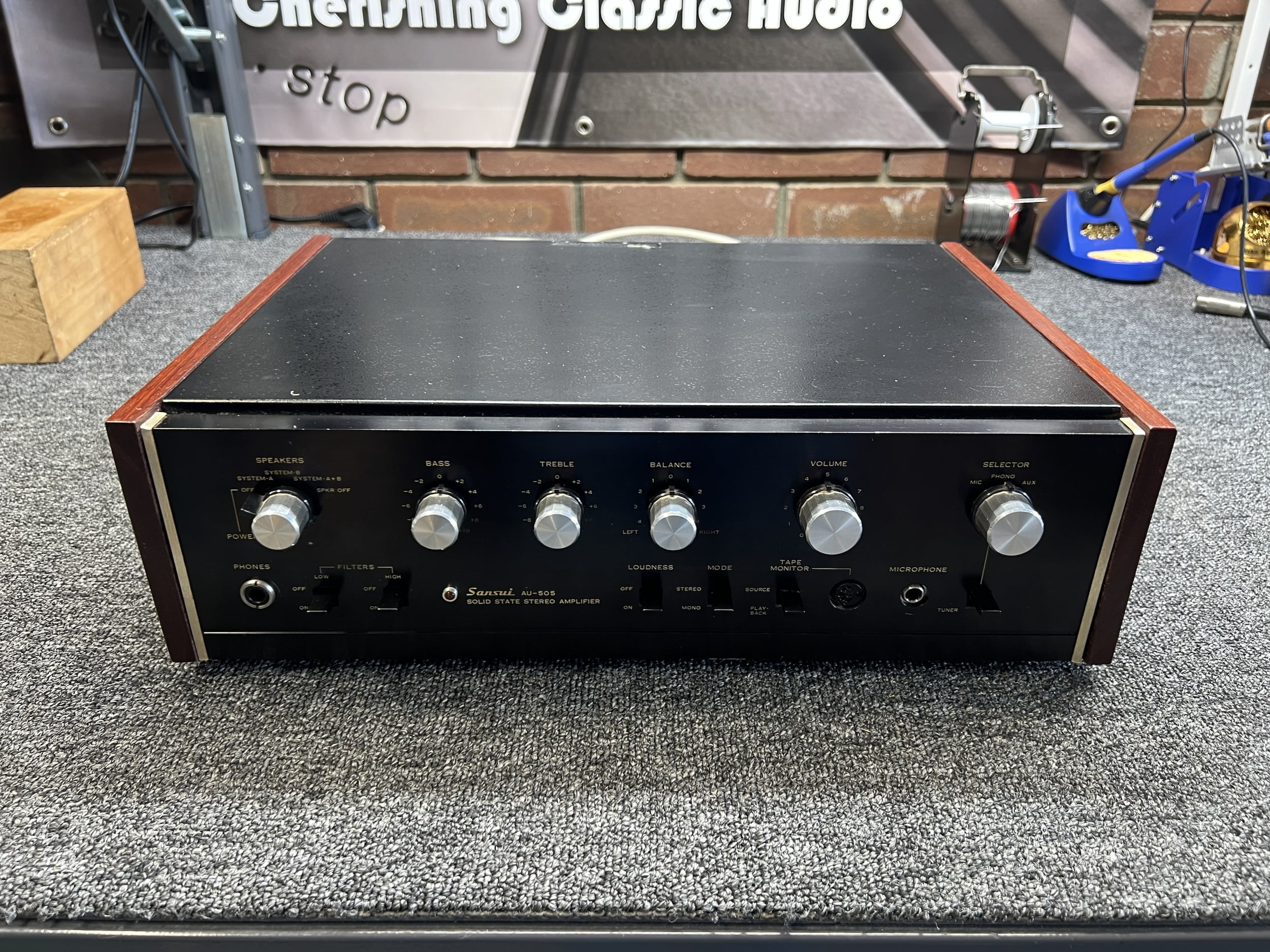
The Jig Is Up
It’s not the worst piece I’ve seen, but in terms of the needless and senseless destruction of a beautiful little amplifier through an utter lack of skill, it is. As far as I’m concerned, this amplifier has been ruined and encapsulates the problems this repairer brings to the hi-fi repair space.
Even fundamental concepts like complementary transistor pairs are beyond this person’s understanding. While we ponder that, just know that Mr RFW is responsible for cases 1, 10, 13, 14, 18, 19 and 20, and many more I haven’t bothered to write up.
Worst of all, after leaving a bad review, this customer was attacked by Mr RFW, as was the repairer who ultimately agreed to fix the amplifier, which wasn’t me BTW. Mr RFW insinuated in his reply to the bad review that the repairer had charged $550 to inspect the amplifier which is of course complete nonsense.
An Important Message
We need to stop this individual from destroying hi-fi equipment but I can’t do it on my own, or with the help of a couple of brave customers. Effective immediately, my new policy regarding customers who do business with or support RFW:
Regrettably, I can no longer offer service and support to folks who engage or recommend this individual whilst cognisant of the overwhelming evidence I’ve documented below. People engaging this business are contributing to the problem and helping to create more victims. Thanks for your support.
Justifications
Here are some of the justifications I’ve heard concerning this business, and my responses:
“But he’s trying.”
Irrelevant.
“But he’s cheap.”
This is why he’s still in business. You get what you pay for.
“But he’s popular.”
So is McDonald’s.
“But he’s providing an alternative when other repairers are busy.”
Yes, a terrible, low-quality alternative.
“But he works for a mining company.”
Irrelevant. He doesn’t even have a university degree!
“But he’s a nice guy.”
Not from what I’ve seen, your milage may vary.
“But my equipment works well.”
Does it? Are you sure about that? You’ve measured it or had a third party inspect it..?
“But he didn’t damage my equipment.”
Didn’t he? You’re sure about that and are able to demonstrate this? All the pieces I’ve inspected that he’s worked on have been damaged and devalued.
At least one owner has stood up to be counted though and that case was heard in court in March 2024. I’ve been involved in that one, taking photos and viewing the damaged equipment firsthand, helping my colleague identify the issues. UPDATE: Mr RFW LOST THAT CASE!
That’s how it was with this latest amplifier, the owner is a lovely guy and trusts that the work he is paying for is being done correctly. But it isn’t and he knows that now. Let’s take a look at this beautiful Sansui AU-505.
Note: I generally refuse to touch equipment like this that’s been damaged by RFW. I inspected the equipment, wrote a condition report for my customer and promised to resolve the dead channel for him which I did.
Mr RFW doesn’t like that I inspect equipment he’s worked on. I wonder why that might be..? He blames the messenger. I blame the perpetrator.
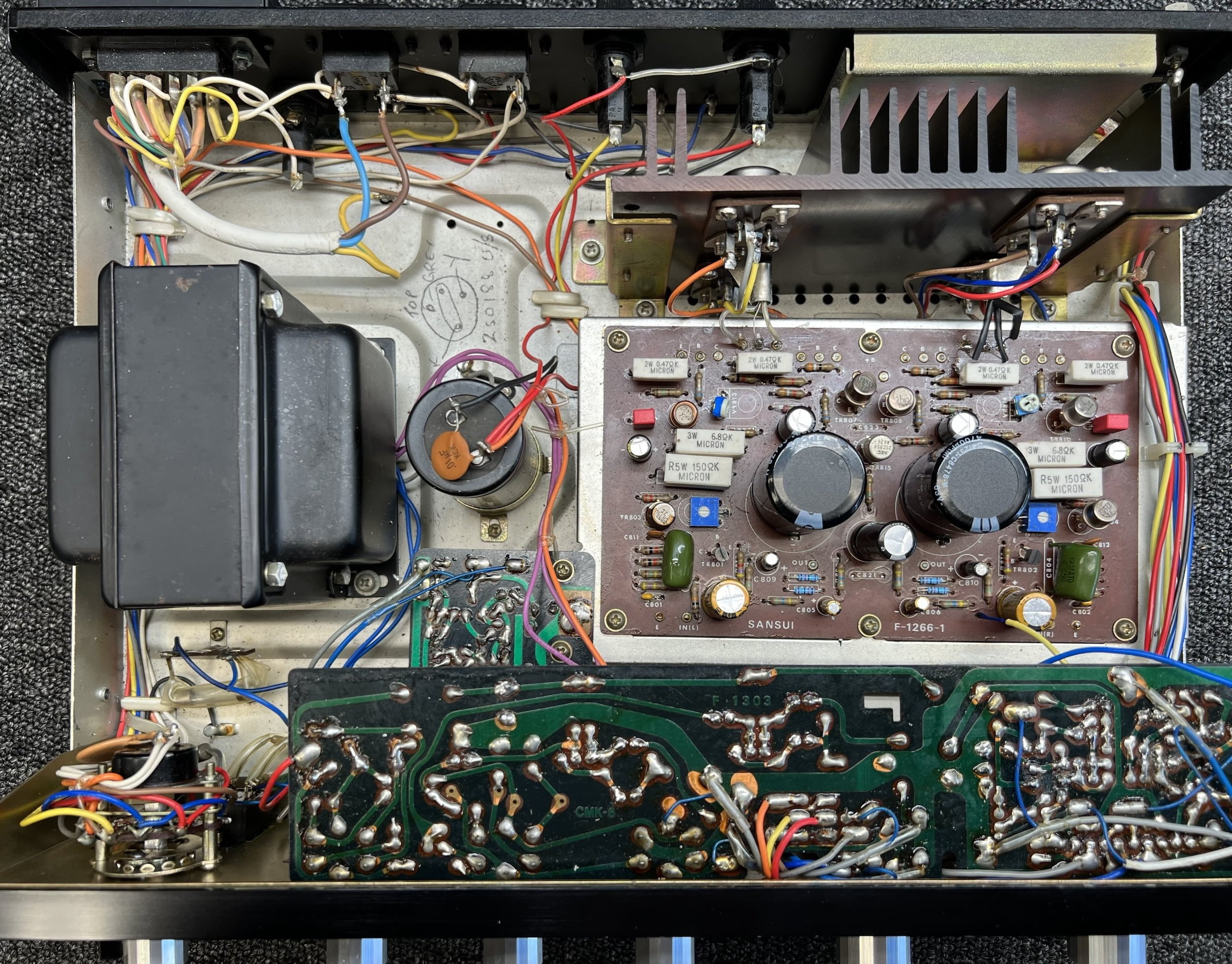
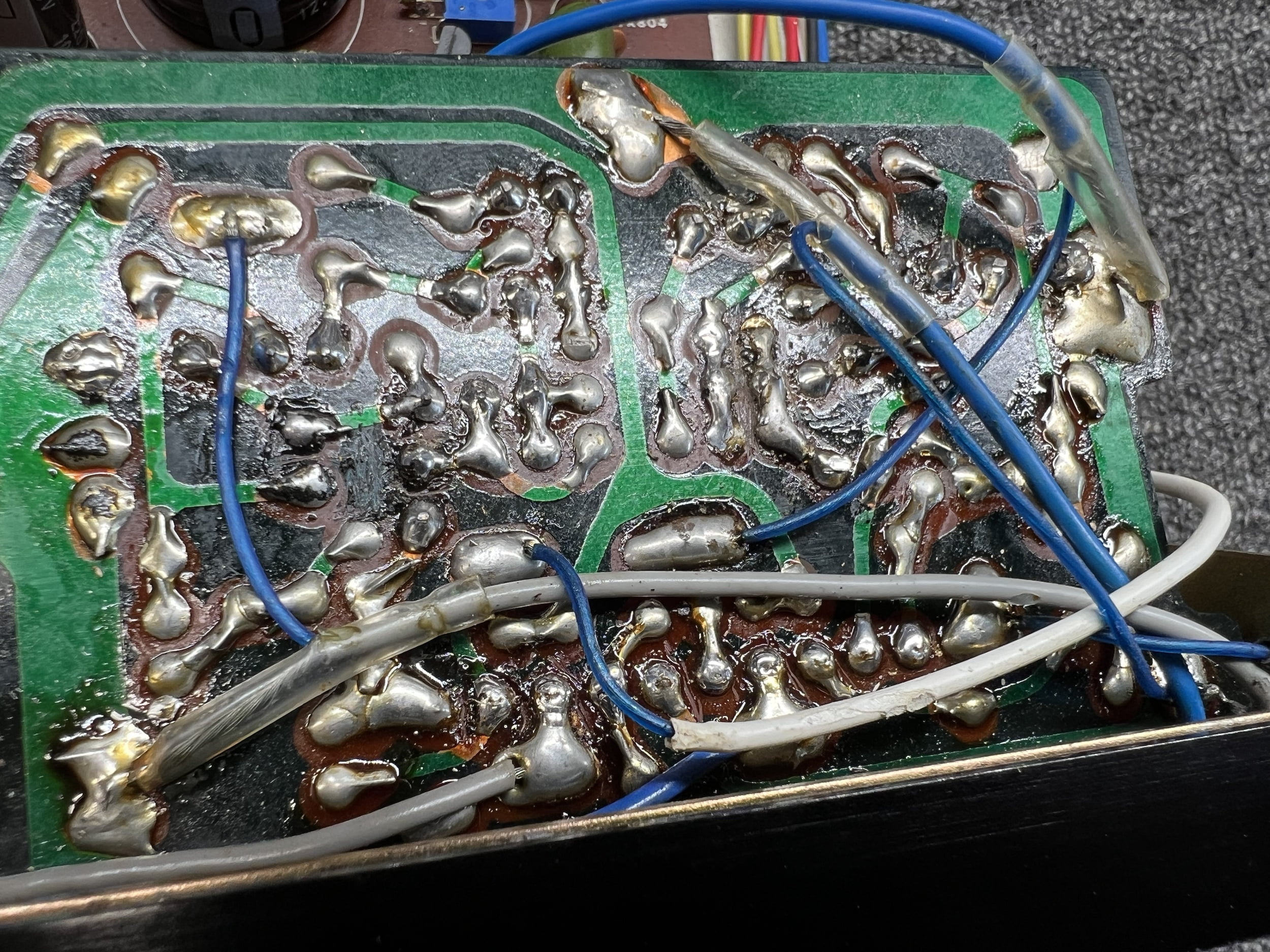
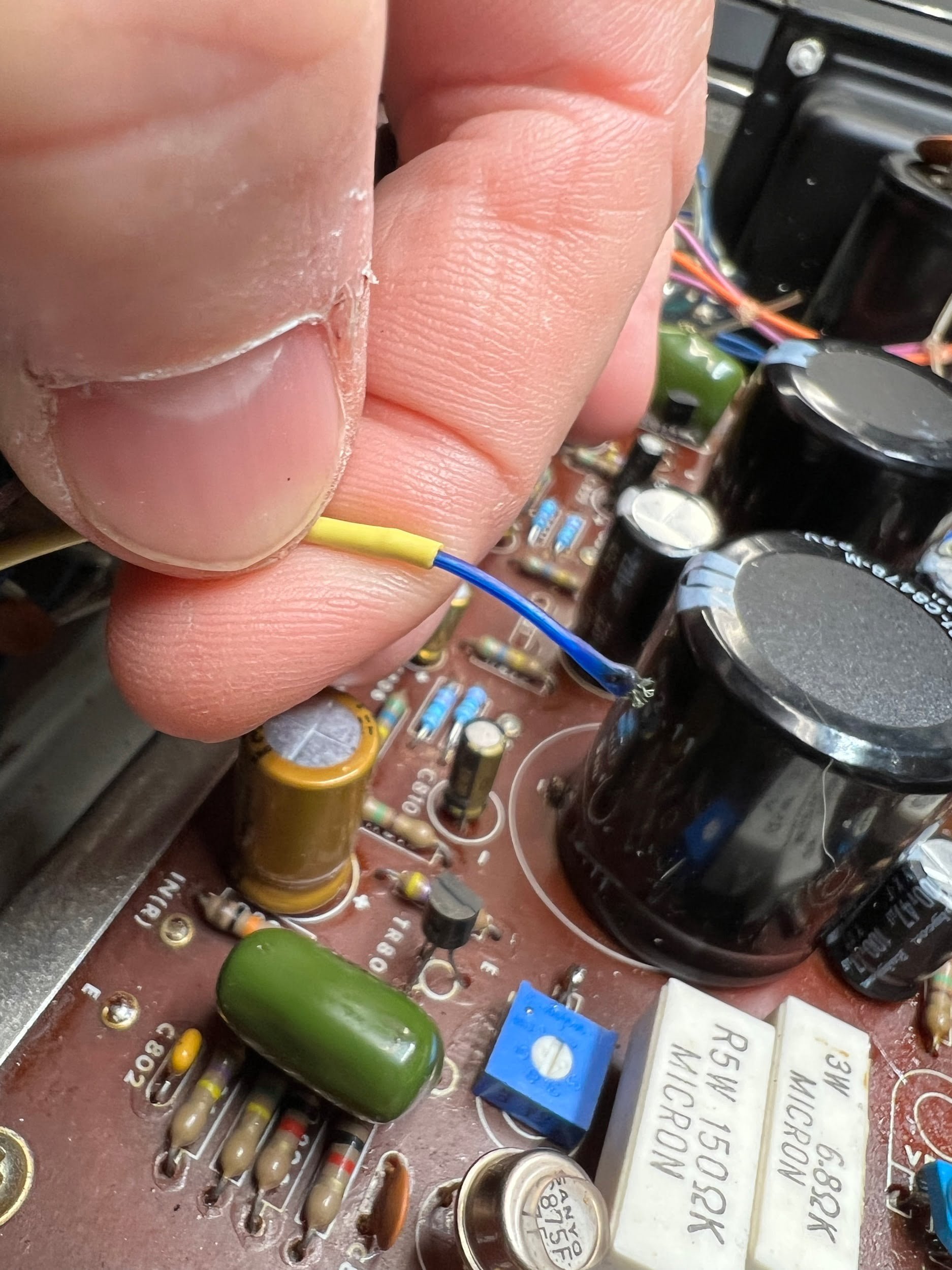
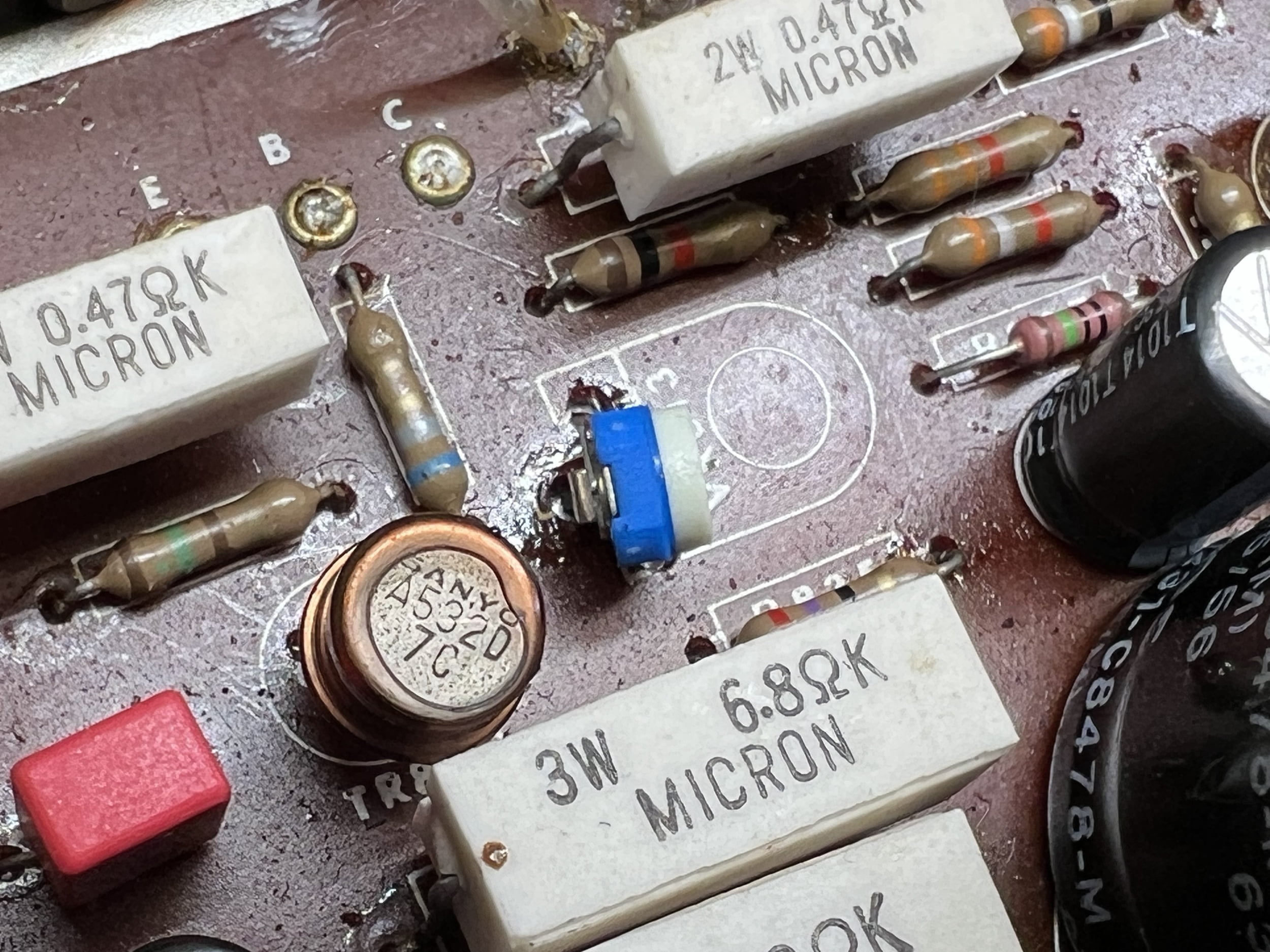
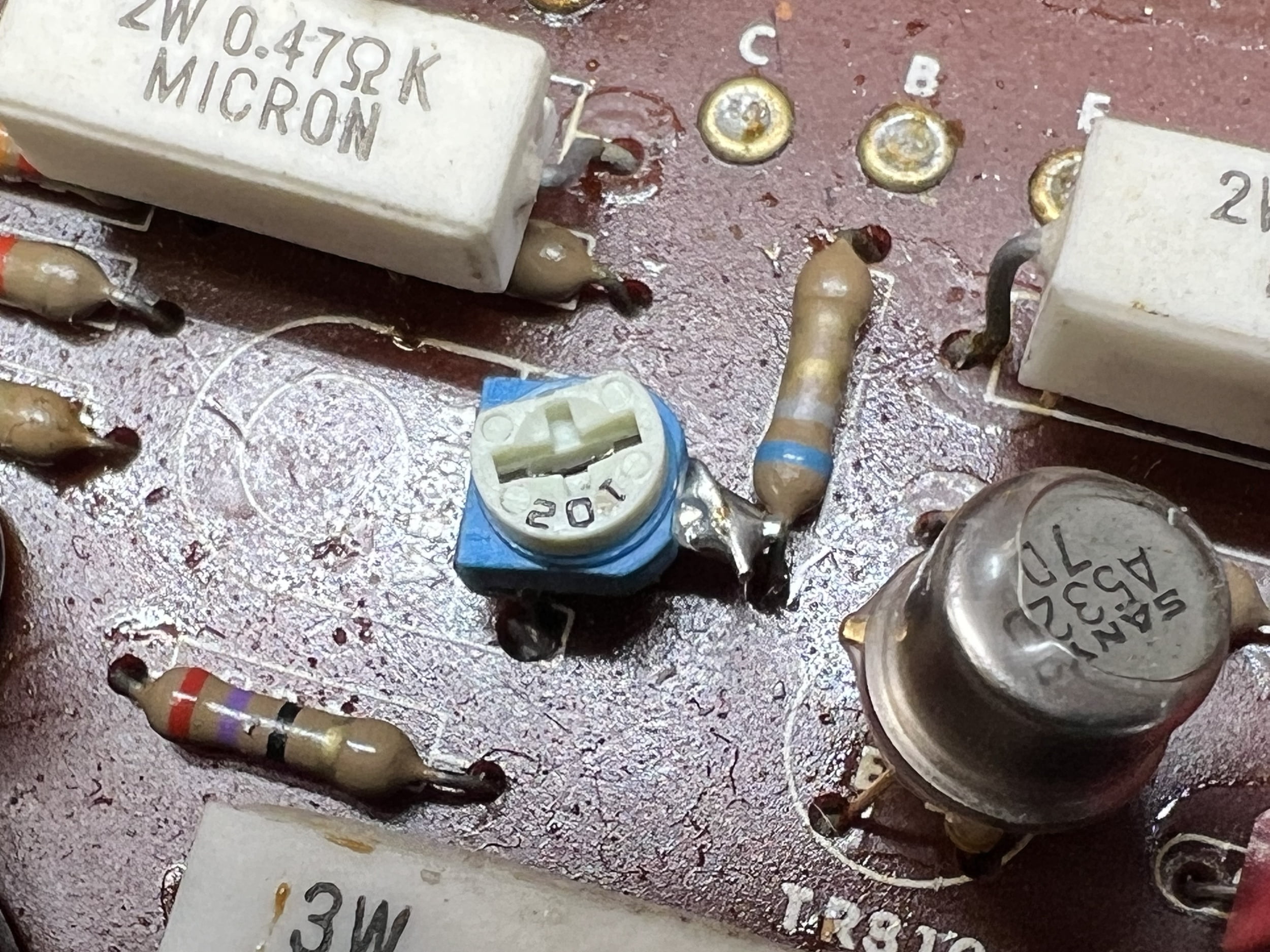
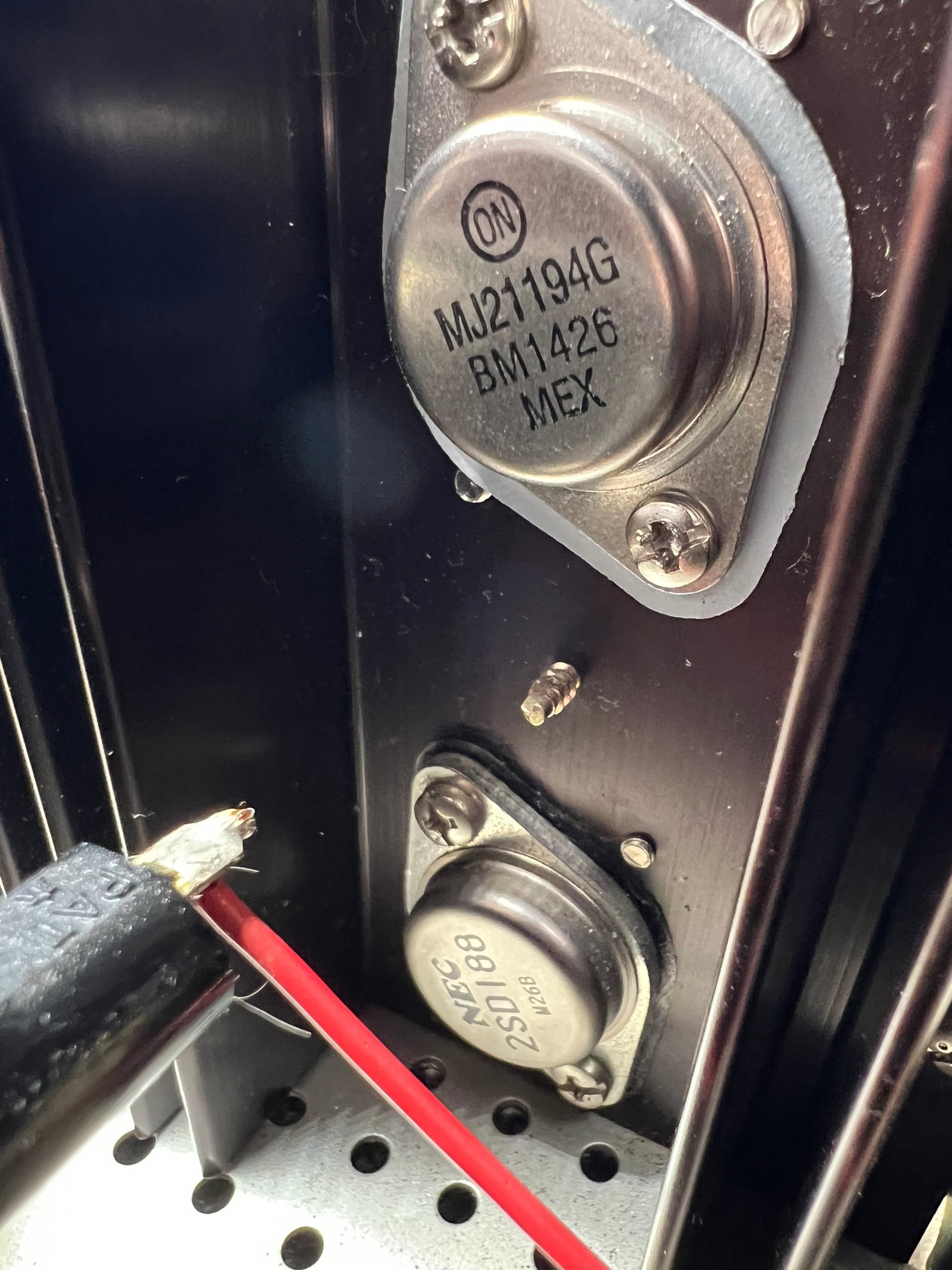
Alright, so one question I’m often asked is: “Mike, how can you tell Mr RFW did this? Easy. His initials are watermarked on this image and my customer told me who did this anyway, he took the amplifier there! Everyone has a signature though and his work always looks like this. By “like this” I mean precisely like this. It’s like handwriting.
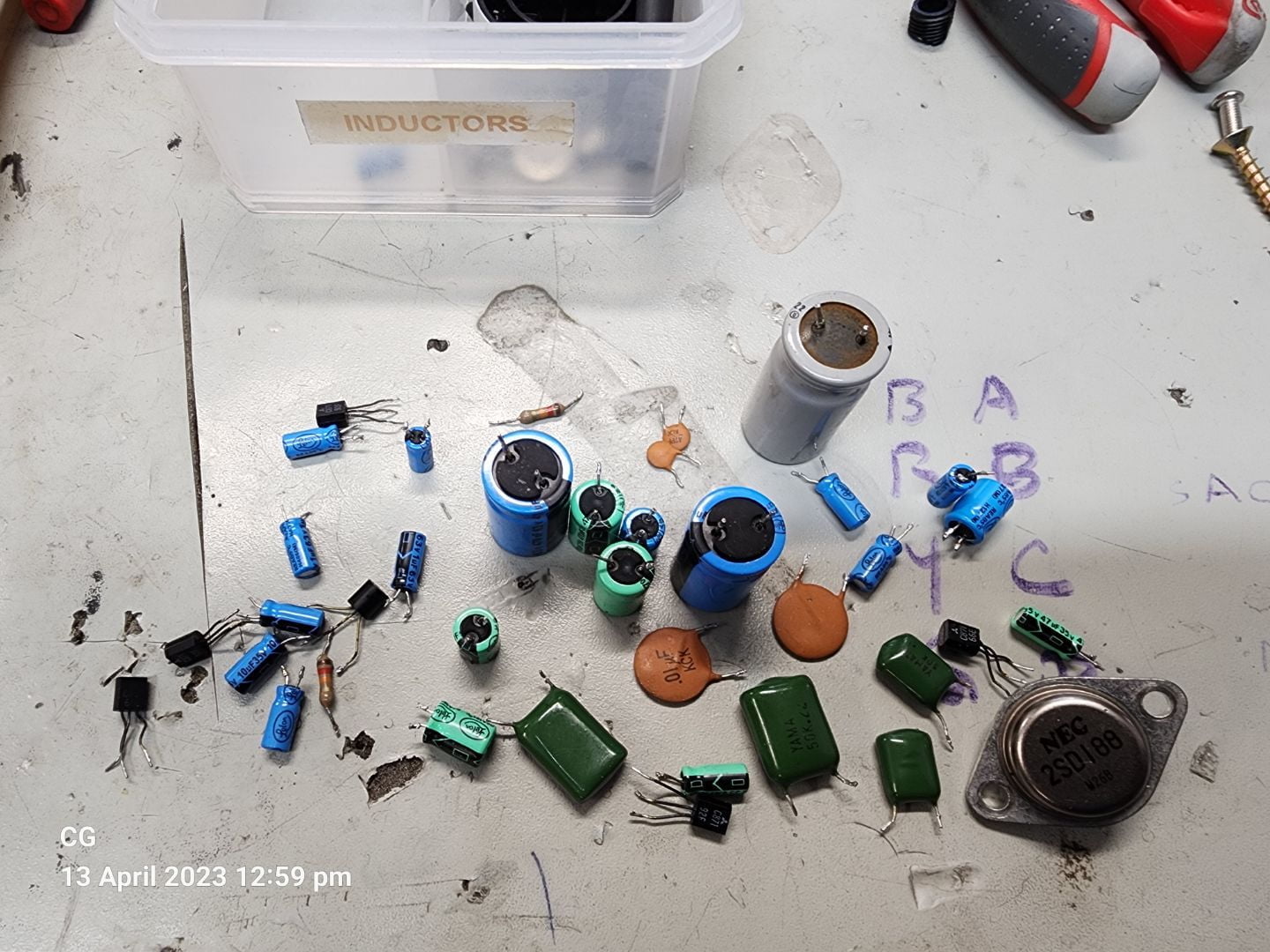
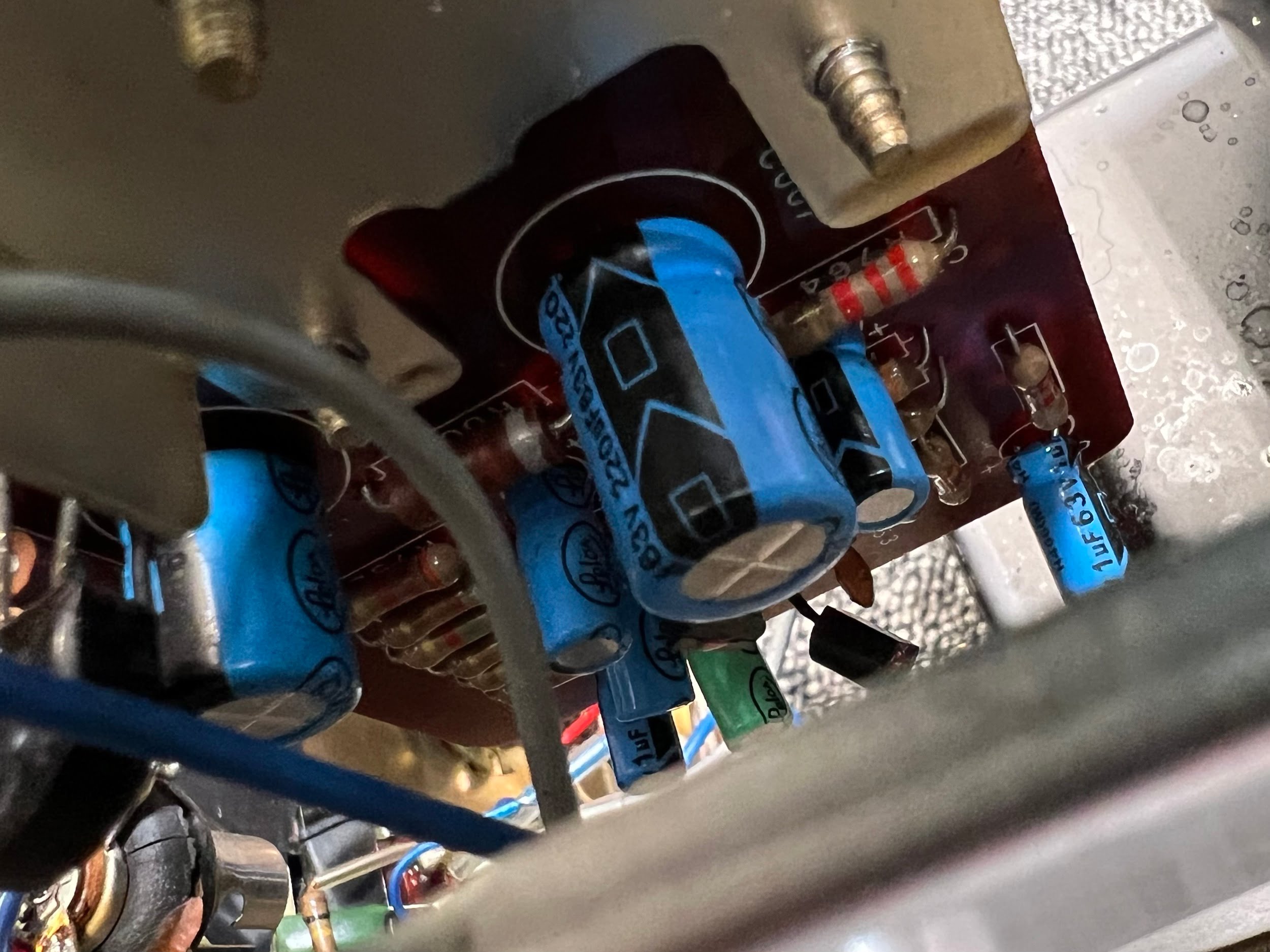
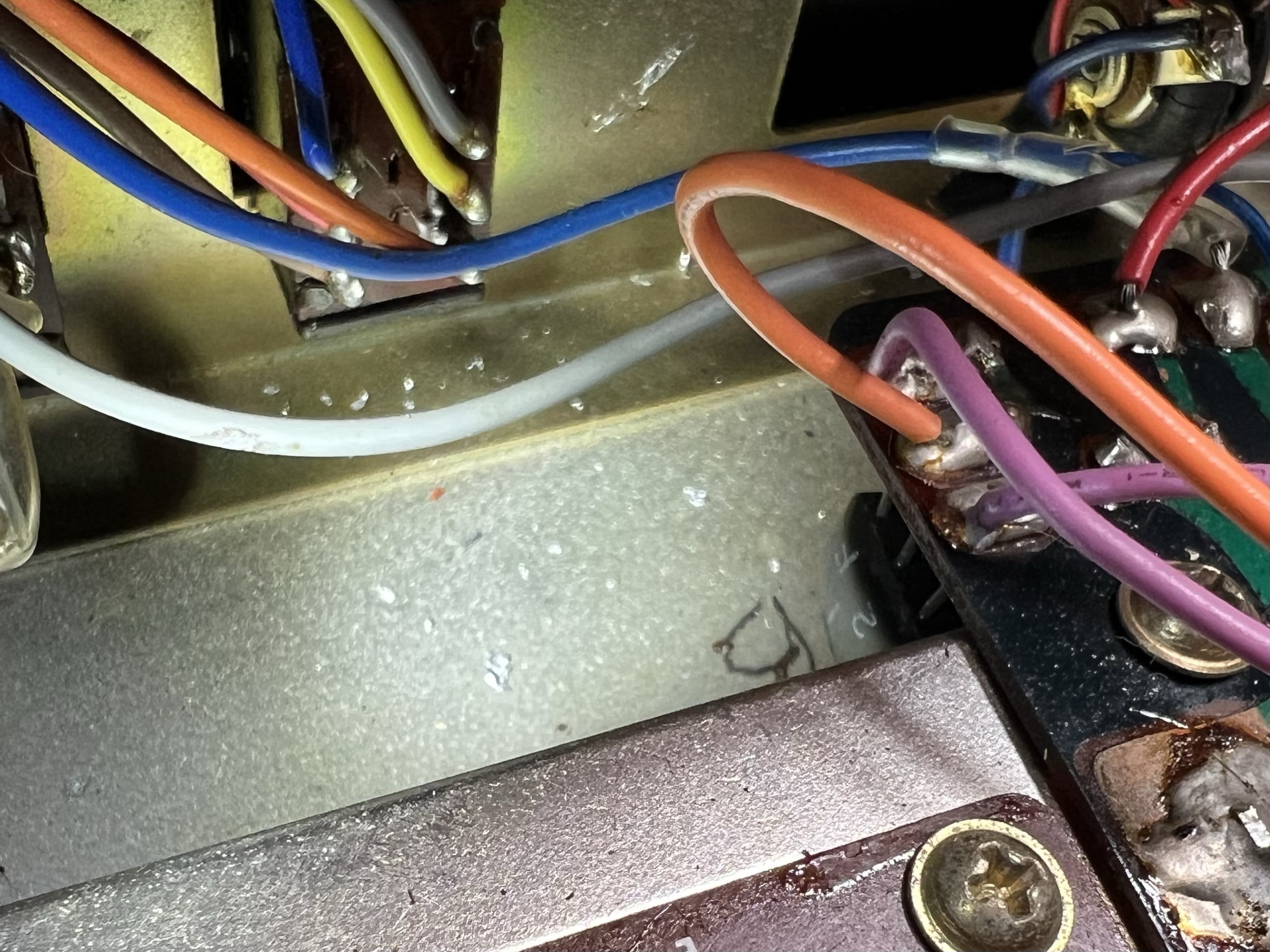
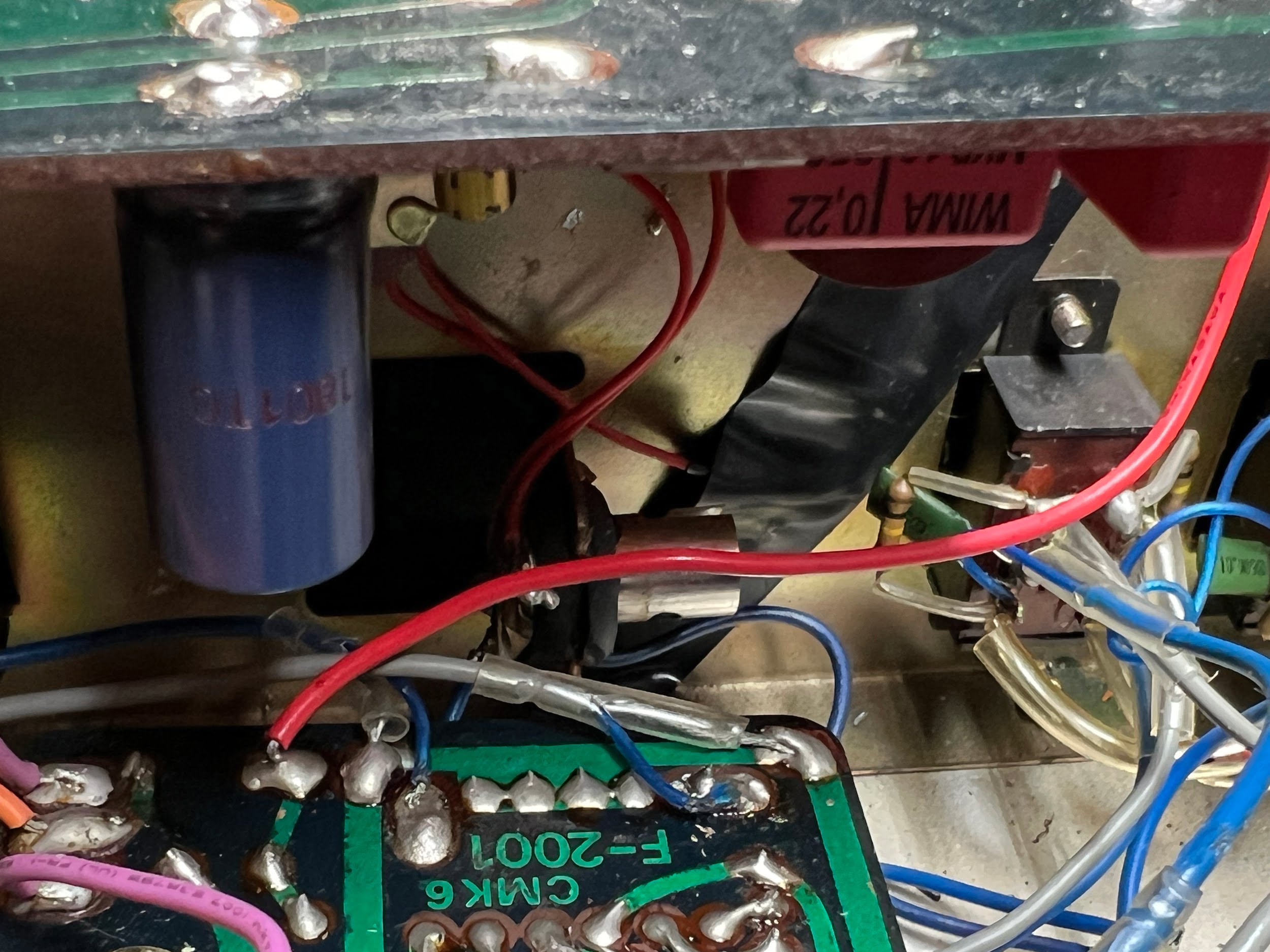
But Mike, he’s using WIMA capacitors like I’ve seen you do!
Someone, somewhere
Yes, I’d noticed, though there’s not much point if this is the price you pay for it:
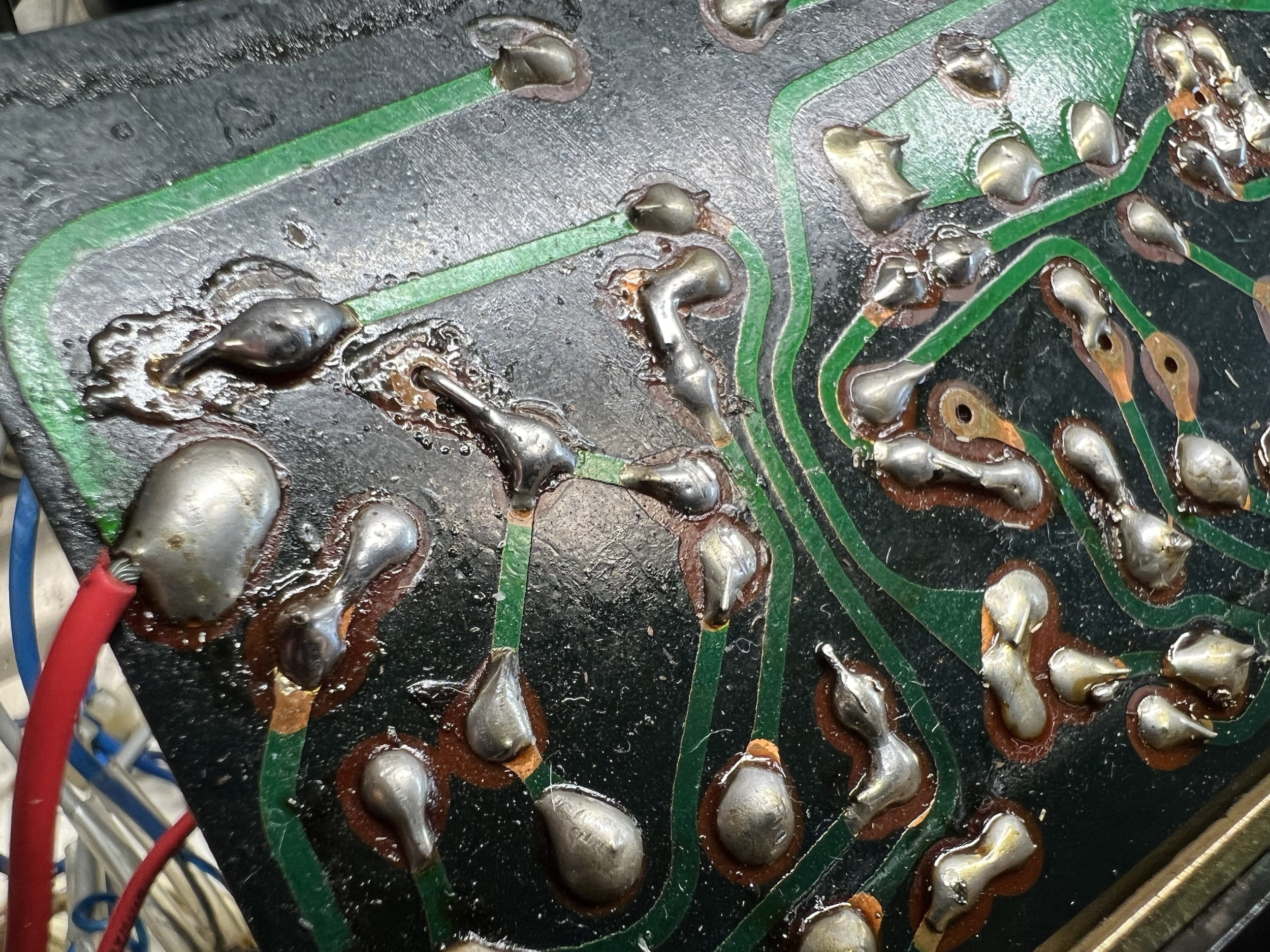
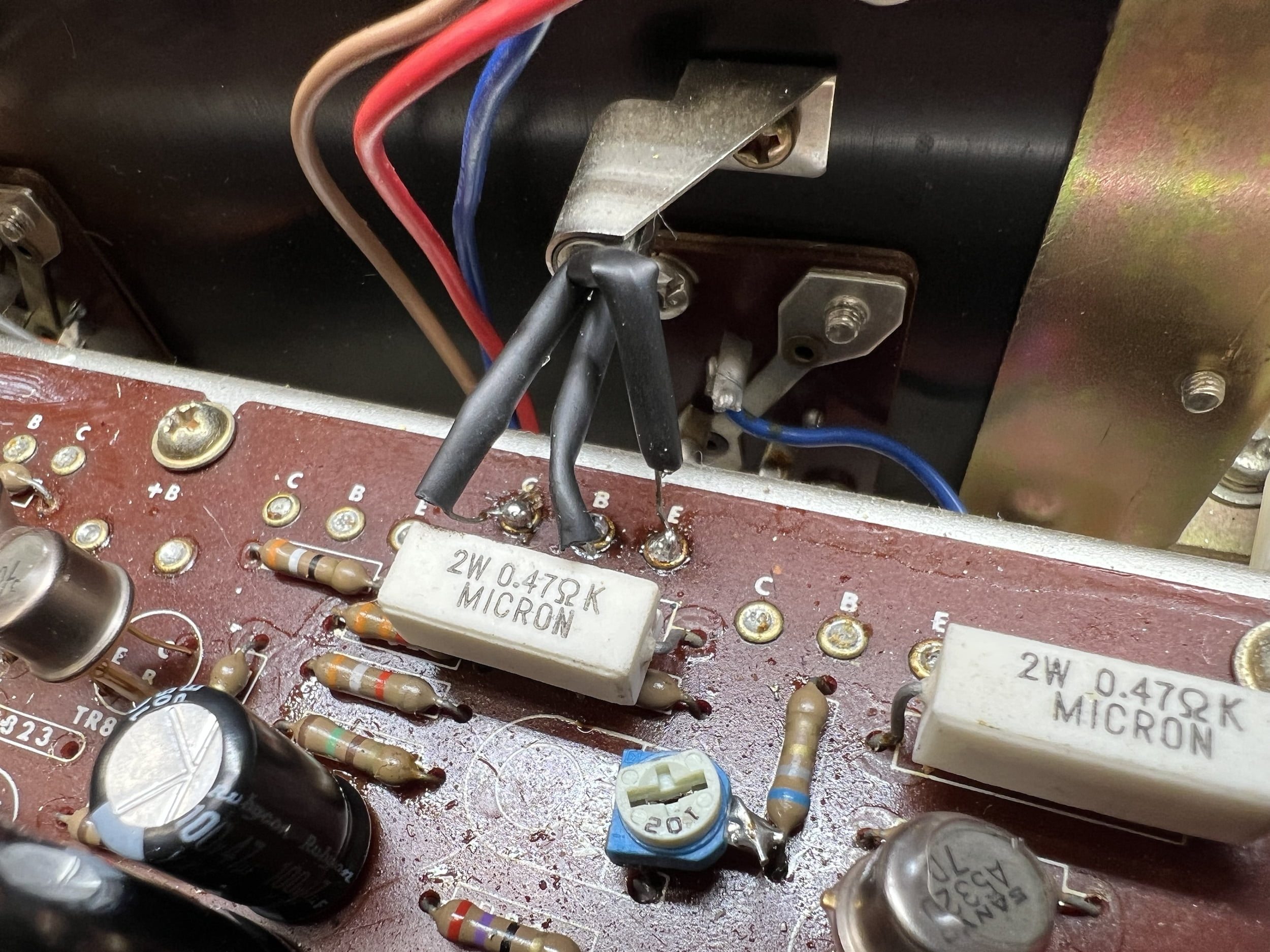
Takeaways
This lovely little Sansui AU-505 at the very least, now needs extensive remedial work beyond its modest value. This is the perfect example of someone taking a good amplifier needing minor repair and killing it with ill-judged, unnecessary and poorly executed work. It’s so unnecessary and wasteful and I look forward to a time when we see less of this.
There is certainly a place for well-executed restorative work on hi-fi equipment and I’ve tried to showcase that in my work over the years. I recommend restoration in cases where it’s warranted and worthwhile, but note that restoration isn’t “Outback Jack’s Sansui modifications”. The best approach is always a conservative, technically informed one, focused on preserving equipment rather than harming it.
This customer has requested a refund and I hope he receives it. He left a justified, negative Google review which as I said drew the ire of Mr RFW. This alone tells you everything you need to know about this repairer. Don’t say you haven’t been warned!
Case 18 – Beautiful Kenwood KA-9150 integrated amplifier ruined
Some of the repairers featured here in the Hall of Shame stand out as repeat offenders, none more so than our friend Mr RFW featured in this case, and many others here, including cases 1, 10, 13, 14, and now this one.
I know what you’re wondering and it’s the same thing that crosses my mind every time a piece of equipment visits my workshop, having been to him first: how does this technician remain in business?! I honestly don’t know, but it’s a combination of:
- Misrepresentation of ability and results
- The promise of cheap work
- Most owners are unable to tell the difference between good and bad work and never look inside their equipment
- Most aggrieved owners don’t follow up
- Some aggrieved customers are convinced to remove bad reviews, possibly by the promise of refunds
Coming soon!
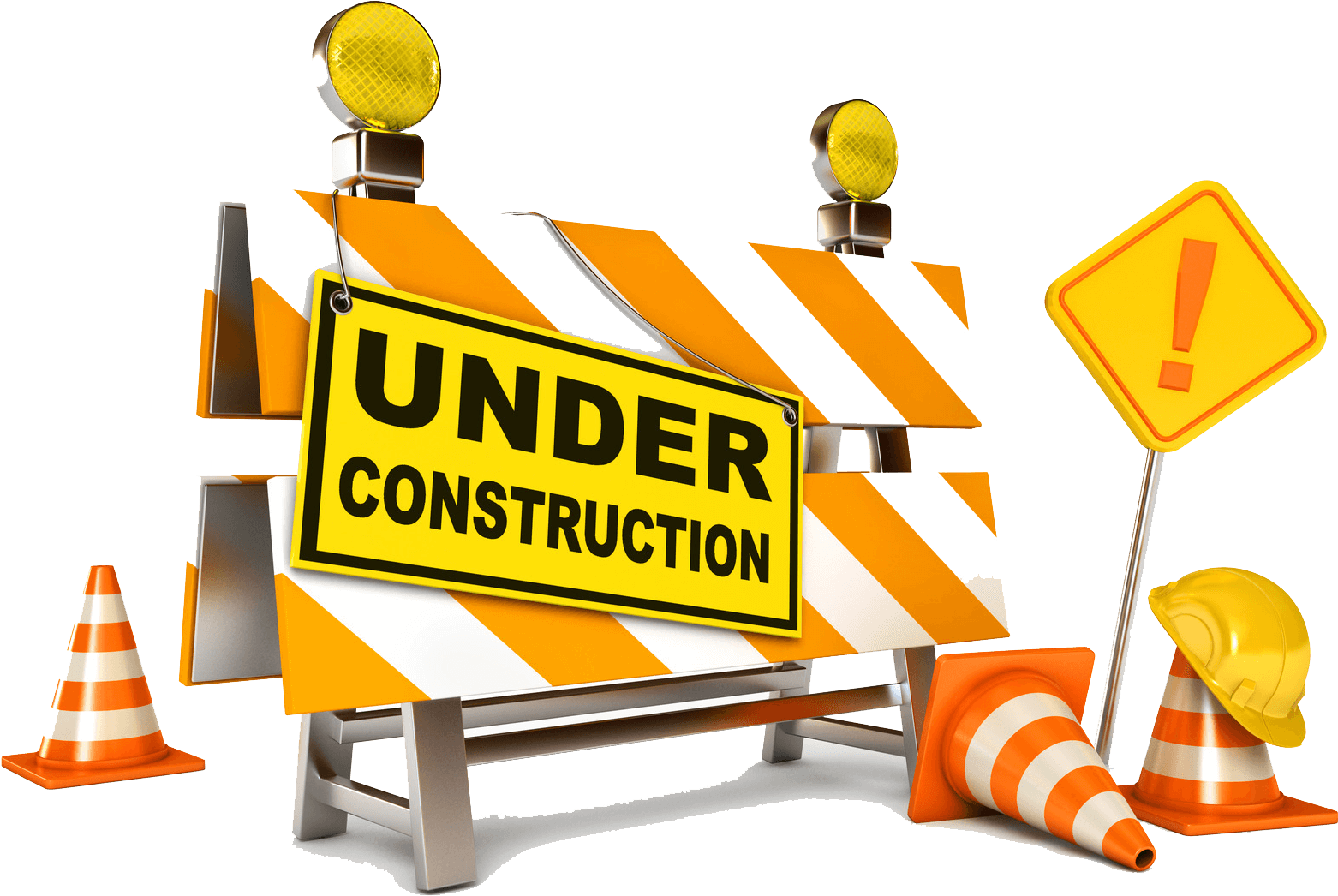
Case 17 – Marantz 2270 receiver bodges – Frampton Strikes Again!
This is another sad one, yet typical of what I see, day-to-day. The unfortunate reality is that several ‘specialist’ workshops take on equipment with little to no understanding of what makes it run well or what precision workmanship actually looks like. These folks typically fail to do anything of value and instead, usually damage and devalue the equipment they work on.
This is most egregious when these people pretend to be gurus, like our old friend and “soldering teacher” Mr ‘Frampton’ (not his real name, but with only one letter changed!) from the ACT. Frampton is responsible for case #4 – quite literally the single worst case of butchery I’ve ever seen, and many others I’ve not documented. Mr Frampton added his trademarks of terrible soldering, poor parts placement and avoidable board damage to this beautiful Marantz 2270 receiver.
I thought I recognised the work inside this beautiful piece and when I asked the owner ‘whodunnit’ he told me it was the man himself. Frampton also told my customer he “taught soldering”, something that has come up before. One can only pity his students and equipment owners like this one, who were duped by the BS. Anyway, let’s take a look, I’ll explain the issues as we go.
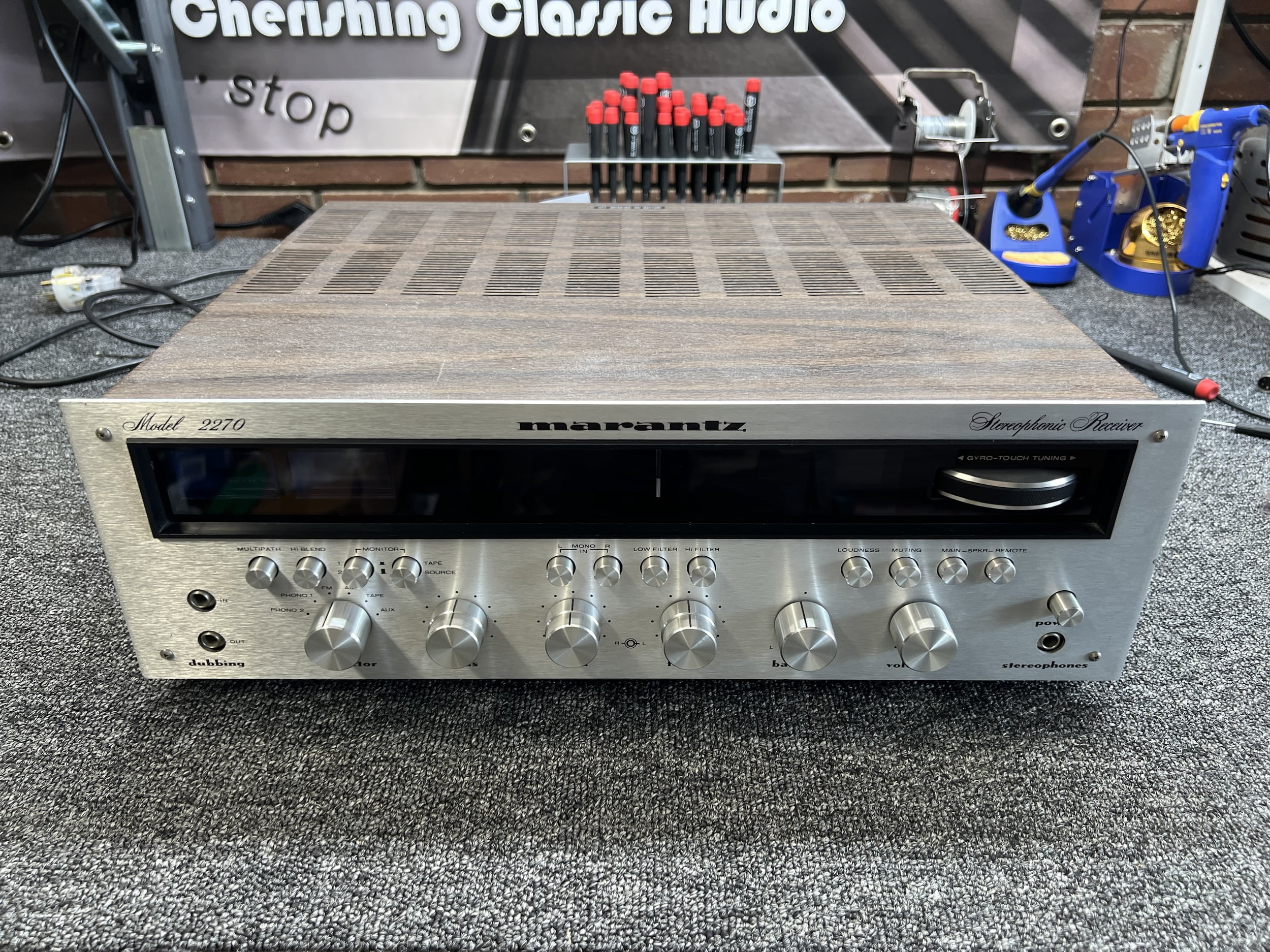
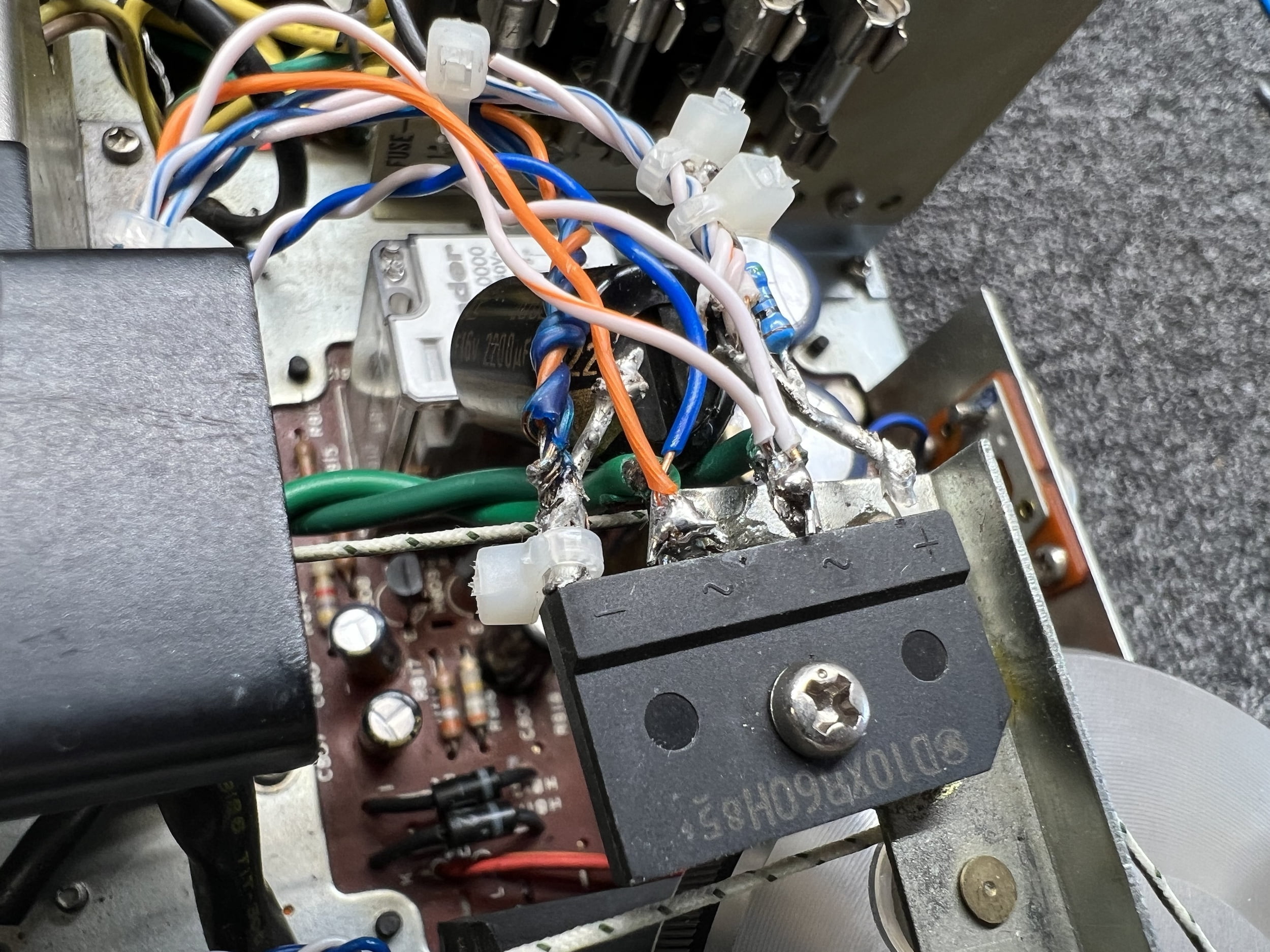
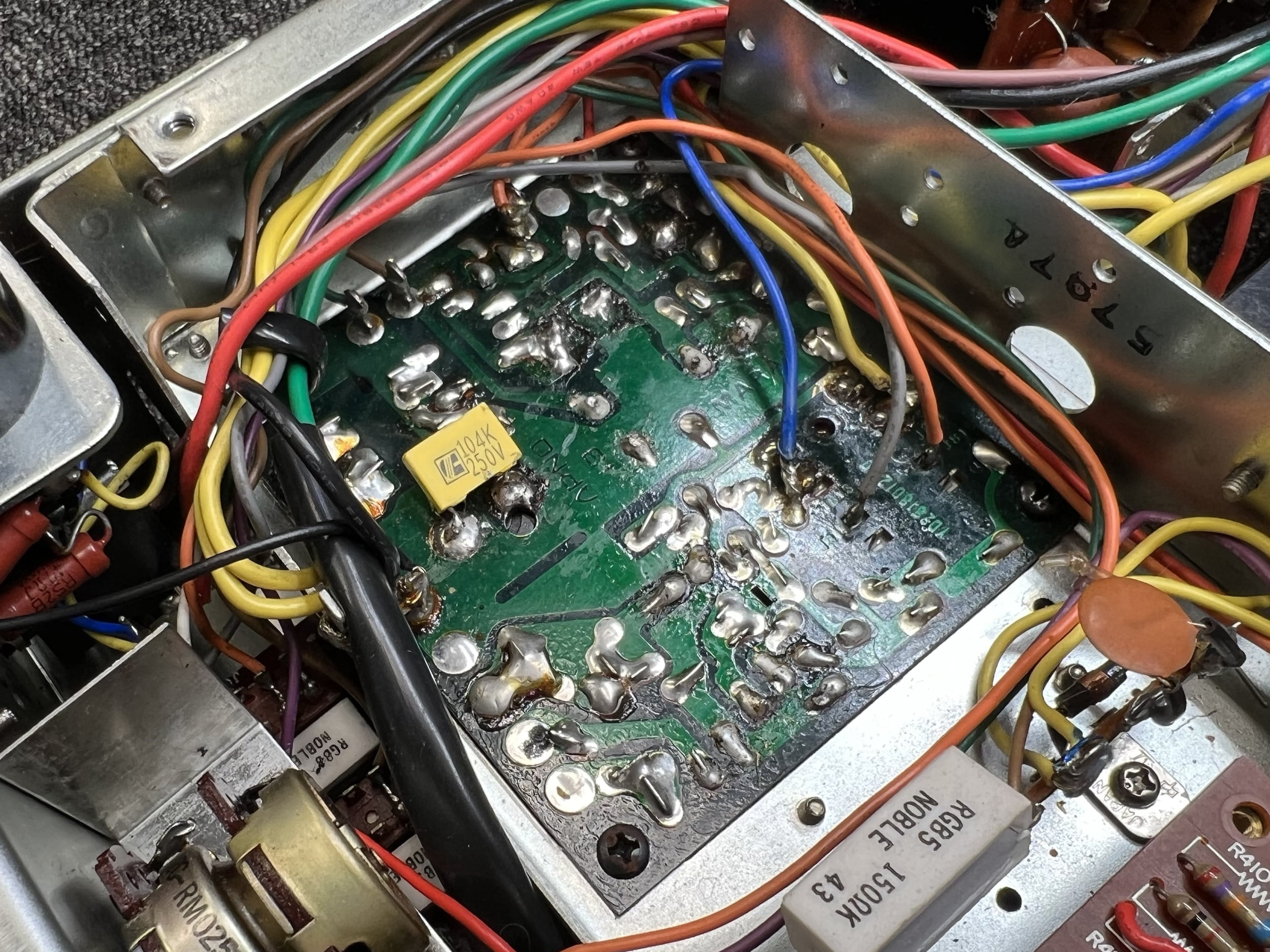
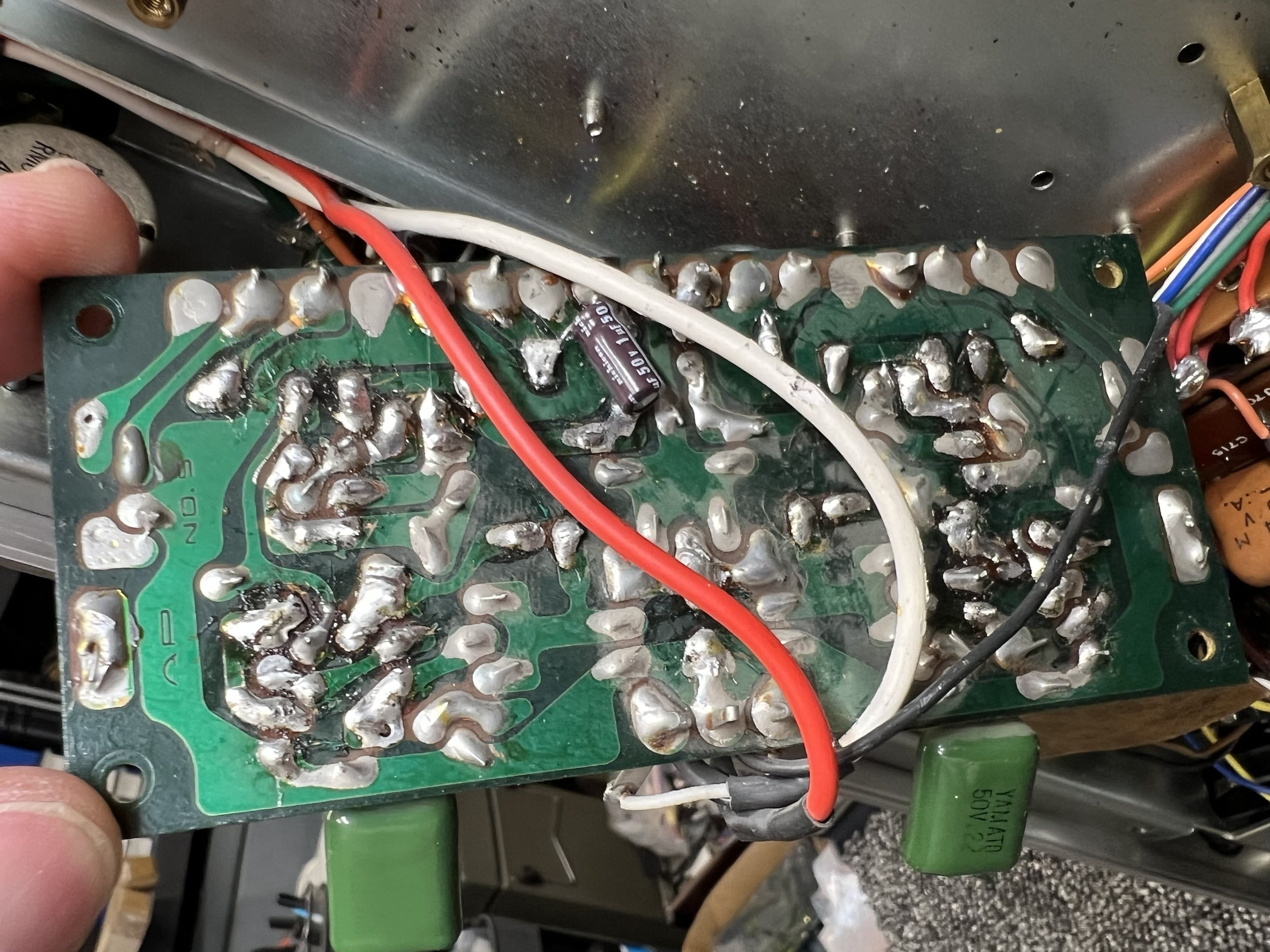
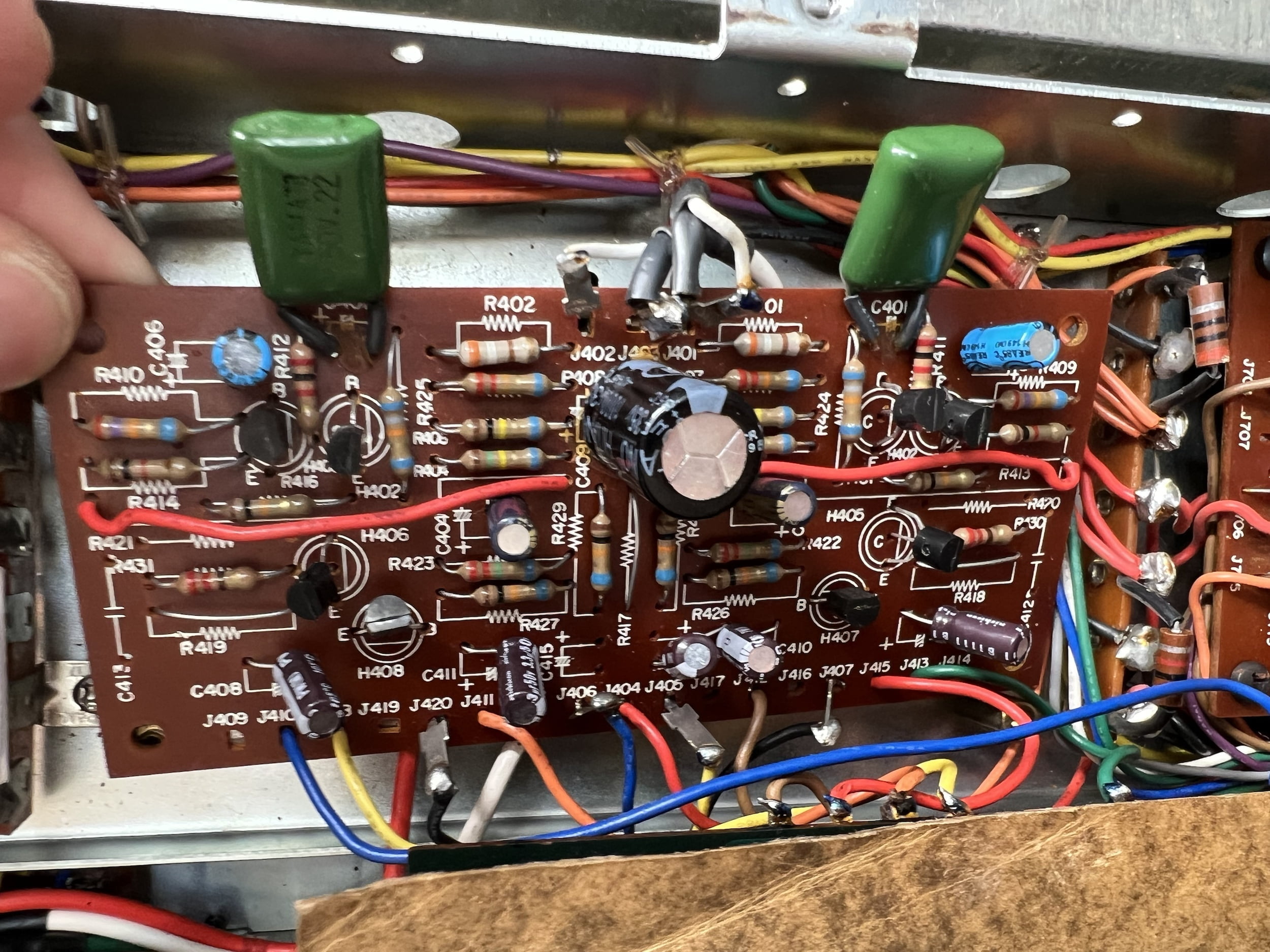
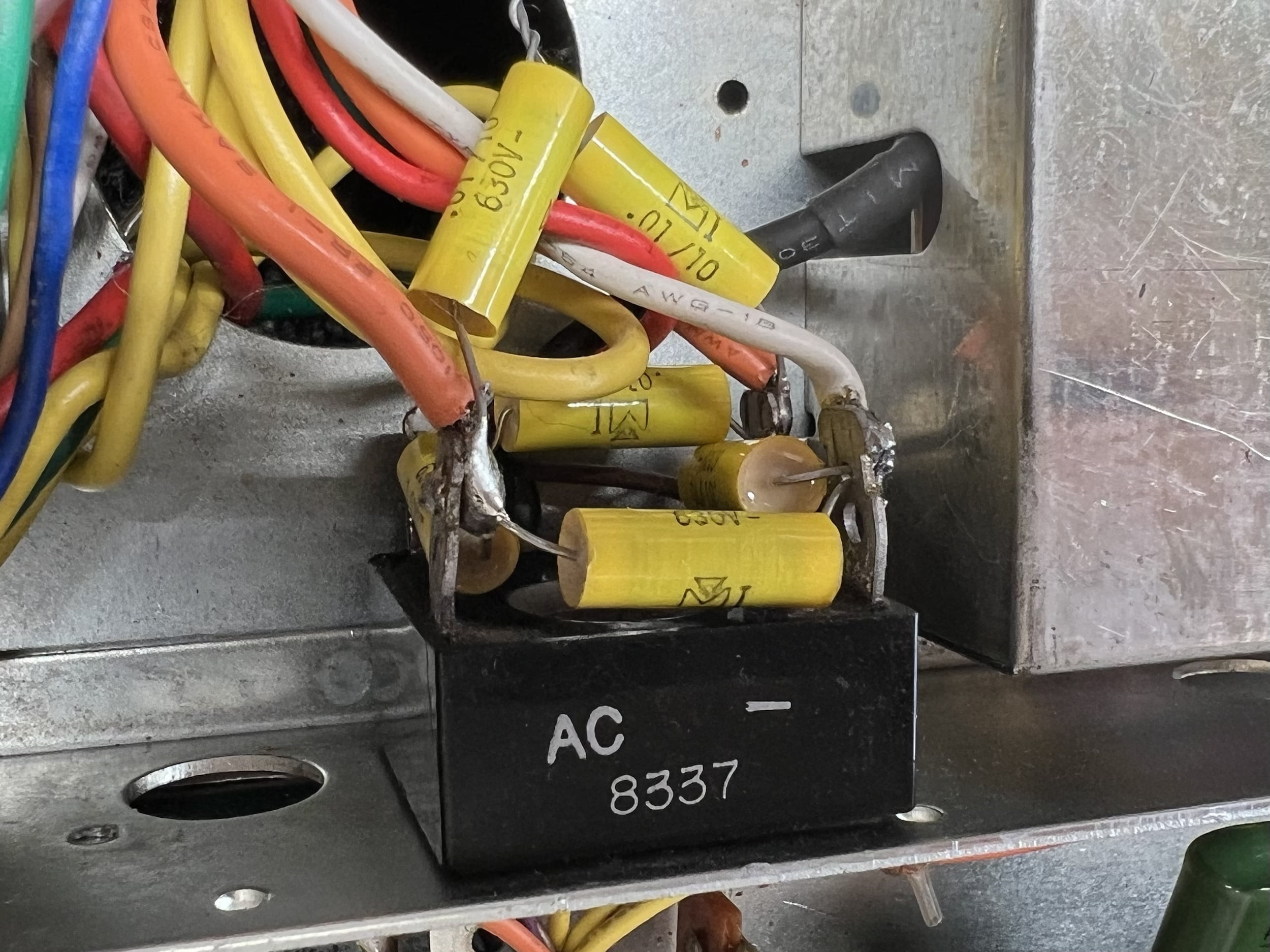
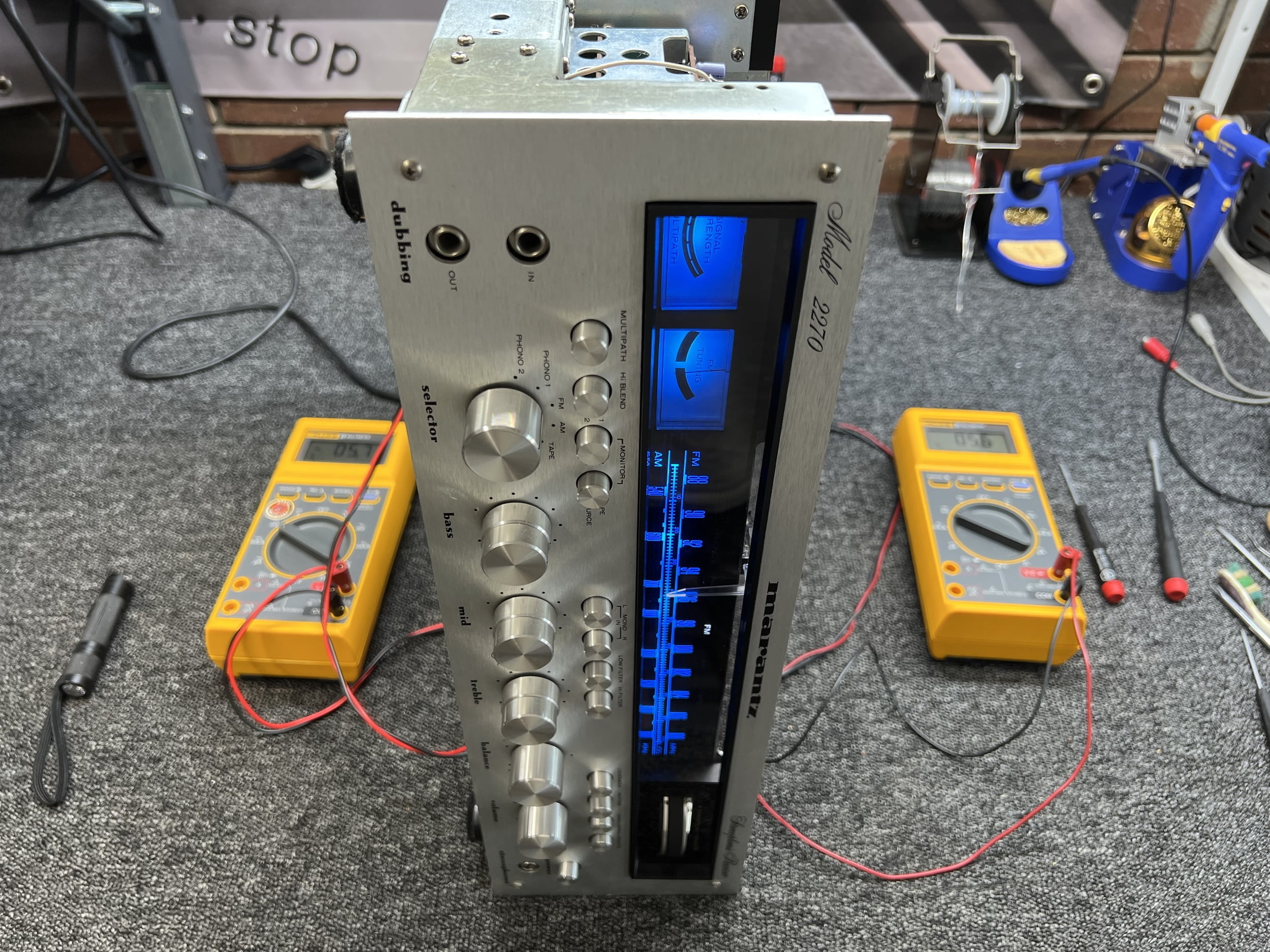
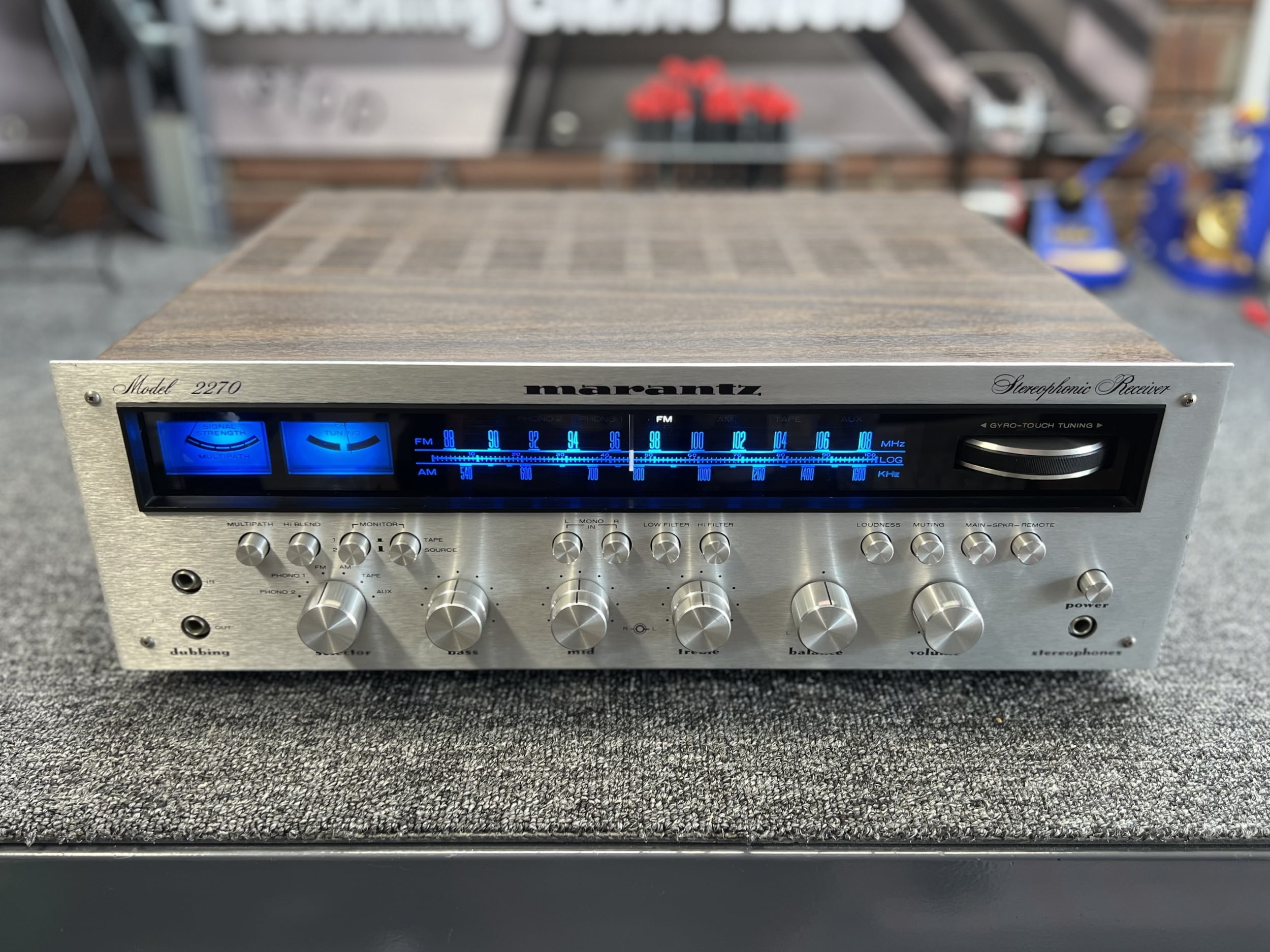
In cases like this, my job is not to rectify all the mistakes I’ve shown here. I avoid this sort of work because quite honestly, it’s painful and not what I am here for. I will however always try to get a piece like this running as well as it can, and render the best outcome for my customers, despite what might have happened to it previously.
My best advice to people reading this and who own lovely hi-fi equipment is to utilise resources like this one, ask around and look for evidence of the good work done by the best repairers. I put examples like this here for a reason and that is to save people from poor work like this.
Case 16 – ‘High-Quality’ Western Australian Tube Preamplifier
Updated May 2023
Welcome to one of the silliest cases I’ve dealt with. The equipment is bad enough, but conversing with its creator has been a truly ‘unique’ experience. Perhaps that’s all I need to say, but if you want a deep dive into this case and how to dig the ultimate hole, keep reading.
I think many hi-fi lovers appreciate high-quality, hand-made, locally-produced equipment. If something is genuinely well-designed and well-made, using high-quality parts and sounds fantastic, I’ll be the first to tell you about it. But, if a piece of equipment is terribly built, with low-quality parts, stupidly expensive and/or potentially dangerous, don’t expect me to ignore it either.
Sonics aside, we are talking about people’s hard-earned money and there are no grey areas when it comes to safety. The problem for me is that the sellers of equipment like this suck in those who don’t know any better, with pseudoscience and “construction doesn’t matter” bull$hit. That’s where I step in, bringing a healthy dose of science-informed scepticism and experience.
What I am about to show you is one of the worst-constructed pieces of equipment I’ve seen. I’m not exaggerating and I’m certainly not the only person who thinks so. Read a few of the comments repairers and astute observers have left in the comments section after the article and you’ll gain an even greater appreciation of just how bad this equipment is.
In short, I don’t want people wasting their money and I especially don’t want to see anyone hurt. Let’s see if anyone claims this one. The creator won’t want to own up to it because the work is so egregious, and yet they won’t want you to see it either.
Threats
Well, someone has claimed it as their work, thank you to the business owner for reaching out. On 10 May 2023, the owner of the business I knew to be responsible admitted to building this piece. The problem is, that he is now trying to scare me into removing this case by making meritless legal threats.
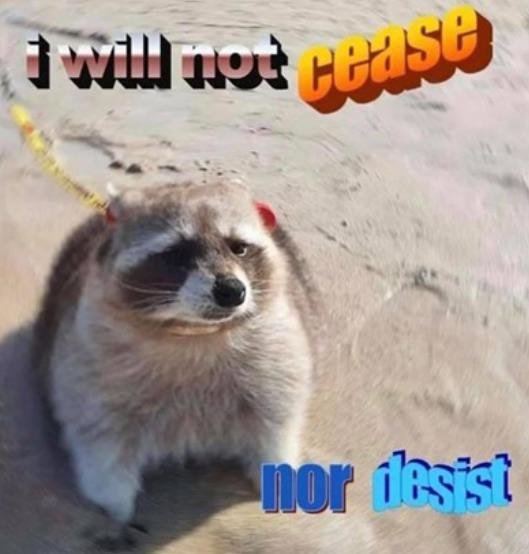
I will always fiercely defend my right to free speech and to inform the public about cases like this. I’d like to take this opportunity to assure readers that no amount of threatening behaviour, misrepresentation of the facts or diversion will change this.
The business owner has now made additional threats including promising to get together with others featured in the HoS to try to silence me.
Does this seem like professional behaviour to readers? Banding together with miscreants and riff-raff responsible for the appalling work featured here really isn’t the sort of professional association a manufacturer should want to cultivate. I’d be running a mile from any of these people, but this guy wants to hang with the unethical businesses ripping good people off.
No problem, readers and potential customers will make up their minds of course, but I wouldn’t want to buy anything from a business defending those who destroy hi-fi equipment and rip people off!
Digging Holes
The manufacturer has now amended his claims, stating that he built this thing, but “doesn’t recognise it” because “it has been modified.”
I understand the manufacturer is embarrassed. This equipment looks diabolically bad and he doesn’t want you to see it. He now wants to walk back his initial claim that the equipment is “meant to look like this” and morph it into “it isn’t meant to and we didn’t do it” but without being willing to provide any evidence to support this. One might reasonably wonder if all their equipment is built like this.
It would have been smarter to say: “Mike, this looks bad, we goofed with this unit, let me show you how it should look,” etc. Instead, he chose to attack me. This is called digging yourself a very deep hole.
Resolution?
I’ve been patient but I’ve also warned this individual from the southwest of WA that I won’t tolerate unreasonable behaviour. One thing I do well is communicate, and that’s what I’ve done with him. Three times I offered to discuss the details and to revise or redact anything libellous or factually incorrect in polite and respectful emails. In return, I received abuse and threats, but no details of anything unlawful or incorrect. I was even told to expect a summons. A summons? To what, a Royal Commission..?!
Here is an extract from one of my last emails to the business owner:
…Here is my (I think) reasonable suggestion for how to move forward:
Stop, take a breath, step back. My goal is not to cause you stress. The article neither mentions you nor your business. However, the equipment in question is terribly built, this is indisputable, and there are other concerns that I’ve not yet raised.
For the third time, I offer to revise or redact any libellous or factually incorrect information, subject to further discussion and assurances. I will not publish further concerns relating to the piece in question and will revise the article to reflect any reasonable discussions we have, if we can have one!
I’m sure we could end the article on a positive note, but we definitely can’t if you keep sending rants…
Liquid Mike
These polite, professional emails did the job, temporarily anyway. More on that in a moment, but first, to the equipment.
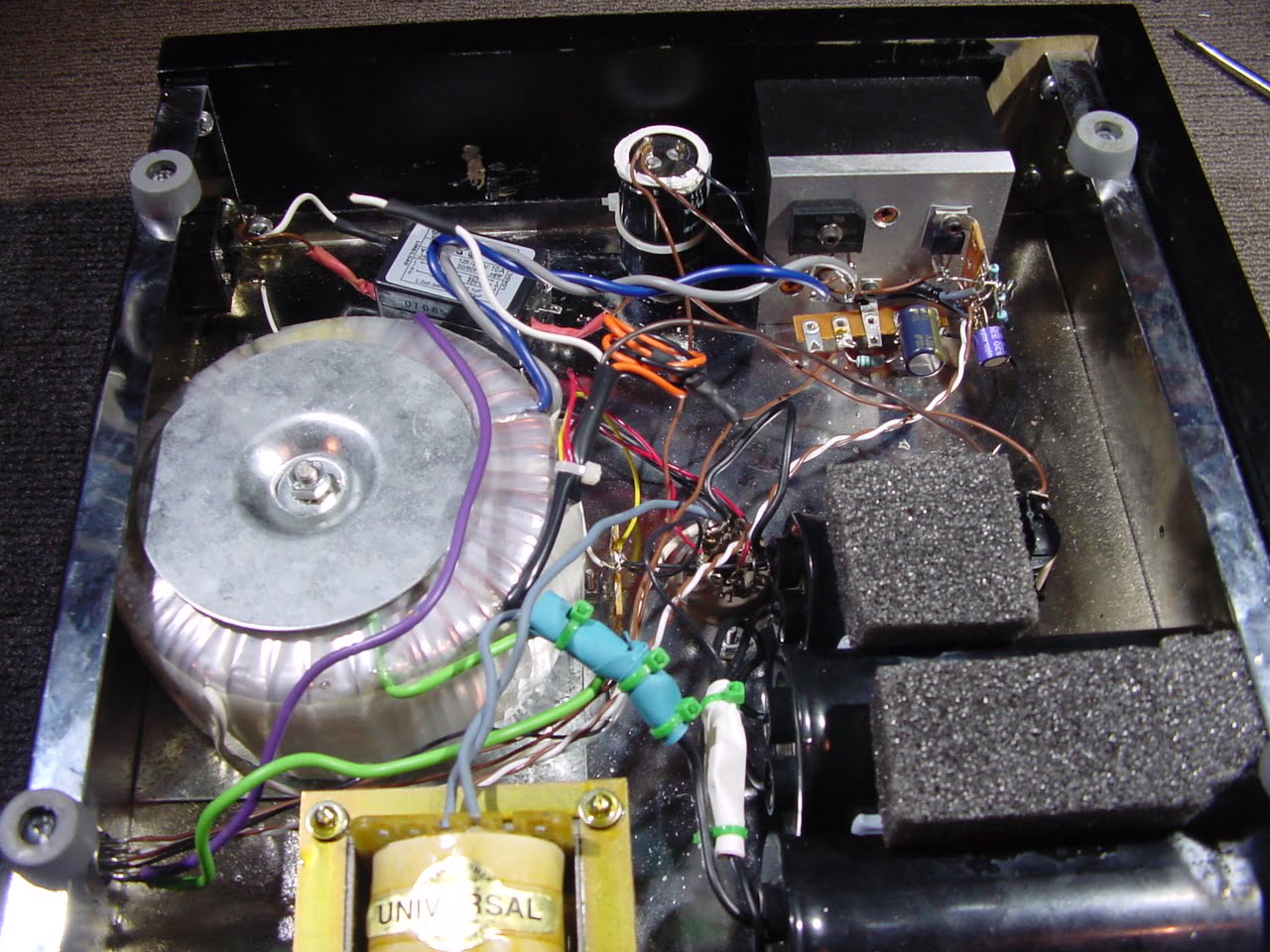
Special features to look out for here include foam, spaghetti wiring, green cable ties, cheap Chinese toroid and diode bridge, parts soldered to tag strips and some of the worst build quality I have ever seen.
I’d politely suggest that you might not want to own gear like this if you care about your family. Do you want to feel afraid of electrocution whilst using your hi-fi equipment..? No, me either.
The creator now claims: “I don’t recognise the parts and wiring” after first telling me it was “meant to look like this.” When I asked him to provide photos of what it should look like, he said he didn’t want to talk to me any more…
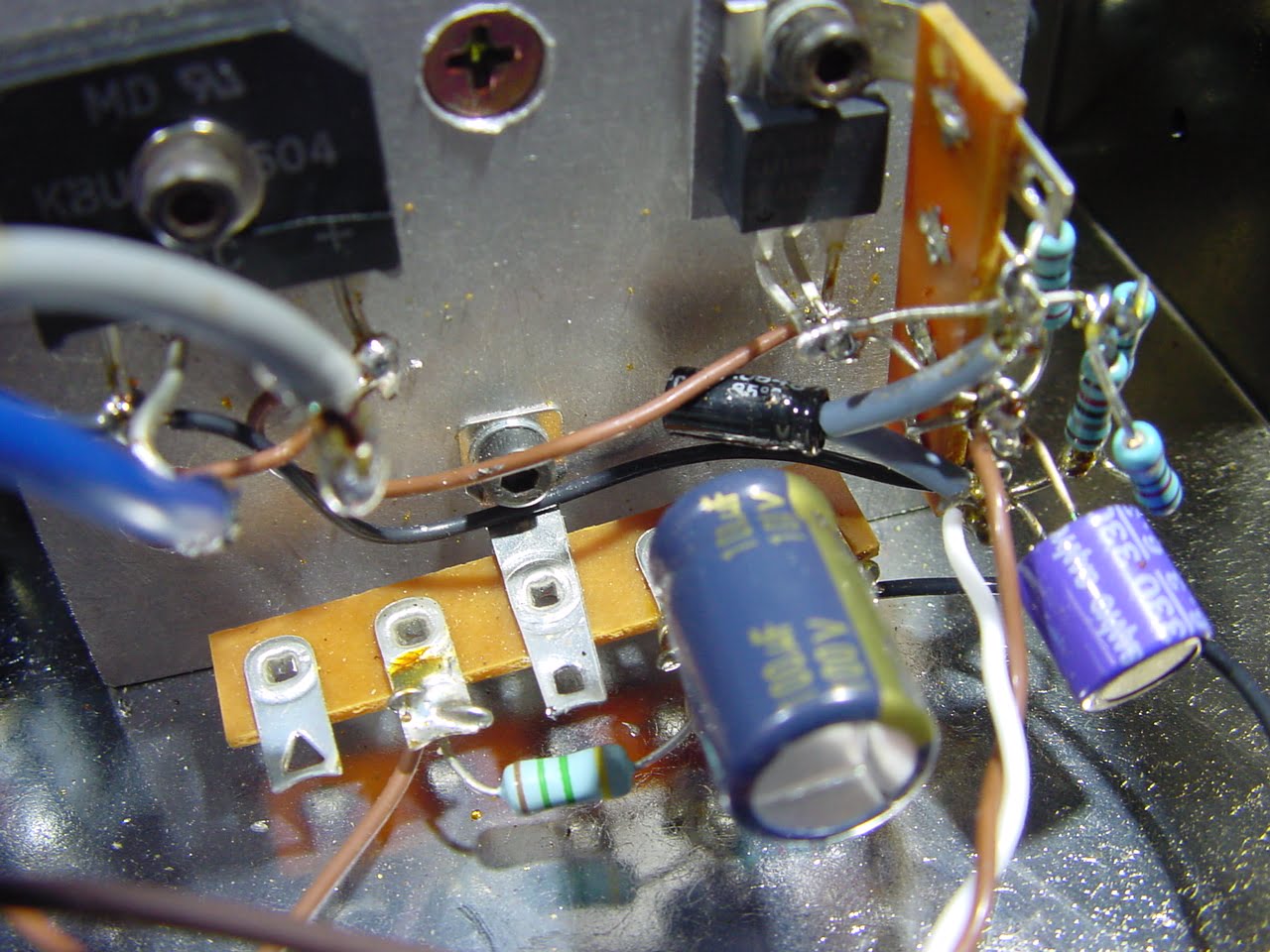
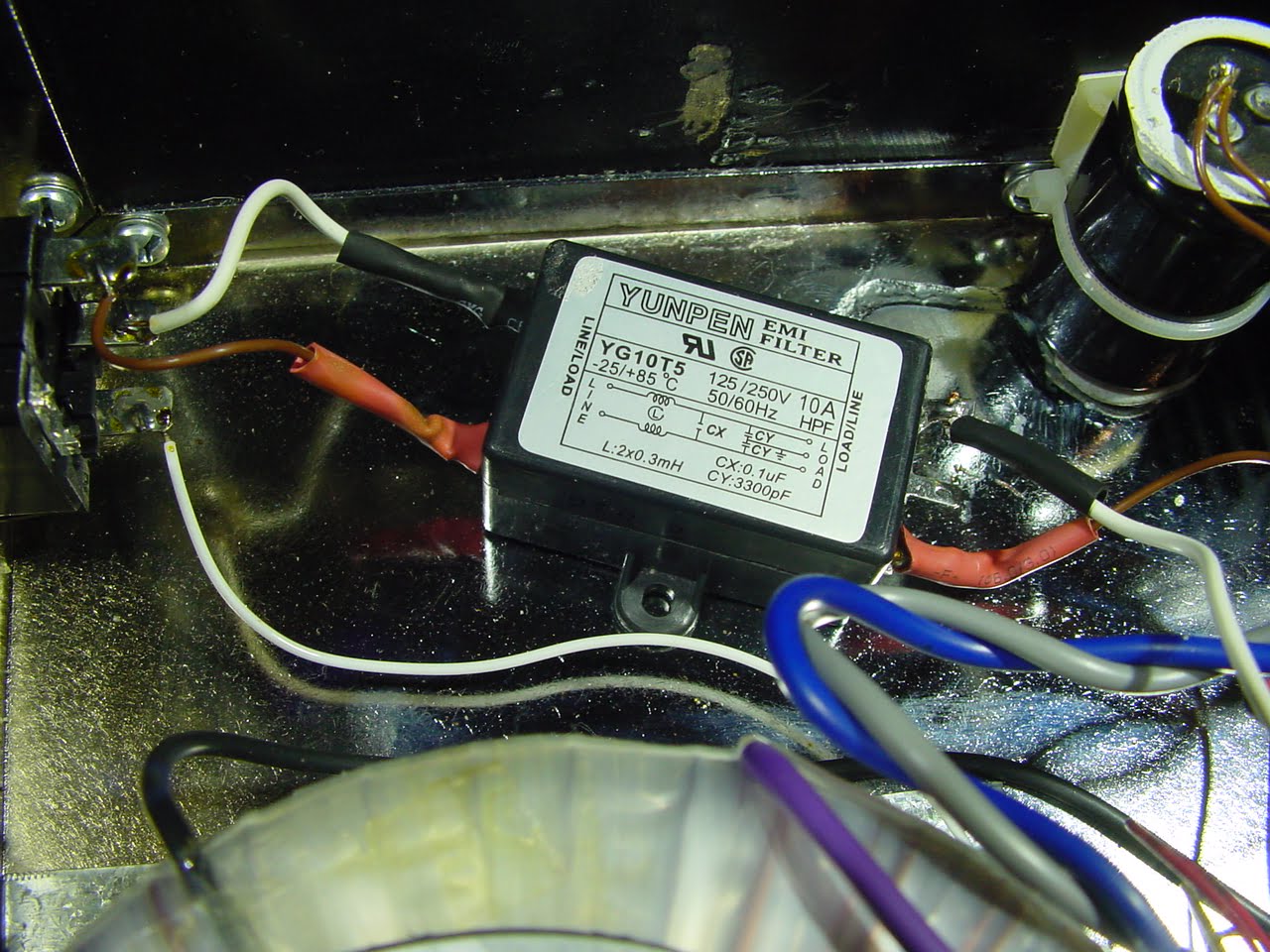
I know what else you’re wondering: “Mike, did this equipment pass the required Australian design rules, regs and safety testing etc..?” Look at it. What do you think?! Stop and consider that for a moment. This is the elephant in the room and this is what made the creator of this mess drop the stupid legal threats.
Think very carefully about equipment like this vs properly engineered and constructed equipment. There’s a reason good equipment doesn’t look like this.
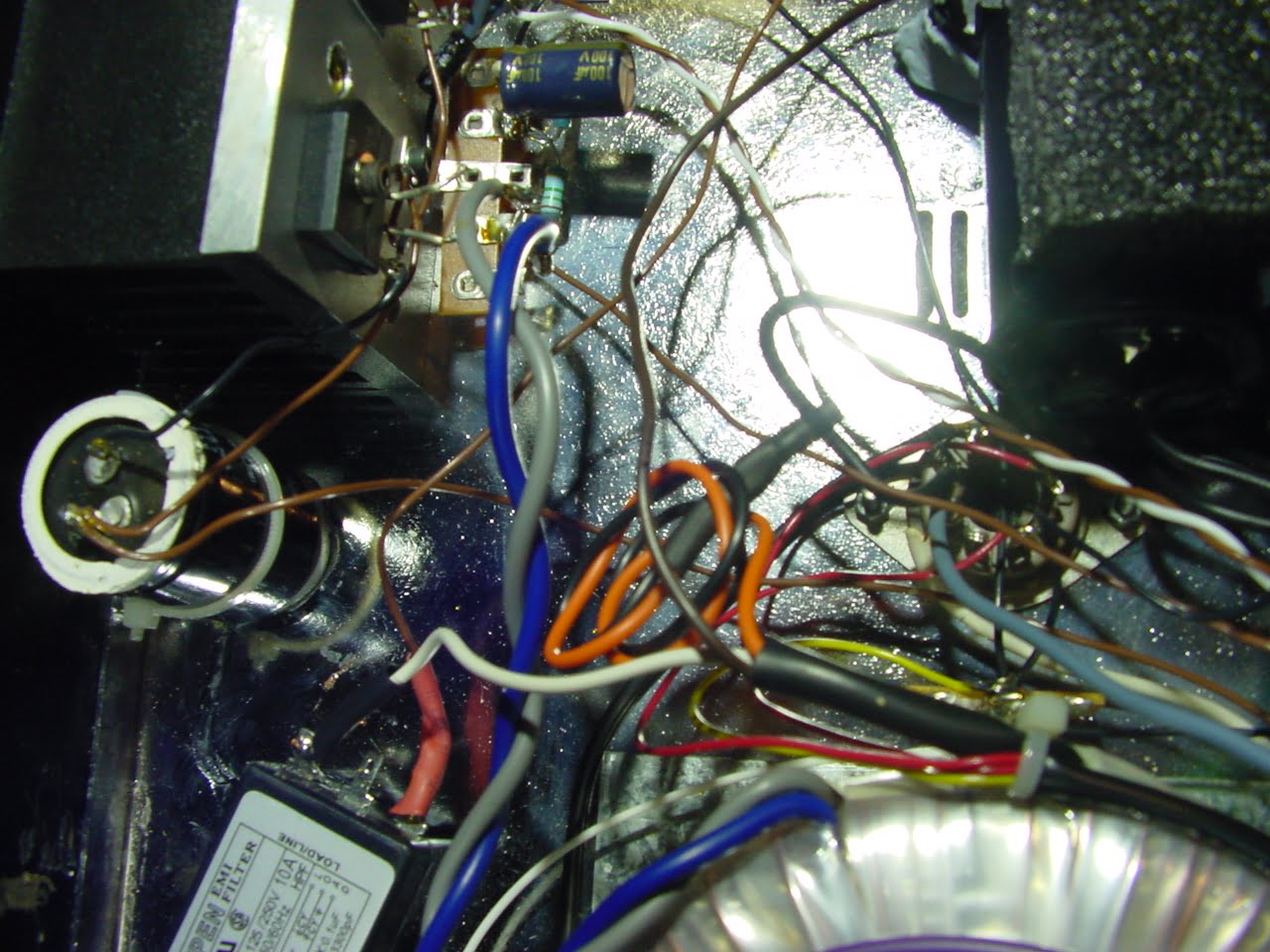
You’re perhaps wondering about crosstalk, parasitic capacitance, inductance and noise. The genius is in the layout, wiring and cheap parts, apparently… Maybe really good gear doesn’t look like this because it lacks genius, or maybe, just maybe, really good gear doesn’t look like this because this is no good at all.
This next image is an Airtight ATM-4, a highly regarded piece of tube gear, superbly well-designed and built. This sort of build quality is what every manufacturer should aim for.
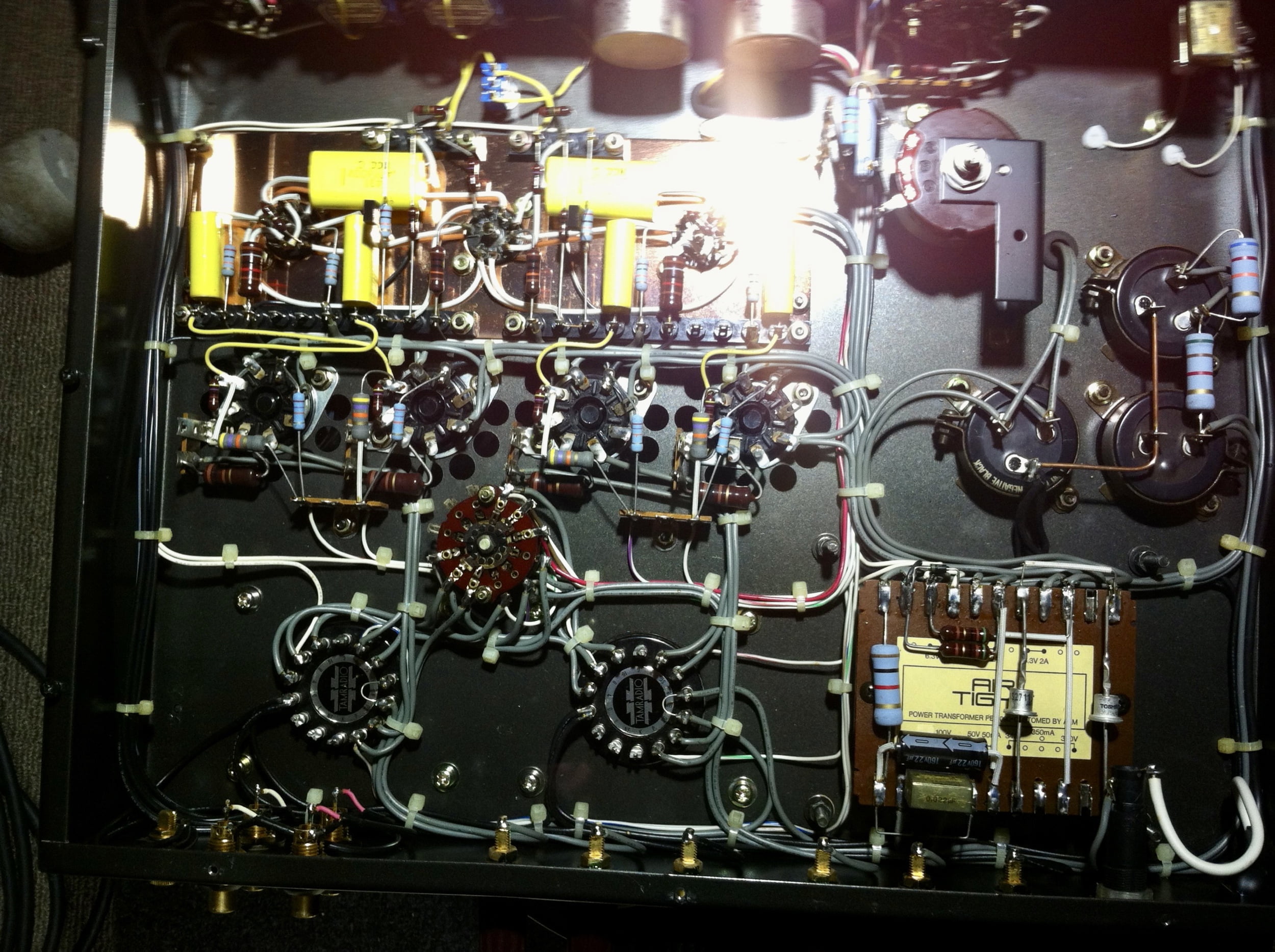
Gurus
Alright, so who built this expensive, poorly built preamp? Well, I’m not going to tell you, as a courtesy this builder doesn’t deserve at this point, but it’s a Western Australian-made preamp from somewhere in the southwest, which is where most of the people are in WA if you are not from here.
Be wary of what I call gurus and guru-made gear – that is anyone telling you that build and parts quality don’t matter, that their home-made equipment is better than anyone else’s and that you should only buy their equipment, which inevitably looks like the equipment in this case. Understand that no genuinely well-engineered equipment looks like this. For confirmation, look at aerospace, aviation, test and measurement equipment, or really good consumer audio gear.
This ‘guru’ thing is how cults work. Take a self-styled guru, add a little pseudo-science, some hokey build and a few gullible people looking for the promised land and soon you’ll have a culty brand and die-hard followers who’ll swear their saviour can do no wrong and that the gear is the best thing in the world. This happens in hi-fi, but it relies on a) gurus and b) the existence of gullible/susceptible people.
The closest thing to real gurus are people like the legendary Peter Walker of Quad fame and the equally legendary Nelson Pass, of Threshold and Pass Labs fame, amongst others. Unironically, they don’t behave like gurus, there’s no BS from engineers like these. Both gentlemen are giants in the field of electronics design engineering and if you want to see what real legends look like, these are the sorts of people. Between them, you’ll not find a piece of gear that looks even remotely like the equipment in case #16.
Thankfully, most don’t fall for this guru thing, but many do. Common sense and rational thought generally prevail though.
Victory!
Update: 16 May 2023. The truth and ethical behaviour will always win and I’m proud to announce victory in this case.
By sticking to the facts, observing the law and calling the bluff of this business owner and his ‘lawyer’, they were forced to concede defeat, for a few weeks anyway. In Australia, you can’t sue someone just because you don’t like what they’ve said. By all means, sue someone if they’ve defamed you, but in a case like this, it’s just a waste of everyone’s time.
For a claim of defamation to be proven, the alleged defamer must:
- Lie about someone or something – I have not
- Know that the statements are a lie – My statements are 100% truthful
- Identify the claimant – I have not
- Directly harm the claimant with their untrue comments – I have not, the alleged claimant is never identified.
The claim that I have defamed anyone here is nonsense. Even if I told the man’s name and his business name, the information here is factual reporting. The gear is as terrible as it looks. Period.
Spin
Rather than accept any responsibility, the owner tried to spin all this into being my fault, as you do if you have a poor grasp on reality. I guess he came to that conclusion by reading articles in the Hall of Shame about other diabolically bad businesses.
My site, about classic hi-fi gear, has received more than 2 million views and contains over 500,000 words, 15,000 of which are in the Hall of Shame. That’s roughly 97% regular positive content vs 3% HoS. Even a cursory glance reveals a showcase of the best hi-fi equipment and technical work from one of the most respected voices in this community, but that doesn’t suit his narrative.
This manufacturer who portrayed himself as a beacon of kindness and positivity called me: “a vindictive prick”, “a sick puppy” and “delusional” with a “god complex”. Paradoxically, he claimed that I think I “am above everyone else”, but that he “wouldn’t stoop to my level”.
All of this drama is pointless and my question is simple: If this equipment has been modified as claimed, rather than rabbit on about how you’re such a great guy and I’m evil, why not just do as I’ve asked and send me images of the unmodified equipment I’ve requested so that I can amend the article, and clear you? Bueller..?
Lessons
I’d love to be able to tell you that this business owner learned something, but he was unwilling to concede that anything might be his fault. Dismissing serious concerns about build quality and customer safety, he blamed me for his problems rather than accept responsibility. Instead, he spent valuable communication time gloating about how he thinks his hi-fi gear is better than mine, as you do:
“As I said, going from your web site you aint heard nothing.”
Business Owner, case #16
That’s great, I’m sure the spaghetti bowl of Jaycar parts in the images is better than any properly engineered and built equipment, but grammar aside, what does that have to do with this case!?
This sums up case #16 – the equipment is bad but the person and ego behind it is the real problem. Perhaps time will afford him a more helpful perspective, but I deeply doubt it.
Postscript: Deeper Holes 2.0
It will perhaps come as no surprise to learn that, despite telling me never to contact him again, this dude contacted me again, on 25 July 2023! He claims that I caused his business to fail, has no orders on his books because of me and is suing me (again) for AUD $200,000. How this has anything to do with me, I don’t know.
The failure of his business and lack of any new orders has nothing AT ALL to do with the equipment he makes and people choosing not to buy it. No, it’s my fault. I even had a brainwashed follower gaslight me on Facebook, telling me that I was at fault for bringing this case to light and that I “shouldn’t have”. Shouldn’t have..? Why not?! That sounds like censorship to me.
This blame-shifting only adds fuel to the garbage fire that is case #16 and begs one simple question: If this equipment is so incredibly good and the maker is secure in that belief, why would he or anyone else care what I think about it?
McFly…?
The truth, conveniently ignored by those attempting to divert attention from it, is that this expensive and poorly made equipment is typically sold to gullible customers who lack a useful understanding of what they are buying. I have a problem with that and I promise that no amount of threats, gaslighting, blame-shifting or attempts to cast me as the villain will change that.
None of this helps the manufacturer of course, either. Who would say anything positive about this after being abused and threatened for simply reporting the truth?! In what universe is that fair or reasonable?! Anyway, Sophocles says this more eloquently than I ever could:
“All men make mistakes, but a good man yields when he knows his course is wrong, and repairs the evil. The only crime is pride.”
Sophocles
Boom!
Case 15 – Yamaha CR-600 Receiver ‘Precision’ Repair
This case comes from my good friend Jason @ The Speaker Doctor. His images, my commentary. I can’t print what Jason says, it’s far more offensive than anything I would say!
Time for another story and this one annoys me. I met the guy who did this or runs the business where it happened. We talked specifically about bad businesses doing terrible work and he seemed very much against it, as I am.
So, Jason’s customer brings in a Yamaha CR-600 receiver for inspection after some recent work, because it’s not working properly. It’s a lovely old stereo receiver that’s been to a repairer in the northern suburbs. It had a sticker on the back claiming “precision circuit board repair”.
Let’s take a look together and see if any of this looks like precision work.
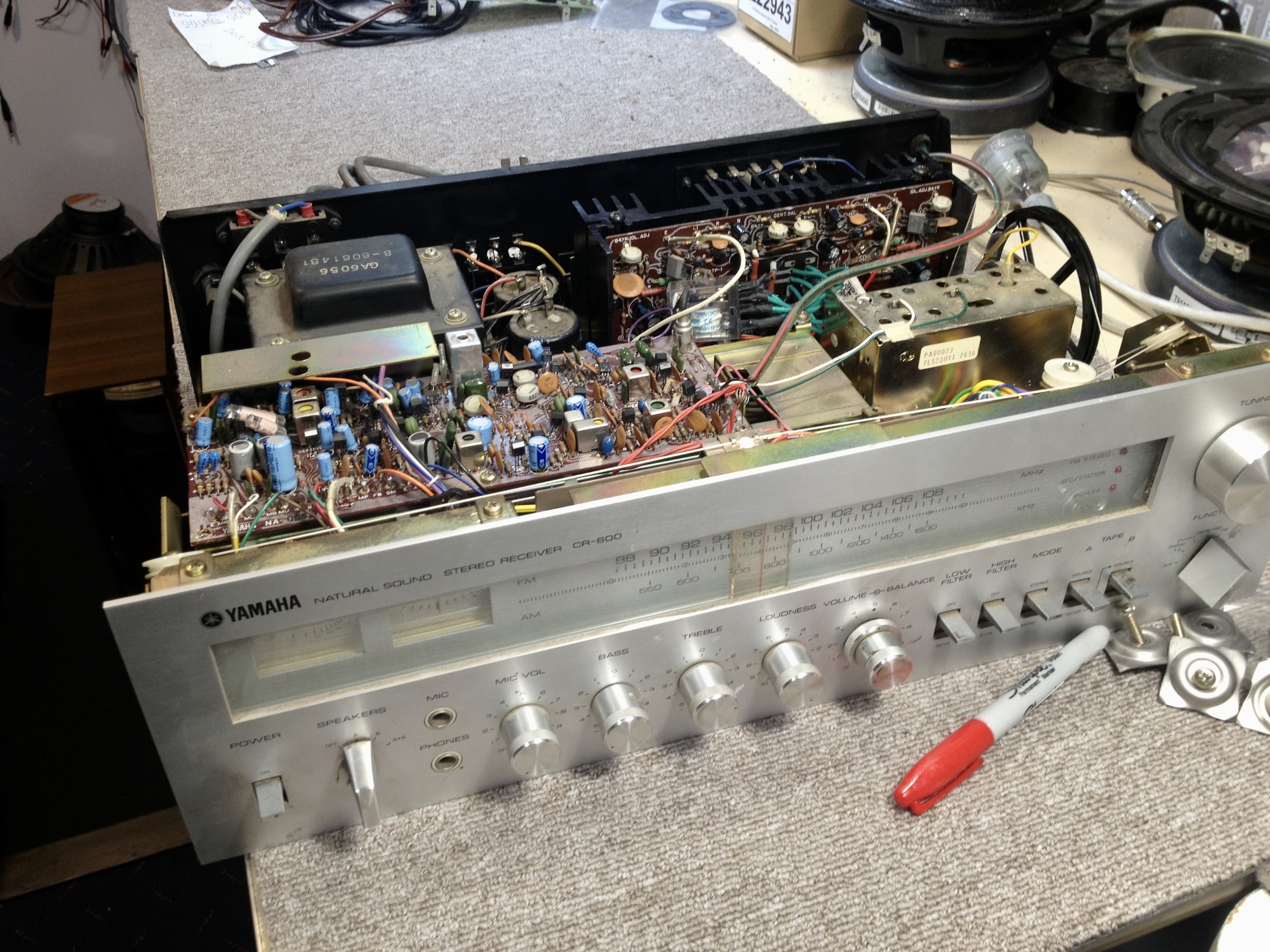
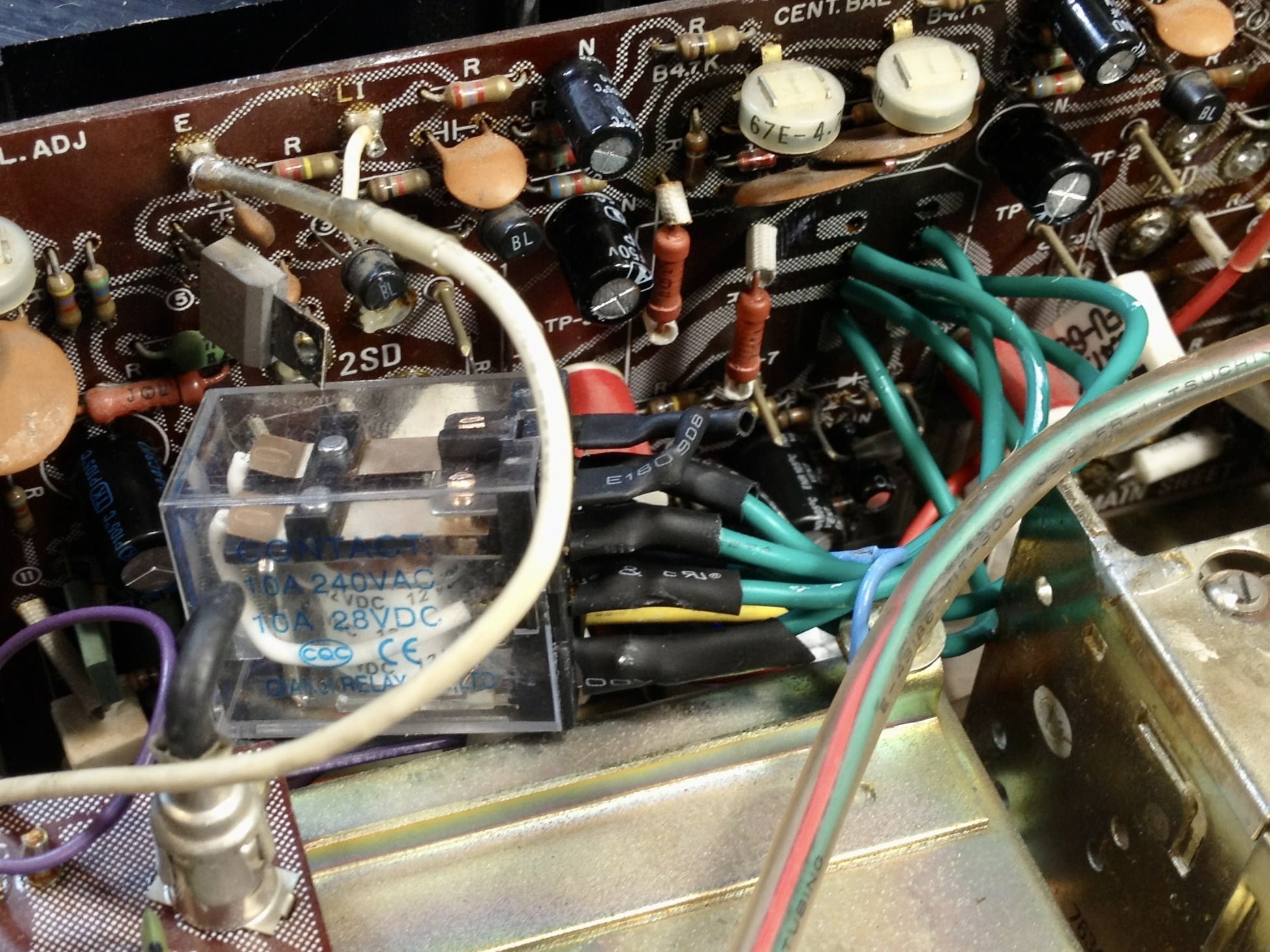
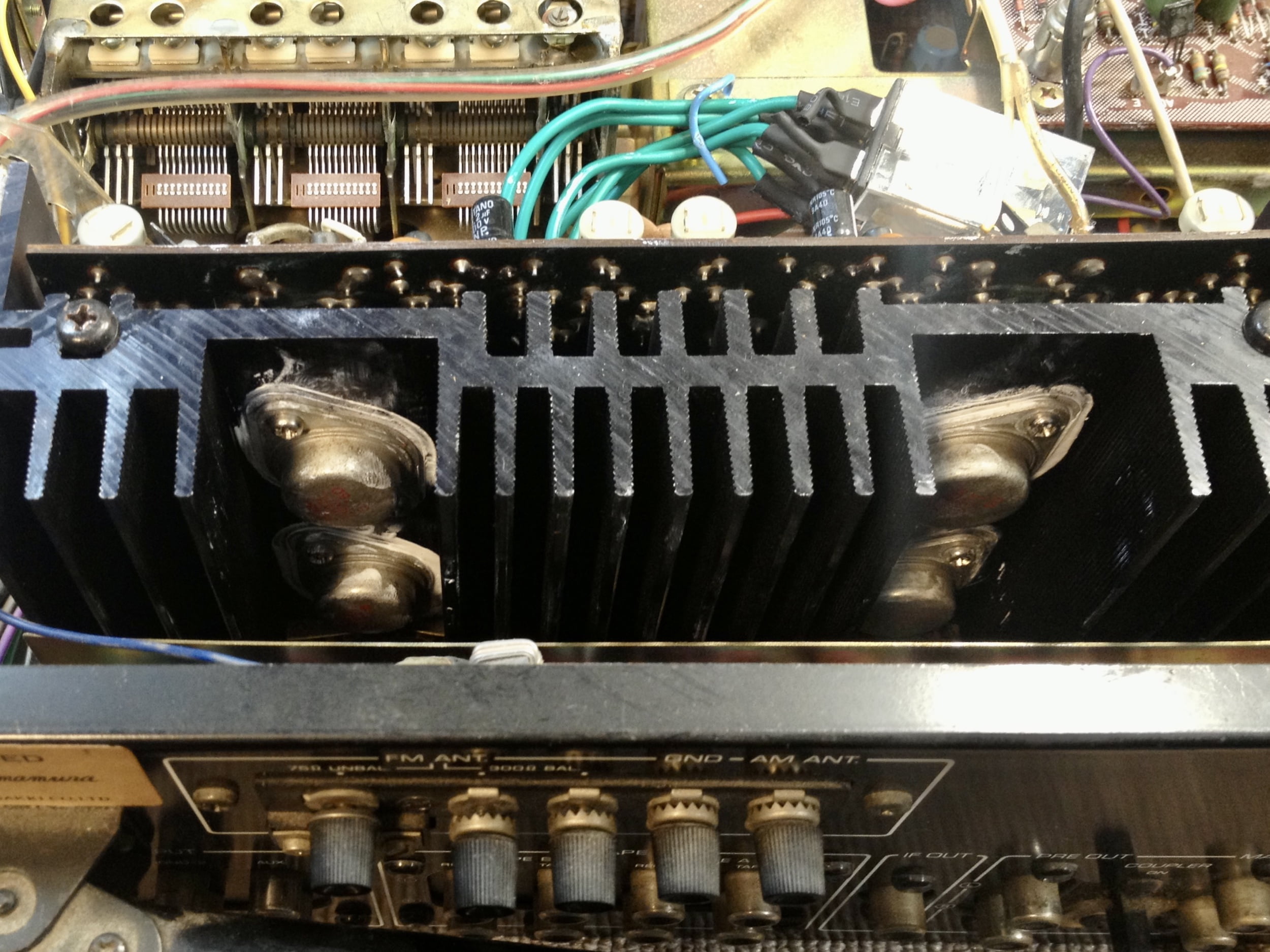
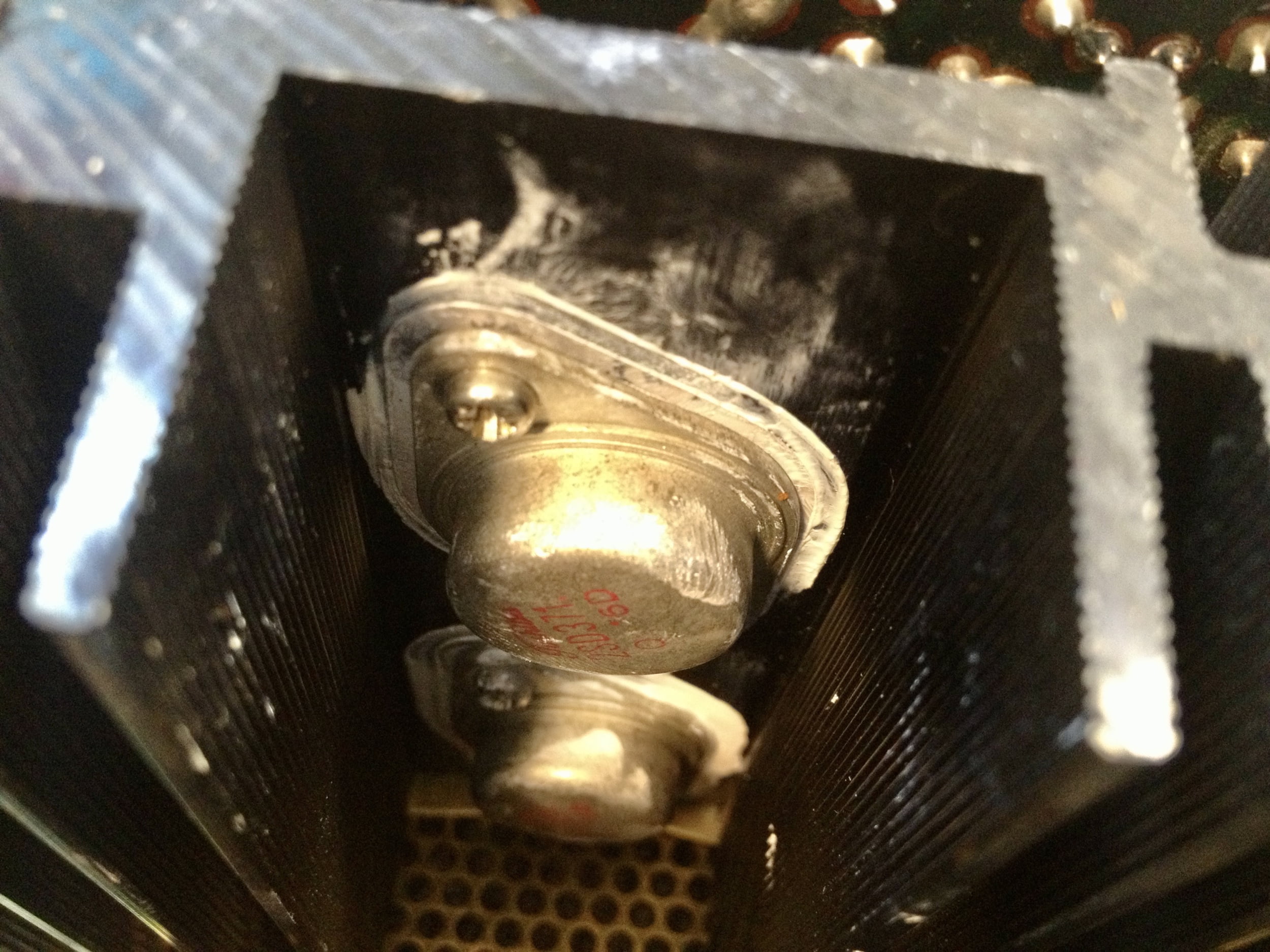
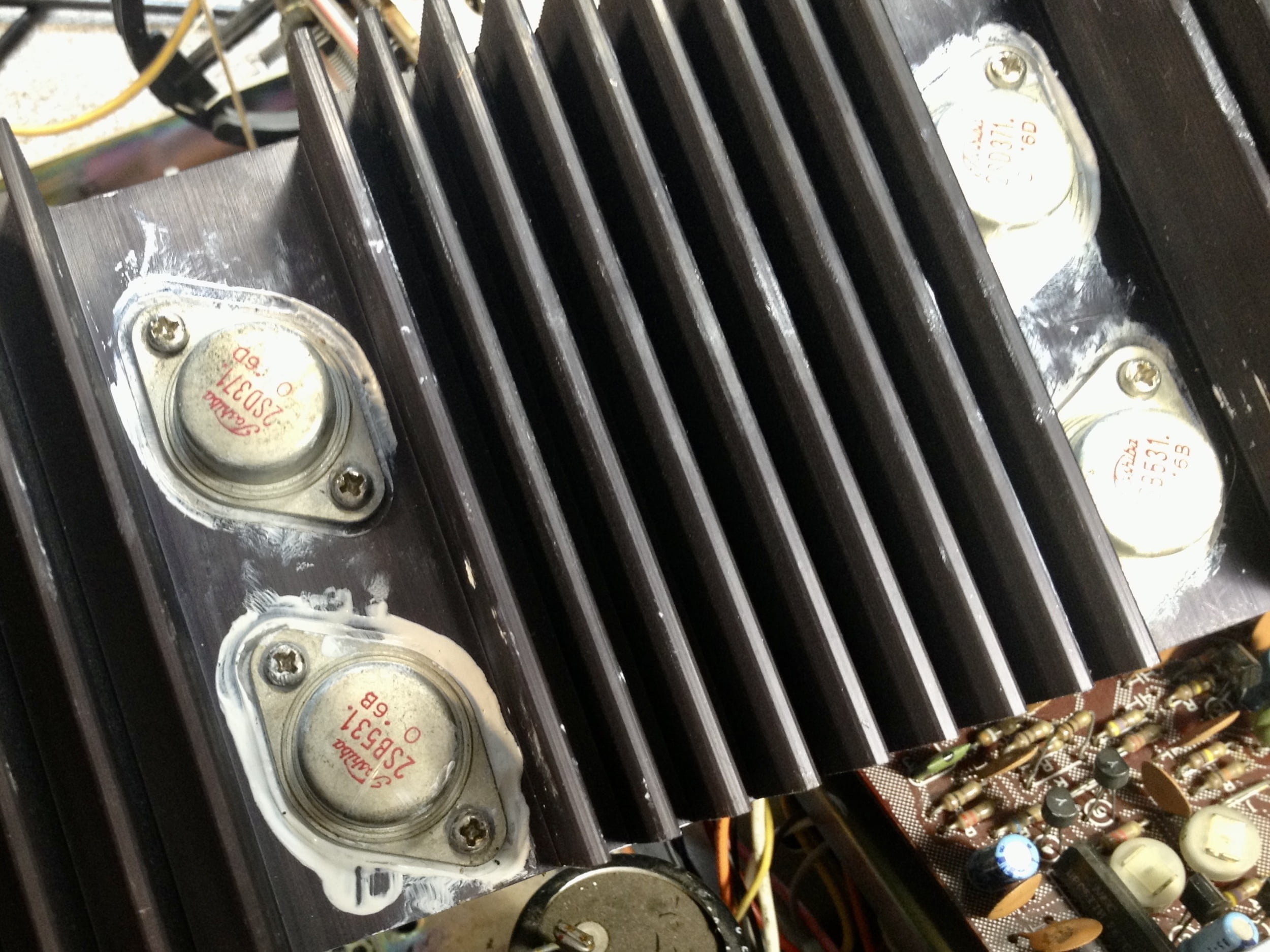
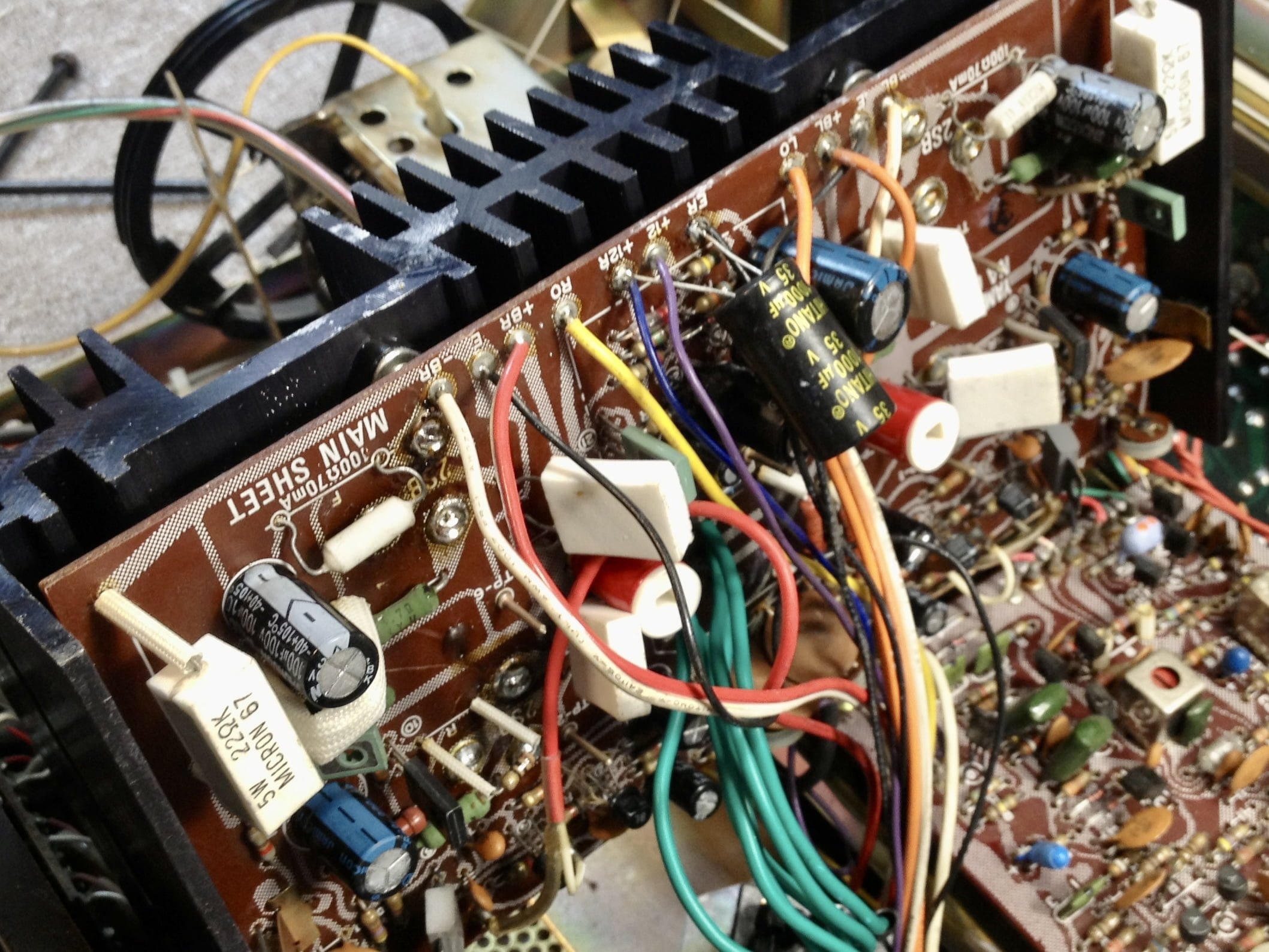
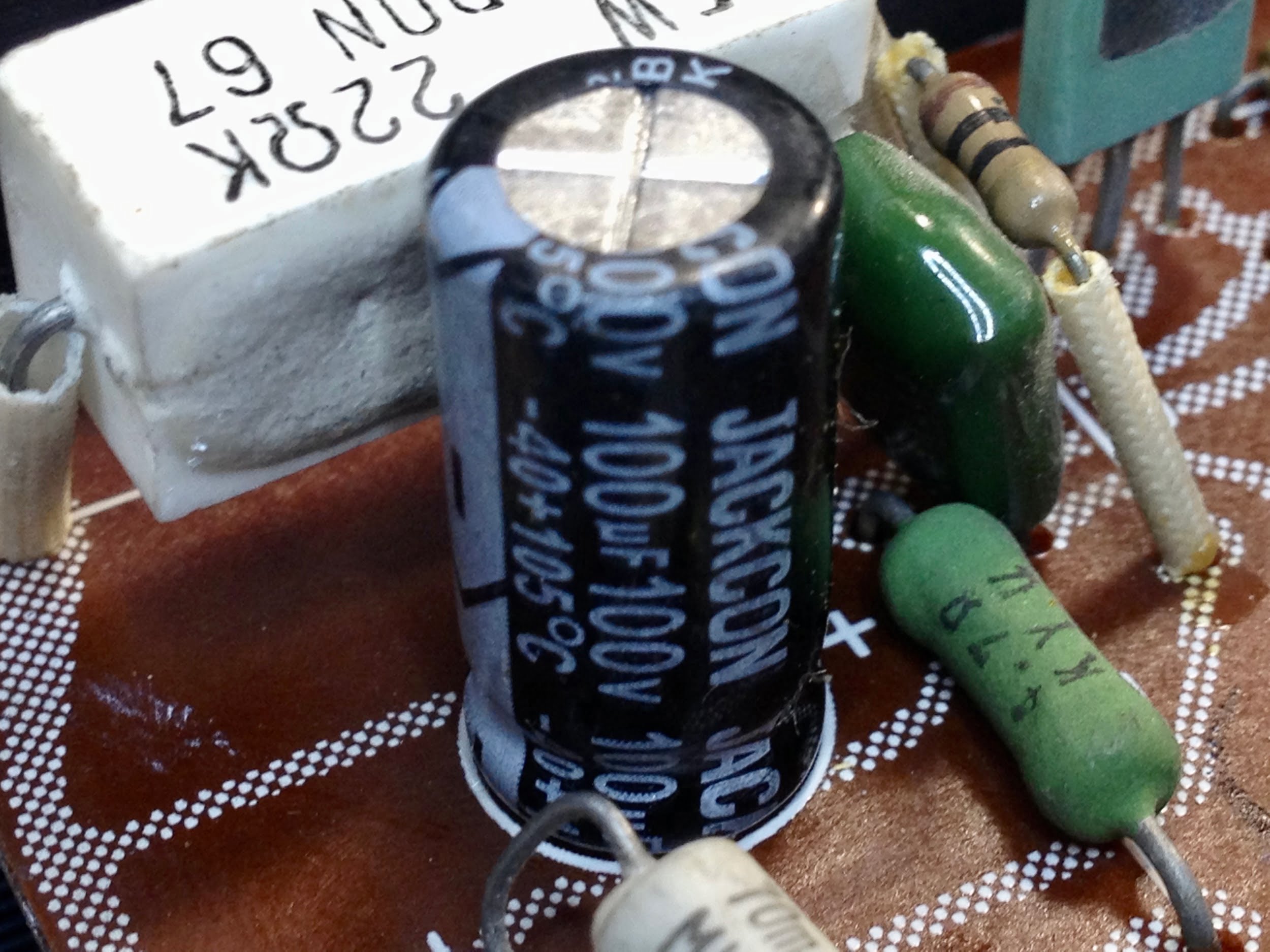
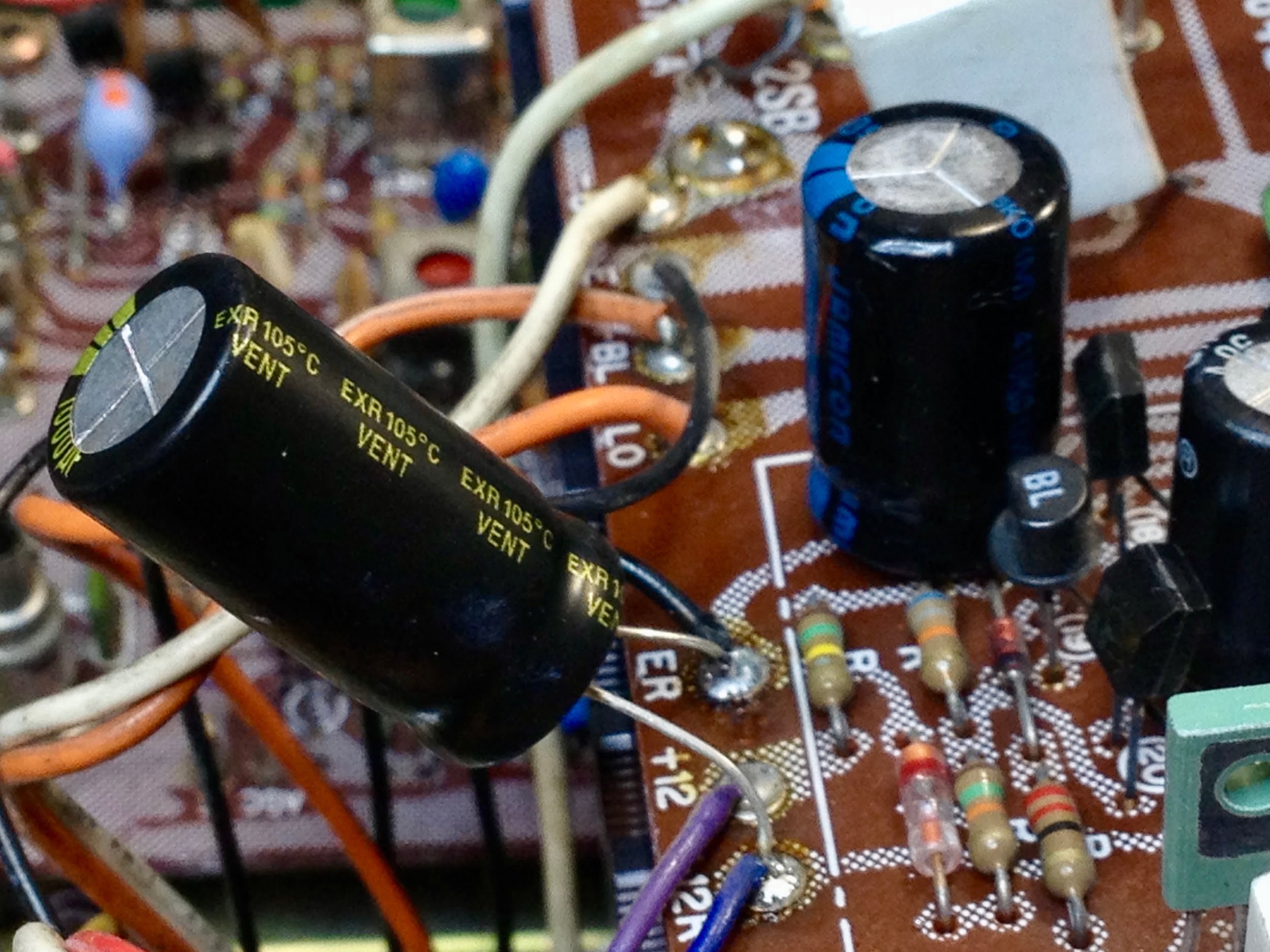
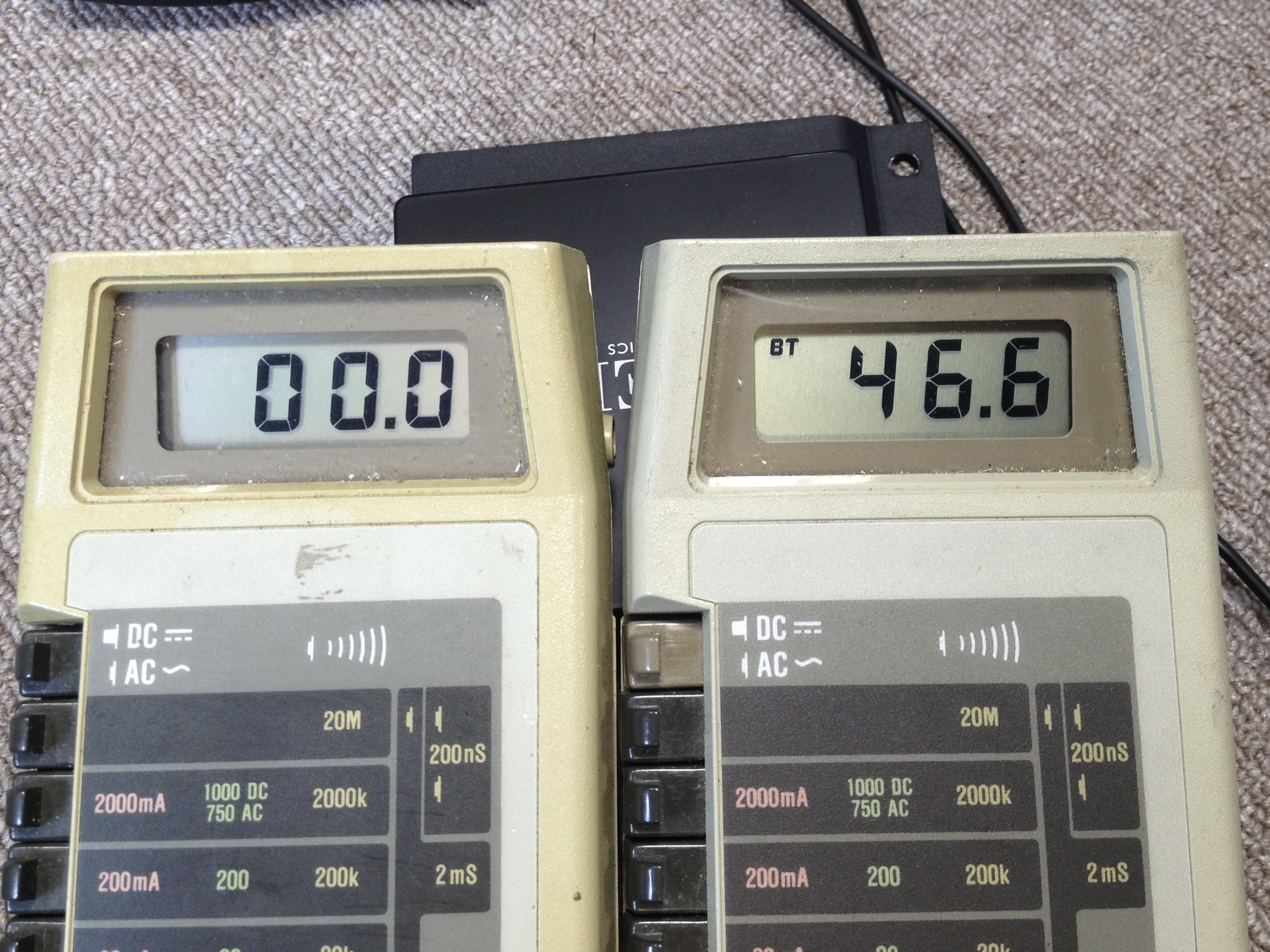
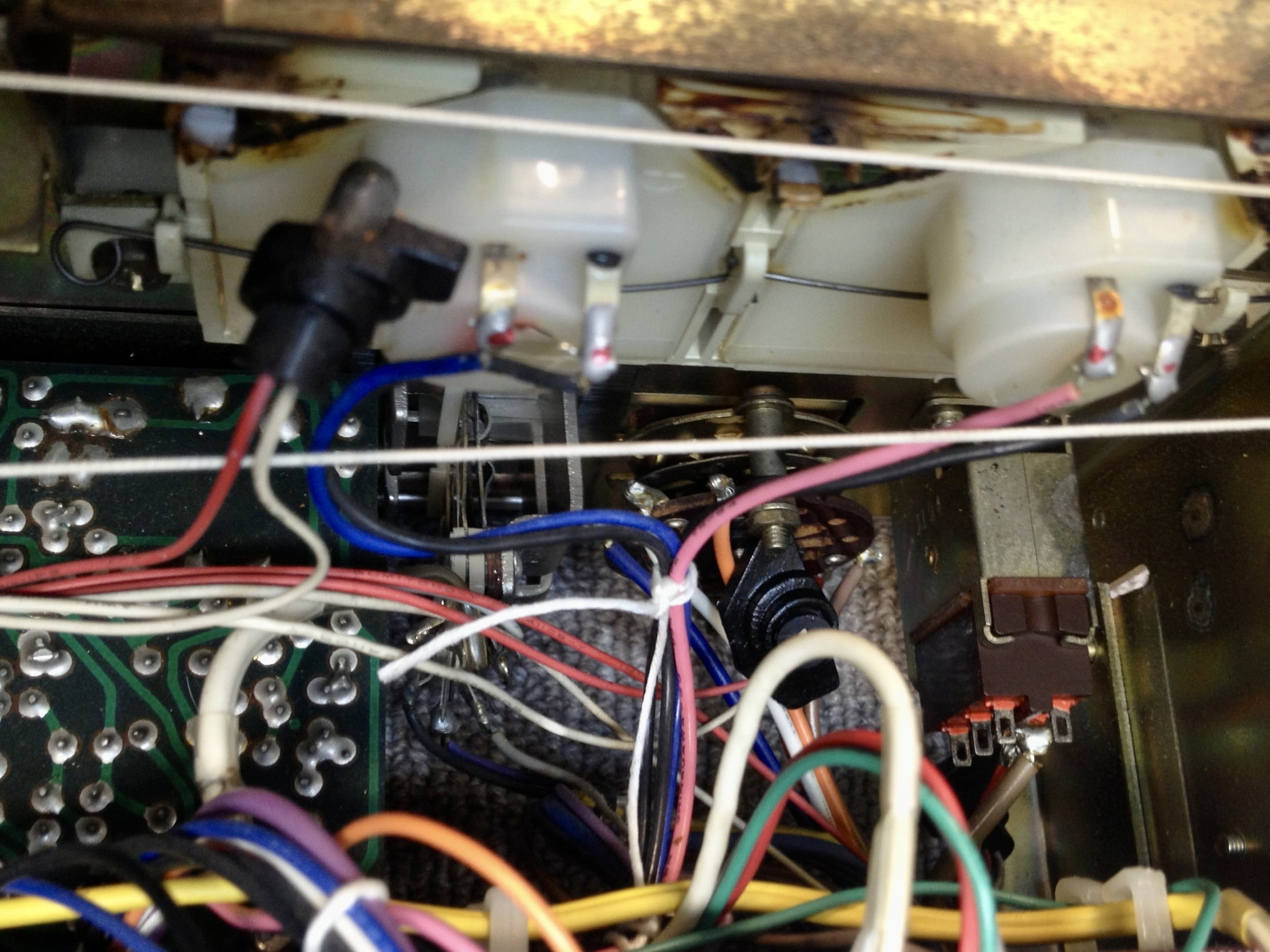
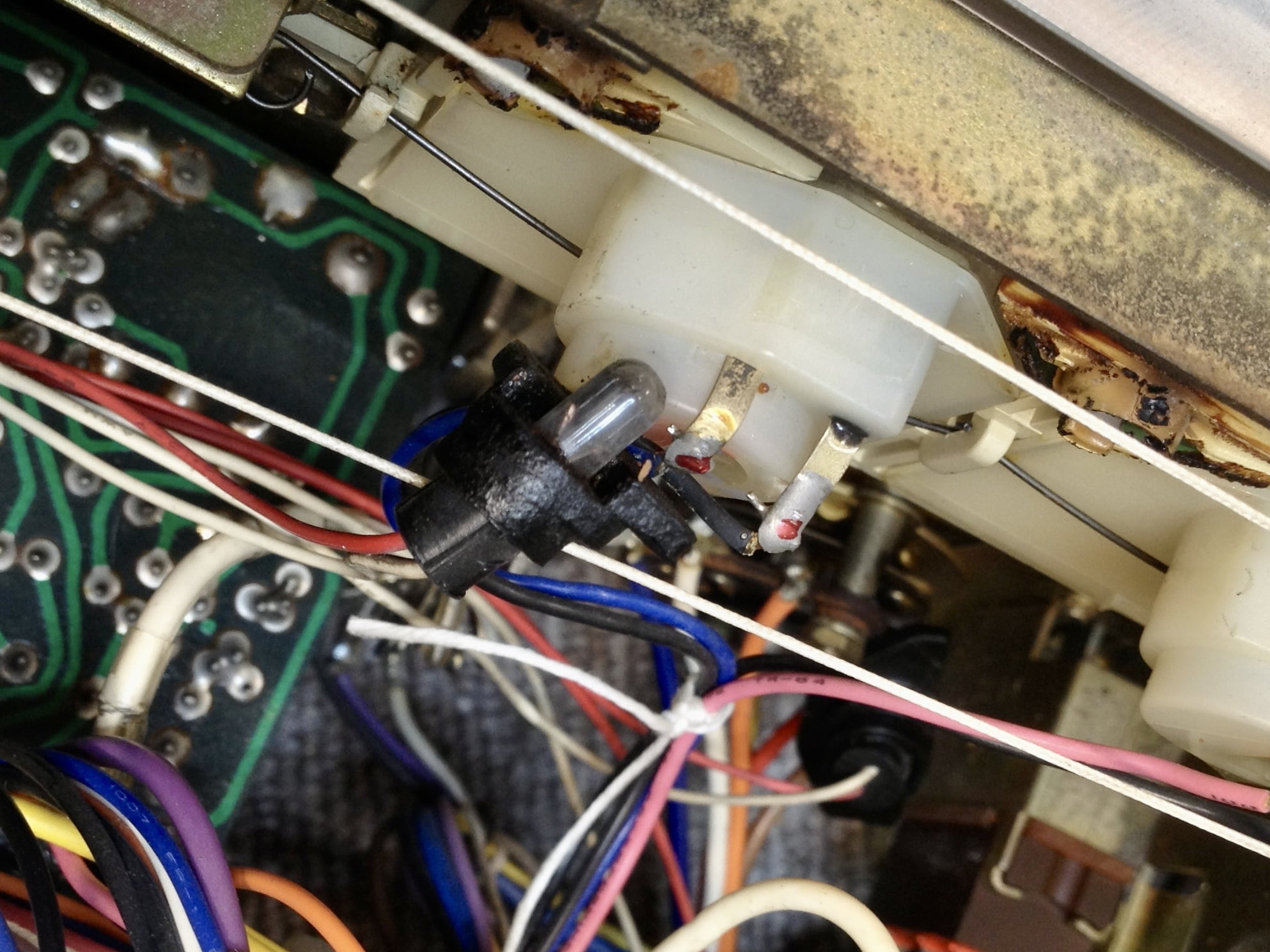
Here’s what’s on the board, underneath where the relay originally sat, and why the receiver only works some of the time: bad soldering, broken pads and traces, and rivers of flux:
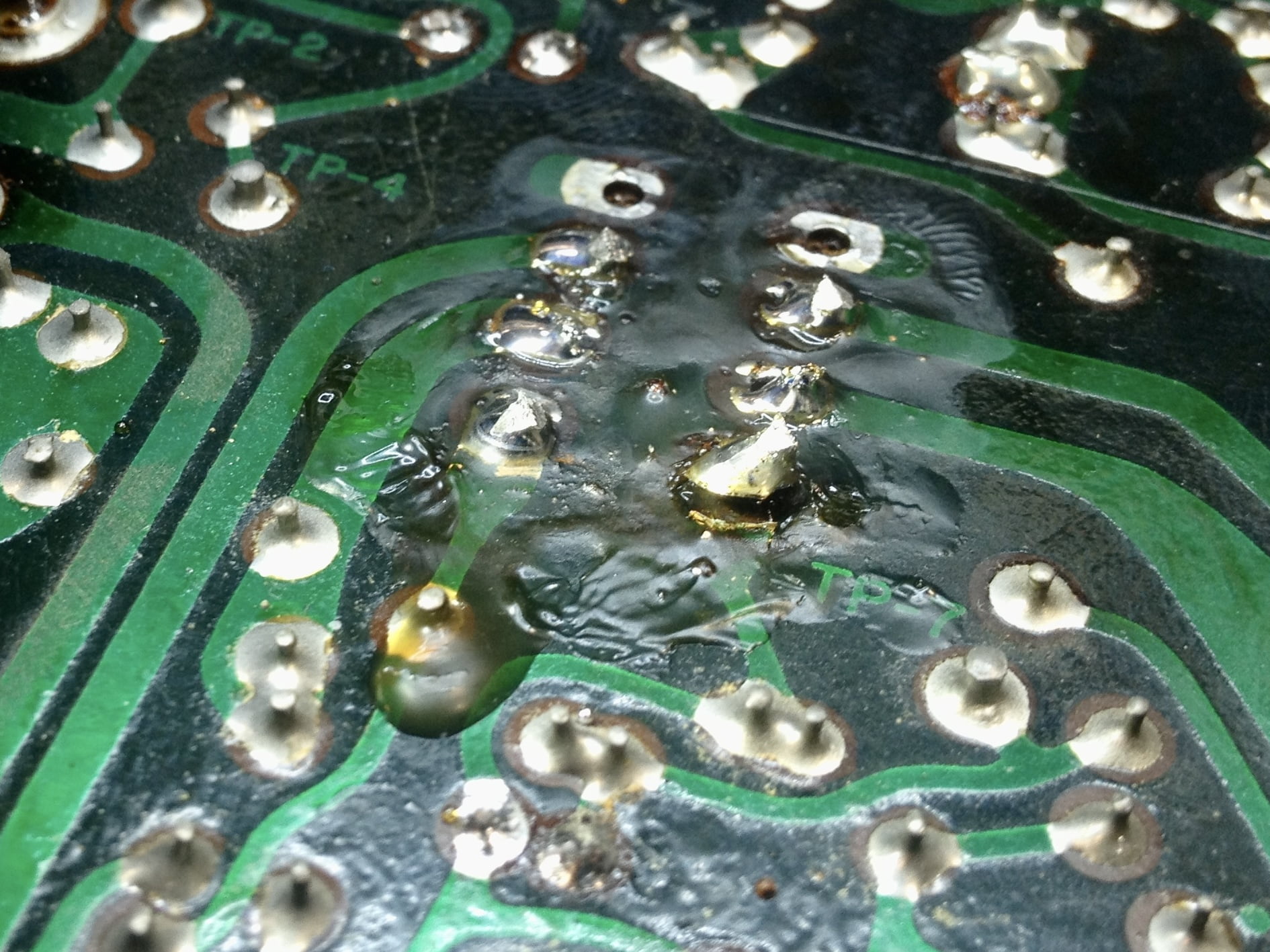
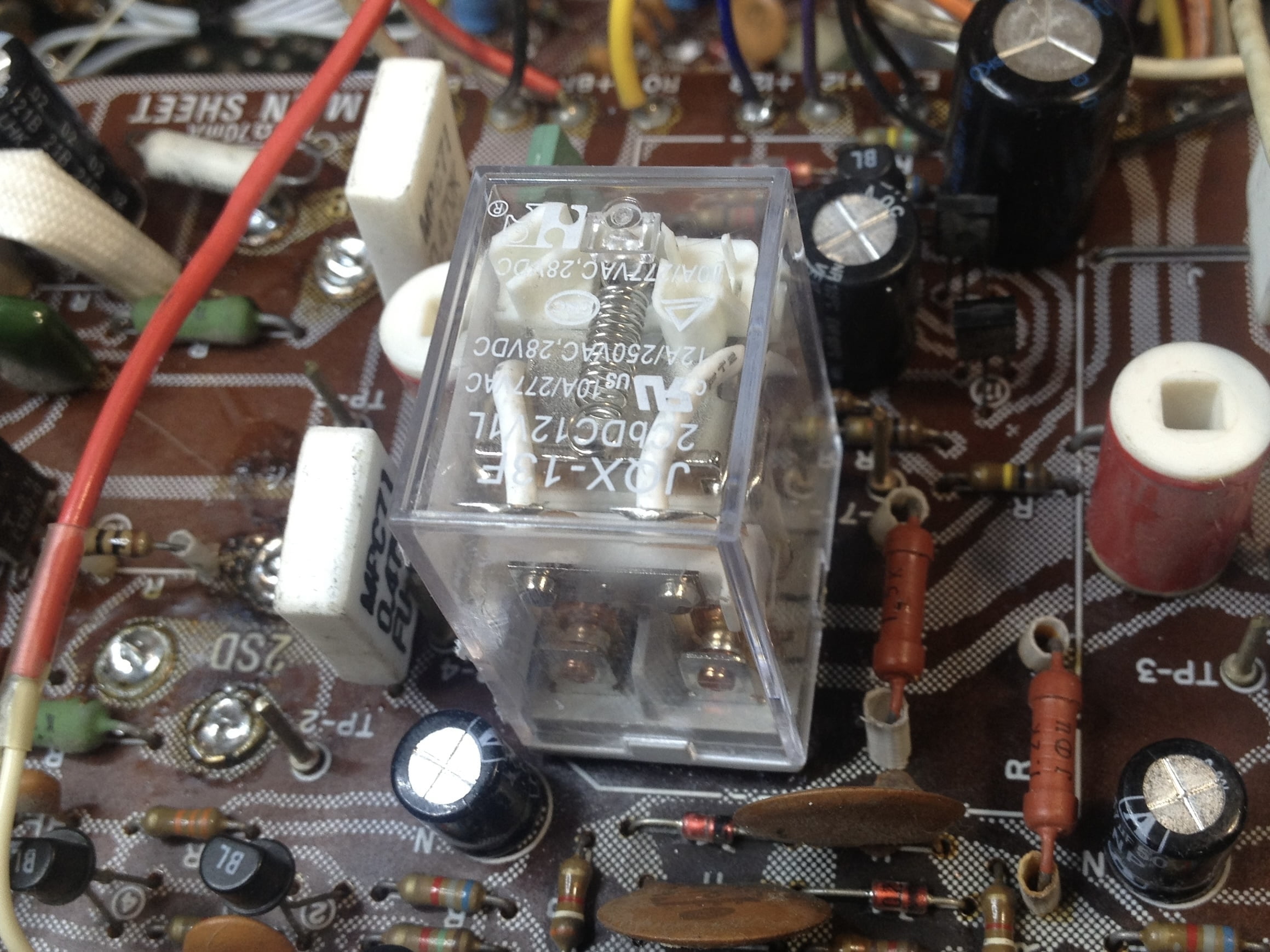
Learnings
I think you’ll agree that no precision work of any kind has been done here, except the remedial work done to resolve the issues created by this repairer. It’s a shame but all of this only serves to validate my advice about paying a little more, finding a good repairer, etc. People ask why we are fully booked, and why things take time. This is why.
A fancy sticker, fancy workplace or claims of working on fancy equipment don’t automatically mean good work. I am proud of the work I hand back to customers. Nobody’s proud of the work you see in this case. That’s why it’s here.
Case 14 – Naim Power Amplifier
More soon!
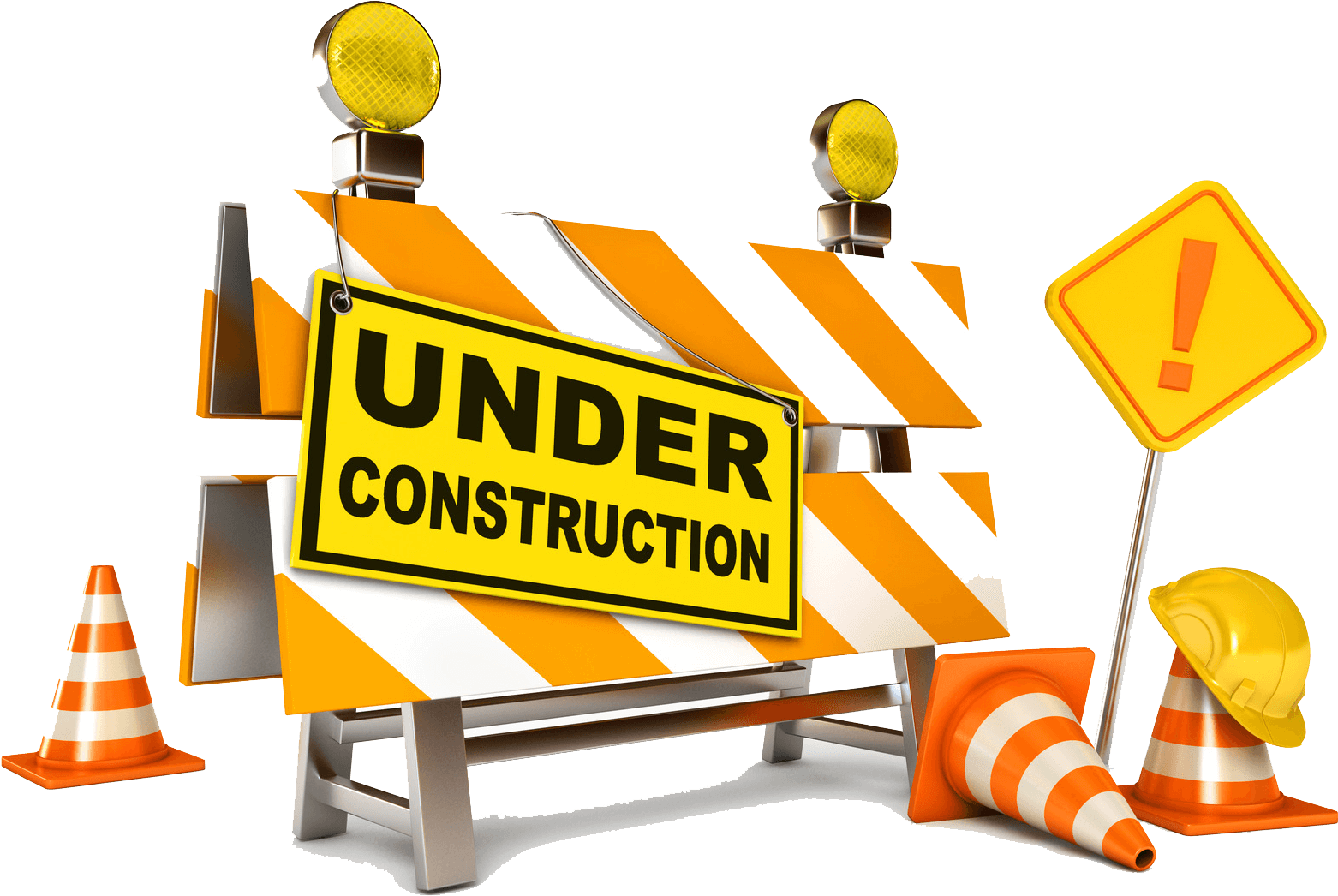
Case 13 – NAD 218THX Power Amplifiers + Speaker Death Story Time
It pains me to write this, but one of Perth’s better-known bad repairers has again made himself famous recently with a couple of higher-profile cases that destroyed a lot of gear and, in this case, ended up with him being scheduled to appear at the Fair Claims court here in Perth. These are covered here, in Case 13, and above, in Case 14. The original Mr RFW case was, of course, case #1!
This is the funnier of the two cases and probably the funniest case from 2021. So, Mr RFW recently ‘upgraded’ a pair of NAD 218THX power amplifiers. Based on what I’ve seen of his work, this can’t be good.
So he ‘upgrades’ the amplifiers and his customer collects them, takes them home and connects them back up to his expensive speakers, expecting to hear the glorious results of a Mr RFW upgrade. It was at this exact moment that Mr RFW’s telephone started ringing.
The customer had hooked them up, hit power, and then watched as smoke rose from where his tweeters used to be. These recently improved and upgraded examples of NAD’s finest incinerated his speakers at first turn on, within a couple of milliseconds.
The owner “wasn’t happy” and immediately rang the only person who had touched the amplifiers, Mr RFW. Mr RFW said, “No way, that’s impossible, bring the amplifiers back to me immediately.” That’s when things got funny. The customer returned to Mr RFW with his amplifiers and they set them up, this time with Mr RFW’s expensive speakers. Mr RFW was mumbling that it was impossible for the amplifiers to be faulty, etc.
Unfortunately (or perhaps fortunately, depending on how you view this), once again, the moment the NAD 218THX amplifiers flickered into life, smoke also billowed from Mr RFW’s speakers, where the tweeters used to be. He nearly fell over as he ran to turn the amplifiers off, but it was too late, his speakers had now also been incinerated. Mr RFW subsequently agreed that there was a ‘problem’ with the amplifiers.
This raises two fairly obvious points that I’ll mention for those who might not be quite there:
- If one tests a finished product like these amplifiers in the workshop before a customer hooks them up, faults can be caught before they do any damage. This must always happen. That’s why I always laugh when someone asks me if I’ve tested their equipment.
- One should only ever test an amplifier suspected of faulting with proper test and measurement equipment, NEVER with valuable speakers!
In the end, the customer’s amplifiers were written off because they were deemed to be beyond economic repair. The speakers were repaired, at great cost to the owner. I don’t know what happened to Mr RFW’s speakers.
Why don’t these reviews appear anywhere on Mr RFW’s site or profile?!
Case 12 – Accuphase C-280 Preamplifier
As an independent specialist who works on a lot of Accuphase gear and LOVES this equipment, nothing pains me more than seeing the damage wrought on a stunning preamplifier like this Accuphase C-280.
This is a case from 2020, my role here was to inspect this new acquisition (one of our services) and advise on how to proceed.
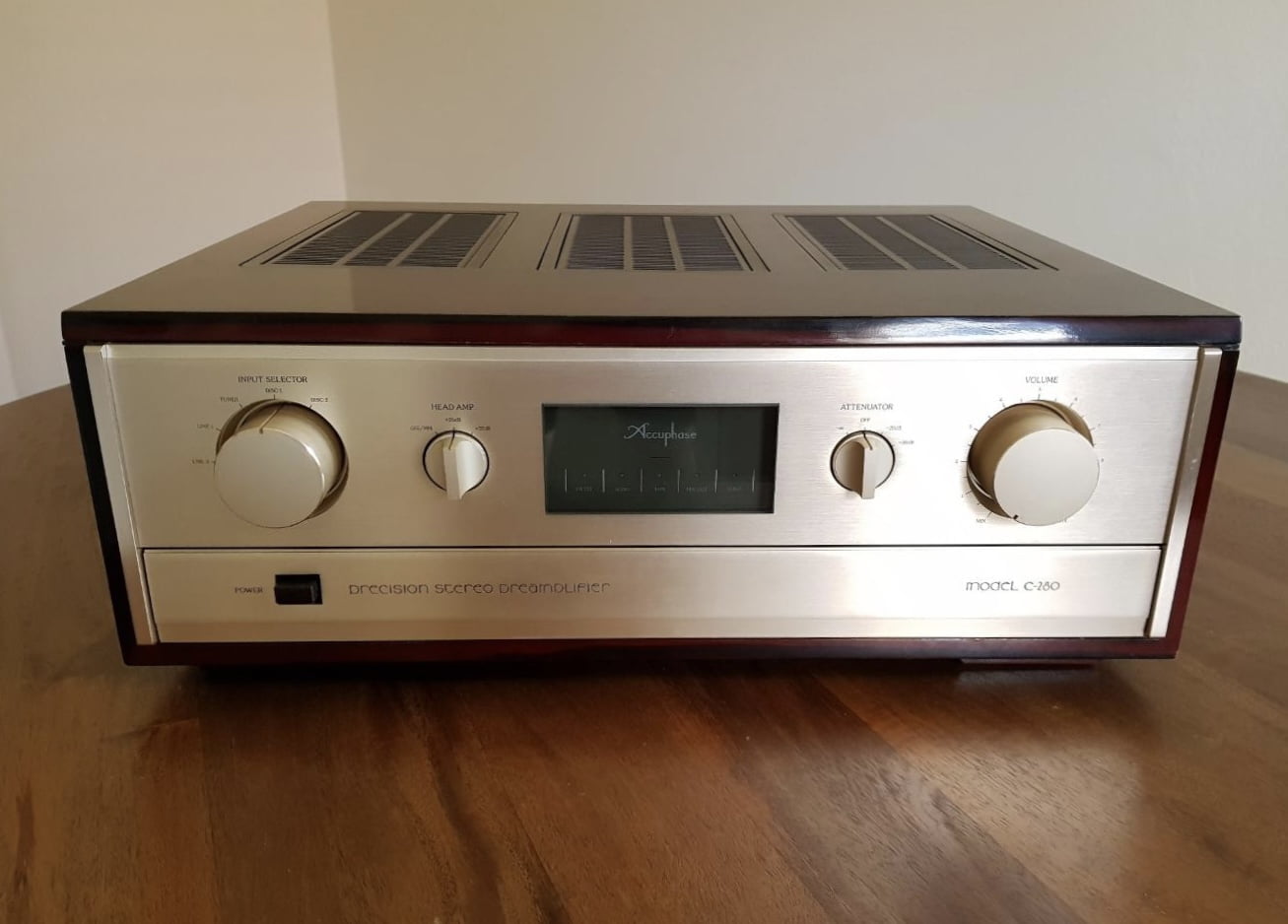
This one was purchased by a customer of mine from a seller in Adelaide a couple of years ago. The seller seemed like a nice enough fellow, but like so many beautiful pieces of gear, this C-280 had a story, part of which involved her visiting the wrong people.
I’ve worked on quita e few pieces of Accuphase equipment that have come from Adelaide and all been botched in some way, so that’s concerning. I don’t know if they are all from one source, but this lovely old girl had visited one of the better-known hi-fi repairers in Victoria. I never did quite get the full story about what happened here, but I heard a couple of different versions via the seller and her new owner.
When I saw this Accuphase C-280, she still didn’t work properly, though she now had a detachable mains cable, some craptacularly bad capacitors and bodgy soldering. What this preamp didn’t need was a detachable mains cable, bad caps and crappy soldering. She needed care and thoughtful maintenance focused on actually improving performance and resolving issues rather than adding useless features.
Bling. Not important. Good condition, originality, sound and performance are VERY important.
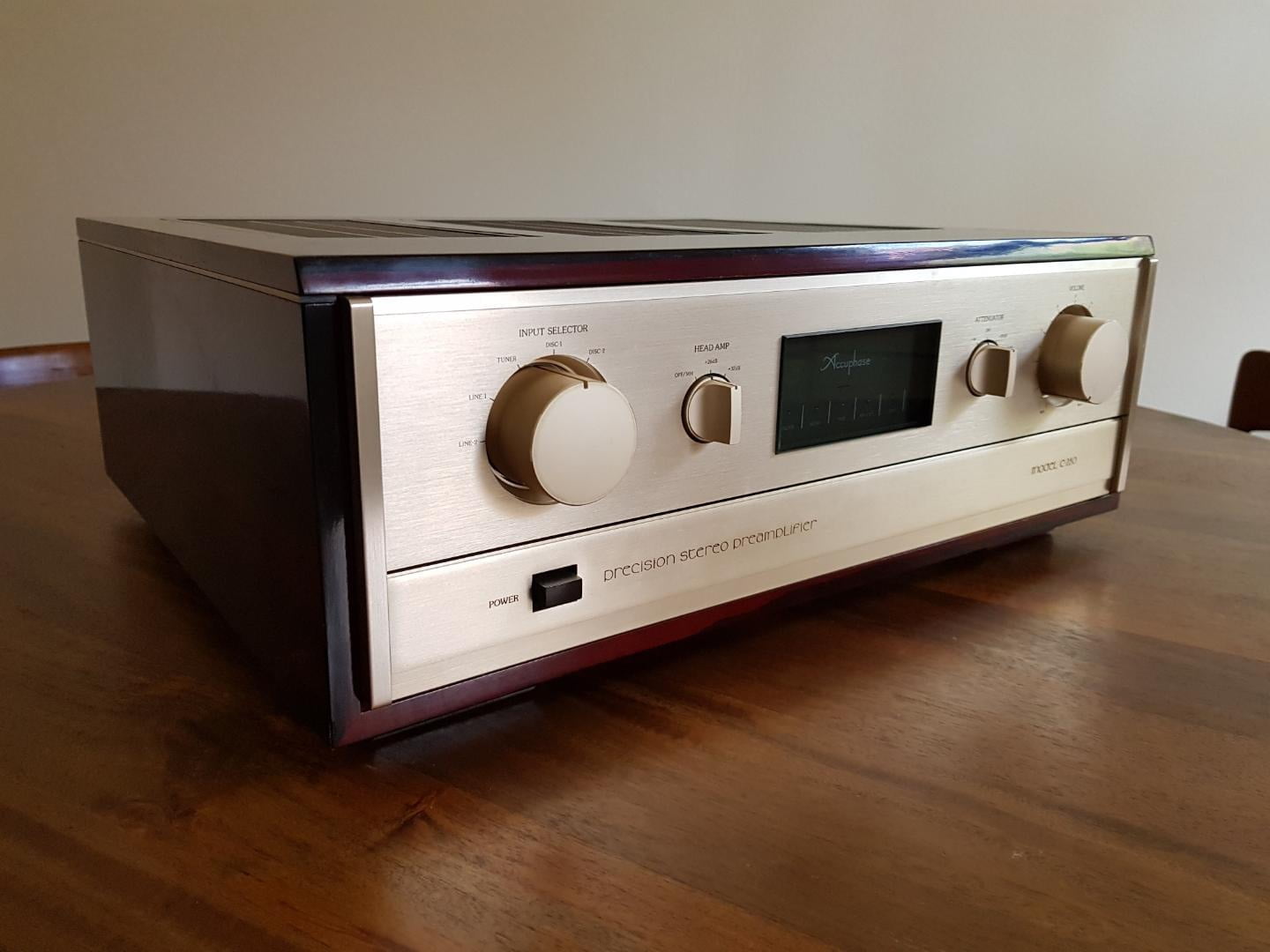
The first sign of trouble was that detachable cable and added-in IEC mains inlet. People often mistakenly have these installed after they are told that aftermarket mains cables are better/essential/God-like etc. What they aren’t told is that a hard-wired cable is potentially better and an original hardwired Accuphase cable is a very good cable. Why not? Well that doesn’t sell cables, does it? What’s the best connection? A hard-wired connection, ie, no connector at all, and good cable of course.
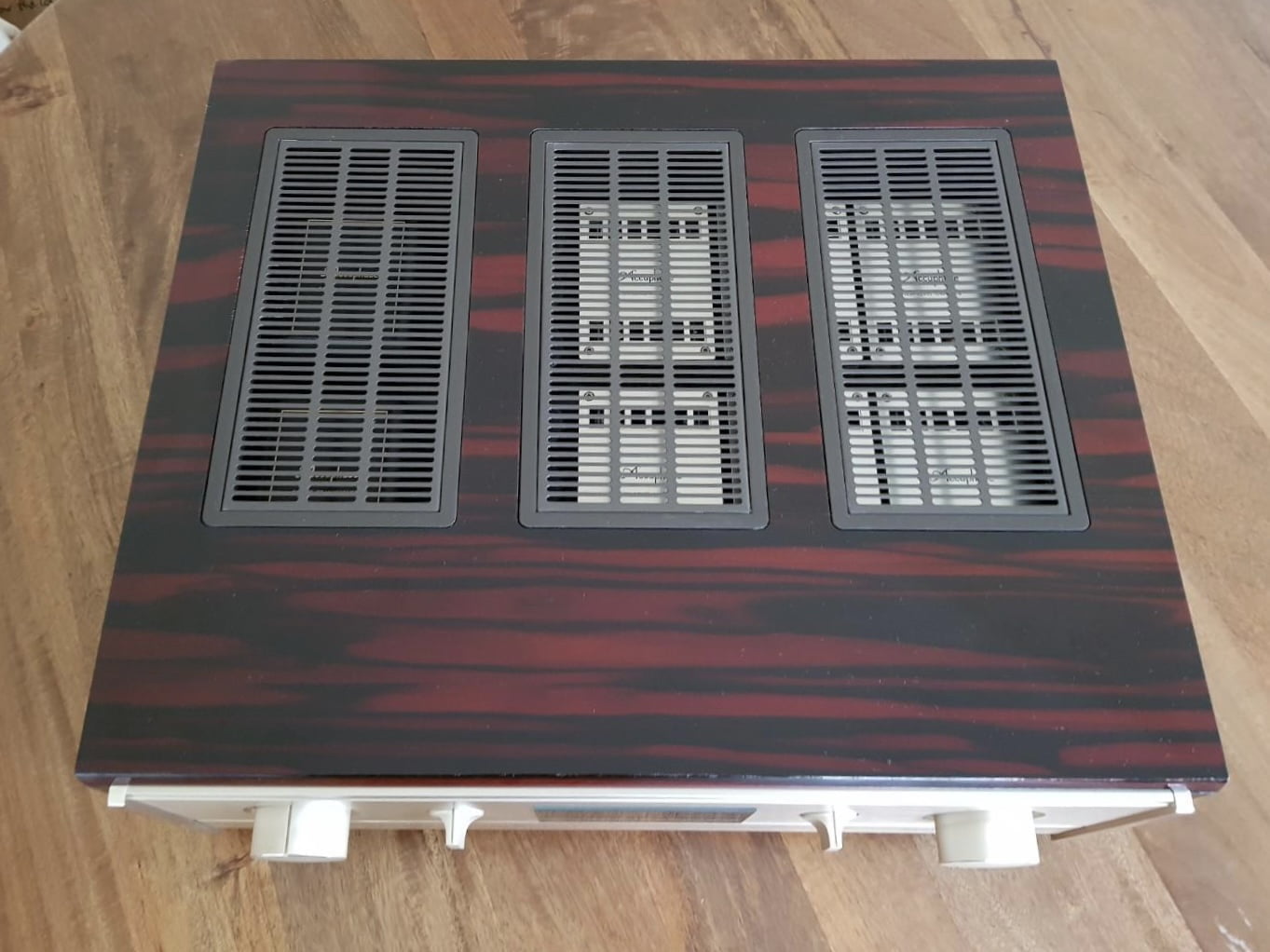
Taking the preamp out of its wooden chassis sleeve, I quickly found signs of poor work:
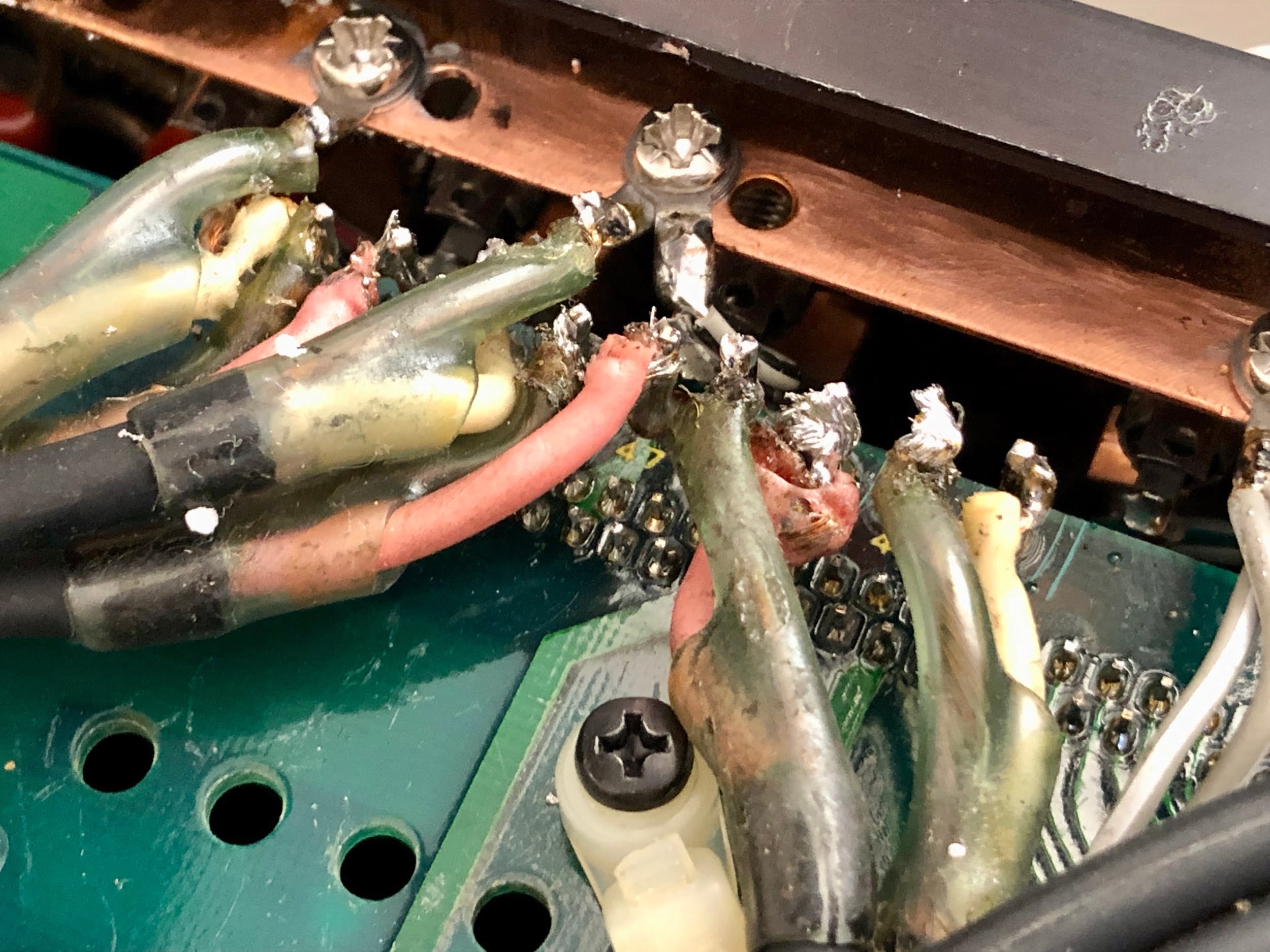
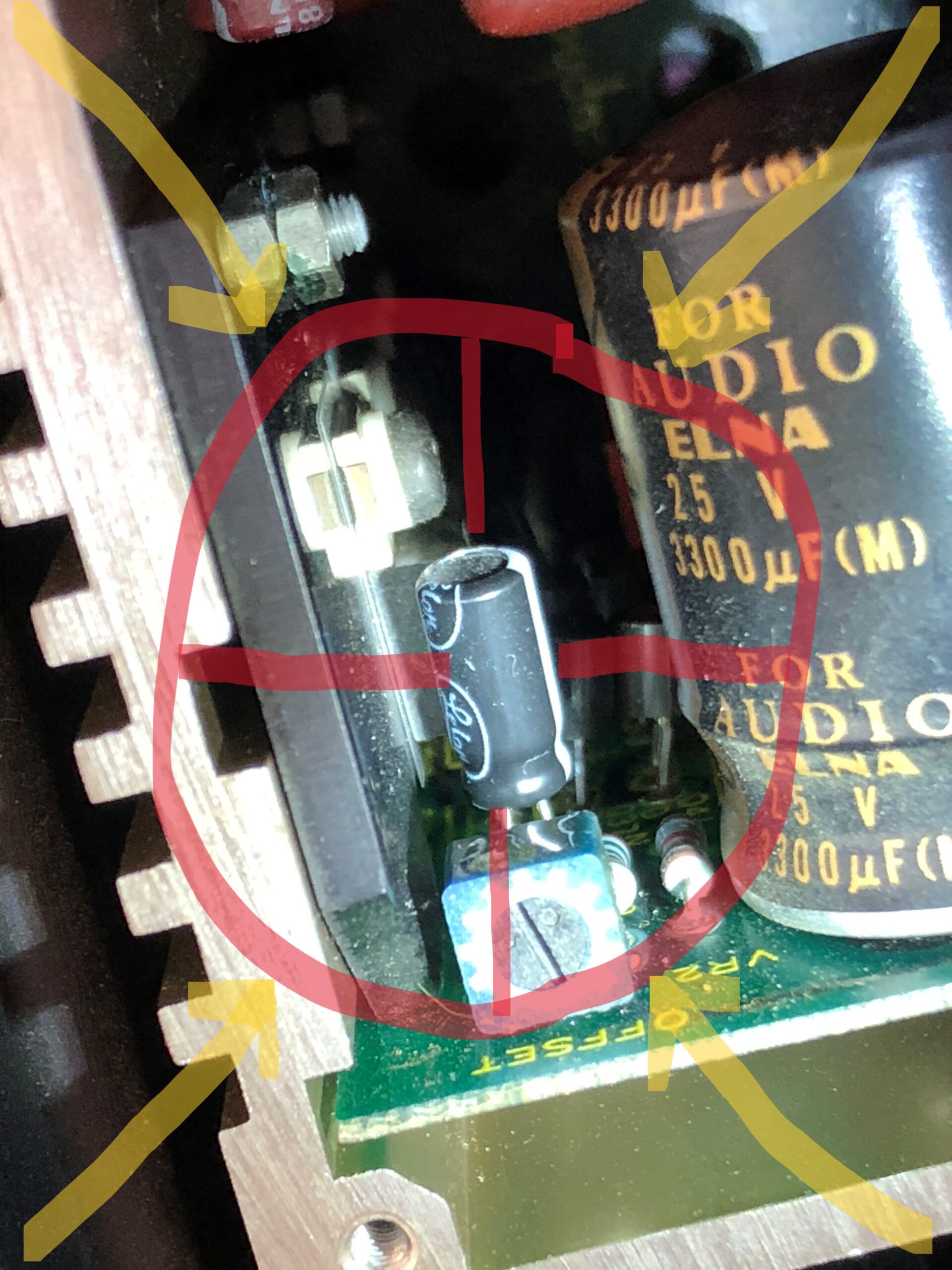
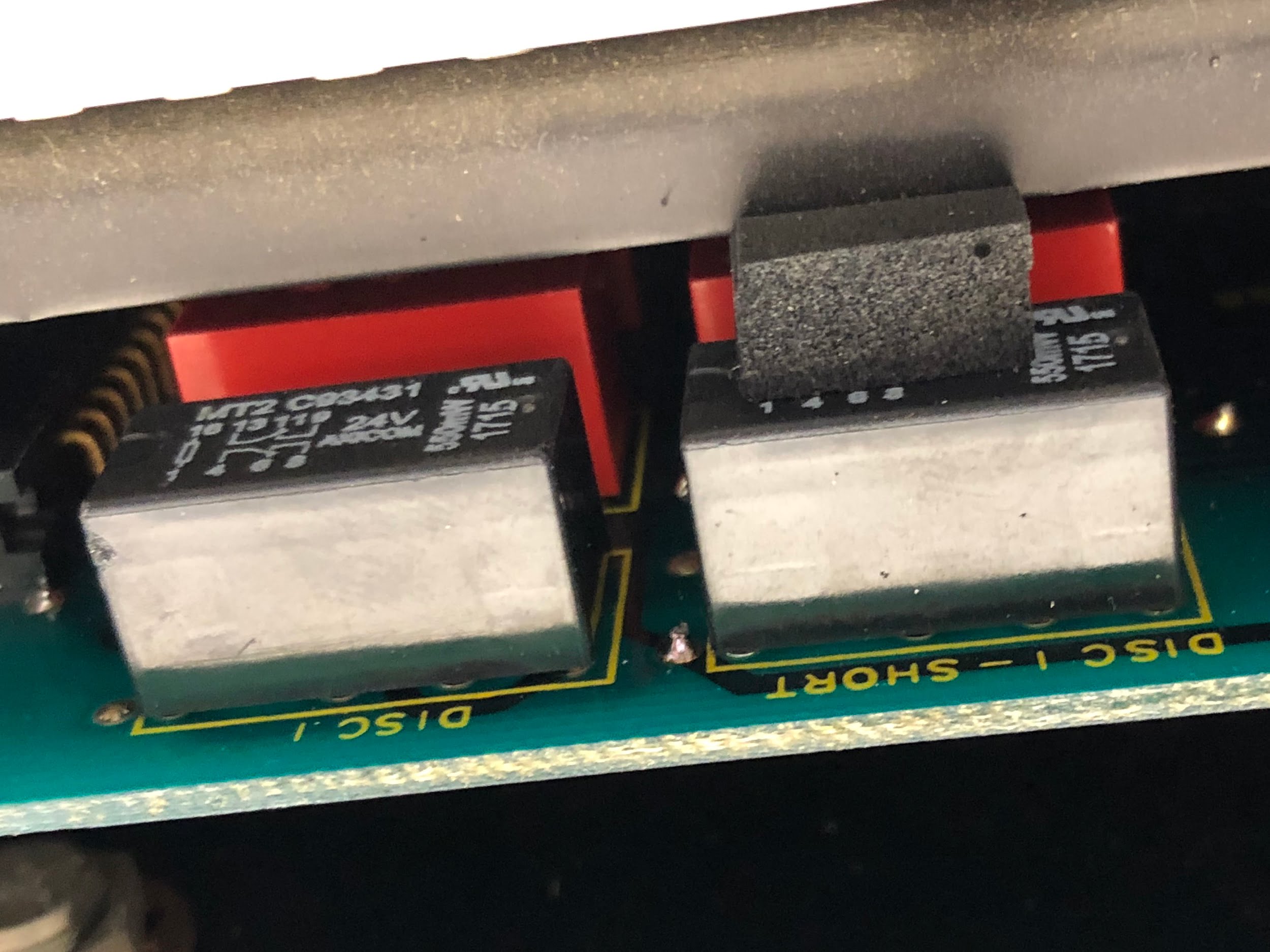
I showed my customer the areas of concern and work that would be needed. Ultimately, this beautiful Accuphase C-280 preamplifier needed a lot of work, including rectification of the problems we see here, and a full overhaul at this age. My customer didn’t want to go down that path, he decided to move it on and I think that was a sensible decision.
Learnings
There are two takeaways here. Many technicians are ill-equipped to work on gear like this. You’ll have to trust me on this but a look around here will help you understand this point. If you want one of these spectacularly good preamplifiers, you want one that either hasn’t been worked on or that’s had the least invasive and neatest possible work done.
Case 11 – Denon PMA-1060 Integrated Amplifier
Sadly, we have yet another case of someone who shouldn’t go anywhere near a soldering iron, this time “upgrading” this classic Denon PMA-1060 integrated amplifier and then selling it on Gumtree. The individual who does this work is located in Perth’s southern suburbs, Wellard I’m told, by the unfortunate new owner of this beautiful integrated amplifier.
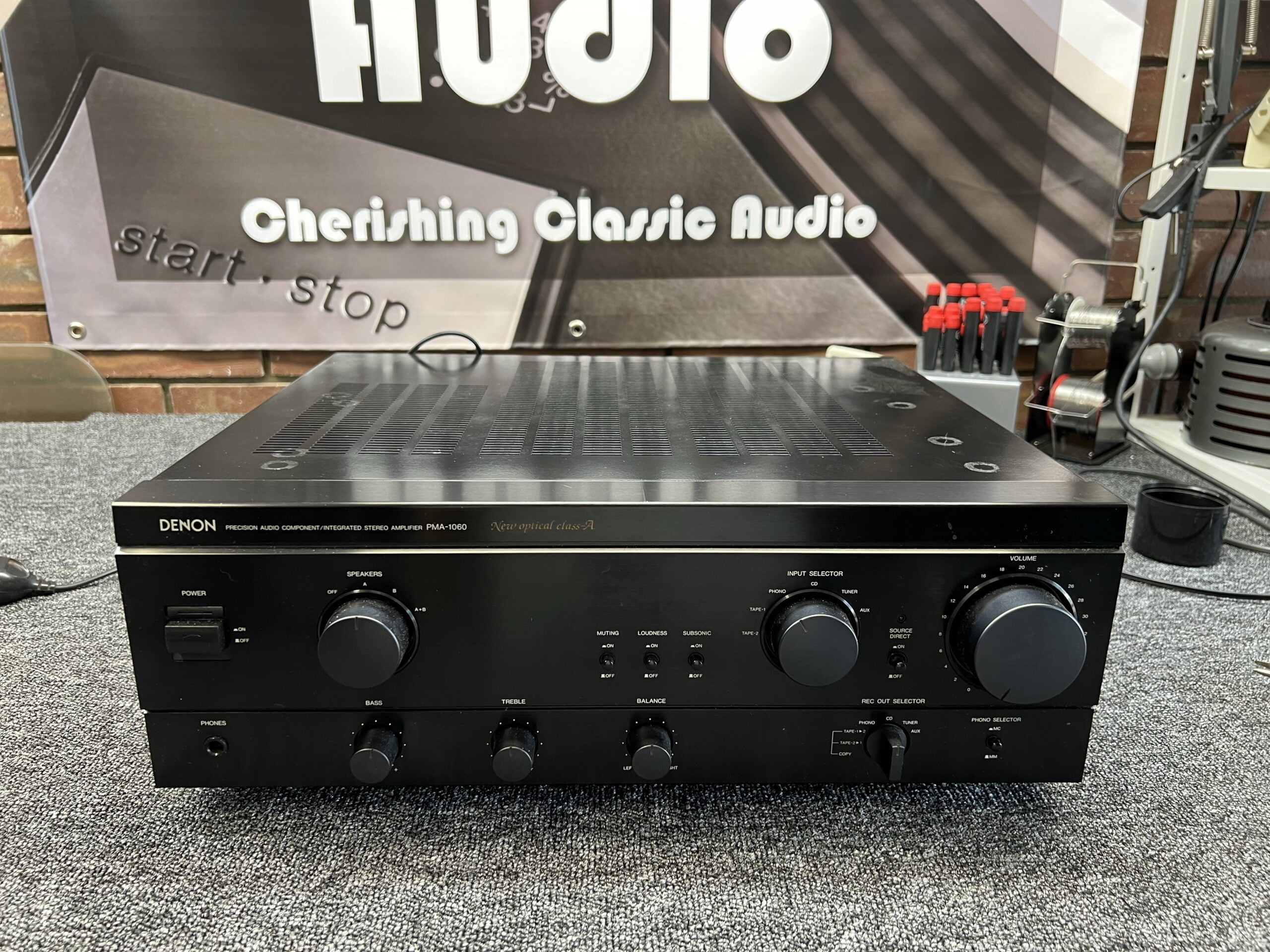
In this case, the filthy dirty amplifier was not cleaned and left with most of its dust, grime and mud installed. Whoever did this simply worked around the muck and used a cotton bud here and there in a vain attempt to clean, then damaged the main board, badly installed various audio grade caps and either made no or incorrect electronic adjustments.
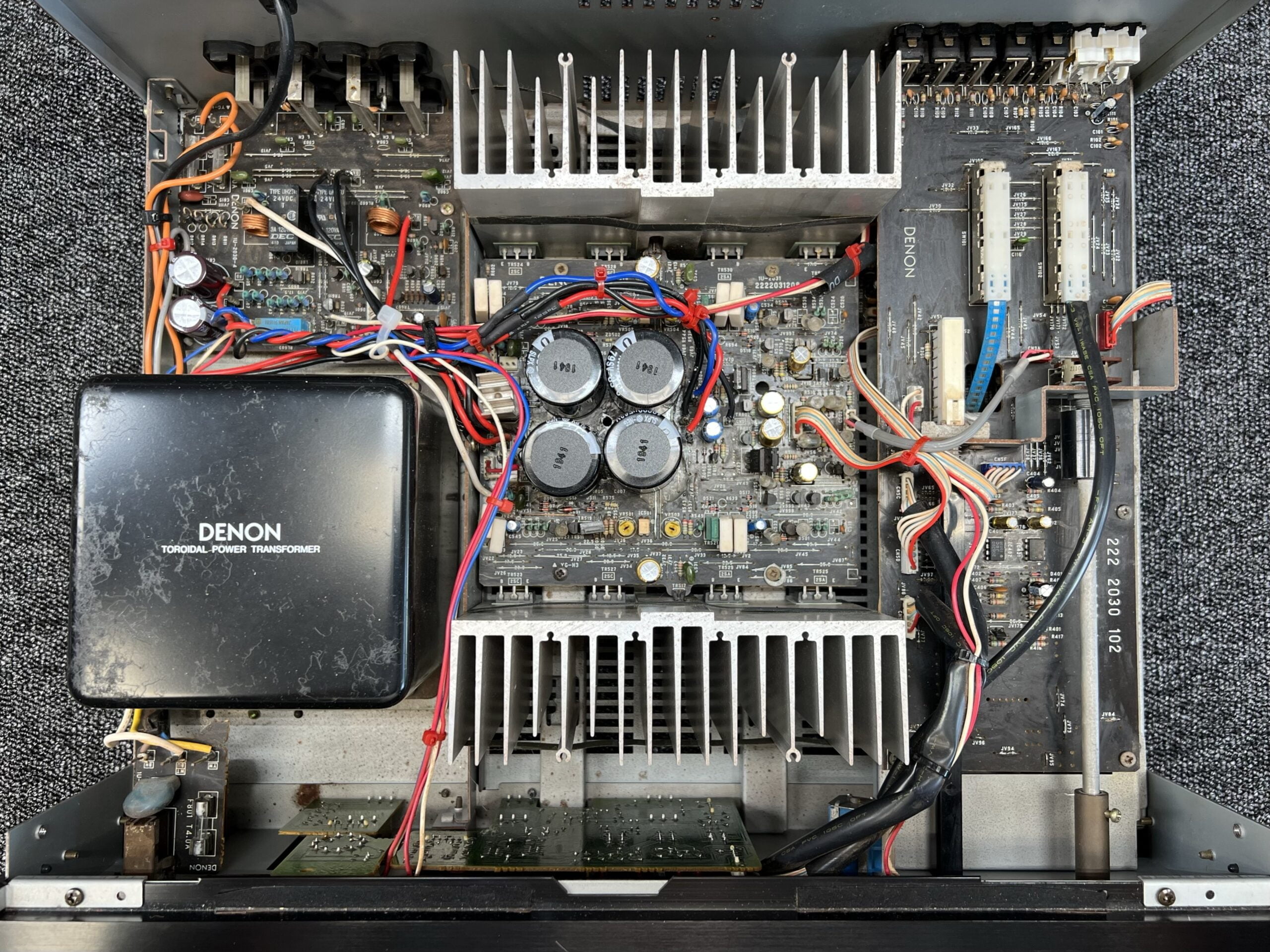
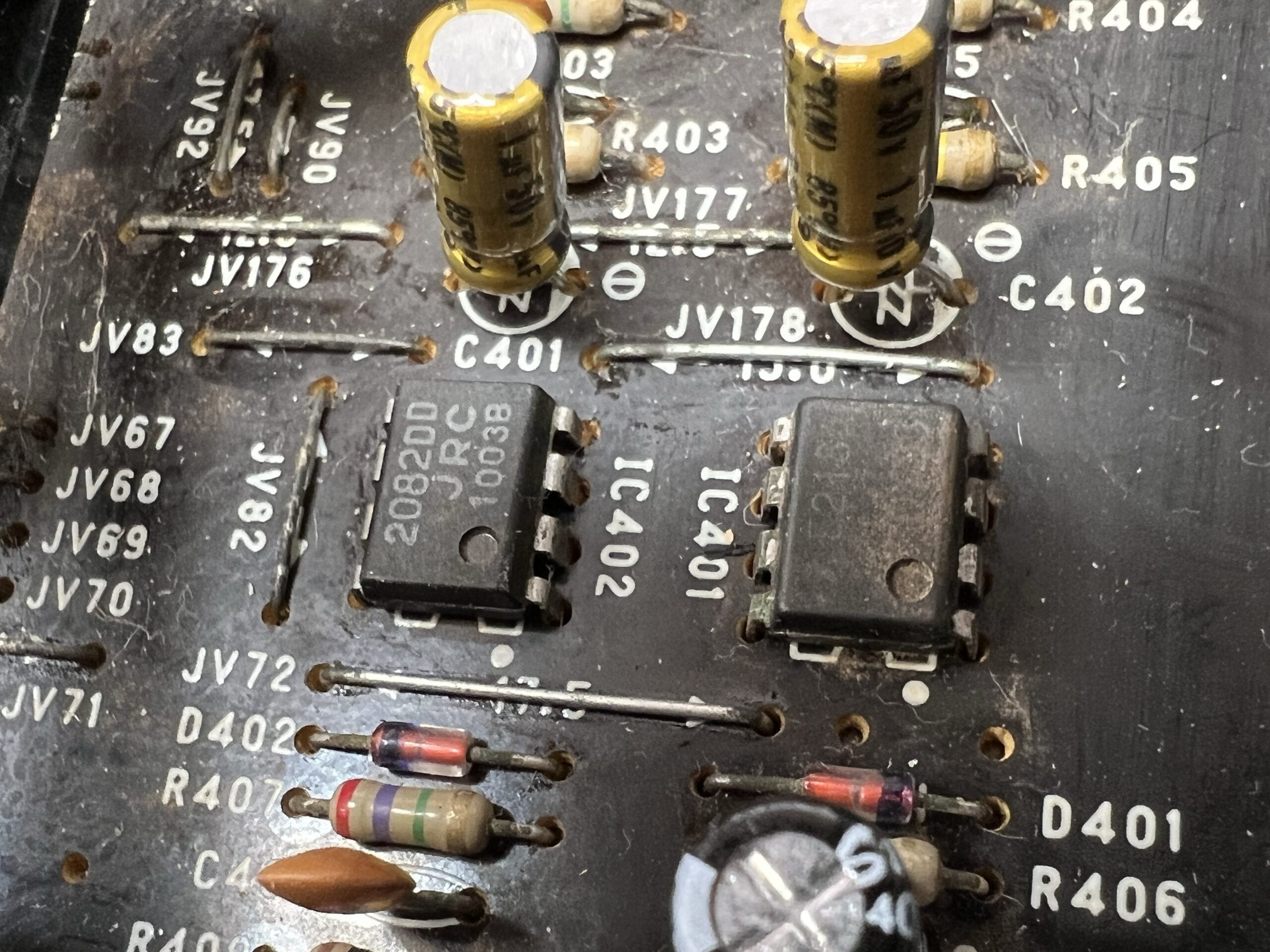
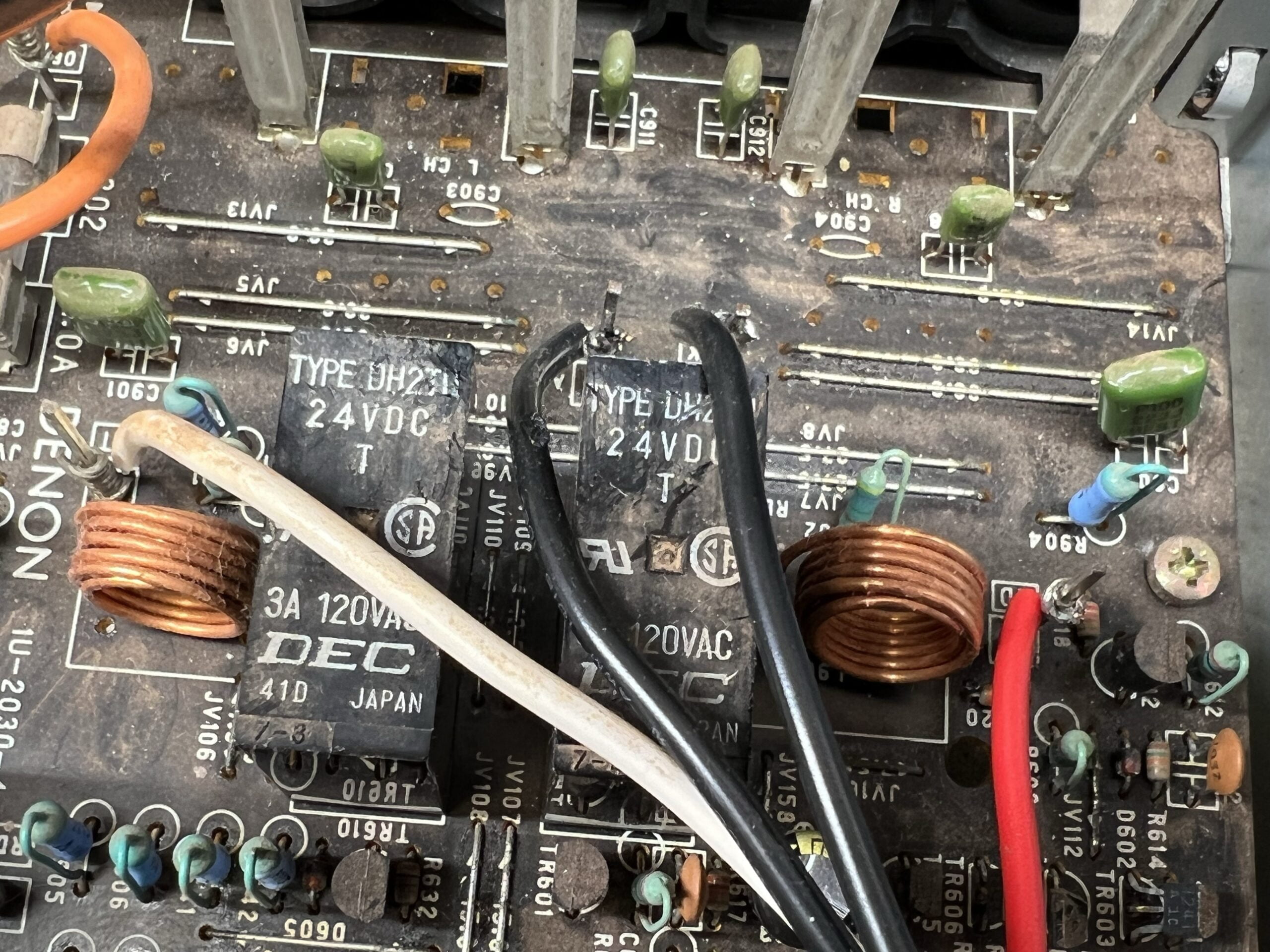
The owner brought it to me and I had to pass on the bad news. It was running on one channel, the quiescent current was way out and the trimmers for setting it were so clogged up with dirt that moving them slightly caused massive jumps in bias that threatened to kill her output devices. Scary stuff.
Setting bias on a Denon amp like this is a two-stage process and one that was unfortunately beyond the comprehension of whoever did this. Trimmers have to be clean and power consumption should always be monitored whilst adjustments are made.
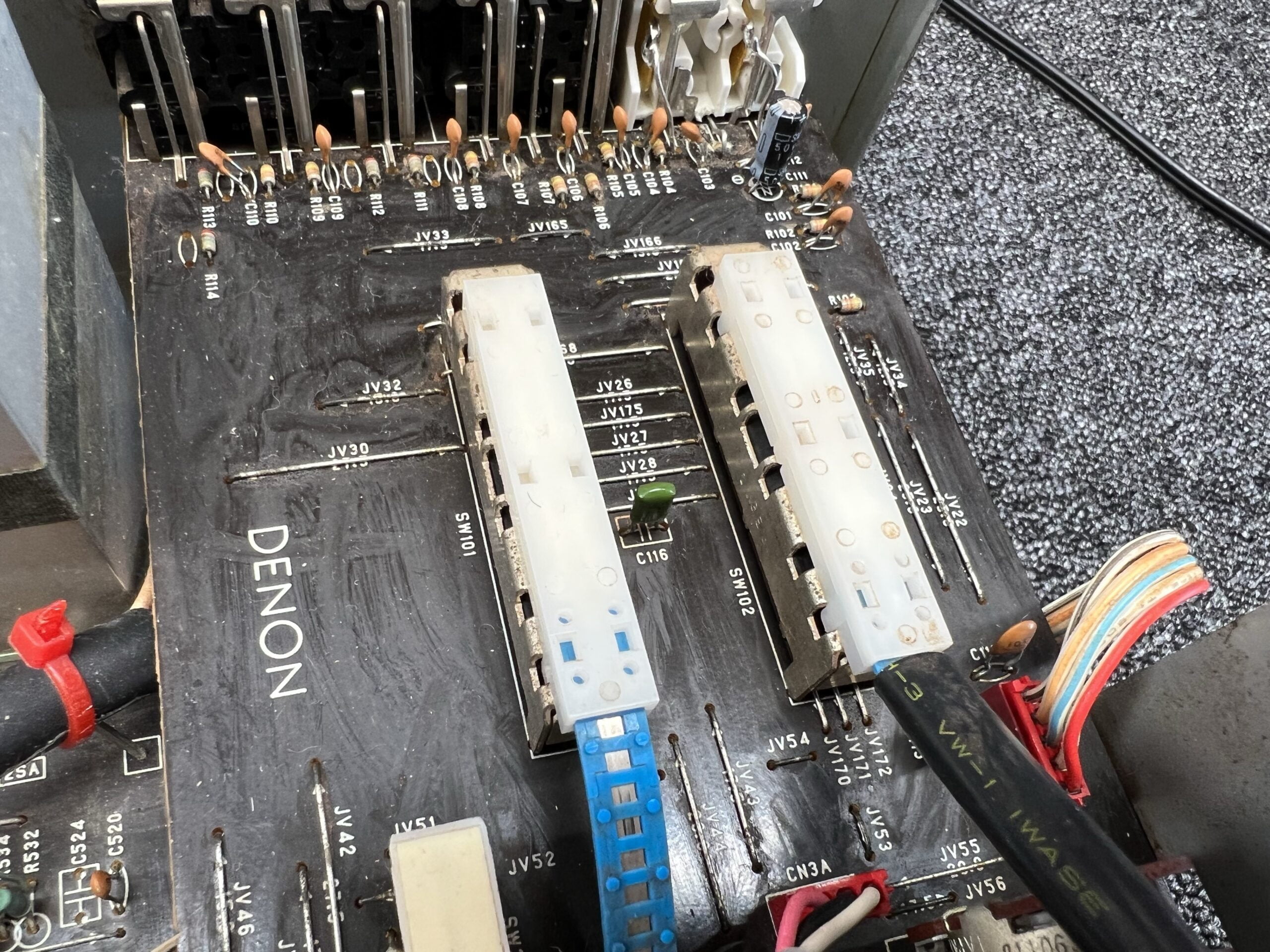
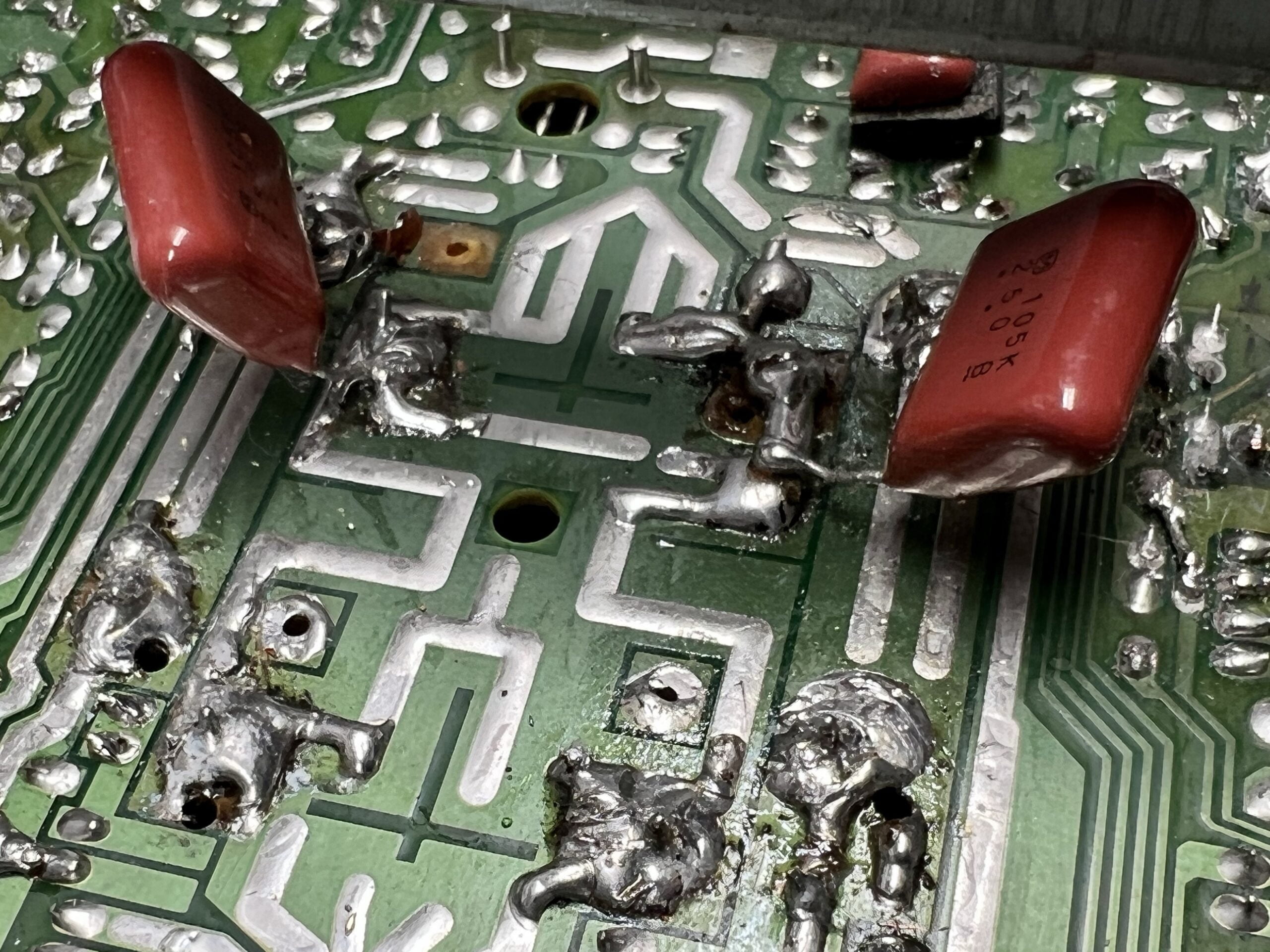
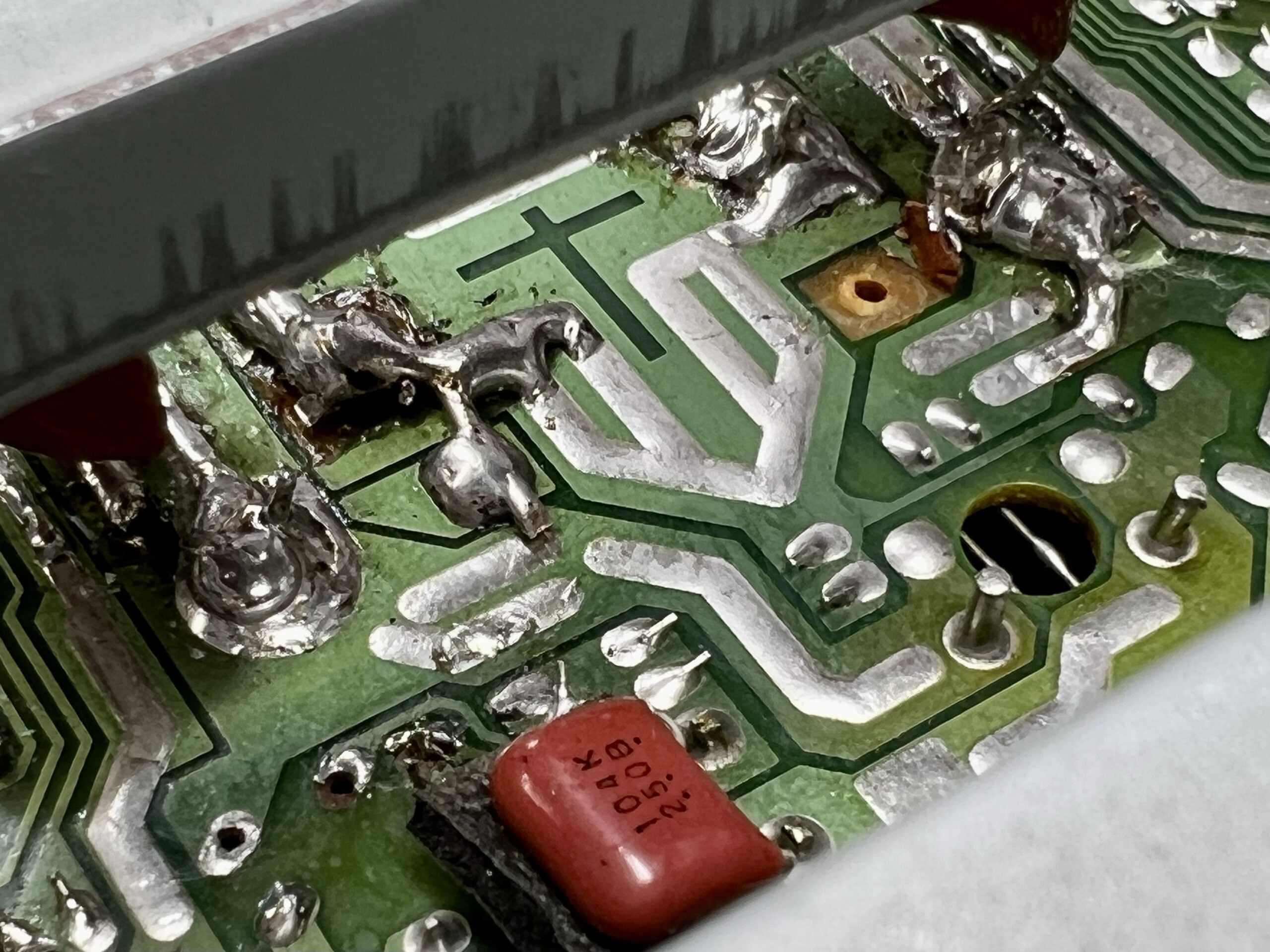
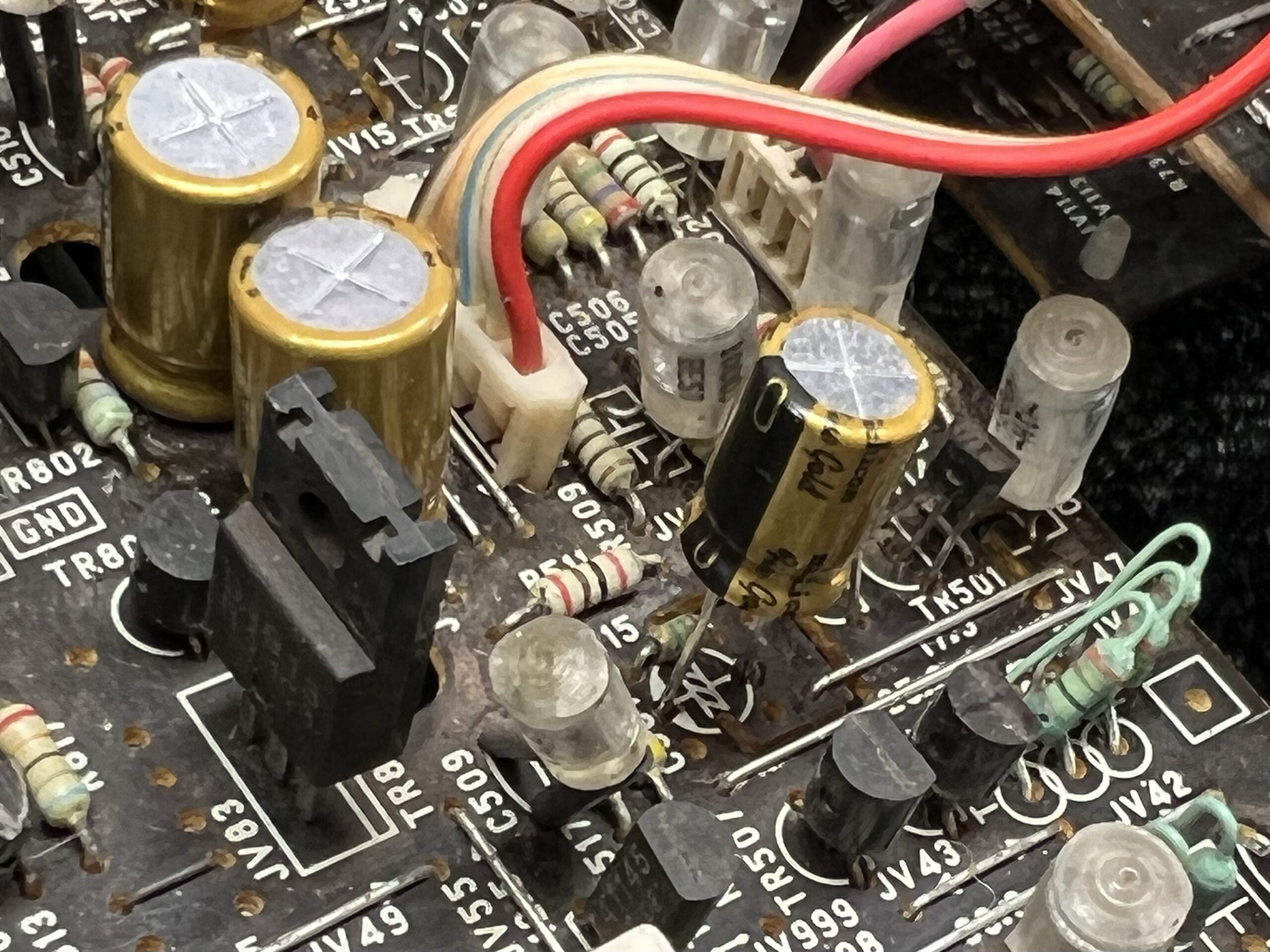
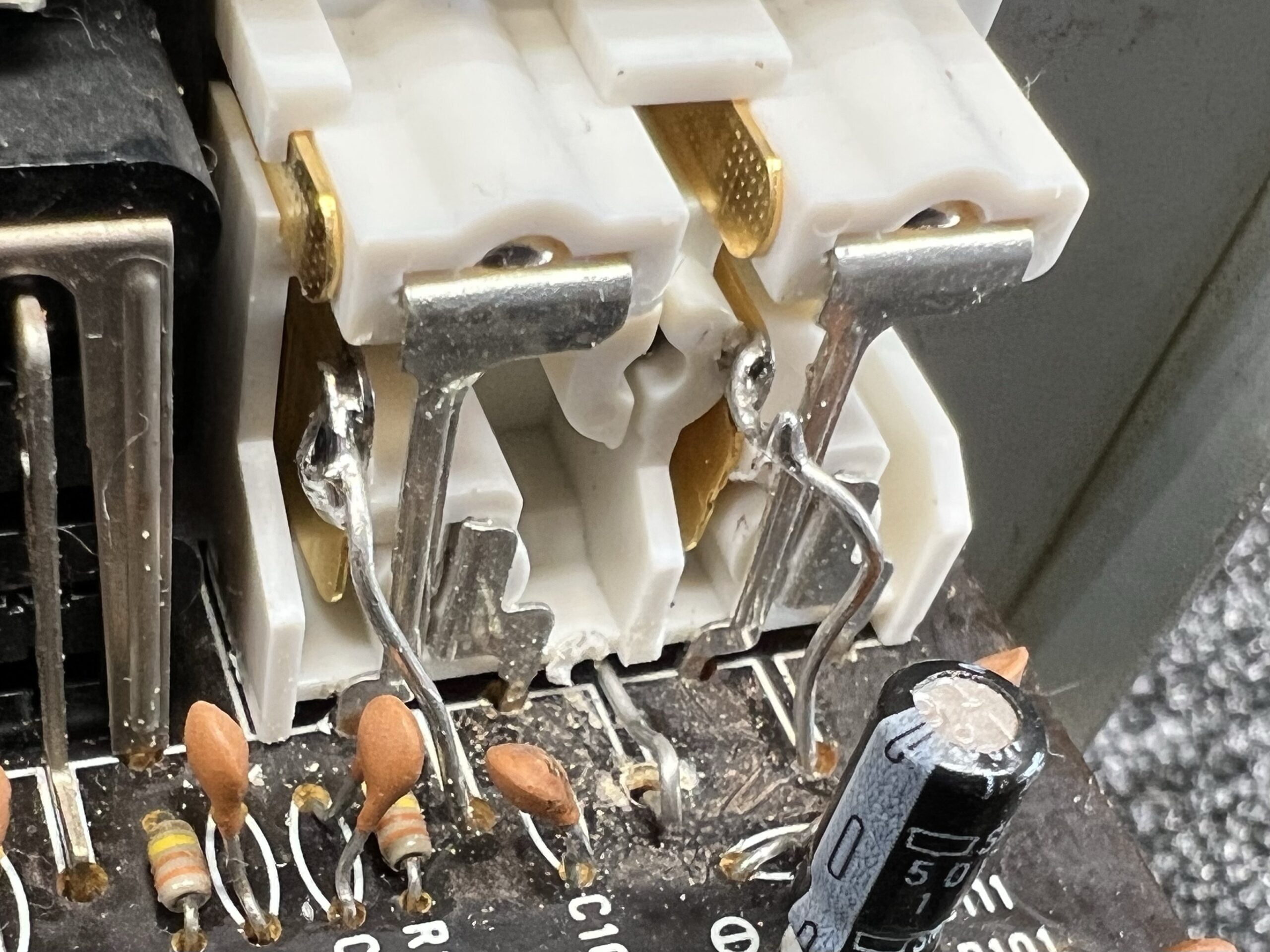
At least I was able to get this Denon PMA-1060 running well, idling stably. I resolved the absent channel and scary bias trimmer issues. I did not tackle the cleaning. Keep in mind that gear that arrives like this is not my problem to take on. My goal is to help the owner, but not reverse the damage done by others in most cases. In this instance, I could best serve this owner by repairing the amp to restore full functionality, which I did, and then advising him to move it on, which I also did. He was very appreciative, though understandably annoyed at the seller.
Learnings
Be very wary of a Gumtree seller in Perth’s southern suburbs (Wellard). This is one of the worst pieces I’ve seen in a while in terms of general internal condition. Whoever did this needs to find another hobby or seek out some professional assistance to get him on the right track. If you are reading this, Wellard man, you are destroying equipment. Stop doing it.
Case 10 – Gryphon DM100 Class-A Power Amplifier
This is another sad story that forces you to drop your head to your hands, Piccard-style and breathe, deeply. I’m sorry to have to say this, but owners of equipment like this stunning Gryphon DM100 bear some responsibility for how they look after their equipment, and who they take it to.
Note: I’m not victim-blaming the owners for what happened, they wouldn’t have chosen to have their amplifier butchered like this. However, after talking with the current owner, it seems that people tried to save money with this lovely amplifier by having work done on the cheap. What you’re about to see is the result of that misguided approach.
We all have to exercise discretion and good judgment. With any amplifier like this, speak to a few people, get some perspective, and talk with respected repairers who work on this sort of equipment. See if ANYBODY recommends getting cheap work done on something like this.
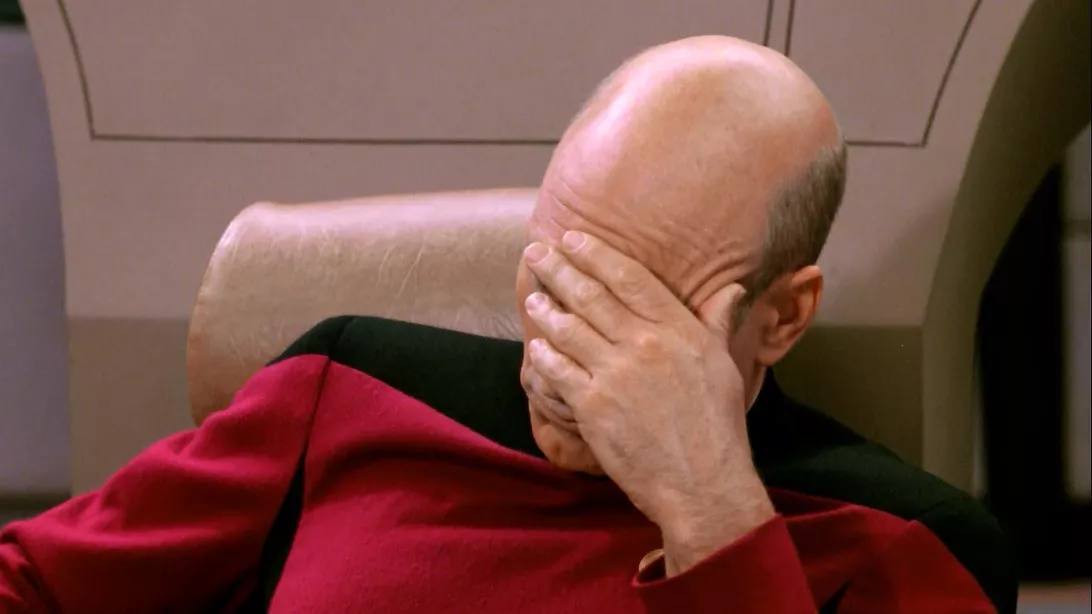
Equipment like this Gryphon DM100 simply MUST go to a competent, well-regarded repairer. I don’t just mean someone who has a website and a few Google reviews, I mean someone who others know can tackle gear like this. Sending this amplifier to a TV repair guy or outer suburbs ‘VCR guy’ is like taking your Ferrari to a country petrol station for service. I’m afraid it’s just utterly silly and will only ever end badly.
For most, all of the above will seem obvious, so I apologise for hammering the point. The bigger question, therefore, is: how does a stunning, rare and irreplaceable piece of Danish hi-fi history end up with a boondocks repairer anyway? In most cases, it’s because someone was trying to save money, or a repairer misleadingly said they could fix it.
How the saving money equation makes sense to people is beyond me, but it’s common. I’ve had customers baulk at spending a few hundred dollars on a Krell preamplifier repair. People often just don’t want to spend money, even on a $50,000 amplifier. This is of course ridiculous, but I’m sure most of us have seen a Rolls Royce at a Kmart Tyre and Auto and wondered why. One can only educate and perhaps influence things a little, by raising awareness with articles like this one.
I’m sure the guys at Gryphon aren’t amused. I’m sorry guys, I tried with this one and lost money on it too. I couldn’t risk all the problems with it suddenly becoming my problem.
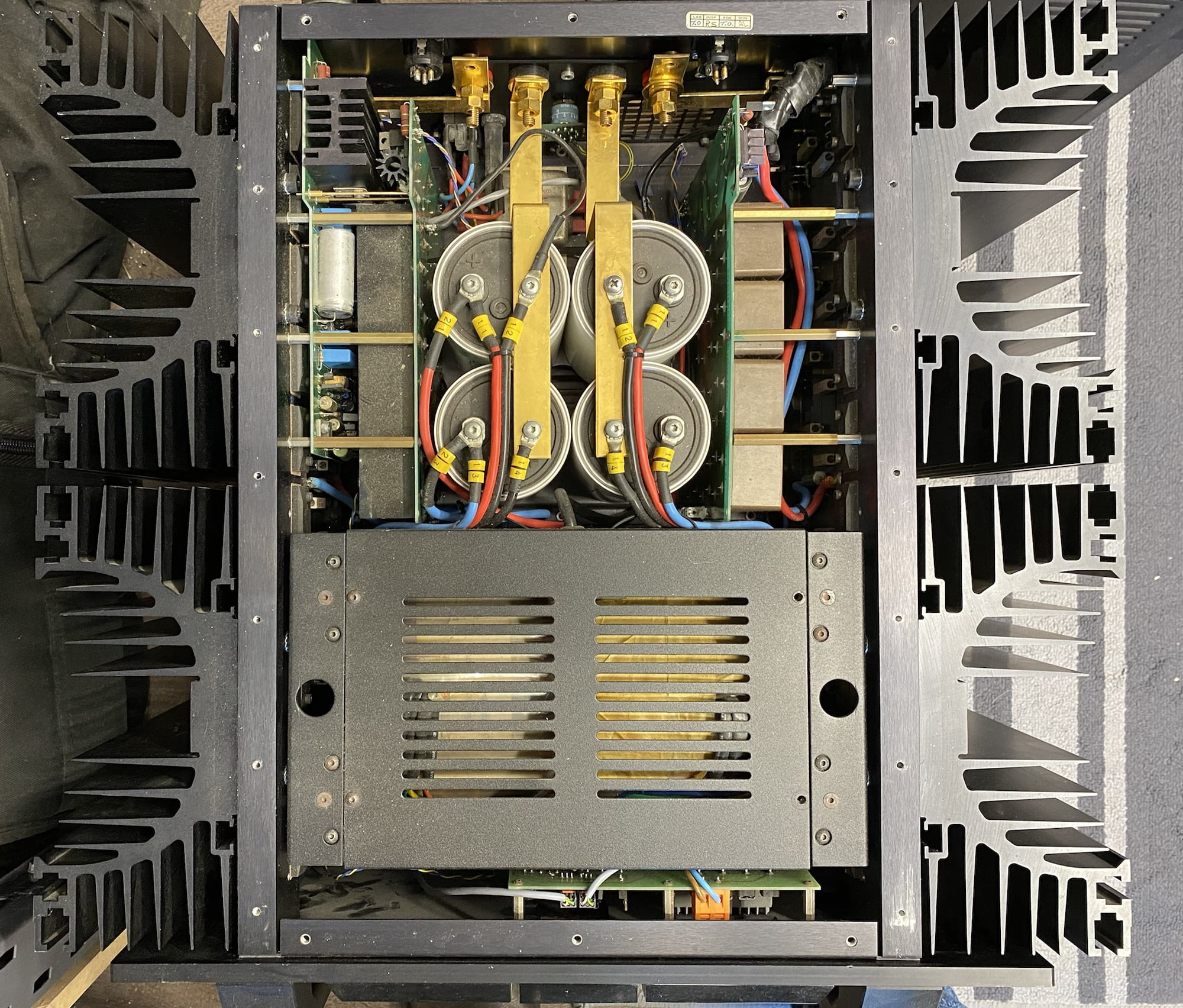
Speaking of Krell, Gryphon is a Danish high-end hi-fi equipment manufacturer, one of the best-regarded in my opinion and a company that produces some stunning gear. For me, they are a Danish Krell, if that makes sense. Similar design ethos, similar build, and a similar need for the right attention and maintenance.
The Gryphon DM100 is, without a doubt, one of the great class-A power amplifiers. It weighs 76kg or 168 pounds. It was Gryphon’s first power amplifier and a true statement piece. As such, it’s a rare piece of audio and Gryphon history. You can read more about it here, and here.
It’s a minimum two-man lift and, if you read my articles, you’ll know what that means. These amplifiers are a $10K seller all day long. Replacing it would set you back $50K+, and for that money, you’d likely end up with something not as good as this beautiful old girl. I thought my old Krell KSA-150 class-A amplifier was a beast. It was, but this DM100 goes to 11. You can probably see where this is going.
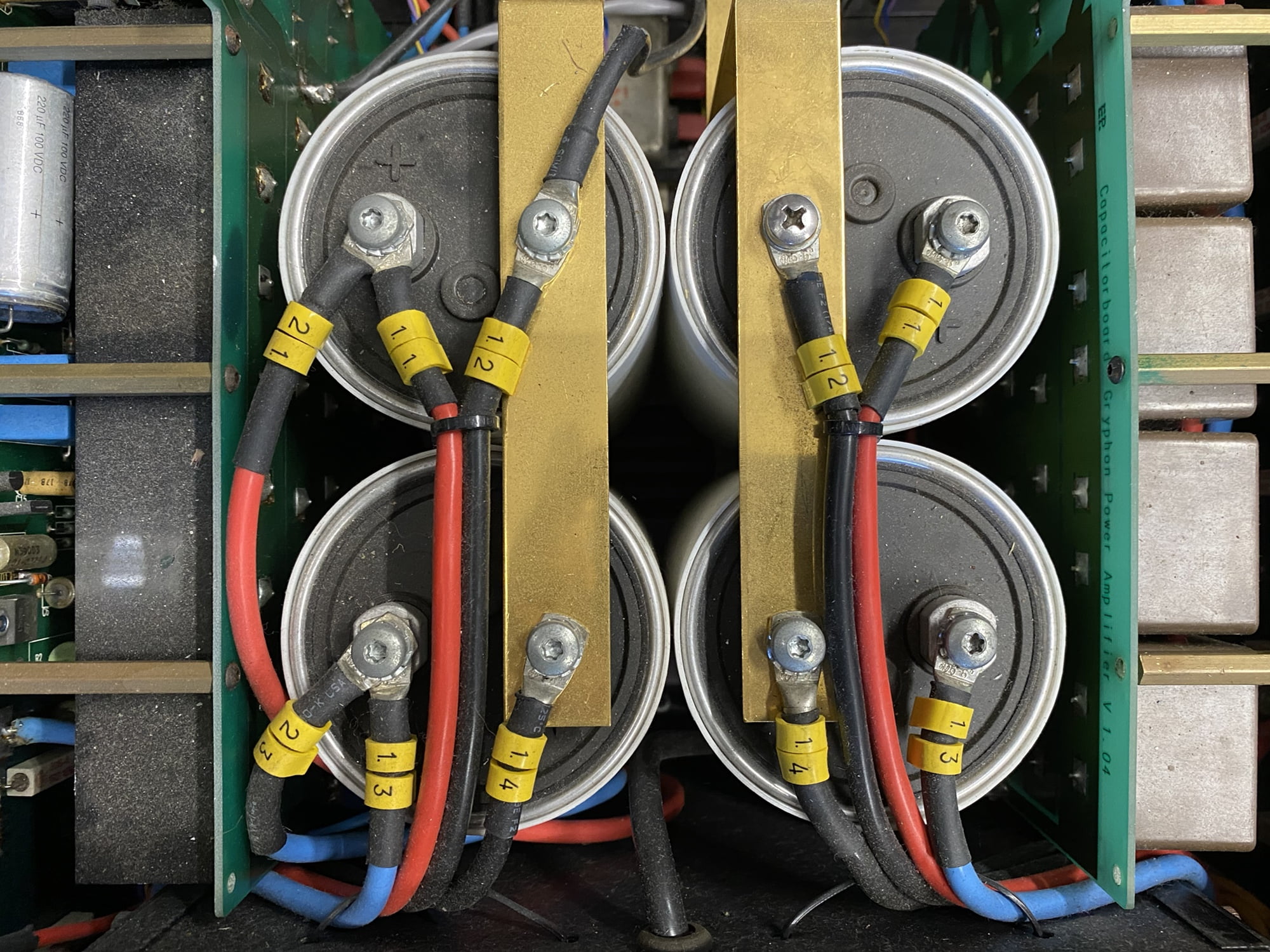
As the owner of a beautiful piece like this, you have a responsibility to properly care for it. When you see what was done to this stunning amplifier, you’ll appreciate the irony of trying to save money repairing it. Far from saving anything, this cost someone, BIGTIME. This amp is effectively a write-off and Gryphon didn’t make many of them. All that needed to happen was for it to go to the right repairer.
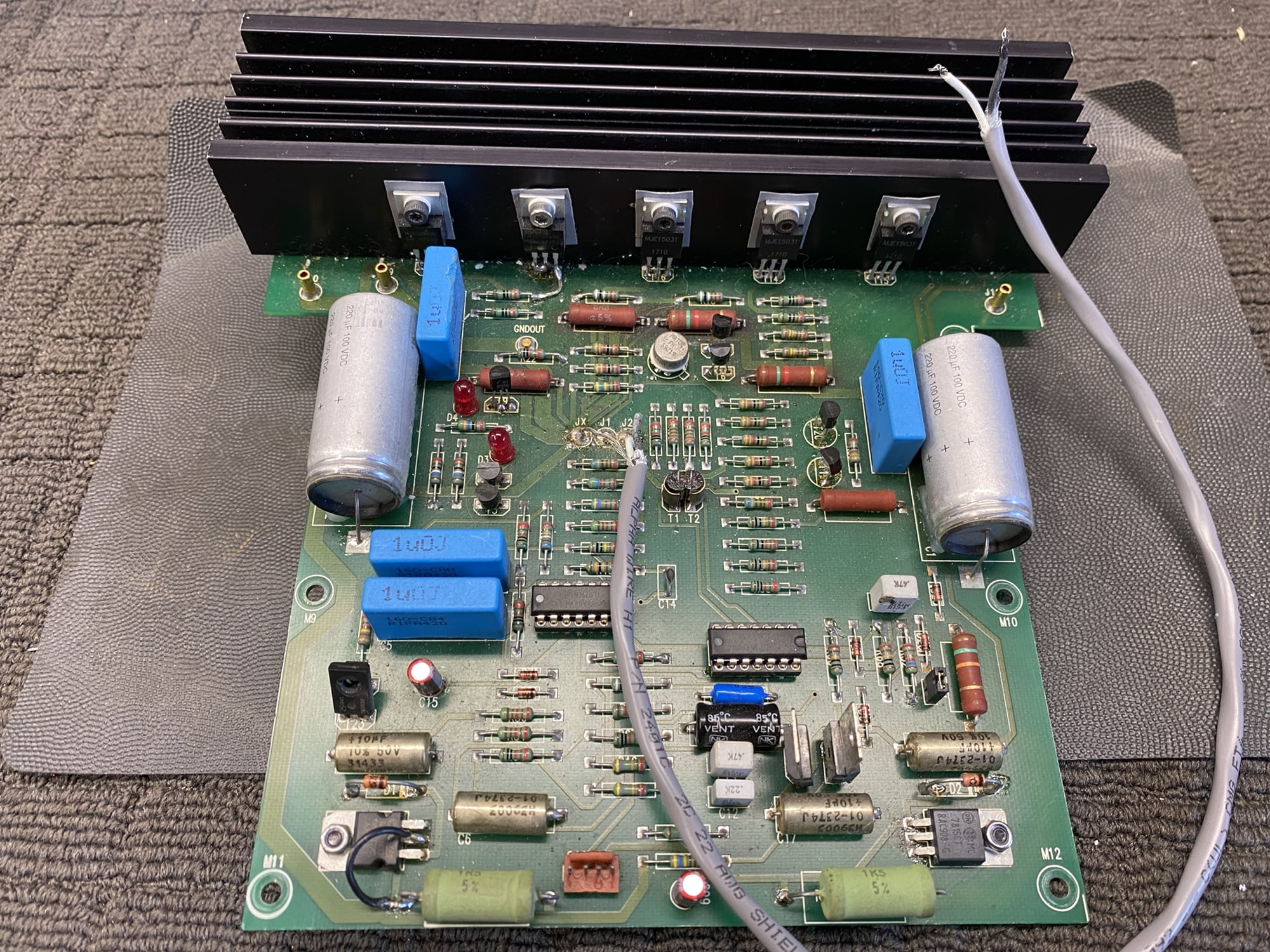
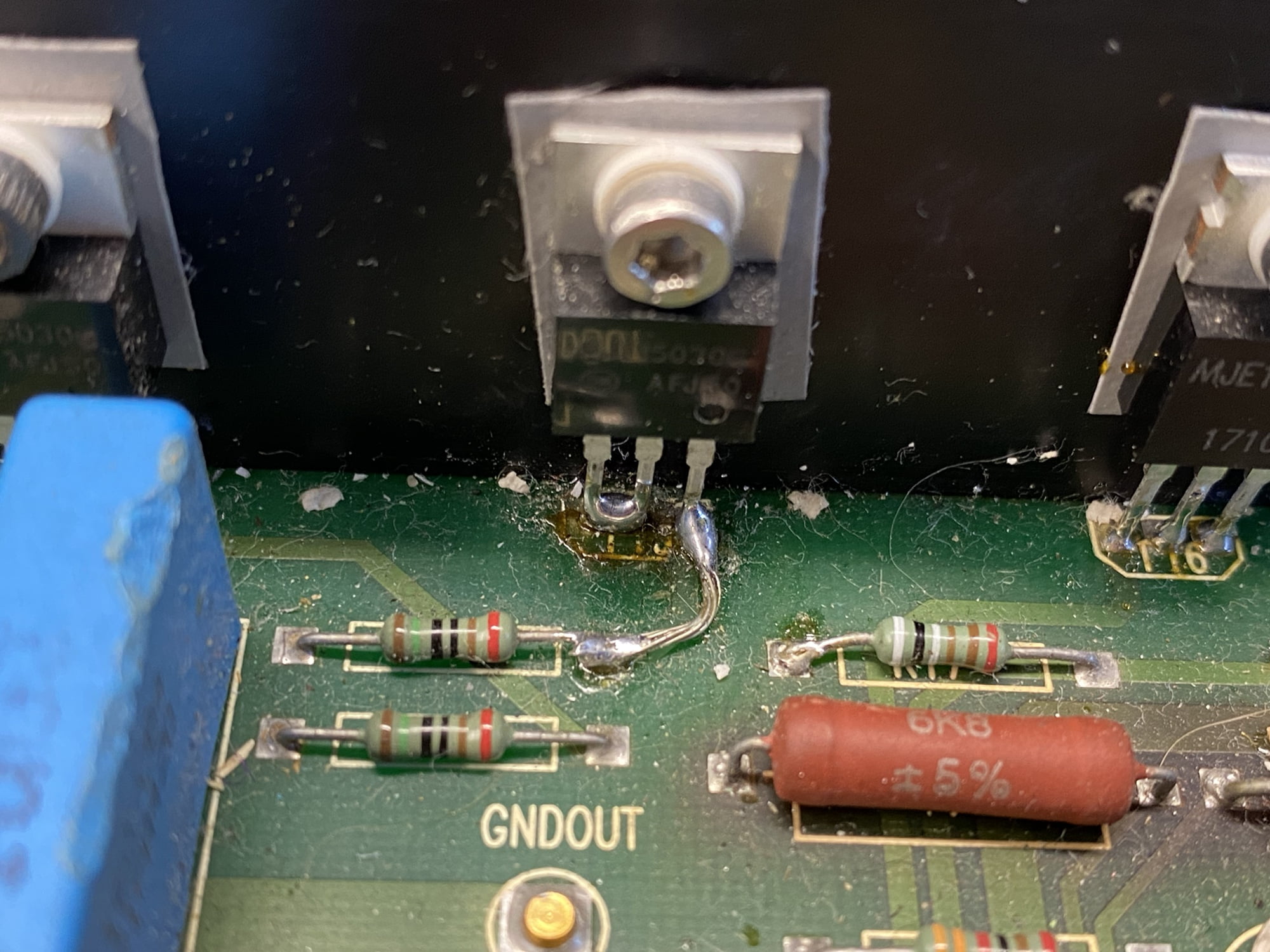
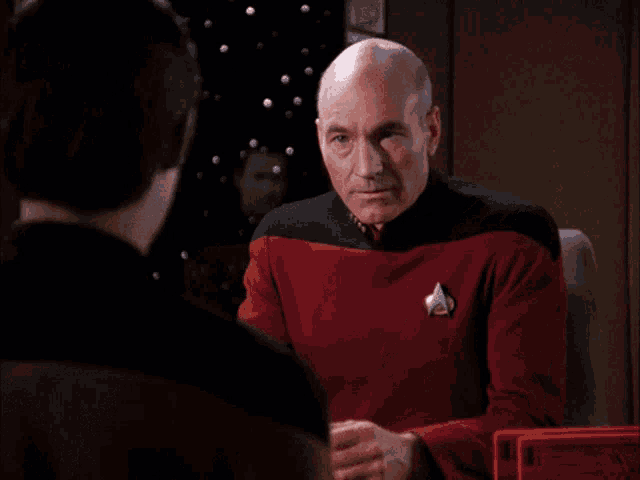
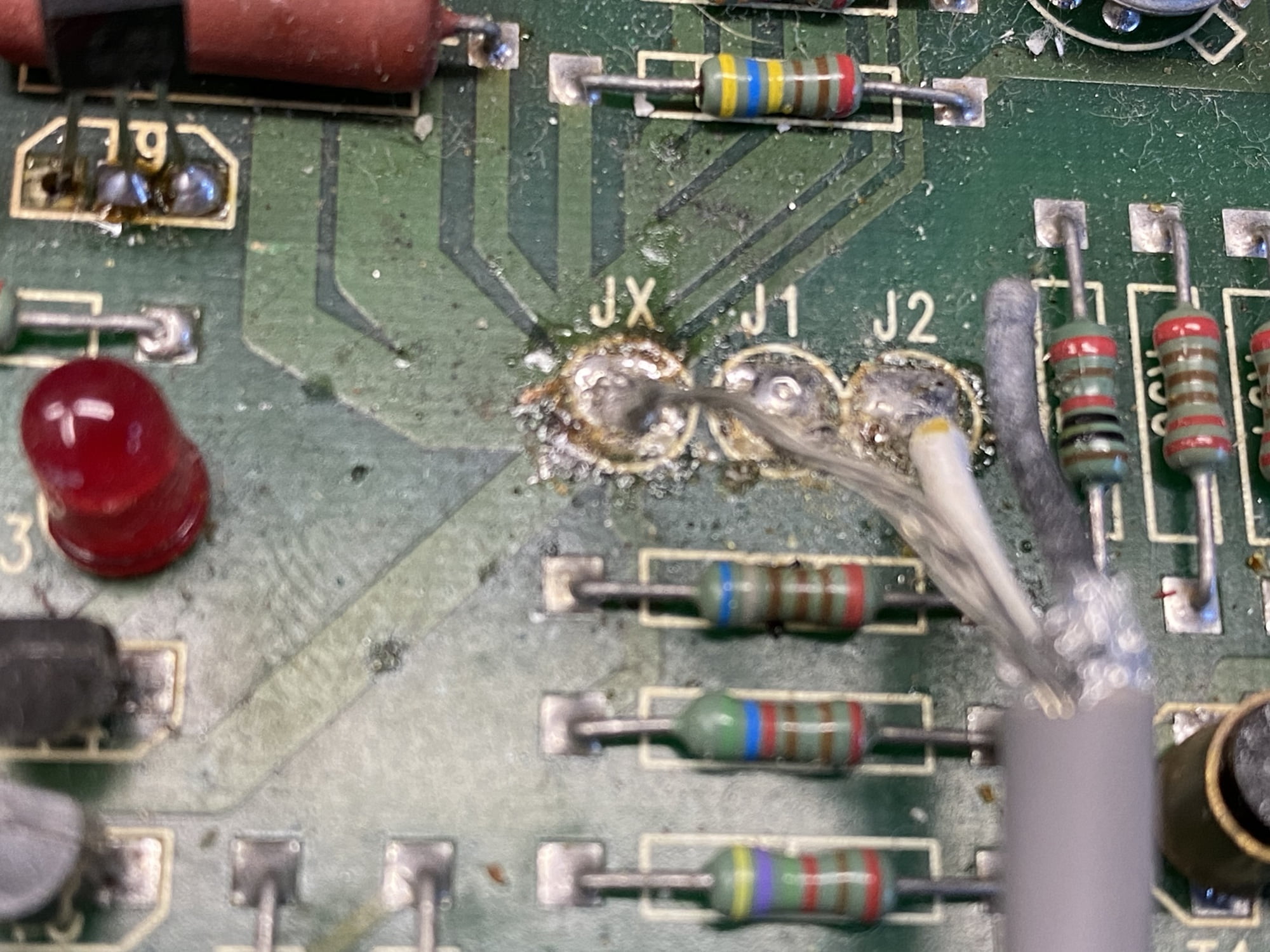
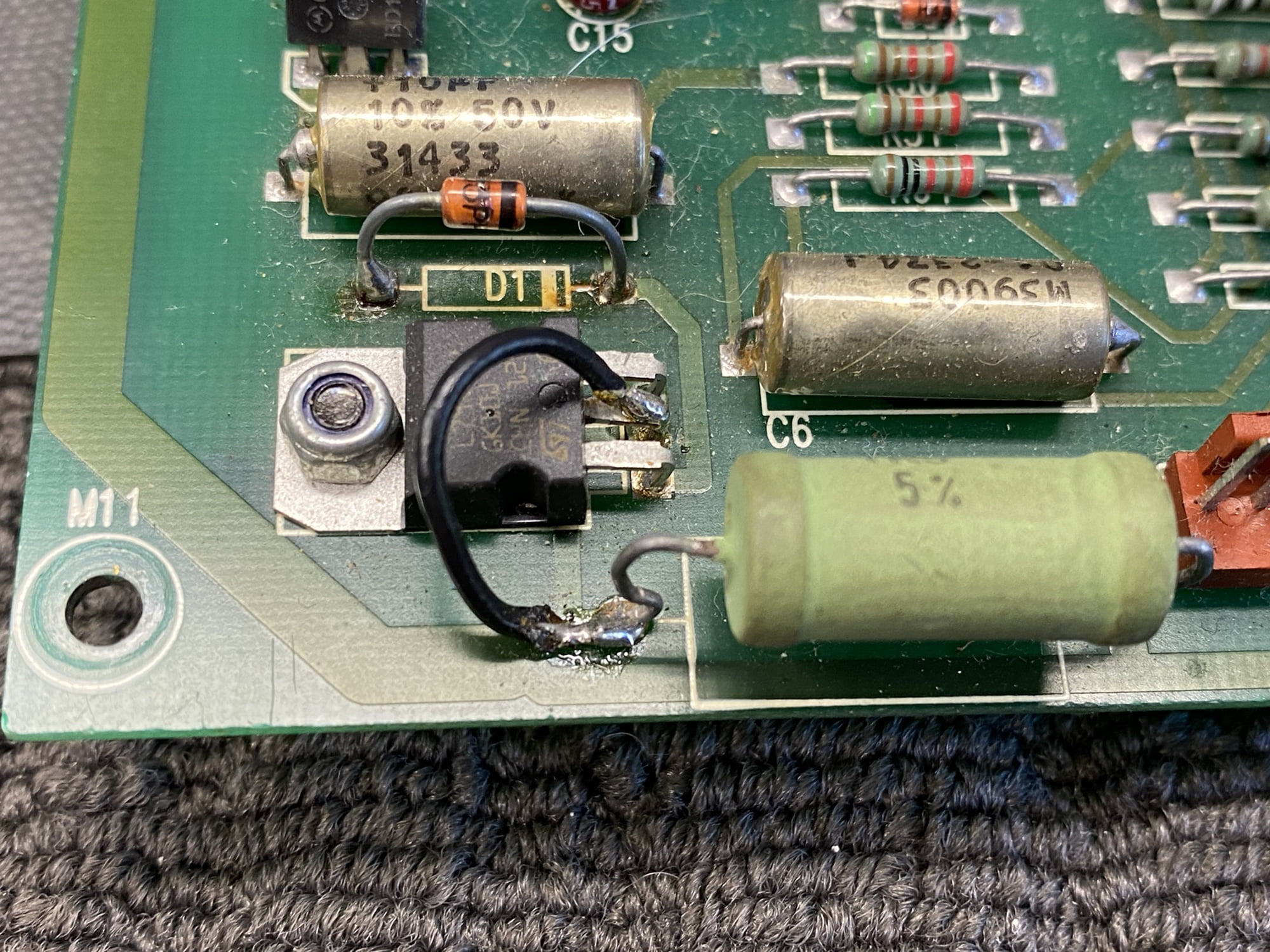
The last repairer this went to before I saw it – Mr RFW- is featured elsewhere on this page and I’ve worked on many pieces he has damaged. It also went to a semi-country repairer, and/or a ‘guru’ in the Perth hills, or both. I don’t exactly know. I tried to find out but just couldn’t get clarity on this. I asked a lot of questions about this one.
The current owner swears Mr RFW didn’t do the damage and tried to convince me of that. I’m not sure what that means exactly. Maybe it was the Buzztronics boondocks guys, maybe it was Mr RFW, I just don’t know who to believe I’m afraid. But somebody did this and I want to know who because everybody deserves to know that.
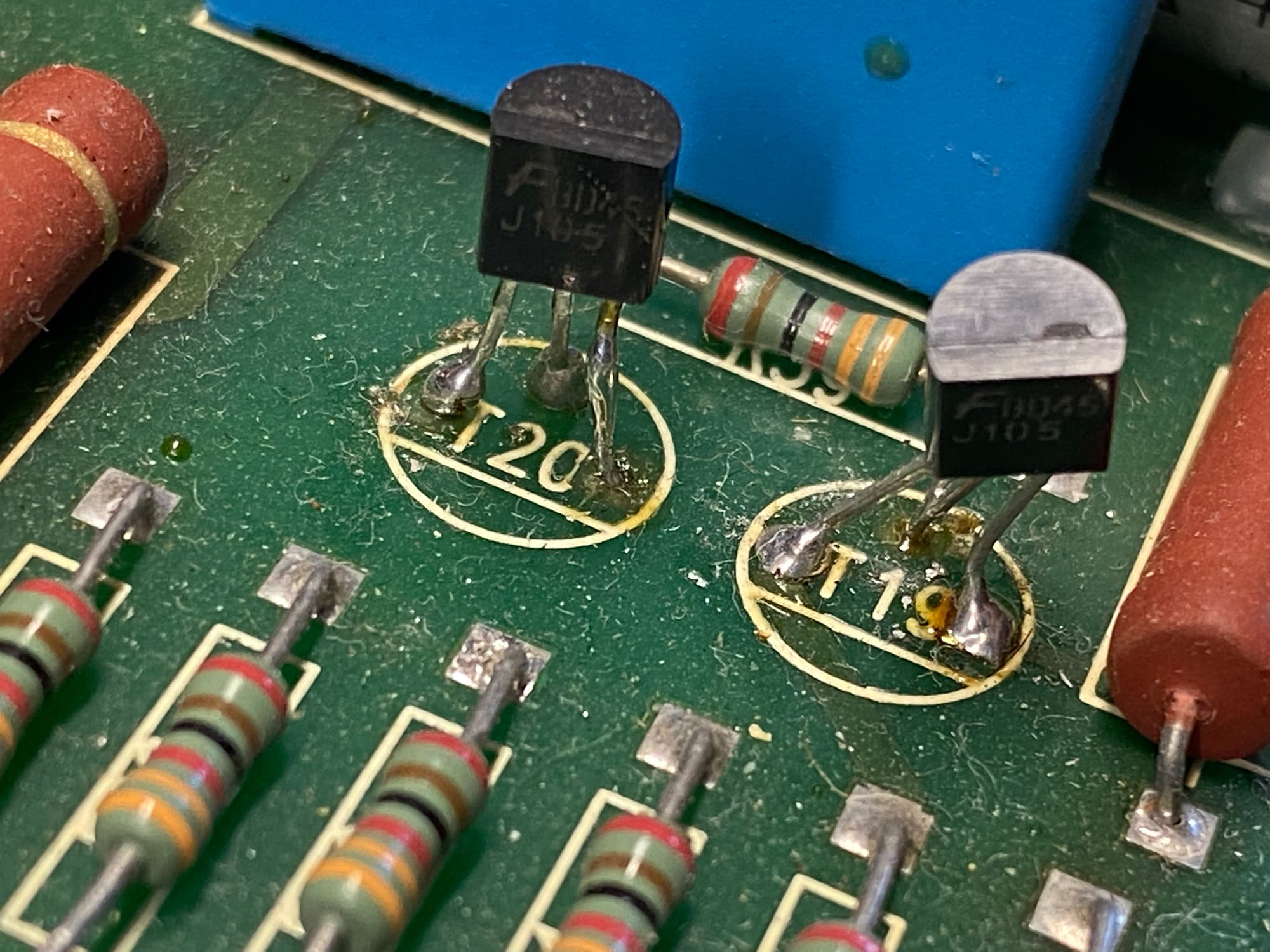
Learnings
The moral of this story? DO NOT take beautiful, high-end hi-fi gear to cheap repairers, VCR and TV guys, gurus or people who make their own ‘brand’ of homemade amplifiers. It’s NEVER worth it, it only ever causes problems and in this case, it has written off yet another stunning piece of equipment.
This amp carries a $50K+ replacement cost. It’s NEVER worth trying to save a few hundred bucks with an irreplaceable piece like this. Forgive me, but I’m going to go out on a limb here and say that this was a really stupid decision by whoever made it. Sorry.
For reference, if a repairer seems too eager, not busy enough, not in possession of the right equipment, or unable to converse fluently on the topic of repairing your equipment, read between the lines and find someone else. There’s a reason why the people who should look at this are busy.
Nobody can quote you upfront on a job like this. Nobody who knows what they are doing would say they don’t need service data or factory support for a repair like this. Nobody competent would suggest this job should be straightforward. If someone gives you the impression that fixing an amplifier like this is easy, walk away.
AGAIN: Don’t take your Porsche to the local garage, don’t take your Rolex to a shopping centre watch booth and DON’T take your Gryphon amplifier to Buzztronics or Mr RFW. EVER.
Is this amplifier repairable? Sure, given time and money, almost all gear is repairable. The key is to find someone willing to take it on, despite all that’s happened to it (I’m not) and someone willing to pay for it (the current owner is not).
There’s more to this story but I lost enough time and money on it, digging around, trying to help the owner, billing him a pittance and receiving little appreciation for it. Ultimately, my job is to educate and offer sensible advice and do the very best technical repair work possible on equipment like this, where it makes sense to do so. I can’t do much more than that!
Case 9 – Pioneer PDS-507 CD player
This is another sad case, likely perpetrated by a local tinkerer known in the ‘scene’ here in Perth. Local readers may know who I’m referring to. On the surface, we have a perfectly nice and quite classic Pioneer PDS-507 CD player. These were good machines, nice transports, but often people tinkered with them and installed clocks, regulators and other bits and pieces, usually pretty terribly. Such is the case here.
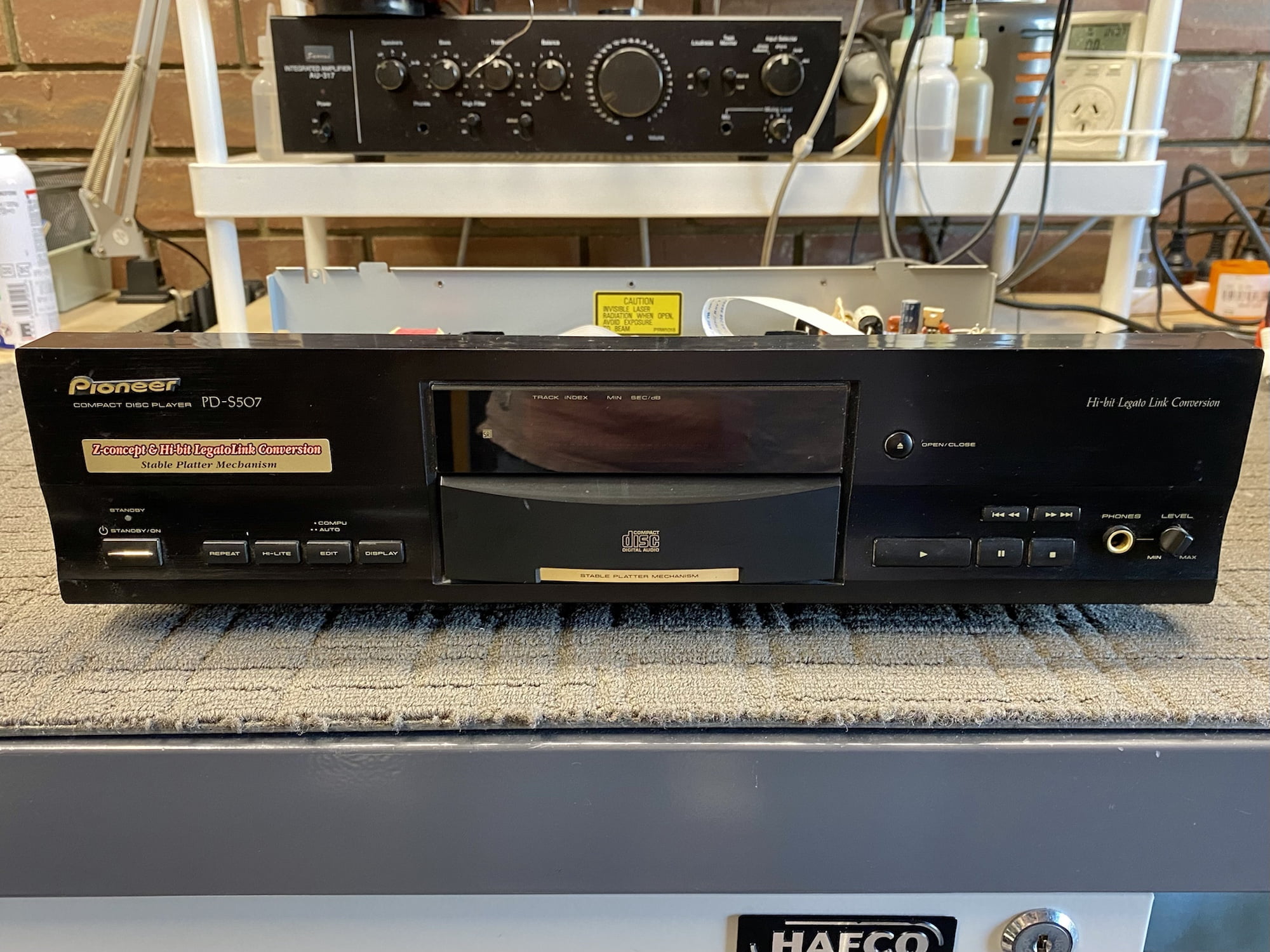
Underneath the hood, all is revealed…
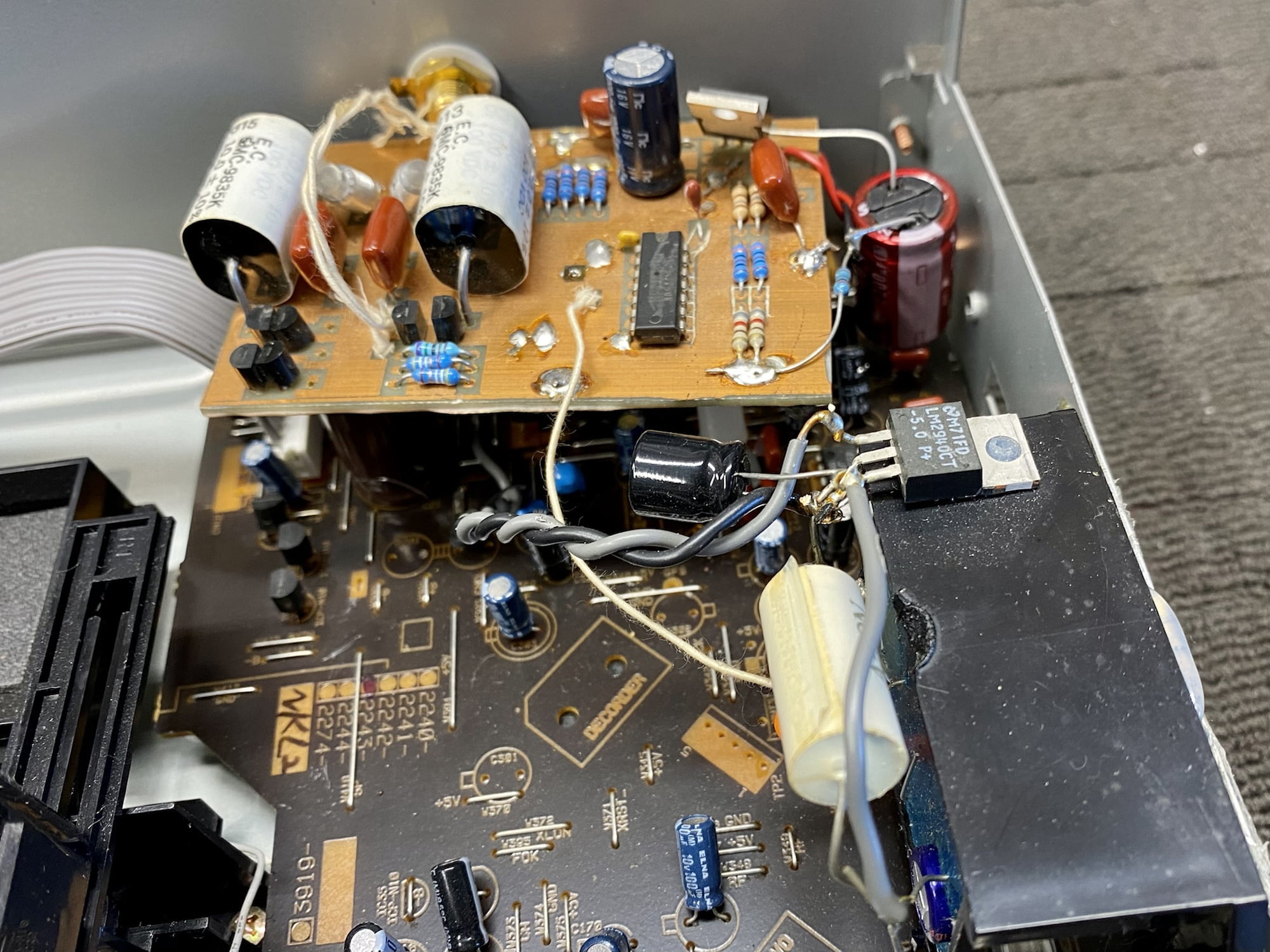
Quite honestly, you couldn’t build something much worse than what you see here. Well, excluding the Marantz CD player mod in case # 5, which is worse!
Big globs of solder, crappy little wires holding a heavy board in place, burn marks. I know some people think work like this is ‘cool’ but it’s not. I secured the board with some decent hot glue and told my customer two things:
- Don’t go to ‘gurus’ for work like this, it wastes time, and money and devalues equipment.
- Don’t shake this CD player around too much!
Now, for the record, I’m not against modifications and improvements. On the contrary, I support well-engineered improvements to hi-fi equipment, but if you can’t do the work neatly and safely, get someone else to do it.
Case 8 – MAS (Metaxas) Solitaire Power Amplifier #2
It’s probably best to check out the first MAS Solitaire I looked at from this pair of beautiful amplifiers before checking this story out. I won’t go through the details again, but you can read about the first Solitaire in Case 7.
This is the second amp from the pair. The owner was sure this one was OK and it looked good from the outside. Sadly, it was as bad or worse than the first one, truly diabolically butchered.
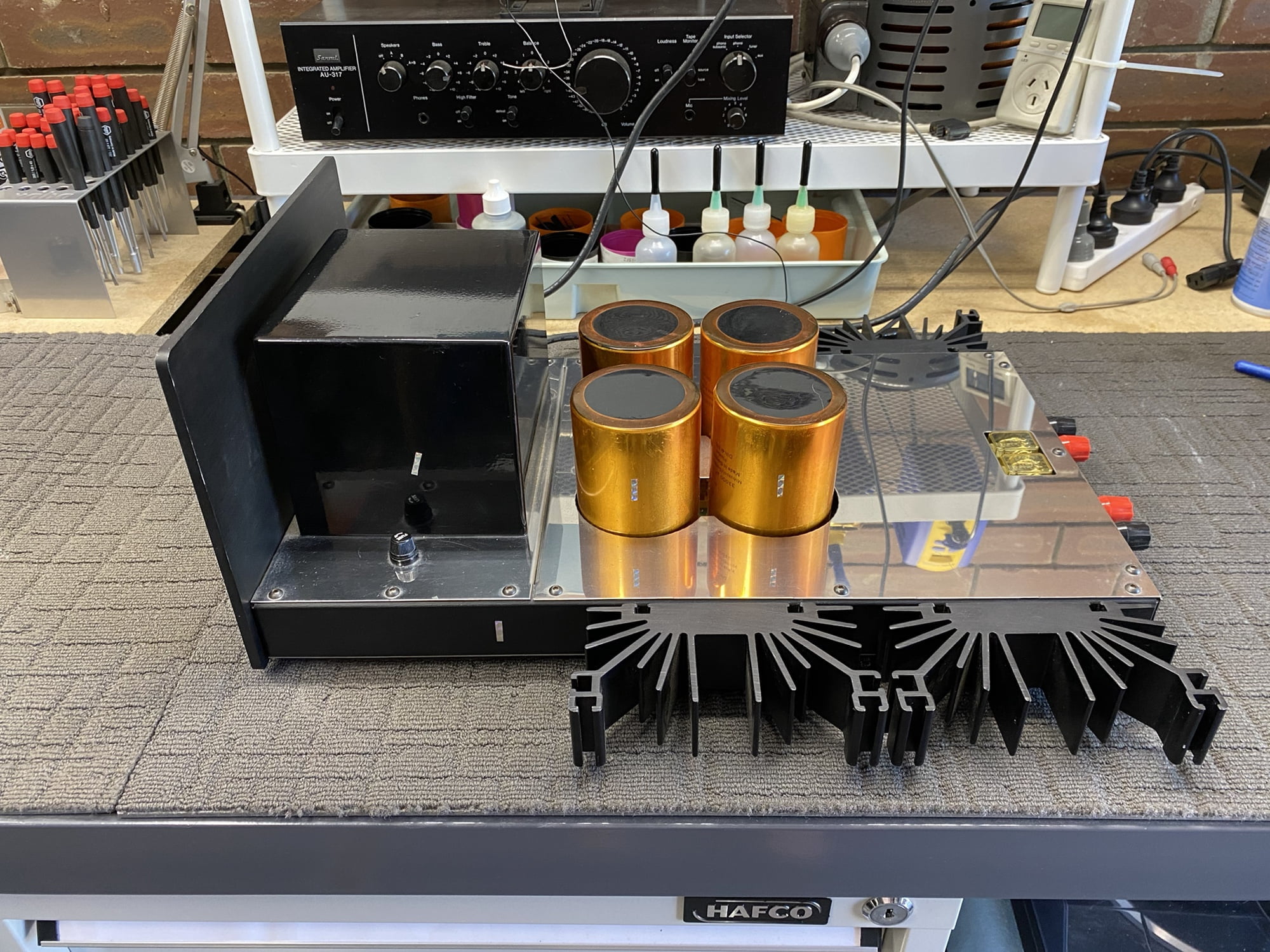
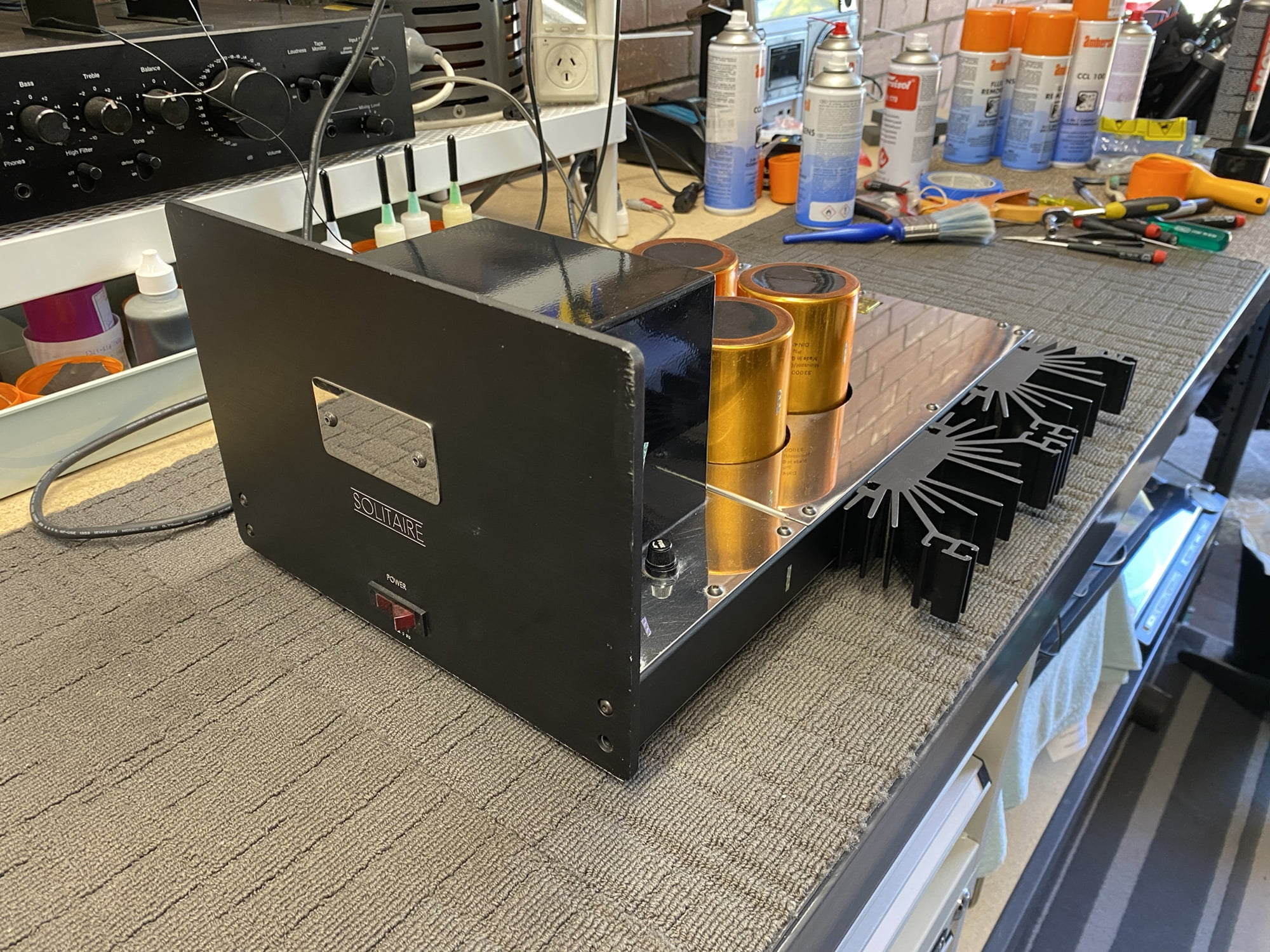
Sadly not so beautiful inside, at least not this poor Solitaire. Let’s examine some of the issues.
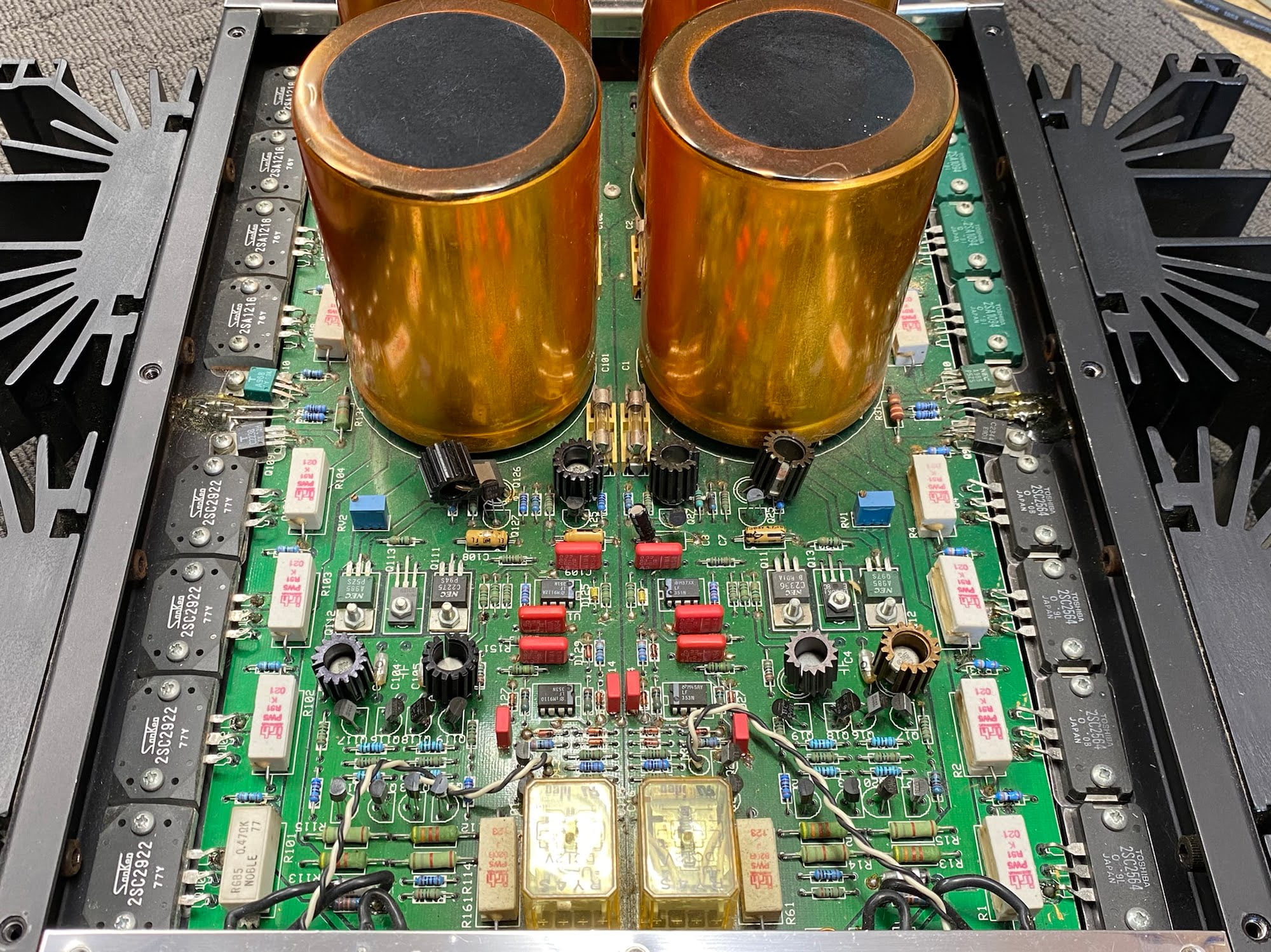
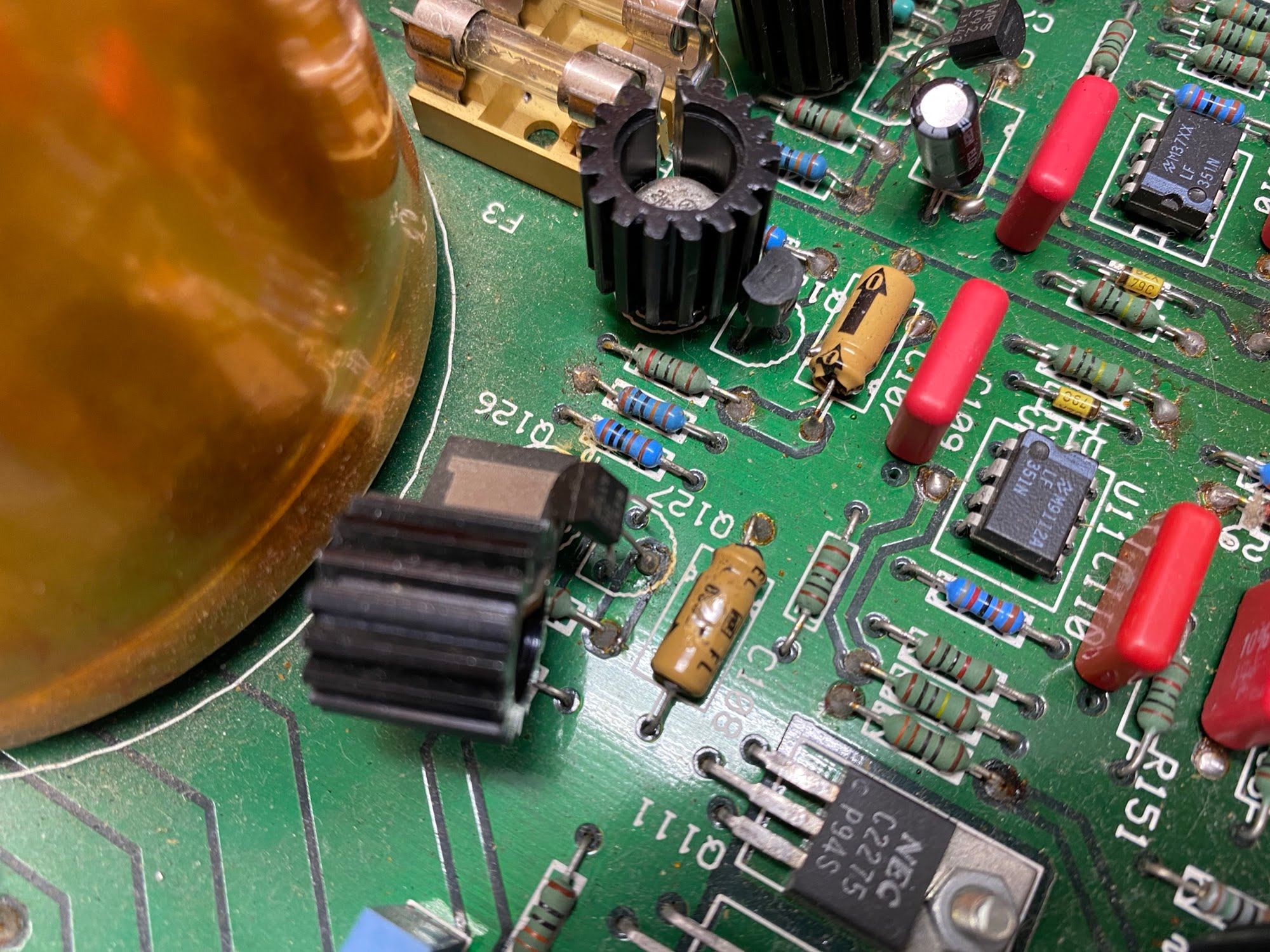
OK, so let’s start here. This was a TO-18 device, part of a complementary transistor pair. When you replace one device with, in this case, a different TO-220 device, you HAVE to replace the complementary device. These two transistors are mismatched and can never work properly together. Also, it’s necessary to use a heatsink that suits the transistor package. So, a TO-220 heatsink should have been used on this odd TO-220 device. Instead, this lazy repairer simply clamped the old TO-18 heatsink onto this new device, guaranteeing that it will overheat, short against something or fall off.
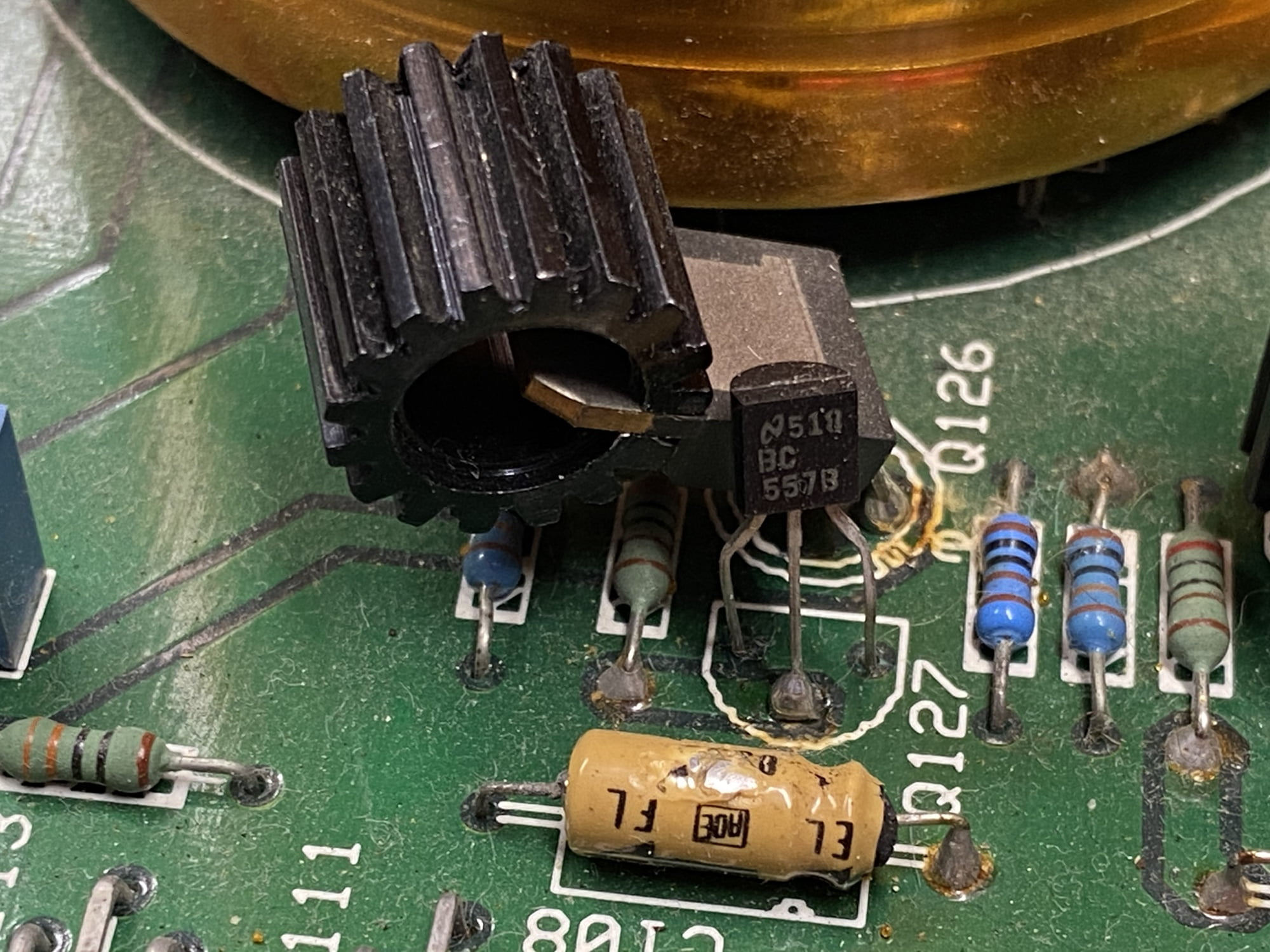
Apart from the obvious butchery here, the soldering and general filth are unbelievable, aren’t they? Honestly, as I put this case together, I can hardly believe what I’m seeing, and I’ve seen it all before!
Right, what’s next…
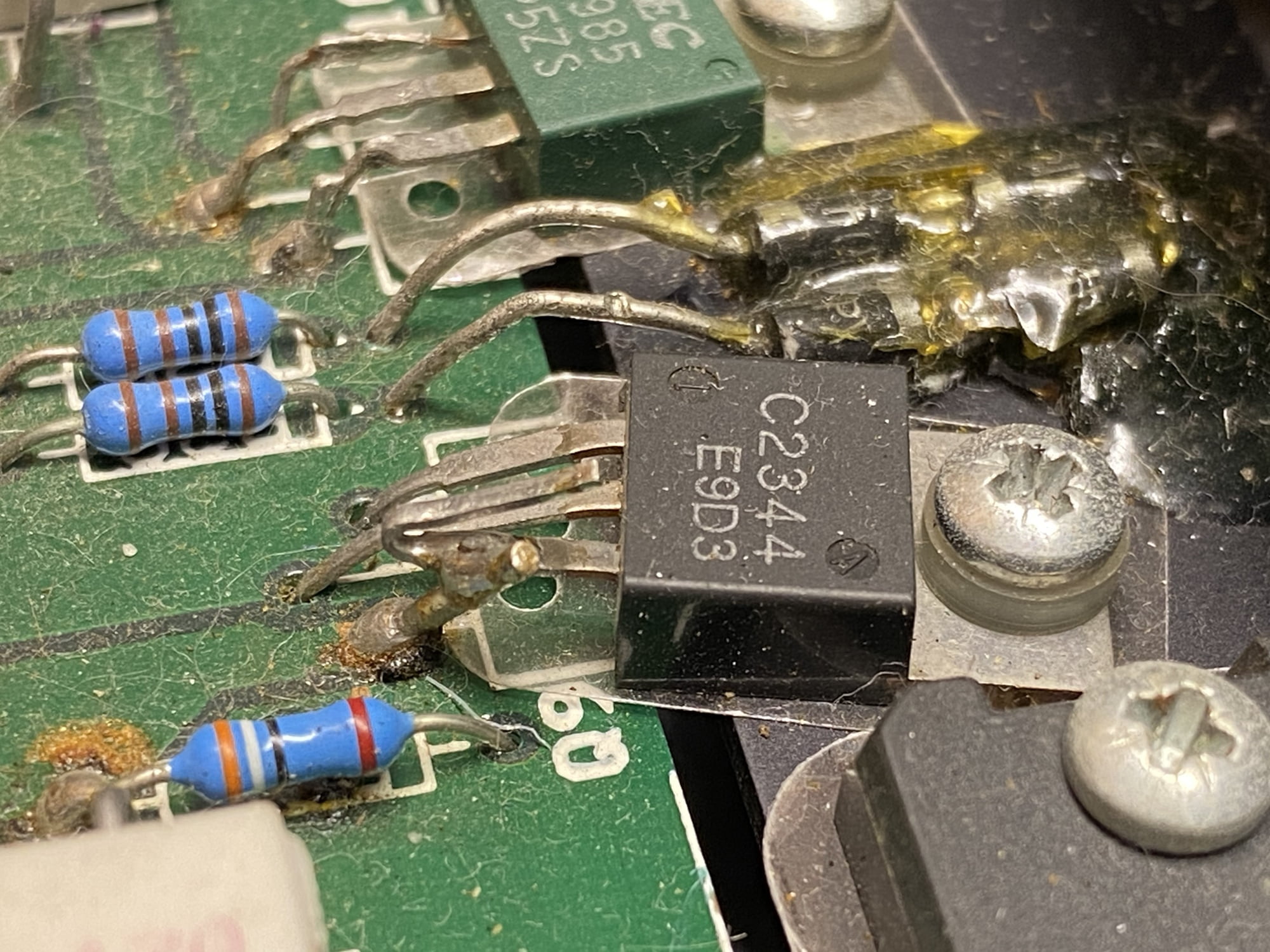

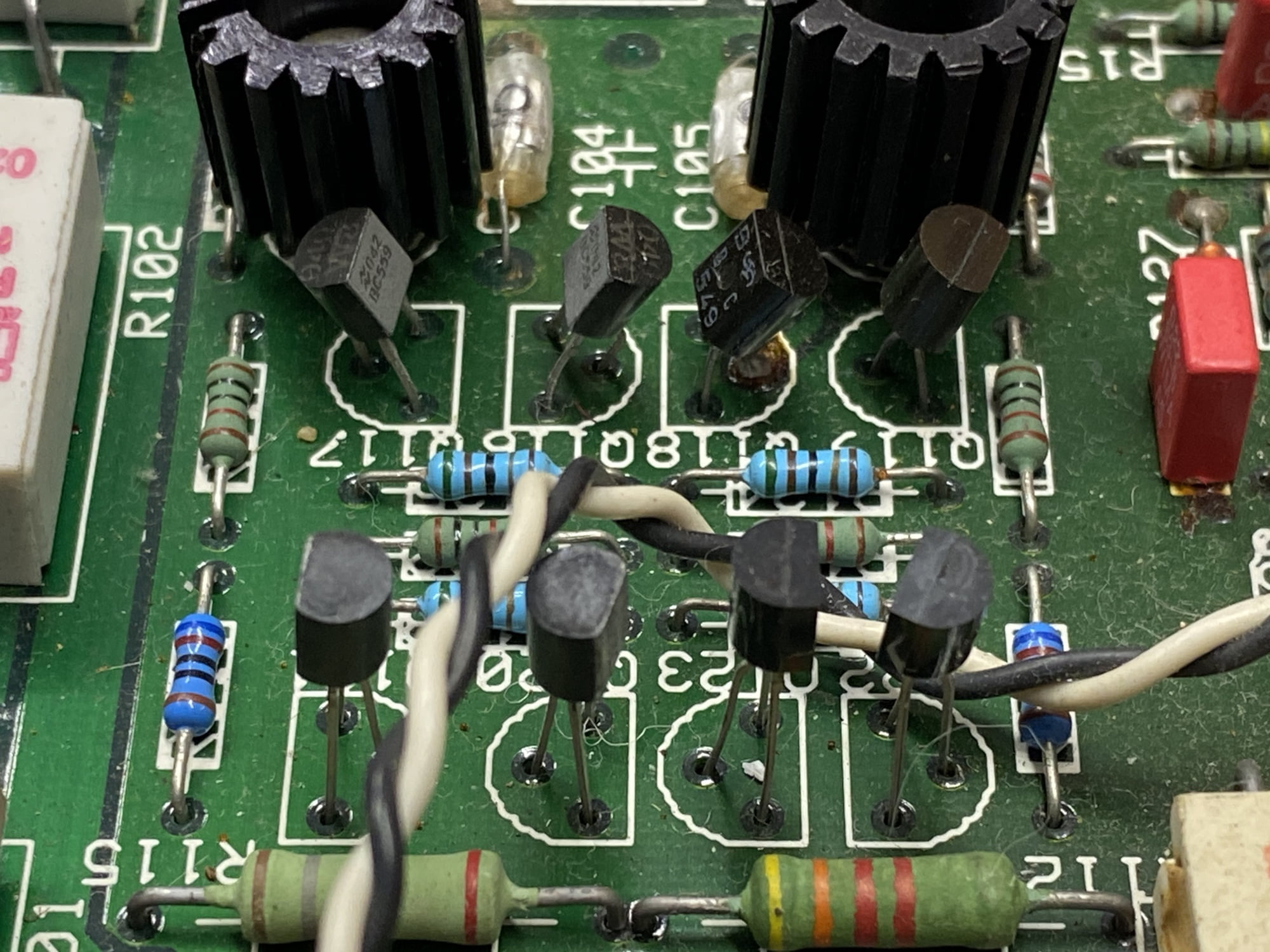
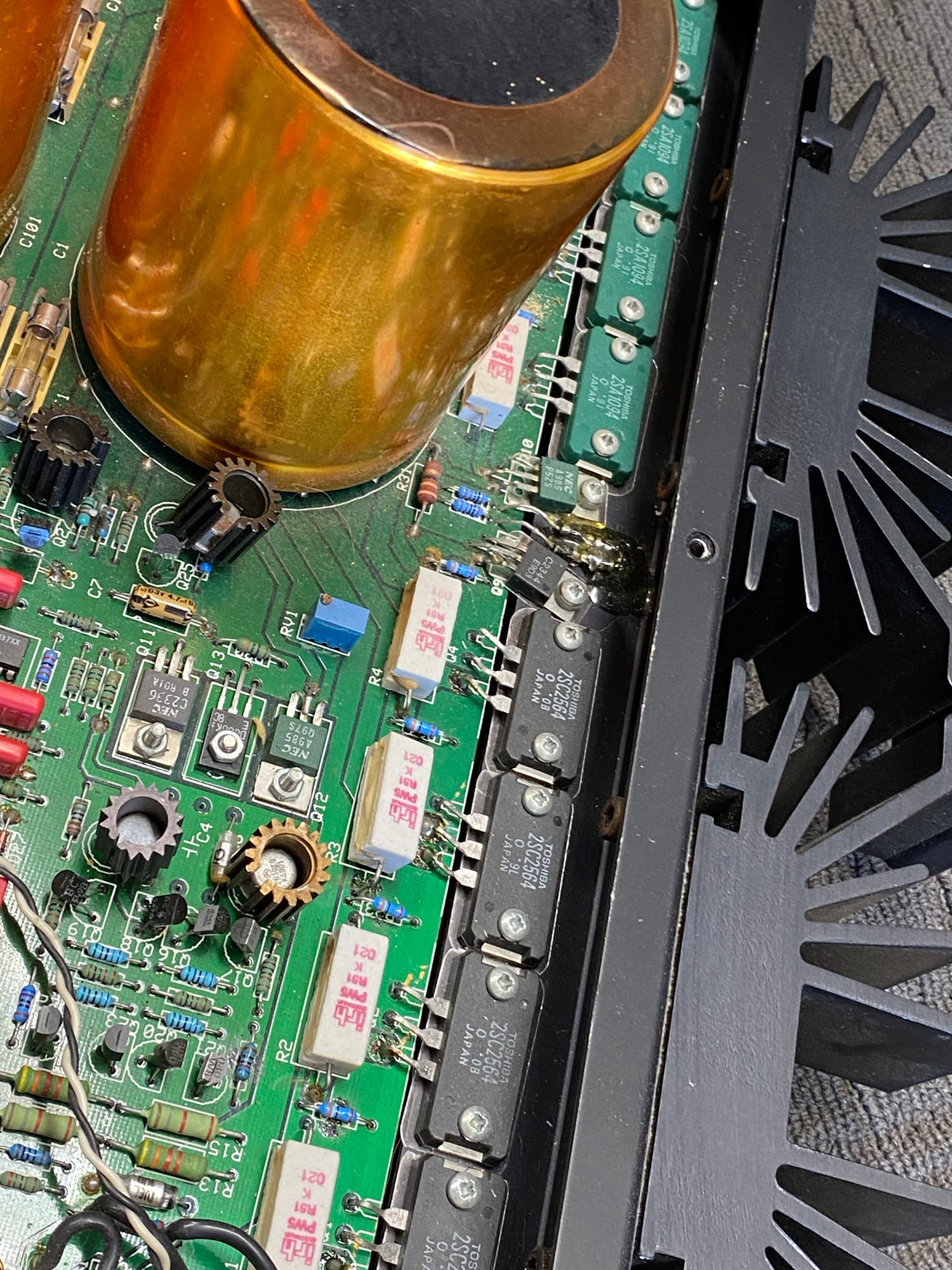
So, that’s it for another case of amplifier butchery. This is disgraceful work, there’s no other way to put it. People sometimes ask why I don’t fix amplifiers in this condition. The amount of destruction and introduced faults make it so hard for anyone else to go in after and fix things that the pain is just too great. I could spend a week working on this, researching and locating parts, repairing damaged traces, and sourcing NOS bits. Maybe it still wouldn’t work? Quite frankly, in some cases, the gear is past the point of no return.
Case 7 – MAS (Metaxas) Solitaire Power Amplifier #1
Sadly, we have another case butchered by a technician back in the heyday of hi-fi retail. Given my updated knowledge of the pedigree of this amplifier and its partner, the work appears to have been done by Vince Ross’s old technician.
This amplifier came to me for repair, but my first look told me everything I needed to know about my chances of success on this otherwise stunning amplifier, designed by the legendary Kostas Metaxas.
The MAS Solitaire is an extraordinary amplifier. With a claimed slew rate of 1000V/uS and outrageous styling for the time, this is a super-fast, wide-bandwidth amplifier, with power, stunning looks and premium parts. People rave on about ME, but ME gear has back-yard build quality compared to this beauty.
BUT, when you repair a MAS Solitaire using crappy tools, crappier parts and zero care, this is the inevitable result. The mainboard is too badly damaged and too many crappy parts have been installed to make working on this one viable. Someone might like to try, but not me. It’s a real shame, a sad end to this otherwise lovely unit.
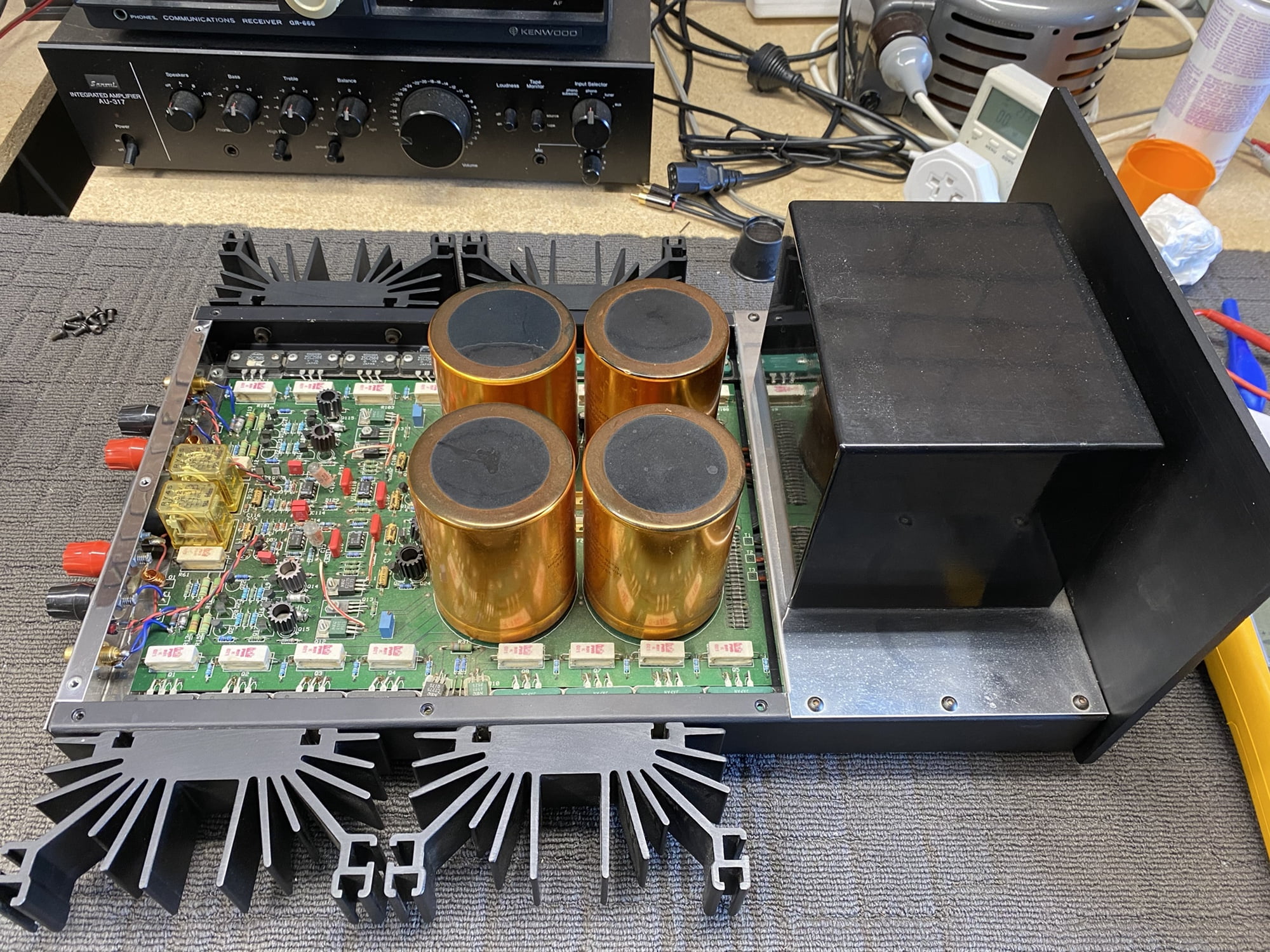
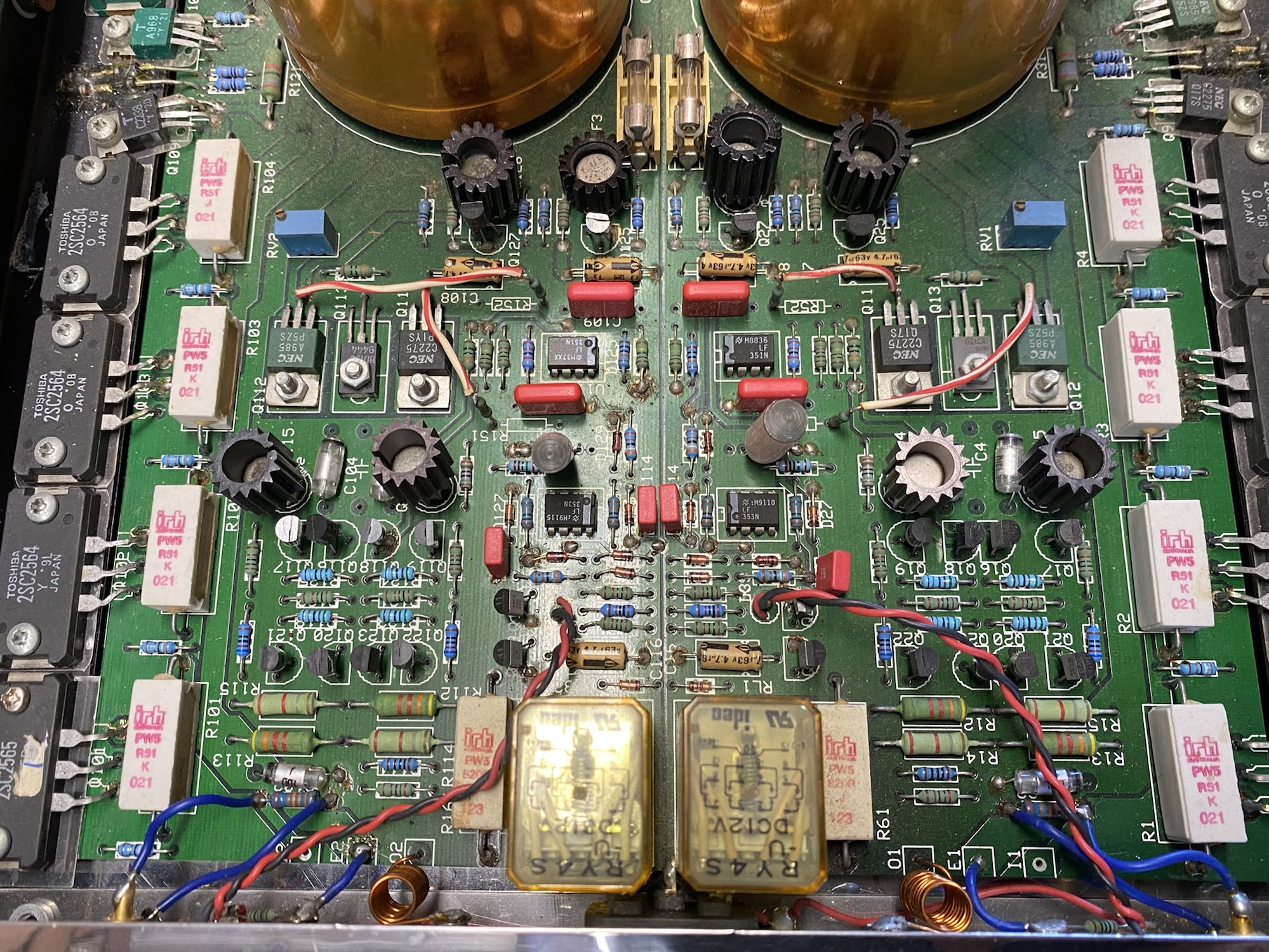
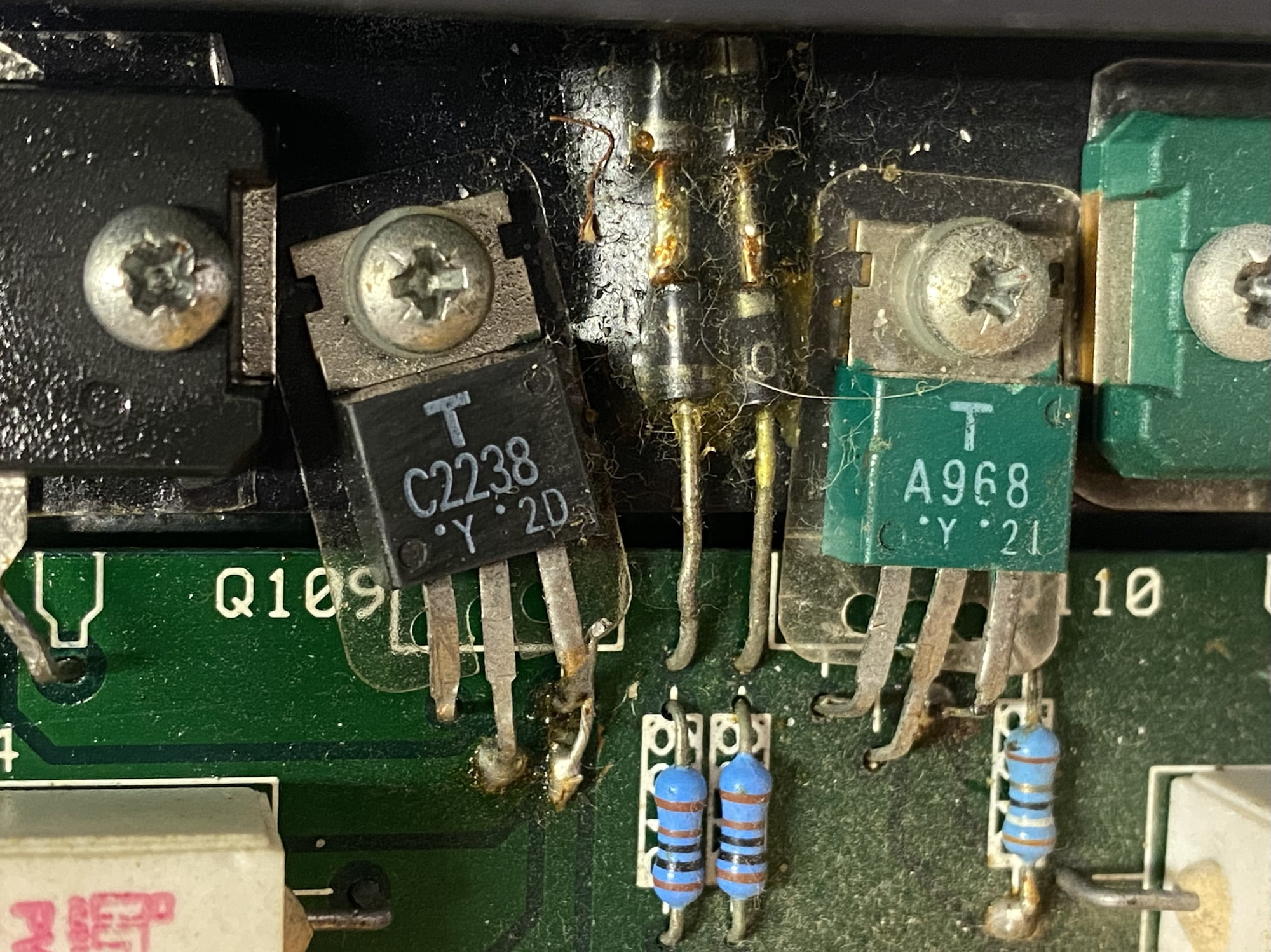
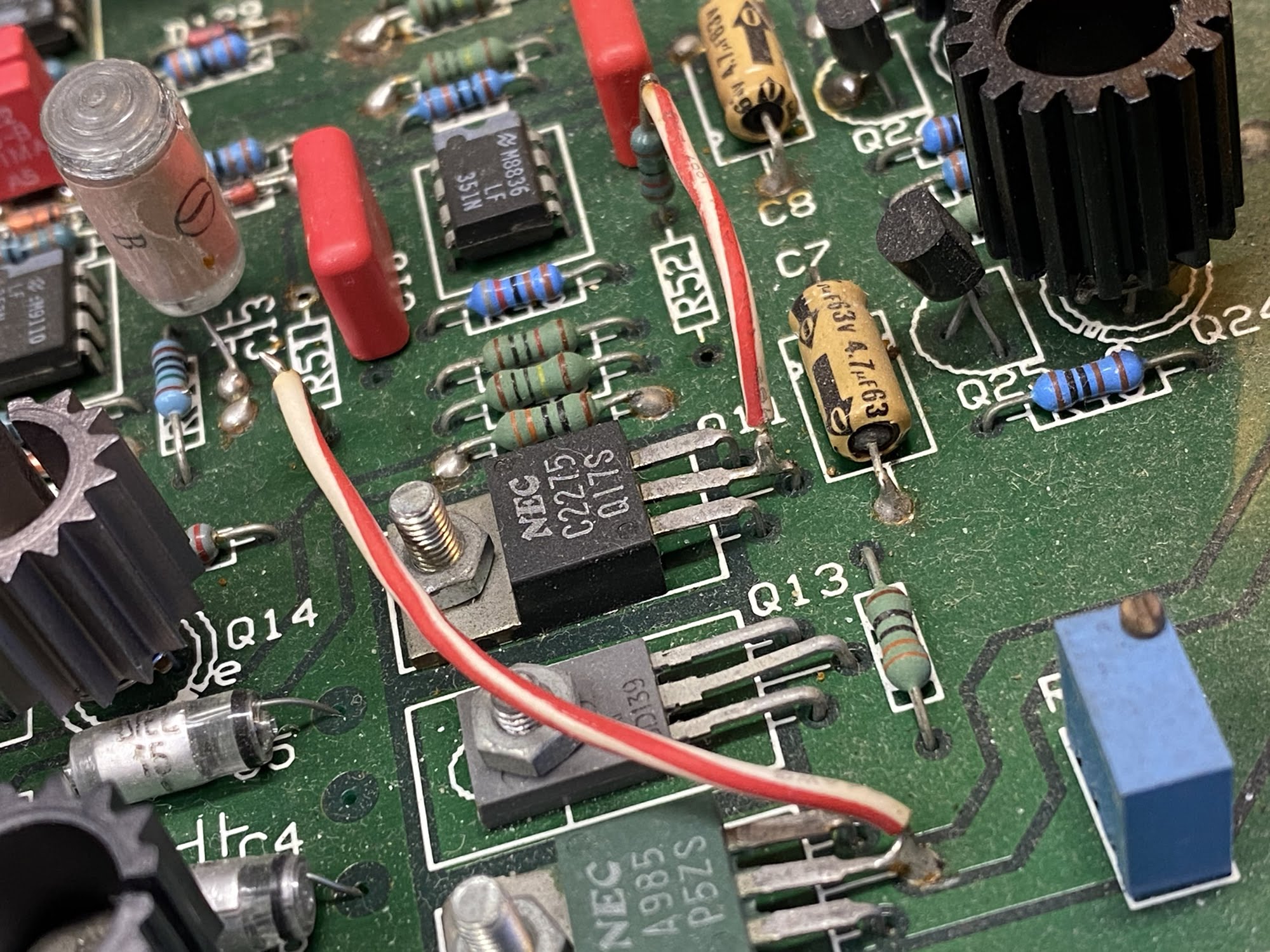
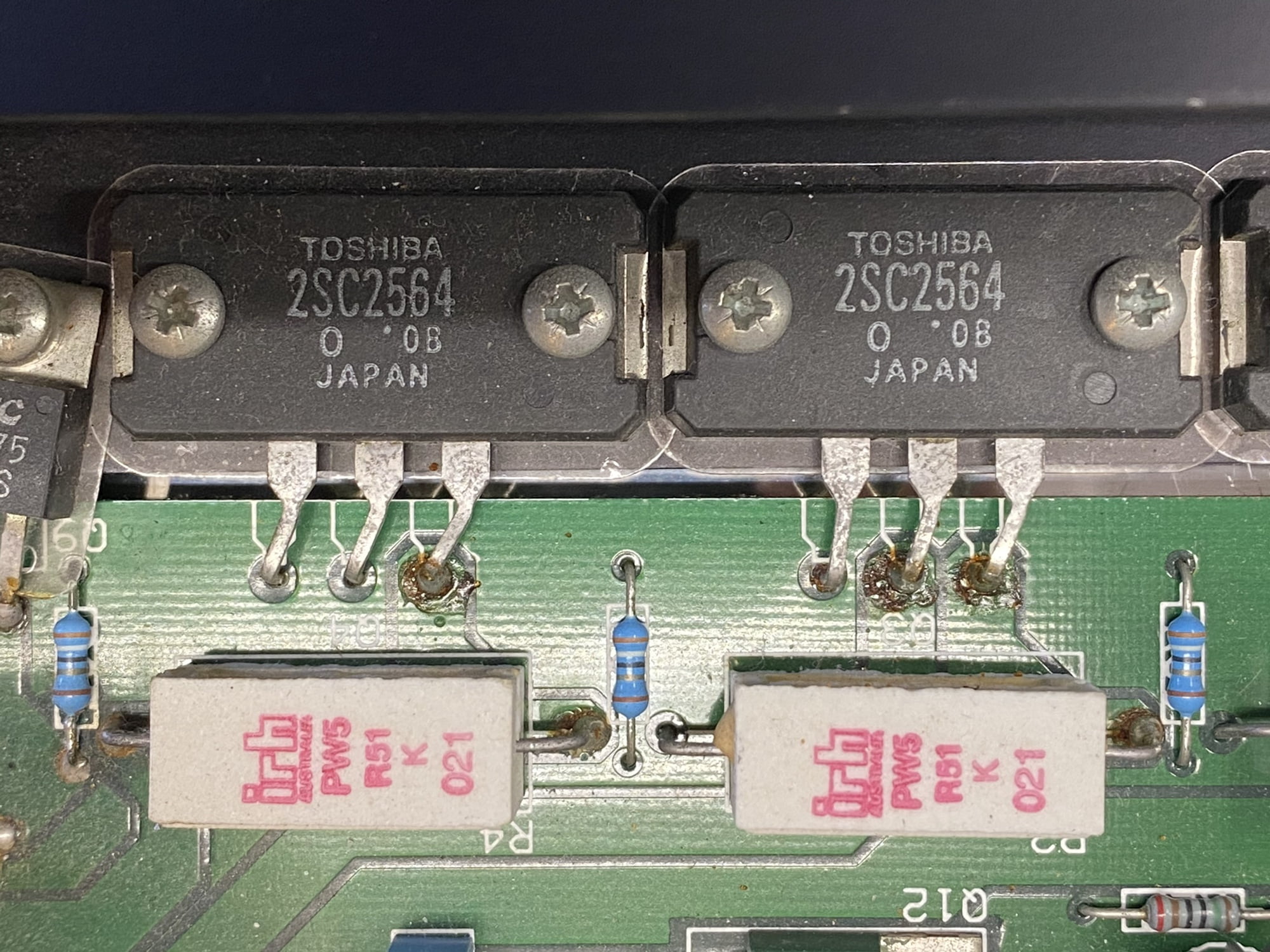
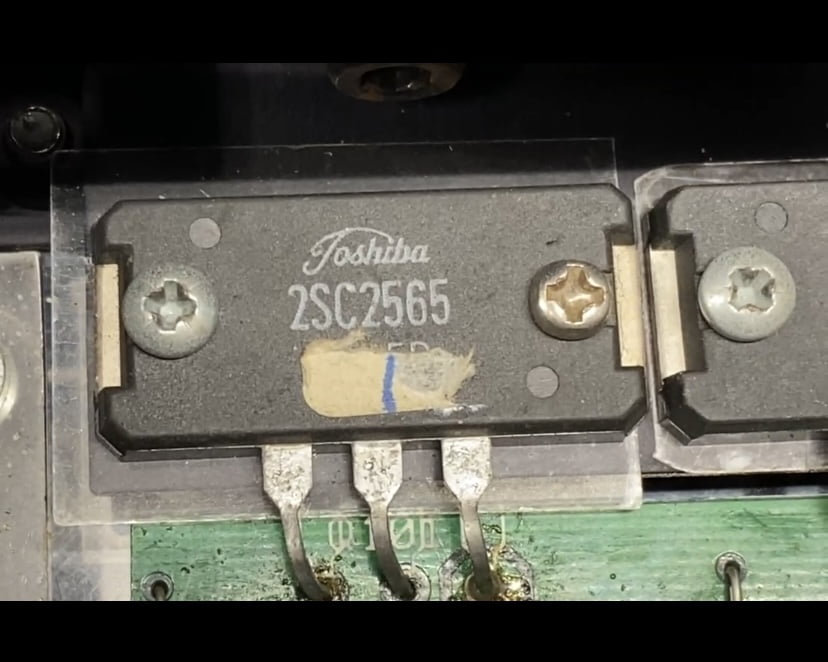
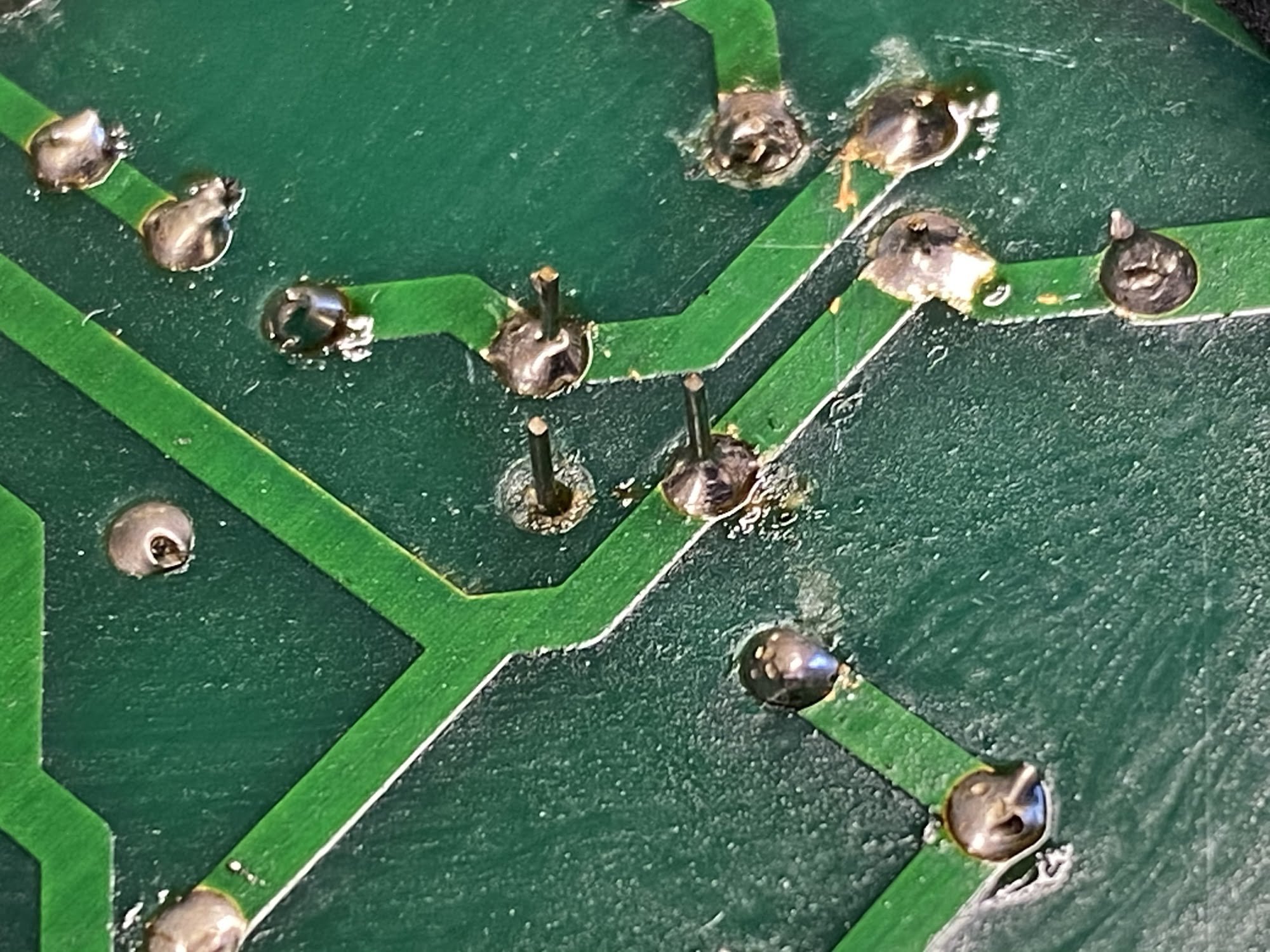
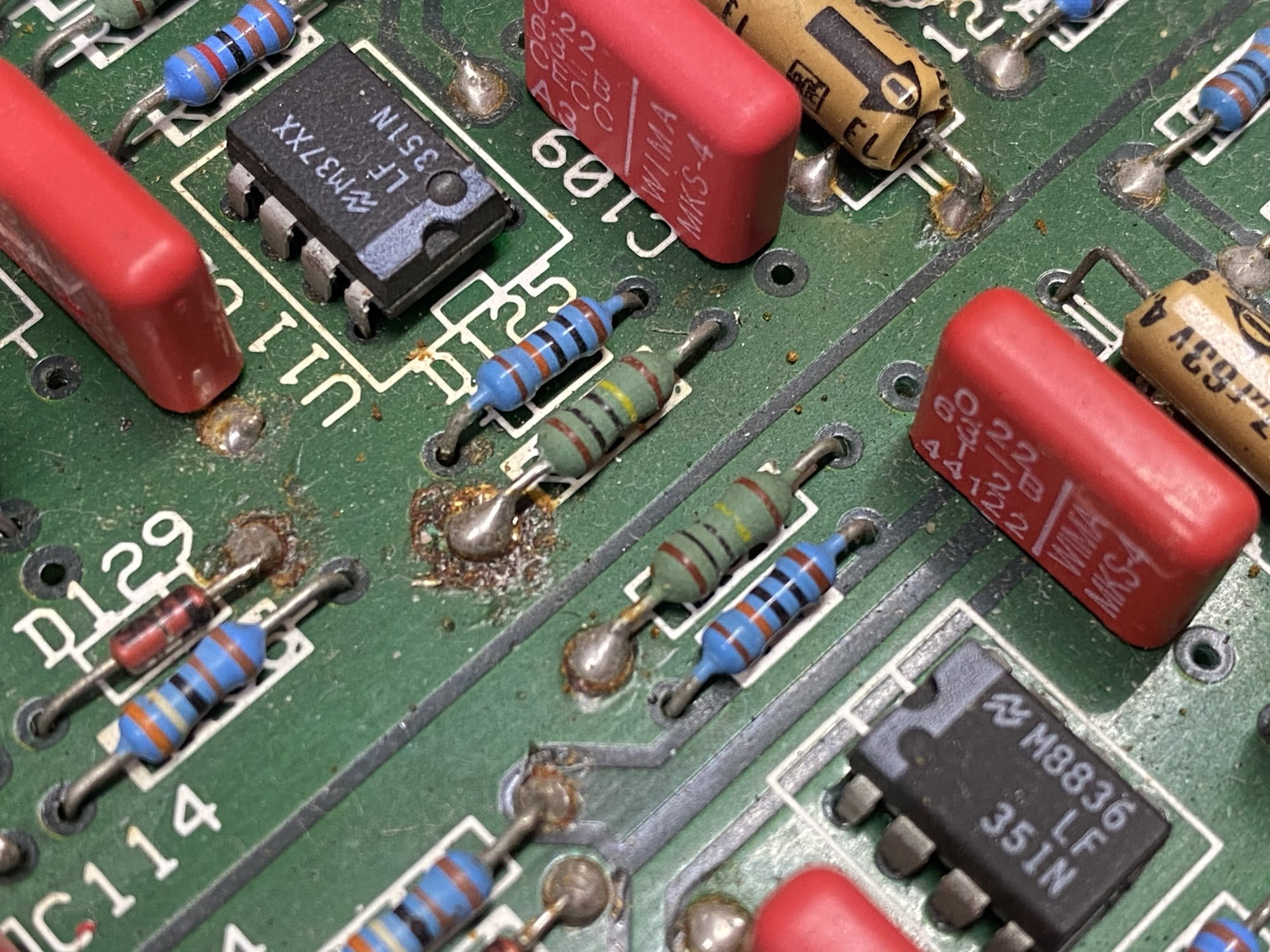
The owner has another MAS Solitaire, and it is now with me for service. Let’s see what a good one should look like, stay tuned.
UPDATE: See case # 8, the second MAS Solitaire. It’s no better, could almost be worse. Whoever did this worked on both amplifiers.
Case 6 – Krell KSA-150 Power Amplifier
This classic case fully warrants its place in the Hall of Shame. I bought this amplifier many years ago from a hi-fi dealer in Australia called Trevor Lees. Trevor is unhappy about being featured in the Hall of Shame but you reap what you sow as they say.
Trevor misrepresented the condition of the equipment, fraudulently claimed he sold the amplifier new and authorised the appalling repairs made to this beautiful amplifier. Peter, the technician who did the work, contacted me sometime later by phone and tearfully apologised for the poor workmanship, done under duress. I appreciated that.
Over the years, I’ve been contacted by numerous people, telling their own stories of woe about Trevor Lees. Incredibly, the technician who did this awful work contacted me directly to apologise. I felt bad for him because he explained that he was always pushed to repair things on the cheap. That’s definitely evident here.
Case 5 – Marantz CD85 CD Player
Check out this modification abomination that rendered a wonderful old Marantz CD player unserviceable, cementing its place in the Hall of Shame.
The obvious question here is why? It’s hard to know, but I’d suggest the perpetrator read about improving the clock on a forum and failed to understand that the way you do something is actually more important than what you do. Equipment can often be improved, but not like this.
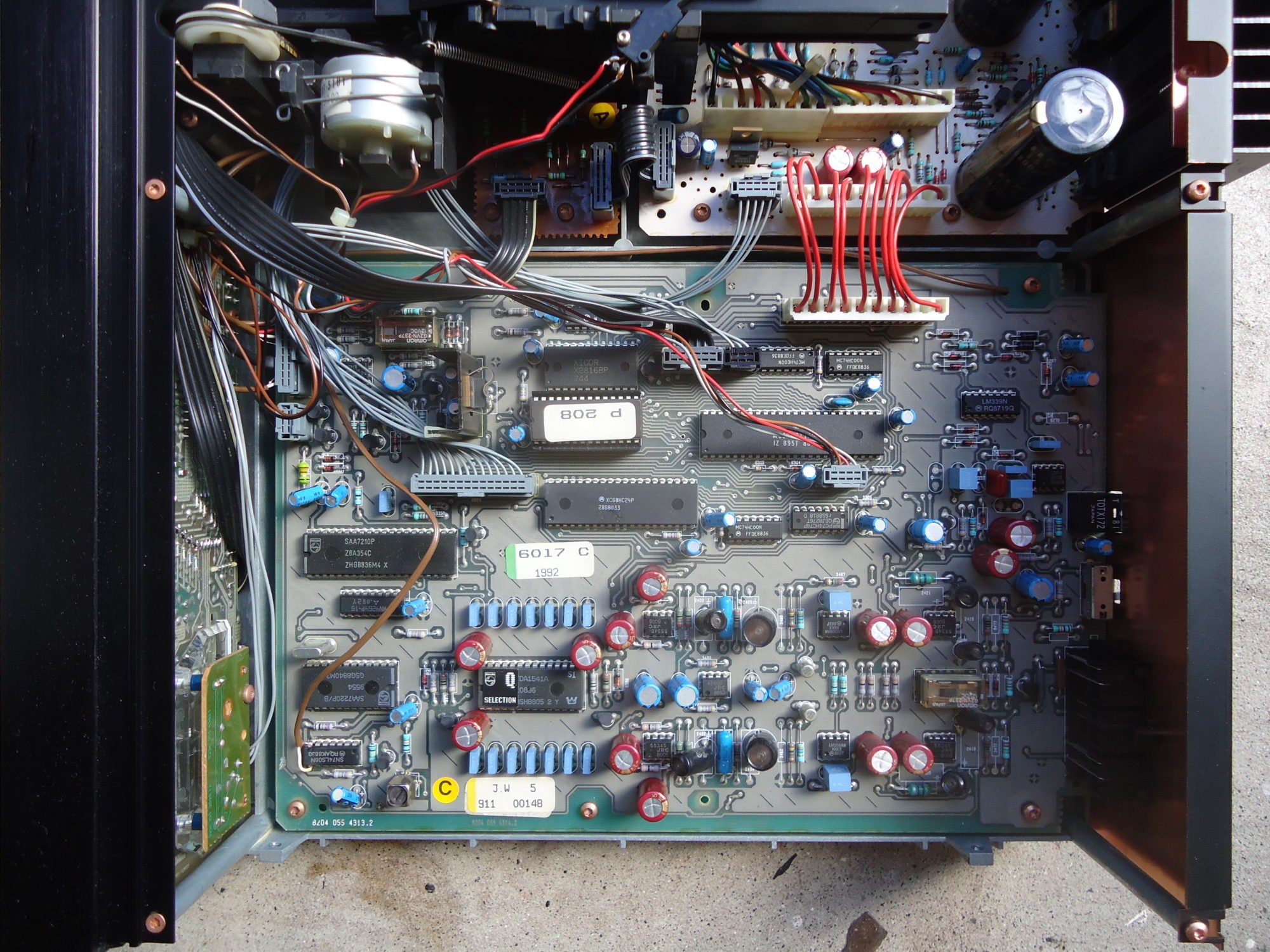
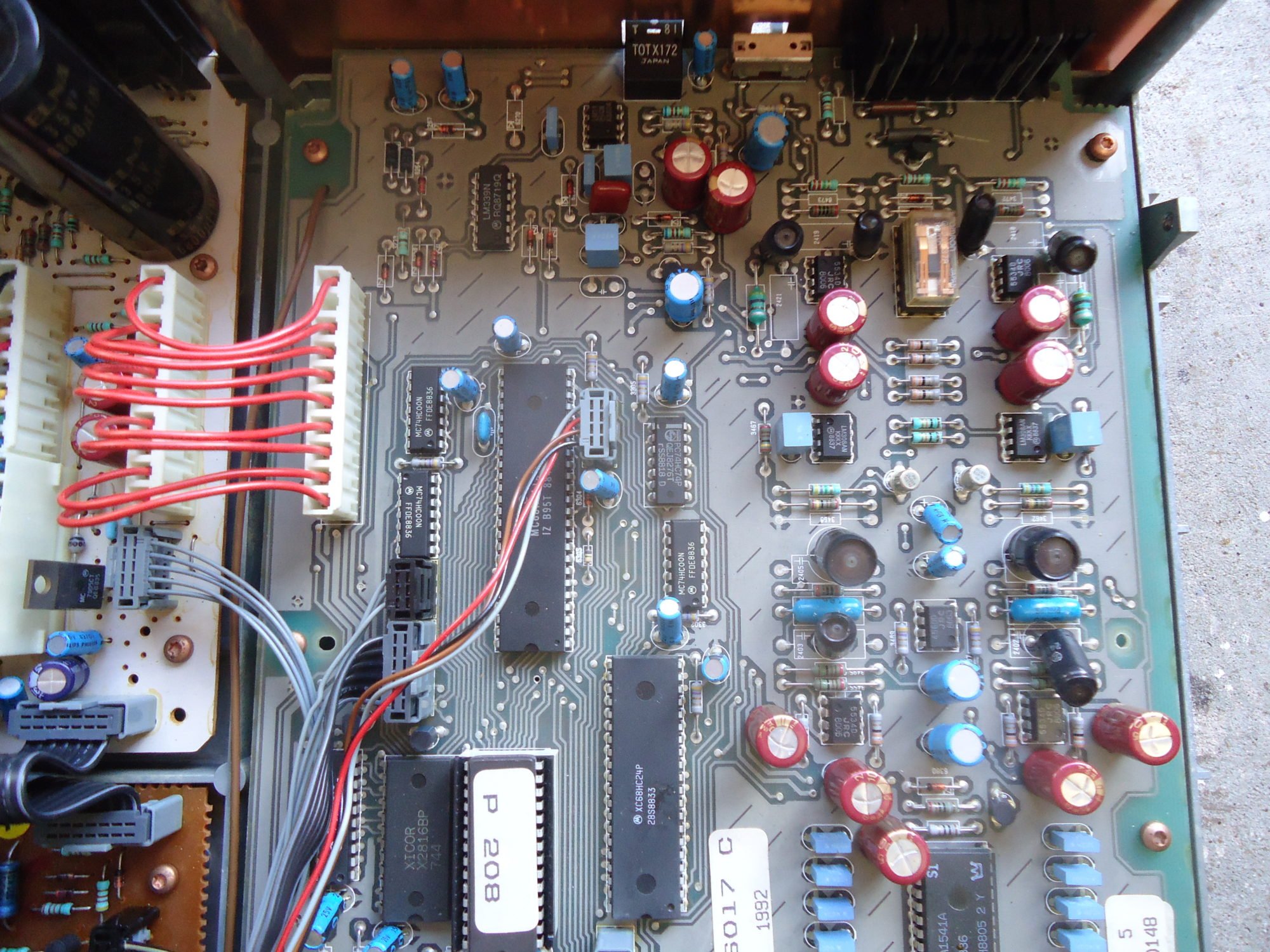
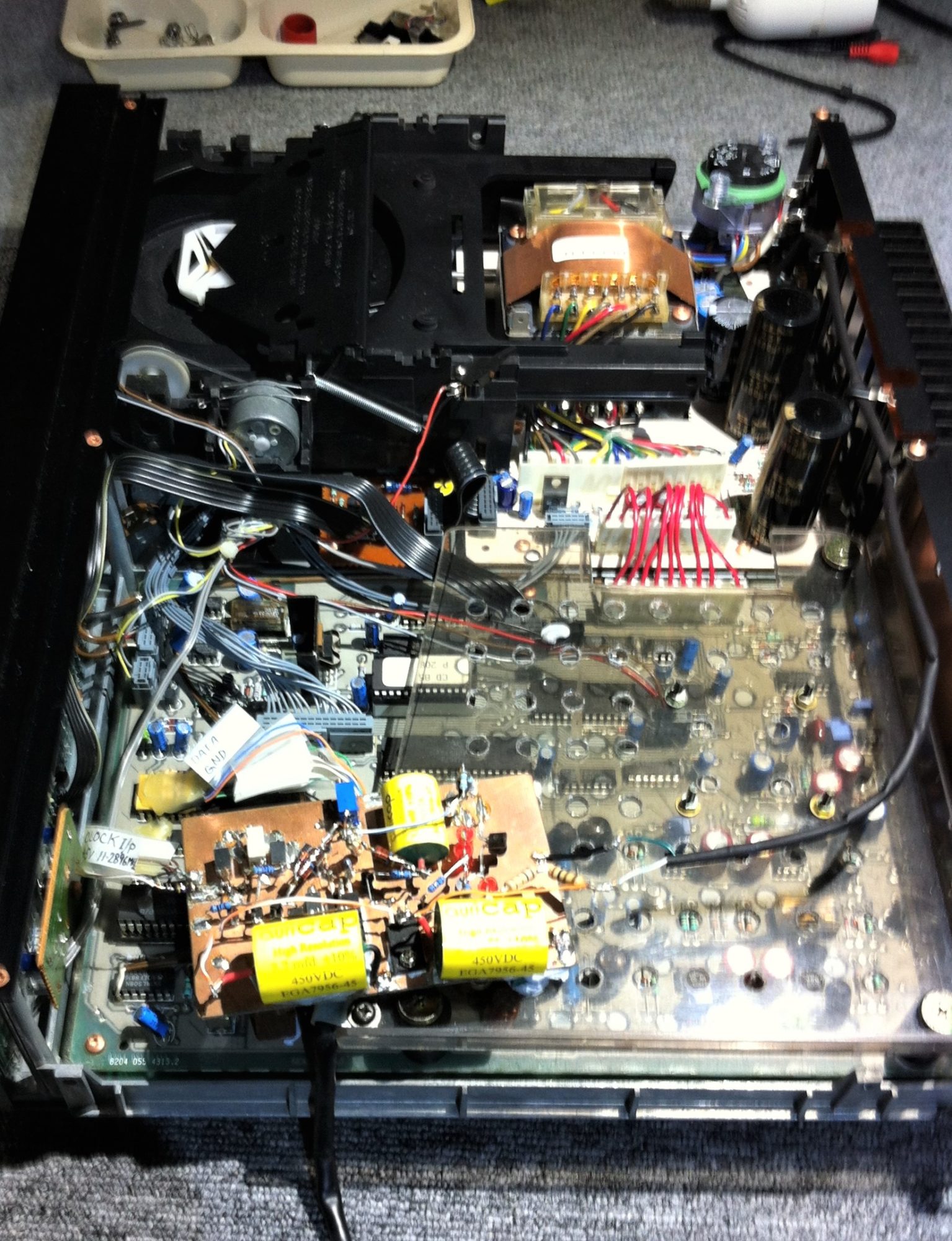
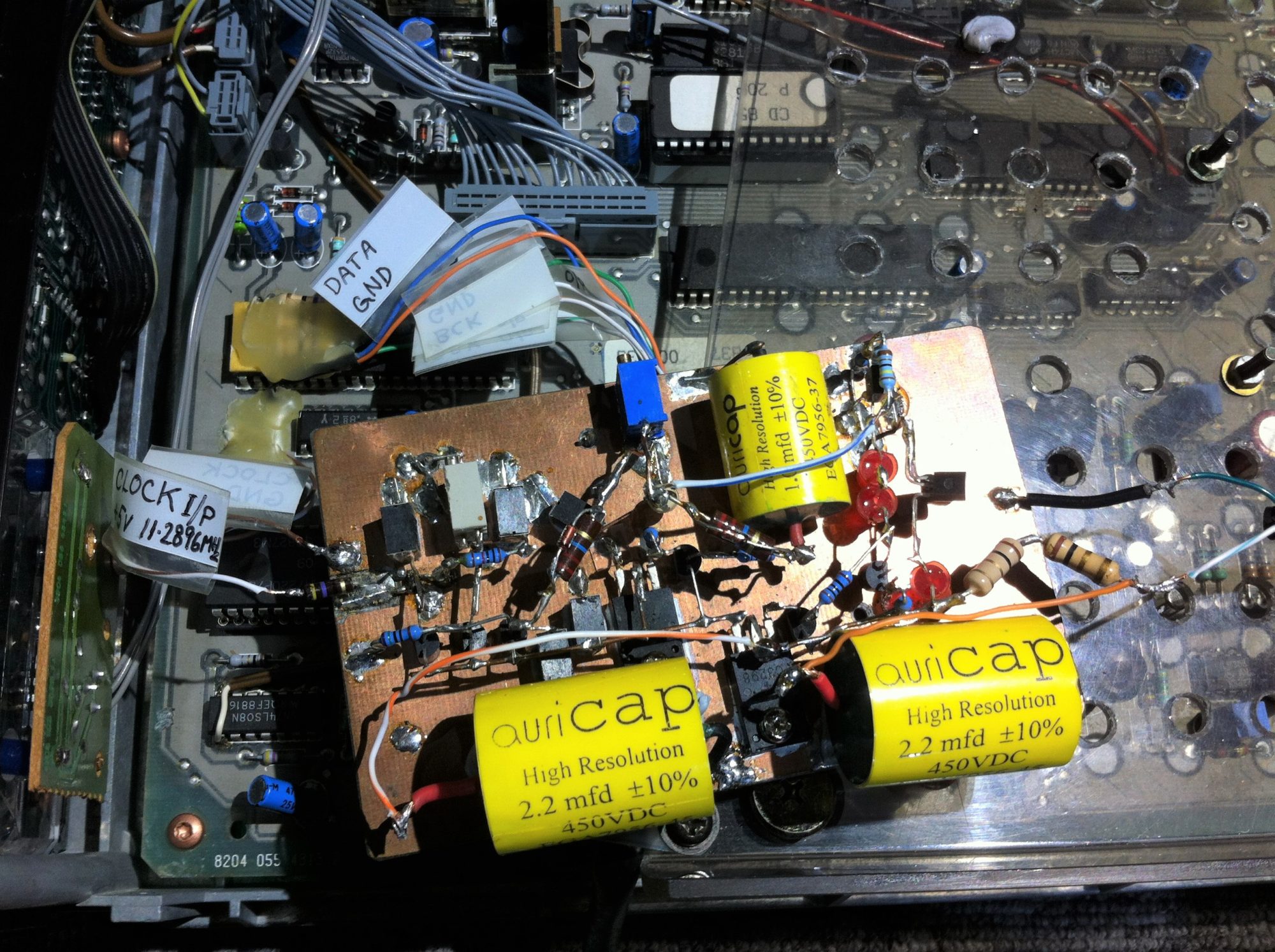
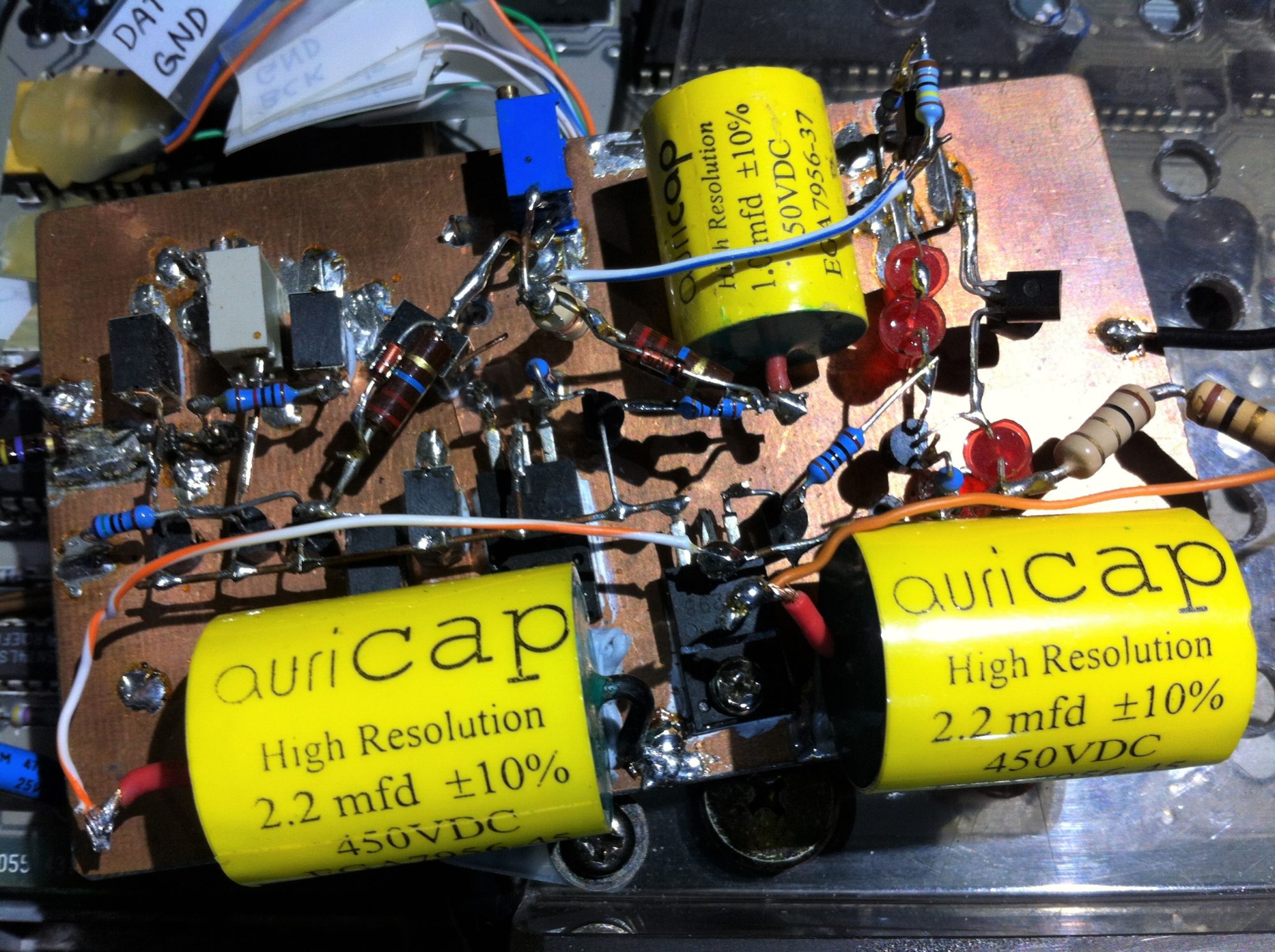
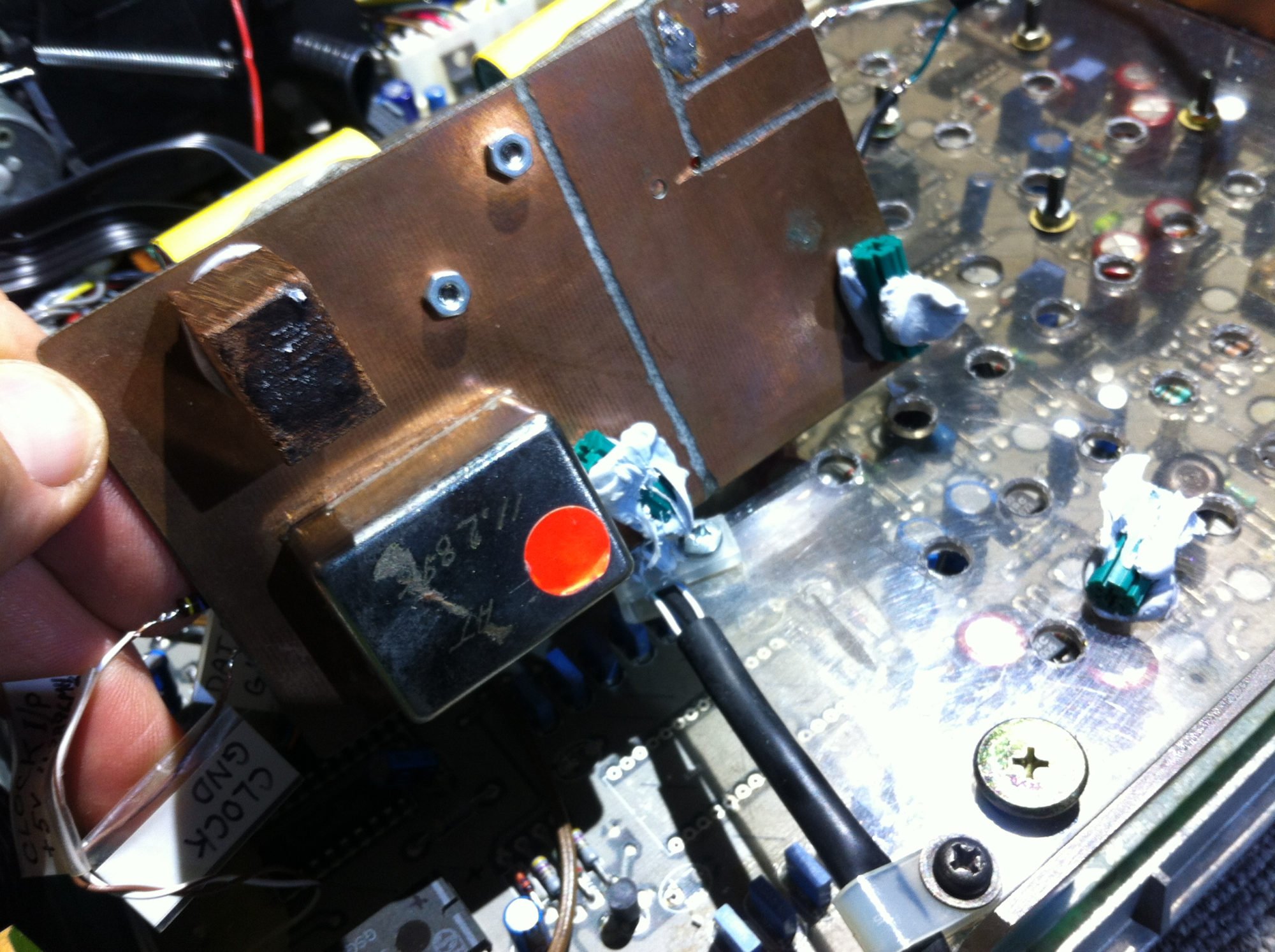
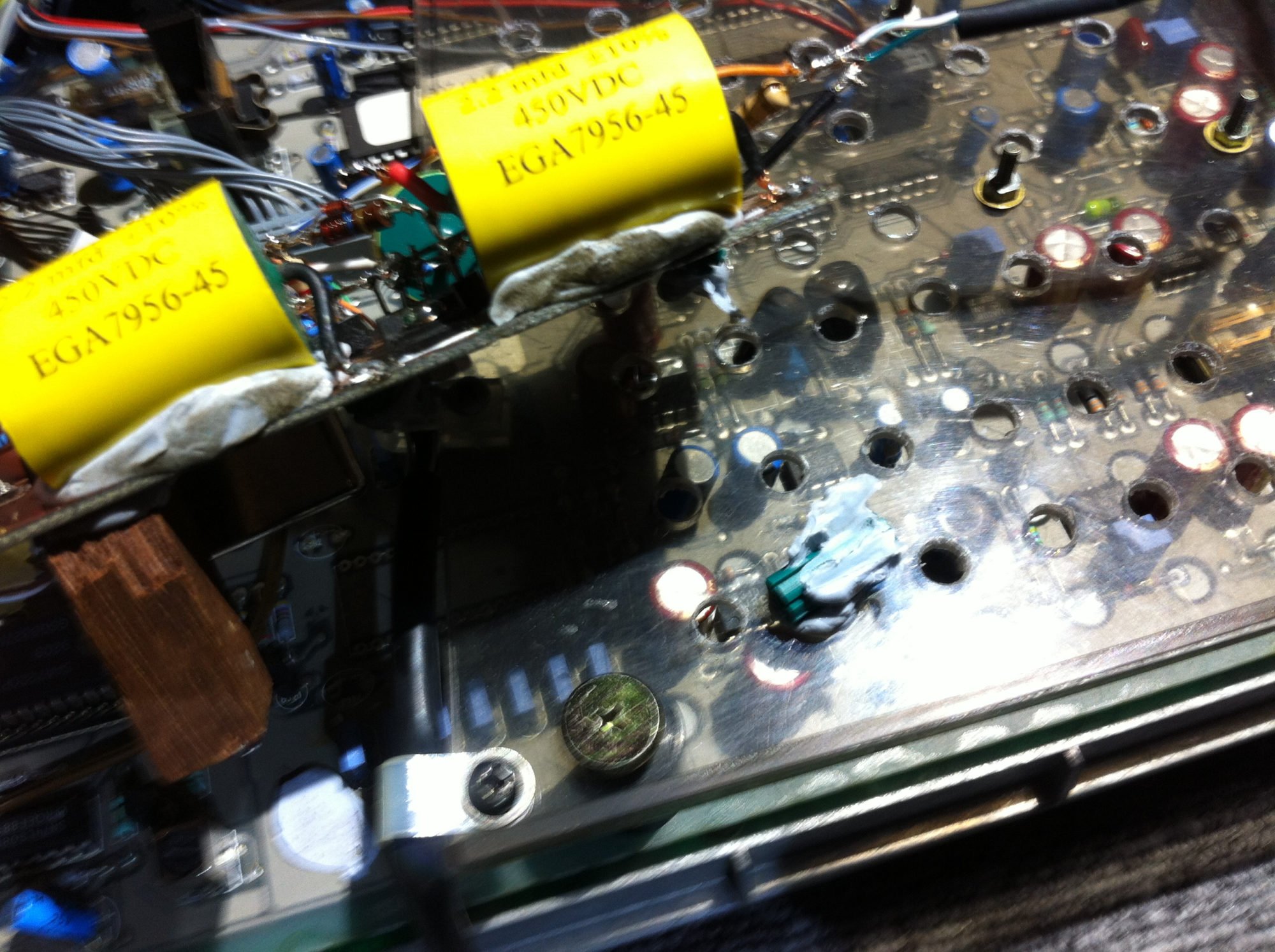
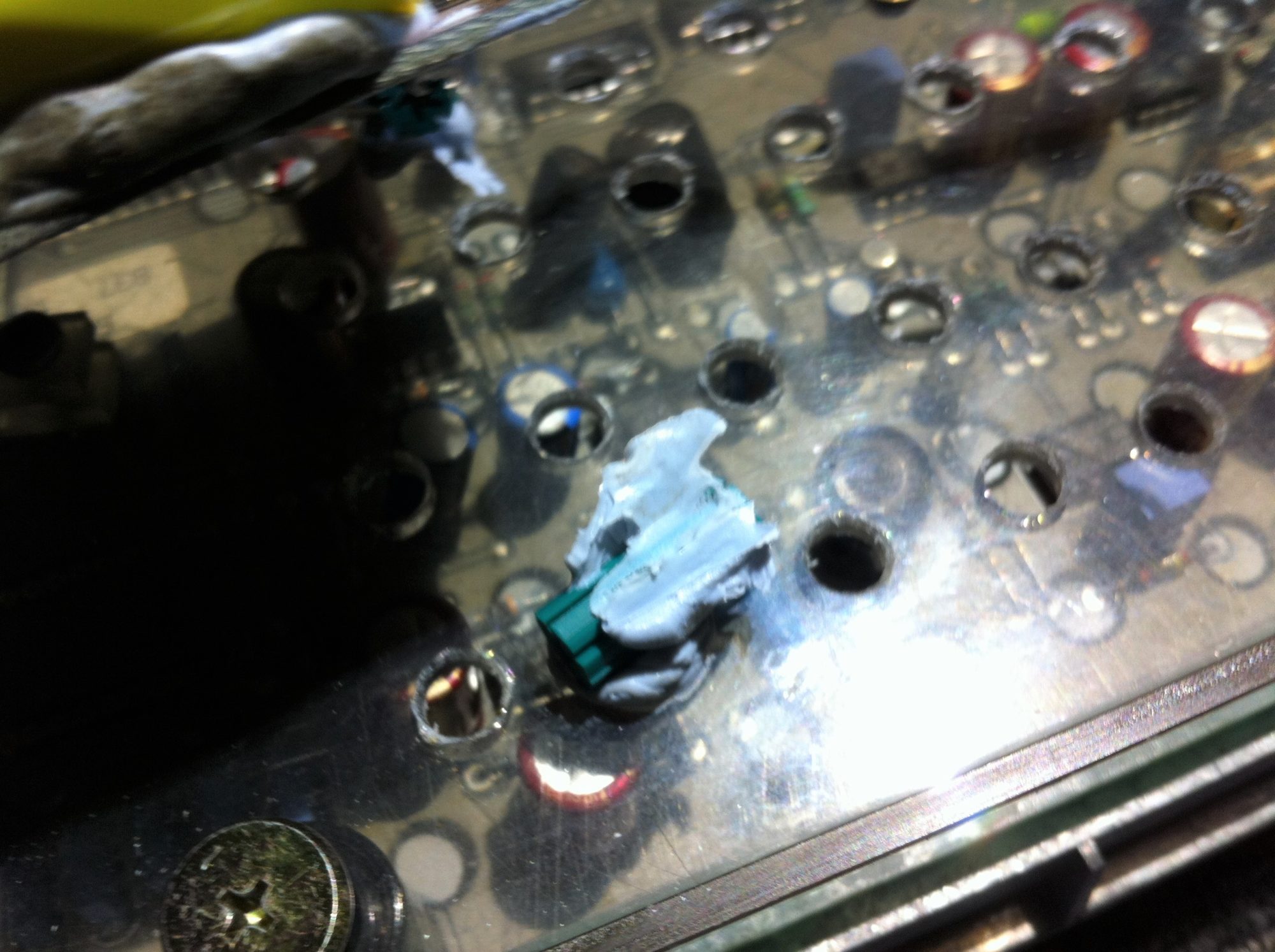
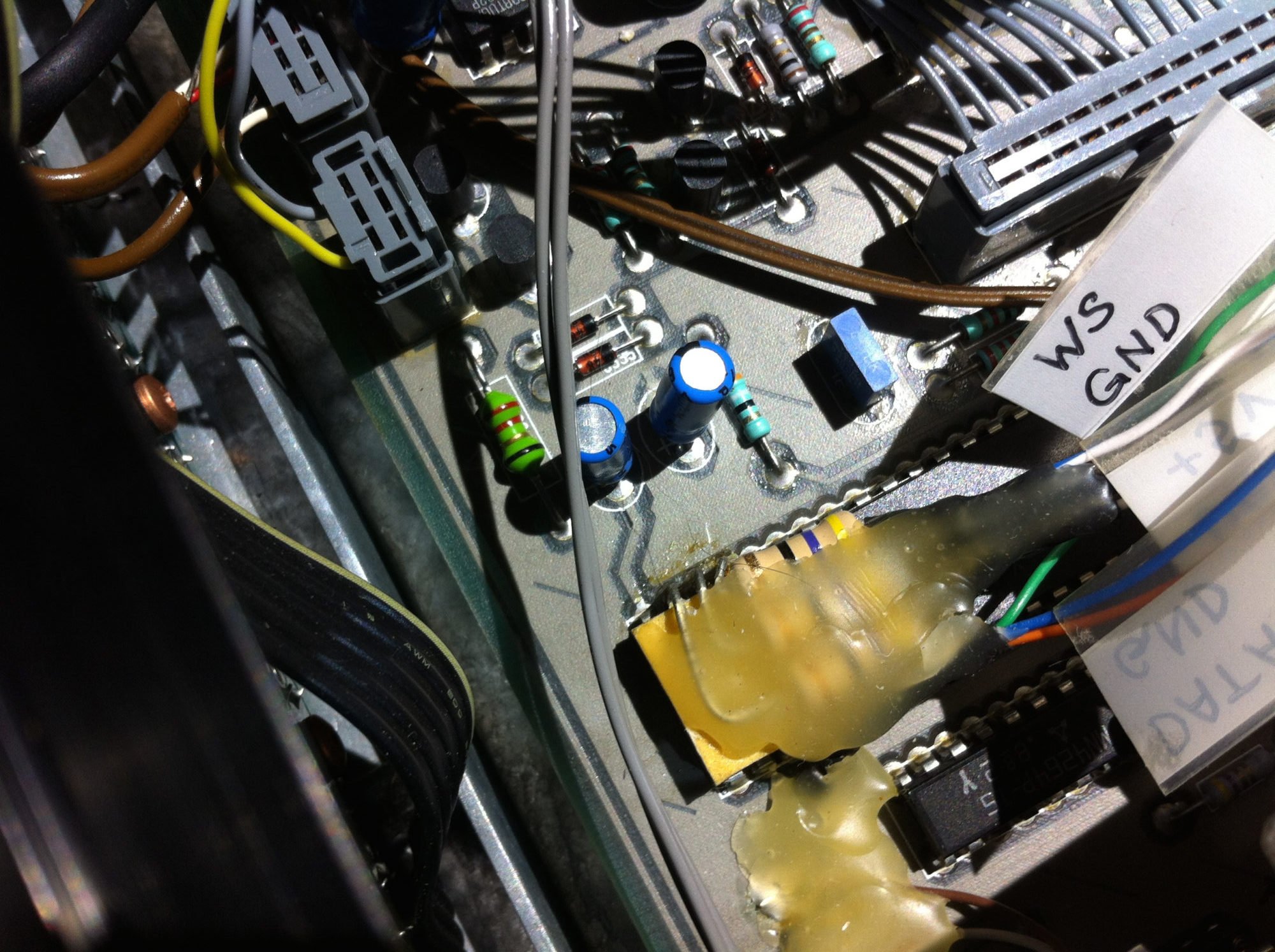

Case 4 – Krell KRC Preamplifier
This one hurts the most and is the single worst case here and the one most deserving of its place here in the Hall of Shame. My good friend Jason @ The Turntable Doctor shared this case with me and we’ve discussed the need to get the story out. Read on, because you won’t believe this one.
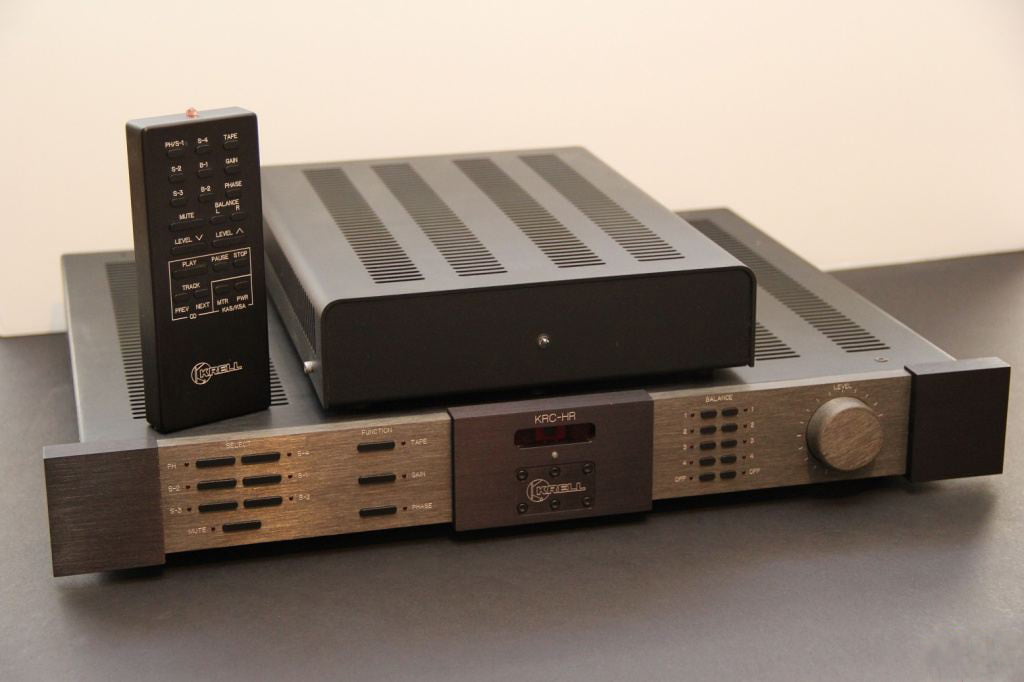
There’s a repairer on the east coast of Australia we’ll call Mr ‘Frampton’. No offence to the great Peter Frampton, but change one letter and you have this guy’s last name. Anyway, ‘Frampton’ supposedly improves hi-fi equipment, so a Perth local sent his cherished KRC-HR over to him. Here’s what happened.
First Signs of Trouble
When the customer eventually got his preamp back, neither the preamp nor the Krell remote control worked properly. He found a cheap Chinese remote control included in the package and when pressed, Frampton informed the owner that he had ‘upgraded’ the volume control and included an ‘improved’ $6 Chinese remote control to replace the clunky old machined and anodised aluminium Krell remote… Classy.
Oh boy, try to stop me from writing the rest of this…
The Krell KRC is a superb preamp. If you want to see more, check out my KRC-HR restoration. Costing over $10,000 AUD in the mid-1990s, there aren’t many improvements you can make to a preamp like this and any real repairer would know enough not to try anything silly.
The KRC and KRC-HR use logic-controlled stepped resistive attenuators for volume control. This is the best way to control volume. The attenuator uses an array of 0.1% precision laser-trimmed resistors, an optical encoder, a CPU and switches. The signal is routed through expensive nitrogen-filled relays.
Let me be clear – this volume control can’t be upgraded, period. Krell did the engineering and it’s for us to try to learn something from it. It’s unbelievably foolish and naive to think that a hack doing second-rate repair work could improve the volume control implementation in this preamp.
Wanna see some REALLY bad repairs? Let’s go.
A Normal Krell KRC
This is what a Krell KRC preamp looks like. Check out this article where I completely restored one of these beauties.
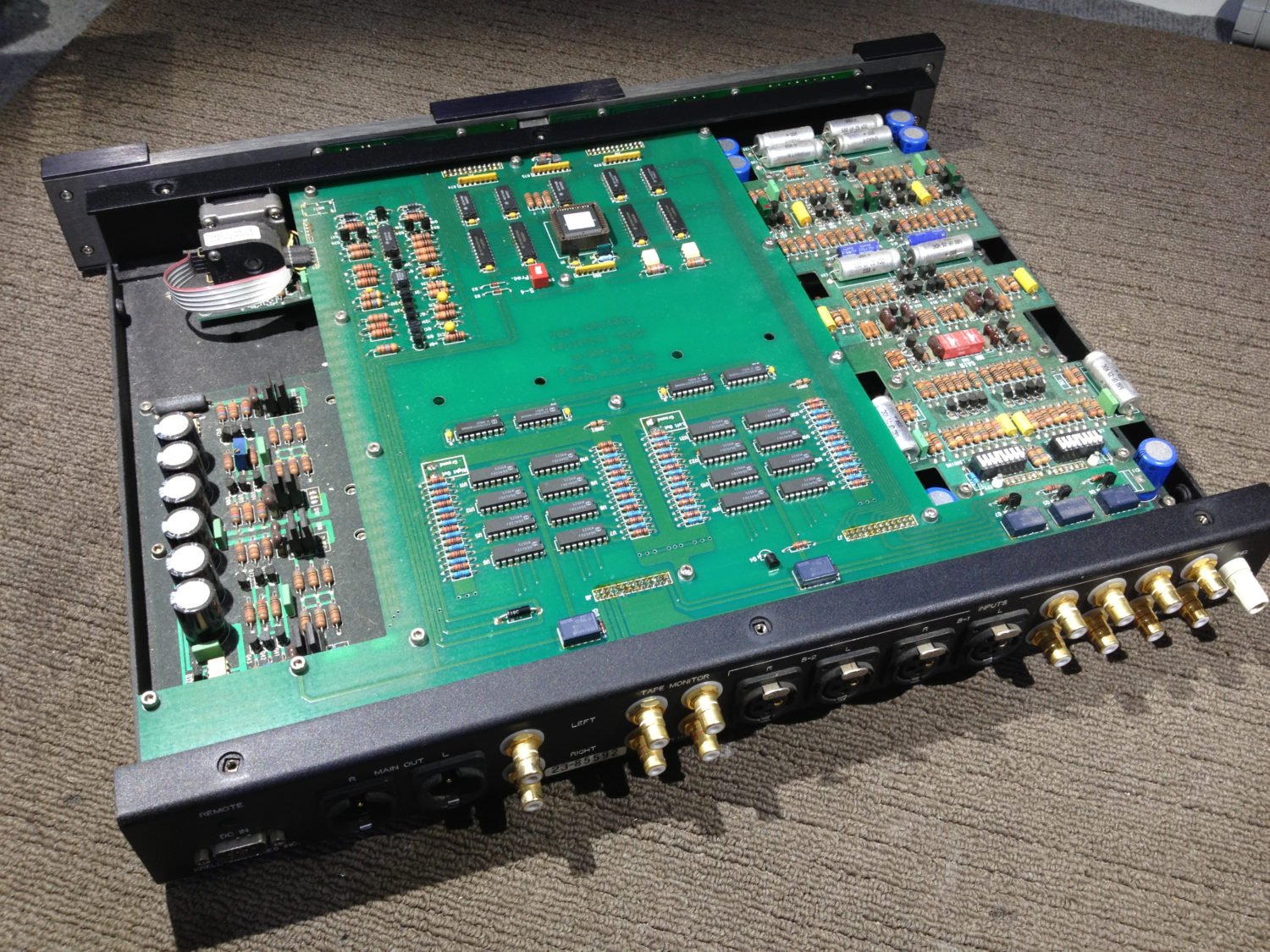
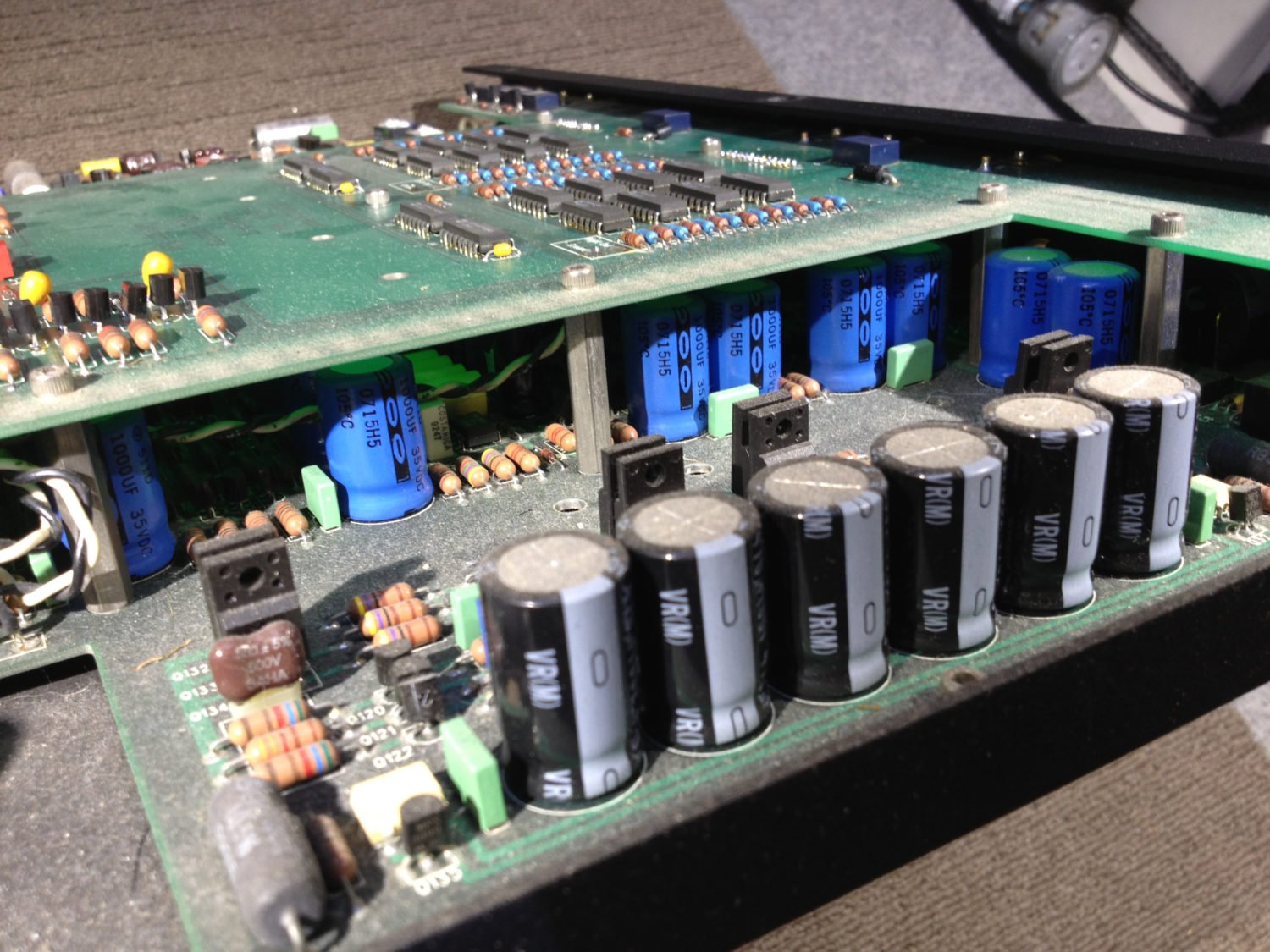
The Frampton Krell KRC…
Let’s take a look at the ‘improved’ KRC, after some bad repairs by Mr Frampton. We’ll start with the preamp and then look at the power supply.
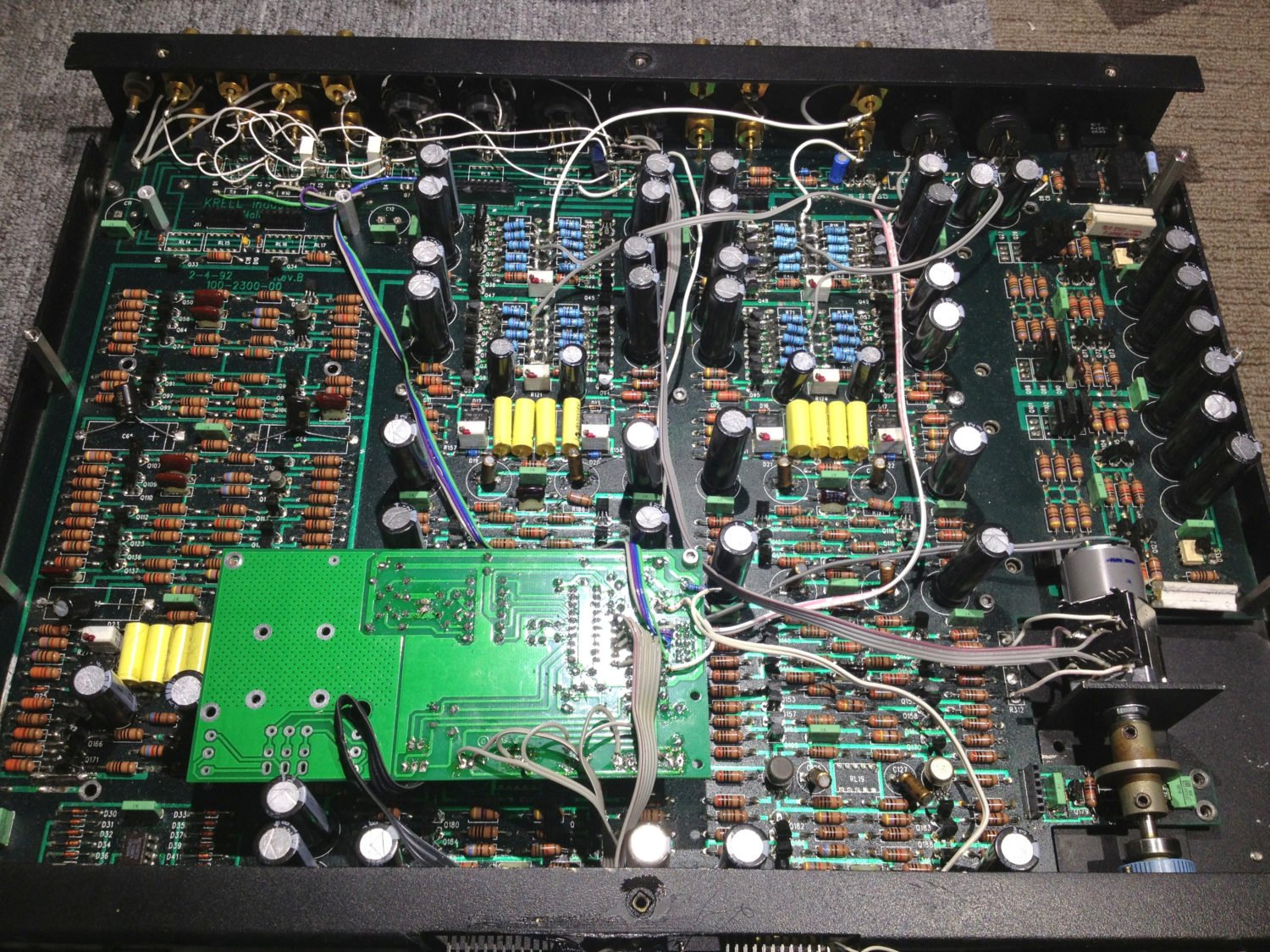
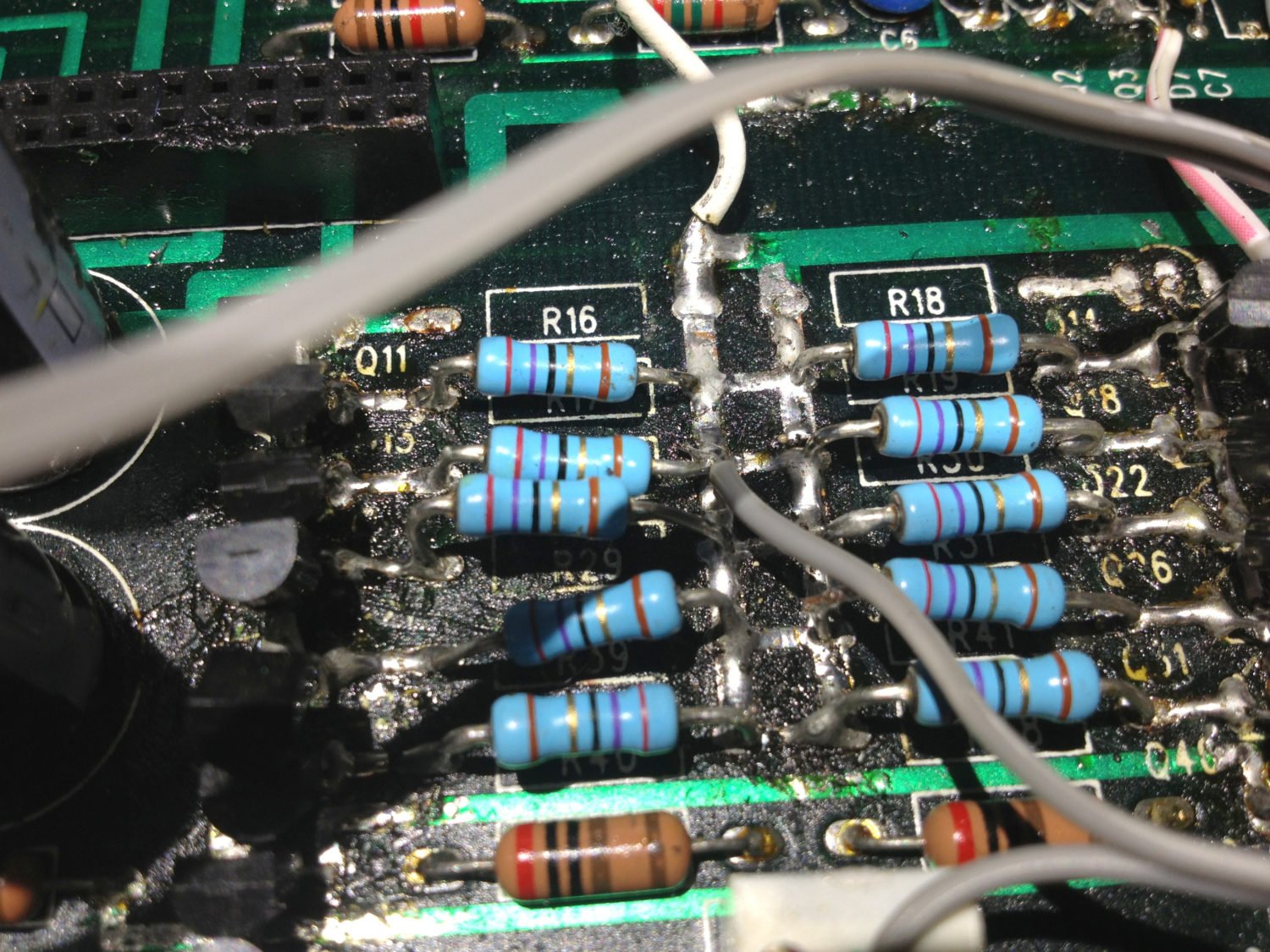
Frampton probably destroyed the precision Krell volume control board by accident. Nobody of sound mind would assume they could ‘upgrade’ it, let alone try to.
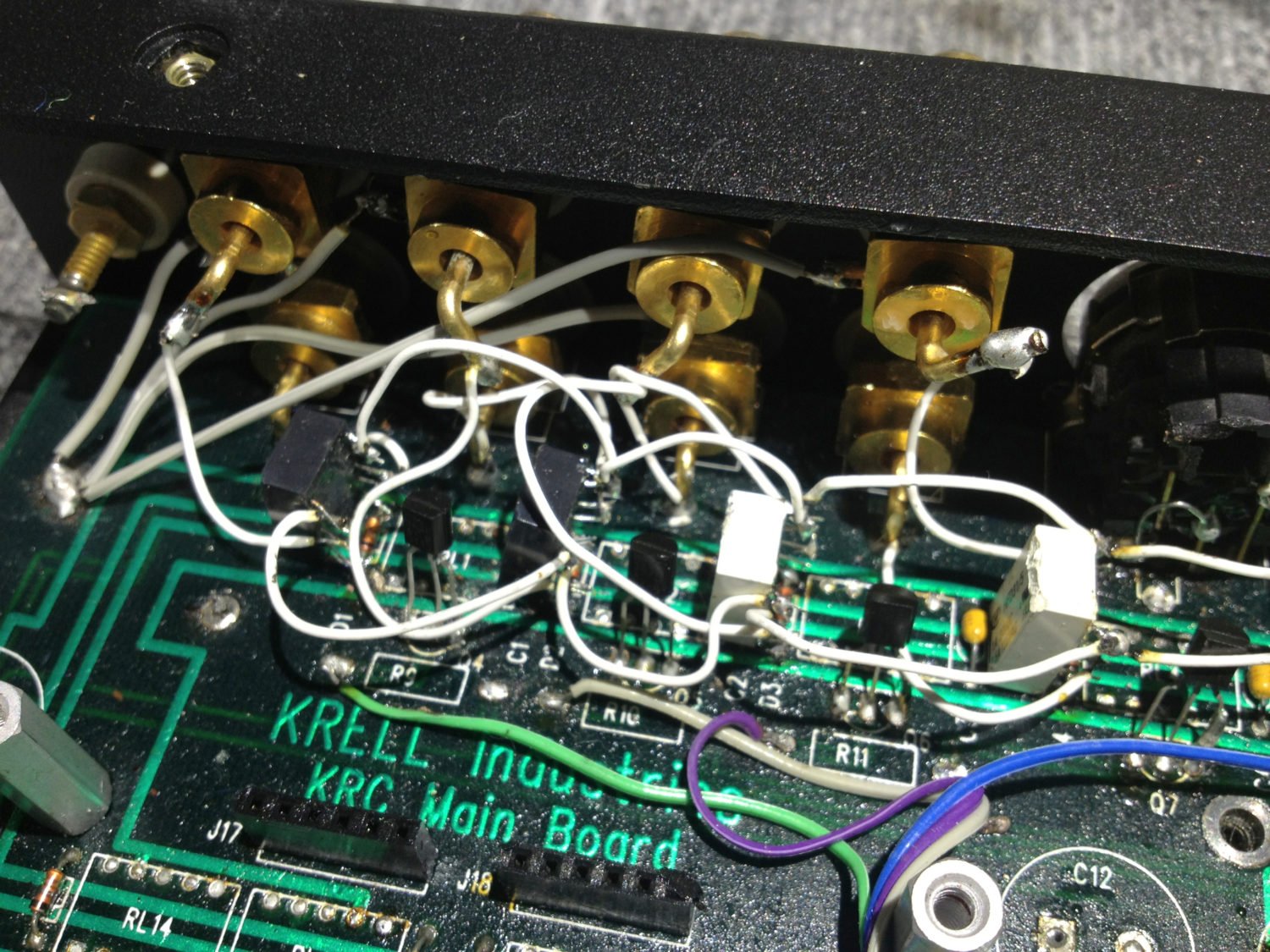
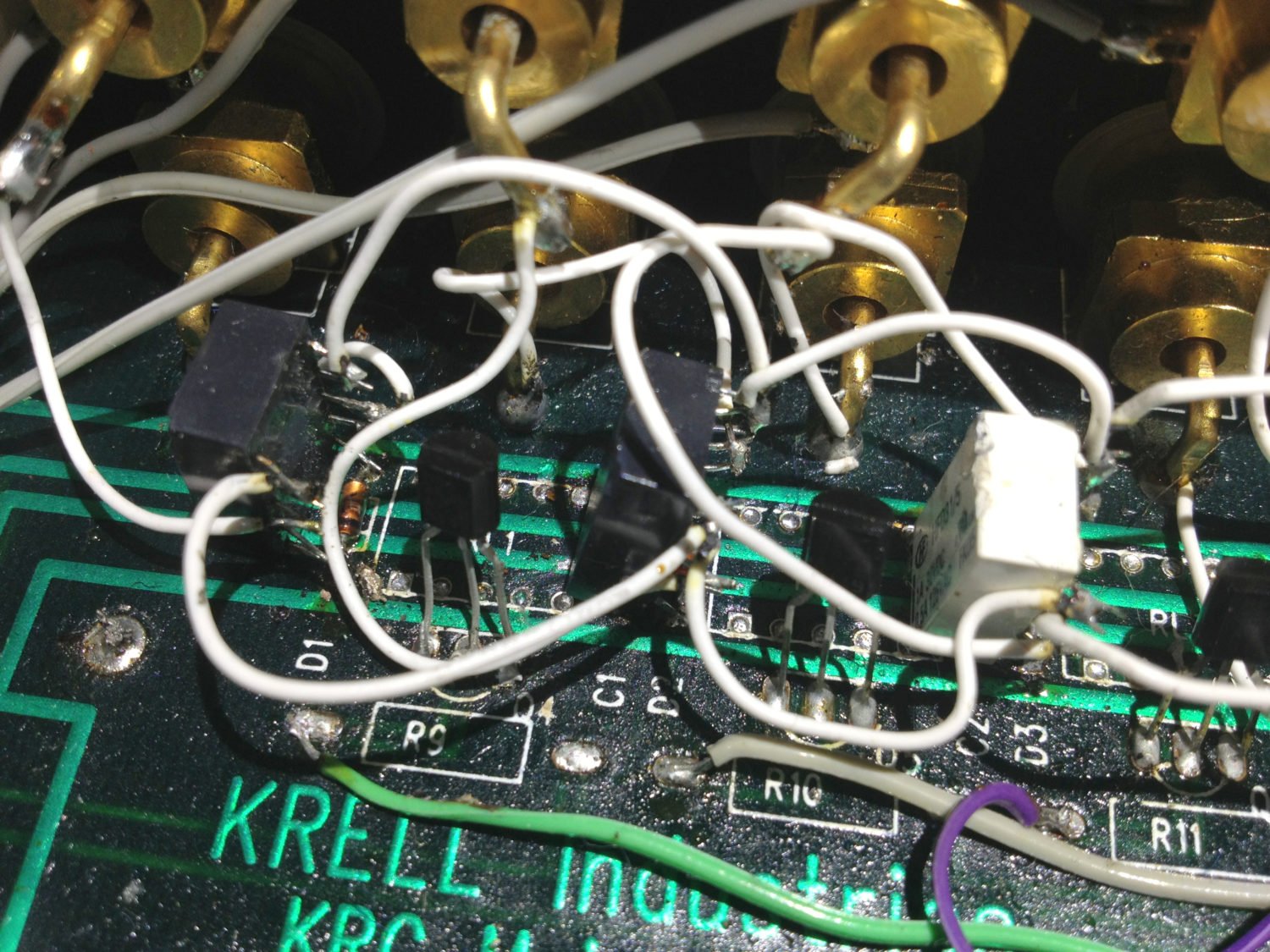
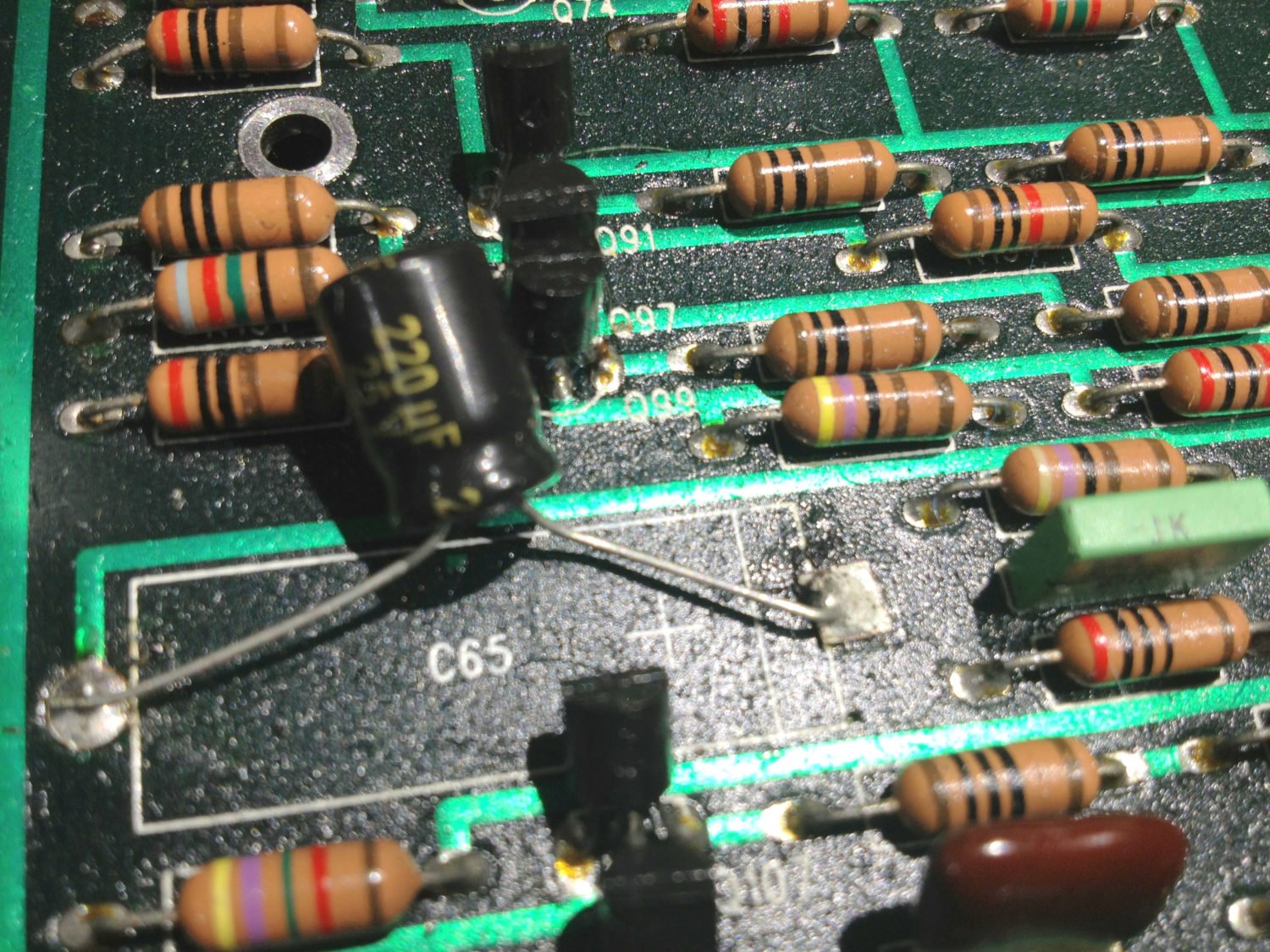
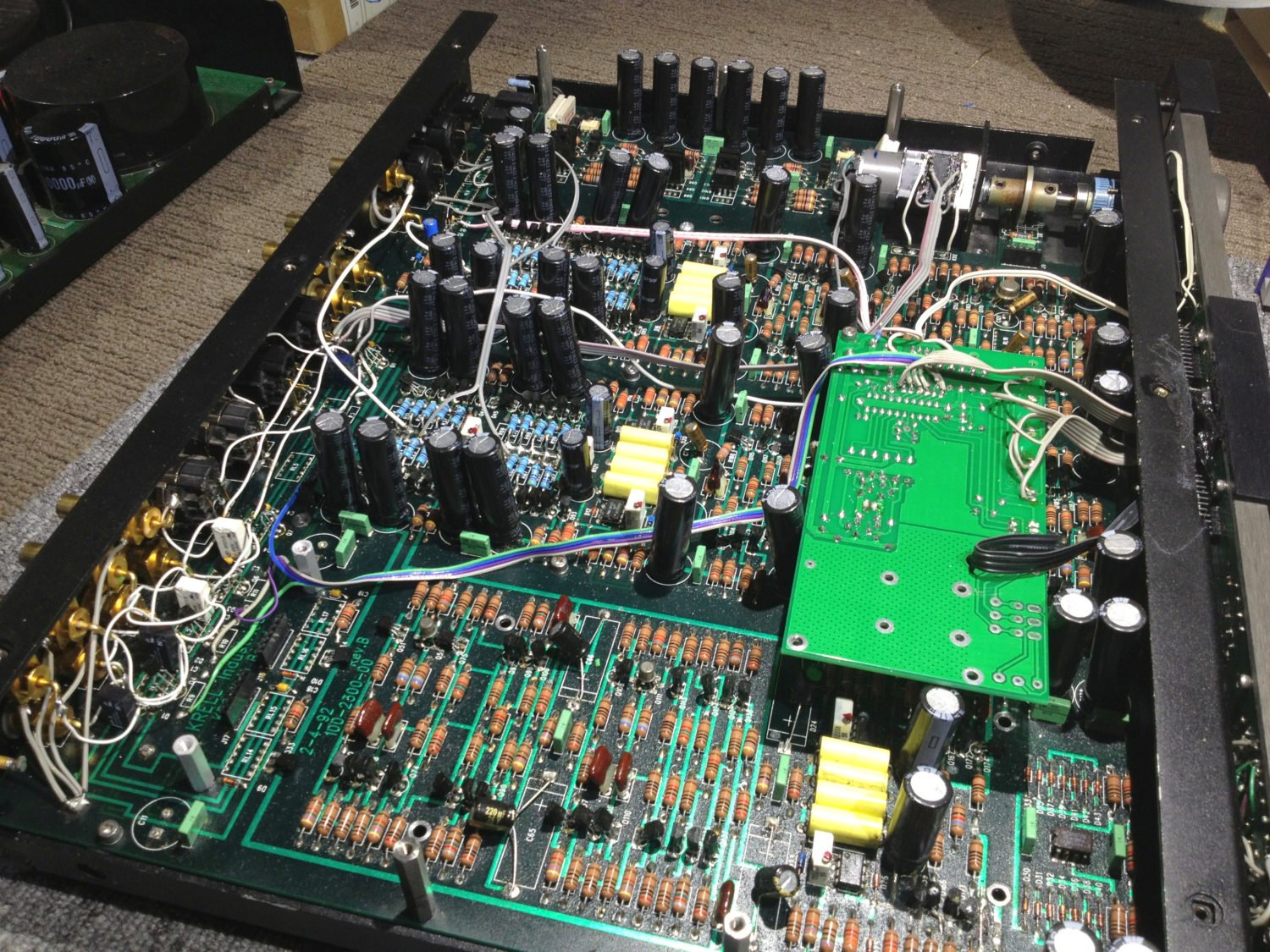
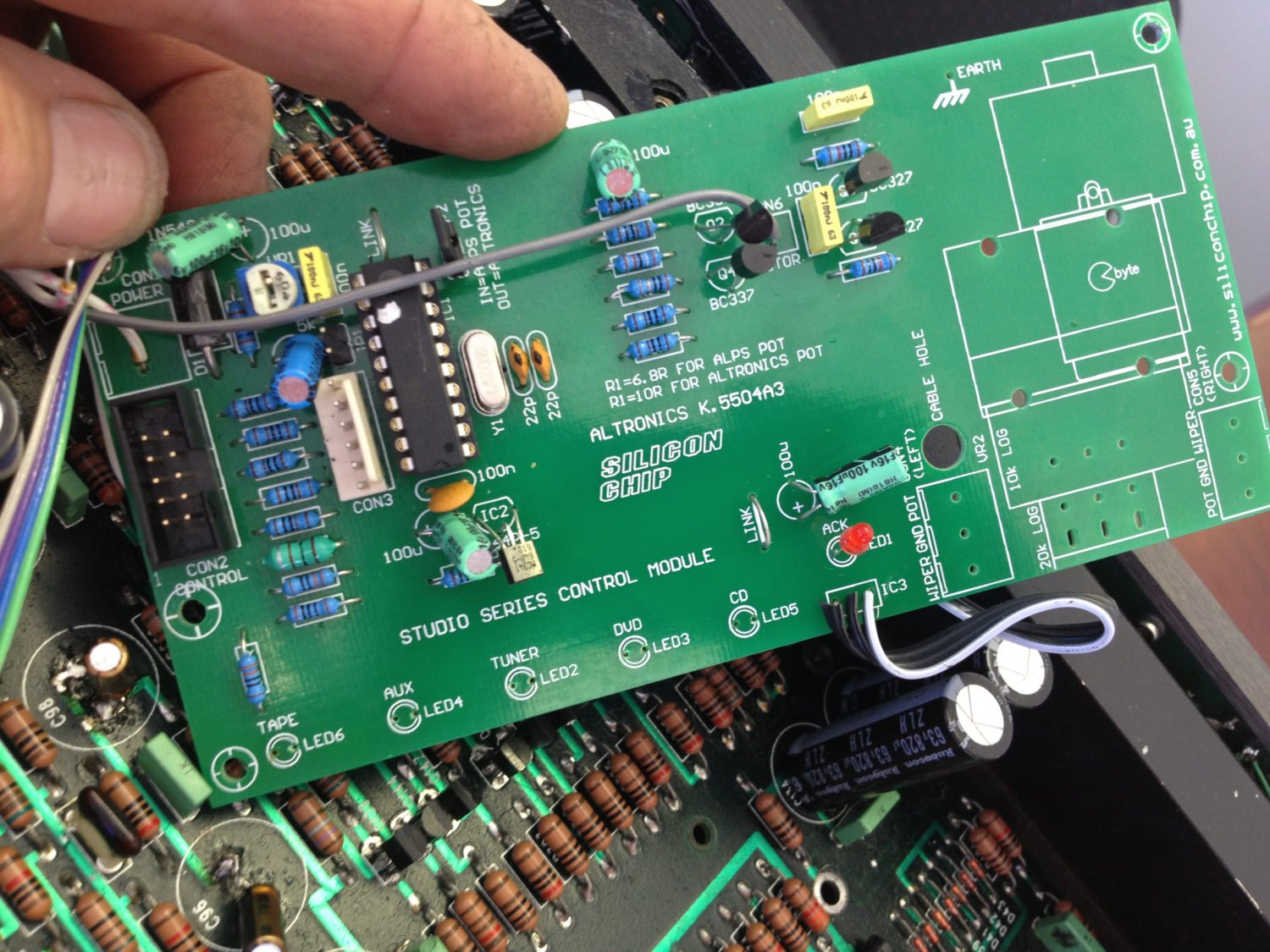
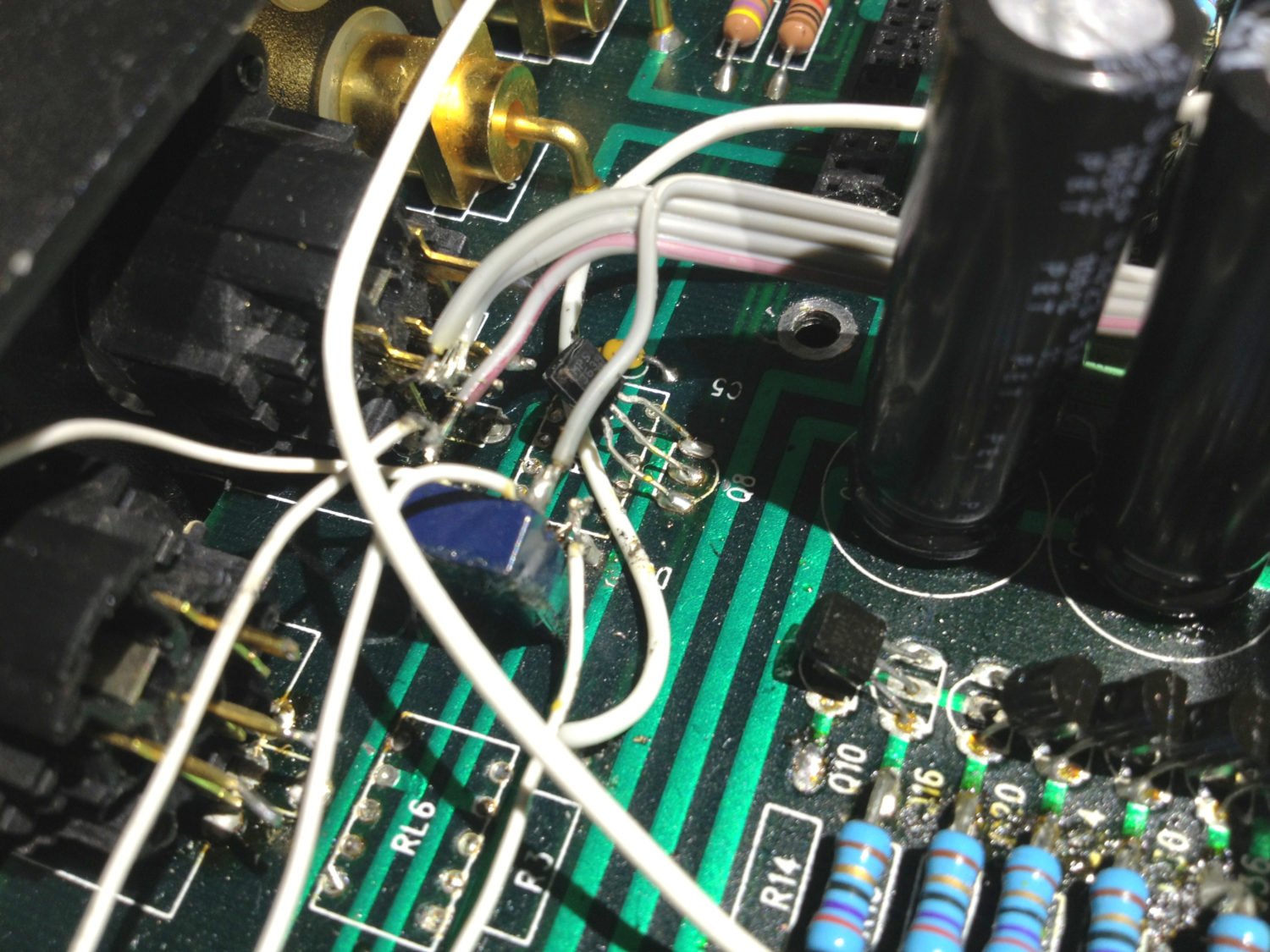
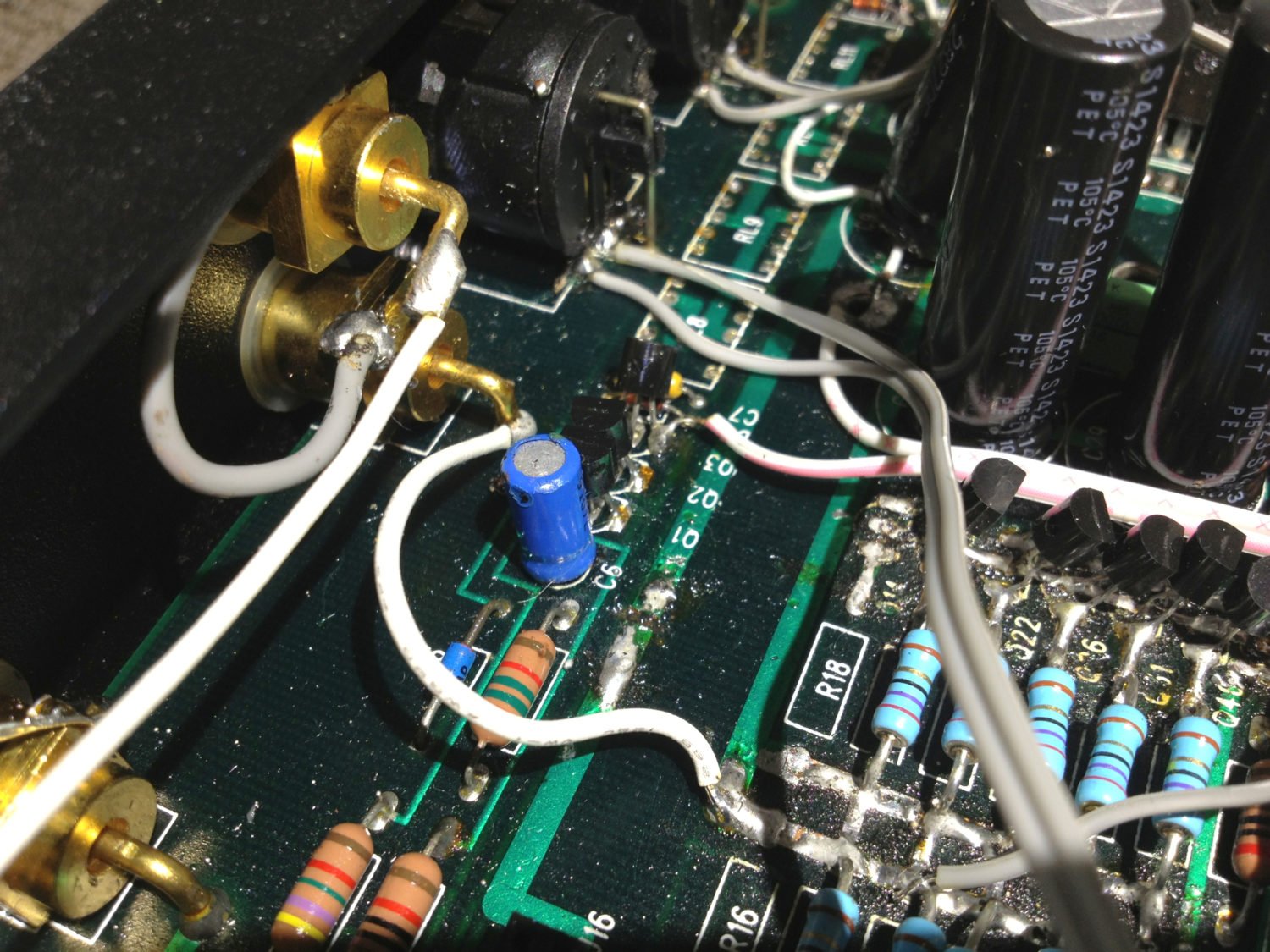
When asked how he could possibly have produced work of this standard, Mr Frampton cheerfully replied that he “taught this stuff”. Yes, he said that. I’d ask for a different teacher, kids.
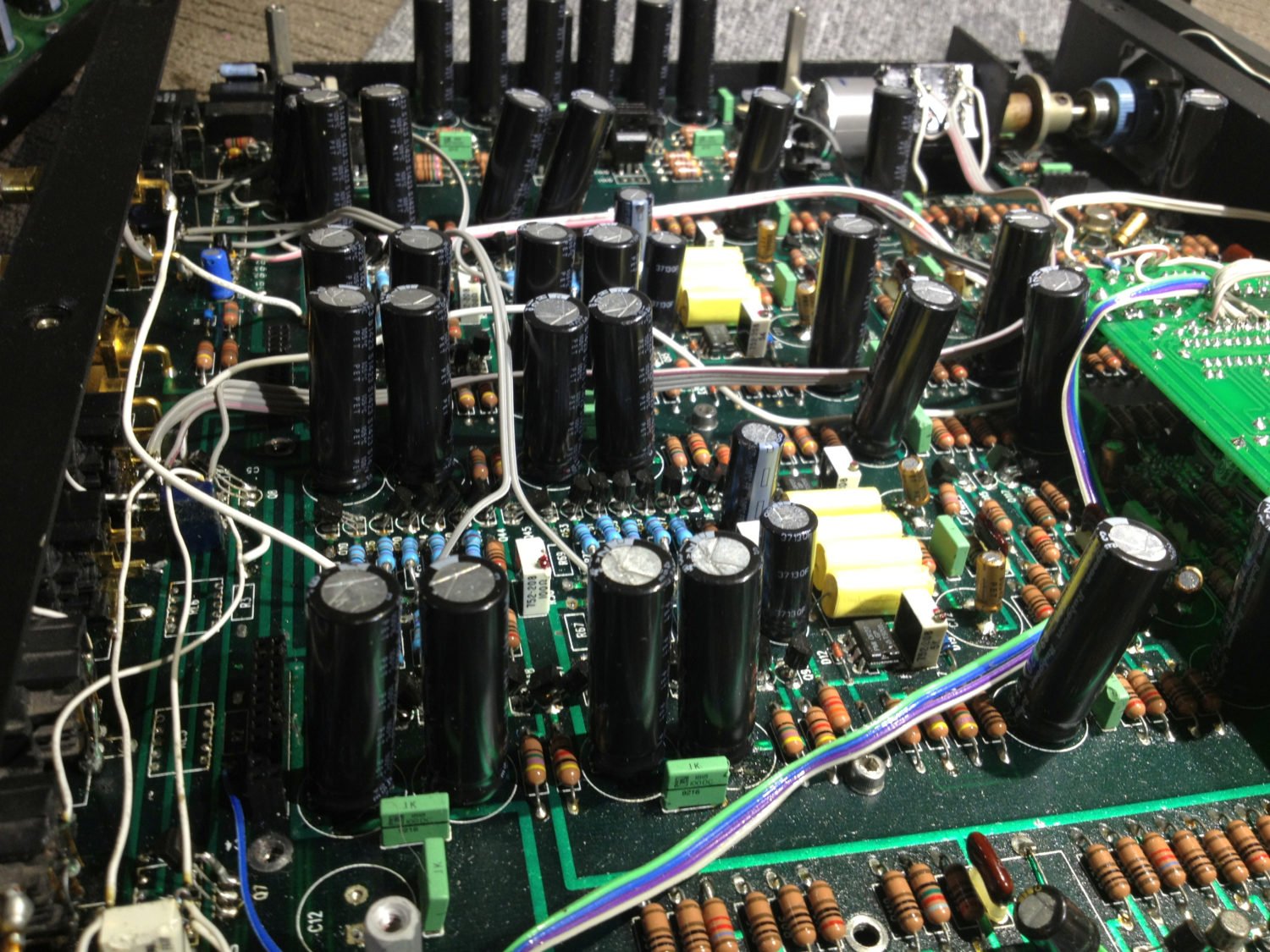
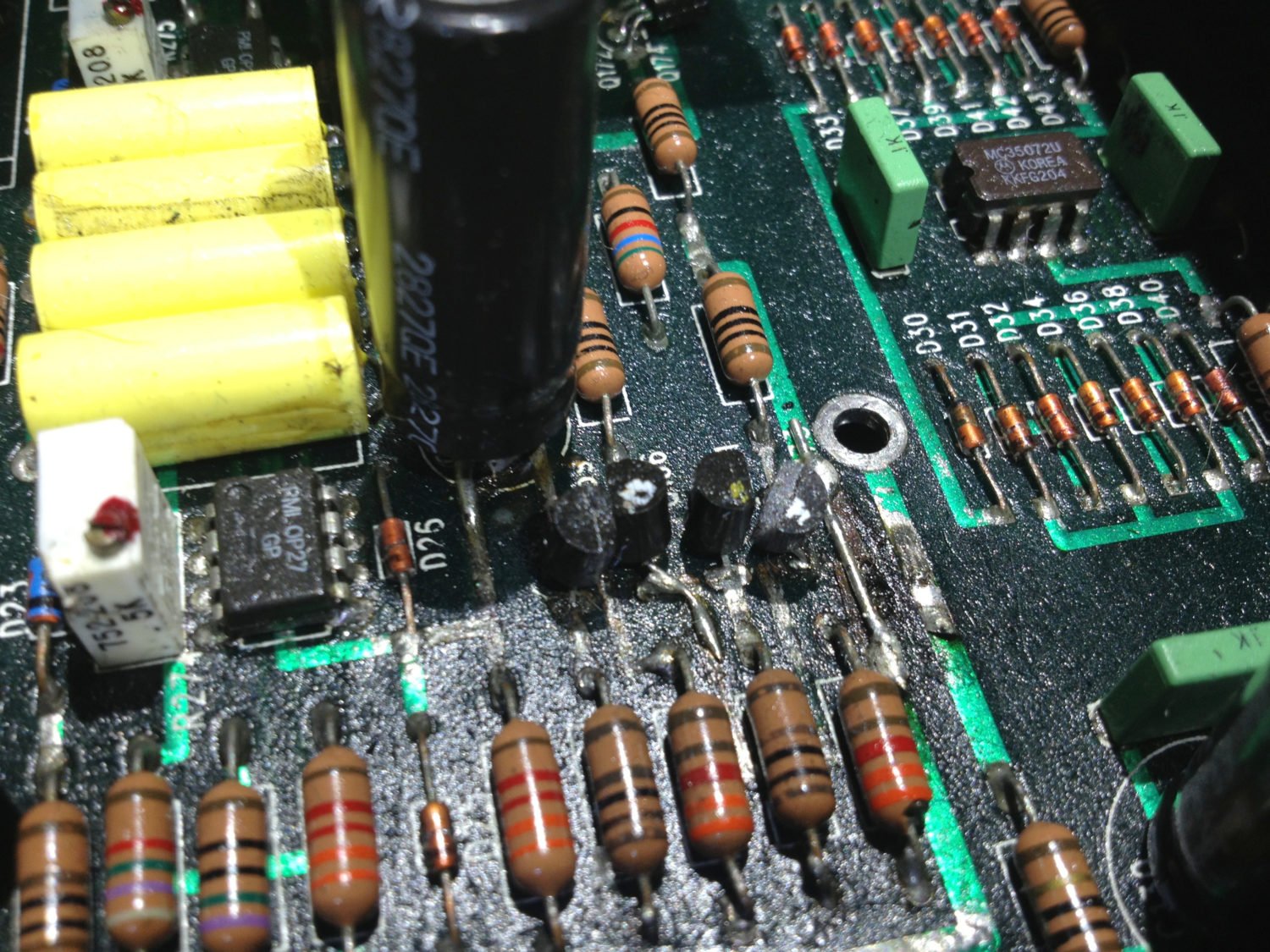
The Power Supply
Let’s take a look at bad repairs in the KRC power supply.
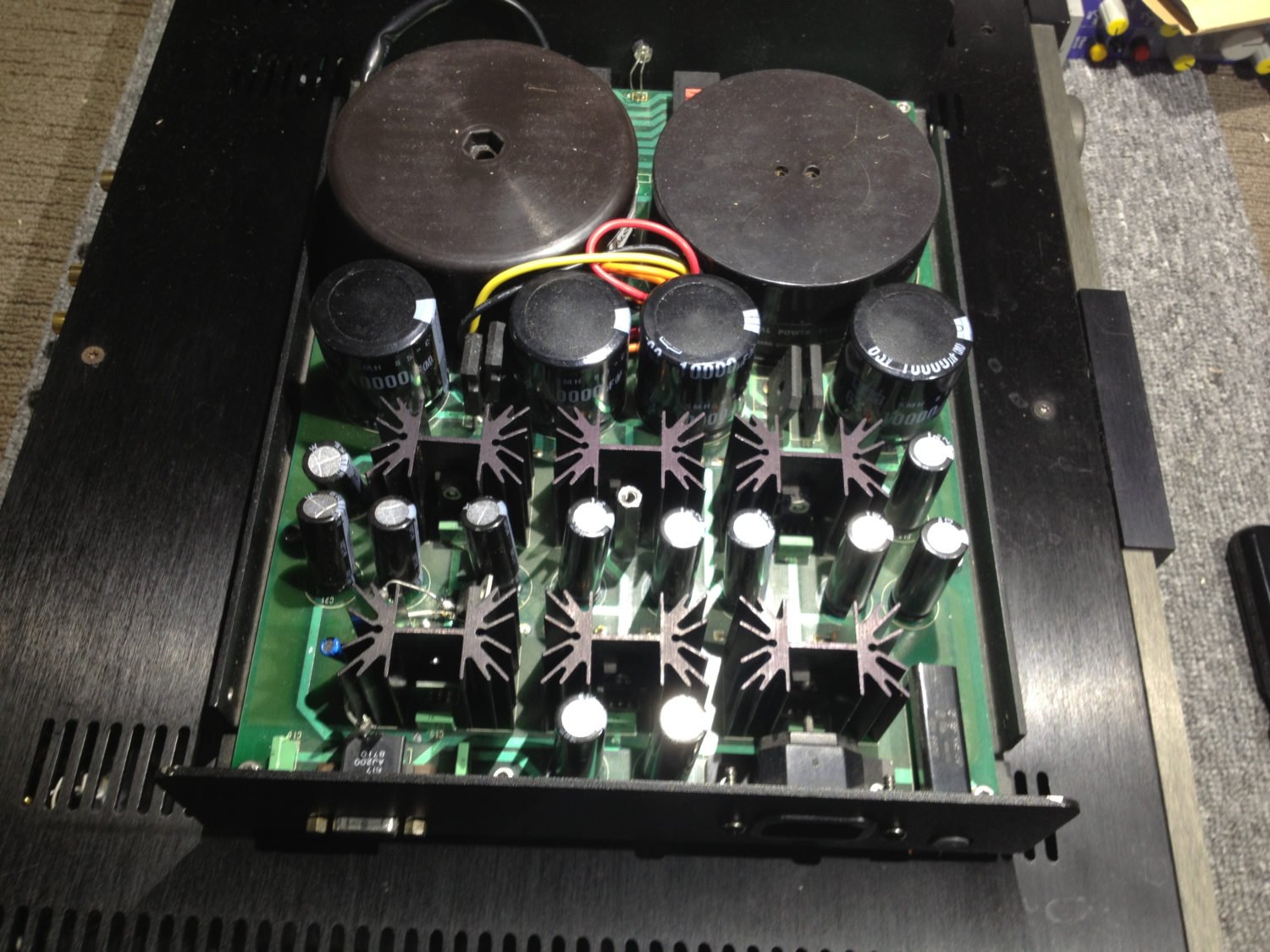
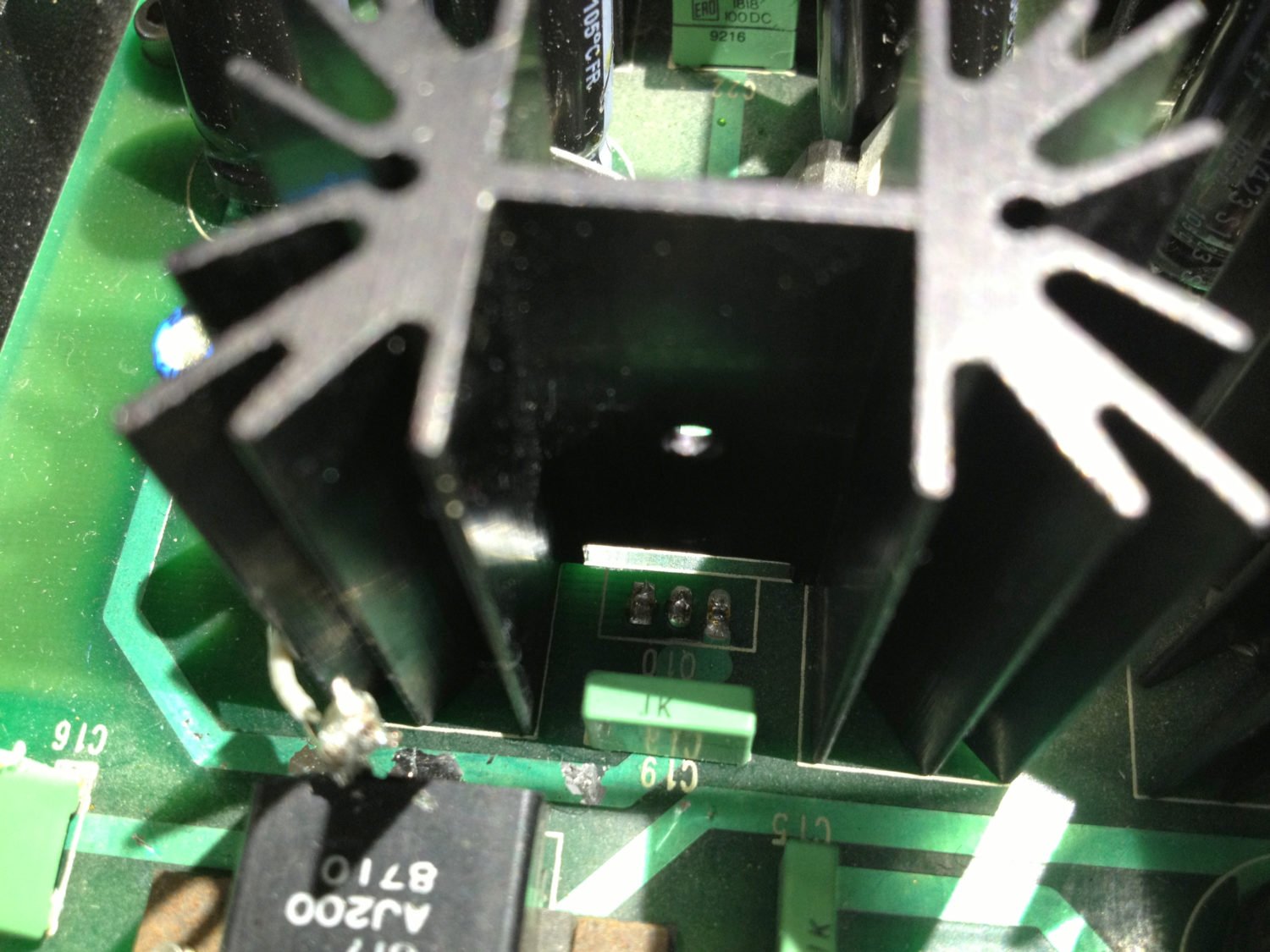
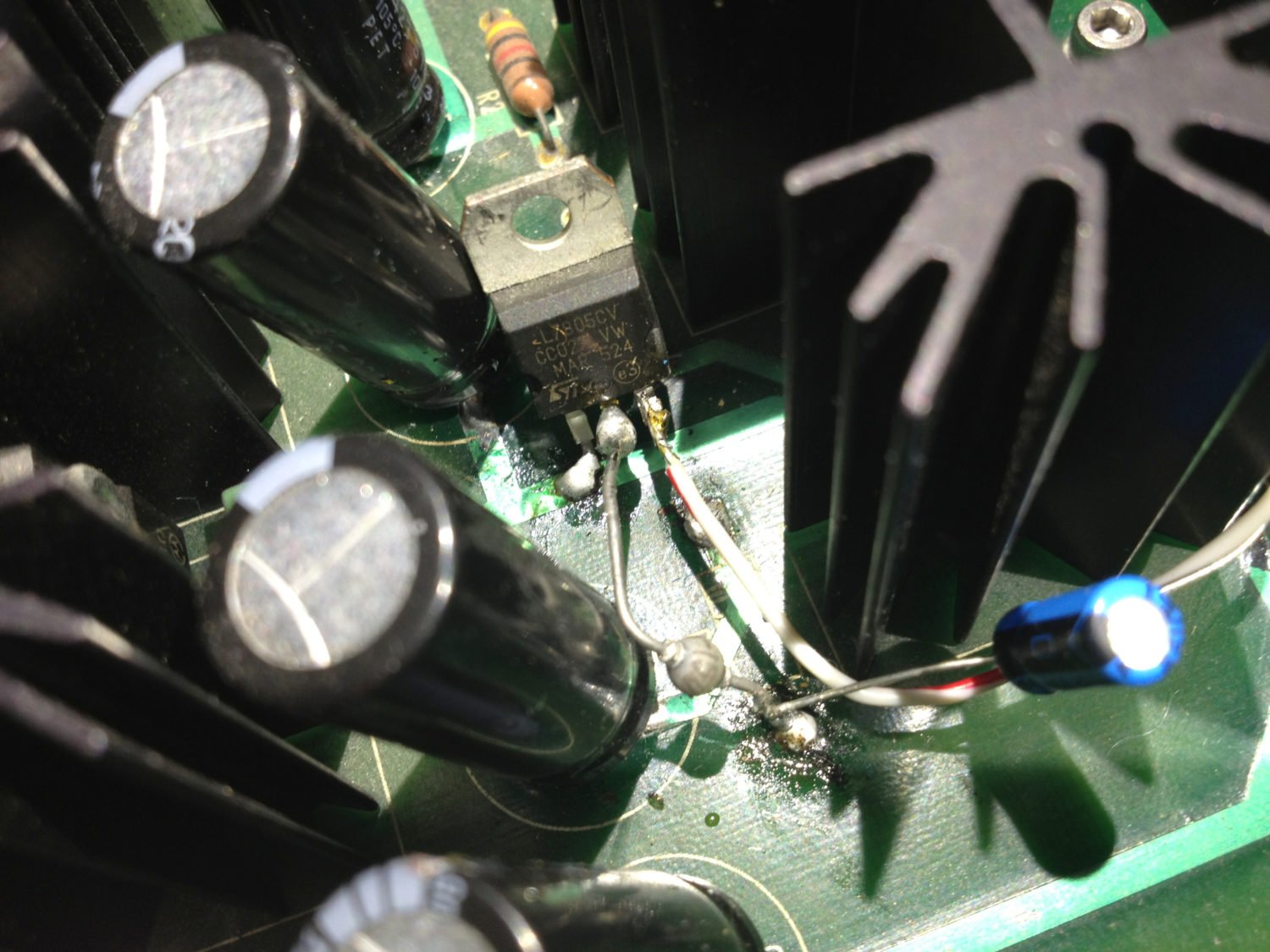
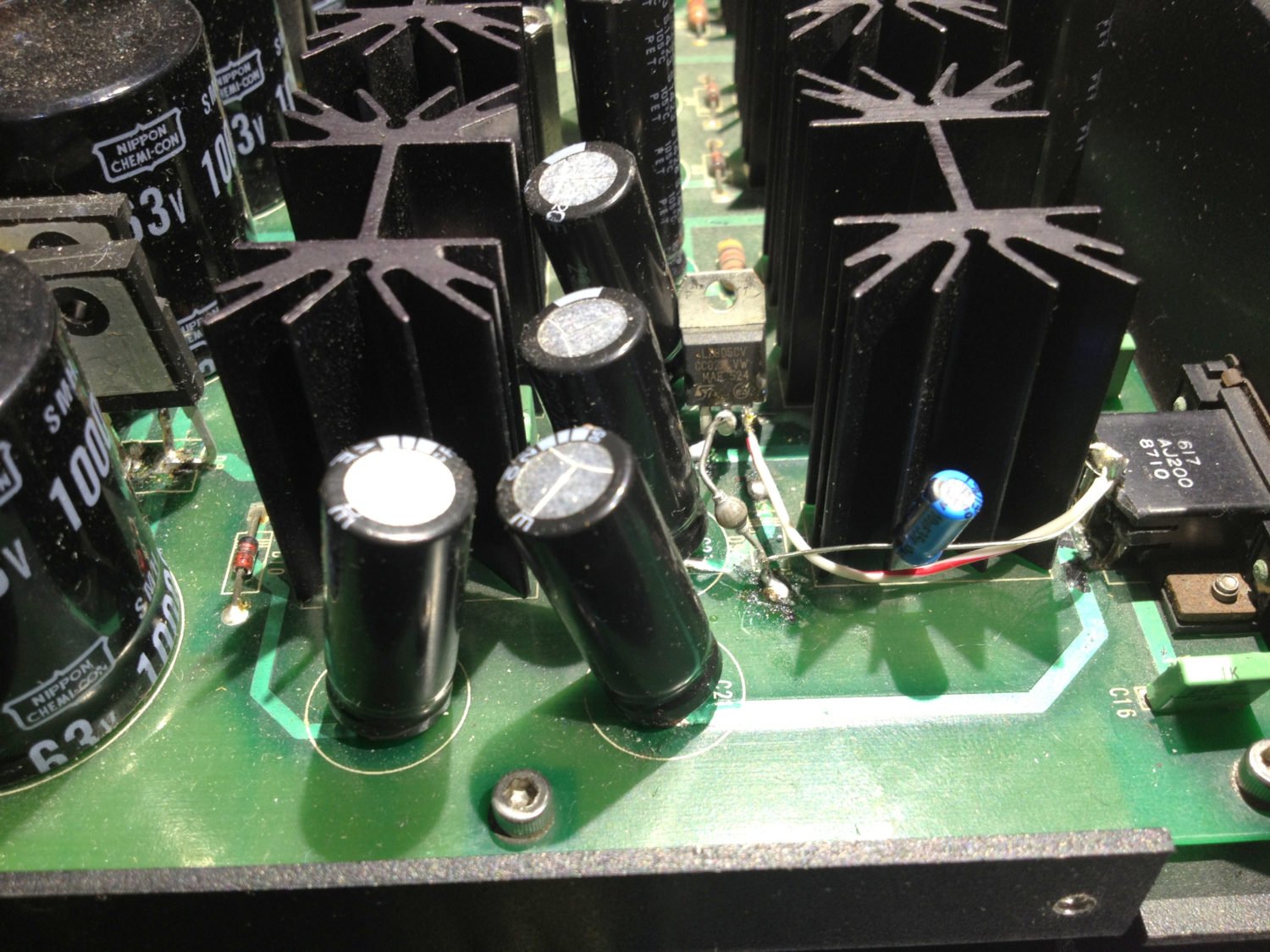
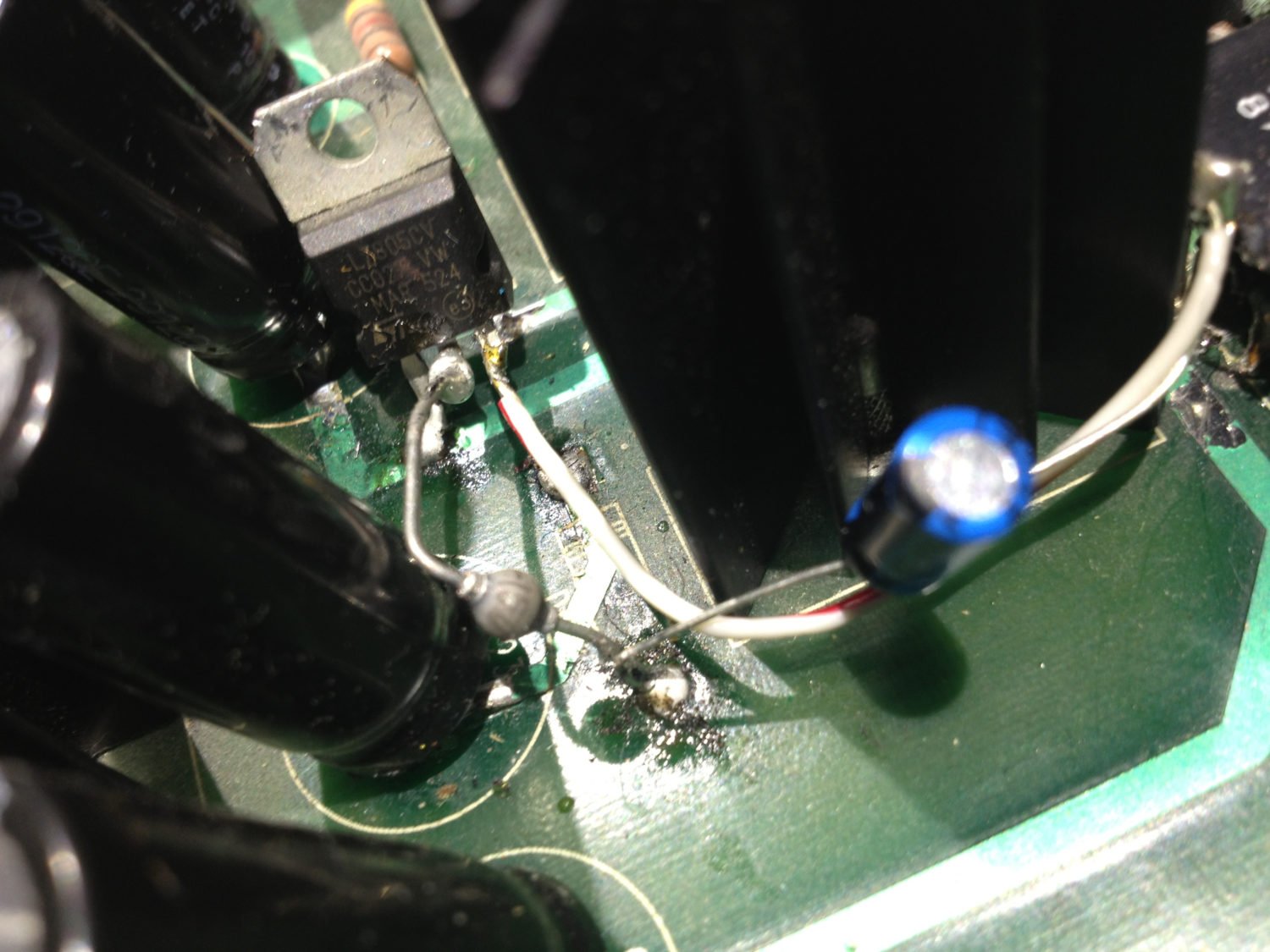
Mr Frampton likely blew up the power supply by shorting something in the preamp. Here’s more evidence.
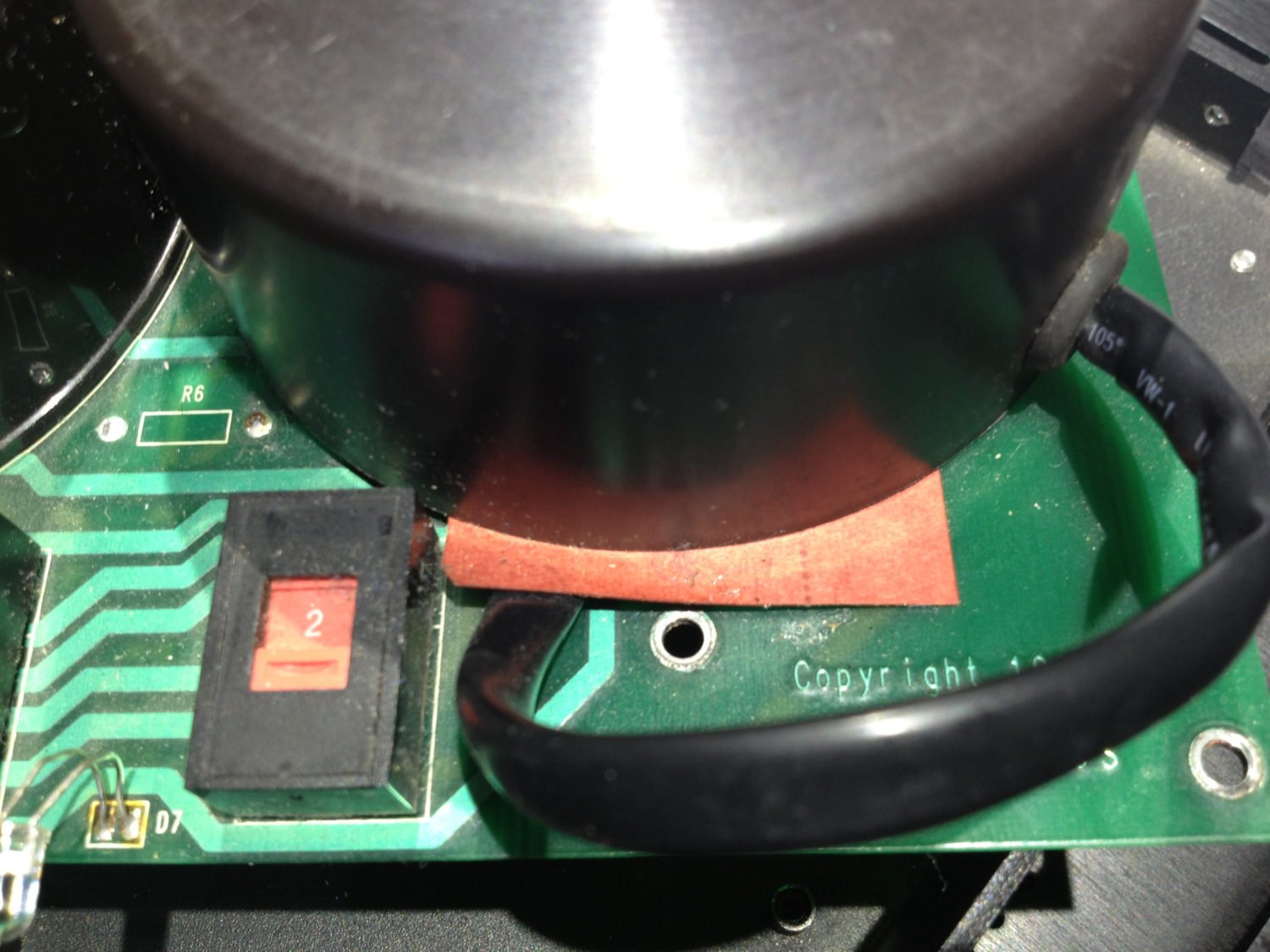
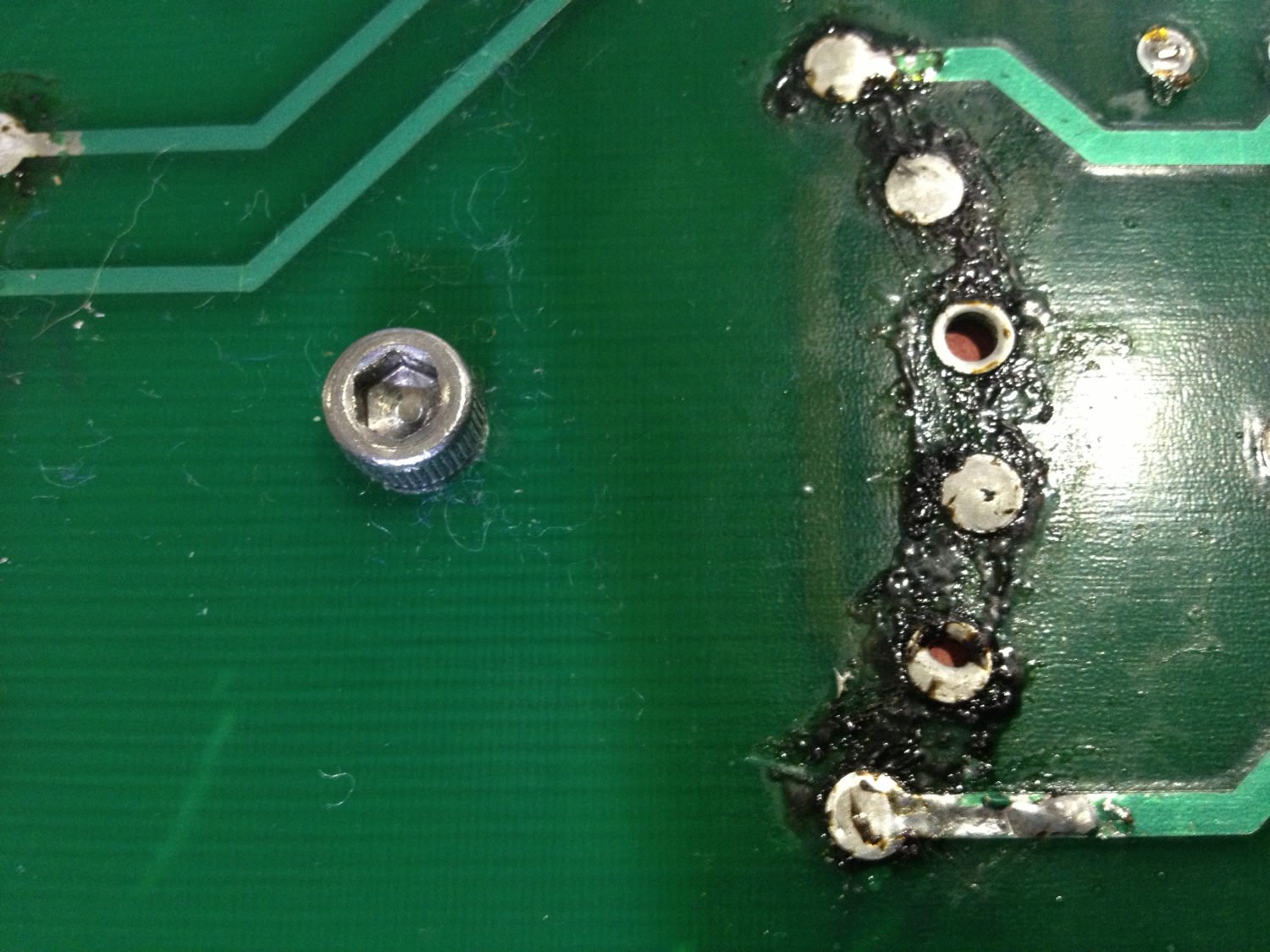
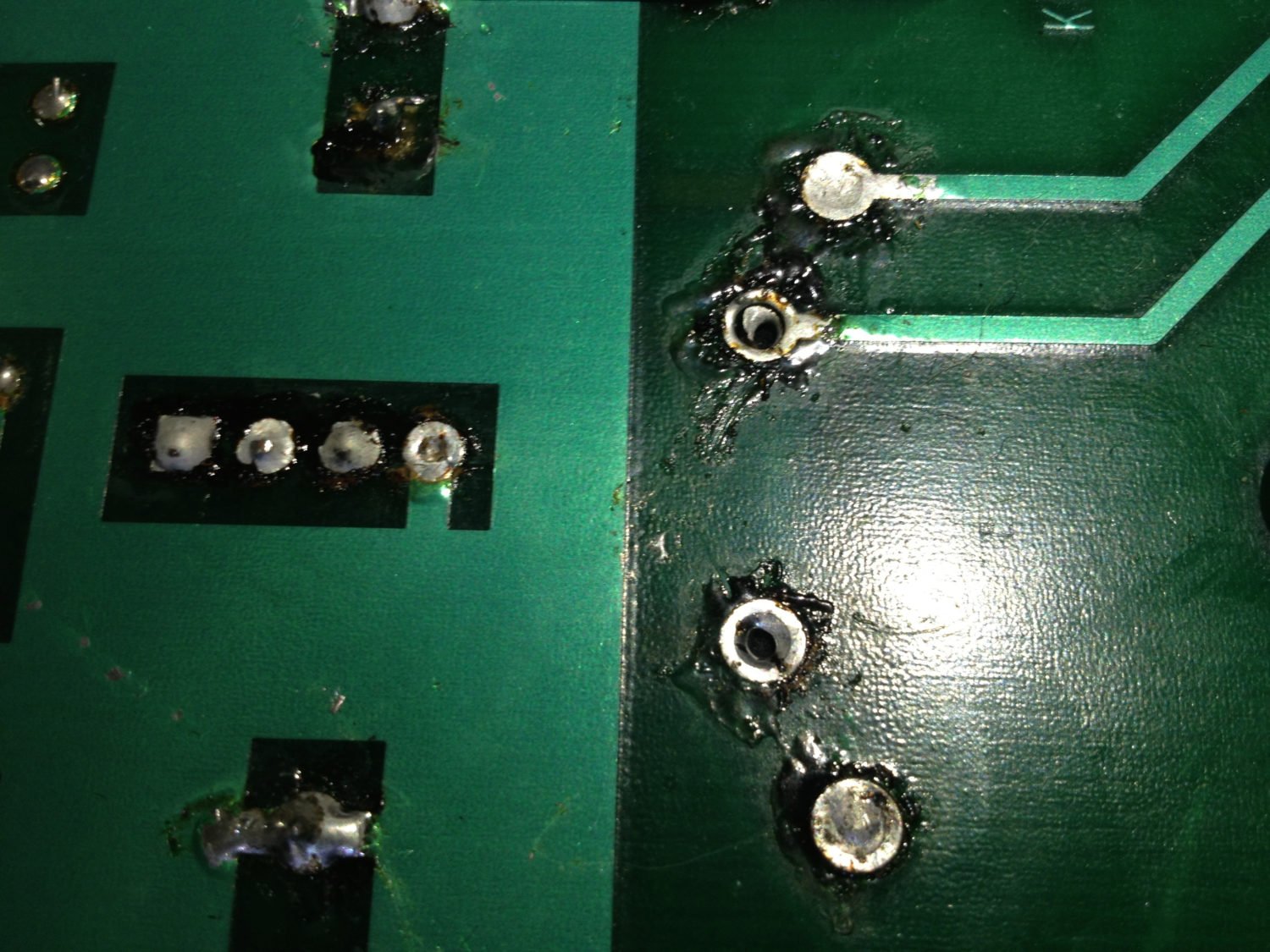
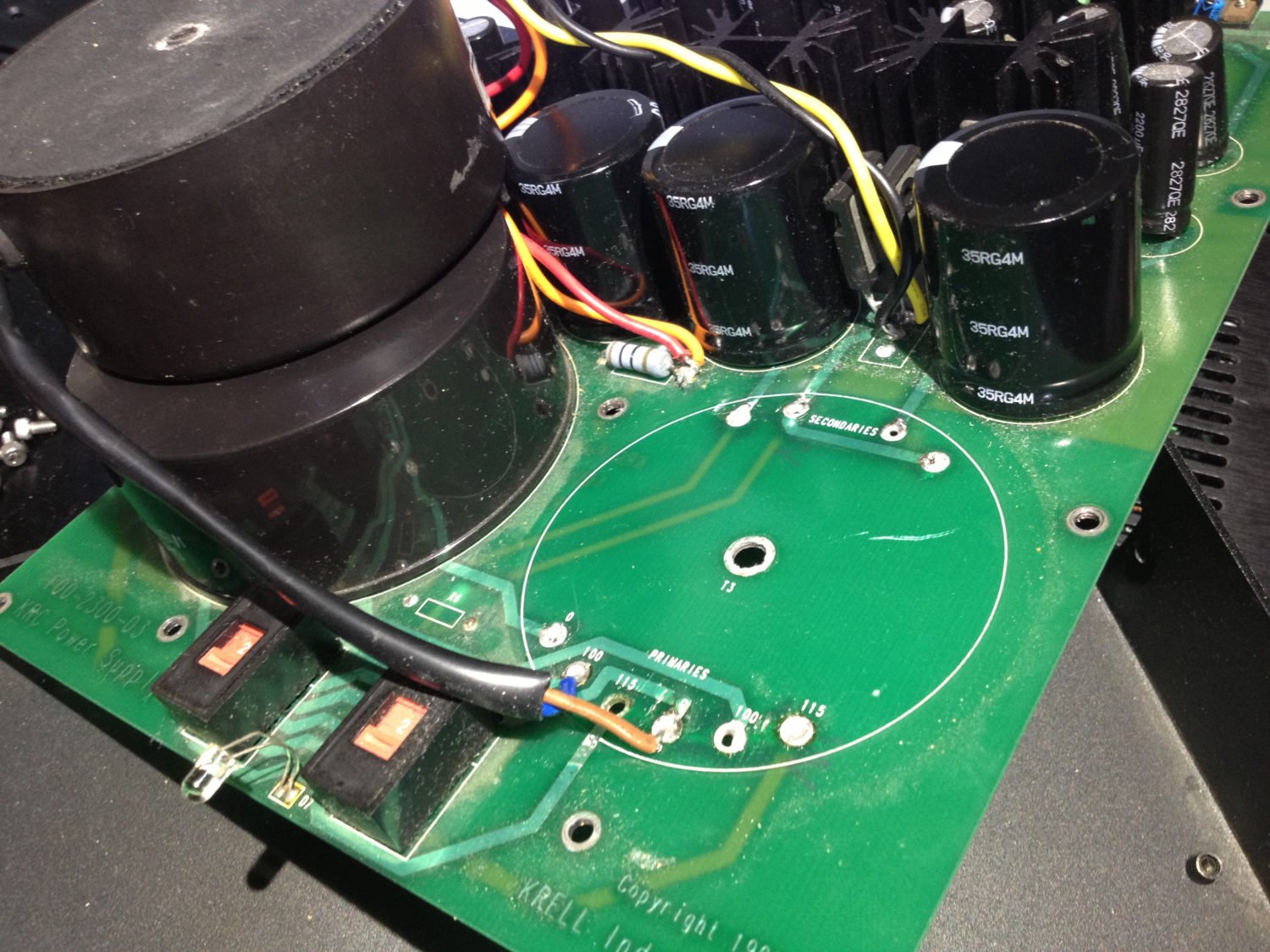
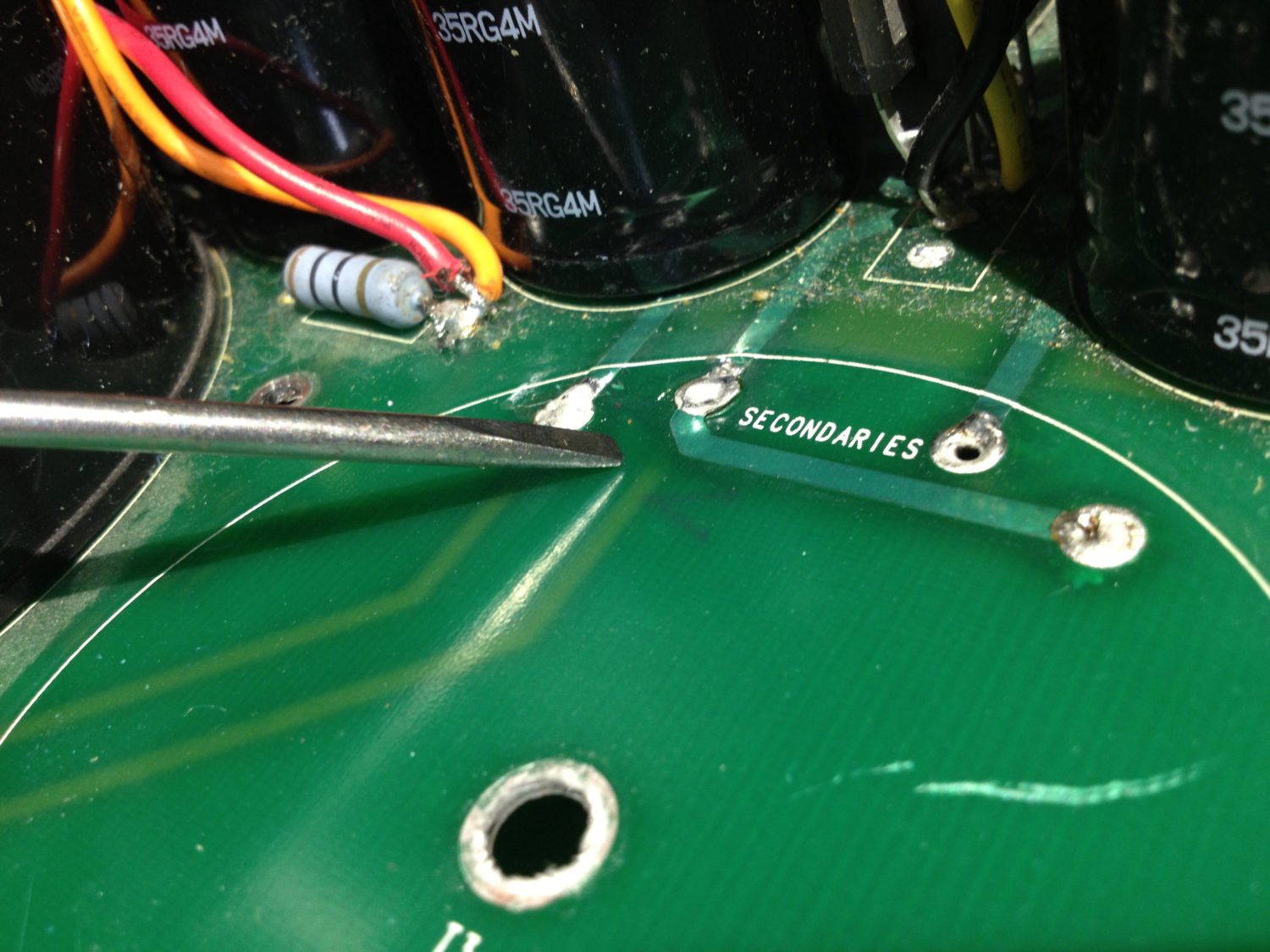
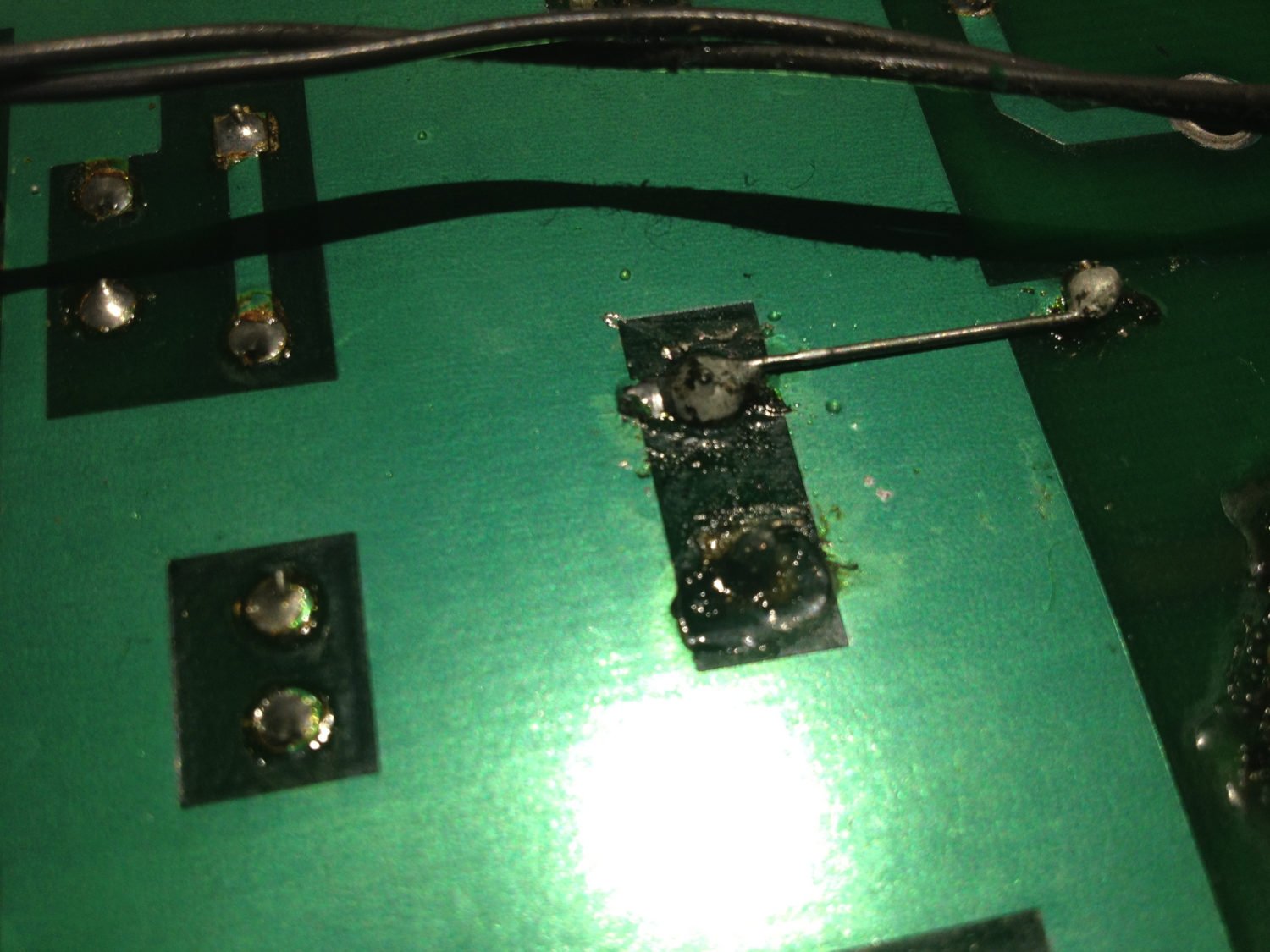
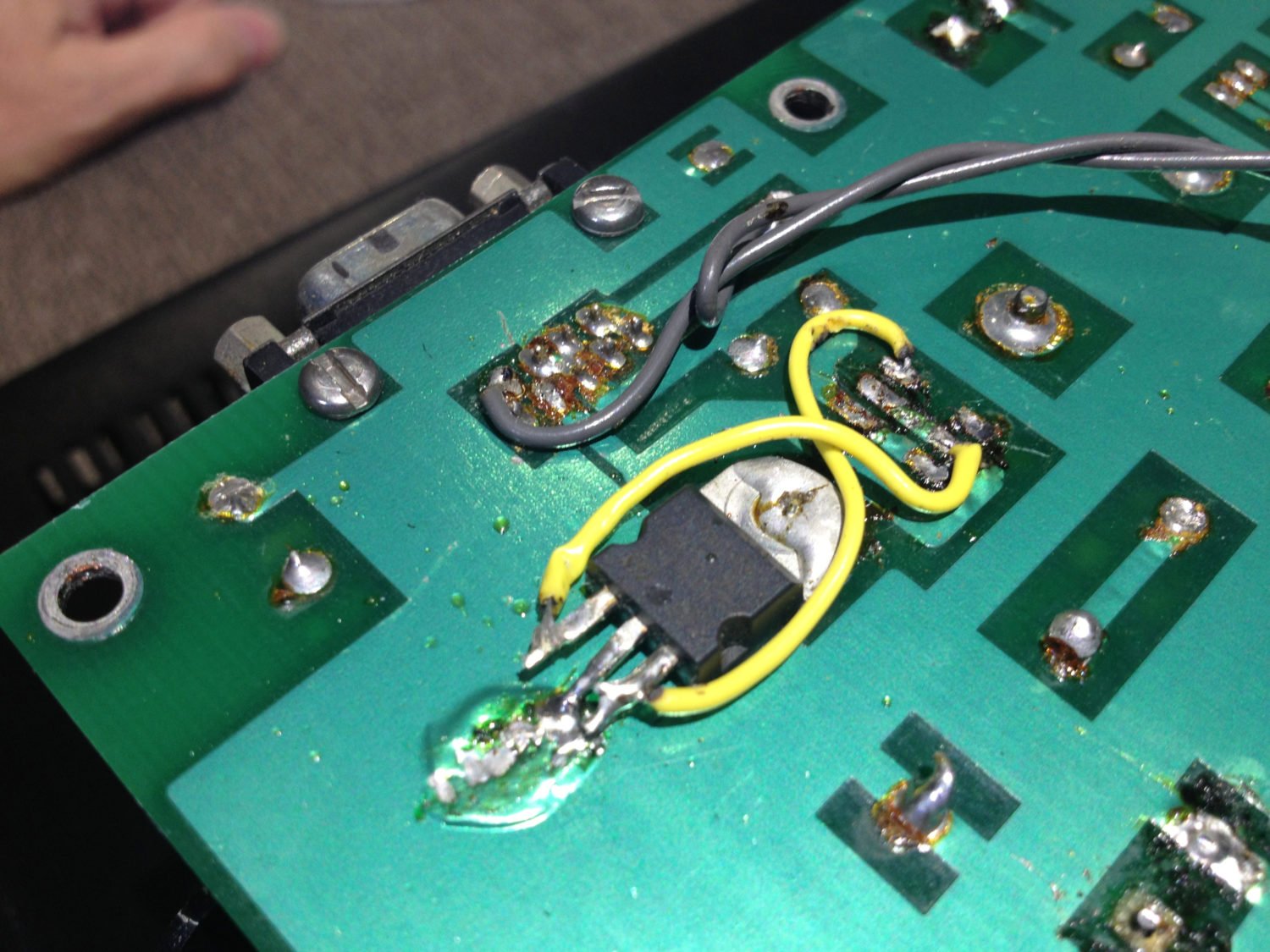
Follow-Up
After the unit was assessed here in Perth, the owner contacted Mr Frampton. Frampton was unapologetic, explaining that he ‘improved’ the volume control. Helpfully, he explained that the attenuator board ‘broke’. He also explained that parts were no longer available from Krell (they were, we checked).
I guess that by saying the volume board ‘broke’, he meant like when you spill petrol on your hot lawnmower and it ignites, ‘breaking’ it. Perhaps it’s like when you drive your car into a wall because you are looking at your phone and ‘break’ the car… Anyway, Frampton offered to fix the preamp (it cannot be fixed). Against the strongest advice, the owner sent it back. We don’t know what ever became of it.
Learnings
The moral of this story is to NEVER take hi-fi equipment to this repairer. He now conveniently claims he doesn’t work on Krell and one can only say THANK GOODNESS!
Case 3 – Harman/Kardon PM-655 Integrated Amplifier
This case of bad repairs came to me in February 2018. My customer bought this new from Vince Ross Audio, back in the day. It worked well for years until it developed a fault.
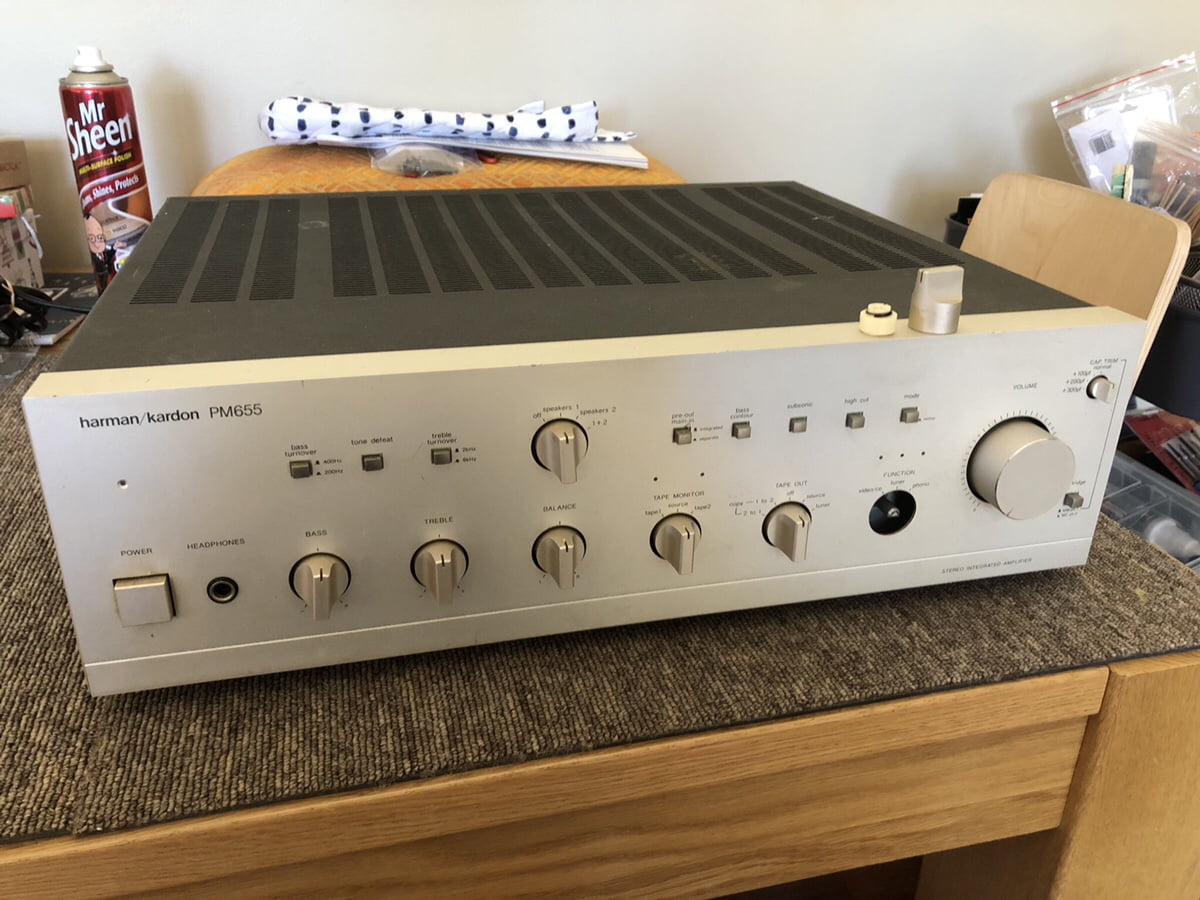
Vince used a repairer called Klaus, you may know of him. He worked on a lot of gear, sometimes successfully, other times not. This case falls into the not category. I should point out that Vince is a lovely guy and used this repairer in good faith. This repairer likely did good work at some point, I don’t know how it came to this.
Anyway, this repairer destroyed several boards in his attempt to repair a volume control. He used the lowest quality Jaycar volume pot and ribbon cable and destroyed traces associated with the front panel controls, many of which no longer work. I found horrible flux residue everywhere due to the lowest-quality solder and failure to clean up. Needless to say, the volume control never worked properly after this.
It does now, I had a look and did my best to rectify this appalling mess and make the amp reliable for my customer. I serviced the unit and fixed the volume problem. Needless to say, the owner was horrified to see these images. He confirmed for me that it had only ever been to Klaus.
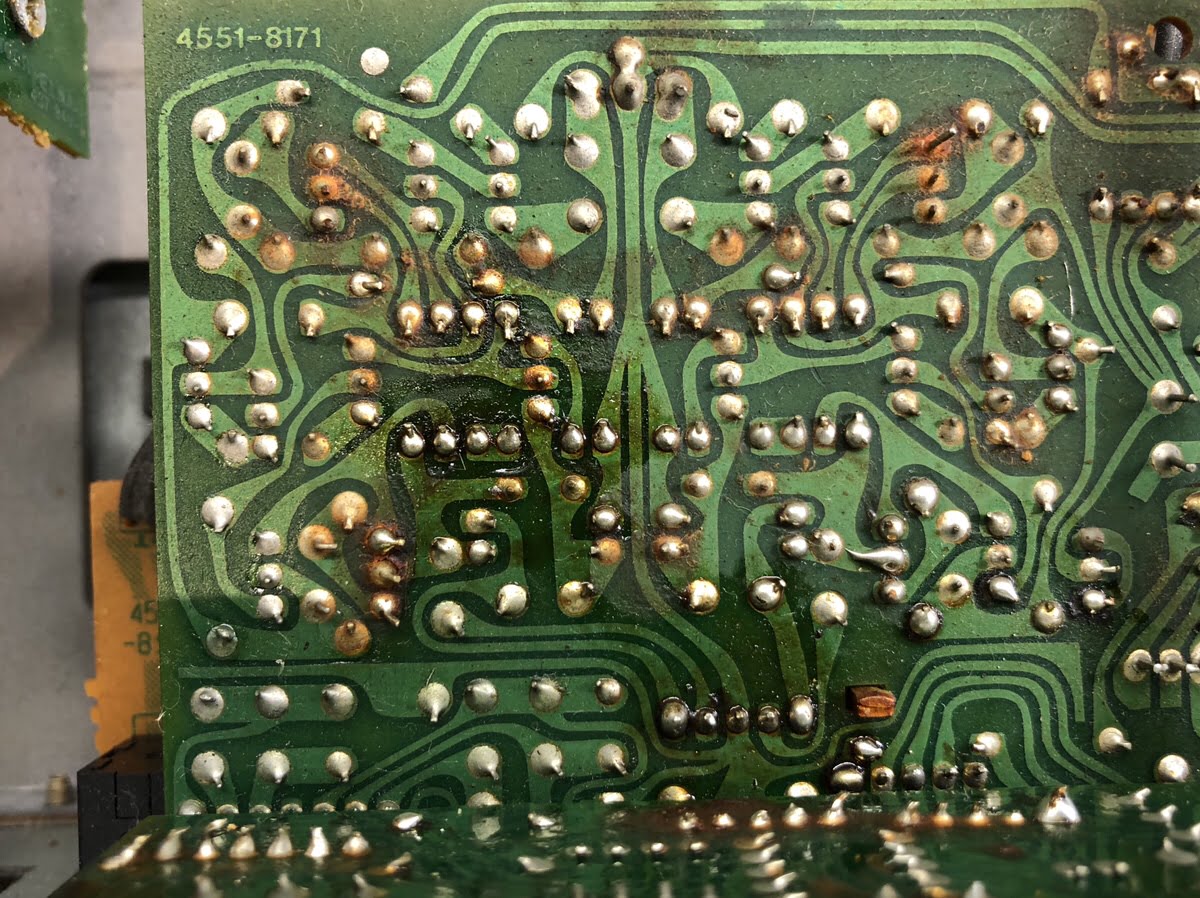
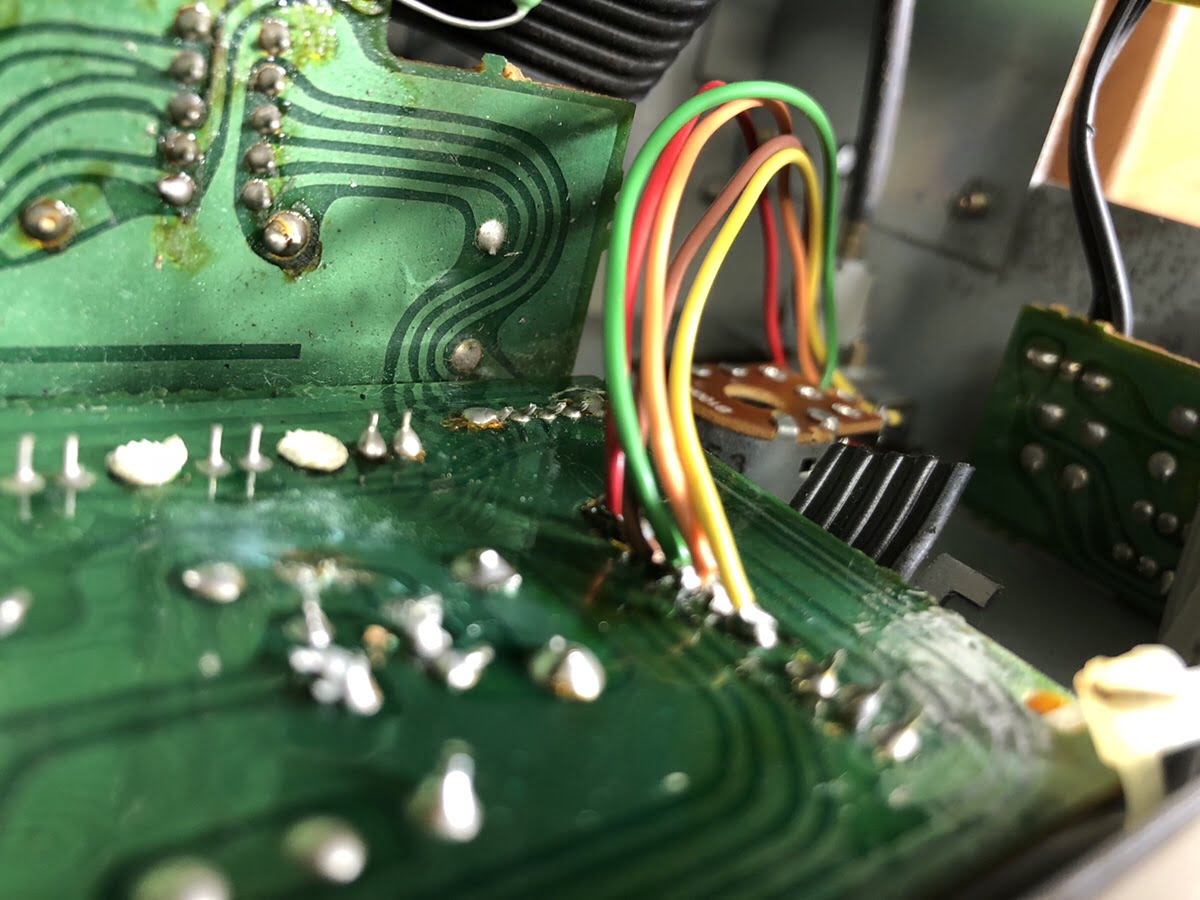
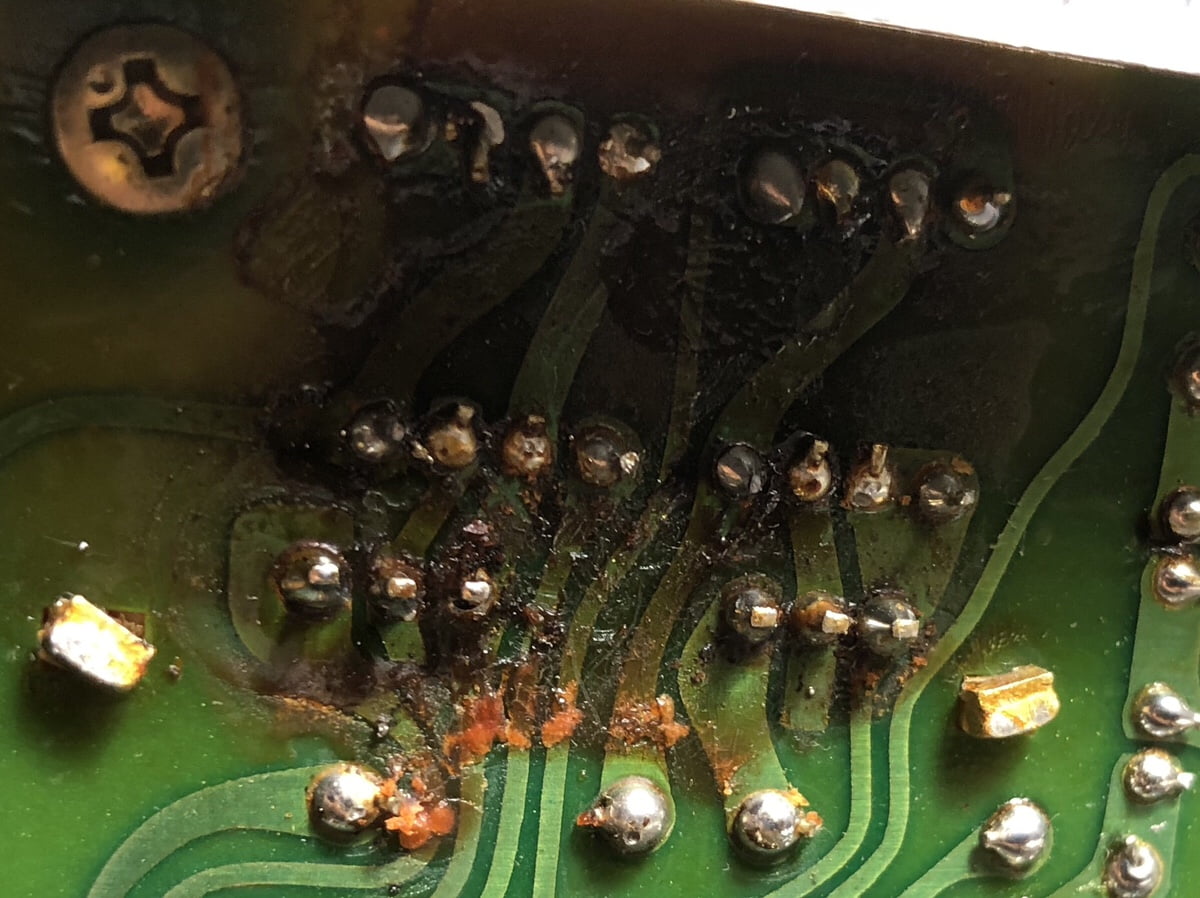
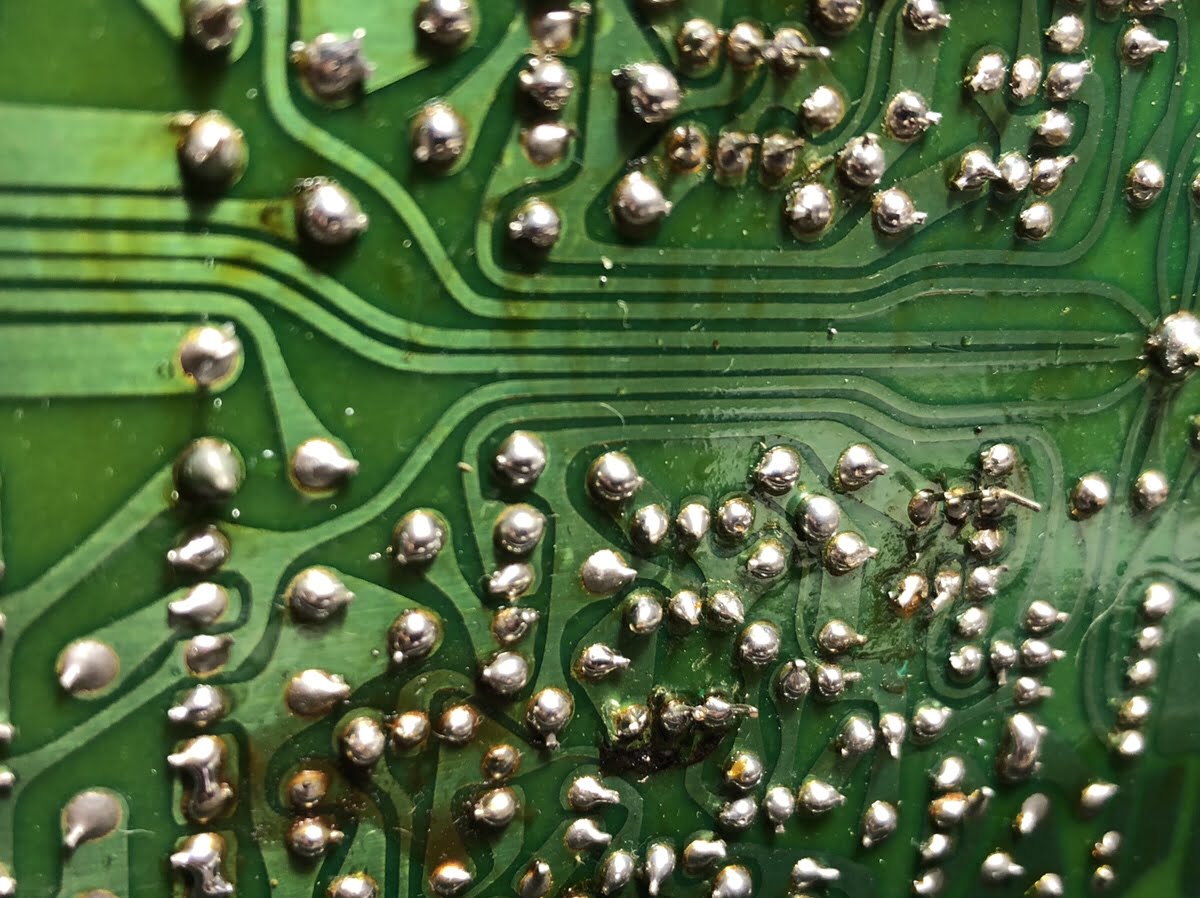
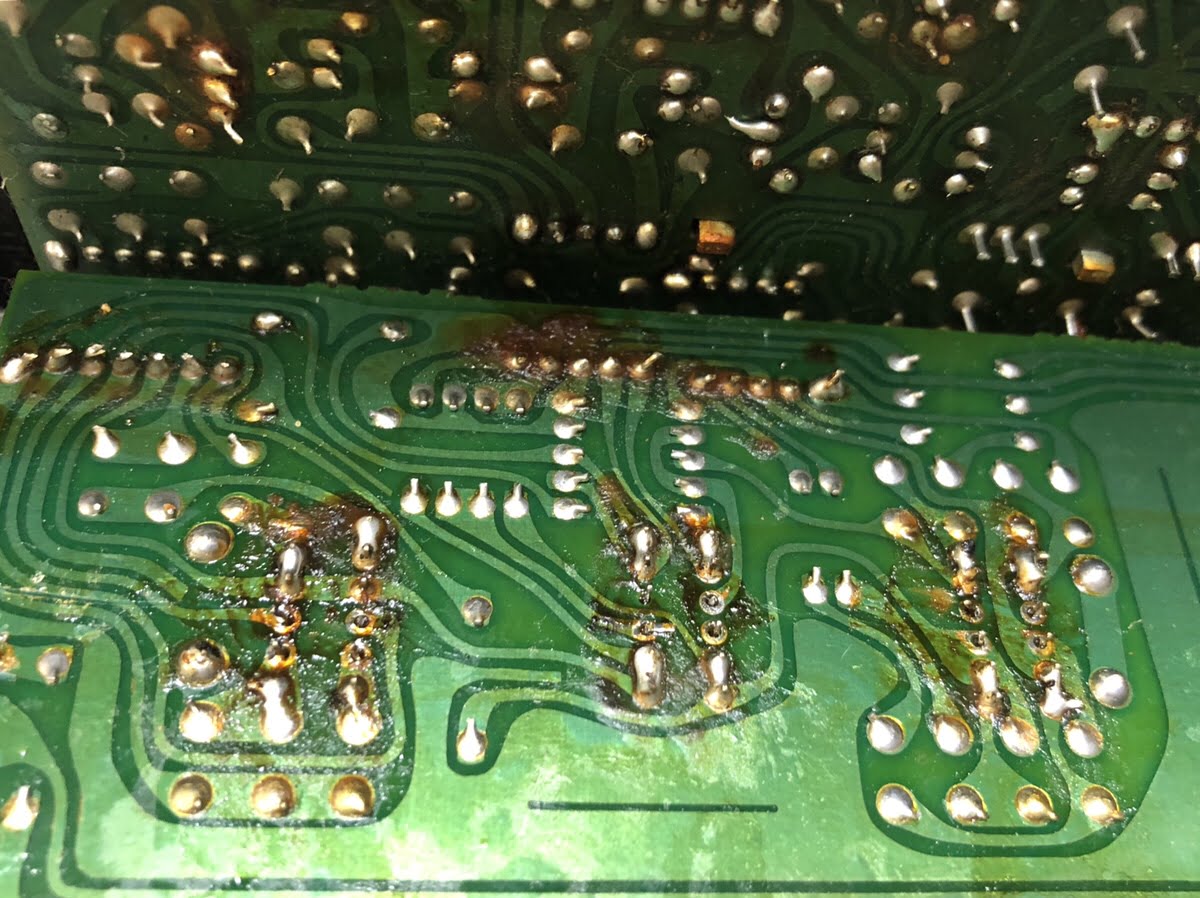
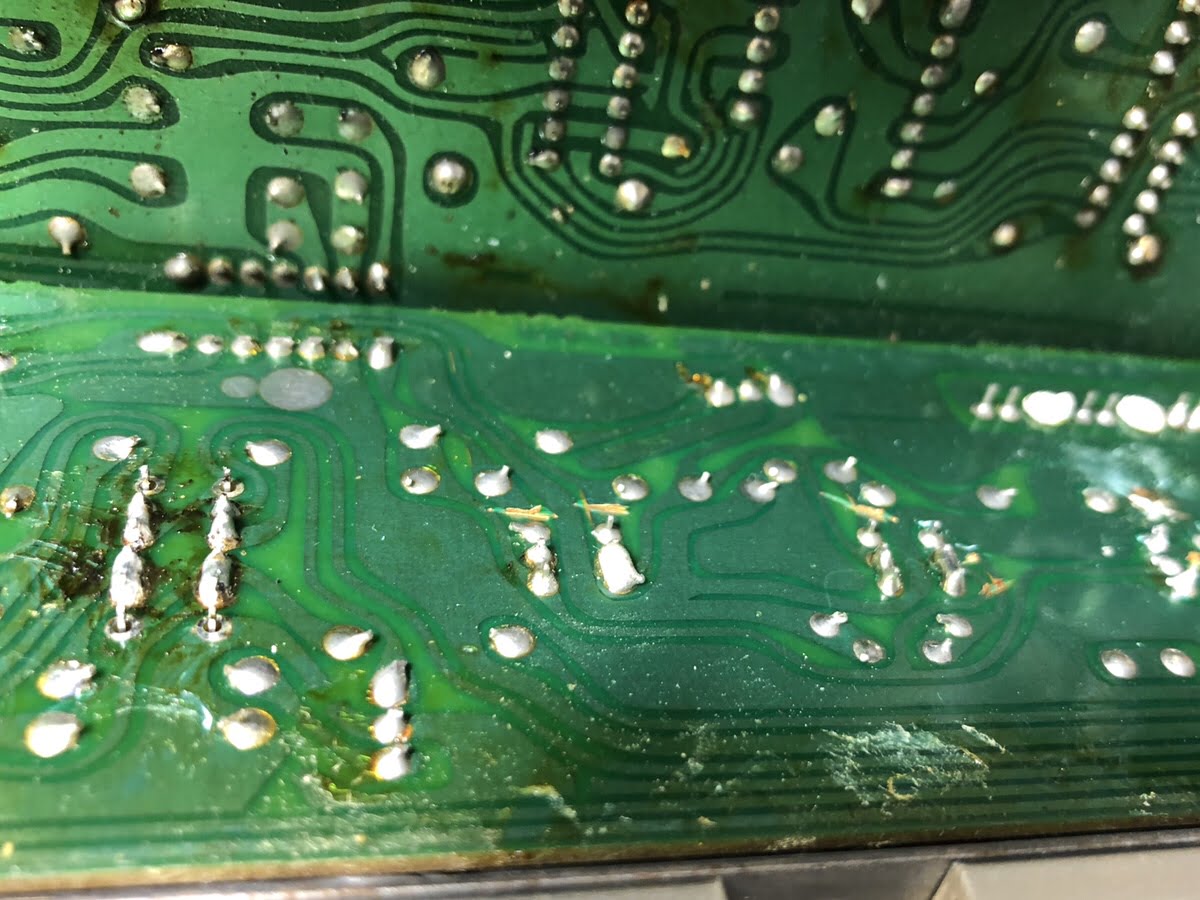
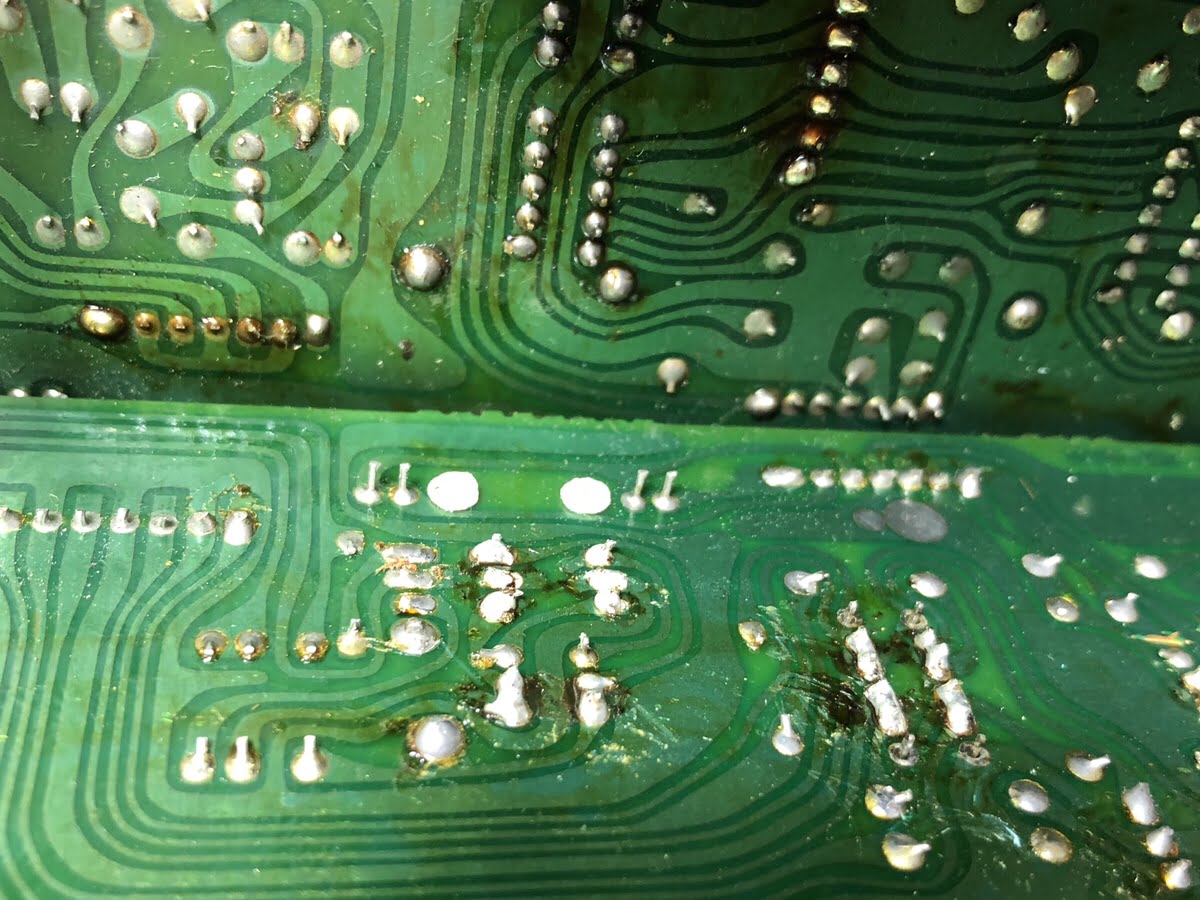
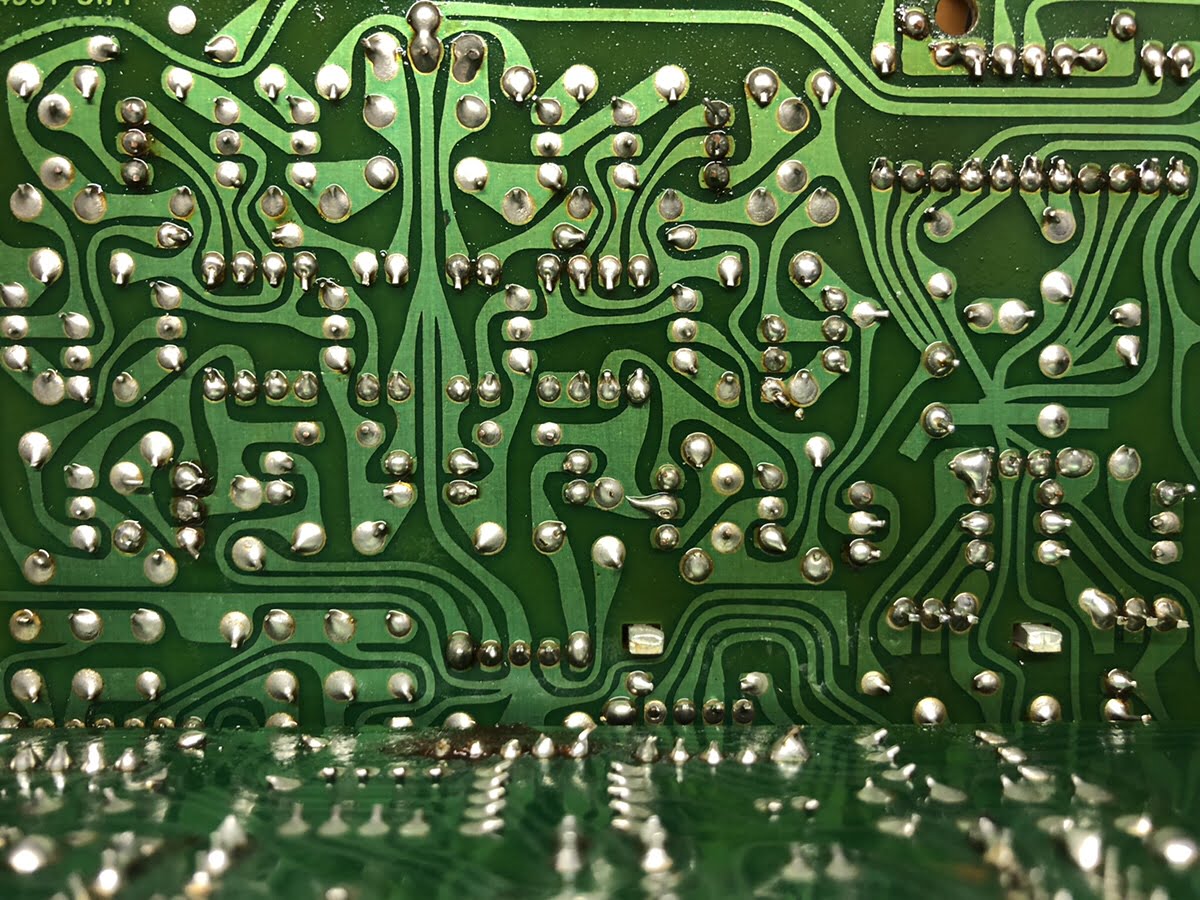
Case 2 – Perreaux PMF 3150 Power Amplifier
This addition to the Hall of Shame is another case from my friend Jason (Speaker Doctor and Turntable Doctor). This amplifier came to Jason for repair. The owner bought it for $900, from a guy who ‘upgraded’ it. You be the judge on whether these are upgrades…
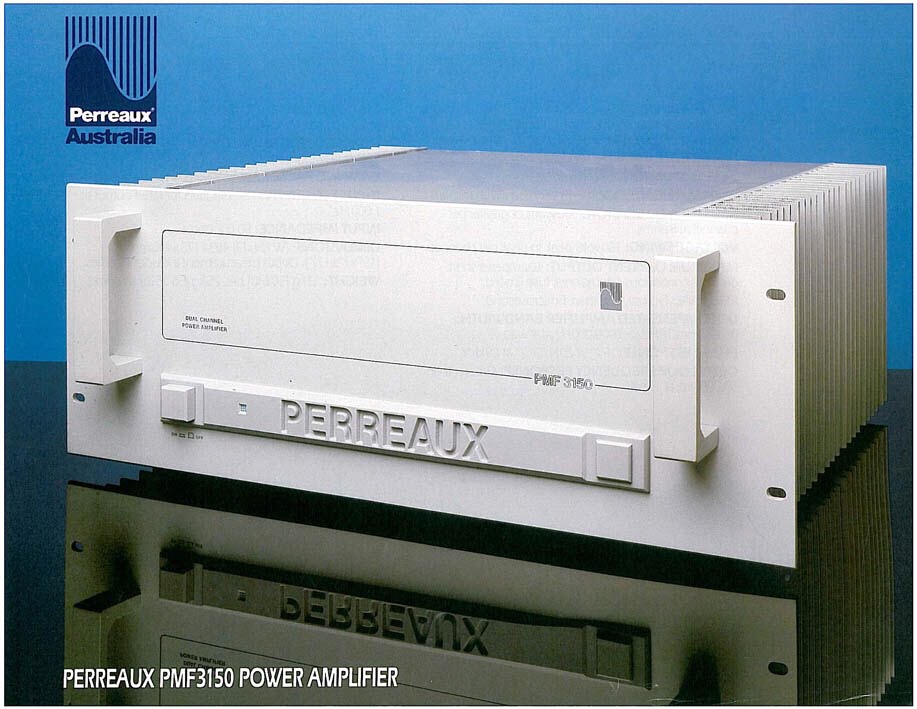
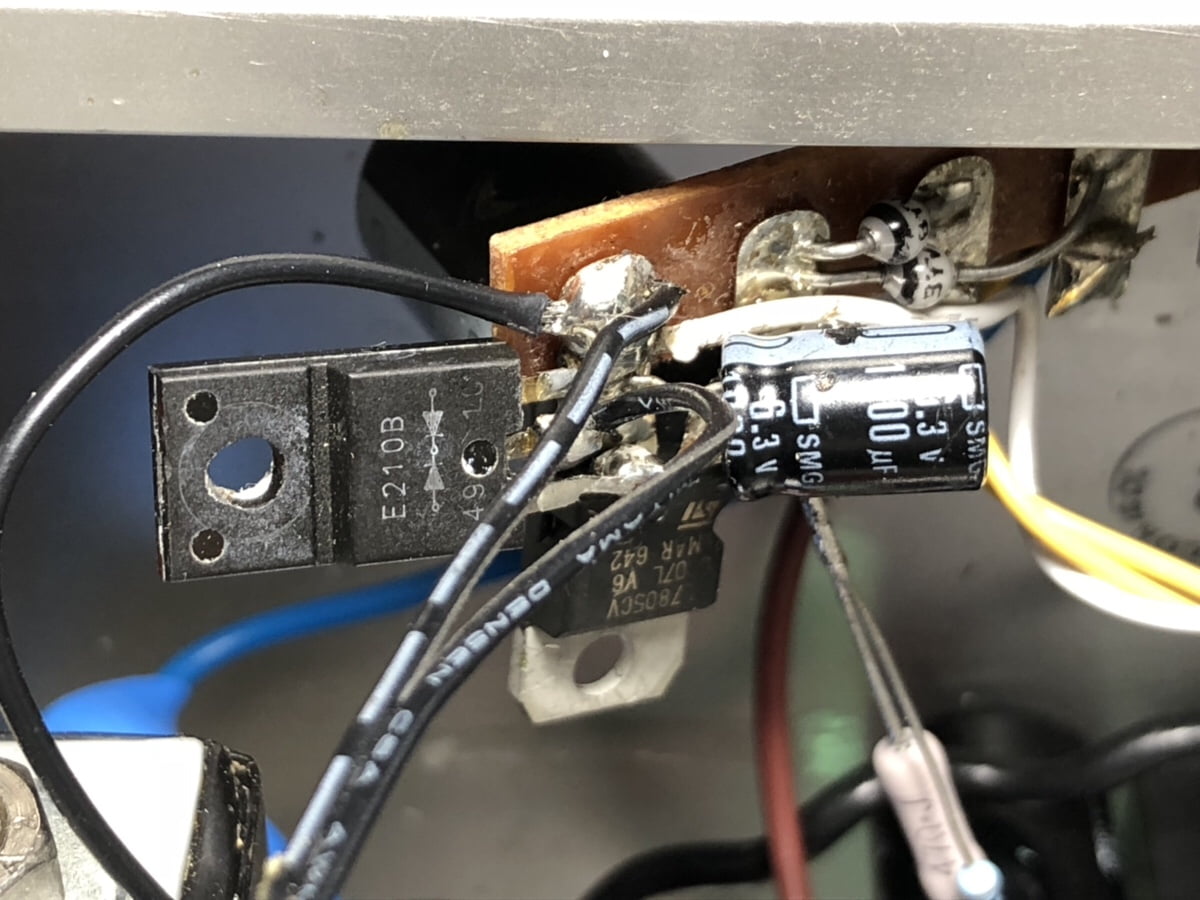
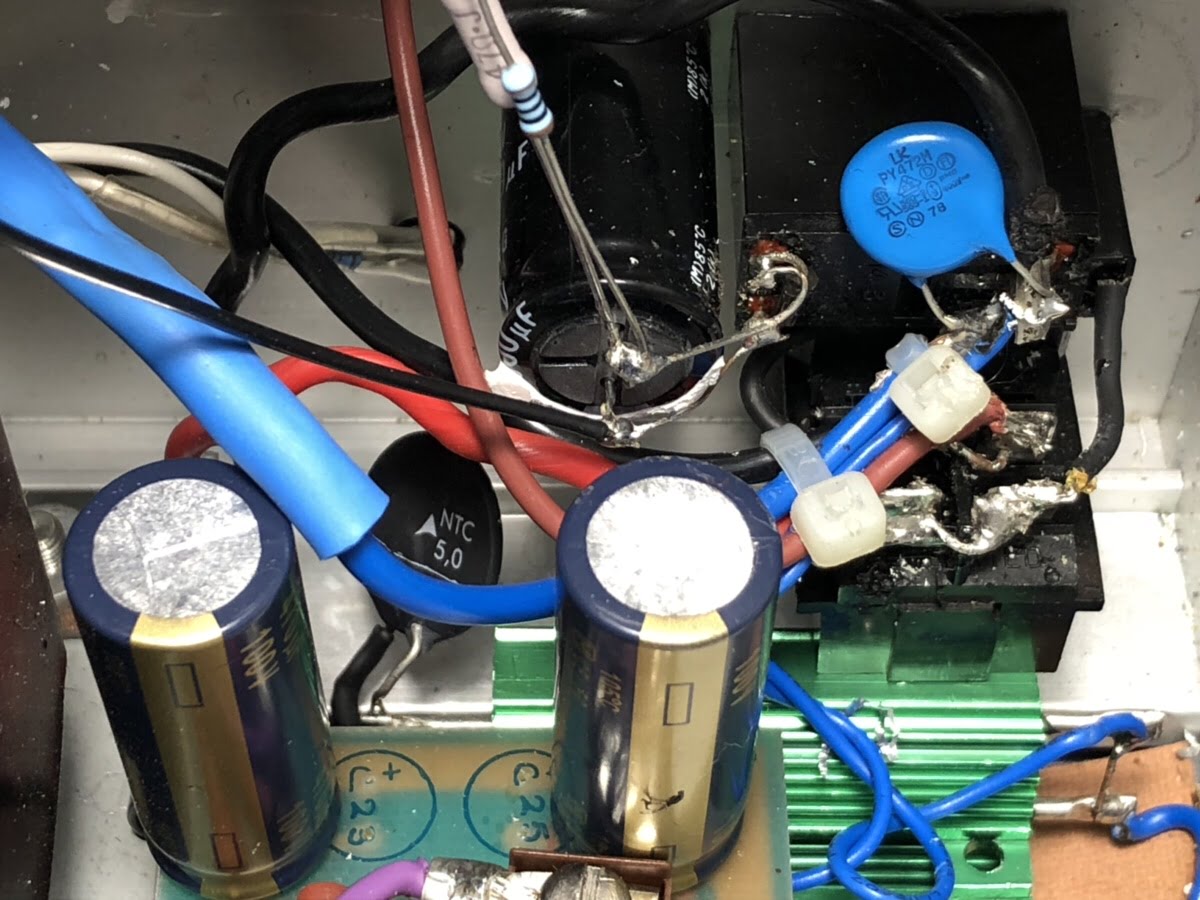
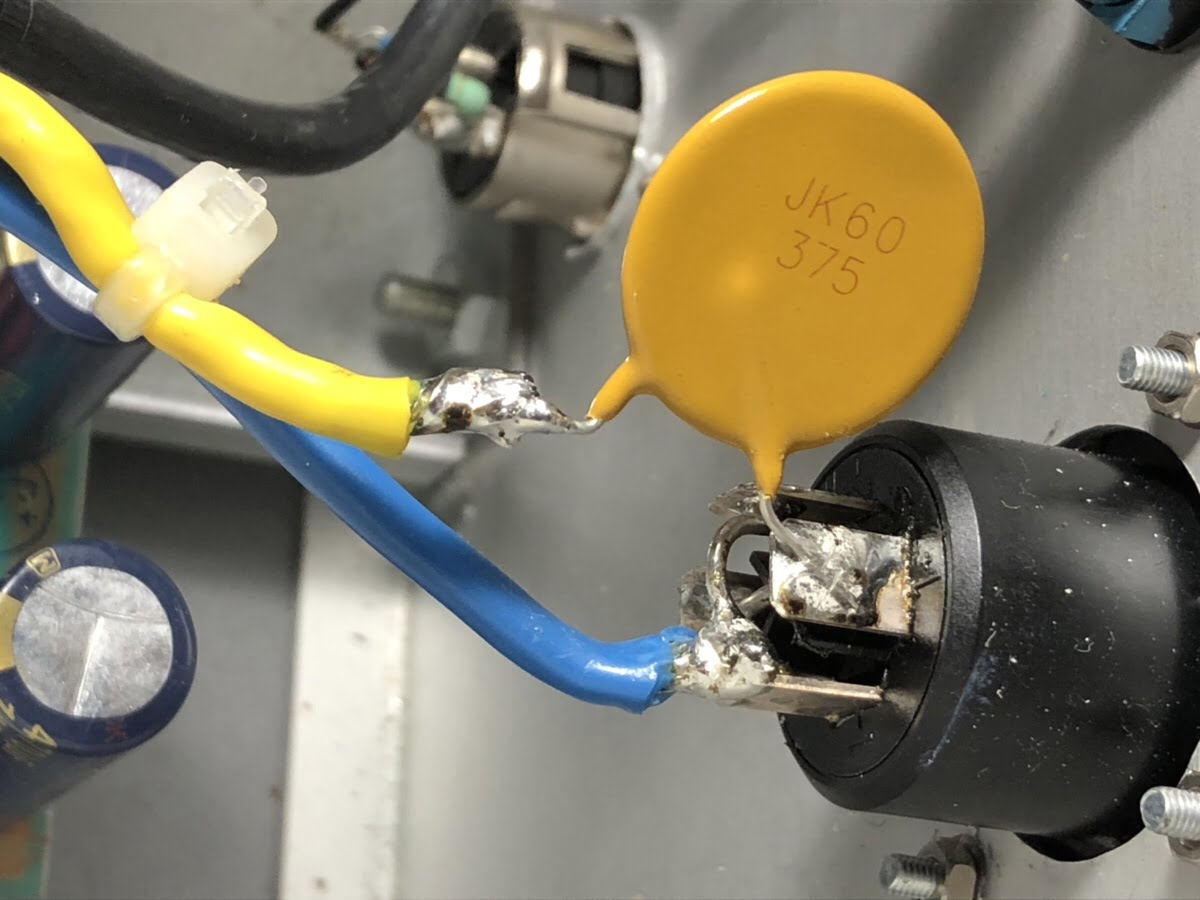
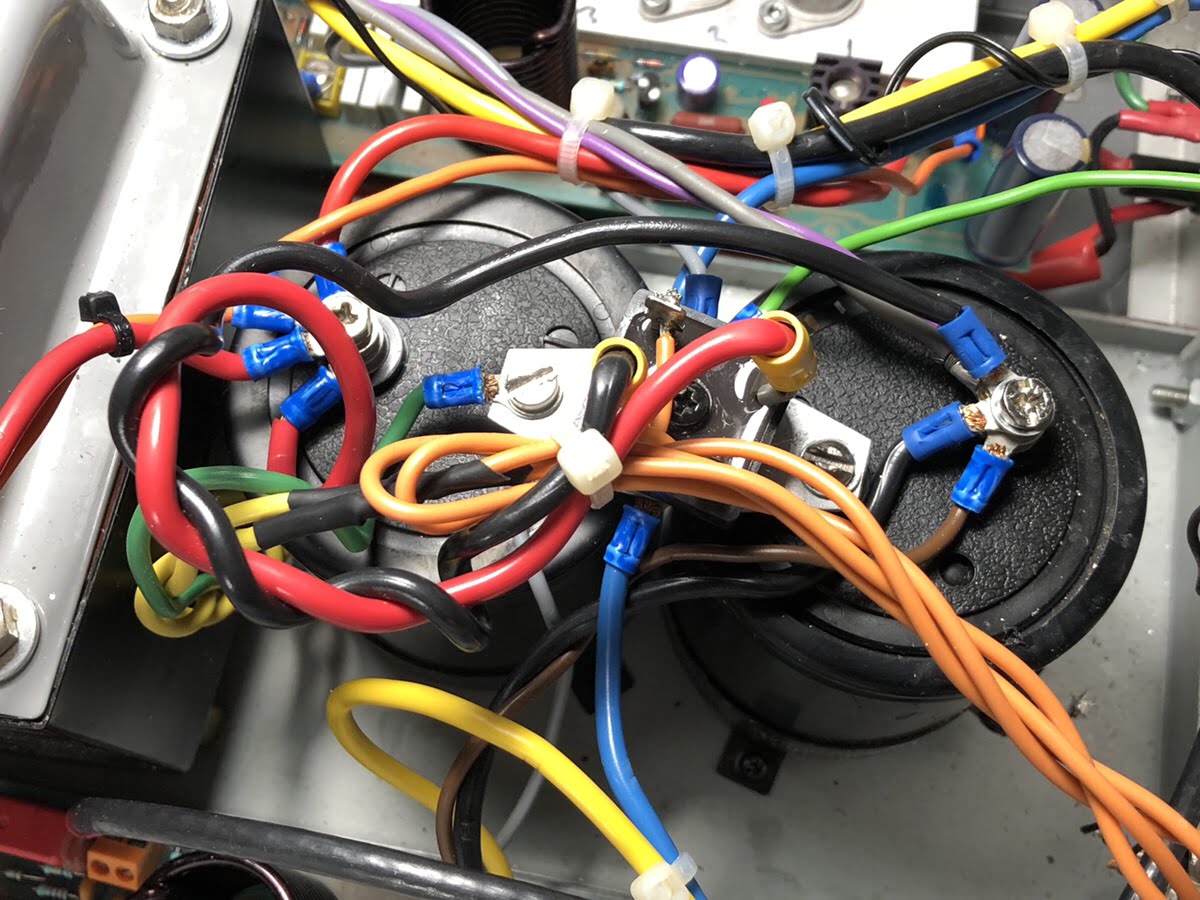
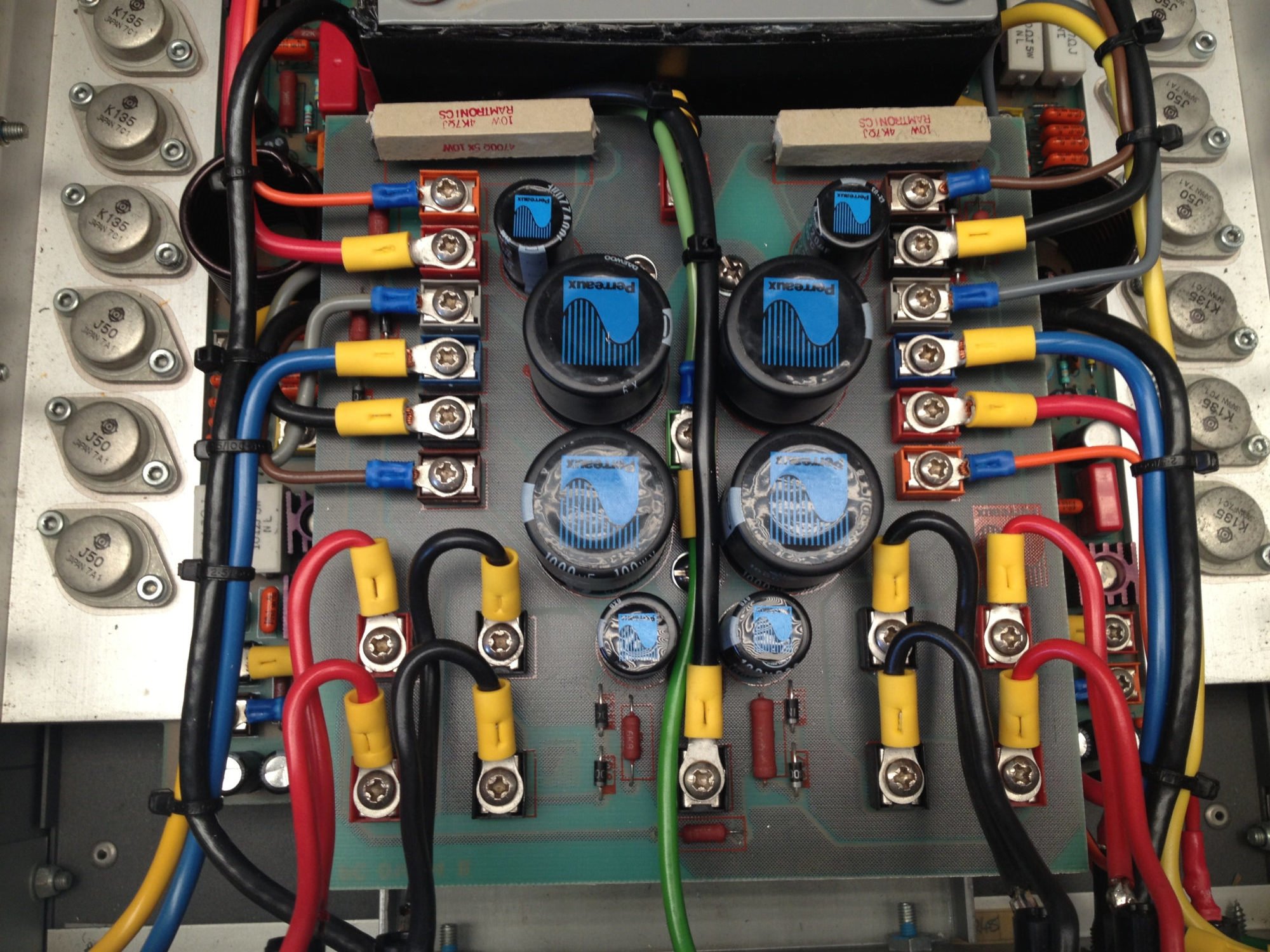
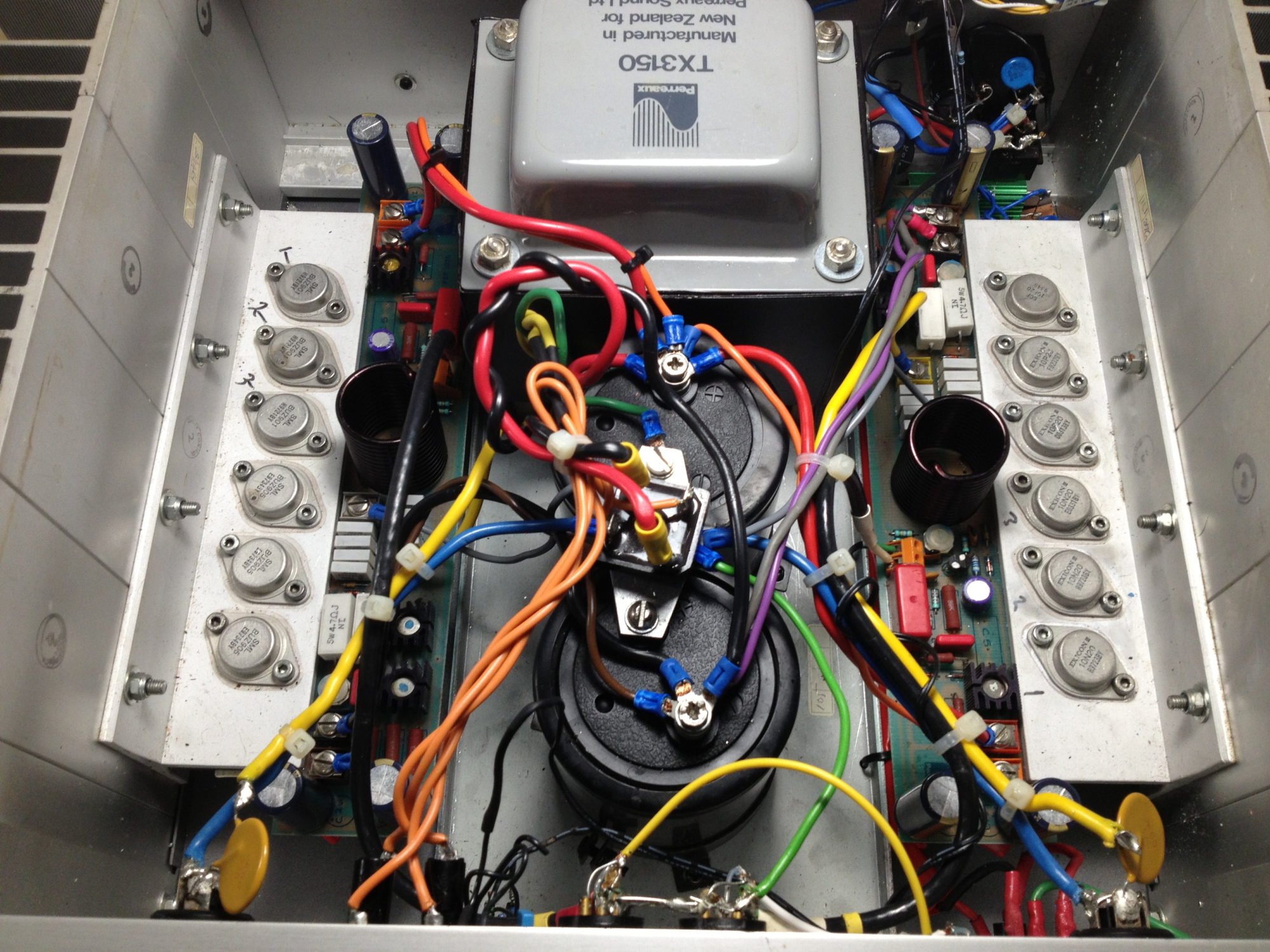
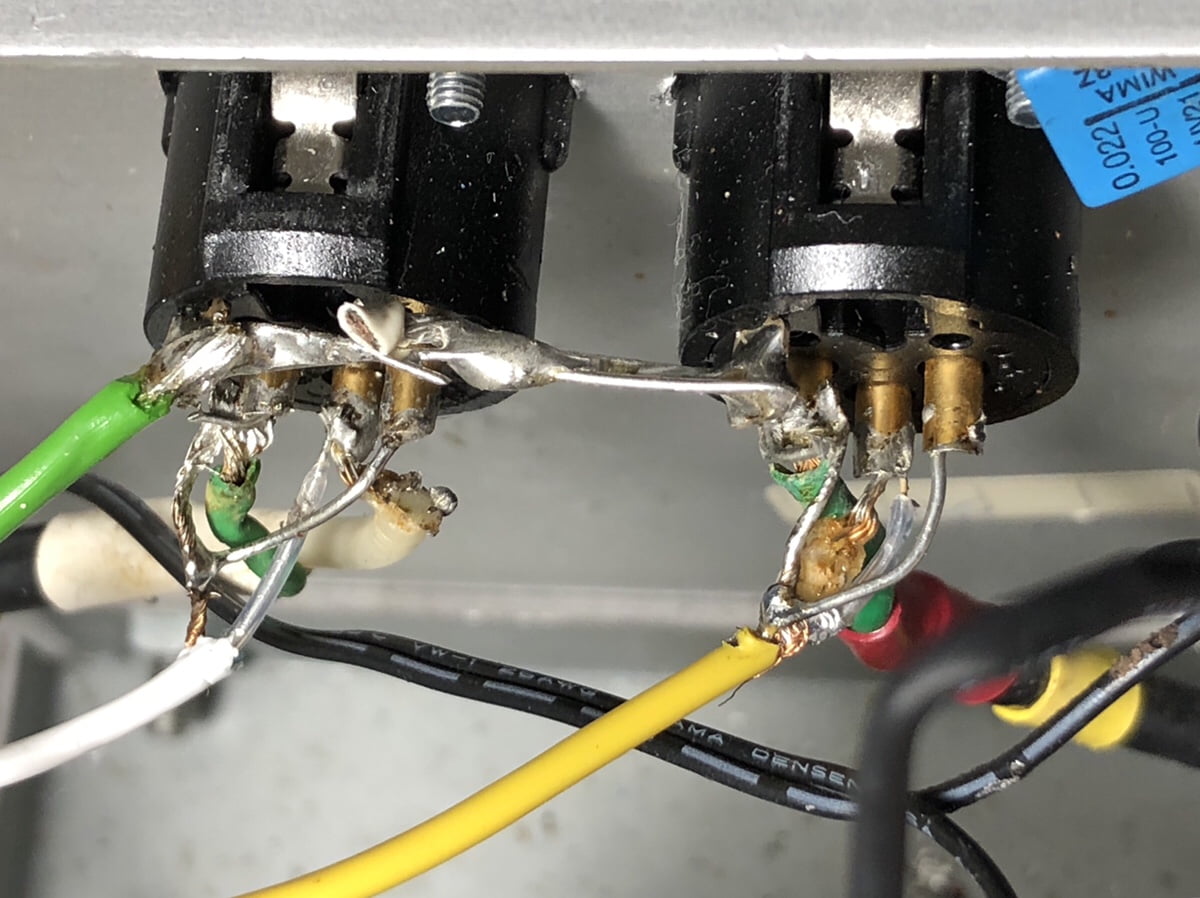
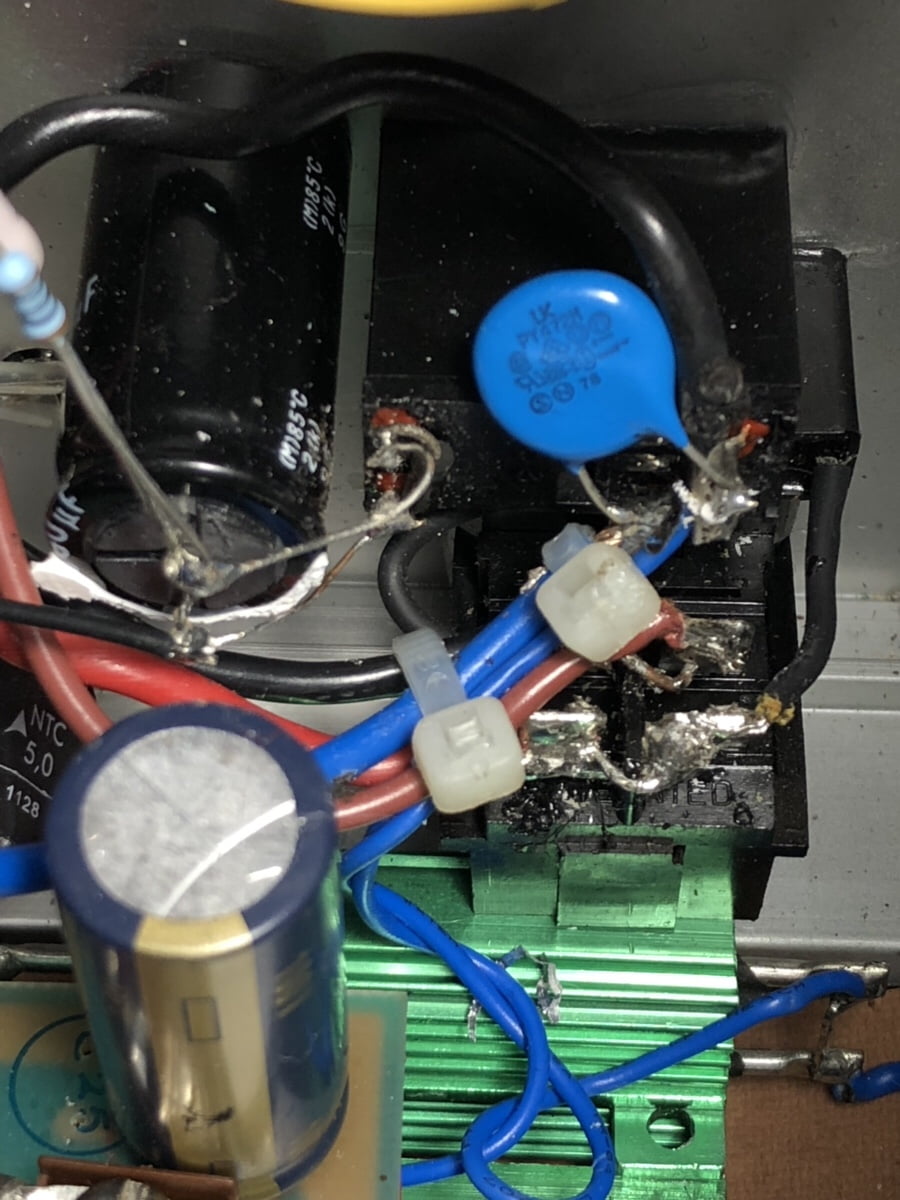
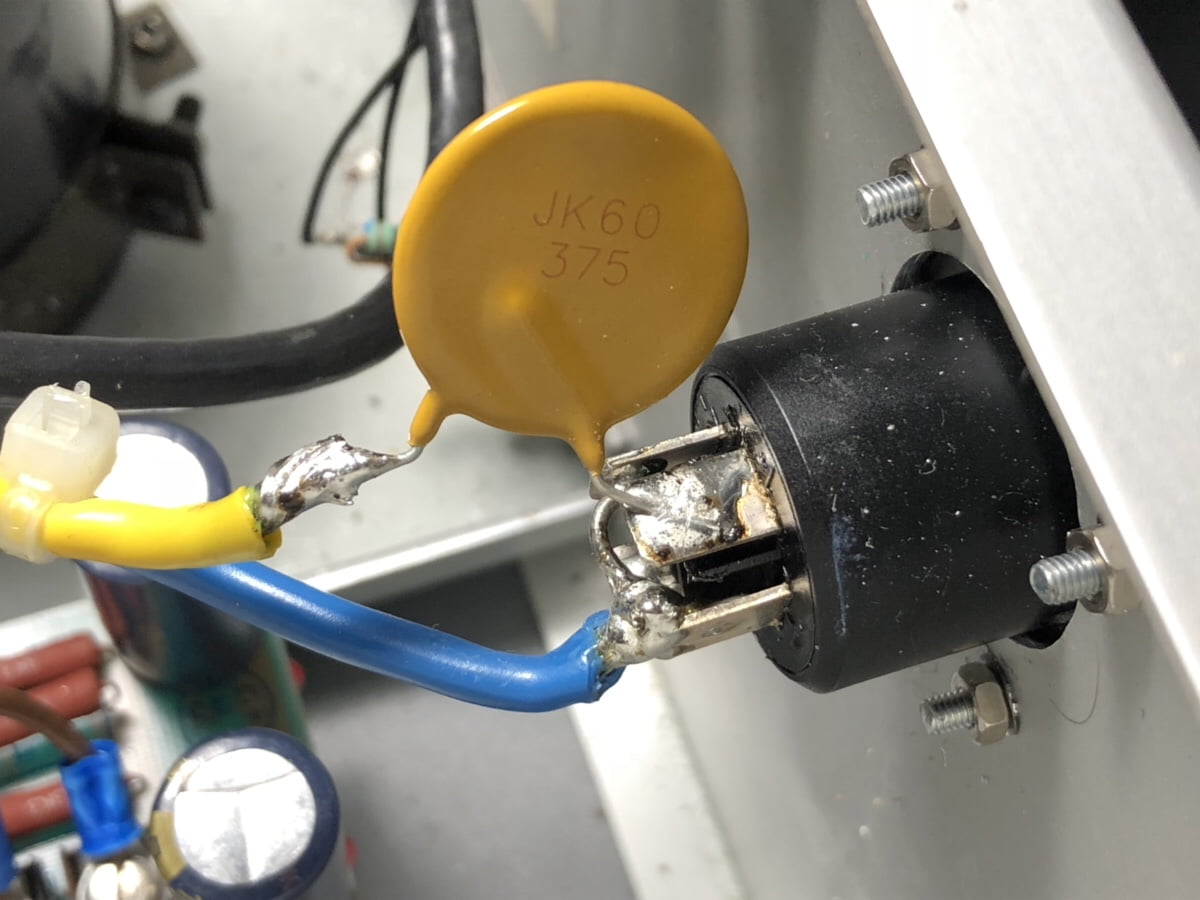
Case 1 – Kenwood KA-5700 Integrated Amplifier
This lovely little amplifier came to me via a very nice customer. She’d taken this otherwise good amp to a local repairer called Mr RFW. You can see from the images below that the repairer has ‘upgraded’ this circuit board to include a special short circuit that prevented the amp from working properly.
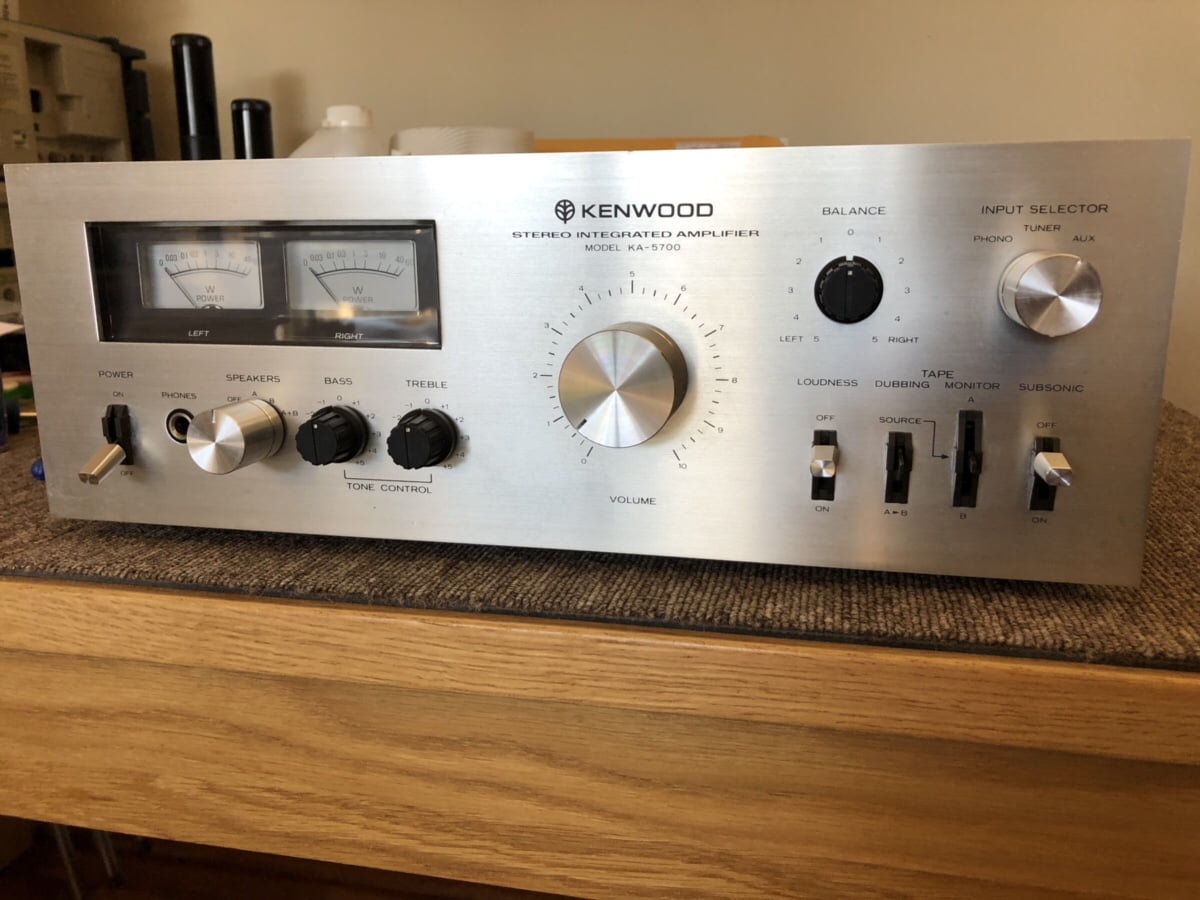
My customer took the amplifier back to Mr RFW. He had the audacity to say that the unit is too old and damaged to be repaired! But he did the damage!!
Thankfully, this lovely customer brought the unit to me and I’ve repaired it. The KA-5700 is now working perfectly, though a little worse for wear after its near-death experience at the hands of Mr Radio Waves.
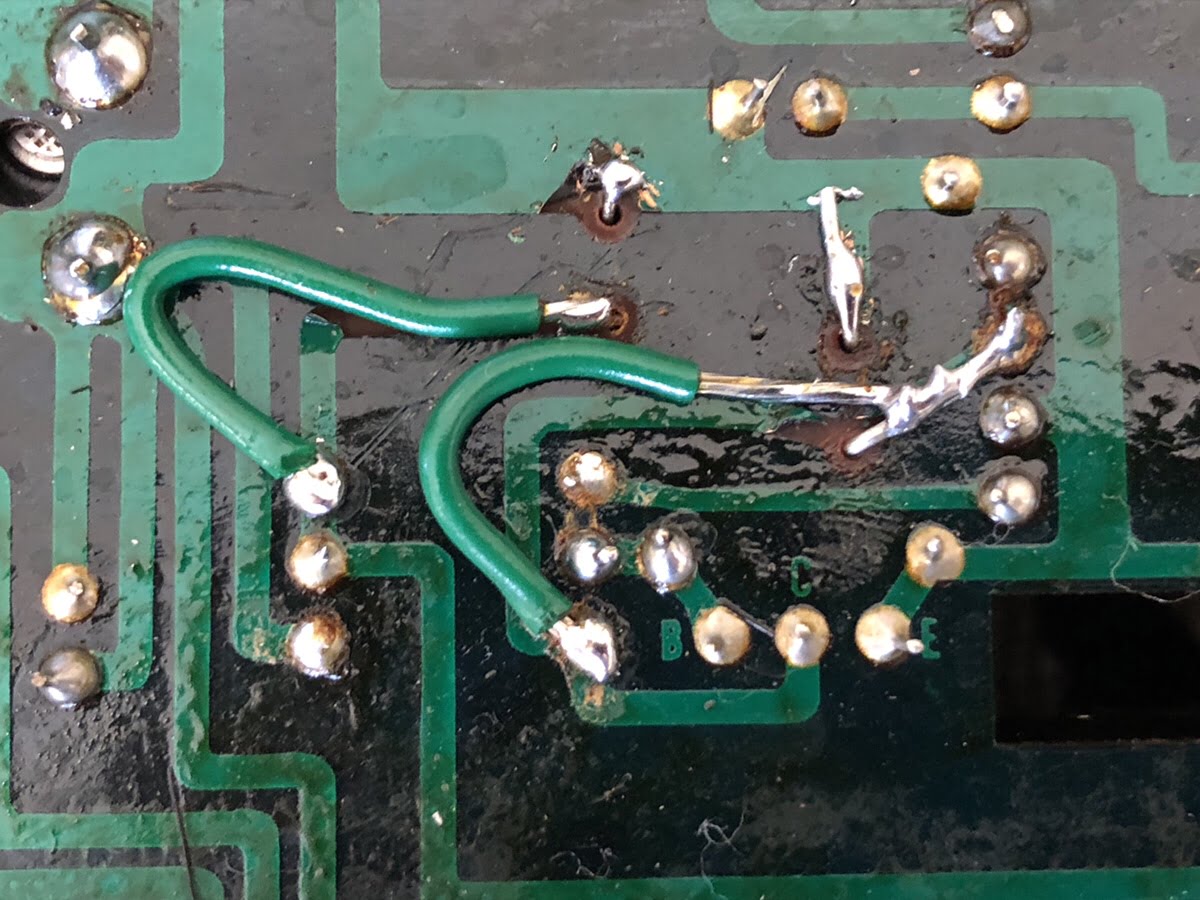
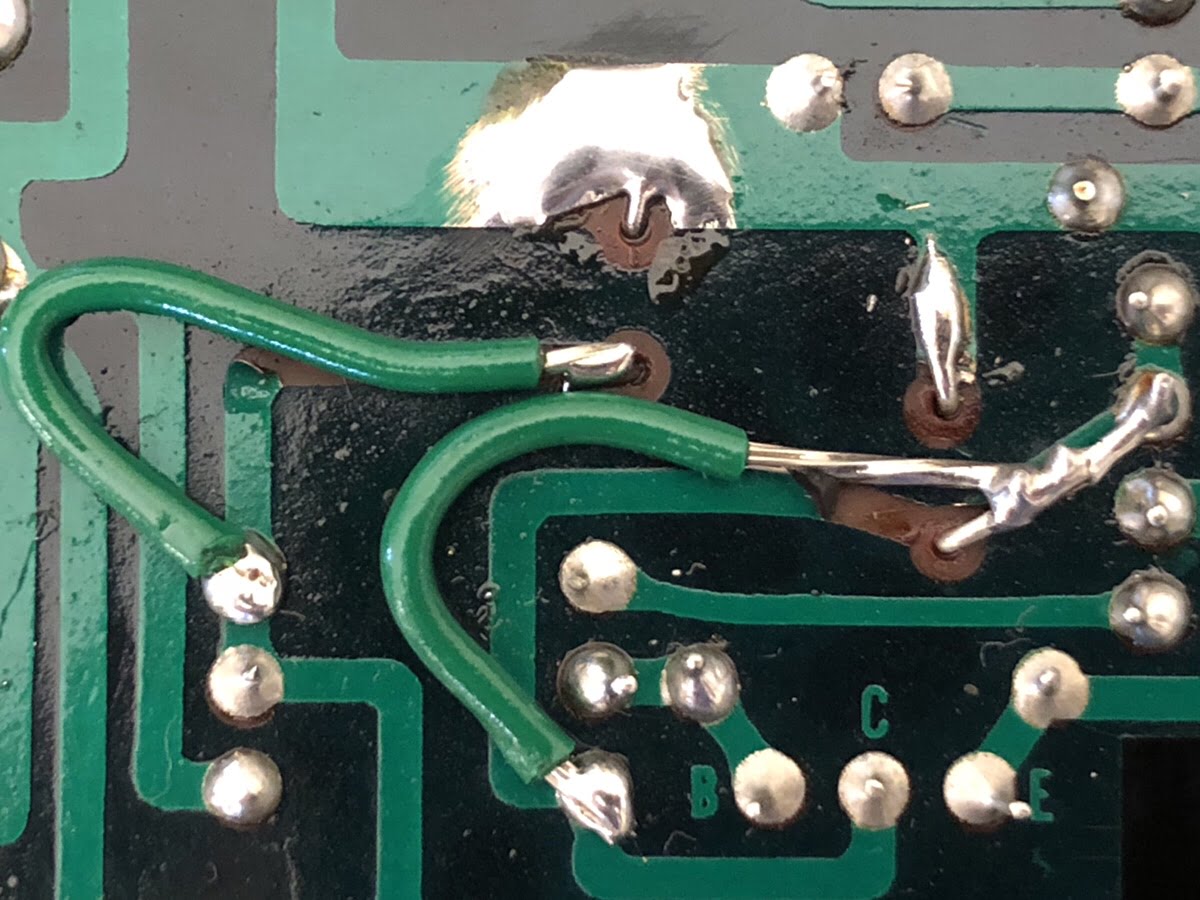
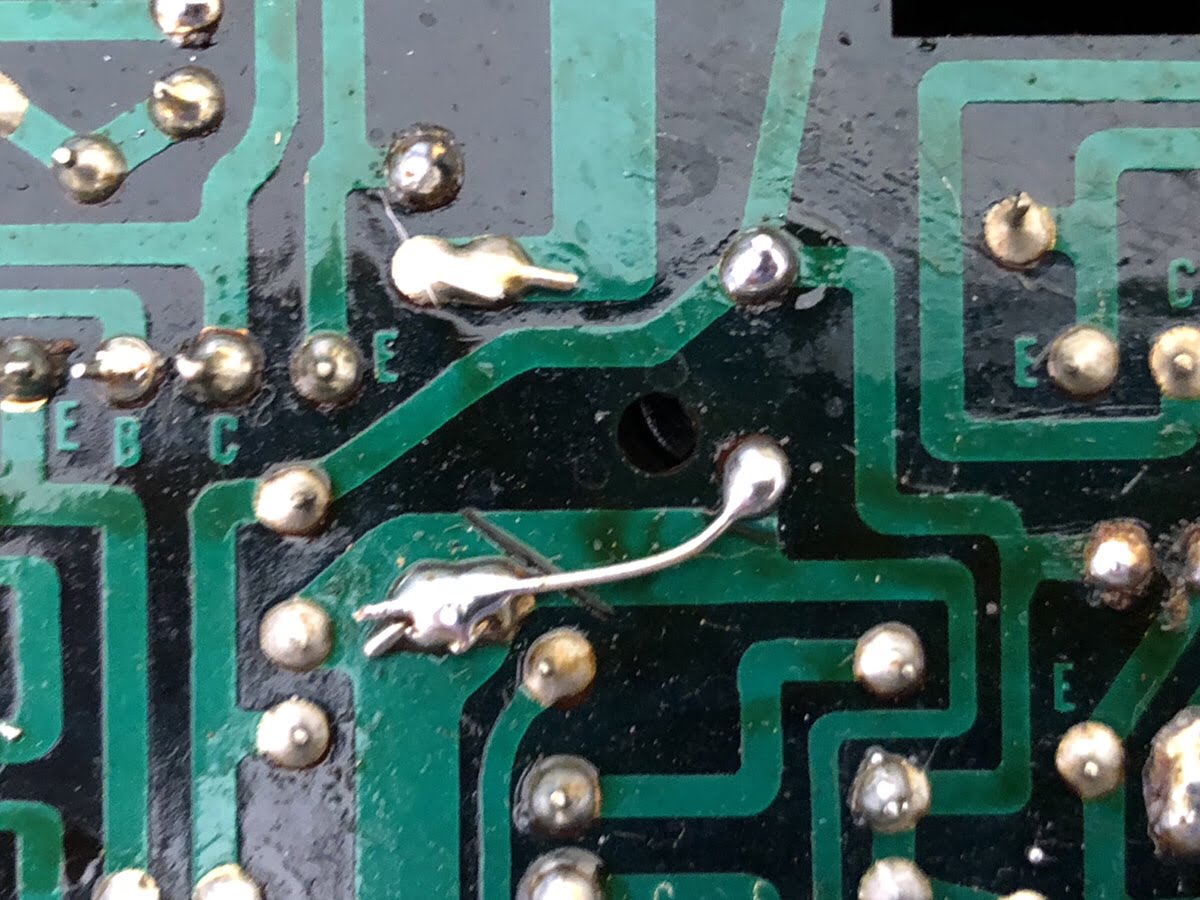
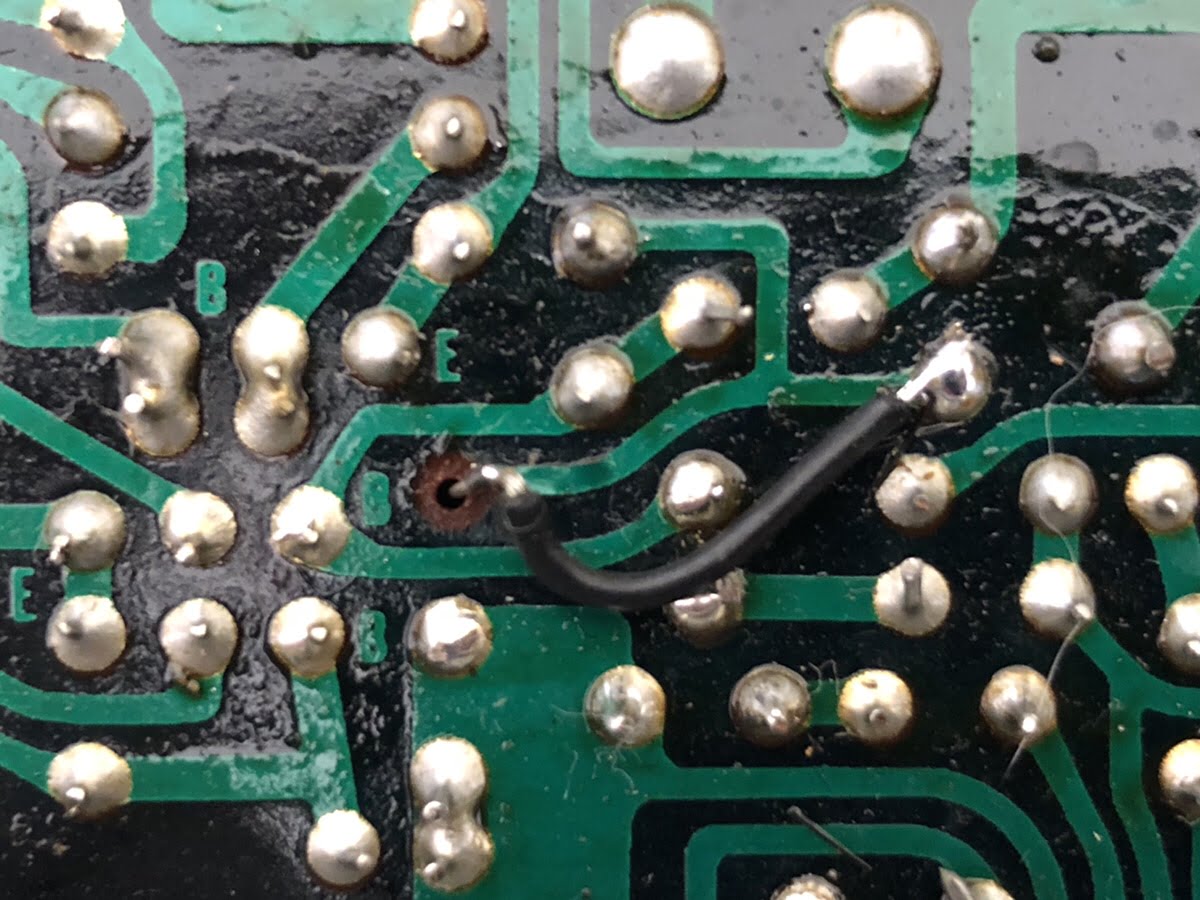
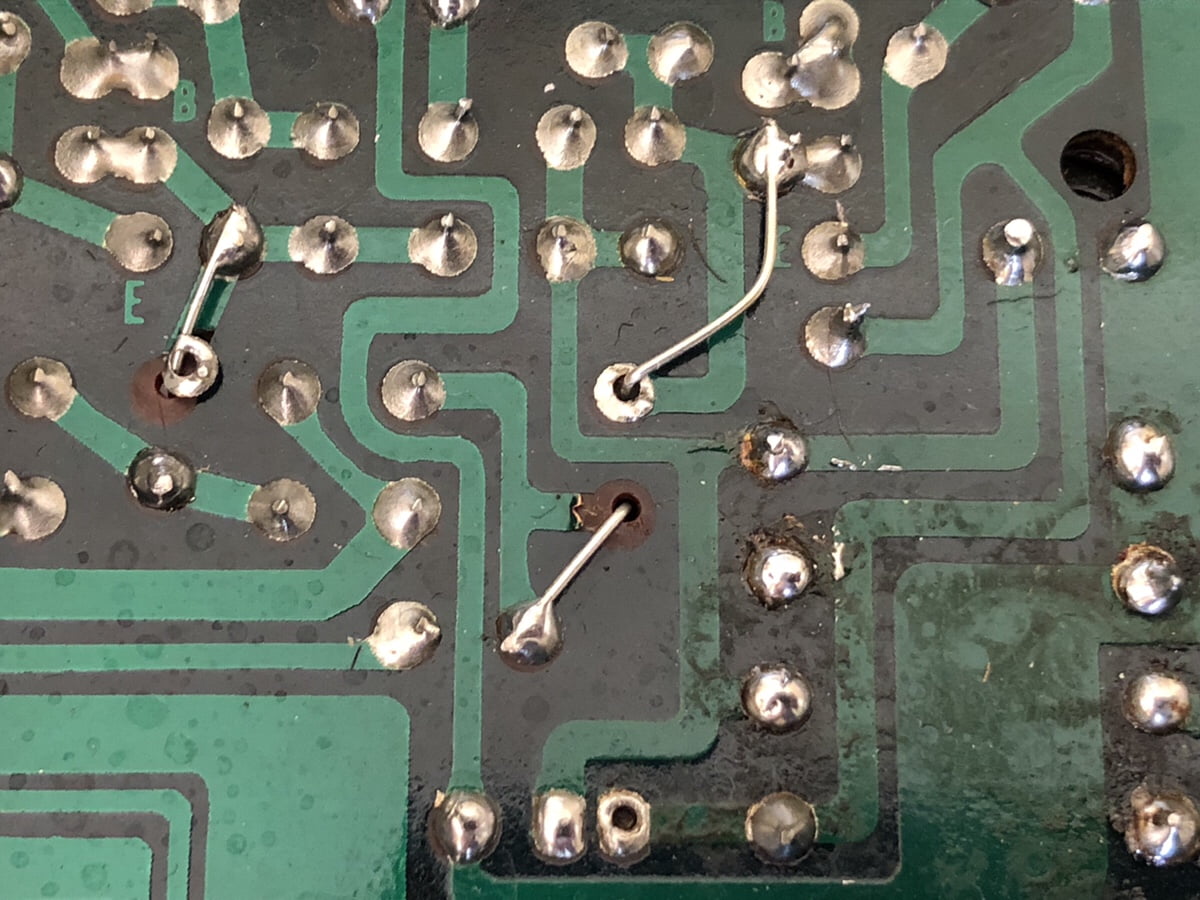
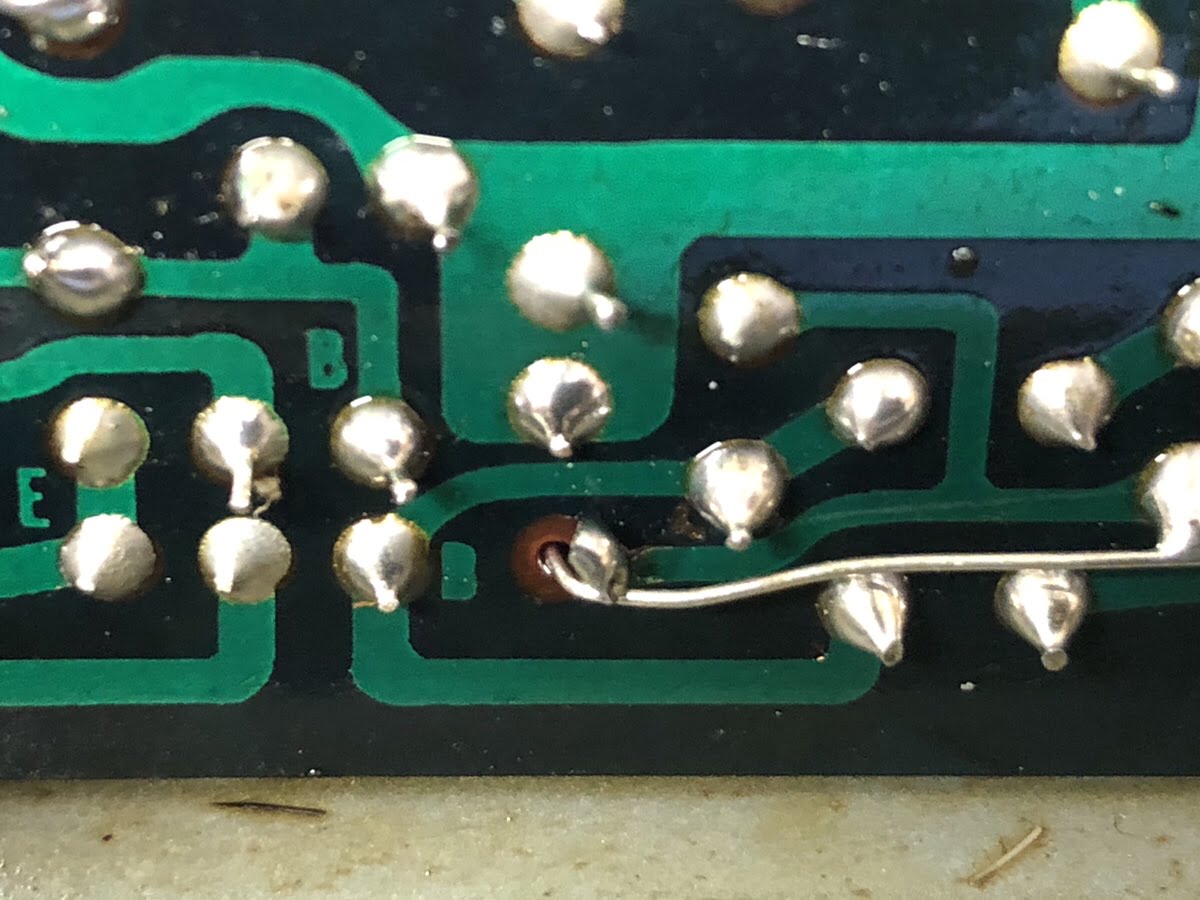
OMG, that Perreaux. Shocking.
Agreed, absolutely appalling!
Hi Mike,
Just wanted to say you’re doing an amazing job bringing things like this to light and putting the offenders on display!
I work as a motorcycle mechanic for a small used dealership/workshop myself and likewise have seen some absolutely appalling repairs and modifications made by “professionals” including soldering that might just make you weep! I’ve long thought about doing something similar to this but just don’t quite have the customer flow to do so with any degree of anonymity, not helped by the fact that probably similar to yours, my industry and the community within it are small and tightly-knit and certain lines have to be walked when you’re a small fish in that kind of pond…
All that said, having seen jobs like this done on motorcycles, cars and – in my previous careers in tool repair and watchmaking – on a raft of smaller and more intricate assemblies, it amazes me that there seems to be no limit to the areas where (allegedly) trained and practised professionals can look at any of these jobs and think “yep, that’ll do!” Especially when someone like me who has been self-taught in all my technical backgrounds and attained relevant certification through Recognition of Prior Learning wasn’t making mistakes of that level back when I was a child first learning how to use a soldering iron and multimeter!
Keep it up mate, it definitely makes me squirm to see and read but can’t deny the catharsis of it not being my problem! 😉
– Mason
(Funnily enough, I actually own a pair of Trevor Lees’ tower speakers that I pair with my Focal Sigma’s for a bit of bass. Gotta say after having read about the bloke here and elsewhere, I’m glad they were given to me by my father and I never had to meet the man in person!)
Thanks Mason, much appreciated and thanks for sharing your own experiences. I also love motorcycles and have seen some terrible mechanical stuff over the years. Totally hear you on deciding on whether to do something like this or not. I receive a small but steady pushback from offenders and their friends, though surprisingly little overall, because the evidence is so overwhelmingly damning. It’s extremely hard to argue when it’s all there in 4K and offenders generally know how bad their work is anyway. They also know that if they go after me for outing them the gloves will come off and the smart ones don’t want to make things worse. For me, it comes down to whether documenting work like this is in the public interest. In this case it is and the vast majority of people really appreciate having access to such information. That’s hilarious about the Trevor Lees speakers, thank goodness you don’t have to deal with him!
I didn’t think my amateur work was that great but after seeing these horror stories I don’t feel so bad !
I think I might cry if some of my work looked like these examples.
Thanks for commenting, Mike. I guarantee that your work is 100% better than anything in the Hall of Shame! It’s truly staggering to me that work like this is seen as acceptable by the perpetrators.
Yep. Cowboys who ride a 3 legged horse, claiming it has 4! It`s a wonder they didn`t perish in the stampede.
I have worked in both pro and high-end consumer audio manufacturing. Those ‘repairs’ make me want to weep!!! Where is the care and love for these lovely bits of kit? Disgraceful!
Hi Nicki, thanks for your comment and I couldn’t agree more. The work I highlighted here is truly disgraceful. It would almost be acceptable if it was the result of backyard tinkering, but these are the results of so-called specialist repairers. It’s mind-boggling!
Wow, absolutely atrocious work by self proclaimed “techs” – I see this all too common too, especially when it’s the equipment owners trying to repair their own gear. Even someone with no experience and a cheap dollar store soldering iron is almost guaranteed to do better work than the work on this thread. This is absolutely appalling. Thanks for sharing!
Hi Connor, yeah, this sort of work might almost be excusable if was owner-induced. The really sad part is that it was all done by so-called “experts”. I’ll never understand how people like this operate and stay in business?!
I totally agree, Mike. I have chosen my repair techs carefully over the last 40 years. Sadly in my city they have all retired and now there is no one. Fortunately, my stereo components are near new. Only the Akai GXC-760D Tape Deck is over 40 years old, and still performs like new. Akai originally guaranteed these Glass Heads to last @ 24hours -non stop play. for 16 years . That`s over 41000 hours. More than a lifetime. I estimated since 1977 when I purchased this machine, new $CDN 1000:00 it has less than 1000 hours of use. Best sound ever for a cassette deck. love your columns. Take care.
Best.
Brian.(N.Z.)
Thanks, Brian and keep enjoying those tapes!
There is a crooked repair shop here in the USA that specializes in Carver equipment and does nationwide business that does crummy work and charges top top dollar. He has special resources to promote his crooked business. How can I alert people to stay away from him??
Hi Michael, you can alert people via the usual forums and places people commonly visit, that’s probably the best way to start.
I totally support shaming dodgy technicians and in particular the unscrupulous bosses who bully their techs to spend as little time and money on a repair job as possible. Likewise the owners handing in their gear for repairs should be prepared to allow the time and money to do the optimal job and not push for quick and cheap repairs.
Thanks Ralf, and you make a very good point about business owners forcing technicians to do cheap work. Almost everyone featured on this page runs/ran their own repair business, goodness knows how, but case number 6 featuring my old Krell KSA-150 is a classic example illustrating your point. Owners wanting cheap work are thankfully not something I see often due to the way I run my business, but I do occasionally see them and try to steer them elsewhere.
ME has a “backyard build quality”? Really? Compared to MAS? In what sense? I have an old MAS amp on my bench right now and it reeks. Big time. I’ll post some photos in due course. Later models are better for sure, but MAS attention to heat is appallingly poorly implemented. When I see/measure TO5 devices operating at 80 degrees C, I sense big problems. The stuff looks great from the outside though.
As for Krell, well, I had one on the bench awhile back. The drivers were bolted to their heat sinks using plastic bolts. Saves the effort of using proper mounting procedures, but when those plastic bolts let go (and they all do), there are big problems. The old Krells (fan cooled models) were better. Except for the ones where the fan was arranged to blow air DOWN through the heat sink tunnel. Sheesh!
So, tell us, what PRECISELY is wrong with ME design and construction techniques?
And yes, as you may have guessed, I do have a horse in this race.
Hi Trevor, my name is Mike, thanks for commenting. My apologies for the delayed reply, I’ve just returned from a two-week camping break.
A quick note that I’m happy to grant permission to comment on my site, as long as interactions are polite and respectful. I have a name for example and greetings are normal. I see that you’ve emailed and commented elsewhere, I’ll reply as/where appropriate, once I sort through the several hundred emails in my inbox!
I’m not interested in debating the obvious, especially not where one party has a conflict of interest as you admit to. I’m only interested in facts, my work is not influenced by any brand affiliation. This is rare and something I’m especially proud of, along with the work I do to educate people about hi-fi equipment and expose dodgy repairers. We all benefit from this, of course!
PRECISELY what’s wrong with the ME gear I’ve worked on is that it is very crudely built, as I already mentioned, and absolutely awful to work on. Parts, construction and serviceability range from poor to terrible. I know that there are religious followers of this brand and some may be afraid to speak the truth but these are facts and any assertion to the contrary is factually and technically incorrect at best, dishonest at worst.
The Krell gear I’ve worked on has been in a different universe in terms of construction, build quality and serviceability, so much so that your comments suggest a lack of familiarity with such equipment. My comments about MAS refer specifically to the amplifiers here, no others. I work on lots of Krell gear and I haven’t found plastic bolts anywhere BTW. Nylon and other plastic fasteners are used sometimes for electrical isolation, though I’ve not seen any in Krell gear I’ve worked on.
Anyway, on these points, we may have to politely agree to disagree, and that’s OK. Again, thanks for visiting and commenting.
I am sorry for asking a stupid question but what is ME gear? What brand is that? I didn’t see it anywhere on this page
Hi Mike, no problem and not a stupid at all, ME is/was a small Australian brand, it’s short for Modular Electronics.
Please understand that I readily accept and acknowledge any criticism levelled at ME gear. Peter Stein (the creator) is somewhat less accepting of criticism though. I will address your points in order:
Parts. Yes, you won’t see $5.00 Dale resistors in an ME product. You will see high quality, $0.05 resistors, which, in specific areas, are matched. Some to within 0.05% tolerance (RIAA stages). Electrolytic capacitors are manufactured to ME specifications in Taiwan, using foil from Germany and electrolyte from Italy (or the other way ’round – I forget). And those caps last a very long time. I’ve pulled caps from amps built in the mid-1980s (convection cooled) and they still meet spec (ESR, ESL and capacitance). And that was for convection cooled amps. By comparison, I’ve had three Mark Levinson amps in over the past year or so. The main filter caps could be used as a baby’s rattle. Emitter resistors in ME amps are standard, low inductance types, matched to within 1%. Semiconductors are standard TO3 Motorola types, US sourced low signal types, or Japanese drivers and outputs, depending on the model. All semiconductors are matched to within 1% tolerance for hFE and Vbe. Switches are gold plated, Lorlin or C&K. Pots are Alps ‘Blue Velvet’. Trouble with ME products is the stuff you DON’T see. Like the extreme level of matching used for EVERY semiconductor (except for control ones) in the amps. As you would be well aware, to match 8 TO3 output devices to within 1% tolerance requires a substantial stock holding and a great deal of labour.
Crudely built. I guess that is a matter of opinion. When I worked on the Levinson amps, it took the best part of a day to remove ONE output stage. It was impossible to test the output stage on the bench. By comparison, I can remove BOTH output stages from an ME1400/1500, ME850, ME750, ME550 in less than 30 minutes. I can connect it to my bench power supply and operate on the module as required. Dismantling the module, itself, takes another 5 minutes, when any faulty parts can be replaced. Simple, quick and easy. The Krell I have out back is waiting on some unobtainable FETs. Don’t get me started. Don’t get me wrong, the Krells I’ve seen are decent enough to work on (except those KAV things) and they do use quality components. Easier to work on than any Levinson? Yep. Easier than an ME? Nup. I readily acknowledge that the most polite comment about ME STYLING would be: Industrial. They ain’t pretty. But they are exceptionally well engineered. The fan cooled models draw air through the main filter capacitor banks and then through the heat sinks. Output stage temperatures are kept with 5 degrees C by a continuously variable speed fan. Great design and part of the reason why the main electros last so long. In fact, I would call the design (of the cooling system) borderline genius. And I’ve seen an awful lot of amps in my 50+ years in the biz (i started when I was still in school, servicing for the local music store). FWIW: I refuse to accept Mark Levinson amps for repair anymore. I have more to do with my life. Krells are fine.
Seviceability. Sorry Mike. You are flat out wrong. I’ve been servicing audio equipment for more than 50 years. Those 1970s Marantz receivers were a little easier than an ME, when I was national service manager in Brookvale, but I’ve not seen much else that is easier than an ME. Certainly nothing in the high end arena anyway. Not Mark Levinson, nor Krell, ARC, Rowland, whatever.
I am reasonably familiar with Krells. I’ve worked on a few, ranging from their ancient stuff (KSA50 and KSA100), to the KSA250 (I think) and the one I mentioned with plastic bolts. I can’t recall the model number, but I’d guess it was a late 1990s product and the plastic bolts were factory fresh. Generally, Krells are well built and reasonable to service. That said, they ain’t perfect either (no amp is), but they are certainly decent enough. Cosmetics are second-to-none. WAY nicer than any ME amp.
As for your honesty, I expect nothing less. Which model/s of ME amps have you worked, BTW? I should add that there are a couple of really good reasons why there are so many ME fan bois around:
1) Sound quality. NOTHING sounds quite like an ME.
2) Price. ME amps were typically way less than half the price of an equivalent foreign product. Listen to an ME850 sometime and tell that it is not a world class amp.
Now if you want to see rubbish design, look at Musical Fidelity, Sim Audio and others.
Anyway, sorry for the rant and thanks for responding.
Hi Trevor, no worries, good discussion, though this does read like an advertisement for ME and as you represent the brand, we might finish this particular discussion here. Appreciate your thoughts though and people can make up their own minds.
Briefly, as I am inundated at the moment:
Regarding engineering, to say the ME gear is exceptionally well-engineered to me is like saying a Lada is exceptionally well-engineered. You are way off here IMHO! In terms of build, the ME I’ve seen has been solid, but again, crude. Parts are disappointing, no matter how well-matched they may be. Five cent resistors and re-badged Taiwanese caps are not good enough in high-end gear. I’ve said this about MF, Redgum and others.
In terms of serviceability, almost everything I’ve worked on has been more serviceable than the ME gear I’ve looked at. Perhaps I’ve been spoiled but even basic Japanese gear has been easier to service. I’m willing to be persuaded but I need to see some nicely made, serviceable ME gear.
I’ve found sonics to be disappointing, though reflective of the design decisions made. Appearance I don’t really care about. An amplifier could be the ugliest thing in the world but if it sounds good and is well-made I’ll like it!
At the end of the day, if people like the stuff, no problem. I’ve found it disappointing but I work on a huge range of gear that most never see in a lifetime. No disrespect intended towards Peter Stein either, good on him for successfully creating the brand, I take my hat off to him for that.
I’m always open to being surprised, so rest assured, if I find and work on a really nice piece of ME gear, I’ll write about it!
Onwards!
Fair point, Mike. I did not want it to sound like an advertisement. I seek only to correct misconceptions about the product. As discussed. please give me a call sometime. I do have some things I’d like to discuss with you that may be beneficial to both of us.
No problem at all Trevor and will do.
The hole Trevor Lees has dug for himself is twice as deep as the initial damage done by some bad publicity.
He’s lost his shop and basically lost his pants but is still desperately clinging to some perceived bygone glory and bombastically claiming the higher ground on social media.
So true Ralf. The problem is that Trevor is both dishonest and not the sharpest tool in the shed, an unfortunate combination. All of this could have been easily resolved had he owned the problem and fixed it, but that assumes he’s honest and didn’t know there was a problem. In truth, he knew exactly what the problem was and sold the amp anyway, misrepresenting its condition and history. Then he doubled down and, most unethically of all, blamed me for everything! All I did was give him lots of money and look inside my amplifier! Stand up guy, blaming me!! But then I exposed him, and he didn’t like that at all. Scammers like this hold onto their money with a death grip, the result was inevitable.
Hey Mike. I’m a 61 year old gay DJ from Melbourne. I’ve been around technology all of my life (I got my first electric shock at 5 years of age). Are some of these bodgy repair jobs for real? Some of these repairs are outright lethal. I will not tolerate any crap like that and he’s gonna sue you?? Fuck Off!!! I own a Primaluna HP Integrated Valve Amp running 8 EL34s. A brand new Technics SL1200MK2 turntable for play back use only fitted with an Ortofon blue cartridge and a Cambridge pre-amp for the turntable. I also own a Pioneer CDJ for play back use only. The turntable was set up using the usual protractors etc etc and I use the original rubber mat because the record is only suspended by the outer 4 cm rim of rubber to keep the centre of the record away from the motor…….not that I can hear any noise of any real issue. This gear is in my bedroom and the speakers are Wharfdale 2 ways. My man cave is set up with an Onkyo 7.1 surround amp, 2 Jensen side fired subs and 3 Blu-ray players to get around the Zone issues. My speakers are JBL towers the centre channel is a locally made Revolution and my 4 surround channels are believe it or not Dick Smith floor standing units which sound better than some at 5 times the price?? My Panasonic plasma is a HD unit which looks better than some 4K displays available today. I’m an avid trekker and am waiting to get Picard on a boxed Blu-ray edition along with Enterprise with the first episode A Vulcan Hello. Anyway take care mate and watch out for the humans masquerading as technicians. Cheers.
Hi Andrew, thanks for your comment! Yes, sadly, these are all real cases, hard to believe when you look at some of the work in these cases. I echo your sentiments regarding being sued, it’s comical, yet I see customers who’ve been burned like this and that’s partly why I created the Hall of Shame. Keep enjoying the man cave. Live long and prosper
You’re doing the lord’s work here Mike. Great to see the quality of your work and your pride in it.
What’s super scary is that your hall of shame is just what you’ve seen. Heartbreaking to think how much of this crapola must be out there.
Your customers are lucky. Thanks for being one of the good guys.
Thanks Brett, I really appreciate that. Absolutely agreed regarding just how much of this nonsense is out there. I see just a snapshot and it’s horrifying.
Dear Mike, I wish i had discovered this page years ago before by my Krell FPB 300w was butchered, it is always good to know who to avoid. I searched far and wide for someone knowledgeable and thought I was safe with an authorised Krell service centre. What could possibly go wrong? But, an incorrect repair quickly led to faults, and really serendipity (or divine intervention), saved me from an explosive catastrophe. Unbeknown to me, the safety shut off circuit had been bypassed, my biasing was a mess, some of the caps were already failing and the current draw from the wall was next to demonic – and that wasn’t the half of it. The 1st issue may have caused a cascade of events but the safety circuit is there for a very good reason and allowing that unit to leave their hands (even if they didn’t create it) was not ok. Thankfully now, my 300w unit and both 600w units have been graced by someone like you, who has passion for their work as demonstrated though quality workmanship. I never appreciated how complex the repair/service process is on these units until recently; near enough wont be good enough. Overall I learnt so much from this experience it made the wasted $1000s worth it. The deeper appreciation for their design was a light bulb moment. I’ll never part with them – ever!
Keep up the good work, resurrecting them one by one:)
Hi Teo, thank you very much for sharing your thoughts on this and I’m very sorry to hear of the problems you had with your Krell amplifiers. The good news is that you seem to have emerged with everything resolved which is a terrific result. Sadly, your experience is a common one, perhaps even the norm. As you note, in most cases, owners have no real understanding idea of just how complex such work is and many technicians are not capable of doing it, to be honest. Just have a look at my KSA-100S repair for example: https://liquidaudio.com.au/krell-ksa-100s-amplifier-repair-restoration-review/. Several days of work may be needed in cases like this. Anyway, thanks again for visiting and keep enjoying those amplifiers!
Hi Mike,
That pre-amp built in Western Australia is IMHO a shocker. It never ceases to amaze me what dodgy stuff some people will produce and sell to unsuspecting customers. 🙁 At the moment I have someone’s DIY Nelson Pass FirstWatt F3 in for repair. Ever had one of those days when you said to yourself “What was I thinking when taking on this job?” I suspect you have, and for me this is one of them.
On opening the case it would have been an extremely short list to compile of what was right with this power amplifier. It is an electric shock / electrocution hazard just waiting to happen. 🙁
– Mains wiring just twisted together and taped up with electrical tape.
– Aluminium chassis with no protective earth connection and no evidence there ever was one.
– Single pole mains switch installed in a hole that’s too big to properly accommodate it. It can easily be pushed through the panel with minimal pressure.
– The “builder” of this amplifier decided to switch the neutral side of the 240v mains rather than the active side.
– The equipped mains fuse was twice the current rating for what was supposed to be installed.
– Someone had cut four 50mm diameter holes in the front and rear panels (presumably to install something – fans??) but these were not installed so left uncovered. One could easily put at least two adult sized fingers through them and touch the exposed mains wiring on the inside.
– Double sided PCBs with half the joints not soldered correctly.
– Through hole component leads cut off virtually flush with the pads so of what solder there was on there didn’t take.
– There is significant PCB pad/ trace damage due to what looks like excessive soldering temperature and dwell time resulting in some delamination of the traces and pads.
– Some of the crimp spade terminals were the wrong size for the wires. I’m guessing the “builder” of this DIY amp didn’t know or completely ignored the significance of the colour coding of the connectors which indicate what wire gauges are intended to be accommodated in them.
– One of the output wires going from the supposedly working channel PCB to the speaker post wasn’t even soldered and whilst performing a quick visual inspection it just came adrift from the PCB. It was literally just making physical contact with the pad.
– The inside chassis was speckled with solder splashes which as you know don’t stick to aluminium so there was a good possibility one of them may have dislodged and shorted potentially shorted something out.
– You could easily see where the tip or the barrel of the “builder’s” soldering iron had touched up against some of the capacitors and melted the plastic on them. Yet another sign of shoddy handiwork.
After questioning the owner of this “little gem” (LOL), he said he cut the holes in the panels to instal some fans because he was concerned the amplifier was getting too hot. Well, the FirstWatt F3 normally runs quite hot as it’s a Class A power amplifier. Installing fans inside the chassis would have reaped little or no benefit as the radiating fins of the heatsinks are on the outside of the chassis. I asked if he built the amplifier himself and his reply was – “no, it was built by a DIY expert. Yeah…. right (LOL).
Hi Alan, thanks for your comment and yes, that Western Australian preamp is appalling. The sad/scary thing is that this sort of thing is accepted as normal by many who simply don’t know any better, through no fault of their own. I don’t work on this or any of the homebuilt stuff like the FirstWatt you have there for this reason. If it isn’t properly built by a reputable manufacturer, I won’t look at it.
Hi Mike,
The supposed reworking and improvement on the Krell Pre-Amp was an absolute travesty.
I find it totally bewildering, that someone that does so called repair work of that quality can not see how bad their workmanship is. Then again, I suppose as the saying goes “Ignorance is bliss”.
Pseudo Technicians like that, should be up on criminal charges, for putting people’s lives in danger.
The repair of a Krell is difficult at the best of times, even if you have vast experience on the brand. Anybody that has worked on a Krell, will know that these units are engineered and built to the highest standard. Even attempting a so called – upgrade – is ludicrous.
Hi Tony, thanks for stopping by and I agree with you 100%. I’m assuming you know who did this, he is based in the ACT. Thankfully, he now says he doesn’t work on Krell gear. For anyone following along, the engineers who designed this equipment knew what they were doing. A kit from Jaycar cannot improve this preamp. Anyone who knows what they are doing and has experience working on (rather than reading about) Krell equipment from this era will confirm that it is built to the highest standards. If anyone tells you they can ‘upgrade’ something like this, run.
Hi – I’ve been reading with equal amounts of fascination and horror. I’m in Canberra and have a – never opened – Denon PMA-1500R with a dodgy phono preamp stage… and now I’m terrified to have it looked at! Cheers, Tom
Hi Tom, thanks for visiting and your response means the HoS is at least having the desired effect, shocking though it is! Given that you are in Canberra, you’re hopefully aware that the offender responsible for possibly the worst case I’ve ever seen – case #4, plus case #17, is based in the ACT. This guy is one of the worst offenders, so please be careful.
Mike,
Very appalling, but entertaining as well; amazing to see treasure pieces treated with such disrespect. I need to have my 2285B worked on as the caps are failing, and since the originals are no longer available it takes some expertise and finesse to do a clean job. Now I am rolling over in my sleep praying I put it in the right hands, I wish I was in Australia and could use your services!
~ Robert
Thanks, Robert. These cases really are appalling, but quite common, sadly. Let’s assume the person you took your Marantz to knows their stuff, but just have a good look over her when you get her back. Many of the folks who owned the equipment in the HoS didn’t realise how badly damaged it was until I showed them the details.